塑胶制品不良原因之判定及处理方法文档格式.docx
《塑胶制品不良原因之判定及处理方法文档格式.docx》由会员分享,可在线阅读,更多相关《塑胶制品不良原因之判定及处理方法文档格式.docx(24页珍藏版)》请在冰豆网上搜索。
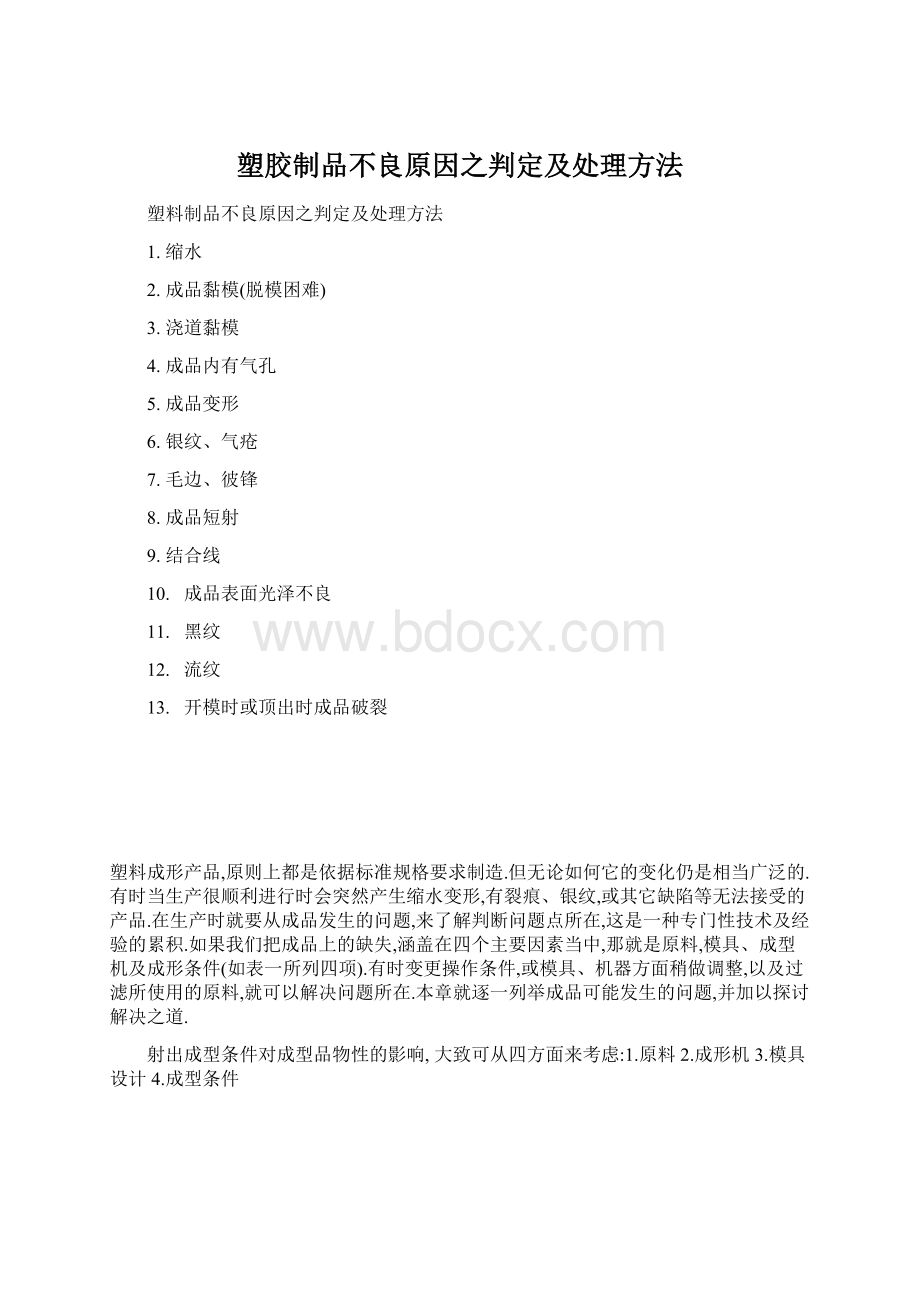
流动性模具温度
强韧性
热安全性
耐热变形性耐定性注口形状
耐药品性成形品物性
可塑化容量射出压力
锁模力料管温度(树脂温度)
可塑化方式冷却时间SCREW转速
(模具温度)
射出速度
4-1缩水
塑料品在表面的凹陷、空洞都称为「缩水」,除了会影响产品外观亦会降低成品质量及强度.缩水的原因与成型技术、模具设计及使用塑料均有关系.
塑料:
不同塑料原料的缩水率,表一参考数据.通常易缩水的原料都属于结晶性
的,如尼龙、百折胶等等.在射出过程中,结晶性塑料受热成流体状态,分子呈无规则排列;
当射入较冷的模腔时,塑料分子便慢慢整齐排列形成结晶,结果体积缩小小于规定尺寸范围,就是所谓的“缩水”.
表二:
各种塑料的缩水率
代号
塑胶原料
缩水率%
GPPS
普通级苯乙烯、硬胶
0.4
HIPS
不碎级苯乙烯、不碎硬胶
SAN
AS胶
0.2
ABS
聚丙烯胶、丁二烯、苯乙烯
0.6
LDPE
低密度聚乙烯、软胶
1.5~5
HDPE
高密度聚乙烯、软胶`
2~5
PP
聚丙烯、百折胶
1~4.7
PPO
PPO胶
PA6
尼龙6
1.0
PA66
尼龙66
0.8~1.5
ACETAL
COPOHYMER
聚缩醛、赛钢、特灵
2
CAB
酸性胶、酸醋纤杂
0.5
PET
PET胶
2.25
PBT
PBT胶
1.5~2.0
PC
聚碳酸酯、防弹胶
PMMA
亚克力
PVC硬
硬PVC
0.1~0.5
1~5
PU
PU胶、乌拉坦胶
0.1~3
EVA
EVA胶
PSF
聚偑
0.7
射出技术:
在射出技术控制方面,出现缩水的情况有:
压力不足、射出速度太慢、烧口太小成浇道太长等等.所以在使用射出机时,必须注意成形条件及保压是否足够,以防造成缩水问题.
模具及产品设计方面:
模具的流道设计及冷却装置、对成品之影响亦很大出于塑料之传热能力较低,故距离模壁越远越厚、则其凝固及冷却较慢,应有足够的塑料填满模腔,使射出机的螺杆在射出或保压时,塑料不会倒流而减低压力,另一方面水面亦不能冷却太快,以免半固塑料阻塞流道造成压力下降,引致成品缩水.不同的模流过程有不同的收缩率,熔融筒的温度控制得宜,可防止塑件过热;
延长周期,可确保制品有充分时间冷却.
缩水问题如获适当解决,可提高成品质量,减低次废产品并提高生产效率.下表即为缩水可能发生之原因及处理方法.
表三
故障原因
处理方法
模具进胶不足
增加入料
熔胶量不足
适量入料,适度调高背压
射出压力太低
增加熔胶计量行程
保持压力不够
提高射压、保压压力
射出时间太短
增长射出时间
射出速度太慢
增加射速
浇口不对称
调整模具入口大小或位置
射料嘴阻塞
拆除清理
料温过高
降低料温
模温不常
调整适当之温度
冷却时间不够
酌延冷却时间
排气不良
在缩水处设排气孔
料管过大
更换较小规格料管
螺杆止逆环磨损
拆除检修
塑品厚薄不均
增加射压
4-2成品黏膜(脱模困难)
在射出成型时,成品会有黏膜发生,首先要考虑射出压力或保压压力是否过高.射出压力太大会造成成品过度饱和,使塑料充压入其它的空隙中,致使成品卡在模穴里脱模困难,在取出时容易有黏膜发生.
而当料管温度过高时,通常会出现两种现场.一是温度过高使塑料受分解而变质,失去它原有之特性;
并在脱模过程中出现破碎或撕裂,造成黏膜.二是胶料充填入模穴后不易冷却,需加长周期时间,殊不合经济效益.所以需适度依胶料之特性调节其运作温度,至于模具方面的问题,假如进料口不平衡,会使成品脱模时易有黏膜
现象,这时就要在模具上作改进的措施,下表即为成品黏膜可能发生的原因及处理对策:
表四
填料过饱
降低射出剂量、时间及速度
射出压力或料筒温度过高
降低射出压力或料筒温度
保压时间太久
减少保压时间
射出速度太快
降低射出速度
进料不均使部分过饱
变更溢口大小或位置
冷却时间不足
增加冷却时间
模具温度过高或过低
调整模温及两侧相对温度
模具内有脱模倒角(undercut)
修模具除去倒角
多穴模进料口不平衡,或单穴模各进料口不平衡
限制塑料的流程,尽可能接近主流道
探筒件脱模排气设计不良
提供充分的逸气道
螺杆前进时间太长
减少螺杆前进时间
模心错位
调整模心,并使用「退拨」角锁紧之
模子表面过于粗糙
打光模穴表面,喷脱模剂
4-3浇道黏模(脱模困难)
表五
浇道过大
修改模具
浇道冷却不够
延长冷却时间或降低料管温度
浇道脱模角不够
修改模具增加角度
浇道凹弧与射嘴之配合不正
重新调整与配合
浇道内表面不光或有脱模倒角
检修模具
浇道外孔有损坏
无浇道抓锁
加设抓锁
4-4成品内有气孔
在射出成型过程中,有时会出现内有许多小气泡的成品,不但影响制品强度及机械性能,对成品外观价格值亦大打折扣.所以当成品出现气泡时,可检查下列几个因素,并做处理.
通常成品因厚薄不同,或模具有突出肋时,塑料在模具中的冷却速度不同,则收缩的程度不同,容易形成气泡,所以对模具设计须特别留意.
而在使用的原料方面,假如塑料带有水气,在熔胶时塑料受热后分解,则射胶螺杆公差太小时,空气容易进入模腔内形成气泡,以下即归纳可能发生原因及处理方式.
收缩程度不同容易形成气泡
材料中有水气
塑造以前将材料确实烘干,避免在塑造以前发生过度的温度变化
射料不足(气孔在结合线的位置)
检查温度射出压力、射出时间是否不够
填料量不足以防止过度之缩水
成品断面,肋或柱过厚
变更成品设计或溢口位置
提高射出压力
射出时间不足
增加射出时间
浇道溢口太小
加大浇道及人口
调慢射出速度
原料温度过高以致分解
降低原料温度
冷却时间太长
减少模内冷却时间,使用水浴冷却
水冷却过急(气孔在制品表面)
减短水浴时间或提出水浴温度
背压不够
提高背压
模具温度不平均
调整模具温度
料管温度不当
降低射嘴及前段温度,提高后段温度
4-5成品变形
塑品出现翘曲的原因很多,例如出模太快、模温过高、模温不均及流道系统不对称等.其中两种最大的可能性为1.塑件厚薄不均或转角不够圆形,因而不能平均冷却收缩,导致翘曲变形.2.有些平板型塑件,为了表而美观,流道浇口得设在浇口边角上.而射胶时,熔融塑料只能由一端高速射入模腔内,因此被凝固于模腔内的塑料份子,均被拉直往同一方向之排列状态(称为取向,此时塑件之内应力很大;
脱模时这些份子又被拉回原来的状态,因而产生变形.
为了使熔融塑料能顺利充填模腔,其设计要尽量避免以下各点:
1.同一塑件中厚薄相差太大.
2.存有过度脱角.
3.缓冲区过短,使厚薄转变相差悬殊.
从浇口分析,模具的设计要保证塑料能顺利进入模腔,故分流道要避免采用直角转弯形式,转弯点比较适合采用弧形过度区,因此短而粗的分流道最理想,有助
于减少流体取向现象.但要考虑的问题是过大的浇口会增加流道废料,亦影响塑件的外观.
另外为了避免塑料充填时紧密程度不同,导致脱模困难而引起变形,分流道的截面形状大小就要依射胶量及产品形状面改变.产品较难成型的部份分流道加子粗后,主流道也应相对加大,使主流道截面积等于引流道截面积总值.
除此之外,还有两个值得注意的问题,其一是塑件顶出装置的形式.如果顶针设备太少,容易造成变形及翘曲现象;
但顶针数量过多,会令部份成品不够美观,此时应考虑采推板方式、其二是模腔冷却流道的设计,应让塑件整体能均匀收缩,提高产品素质.
以下即将成品容易产品变形的因素一一列出,提供成型技术上参考之
表七
成品顶出时尚未冷却
降低模具温度,加大冷却水流道
延长冷却时间,降低冷却时间
成品形状及厚薄不对称
脱模后以定形架固定
变更外形设计
填料过多
减少射出压力、速度、时间及剂量
几个溢口进料不平均
更改溢口
顶出系统不平衡
改善顶出系统
模具温度不均
调整模具及冷却水路
返溢口部份之原料太松太紧
增加或减少射出时间
4-6银纹、气疮
射纹的形成,一般是由于注射起动过快,使模腔前段的空气无法被胶料融体压迫排出,空气混合在胶料内,使得制品表面光管及颜色不均,使是所谓的银纹.银纹不但影响外观,也且令成品之机械强度降低许多.所以为避免发生这种缺陷,必须找出原因并了改善.
射纹的形成,既然是由于融体塑料中含有气体,那么探讨这些气体的主要来源分别为:
塑料本身含有水份或油剂:
由于塑料在制造过程曝露于空气中,吸入水气或油剂,或者在混料时,掺入了些错误的比例成份,使这些挥发性物质在熔胶时,受高热而产生气体.
原料受分解:
如果熔胶同的温度,背压及熔胶速度调得太高,或成型周期太长,则对热
敏感的塑料如PVC、赛钢及PC等,容易因高温受热分解产生气体.
空气:
塑料颗粒与颗粒之间均含有空气,如果熔胶筒在近料斗处的温度调得很高,使塑料粒的表面在未压缩完全使熔化面黏在一起,则塑料粒之间的空气使不能完全排除出来.
所以把塑料烘干,并采用适当的熔胶温度和速度,再配合适当的背压,才能得到理想的塑制品.此外,模具设计亦是很重要的一环.通常流道很大而注口很小的工模,气体进入模腔内的机会会减少很多,而排气系统设计适当,则射纹产生的产生的机会亦会降低,如图4-1所示.
图4-1能防止少量气体进入模腔的注口设计
在射出成型技术上,有一种方法来防止射纹之产生,使模具的构造中有加压设备,但一个压缩空气入气孔.锁模后,则压缩空气进入模具中,使模内气压增高,当熔融塑料进入这高压模具时,模具的气孔在此时开始排气,使模腔内保持一定压力,增加模内空气压力,确能使模射纹发生的机会,举例说:
普通的射出方法在处理ABS水份含