No07泵解析文档格式.docx
《No07泵解析文档格式.docx》由会员分享,可在线阅读,更多相关《No07泵解析文档格式.docx(21页珍藏版)》请在冰豆网上搜索。
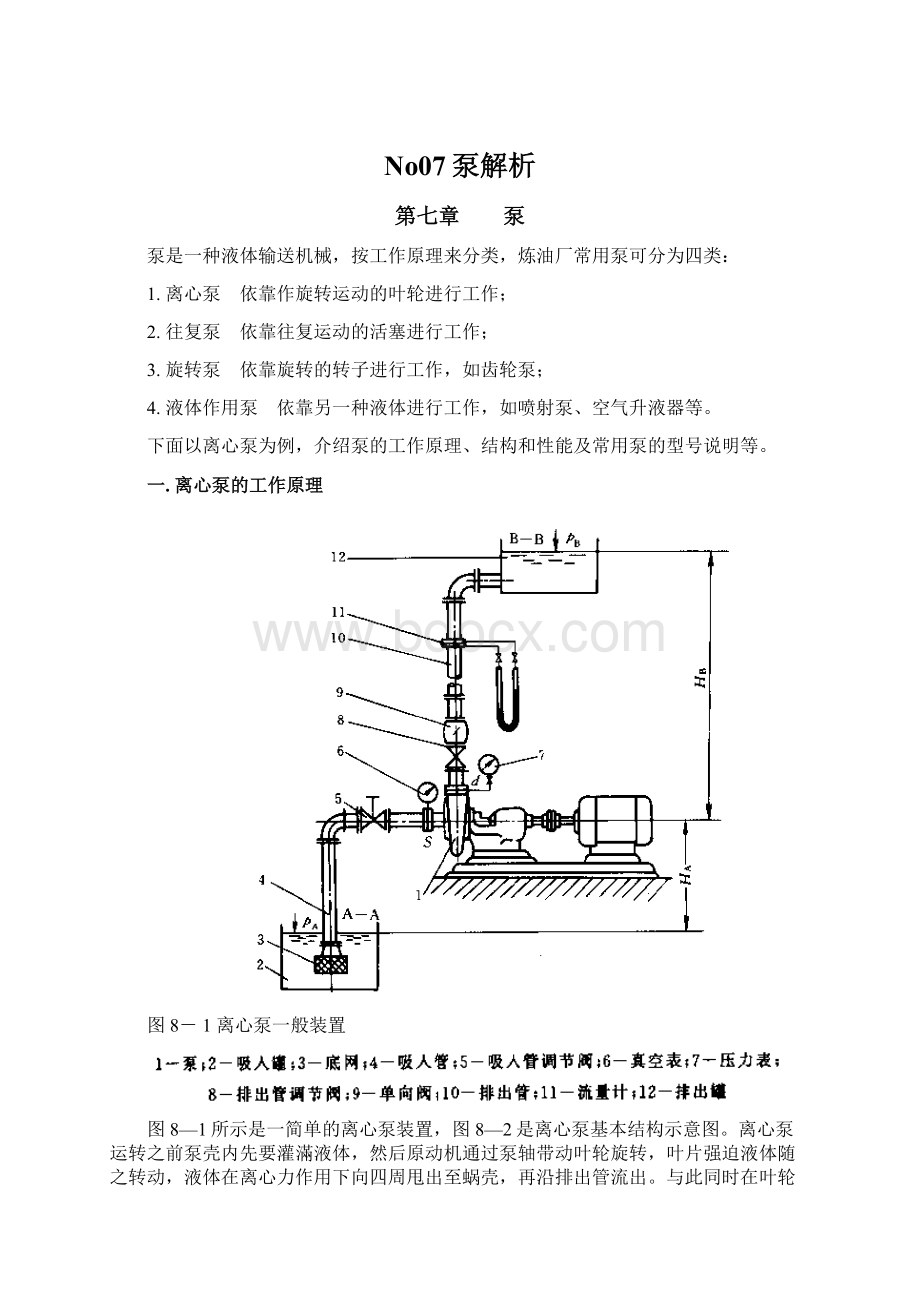
图8—l是吸入罐液面低于泵中心线的情况,称为吸入头(HA)。
炼油化工厂中更多的情况是是吸入罐液面高出泵中心线。
由于液体的质量力,使叶轮入口存在一定压力,这种情况称为罐注头。
此时液体的质量力驱使液体不断流进叶轮中心。
二.离心泵的分类
根据结构和使用目的不同,离心泵可以有很多种类型,常见的有以下几种分类方法。
按液体吸入叶轮的方式可分为单吸泵和双吸泵。
单吸泵的叶轮只有一侧有吸入口,液体从叶轮一侧进入(图8—3)。
双吸泵的叶轮两侧都有吸入口(图8-4)。
双吸泵适用于排量较大的场合。
按叶轮级数,可分为单级泵和多级泵。
多级泵是在同一根泵轴上串联了两个以上叶轮。
图8—5所示为一台两级单吸泵。
级数增多时,泵的扬程提高,可以达到的压力也随之提高。
级数更多的泵体一般制成分段式,其结构特点是壳体分为吸入段、中段和压出段,各段之间用拉紧螺栓固紧(见图8—6)。
按壳体剖分方式,可分为水平剖分式和分段式。
图3—4所示的双吸泵属水平剖分式,壳体在通过泵轴中心线的水平面上分开。
多级分段式的壳体是以与泵轴相垂直的平面剖分(见图8-6)。
图8-3 单级单吸离心泵
按输送介质,可以分为水泵、油泵、酸泵、碱泵等。
图8—3、图8—4、图8—6都是水泵,图8—5是油泵。
水泵的轴封一般采用填料密封,油泵则由于油类易挥发,同时泄漏后容易引起火灾,在密封上要求比较严格,通常采用密封效果比较好的机械密封(见图8—5)。
图8—5油泵的进出口接管均垂直向上,这是为了便于排出泵壳中的气体。
油泵根据油品温度的高低,又分为冷油泵和热油泵,一般把输送油品温度在200℃以上的泵称热油泵。
热油泵在结构上需考虑热膨胀问题,如中心支撑、支架冷却、底座中央常装有滑动导块。
此外热油泵对材料的要求更高,如冷油泵壳体可用铸铁,热油泵泵体要用铸钢。
图8—7所示是一台分段式多级高压热油泵,其结构上的显著特点是有双层壳体,以保证使用的安全,图中轴封为早期结构填料密封,现均已改用机械密封结构。
三.离心泵的型号
现将石油化工厂使用最多的水泵、油泵、耐腐蚀泵及近年来引进的流程泵型号介绍如下;
图8-4双吸式离心泵
国产泵的型号大部分按汉语拼音等编制,型号通常分首、中、尾三部分。
首部是数字,表示泵的主要尺寸(一般为泵的吸入口直径,以mm或英寸为单位);
中部是汉语拼音字母,表示泵的特征或型式;
尾部的数字表示该泵的性能参数,旧产品中该数字代表泵的比转数nl除以10的整数值,新产品中代表该泵的单级扬程(m)。
有时尾部数字后面还带有英文字母A、B、C等,它表示泵中装着外径切割过叶轮。
多级泵尾部由两个数字相乘表示,其中乘号前的数字代表泵的单及扬程[m],乘号后的数字表示泵的级数。
例如:
图8-5双级悬臂Y型油泵
图8-6多级离心水泵
图8-7分段式多级高压离心热油泵
Y型油泵的材料分为I、Ⅱ、Ⅲ三类,根据介质温度和腐蚀性来确定主要零部件的材料,见表8-1。
表8-1Y型油泵主要零件的材料
随着工业的发展和技术有进步,泵的系列也在不断地补充和更新。
例如JS型清水泵是靠近国际标准的高效节能泵,是BA型和B型的替代产品。
同时还引进了一些较先进的流程泵以便逐步替代一些效率较低的泵。
这些泵的型号大都以泵的形式、进出口直径及叶轮直径表示,
根据工作介质和使用要求及泵系列来源的不同,离心泵的型号很多,这里不一一列举,具体型号与泵性能应查阅产品样本及产品说明书。
在泵型号中出现了扬程一词,扬程是离心泵的主要性能参数,它是离心泵抽送的单位质量液体从泵中获得的能量,单位是J/kg,而生产中和样本上经常用米(m)来表示,其两种单位的关系为:
“m”=“(J/kg)·
g”,g=9.8m/s2。
四.离心泵的主要部件
1.叶轮
叶轮是离心泵中唯一的能量传递元件。
叶轮和轴以及固定于轴上的所有零件统称为转子。
当原动机带动泵轴旋转时,固定于轴上的叶轮也随之旋转,通过叶片把原动机的能量传给液体,使液体提高压力。
通过泵后液体压力的升高值ΔP(Pa),与扬程H(J/kg)和液体的密度ρ(kg/m3)有关,即ΔP=ρH(MPa)。
叶轮通常由轮盘、叶片和轮盖三部分组成。
根据三者的组合情况可有闭式、半开式、开式及双吸叶轮等结构,如图8—8所示。
叶轮多数情况下用铸造或精密铸造法整体制成。
当流道很窄不易铸造时,可采用在轮盘上铣出叶片后与轮盖焊接或铆接的结构。
叶片有前弯叶片、径向叶片和后弯叶片之分,如图8—9所示。
离心泵中大都采用后弯形叶片,即叶片弯曲方向与叶轮转动方向相反。
图8-8离心泵叶轮型式
图8-9不同叶片弯曲型式的叶轮
2.吸入室
吸入室位于叶轮入口之前,其作用是将吸入管中液体以最小的能量损失导入叶轮。
吸入室一般有三种形式,如图8—10所示。
锥形吸入室用于小型单级悬臂式离心泵中。
螺旋形吸入室目前多用于悬臂式离心油泵和剖分式多级蜗壳泵中。
环形吸入室常用于多级分段式离心泵中。
3.泵体
泵体主要是压液室,压液室的作用是收集液体和转换能量,即把从叶轮排出的液体收集起来导向排出管,同时降低液体的速度,使动能转化为压力能。
压液室是指叶轮出口到泵出口法兰(对分段式多级泵是到下一级叶轮入口)的过流部分,常见的有蜗壳和导叶(也称导轮)两种型式。
蜗壳因流道做成螺旋形而得名,如图8—11所示。
液体沿螺旋线流动,随着流道截面的增加而降低速度。
螺壳后有一扩压段,在该段主要起降速扩压作用。
对分段式多级泵,为了使结构简单紧凑,每级叶轮和下一级叶轮之间的能量转换采用导叶(导轮)结构,导叶有径向导叶和流道式导叶两种,如图8—12所示。
径向导叶流动性能稍差,流道式导叶流动性能较好,但制造困难。
离心油泵与一般分段多级泵多用径向式导叶,而分段多级高压热油泵则用流道式导叶。
图8-10吸入室型式
图8-11蜗壳图
图8-12导叶图
4.轴向力平衡装置
离心泵运转时,转子受到一个与轴心线平行的轴向力,其产生原因可作如下解释:
液体流经叶轮后压力升高,因此在叶轮前后两侧压力的分布不同,如图8-13所示。
在轮盖侧r1范围内的压力为p1,轮盘侧r2范围内为p2且呈抛物线分布。
显然轮盖侧压力低,轮盘侧压力高,这就是产生轴向力的主要原因。
轴向力一般自叶轮背面指向叶轮入口。
图8-13叶轮两侧压力分布
由于轴向力相当大(特别是叶轮的级数较多时),除个别单级小型水泵利用滚动轴承承受轴向力外,一般都需要采取平衡轴向力的措施。
单级泵常用的平衡轴向力措施:
1)采用双吸叶轮。
双吸叶轮两侧对称,轴向力相互抵消,这种叶轮一般用于流量较大的场合,如图8—4所示的泵。
2)开平衡孔或接平衡管。
在叶轮轮盘上相当于吸入口直径范围内开若干平衡孔,使轮盘前后空间相通,液体从轮盘后经平衡孔流到进口,使叶轮两例压力分布基本相同。
这种结构的叶轮在叶轮背后与泵壳间增设密封环.其直径与轮盖入口处的密封环的直径相同,如图8—14所示。
图8-14平衡孔和平衡管
3)平衡叶片。
此法是在叶轮轮盘背面装有若干径向叶片,如图8—15所示。
当叶轮旋转时,叶片推动叶轮与泵壳间的液体旋转,使叶轮背面靠叶轮中心部分的压力下降,使轴向力减小。
此法还具有减小轴封负荷,防止固体颗粒进入轴封的作用。
图8-15平衡叶片
多级泵常用的轴向平衡措施有以下几种:
1)叶轮对称布置。
图8-5是叶轮对称布置的两级泵。
叶轮对称布置一般用于叶轮数为偶数的水平剖分式多级蜗壳泵,如果级数为奇数时,第一级叶轮要做成双吸叶轮。
图8—16为叶轮对称布置的几种形式。
叶轮对称布置的要求是轴封所受压力较小;
级间泄漏量要小,即相邻级间的压差应尽量小;
同时流道应尽量简单。
2)平衡鼓。
如图8—17所示,在多级分段泵的未级叶轮后装一个圆柱形平衡鼓(也称
图8-16叶轮对称布置型式
卸荷盘),平衡鼓左面的压力为末级叶轮出口压力p2,平衡鼓与泵壳有间隙密封,平衡鼓右面是平衡室、平衡室通过平衡管与泵入口连通,其压力为p0(稍高于一级人口压力)。
因p2大于p0,故产生一个与轴向力方向相反的平衡力P平=π(r2-rm2)(p2-p0),使轴向力得到平衡。
当轴向力发生变化时,平衡鼓不能调整平衡力,仍需安装止推轴承来承受残余的轴向力。
图8-17平衡鼓
3)自动平衡盘。
在多级泵中,为适应轴向力的变化,自动调整轴向力的平衡,采用图8—18所示的自动平衡盘装置。
在此装置中末级叶轮后的压力为p,液体流过径向间隙b后压力下降为p′,再经轴向间隙b0后的压力变为p0。
p0是平衡盘后的压力,与泵入口连通,压力稍高于泵入口压力,基本不变化。
通过径向间隙b和轴向间隙b0的泄漏量q相同。
平衡盘前后压差(p′-p0)与平衡盘工作面积的乘积是平衡力,其方向与轴向力方向相反。
图8-18自动平衡装置
该装置自动平衡轴向力的原理与过程如下:
当轴向力大于平衡力时,转子向左移动,轴向间隙b0变小,泄漏量q也随之变小,径向间隙b中流速下降,使流过径向间隙b的阻力损失变小,平衡盘前压力p′上升,p′-p0值变大,故平衡力上升;
当轴向力小于平衡力时,转子向右移动,轴向间隙b0增大,随之泄漏量q增大,在径向间隙b中液体流速加大,其阻力损失增大,使平衡盘前压力p′下降,平衡盘前后压差p′-p0变小,平衡力变小。
因此,可简化归纳如下:
轴向力>平衡力b0↓→q↓→p′↑→(p′-p0)↑→平衡力↑
轴向力<平衡力b0↑→q↑→p′↓→(p′-p0)↓→平衡力↓
在这种装置中,靠转子左右移动,不断调整平衡力大小,以达到轴向力与平衡力的平衡。
平衡性能的好坏除正确设计平衡盘尺寸外,正确选取径向间隙b是一个重要问题.一般取b=0.2~0.4mm。
当液体粘度大或含泥沙等杂质时,可适当加大径向间隙b,以免间隙过小致使液流不通畅造成平衡盘失效。
4)平衡盘与平衡鼓组合装置。
这种装置兼有平衡盘与平衡鼓的综合效果,多用于大容量分段式多级泵中,如图8—19所示。
图8-19平衡盘和平衡鼓组合装置
5.径向力平衡措施
径向力的不平衡主要出现在蜗壳式泵中,通常认为液体从叶轮中均匀流出,并在蜗室中作等速运动,因此螺旋形蜗室是在一定的设计流量下配合一定的叶轮而设计的。
蜗室基本保证叶轮周围液体作均匀的等速运动,此时叶轮周围压力大体上是均匀分布的.叶轮与蜗室协调工作,不产生径向力。
当流量发生变化.在大于或小于设计流量下工作时,叶轮与涡室的协调性被破坏,在叶轮周围产生速度和压力的不均匀。
当流量小于设计流量时,涡室压力从泵舌开始逐渐上升。
在流量大于设计流量时,蜗室内压力从泵舌开始逐渐下降。
离心泵并不能总在设计流量下工作,启动和停车时在零流量下工作,生产中产量的变化也直接影响泵的流量,因此径向力是不可避免的。
径向力的合力使轴和轴