高效率高精度的柔性化焊装生产线优质PPT.ppt
《高效率高精度的柔性化焊装生产线优质PPT.ppt》由会员分享,可在线阅读,更多相关《高效率高精度的柔性化焊装生产线优质PPT.ppt(11页珍藏版)》请在冰豆网上搜索。
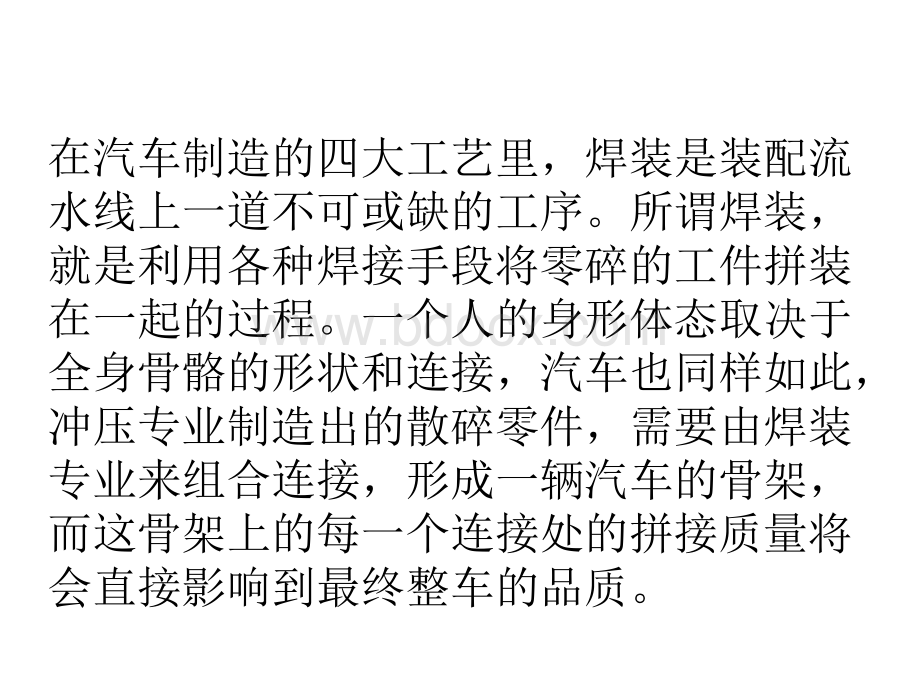
针对公司即将生产的克莱斯勒300C和其后引进轿车的白车身总成焊接工作的实际需要,公司制造工程技术人员严格按照轿车制造工艺流程,参考国内外高级轿车生产厂商先进的制造经验,在BBDC新装焊车间里建立起一套高自动化、高效率、高精度的,适合多种车型不同生产特点的柔性化的生产系统。
装焊车间的焊装作业区分为两大部分,即克莱斯勒轿车柔性化作业区和三菱欧蓝德车型生产作业区。
通过严格的招、投标程序,世界知名的跨国公司ABB公司以明显的优势中标,承担了BBDC克莱斯勒轿车生产线的主设计和制造工程。
轿车生产作业分在三个不同的区域车身分总成装焊生产作业区、车身主装焊生产作业区和车身门盖生产作业区。
公司制造工程人员和ABB公司共同策划和设计了300C工艺平面布置的同时,还兼顾到进一步引进产品的工艺流程,为其它引进车型的工艺布局预留了空间,使整个工艺流程布局更趋合理,有较为充分的发展空间,可满足克莱斯勒300C等多种车型柔性化生产的需要。
机器人在关键工位唱主角机器人在关键工位唱主角克莱斯勒300C车身分总成焊装线为主焊装线提供所需焊装分总成件。
为了有效地利用资源,车身分总成焊装线使用传统人工生产方式进行生产,其产能完全符合主焊装线的需要,并能够高效地保证产品质量的稳定。
分总成零件最终在主装焊线上进行拼装,组成一部完整的车身骨架。
克莱斯勒300C主装焊线是生产线上最重要的一部分,为提高产品质量和空间利用率,有效降低制造成本,在主装焊生产线上的下体焊装工位、车身大装工位(I/II)、顶盖工位及车身冲孔这5个关键工位上,均采用全自动机器人操作。
机器人定位准确、焊接及冲孔精度高、质量稳定,可在人工焊接难以操作的部位出色地完成焊接。
例如,在大装(I)工位,经由输送系统传输至该工位的车身下体总成被工作站定位后,左右各一台机器人利用所持有的侧向夹具抓取左、右侧围内板总成后,与工作站基板夹紧到位,龙门平台最高处的机器人由传输机器人处抓取车身顶盖的各横梁后,将工件与夹具一同与工作站基板夹紧,各机器人松开夹具后,抓取焊钳与其余持有焊钳的机器人一同对车身进行焊接作业。
焊接作业完成后,传输机器人再次抓取工件并解除工作台夹具的夹紧状态,工件即可送至下一个工作站。
在机器人冲孔工位上,装焊车间引进了车身整体冲孔技术,取代了传统的在单一零件上冲孔的操作方式,使车身装配质量大幅度提高。
车身上装配孔位置的精确度,直接影响在总装配时的各种配件能否与车身完美契合;
装配孔之间的空间关系,决定了各个配件经装配后是否处于最佳配合状态,能否发挥出最优的性能。
传统的单一零件冲孔方式,虽然可以保证装配孔在单个零件上的位置准确,但是在白车身总成焊装后,往往因为零件拼接时的误差积累,导致各装配孔的空间位置发生变形,一方面增加了整车装配的难度,另一方面,由于位置偏移,各个配件之间的配合受到一定影响,留下汽车使用时的不良隐患。
而最新采用的车身冲孔技术将冲孔操作移换为焊装的最后一道工序,当白车身总成焊装好以后,再进行冲孔。
在冲孔工位上,4台大型机器人和专用冲孔机系统将车身上关键的孔洞进行空间定位,保证各个孔之间的装配关系,配合专用工装,在车身定位后进行冲孔,保证了装配孔与车身的一致性,大大提高了车辆的装配精度。
根据对公司引进产品结构的分析,针对白车身总成制造过程中的零部件状态及生产过程相似程度的现状,并充分考虑到质量、成本及未来发展等诸要素,300C车身生产线上的各个工作站均为柔性化的加工单位,为今后投产的车型预留出工位,在增加部分设备和工装的情况下,即可以满足多种车型共线生产的需要,在保证提高自动化率的同时,也降低了制造成本。
为辅助各机器人工作站的工作,生产线上还设置了部分人工工作站。
为满足产品质量的需要及适应自动化生产线的高速度,这些手动工作站均采用了一流的加工设备及工具。
先进的中频逆变一体化焊钳系统可以根据自动测量获得的板材信息,自动调整焊接规范,避免漏焊、虚焊,保证了车身焊接质量。
NIMAK中频逆变悬挂焊机的结构设计充分体现了人性特点,操作极为方便,焊装操作时飞溅小,在很大程度上改善了加工人的工作环境。
由于300C机盖及行李箱盖的材料为高强度铝合金,焊接难度大,因此,在内板安装附件时使用了机器人铆接系统对其进行铆接,以替代焊接加工。
加工好的门、盖内板经机器人涂胶机涂刷密封胶后,与外板一同放入机器人滚轮折边系统的夹具上进行合边,保证了车门总成具有良好的牢固性和密封性。
这种门、盖合边工艺以其投资及占地面积少、柔性化强、维修成本低等优势,正逐渐被国内主要汽车厂所采用。
新装焊车间采用了大量的机器人工作站,充分利用了机器人在现代制造业中的优势。
其中,包括使用了机器人点焊、机器人弧焊、机器人搬运、机器人冲孔、机器人涂胶、机器人合边、机器人铆接等作业方式,初步实现了生产过程的自动化。
现代化物流输送体系贯穿始终现代化物流输送体系贯穿始终在新的装焊车间里,每一个加工单元都是经过精心设计、优化组合而成,工件加工效率高,可充分满足生产节拍的高节奏。
这些单元可以看作制造过程的关键节点,而这些节点则需要有一条高效通道来连接,才能形成一个完整的制造系统。
而负责将这些加工单元串接起来的,就是贯穿整个生产车间的输送系统。
车间物流输送体系采用了地面、空中分层运输方式。
在地面,使用轻型转运车、叉车等方式将冲压件、分总成件等零部件运送到工位,工位间采用气、电葫芦进行工件传递;
在空中,白车身骨架总成则由EMS空中电动车自动传送系统从主装焊线传送。
EMS(ElectricalMotorSystem)空中电动车自动传送系统可以根据生产需要,调整不同的传输速率。
该系统的抱具主体结构一致,抱具爪可根据不同车型的要求进行抱具块转换,实现车身混线传输、柔性化生产。
为在生产不同车型时进行车身识别,传送线上采用了SIMENS的E系列MOBY系统,实现记录、识别车身动态信息和电动小车及抱具的检测功能,且可以通过LED显示屏,将生产信息和设备状态进行实时报告。
无论是欧蓝德还是克莱斯勒轿车,焊装后的白车身骨架都要通过一条总长120米的白车身总成调整线,该线以滑橇为车身载体与板式链构成一条20个工位的车身调整线,在沿线工位上完成车门、机盖、翼子板等分总成的安装和车身调整、打磨等工序的操作。
在这里,每一个车身都要经过一系列精心的调试,保证各项工艺间隙的精确度,任何一个不平整的小瑕疵在车身经过检测光廊时都将无所遁形。
经过检验合格后的白车身总成,通过举升机回到空中的车身输送线上,再通过车身识别系统,按照不同车型的分类,有序地存放在车身储存区内。
位于车间上部的储存区可容纳不同车型的白车身63辆,分别排列在7条存储线上,按照“一种车型存放在一条储存线”进行车身存放。
根据下道工序喷漆车间的生产安排,存储区会自动将不同车型的白车身按要求输送至喷漆车间的入口,随后,空滑橇将按照系统规定的路线自动返回车身调整线的开始端进入下一个生产循环。
车间输送体系犹如一条生命的大动脉,在车间里形成一个上下结合、立体交叉的输送网,及时、准确地将物料送至每一个所需单元,为车间的正常运转提供了充足的动力。
而装焊车间1.9万平方米的工作面,因此向上延展至整个空间,达到充分利用空中资源,更好的提高工作效率,保障生产节拍,提高单位空间使用价值的目的。
新的CG/MMC焊装车间的规划中充分体现了新世纪现代化大生产的特点,即以柔性化的自动化生产方式保证产品具有多样性以适应市场需要;
以高效率的批量生产方式降低产品的制造成本;
以高精度的生产设备和工具保证产品的优异质量。
目前,装焊车间已经具备生产克莱斯勒300C和欧蓝德两种白车身总成的装配及25辆/小时的生产能力,待到第三种车型投产后,装焊车间的生产节拍将提升至40辆/小时,年产量可达到15万辆。