机械拆装实训.docx
《机械拆装实训.docx》由会员分享,可在线阅读,更多相关《机械拆装实训.docx(8页珍藏版)》请在冰豆网上搜索。
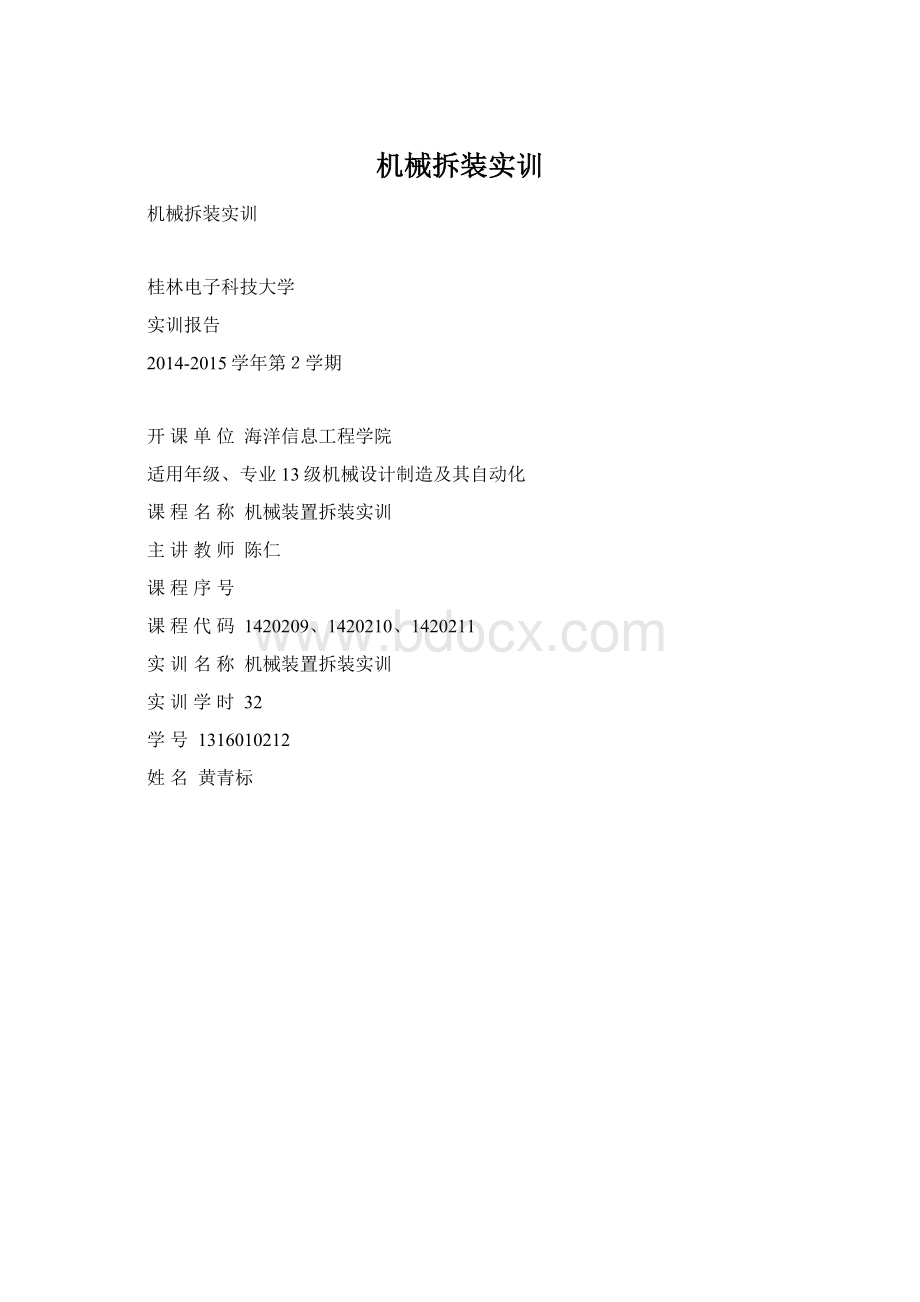
机械拆装实训
机械拆装实训
桂林电子科技大学
实训报告
2014-2015学年第2学期
开课单位海洋信息工程学院
适用年级、专业13级机械设计制造及其自动化
课程名称机械装置拆装实训
主讲教师陈仁
课程序号
课程代码1420209、1420210、1420211
实训名称机械装置拆装实训
实训学时32
学号1316010212
姓名黄青标
提高对本课程知识的综合应用能力。
通过拆装普通型车床,学习中等难度的机械机构、机械装置的拆装方法,通过车床典型部件的拆装及检测、调试检验,牢固掌握专业知识,提高实践动手能力的重要手段,是学生专业技术训练的重要组成部分。
1)专业能力目标
(1)能执行与职业活动相关的保证工作安全和防止意外的规章制度;
(2)能看懂机械设备技术文献、设备主要部件功能及装配图;
(3)能根据机械设备的结构特点,选择正确的拆装方法,对固定机构、传动机构、轴承和轴组机构进行正确的拆卸与装配;
(4)能进行零件测绘,根据测绘数据绘制标准零件图;
(5)能正确选择和规范使用机械设备拆装工量器具;
(6)能合理选择和正确使用机械设备精度检验设备、仪器和工具及保养方法;
(7)能对机械设备进行总装配、调整、试车及精度检验
2)方法能力目标
(1)能通过多种途径、运用多种手段收集完成工作任务所需要的信息,并对信息进行整理和分析;
(2)能自主学习、独立思考、善于分析、总结工作中的经验,吸取失败的教训,达到举一反三,能力迁移的目标;
(3)能通过工具的使用、设备装调的过程,形成一定的空间感、形体知觉及良好的动作协调能力。
3)社会能力目标
(1)能有求真务实、认真工作的态度,爱岗敬业的职业道德;
(2)能认真细致地观察事物,善于思考分析,及时化解不利因素,保持良好心态,尽快适应工作环境;
(3)能与他人正常交流和沟通,具有合作意识,适应团队工作,并能组织和解决工作中出现的问题;
(4)具有较强的社会责任感,良好的节能环保意识和文明生产习惯。
2.实训要求
(1)实训应完成课程规定的各项教学内容,应以学生独立操作为主,结合示范讲解的方式进行;
(2)实训期间,应模范遵守各项规章制度,严格劳动纪律,在教师的指导下严格按照操作规程进行操作,杜绝任何设备及人身事故的发生;
(3)工量具要爱护使用,负责保管、保养,必须按要求整齐,有序的摆放,不准堆放,混放;
(4)实训结束时,擦净精密量具并保养,清刷量具盒工具,经检查清点后方可离去;
(5)爱护室内一切设施和设备,爱护工量具,对损坏、丢失的按学校规定赔偿;
(6)严禁在实训场地内喧哗、吵闹、做与实训无关的事;
(7)实训结束后,每个学生应独立完成实训报告的撰写。
3.常用拆装工具的正确使用与保管
1)每一个同学都应熟练掌握所用工具名称,规格和用途。
2)工具使用完毕和一天工作结束后,要清点工具,并将工具擦干净,然后分类整齐摆放在工具柜。
3)工具由各组保管好,使用时不要相互乱扯。
4)实习完毕应按工具明细表进行核对,然后交还老师,如果有损坏,丢失都要按学院工具赔偿条例处理。
二、实训任务
1.基本知识:
⑴掌握部分:
普通车床的工作原理、主轴箱传动系统、各种零部件的功能及原理,掌握螺纹连接装配工艺、轴承和轴组的装配工艺以及键、销等连接的装配工艺,掌握各种传动机构的装配工艺。
⑵熟悉部分:
熟悉拆装工具的使用,熟悉装配基本知识,包括装配工艺,装配时的连接和配合,装配时零件的清理和清洗等。
⑶了解部分:
了解装配的实质,装配工艺规程及其它各种机床的装配工艺。
2.基本技能:
根据机床主轴箱装配图,掌握各种零部件的拆装方法及其调整。
⑴熟练掌握部分:
熟练掌握下列各种部件的拆装方法:
皮带轮、传动轴、润滑系统、滑动齿轮组、操作系统、三爪卡盘、主轴。
⑵基本掌握部分:
联轴器、链传动的拆装方法。
⑶提高部分:
通过拆装实习,了解各种机床(车床、钻床、铣床、磨床、数控机床)的结构、原理及装配工艺,并对其进行工艺分析。
在实习过程中,应运用现场教学、多媒体教学、讨论、作业、实习报告和参观等多种教学方式,加深和扩大知识面,丰富教学内容。
三、实训的主要内容
1、主轴箱的拆装
2、进给箱的拆装
3、溜板箱的拆装
4、刀架、拖板、尾座的拆装
5、车床检测
四、实训收获与体会
在这万物复苏的3、4月份,我们机械班级进行了为期32个课时的机械装置拆装实训。
通过这次实训、这次车床解剖实训,我从会使用车床到了解车床,从中我学到了基本的车床理论知识、车床拆装的注意事项和课本学到的理论知识得到了巩固、进深一步的理解。
在老师的精心指导下和与老师经验之谈中,我发现我还是太差了,学习到的专业知识可以说是九牛一毛,我们还需要长时间地更深层次地学习。
下面我按课时的顺序来说说这次实训的收获和体会。
1、尾座的拆装
在金工实训使用车床时,我就很好奇尾座是怎么样运行的,当然这个问题我一直都不解,现在通过这次实训终于了解了。
尾座夹紧与松弛轨道是利用了类似于凸轮的机构,旋转摇柄可以实现尾座与轨道的夹紧和松弛;顶针和钻具的夹紧与松弛是靠摩擦来实现的;其中最为重要的是知道了我以前一直无视的地方,尾座底部为什么有一个厚的垫座,不是多余的吗?
通知老师的讲解我知道了这个垫座的作用是调整对心和方便换规格。
拆装的过程,拆的时候很顺利,装的时候出现一些问题,套筒装不回去,经过我们一起动手发现装不回去的原因有两个:
一、键出现了变形,二、加紧与松弛套筒的手柄安装顺序不对。
最后经过我们的修改顺序组装好,完成老师布置的任务。
2、进给箱的拆装
进给箱的组成和我原想的差不多,是一些齿轮的组合来改变转速,以便适用于不同粗糙的工件。
拆时先拆下后盖箱的一个给进给箱动力的大齿轮,再拆光杆,卸下进给箱;卸下进给箱后我们会发现进给箱里面是由两个平行齿轮组组成的。
这些齿轮可以组合成24种转速。
进给箱的机构可以一模了解,所以我们组没有把一个个齿轮都拆下来,不过通过其他组拆卸下来的齿轮,我们可以发现齿轮塔是、以套的形式固定的,然后画出进给箱的传动系统图。
装回进给箱很简单,按拆卸的返步骤装就可以了。
3、主轴箱的拆装
主轴箱是车床等机床的重要的部件,是用于布置机床工作主轴及其传动零件和相应的附加机构的。
主轴箱采用多级齿轮传动,通过一定的传动系统,经主轴箱内各个位置上的传动齿轮和传动轴,最后把运动传到主轴上,使主轴获得规定的转速和方向。
车床工作是要求主轴平稳、基本无径向跳动和前后位移(轴向位移),这既然要求零件的高精度,也要求安装的准确。
所以学习拆卸与安装是一次好的训练。
按照先拆的零件最后装配,后拆的零件先装配的原则进行拆装,主轴箱拆卸基本顺序:
拆卸顺序从主轴箱的左端向右端开始;首先拆卸保护罩与法兰、打开主轴箱盖、移开防松弹簧、松开齿轮紧定螺钉、再放松主轴箱右端圆螺母、松开箱内滑动轴承螺母、主轴左端双锁紧螺母、然后左端锥轴承盖、垫物轻打主轴左端、最后依此取出箱内零件、主轴。
在这拆卸的过程中,我们需要注意的是先松开放松弹簧和固定螺母,再卸下主轴。
如果发现主轴很难卸下,就要及时回头看看那些固定位置没有松开,切勿盲目暴力拆装,拆装时注意听拆装敲打的声音,正确的安装敲打的声音是不会太大的。
卸下后仔细看了主轴箱的传动系统,再画出其传动系统图;测绘主轴、大齿轮、离合器和前轴瓦,记录数据和基本形状,回去后再画出其图。
装回去按原路返回就可以了,安装离合器要注意一定的方法——做键槽位置标记;安装时前轴瓦要是松弛状态的,我们小安装时忘把前轴瓦松开,结果怎么也装不回去,最后发现了问题所在松开前轴瓦就可以装好了;主轴后部安装时需要我们准确记住安装的步骤。
4、溜板箱的拆装
未拆装之前,溜板箱是我最不解和最好奇的方法,不知道它是怎么工作的。
拆卸下来我们不难发现溜板箱是通过离合器和齿轮啮合情况来实现手动与自动、横向与纵向不同的进给。
拆卸的顺序:
卸下刀架、横向走刀板,再卸下光杆,在拧开螺铨卸下溜板箱。
然后了解传动系统并画出传动系统图。
再按先拆后装的原则安装回去,安装时,我们遇到了一个问题:
离合器不能调节。
我们无法解决,最后请教了老师,才知道我们的溜板箱少了个固定销,所以离合器不能调节。
到这里车床的拆装就到此结束了,从而可以画出传动系统图、主轴图、大齿轮图、离合器图和前轴瓦图,如图。
车床传动系统图
前轴瓦图
5、车床检测
(1)床身导轨在垂直平面的不直度
采用框式水平仪进行检测,首先,把溜板按150mm划分成若干段,然后在框式水平仪不旋转的情况下,进行检测,检测的数据=检测贴片+框式水平仪的读数(刻度=150*0.02/1000=0.003mm),记录数据如下表,并画出不直度表。
溜板在垂直水平面的不直度
测量位置
0-150
150-300
300-450
450-600
600-750
水平读数
-0.238
-0.241
-0.233
-0.247
-0.238
(2)主轴锥孔中心线的径向跳动
简易方法:
此项检验是在CA616型车床上进行,将300mm锥度检验棒插入主轴孔中,用千分表分别在远、近端检测,检测数据如表格。
主轴锥孔中心线的径向跳动
测量位置
第1次
第2次
允差
是否合格
近端a
0
0.15
0.01
否
远端b
0.2
0.18
0.02
是
溜板移动对主轴中心线的不直度
0度位置
a0=0.7
b0=0.91
180度位置
A180=0.83
B180=0.96
误差计算
A=0.13
B=0.05
允差
0.03
不合格
0.015
不合格
实践是检查真理的唯一标准,我们只有通过实践才能真正理解自己学到知识的多少与正确,实践同样可以帮助我们增加理论知识的理解。
这就是这次实训给我最深的体会,只有做了才知道自己有多少知识,只有做了才知道自己是否真的理解和掌握了知识。