皮带轮的数车加工工艺分析数控技术Word格式文档下载.docx
《皮带轮的数车加工工艺分析数控技术Word格式文档下载.docx》由会员分享,可在线阅读,更多相关《皮带轮的数车加工工艺分析数控技术Word格式文档下载.docx(19页珍藏版)》请在冰豆网上搜索。
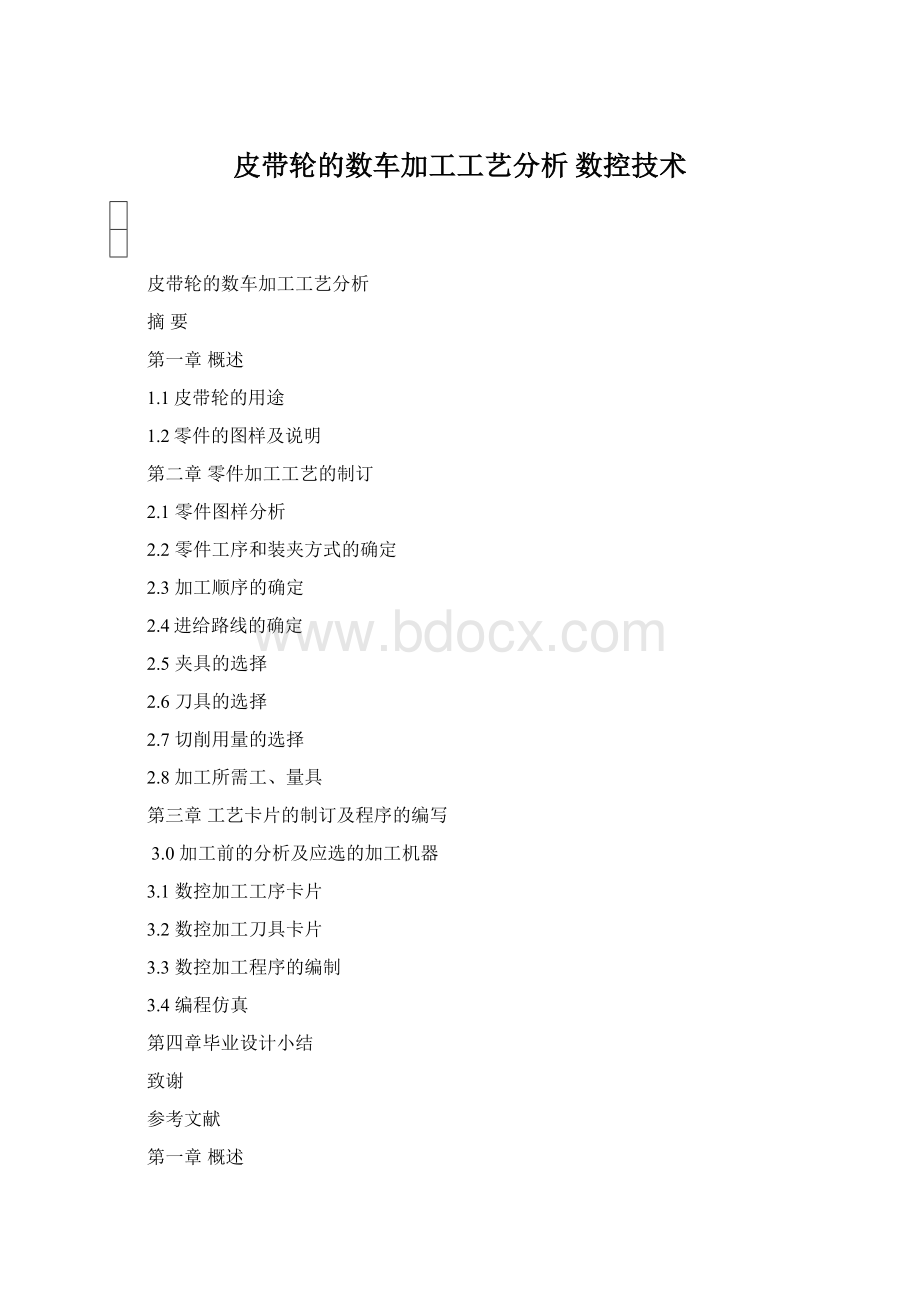
第四章毕业设计小结
致谢
参考文献
生活中,皮带轮对我们来说很常见,它的应用很广泛,机械传动常见的类型有摩擦轮传动、带传动、链传动、齿轮传动、蜗轮蜗杆传动、螺旋传动等类型。
带传动根据横截面形状不同可分为平带传动、V带传动、多楔带、圆形带、齿形带等类型的带传动。
带传动中用于安装传动带的轮子就叫做带轮。
俗称皮带轮。
带轮是成对安装和使用的,一个是主动轮,另一个是从动轮。
机械传动按传动的工作原理分类可分为啮合传动和摩擦传动两类。
啮合传动的优点是工作可靠、寿命长,传动比准确、传递功率大,效率高(蜗杆传动除外),速度范围广。
缺点是对加工制造安装的精度要求较高。
摩擦传动工作平稳、噪声低、结构简单、造价低,具有过载保护能力,缺点是外廓尺寸较大、传动比不准确、传动效率较低、元件寿命较短。
带传动就是摩擦传动中的一个种类。
带传动的工作原理是带紧套在主动轮和从动轮上,因而带与轮的接触表面存在着正压力,当原动机驱动主动轮回转时,在带与主动轮接触表面间便产生摩擦力,使主动轮牵动带,继而带又牵动从动轮,将主动轴上的转矩和运动传给从动轴。
从带传动的原理可知道带轮的作用是通过传动带传递转矩和运动。
皮带轮的外形图
数控车削是数控加工中用得最多的加工方法之一。
由于数控车床具有加工精度高、能作直线和圆弧插补以及在加工过程中能自动变速的特点,因此,其工艺范围较普通机床宽得多。
凡是能在数控车床上装夹的回转体零件都能在数控车床上加工。
针对数控车床的特点,下列几种零件最适合数控车削加工:
1精度要求较高的回转体零件;
2表面粗糙度要求高的回转体零件;
3表面形状复杂的回转体零件;
4带特殊螺纹的回转体零件;
数控铣削是机械加工中最常用和最主要的数控加工方法之一,它除了能铣削普通铣床所能铣削的各种零件表面外,还能铣削普通铣床不能铣削的需2~5坐标联动的各种平面轮廓和立体轮廓。
根据数控铣床的特点,从铣削加工角度来考虑,适合数控铣削的主要加工对象有以下几类:
1平面类零件;
2变斜角类零件;
3曲面类零件;
2.1零件图样分析
皮带轮如下图:
图纸中所选的材料为45钢。
经分析:
该零件图结构合理;
轮廓几何要素所给定的条件充分;
精度及各项技术要求齐全、合理;
由图纸得出,该零件的加工精度要求不是很高,加工方法也就根据所生产批量的不同而有所不同,当然,要考虑到经济性时,用普通机床就可以加工出来,要是考虑到时间及中批量方面的话,可以选用数控机床。
在这里我选用数控加工。
其位置精度有三处,基准都是A基准,加工时要考虑它们跟孔一起进行加工;
中心孔的尺寸公差等级为六级公差带,在车床上加工难达到此种精度,需要进行精磨,精磨的时候要以右端面为定位基准,这样才能保证位置度的正确性,关于磨床着方面,就不做介绍了。
磨削时要以右端面为定位基准。
对于内孔槽的加工是:
铣头装在铣床主轴上,传动轴吧主轴的旋转运动通过一对轴交角90度锥齿轮传递给铣刀主轴,立铣刀装在铣刀主轴的锥孔内,利用工作台的纵向运动,带动工件作进给运动,就能进行平键槽的铣削加工。
在本设计中,我选用线切割的方法来加工内孔槽,方便快捷。
对皮带轮的加工工序,可以分为五个
(1)铣削加工,铣削加工出右端面,包括Φ195到Φ60的端面内槽。
如下图:
(通过Cimatron7.0仿真得出)
(2)车削加工,车削内孔,内部及外部齿形轮廓。
(3)铣削加工,铣出左端面,包括Φ195到Φ60的端面内槽。
(4)精磨内孔,磨出Φ40H6的内孔。
(5)利用线切割来切割内部槽。
由于零件的尺寸精度及表面粗糙度要求不是很高,采用通用夹具就可以满足图纸要求了,在此应选用通用夹具。
工件在进行铣削加工之前,必须准确可靠地装夹在机床上,用来确定工件在机床上的位置点、线或面,称为定位基准。
因为点或线一般由具体的表面体现,所以工件上的定位基准又称定位基准面。
装夹是指将工件在机床上或夹具中定位、夹紧的过程,可采用虎钳或加底板抽螺丝等方式装夹。
装夹时首先将标准垫块放在虎钳口,并放入工件,接着轻轻锁紧工件,然后通过百分表或千分表校正工件的水平和垂直位置,然后再锁紧工件,最后再复核一次工件有没有移位。
在确定定位基准与夹紧方案时应注意如下3点:
(1)力求设计、工艺与编程计算的基准统一。
(2)尽量减少装夹次数,尽可能做到在一次装夹定位后就能加工出全部待加工的部位。
(3)夹具要开畅,其定位、夹紧机构不能影响加工中的走刀,避免刀具与夹紧机构碰撞。
遇到此类情况时,可采用用虎钳或加底板抽螺丝的方式装夹。
2.3加工顺序的确定
在分析了零件图样和确定了工序、装夹方式之后,接下来即要确定零件的加工顺序。
制定零件车削加工顺序一般遵循下列原则:
1先粗后精按照粗车----半精车----精车的顺序进行,逐步提高加工精度。
粗车将在较短的时间内将工件表面上的大部分加工余量切掉,一方面提高金属切削率,另一方面满足精车的余量均匀性要求。
若粗车后所留余量的均匀性满足不了精加工的要求时,则要安排半精车,以此为精车做准备。
精车要保证加工精度,按图样尺寸,一刀切出零件轮廓。
2先近后远这里所说的远与近,是按加工部位相对于对到的距离大小而言的。
在一般情况下,离对刀点远的部位后加工,以便缩短刀具移动距离,减少空行程时间。
对于车削而言,先近后远还有利于保持坯件或半成品的刚性,改善其切削条件。
3内外交叉对既有内表面,又有外表面需要加工的零件,安排加工顺序时,应先进行内外表面粗加工,后进行内外表面精加工。
切不可将零件上一部分表面加工完后,再加工其它表面。
在数控加工中,刀具好刀位点相对于工件运动轨迹称为加工路线。
编程时,加工路线的确定原则主要有以下几点:
(1)加工路线应保证被加工零件的精度和表面粗糙度,且效率高;
(2)使数值计算简单,以减少编程工作量;
(3)应使加工路线最短,这样既可减少程序段,又可减少空行程时间。
(4)确定加路线时,还要考虑工件的加工余量和机床、刀具的刚度等情况,确定一次走刀,还是多次走刀来完成所有加工表面,具体综合上面进给线的特点再根据具体零件具体分析确定进给路线的工作重点,主要在于确定粗加工及空行程的进给路线,因精加工切削过程的进给路线基本上都是沿其零件轮廓顺序进行的。
对于铣削加工时,当工件表面无硬皮,机床进给机构无间隙时,应选用顺铣,按照顺铣安排进给路线。
当工件表面有硬皮,机床的进给机构有间隙时,应选用逆铣,按照逆铣安排进给路线。
因为逆铣时,刀齿是从已加工表面切入,不会崩刃。
对该方案,粗加工时用逆铣,精加工时用顺铣。
铣削封闭的内轮廓表面时,刀具不能沿轮廓曲线的法向切入和切出。
此时刀具可以沿一过渡圆弧切入和切出工件轮廓。
由图纸可得出,该零件的尺寸精度及粗糙度都属于IT8∽IT10公差等级,夹具的选择都采用机床通用的夹具就可以达到图纸要求了。
刀具的选择是数控加工工艺设计中的重要内容之一。
刀具选择合理与否不仅影响机床的加工效率,而且还直接影响加工质量。
选择刀具通常要考虑机床的加工能力、工序内容、工件材料等因素。
与传统的车削方法相比,数控车削对刀具的要求更高。
不仅要求精度高、刚度好耐用度高、而且要求尺寸稳定、安装调整方便。
这就要求采用新型优质材料制造数控加工刀具,并优选刀具参数。
车刀和刀片的种类有焊接式与机械夹固式两大类。
(1)焊接式车刀将硬质合金刀片用焊接的方法固定在刀体上称为焊接式车刀。
这种车刀的优点是结构简单,制造方便,刚性较好。
缺点是由于存在焊接应力,是刀具材料的使用性能受到影响,甚至出现裂纹。
另外,刀杆不能重复使用,硬质合金刀片不能充分回收利用,造成刀具材料的浪费。
我们在实习期间就是用的这种刀具,所以对这种刀具还是比较了解的,在本设计中,用到的就是该类刀具。
(2)机夹可转位刀具机械夹固式可转为车刀由刀杆、刀片、刀垫以及夹紧元件组成。
刀片每边都有切削刃,当某切削刃磨损钝化后,只需松开夹紧元件,将刀片转一个位置便可继续使用。
经分析图纸得出加工该零件时要用到外端面90°
车刀内孔刀以及成型刀1下图2.1和成型刀2下图2.2。
铣刀要一把底角半径为3mm长度大于43mm直径为12mm的铣刀。
直径为12mm平底铣刀长度为30mm左右。
Φ40mm的磨刀,精磨内孔。
型刀1
成型刀2
数控车床加工中的切削用量包括:
背吃刀量、主轴转速或切削速度(用于恒线速切削)、进给速度或进给量。
上述切削用量应在机床说明书给定的允许范围内选取。
实习中背吃刀量为1mm主轴转速选择车每分钟600转,进给速度为80mm/min。
数控铣床的刀具选用高速钢钻头,其切削用量包括:
切削速度、进给速度、背吃刀量和侧吃到量,从刀具耐用度出发,切削用量的选择方法是:
先选取背吃刀量或侧吃刀量,其次确定进给速度,最后确定切削速度。
由于图纸上工件表面粗糙度值要求是6.3,则需分粗铣和半精铣两步进行。
粗铣是背吃刀量或侧吃刀量选取同前。
粗铣后留0.6的余量,在半精铣时切除。
进给速度是单位时间内工件与铣刀沿进给方向的相对位移,单位为mm/min。
它与转速n、铣刀齿数Z及每齿进给量f(单位为mm/z)的关系为:
V=fZn
刀具是硬质合金铣刀,查表得出粗铣时f取0.18,精铣时f取0.13
切削速度经查表得取Vc为80m/min。
2.8加工所需工、量具
种类
序号
名称
规格
精度
单位
数量
工具
1
三抓自定心卡盘
个
2
卡盘扳手
副
3
刀架扳手
4
垫刀片
块
若干
量具
游标卡尺
0~250mm
0.02mm
把
内孔千分尺
25mm~50mm
0.01mm
机械加工工艺过程卡
零件名称
皮带轮
材料牌号
45钢
毛坯
棒料
毛坯尺寸
Ф250x120
件数
工序号
工序名称
工序内容
设备
工时
一
下料
Ф250x97内孔直径为35mm。
终准
单件
二
热处理
不需要进行热处理
三
铣右端面
先铣出个基准面,定位
铣床
平上端面,外圆光一刀
铣出右端Φ195mm、Φ60内盲孔
四
车
先夹住铣床铣出的光面,车出外圆基准。
车床
掉头
车外圆尺寸Φ245mm,孔Φ40内孔
用成型刀车出内部齿形轮廓及右端部分外部齿形轮廓
掉头用铜皮包住右端面齿形轮廓夹紧
车出工件长度75mm尺寸,车刀直径小于242.