抽样水准Word文件下载.docx
《抽样水准Word文件下载.docx》由会员分享,可在线阅读,更多相关《抽样水准Word文件下载.docx(13页珍藏版)》请在冰豆网上搜索。
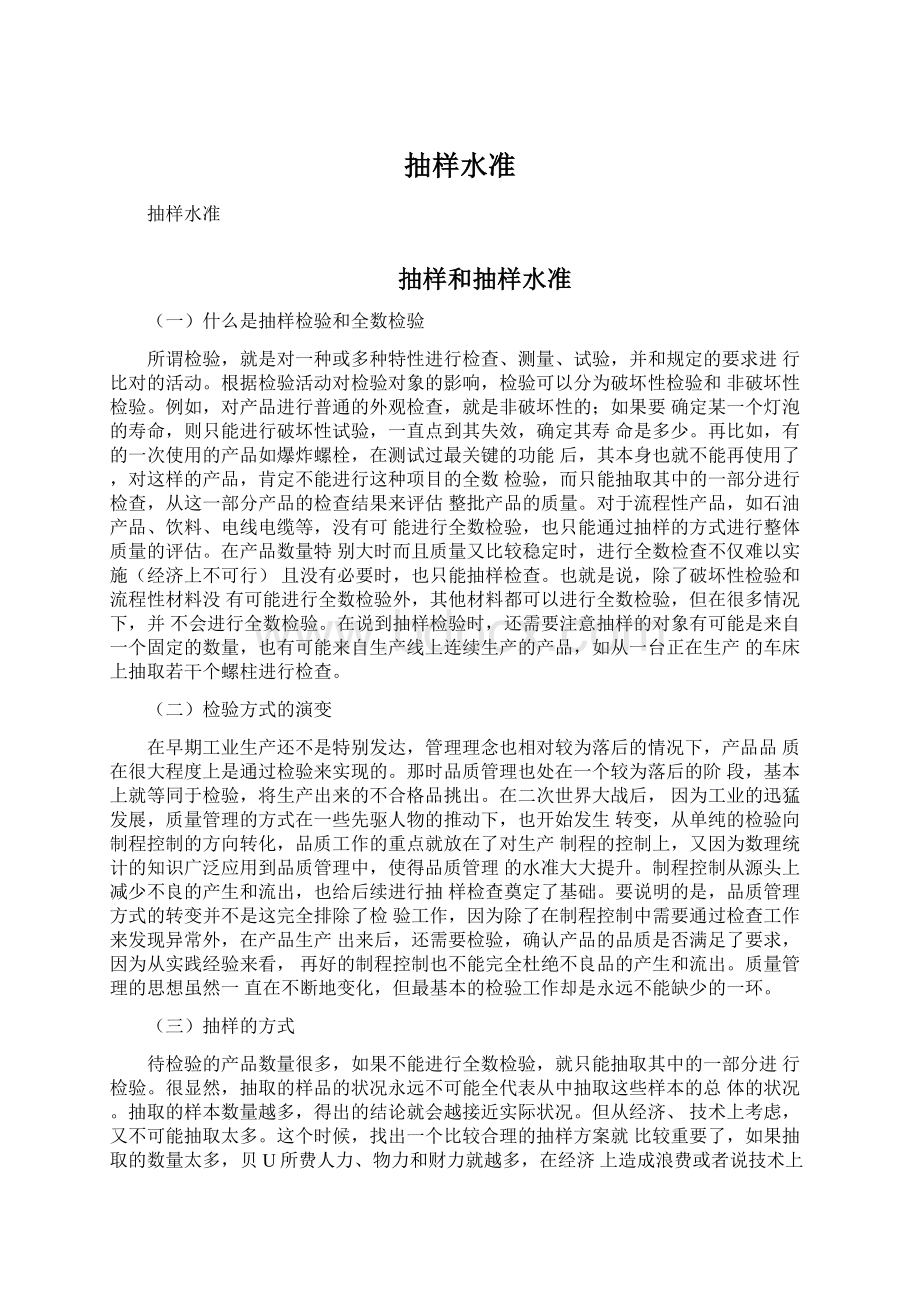
那时品质管理也处在一个较为落后的阶段,基本上就等同于检验,将生产出来的不合格品挑出。
在二次世界大战后,因为工业的迅猛发展,质量管理的方式在一些先驱人物的推动下,也开始发生转变,从单纯的检验向制程控制的方向转化,品质工作的重点就放在了对生产制程的控制上,又因为数理统计的知识广泛应用到品质管理中,使得品质管理的水准大大提升。
制程控制从源头上减少不良的产生和流出,也给后续进行抽样检查奠定了基础。
要说明的是,品质管理方式的转变并不是这完全排除了检验工作,因为除了在制程控制中需要通过检查工作来发现异常外,在产品生产出来后,还需要检验,确认产品的品质是否满足了要求,因为从实践经验来看,再好的制程控制也不能完全杜绝不良品的产生和流出。
质量管理的思想虽然一直在不断地变化,但最基本的检验工作却是永远不能缺少的一环。
(三)抽样的方式
待检验的产品数量很多,如果不能进行全数检验,就只能抽取其中的一部分进行检验。
很显然,抽取的样品的状况永远不可能全代表从中抽取这些样本的总体的状况。
抽取的样本数量越多,得出的结论就会越接近实际状况。
但从经济、技术上考虑,又不可能抽取太多。
这个时候,找出一个比较合理的抽样方案就比较重要了,如果抽取的数量太多,贝U所费人力、物力和财力就越多,在经济上造成浪费或者说技术上也难以完全实现。
如果抽取的数量太少,则有可能发现不了不良,或者据此得出的结果(不良状况)和实际情况相差太大。
最简单的抽样方式就是按照比例进行,比方说5%,如果总数是100个,就抽5个,如果总数是10000个,就抽取500个。
从表面上看,这种抽样方式比较公平,因为对任何批量的待检产品,检验时抽取的比例是固定的。
事实上,这种抽样方式存在着相当大的缺陷,那就是对于同一水准的产品,在批量不一样时,按比例抽检可能会得出不同的结果。
举一个例子说明:
假设某一产品的不良率为1%,按照10%的比例进行抽检,且都按照同样的数量确定是否允收(抽检发现不良数大于1,拒收,小于等于1,接收),则在总体数量分别为100、500、1000、2,000、5,000、10,000时,则它们被接收的概率则是:
总体数量
100
500
1000
2000
5000
10000
不良率
1.0%
总不良数
1
5
10
20
50
抽样数量
200
允收概率(不良
数不大于1)
99.57%
91.06%
73.58%
40.46%
3.98%
0.05%
从上表可以看出,在不良率一定的情况下,如果允收数相同,则在总体数量较多(相应地抽样数量也较多)时,产品的允收概率变化相当大。
也就是说,按照比例进行抽检时,产品的允收机率和抽取样品所在批次的总数有关,且差异相当大。
批量越大,越严;
批量越小,越宽松。
继续分析可以发现,即便对于不同的抽样数,允收数量不固定为某一个值,而是使其和抽样数量之间存在一个比例关系,最终的允收状况也是和总体的数量密切相关。
所以按比例抽样存在先天的缺陷,不是一种合理的抽样方案,现行的国家标准中也禁止使用这种抽样方案。
上面所说的“抽样方案”的意思就是:
从一个或者多个抽取的样品所得到的信息作出某种决定。
其中“决定”的意思就是“接收”或者“拒收”该批产品。
按照规定的抽样方案,“随机地”从一批产品或一个过程中抽取部分个体或者材料进行检验,就是抽样检验。
因为按比例抽样的抽样方案所得出的结果不能准确地反映检验对象的真实品质,所以需要采用其他的抽样方案。
在了解具体的抽样方案前,还有一点需要知道的就是有关“缺陷”的定义以及分类,因为“缺陷”所能造成的后果是不一样的,对产品的影响程度也不相同,如果按照统一标准进行处理,则会产生标准“过严”或者“过松”的问题,在经济上是不合理的,在实际的生产过程中也难以实现。
一般来说,根据对缺陷可能造成的后果的严重性,可将“缺陷”分为三类,一是“致命缺陷”,这样的缺陷可能会对使用、维护、维修的人员的生命安全造成危害、或者会引起重要产品的基本功能丧失;
而是“主要缺陷”,和“致命缺陷”不同,“主要缺陷”会造成产品功能的失效或者严重降低产品的预期功能;
第三种缺陷就是“轻缺陷”,这种“缺
陷”一般不会对产品的功能造成影响,或者影响极为轻微。
需要注意的是,缺陷的严重性
分级还和产品的最终用途、客户要求有关。
所以,什么是缺陷、缺陷的严重程度除了遵循一般的国家标准、国际标准或者行业标准外,最终要的还是要看客户的要求。
如果客户的要求高于一般通行的标准,也是合理的,这个应在签署
合同时由双方共同确认。
在抽样时,根据抽样时是抽取一个样本还是多个样本[一个样本中包含1个或多个样品],分为:
单次抽样、二次抽样、多次抽样、序贯抽样几种。
单次抽样就是一次抽取一个样本;
二次抽样就是根据第一次抽样的结果,再决定是否抽取第二个样本;
而多次抽样则是指可能抽取K个样本,第i个样本(i<
K)的决定是根据前i-1个样本提供的信息来确定的。
而序贯抽样则是逐个(或成组)第抽取个体,但事先并不固定抽取数量的抽样方式。
根据事先规定的规则,直到作出拒收或接收的判定为止。
这种抽样方式一般适用于大型的或者贵重的产品。
最常见的、我们也是用的检验方式是单次抽样方案,一个最简单的一次抽样方案如下图所示:
随机抽取样本大小
为n的一个子样检
验不合格数r
此种计数型抽样检验中,允许接收的最大不良品数或者缺陷数目叫做“合格判定数(接收数)”也就是上边图中的C。
而不允许接收的最小数目叫做“不合格判定数(拒收数)”即上面图中的C+1o一般用Ac(英文Accept的缩写)表示接收数,用Re(英文Reject的缩写)表示拒收数。
因为抽样检验不是全检,所以任何抽样方案都有可能接收质量不好的批次,或者拒收质量合格的批次。
这里隐含的一个前提也就是我们必须面对和承认的一个事实就是,在工业生产中,所产出的产品中不可能达到100%优良,没有任何
瑕疵,只是不良率和不良程度的区分而已。
因此,也是允许不良存在的,只要这种不良在一定的限度之内,这也是采取抽样检验的前提。
如果完全不允许不良品存在,而不论其比例多低,那么就只能采取全数检验了。
下面这个比较极端的例子就可以很好地说明抽检可能存在的放行不良批或者拒收良品批的可能。
假设有1000个产品需要检验,根据某个抽样方案,需抽取20个,且对于某一
类缺陷,其Ac=2,Re=3。
如果这1000个产品中有3个不良品,在抽样20个的时候,正好抽到了3个不良品和17个良品,那么根据规则,这批产品应该判退。
如果这批产品中有18个良品,982个不良品,抽样的时候抽到了18个良品,2个不良品,则根据规则,应该接收这批产品。
也就是一批不良率为0.3%的产品
被拒收了,而不良率为98.2%的产品则被接收了
当然,在仅仅包含3个不良品的1000个产品中,抽取20个,正好抽到了3个不良品的可能性是十分低的(略加计算可以知道,这种状况发生的概率还不到百万分之七),所以这批产品被接收的可能性还是很大,但不能排除被拒收的可能。
同理,不良率为98.2%的那批产品被接收的可能也很低(基本上等于0)。
这两个例子较为极端,但在一定的不良率下,按照某一抽样方案进行抽样,确实会发生拒收合格批或接收不合格批的状况。
因此,为了尽可能减少这两种状况的发生,根据实际的品质水准(不良率),选定一个比较适宜的抽样方案就非常重要。
因为从本质上来说,拒收合格批或者接收不合格批,都是错误,好的抽样方案则能减少这种错误的发生。
在产品100%合格时,无论怎么样抽样,该批产品都会被接收。
但实际上不可能这样,对于存在某一不良率的产品,在给定的抽样方案下,其被接收的概率和拒收的概率都是一定的。
这个概率可以通过概率论的知识很方便地计算出来。
具体的计算这里不详细叙述,可以举两个例子说明一下在同样的抽样方案下,实际不良率对接收概率的影响。
假设有1000个产品,从中抽取50个,Ac=1,Re=2,在其不良率为0.2%、0.3%、0.5%、1%、2%、5%、10%(即这1000个产品中有2个、3个、5个、10、20、50、100个不良品)时接收概率分别是:
99.7548%、99.2879%、97.7752%、91.4692%、73.6043%、27.1691%、3.077%。
接收概率和随不良率上升而下降的趋势从下图上看得十分明显,在不良率上升到一定程度后,接收概率急剧下降。
同样地,如果抽样方案改为抽取50个,Ac=0,Re=1,则在其不良率为0.2%>
0.3%、0.5%、1%、2%、5%、10%(即这1000个产品中有2个、3个、5个、10、20、
50、100个不良品)时接收概率分别是:
90.24%、85.72%、77.34%、59.73.%、
35.49%、7.20%、0.45%。
如下图:
[Ac=0,Re=1]接收概率
率概收接
将这两个图放在一起看,就可以更明显地看出抽样方案不同的情况下,同一品质水平的产品的被接收的概率的差异,如下图。
0.0%2.0%4.0%6.0%8.0%10.0%
从图中可以得出以下几点结论:
(1)在同样的品质水准下,抽样方案越严(接收数小),被拒收的可能就越大;
(2)在同样的抽样方案下,品质越好,被拒收的可能性就越小所以,要保证产品的接收概率,产品的供方就必须控制好产品品质。
(四)抽样曲线
上面的几个图中显示的曲线实际上是该抽样方案下的抽样曲线,对于每一个品质水准(不良率已经确定),在抽样方案确定后,其抽样曲线也就相应的确定了。
也就是说一个抽样曲线中有如下几个参数,一是不良率p,另外几个就是抽样方
案确定的参数,总体数量N、样本数量n,接收数Ac。
进行产品质量检查时,总是首先对产品批不合格品率规定一个值p0来作为判断标准,即当批不合格品率p<
p0时,产品批为合格,而当p>
p0时,产品批为不合格。
因此,理想的抽样方案应当满足:
当p<
p0时,接收概率L(p)=1,当p>
p0时,L(p)=0。
其抽样特线为两段水平线,如下图所示:
LCp)
0pbp%