消失模工艺设计演示教学Word文档下载推荐.docx
《消失模工艺设计演示教学Word文档下载推荐.docx》由会员分享,可在线阅读,更多相关《消失模工艺设计演示教学Word文档下载推荐.docx(7页珍藏版)》请在冰豆网上搜索。
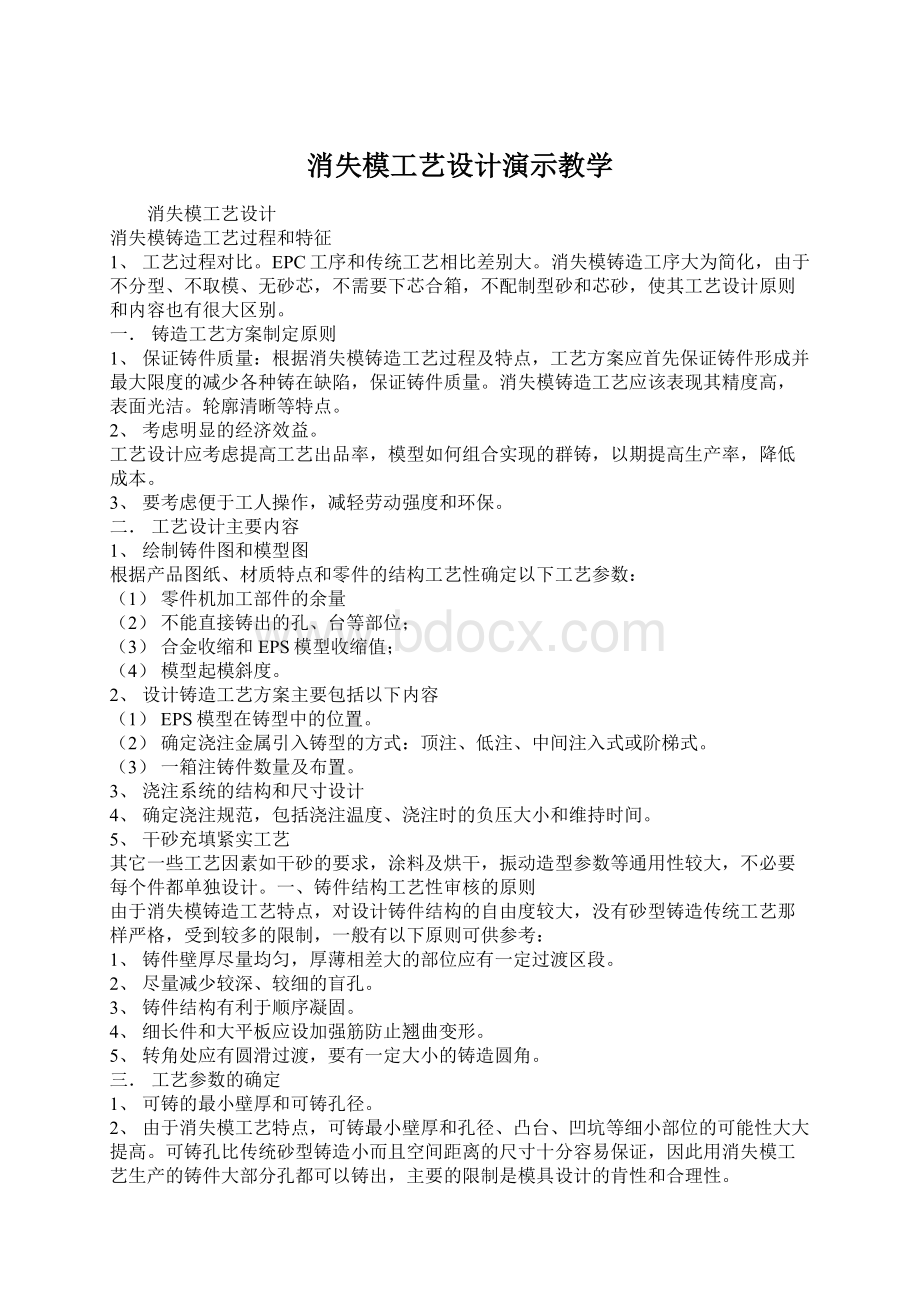
(2)不能直接铸出的孔、台等部位;
(3)合金收缩和EPS模型收缩值;
(4)模型起模斜度。
2、设计铸造工艺方案主要包括以下内容
(1)EPS模型在铸型中的位置。
(2)确定浇注金属引入铸型的方式:
顶注、低注、中间注入式或阶梯式。
(3)一箱注铸件数量及布置。
3、浇注系统的结构和尺寸设计
4、确定浇注规范,包括浇注温度、浇注时的负压大小和维持时间。
5、干砂充填紧实工艺
其它一些工艺因素如干砂的要求,涂料及烘干,振动造型参数等通用性较大,不必要每个件都单独设计。
一、铸件结构工艺性审核的原则
由于消失模铸造工艺特点,对设计铸件结构的自由度较大,没有砂型铸造传统工艺那样严格,受到较多的限制,一般有以下原则可供参考:
1、铸件壁厚尽量均匀,厚薄相差大的部位应有一定过渡区段。
2、尽量减少较深、较细的盲孔。
3、铸件结构有利于顺序凝固。
4、细长件和大平板应设加强筋防止翘曲变形。
5、转角处应有圆滑过渡,要有一定大小的铸造圆角。
三.工艺参数的确定
1、可铸的最小壁厚和可铸孔径。
2、由于消失模工艺特点,可铸最小壁厚和孔径、凸台、凹坑等细小部位的可能性大大提高。
可铸孔比传统砂型铸造小而且空间距离的尺寸十分容易保证,因此用消失模工艺生产的铸件大部分孔都可以铸出,主要的限制是模具设计的肯性和合理性。
可铸的凸台、凹坑及其它细小部分更不受限制,由于模型的图层不影响铸件的轮廓和尺寸,再加之复印性好,所以只要能做出模型,就能铸出铸件。
最小壁厚主要受EPS模式的限制,在生产中模型要求保证断面上至少要容纳下三颗珠粒,这就要求断面厚度大于3毫米,图2表示可成型的最小断面厚度。
实际不同铸造合金在生产中均有一适宜最小壁厚和可铸最小孔径的限制设计中可参考表一1选取:
表一1
铸件合金种类铸铝铸铁铸钢
可铸最小壁厚(mm)2—34—55—6
可铸最小孔径(mm)4—68—1010—12
3、这方面的数据可供参考并有待生产经验的进一步积累。
图2可成型的最小断面厚度铸造收缩率:
消失模铸造,设计模具型腔尺寸时要考虑双重收缩,既金属合金的收缩和模型的收缩。
模型材料收缩,采用EPS时推荐收缩率为0.5—0.7%,采用共聚树脂EPS/EPMMA时推荐为0.2—0.4%。
金属合金的收缩与传统砂型工艺相近,可参考表2所列数据。
表—2
铸件合金铸铝灰铸铁球墨铸铁铸钢
线收缩率(%)自由收缩1.8—2.00.9—1.21.2—1.51.8—2.0
受阻收缩1.6—1.90.6—1.00.8—1.21.6—1.8
设计时模型尺寸(L模型)可按下式计算
L模型=L铸件+K1*L铸件
K1:
可查表—2合金收缩值
设计模具型腔相应尺寸(L模具)=L模型+K2*L模型
K2:
为模型材料收缩值
当铸件尺寸很小时,也可以忽略不计收缩值。
4、机械加工余量:
消失模铸造尺寸精度高,铸件尺寸重复性好,因此加工量比砂型工艺要小,比石蜡精铸略高,
5、拨模斜度:
消失模工艺突出优点是干砂造型,无需起模,下芯、合箱等工序,不需设计拨模斜度,但在制作EPS模型过程中,模具与模型间起模时有一定的摩擦阻力,在模具设计时可考虑0.5°
拨模斜度。
但EPS模型有一定弹力,对于小尺寸也可以不考虑斜度。
四、干砂充填紧实工艺设计
1、干砂技术要求
常用的干砂是石英砂,黑色金属选用粒度在AFS40—60之间,铸铝件可选用细砂AFS50—100。
干砂中含有大量粉尘会降低透气性,浇注是阻碍气体的排出。
沙粒粗大容易出现粘砂,铸件表面粗糙。
圆形或半多角形的干砂可提高透气性。
一般干砂粒度分布要集中于一个筛号上,有助于保持透气性,圆形砂流动性和紧实性最好。
角型砂流动性差,但适当紧实后抗粘砂性能较好,一般不使用复合形干砂,因为它在使用中容易破碎,会产生大量的粉尘。
干砂粒度分布的变化对流动性、透气性、紧实性能会产生重要的变化,因此应在干砂处理了过程中加以控制。
干砂应使用筛砂机去除团块和杂物,减少粉尘,大量生产、车间要使用干砂冷却器控制干砂的温度,应降至50℃以下才能使用,以免模型软化造成变形。
干砂运输应稳定操作,控制粉尘含量,气力输送系统需要大的回转半径,压缩空气应干燥。
灼烧减量是干砂性能一个重要的参数,它反映了模型热解残留物沉积在干砂上的有机物的数量,这种碳氢残余物的积累降低了干砂的流动性,当灼烧减量超过0.25—0.50时更为明显。
为精确测定灼烧减量,被测的干砂式样是单筛砂,因为有机物易于集中在颗粒小的砂粒之上。
2、振动台应用
紧砂需要振动,振动后砂子密度增加10—20%,振动紧实砂子最好在填砂过程中进行,以便使砂子充入模型束内部空腔,保证干砂紧实而模型不发生变形。
振动加速度减小。
频率选择必须避免砂箱或振动台共振。
一般选用振动加速在1—2g范围内效果较好。
振动时间影响铸型密度,时间长密度高,但时间过长效果不明显,反而容易破坏模型和涂料层,影响铸件质量。
在填砂期间振动完成砂子紧实,同时还使的操作时间更合理。
快速填砂和紧实,可获得最高生产率和最小变形。
填砂操作注意事项;
①填砂前应检查砂箱抽气室隔离筛网有无破坏。
②填砂埋箱过程不能损伤模型,不使涂层剥落。
③加砂要均匀速度不能太快模型内外均匀提高砂柱高度,长杆及其它刚度低的模型特别要注意防止弯曲变形。
④对特别难于填砂部位,应辅助工人充填,也可使用自硬砂芯解决局部填砂困难的地方。
⑤干砂温度必须低于
⑥顶部吃砂量,在使用负压条件下不低于50mm
⑦加砂工序需要加强局部抽风罩,防止粉尘污染。
五、浇注系统设计
1、浇注位置的确定、确定浇注位置应考虑一下原则:
①尽量立浇。
斜浇、避免大平面向上浇注,以保证金属有一定上升速度。
②浇注位置应使金属与模型热解速度相同,防止浇注速度慢或出现断流现象,而引起塌箱、对流缺陷。
③模型在砂箱中的位置应有利干砂充填,尽量避免水平向下的盲孔。
④重要加工面处在下面或侧面,顶面最好是非加工面。
⑤浇注位置还应有利于多层铸件的排列,在涂料和干砂充填紧实的过程方便支撑和搬运,使模型某些部位可能加固,防止变形。
六、浇注方式的确定
浇注系统按金属液引入型腔的位置分为顶注、侧注、底注或几种方式综合使用。
1、顶注:
顶注充型所需时间最短,浇速快利于防止塌箱,温度降低少,有利于防止浇不足和冷隔缺陷,工艺出品率高,顺序凝固补缩效果好,可以消除铸铁碳缺陷,但因难控制金属液流。
容易使EPS热解残留物卷入,增碳倾向降低。
由于铝合金浇注时模型分解速度慢,行腔保持充满,可避免塌箱,一般薄壁件多采取顶注。
2、侧注:
液体金属从模型中间引入,一般在铸件最大投影面积部位引入,可缩短内浇道的距离。
生产铸件的采用顶注和侧注,铸件上表面出现碳缺陷的机率低,但卷入铸件内部碳缺陷常常出现。
3、低注:
从低部模型引入金属液,上升平稳充型速度慢,铸件上表面容易出现碳缺陷,尤其厚大件更为严重。
因此应将厚大平面置于垂直方向而非水平方向。
底注工艺最有利于金属充型,金属液前沿的分解产物在界面空隙中排出的同时,又能够支撑干砂型壁。
一般厚大件应采取底注方式。
4、阶梯式注入:
分两层或多层引入金属时采用中空直浇道,象传统空型砂铸工艺一样,底层内浇道引入金属最多,上层内浇道也同时进入金属液。
但是如果采用实心直浇道时,大部分金属从最上层内浇道引入金属,多层内浇道作用减弱。
阶梯浇道引入容易引起冷隔缺陷。
一般在高大铸件时采用。
上述浇注方式,在一定条件下都能生产出合格的铸件。
浇道比例和引入位置
①引入液体金属流,应使充型过程连续不断供应金属不断流,液体金属必须支撑干砂型壁,采用封闭式浇注系统最为有利。
(既内浇道断面最小。
如内浇道:
直浇道=1:
1.2-1.4)
②浇注系统的形式与传统工艺不同,不考虑复杂结构形式(如常用的离心式、阻流式、牛角式、等等,尽量减少浇注系统组成,常常没有横浇道,只有直浇道和内浇道以缩短金属流动的距离。
形状简单,方形、长方形为主。
③直浇道与朱家尖距离(既内浇道长度)应保证充型过程中不因温度升高而使模型变形。
④金属压头,应超过金属EPS界面气体压力,以防呛火。
呛火是液体金属从直浇道反喷出来,中空直浇道和底注有利于避免反喷,(同样适用于做铝件)高的直浇道(压头高)一般容易导致良好的铸件质量和浇注时的安全。
(对EPS/EPMMA共聚树脂模型更为突出)
六、内浇道尺寸大小的设计计算
和传统工艺一样,首先确定内浇道(最小断面尺寸),在按一定比例确定在直浇道和横浇道。
计算方法可以有以下列两种:
①经验法:
以传统砂型工艺为参考查表或经验公式计算后,适当调整,一般增大15—20%即可。
②理论计算方法:
如水力学计算公式,以球铁(包括灰铁)为例
∑F内=G/*t*0.31G;
流经内浇道的液态重量(公斤)(铸件重+浇注系统重)
:
流量系数,可参考传统工艺查表,一般可按阻力偏小来取(如0.3—0.4)
Hp:
压头高度,根据模型在砂箱中位置确定。
t:
关键是浇注时间的选择,快速浇注是EPC工艺最大特点。
可按下式决定t=K1(中小件用公式)
消失模铸造工艺流程:
工艺流程:
1制作泡塑白模,组合浇注系统,气化模表面刷、喷特制耐高温涂料并烘干。
2将特制隔层砂箱置于振动工作台上,填入底砂(干砂)振实,刮平,将烘干的气化模放于底砂上,填满干砂,微振适当时间刮平箱口。
3用塑料薄膜覆盖,放上浇口杯,接真空系统吸真空,干砂紧固成型后,进行浇注,白模气化消失,金属液取代其位置。
4释放真空,待铸件冷凝后翻箱,从松散的干砂中取出铸件。
流程控制:
泡塑珠粒的选用:
消失模铸造专用的泡沫珠粒有三种。
①可发性聚苯乙烯树脂珠粒(简称EPS);
②可发性甲基丙烯酸甲脂与苯乙烯共聚树脂珠粒(简称STMMA);
③可发性聚甲基丙烯酸甲脂树脂珠粒(简称EPMMA)。
常用可发性聚苯乙烯树脂珠粒(EPS),用于铸造有色金属、灰铁及一般钢铸。
珠粒特点:
半透明珠粒,预发泡倍数40~60,粒径为0.18~0.80亳米(6种尺寸),
一般选用的原始珠粒的粒径小于或等于铸件的最小壁厚的1/9~1/10。
模型制作:
有两种情况:
◎由泡塑珠粒制作:
予发泡——熟化——发泡成型——冷却出模
①予发泡
EPS珠粒在加入模具前,要先进行予发泡,以使珠粒膨胀到一定尺寸。
予发泡过程决定了模型的密度、尺寸稳定性及精度,是关键环节之一。
适用于EPS珠粒予发泡的方法有三种:
热水予发泡、蒸汽予发泡和真空予发泡。
真空予发泡的珠粒发泡率高,珠粒干燥,应用较多。
②熟化
经予发泡的EPS珠粒放置在干燥、通风的料仓中一定时间。
以便使珠粒泡孔内外界压力平衡,使珠粒具有弹性和再膨胀能力,除去珠粒表面的水分。
熟化时间在8~48小时。
③发泡成型
将予发泡且熟化的EPS珠粒填充到