柴油机油泵体机械加工工艺规程及夹具设计Word文件下载.docx
《柴油机油泵体机械加工工艺规程及夹具设计Word文件下载.docx》由会员分享,可在线阅读,更多相关《柴油机油泵体机械加工工艺规程及夹具设计Word文件下载.docx(44页珍藏版)》请在冰豆网上搜索。
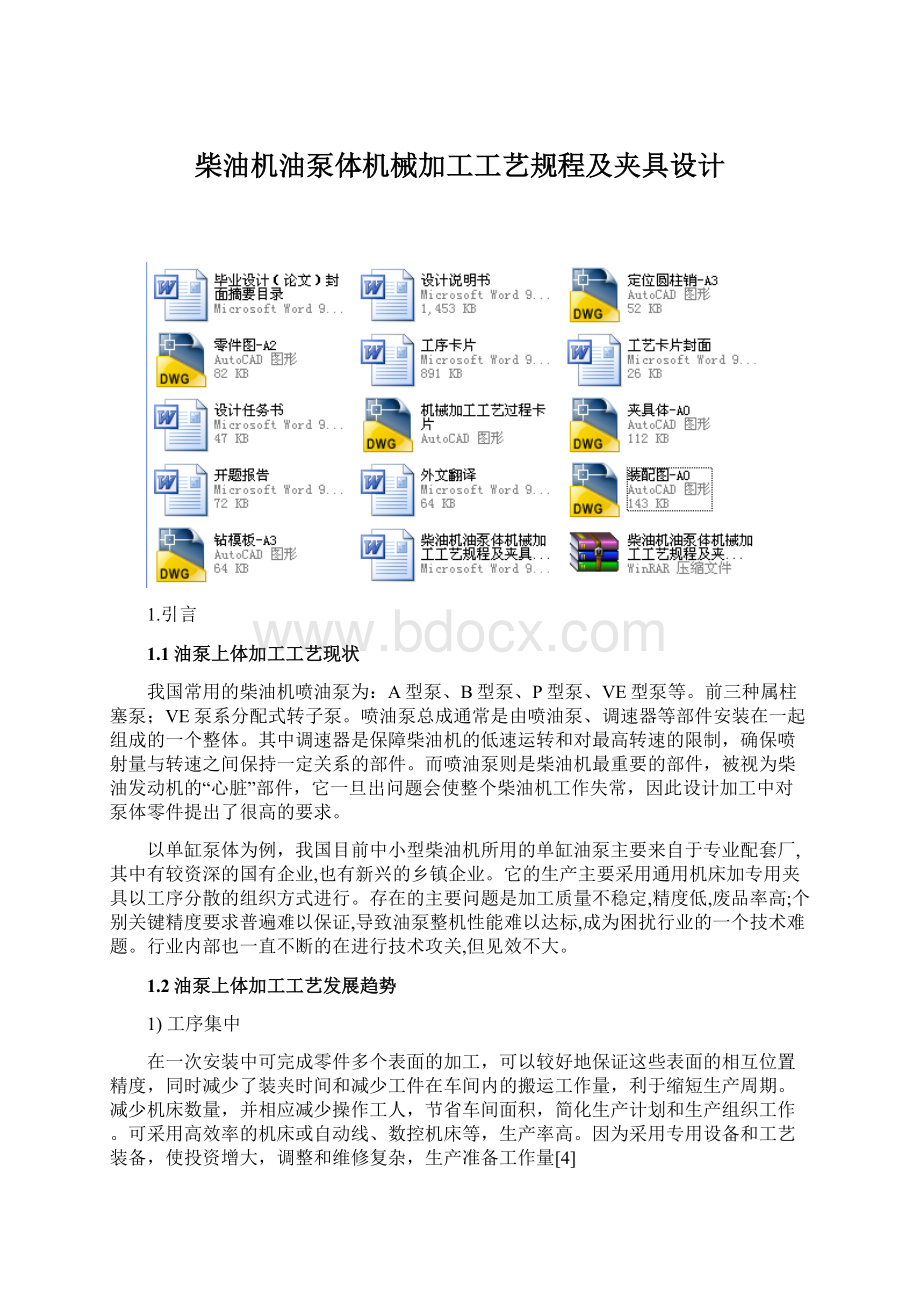
1.2油泵上体加工工艺发展趋势
1)工序集中
在一次安装中可完成零件多个表面的加工,可以较好地保证这些表面的相互位置精度,同时减少了装夹时间和减少工件在车间内的搬运工作量,利于缩短生产周期。
减少机床数量,并相应减少操作工人,节省车间面积,简化生产计划和生产组织工作。
可采用高效率的机床或自动线、数控机床等,生产率高。
因为采用专用设备和工艺装备,使投资增大,调整和维修复杂,生产准备工作量[4]
2)高速加工
高速切削是指刀具切削刃相对与零件表面的切削运动(或移动)速度超过普通切削5~10倍,主要体现在刀具快进、工进及快退三个环节上,是高速加工系统技术中的一个子系统;
对于整条生产自动线而言,高速加工技术表征是以较简捷的工艺流程、较短、较快的生产节拍的生产线进行生产加工。
这就要突破机械加工传统观念,在确保产品质量的前提下,改革原有加工工艺(方式):
或采用一工位多工序、一刀多刃,或以车、铰、铣削替代磨削,或以拉削、搓、挤、滚压加工工艺(方式)替代滚、插、铣削加工等工艺(方式),尽可能地缩短整条生产线的工艺流程;
对于某一产品而言,高速加工技术也意味着企业要以较短的生产周期,完成研发产品的各类信息采集与处理、设计开发、加工制造、市场营销及反馈信息。
这与敏捷制造工程技术理念有相同之处。
[6]
3)自动化生产
自动化技术的成功应用,不但提高了效率,保证了产品质量,还可以代替人去完成危险场合的工作。
对于批量较大的生产自动化,可通过机床自动化改装、应用自动机床、专用组合机床、自动生产线来完成。
小批量生产自动化可通过NC,MC,CAM,FMS,CIM,IMS等来完成。
在末来的自动化技术实施过程中,将更加重视人在自动化系统中的作用。
同时自动化开始面向中小型企业,以经济实用为出发点,满足不断发展的产品多样化和个性化需要。
[3]
由此,现代化技术多采用功率大、功能多的加工中心;
“加工中心”就是多工序自动换刀数控镗铣床;
不仅生产效率高、加工精度高,而且适用范围广,设备利用率高。
箱体大量生产中,还广泛采用由组合机床与输送装置组成的自动线进行加工;
提高生产效率,降低成本,减轻劳动强度,稳定产品质量,降低对工人技术水平的要求
加工中心是指备有刀库,具有自动换刀功能,对工件一次装夹后进行多工序加工的数控机床。
加工中心是高度机电一体化的产品,工件装夹后,数控系统能控制机床按不同工序自动选择、更换刀具,自动对刀、自动改变主轴转速、进给量等,可连续完成钻、镗、铣、铰、攻丝等多种工序。
因而大大减少了工件装夹时间,测量和机床调整等辅助工序时间,对加工形状比较复杂,精度要求较高,品种更换频繁的零件具有良好的经济效果。
加工中心通常以主轴与工作台相对位置分类,分为卧式、立式和万能加工中心。
(1)卧式加工中心:
是指主轴轴线与工作台平行设置的加工中心,主要适用于加工箱体类零件。
(2)立式加工中心:
是指主轴轴线与工作台垂直设置的加工中心,主要适用于加工板类、盘类、模具及小型壳体类复杂零件。
(3)万能加工中心(又称多轴联动型加工中心):
是指通过加工主轴轴线与工作台回转轴线的角度可控制联动变化,完成复杂空间曲面加工的加工中心。
适用于具有复杂空间曲面的叶轮转子、模具、刃具等工件的加工。
[11]
2.方案论证
2.1分析油泵上体的结构特点和精度要求
2.1.1结构特点
我们认为动力源由凸轮轴驱动端传入后,通过挺柱体作用于两对偶件,向外供油,这直接关系着喷油泵总成的供油特性、速度特性及柴油机的动力特性:
与调速器相连的拉杆运动的可靠性和灵活性又直接影响喷油泵总成的调速特性乃至柴油机的调速性能。
因此,轴承安装孔与凸轮轴、挺柱体与导程孔、拉杆孔与拉杆等三对运动副直接影喷油泵总成的三大特性。
同时,燃油的内漏、外漏问题占油泵故障的50%之多,因此法兰套安装孔及密封孔与法兰套之间的静配合直接影响着油泵故障率。
因此,产品设计对轴承安装孔、导程孔、法兰套安装孔及密封孔、拉杆孔以及定位支撑销孔等提出严格的要求
油泵属于典型的箱体类零件,它用于将机器和部件中的轴、套。
齿轮等有关零件连接成一个整体,并使之保持正确的相互位置,以传递转矩或改变转速来实现规定的运动。
它的结构特点是结构复杂,壁薄且不均匀,加工部位多,加工难度大。
对油泵上体的加工主要集中在对一些孔的加工,基本孔可分为通孔、阶梯孔、盲孔、交叉孔等,通孔工艺性最好;
深孔、阶梯孔、相贯通的交叉孔工艺性较差;
盲孔工艺性最差,所以在设计上也尽量避免。
2.1.2主要技术要求
平面精度
零件底面B为装配面,对其表面质量提出了较高要求,粗糙度为Ra1.6,平面度为0.05mm。
另外还有考虑到下一步工序的顺利进行,对一些表面垂直度也提出了相关要求,例如在进行通气斜孔加工前预先铣出的一个平面要求相对孔轴线的垂直度公差为0.1mm。
还有螺塞孔2-M12,套筒定们孔2-M6处的平面也分别提出了相对孔轴线的垂直度公差为0.1mm。
孔径精度
孔径的尺寸误差和形位公差会造成偶件配合不良,因此,对孔的精度要求较高。
从零件图可知,泵体主要有以下几种典型孔的加工:
定位通孔的加工
零件对连接定位孔相对底面B的垂直度要求为Φ0.2/100。
由于L/D>
5,称为深孔,工艺性性并不太好,所以实际工艺上对该加工刀具进行了特殊配置,以保证产品要求。
其中2-Φ8.5自身的尺寸及形状误差在图纸上并没有明确标出,而2-Φ8.2孔表面粗糙度要求为R6.3,两孔孔径相差很小,可以在钻床上先钻出一个通孔,然后对2-Φ8.5进行扩孔,对2-Φ8.2进行粗铰。
阶梯孔的加工
对套筒安装阶梯孔的各级孔都提出了相应的尺寸精度(H6-10级)及表面粗糙度(Ra1.6)要求。
对阶梯孔可以在车床上利用专用夹具及相应刀具进行镗孔得到。
套筒定位交叉孔的加工
交叉孔的工艺性较差,但此零件对其要求并不算太高。
2-M6,通气斜孔是侧向交叉孔,并且都要加工出螺纹,尺寸公差等级为6-7级。
在未加工的铸毛坯斜面的工件上钻孔,钻头产生的偏移较大,且在钻入时单面的侧向负荷易使钻头产生折断,宜采用保护钻头的特殊钻套,并先铣削一垂直于钻孔轴线的小平面,结合本零件的实际特殊性,我们还需要设计出专用钻模(包括相关的定位、夹紧元件)。
另外,零件图对各孔之间的相对位置尺寸误差也提出了要求。
整理成表格后,形式如下:
为了保证连杆的装配精度和工作要求,主要技术要求见表1-1
技术要求项目
具体要求或数值
满足的主要性能
机体顶面粗糙度为Ra6.3,底面B的平面度为0.05
正面两套筒定位交叉孔凹台端面相对孔轴线的垂直度为0.1
螺塞孔凹台端面相对孔轴线的垂直度为0.1
通气斜孔凹台端面相对轴线的垂直度为0.1
孔与平面的形位精度
两细长连接通孔相对底面B的垂直度为
套筒安装阶梯通孔相对底面B的垂直度为
孔与孔的形位精度
相对细长连接通孔的轴心线距离公差为±
0.1
套筒定位交叉孔相对套筒安装通孔的位置度为25:
0.2
套筒安装盛油槽18相对孔14的同轴度为0.1
通气斜孔轴线相对套筒安装孔的倾斜度为0.1
详见:
图2-1零件图
图2-1零件图
2.2加工工艺路线的确定
拟订工艺路线,是设计整个工艺规程的主线,这项工作与确定工艺基准、毛坯、工序、尺寸等穿插进行,因而工作量较大。
应根据有关原则,在充分调查研究的基础上,从本厂、本车间人力、物力、技术水平出发,并结合引进新技术的可能性加以考虑。
我们先研究一下泵体零件图
2.2.1确定生产纲领
根据市场需求及企业自身的市场定位决定产品生产为中批量
2.2.2确定泵体毛坯的制造形式
材料选HT200;
因为灰铸铁成本低,耐磨性、可铸性、可切削性和阻尼特性好;
从零件设计图纸可以看出,零件孔径不大,如果直接浇铸出来很容易出现诸如砂眼‘缩松’裂纹等缺陷,所以实际工艺上毛坯均为实心体,毛坯余量视生产批量和铸造方法等而定;
毛坯在浇铸后要进行退火热处理,以改善切削性能,并消除铸造内应力。
铸造件的成本相对低廉,而且零件毛坯体积不大,形状也并不复杂,根据现有厂里的生产设备和技术水平,选择采用金属型浇铸而成,这种铸造方法可以铸出形状不太复杂的铸件,铸件尺寸精度可达0.1mm至0.5mm,表面粗糙度Ra可达12.5至6.3,铸件力学性能较好,从而可以减少加工余量、节约材料,降低消耗。
2.2.3毛坯形状及铸造尺寸的确定
由于泵体各孔直径不大(≤30mm),毛坯均为实心体,倒圆角处加工要求不高,而且考虑到曲面加工的困难,故倒圆角直接铸造出来。
所以毛坯整体上是一个立方体。
要确定毛坯铸造尺寸,首先得先确定铸件的机械加工加工余量
铸件的机械加工余量的确定
铸件的机械加工余量是为保证铸件加工表面尺寸和零件精度,在铸件工艺设计时预先增加的并在机械加工时切去的金属层厚度。
铸件图上给定的铸件尺寸称为铸件基本尺寸,它包括机械加工余量。
铸件的尺寸公差是指铸件基本尺寸的最大极限尺寸与最小极限尺寸的差值范围。
铸件表面进行单侧加工,铸件机械加工余量(MA)和铸件尺寸公差(CT)的分配。
铸件机械加工余量等级和选用
因为泵体是典型的箱体零件,主要是孔的加工,而毛坯铸件的表面加工并不复杂,所以可采用简单实用的查表确定铸件毛坯的尺寸。
对于成批和大量生产的铸件,机械加工余量(MA)的等级可按机械加工余量表)选取
在保证毛坯成形质量要求的前提下,为了适当降低毛坯铸造对工人技术的要求,我们选取铸件尺寸公差等级为CT10级,机械加工余量等级为G级。
当已确定铸件的尺寸公差等级后,对砂型铸造的铸件,其顶面(相对浇注位置而言)的加工余量等级要比底、侧面的加工余量等级降低一级选用。
当铸件尺寸公差等级和加工余量等级确定后,其机械加工余量数值应按有加工要求的表面上最大基本尺寸和该表面距它的加工基准间尺寸二者中较大的尺寸所在范围选取。
从而得知:
泵体毛坯顶面机械加工余量为4.0mm,底面及侧面机械加工余量为3.5mm。
所以最终不难确定,毛坯理论上尺寸为长×
宽×
高:
81mm×
53.5mm×
49mm。
取整确定为:
80mm×
50mm×
50mm
毛坯图见下图2-4
图2-4毛坯图
2.2.4定位基准的选择
通过进一步分析,我们选择毛坯底平面B作为加工精基准,采用一连接孔Φ8.5、一套筒安装孔Φ14两孔作为两定位孔,与精基准同时加工而成。
同时,工艺上规定毛坯顶面作为粗基准,采用精基准定位加工而成。
这样采用一面两销进行定位,为了防止过定位,应采用一圆柱销一菱形销的定位方式。
2.2.5确定合理的夹紧方式
油泵上体毛坯刚性良好,而且要钻的孔不大,我们不需要采用太过复杂的夹紧方式,通过研究,可以以简单的螺纹旋紧机构对工件进行夹紧,夹紧力作用于机体顶面,作用方向垂直机体顶面并指向底面。
2.2.6工艺路线的比较分析
由上述技术条件的分析可知,油泵上体的尺寸精度、形状精度以及位置精度的要求都较高,在对油泵的需