数控编程及数控仿真技术现状发展趋势_Word文件下载.doc
《数控编程及数控仿真技术现状发展趋势_Word文件下载.doc》由会员分享,可在线阅读,更多相关《数控编程及数控仿真技术现状发展趋势_Word文件下载.doc(11页珍藏版)》请在冰豆网上搜索。
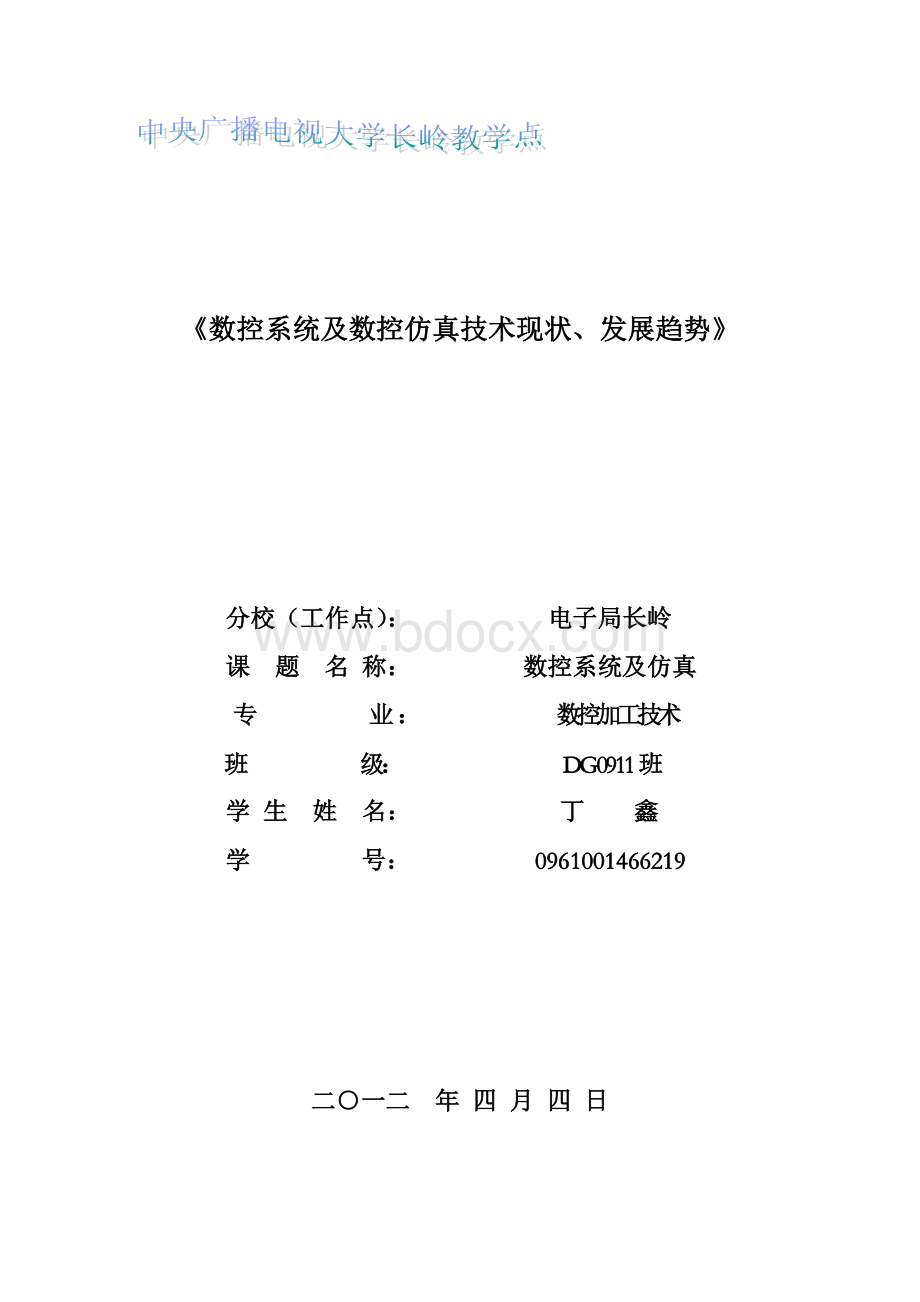
丁鑫
学号:
0961001466219
二○一二年四月四日
数控系统及数控仿真技术现状、发展趋势
摘要:
数控系统是利用数字信号对执行机构的位移、速度、加速度和动作顺序实现自动控制的一种控制系统,数控系统自1952年问世以来,随着科学技术的不断发展,已经经过了六次换代,早起的数控系统仅用于数控机床,自从出现了计算机数控系统后,数控系统不仅普遍用于数控机床,而且在电火花线切割、电火花成型、高压水射流切割、激光切割、快速原型制造和机器人等自动化控制领域也获得了越来越广泛的运用。
现代制造技术正朝着高效率、高速度、高精度、高集成和高智能方向发展,加工智能化和虚拟制造已成为现代制造业中最重要的组成部分和发展方向,并成为提高产品国际竞争力的关键技术。
而机械加工过程仿真在虚拟制造中占有重要地位,它通过对机床—工件—刀具构成的工艺系统中的各种加工信息的有效预测与优化,为实际加工过程的智能化实现创造了有利条件,同时它也是研究加工过程的重要手段。
本文主要概述了数控仿真技术的发展过程以及国内外运用这一新技术的综合概况.
关键词:
数控系统;
数控技术、数控仿真、虚拟、制造
国内外数控系统发展概况
随着计算机技术的高速发展,传统的制造业开始了根本性的变革,各工业发达国家投入巨资,对现在制造业进行研究和开发,提出了全新的制造模式。
在现代制造系统中,数控技术是关键技术,它集微电子,计算机,信息处理,自动检测,自动控制等高新技术于一体,具有高精度,高效率,柔性自动化等特点,对制造业发生根本性的变革,由专用型封闭式开环控制模式向通用型开放式实时动态全闭环控制模式发展。
在集成化基础上,数控技术实现了超薄性,超小型化;
在智能化基础上,综合了计算机,多媒体,模糊控制,神经网络等多学科技术,数控技术实现了高速、高精、高效控制,加工过程中可以制动修正、调节与补偿各项参数,实现了在线诊断和智能化故障处理。
长期以来,我国数控系统为传统的封闭式体系结构,CNC只能作为非智能的机床运动控制器。
加工过程变量根据经验以固定参数形式事先设定,加工程序在实际加工前用手工方式或通过CAD/CAM及自动编程系统进行编制。
CAD/CAM和CNC之间没有反馈控制环节,整个制造过程中CNC只是一个封闭式的开环执行机构。
在复杂环境及多变的条件下,加工过程中的刀具组合、工件材料、主轴转速、进给速率、刀具轨迹、切削深度、步长、加工余量等加工参数,无法在现场环境下根据外部干扰和随机和实时动态调整,更无法通过反馈控制环节随机修正CAD/CAM中的设定量,因而影响CNC的工作效率和产品的加工质量。
由此可见,传统CNC系统的这种固定程序控制模式和封闭式体系结构,限制了CNC向多变量智能化发展,已不适应日益复杂的制造过程,因此,大力发展以数控技术为核心的先进制造技术已成为我们国家加速经济发展、提高综合国力和国家地位的重要途径。
数控系统发展趋势
从1952年美国麻省理工学院研制出第一台试验性数控系统,到现在已走过了半个多世纪的历程。
随着电子技术和数控技术的飞速发展,当今的数控系统功能已经非常强大,与此同时加工技术以及一些其他相关技术的发展对数控系统的发展和进步提出了新的要求。
数控编程是目前CAD/CAPP/CAM系统中最能明显发挥效益的环节之一,其在实现设计加工自动化、提高加工精度和加工质量、缩短产品研制周期等方面发挥着重要作用。
在诸如航空工业、汽车工业等领域有着大量的应用。
由于生产实际的强烈需求,国内外都对数控编程技术进行了广泛的研究,并取得了丰硕成果。
下面就对数控编程及其发展作一些介绍。
<
1>
数控编程的基本概念
数控编程是从零件图纸到获得数控加工程序的全过程。
它的主要任务是计算加工走刀中的刀位点(cutterlocationpoint简称CL点)。
刀位点一般取为刀具轴线与刀具表面的交点,多轴加工中还要给出刀轴矢量。
2>
数控编程技术的发展概况
为了解决数控加工中的程序编制问题,50年代,MIT设计了一种专门用于机械零件数控加工程序编制的语言,称为APT(AutomaticallyProgrammedTool)。
其后,APT几经发展,形成了诸如APTII、APTIII(立体切削用)、APT(算法改进,增加多坐标曲面加工编程功能)、APTAC(Advancedcontouring)(增加切削数据库管理系统)和APT/SS(SculpturedSurface)(增加雕塑曲面加工编程功能)等先进版。
采用APT语言编制数控程序具有程序简炼,走刀控制灵活等优点,使数控加工编程从面向机床指令的“汇编语言”级,上升到面向几何元素.APT仍有许多不便之处:
采用语言定义零件几何形状,难以描述复杂的几何形状,缺乏几何直观性;
缺少对零件形状、刀具运动轨迹的直观图形显示和刀具轨迹的验证手段;
难以和CAD数据库和CAPP系统有效连接;
不容易作到高度的自动化,集成化。
针对APT语言的缺点,1978年,法国达索飞机公司开始开发集三维设计、分析、NC加工一体化的系统,称为为CATIA。
随后很快出现了象EUCLID,UGII,INTERGRAPH,Pro/Engineering,MasterCAM及NPU/GNCP等系统,这些系统都有效的解决了几何造型、零件几何形状的显示,交互设计、修改及刀具轨迹生成,走刀过程的仿真显示、验证等问题,推动了CAD和CAM向一体化方向发展。
到了80年代,在CAD/CAM一体化概念的基础上,逐步形成了计算机集成制造系统(CIMS)及并行工程(CE)的概念。
目前,为了适应CIMS及CE发展的需要,数控编程系统正向集成化和智能化方向发展。
在集成化方面,以开发符合STEP(StandardfortheExchangeofProductModelData)标准的参数化特征造型系统为主,目前已进行了大量卓有成效的工作,是国内外开发的热点;
在智能化方面,工作刚刚开始,还有待我们去努力。
趋势之一:
数控系统向开放式体系结构发展
20世纪90年代以来,由于计算机技术的飞速发展,推动数控技术更快的更新换代。
世界上许多数控系统生产厂家利用PC机丰富的软、硬件资源开发开放式体系结构的新一代数控系统。
开放式体系结构使数控系统有更好的通用性,柔性,适应性,可扩展性,并可以较容易的实现智能化,网络化。
近几年许多国家纷纷研究开发这种系统,如美国科学制造中心(NCMS)与空军共同领导的“下一代工作站/机床控制器体系结构”NGC,欧共体的“自动化系统中开放式体系结构”OSACA,日本的OSEC计划等。
开放式体系结构可以大量采用通用微机技术,使编程、操作以及技术升级和更新变得简单快捷。
开放式体系结构的新一代数控系统,其硬件,软件总线规范都是对外开放的,数控系统制造商和用户可以根据这些开放的资源进行的系统集成,同时它也为用户根据实际需要灵活配置数控系统带来极大的方便,促进了数控系统多档次,多品种的开发和广泛应用,开发生产周期大大缩短。
同时,这种数控系统可随CPU的升级而升级,而结构可以保持不变。
趋势之二:
数控系统方向软数控方向发展
现在,实际用于工业现场的数控系统主要有一下四种类型,分别代表了数控技术的不同发展阶段,对不同的数控系统进行分析后发现,数控系统不但从封闭式体系结构向开放式体系结构发展,而且正在从硬数控向软数控方向发展的趋势,传统的数控系统,如FANUC0系统,MITSUBISHIM50系统,SINUMERIK810/M/T/G系统等。
这是一种专用的封闭体系结构的数控系统。
目前,这种系统还是占据了制造业的大部分市场。
数控机床是数字控制机床(NumericallyControlledMachineTool)的简称,亦称NC机床,是为了满足单件、小批、多品种自动化生产的需要而研制的一种灵活的、通用的能够适应产品频繁变化的柔性自动化机床,具有适应性强、加工精度高、加工质量稳定和生产效率高的优点。
它综合应用了电子计算机、自动控制、伺服驱动、精密测量和新型机械结构等多方面的技术成果。
随着机床数控技术的迅速发展,数控机床在机械制造业中的地位越来越重要。
第一台数控机床是适应航空工业制造复杂零件的需要而产生的。
1948年,美国帕森斯公司(ParsonsCo)在研制加工直升机叶片轮廓用检查样板的加工机床时,提出了数控机床的初始设想。
1949年,帕森斯公司正式接受委托,与麻省理工学院伺服机构试验室合作,开始从事数控机床的研制工作。
经过三年时间的研究,于1952年试制成功世界上第一台数控机床样机,这是一台直线插补三坐标立式铣床,其数控系统全部采用电子管,也称第一代数控系统。
经过三年的改进和自动程序编制的研究,于1955年进入实用阶段,一直到20世纪50年代末,由于晶体管的应用,数控系统提高了可靠性且价格开始下降,一些民用工业开始发展数控机床,其中多数是钻床、冲床等点位控制的机床。
数控技术不仅在机床上得到实际应用,而且逐步推广到焊接机、火焰切割机等,使数控技术不断地扩展应用范围。
我国的数控机床是从1958年开始研制的,经历了40多年的发展历程,目前数控技术已在车、铣、钻、镗、磨、齿轮加工、电加工等领域全面展开,数控加工中心也相继研制成功。
数控仿真技术发展概况
数控技术是先进制造技术的核心,世界各国制造业广泛采用数控技术,以提高制造能力、适应市场能力和竞争能力。
虚拟制造技术就是根据企业的竞争需求,在强调柔性和快速的前提下,于20世纪80年代提出的,并随着计算机,特别是信息技术产业的发展,在90年代得到人们的极大重视,获得迅速的发展。
在不长的时间里,已成为企业界、学术界的研究热点之一,是当今国际上科技领域的前沿课题,目前在美、英、日、西欧诸国已经形成了相当规模的新兴产业部门,商品化软件已趋于成熟,应用比较广泛。
随着我国加入世贸组织,综合国力进一步增强,我国经济全面与国际接轨,并正在成为全球制造业中心,进入了一个空前蓬勃发展的新时期,随着机械零件制造复杂程度的提高,对数控代码正确性验证的需求越来越迫切,数控仿真系统利用计算机图形显示技术模拟实际加工过程,是验证数控加工程序正确性的有力工具之一,这必然对掌握现代化制造技术的人才、特别对一线数控技术工人形成了巨大的需求。
[1]
计算机仿真的概念及应用
从工程的角度来看,仿真就是通过对系统模型的实验去研究一个已有的或设计中的系统。
分析复杂的动态对象,仿真是一种有效的方法,可以减少风险,缩短设计和制造的周期,并节约投资。
计算机仿真就是借助计算机,利用系统模型对实际系统进行实验研究的过程。
它随着计算机技术的发展而迅速地发展,在仿真中占有越来越重要的地位。
计算机仿真的过程可通过图1所示的要素间的三个基本活动来描述:
建模活动是通过对实际系统的观测或检测,在忽略次要因素及不可检测变量的基础上,用物理或数学的方法进行描述,从而获得实际系统的简化近似模型。
这里的模型同实际系统的功能与参数之间应具有相似性和对应性。
仿真模型是对系统的数学模型(简化模型)进行一定的算法处理,使其成为合适的形式(如将数值积分变为迭代