数控车床自动回转刀架机电系统设计说明Word文档格式.docx
《数控车床自动回转刀架机电系统设计说明Word文档格式.docx》由会员分享,可在线阅读,更多相关《数控车床自动回转刀架机电系统设计说明Word文档格式.docx(18页珍藏版)》请在冰豆网上搜索。
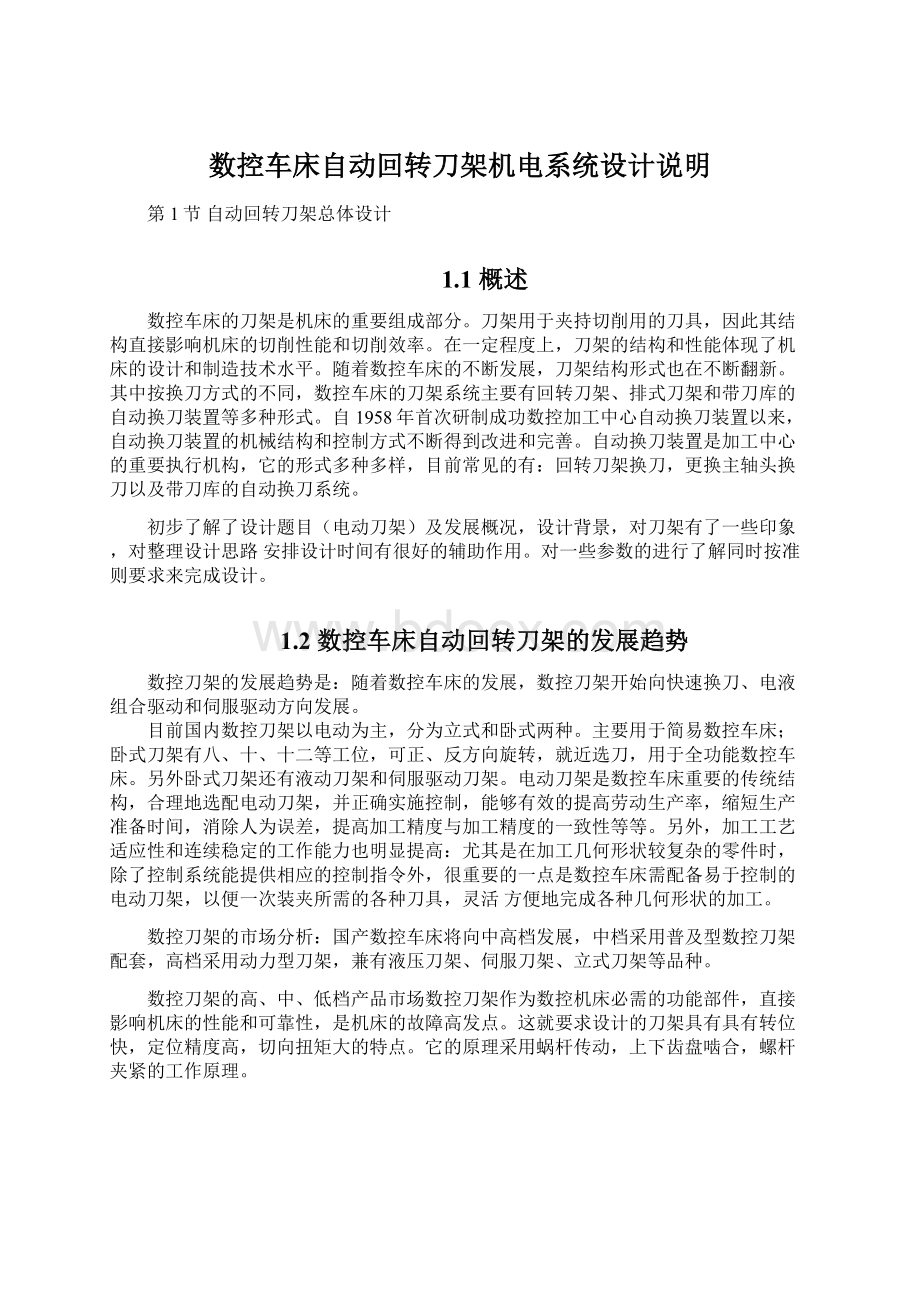
另外,加工工艺适应性和连续稳定的工作能力也明显提高:
尤其是在加工几何形状较复杂的零件时,除了控制系统能提供相应的控制指令外,很重要的一点是数控车床需配备易于控制的电动刀架,以便一次装夹所需的各种刀具,灵活方便地完成各种几何形状的加工。
数控刀架的市场分析:
国产数控车床将向中高档发展,中档采用普及型数控刀架配套,高档采用动力型刀架,兼有液压刀架、伺服刀架、立式刀架等品种。
数控刀架的高、中、低档产品市场数控刀架作为数控机床必需的功能部件,直接影响机床的性能和可靠性,是机床的故障高发点。
这就要求设计的刀架具有具有转位快,定位精度高,切向扭矩大的特点。
它的原理采用蜗杆传动,上下齿盘啮合,螺杆夹紧的工作原理。
1.3自动回转刀架的工作原理
回转刀架的工作原理为机械螺母升降转位式。
工作过程可分为刀架抬起、刀架转位、刀架定位并压紧等几个步骤。
图1.1为螺旋升降式四方刀架,其工作过程如下:
1刀架抬起当数控系统发出换刀指令后,通过接口电路使电机正转,经传动装置、驱动蜗杆蜗轮机构。
蜗轮带动丝杆螺母机构逆时针旋转,此时由于齿盘处于啮合状态,在丝杆螺母机构转动时,使上刀架体产生向上的轴向力将齿盘松开并抬起,直至两定位齿盘脱离啮合状态,从而带动上刀架和齿盘产生“上抬”动作。
2刀架转位当圆套逆时针转过150°
时,齿盘完全脱开,此时销钉准确进入圆套中的凹槽中,带动刀架体转位。
3刀架定位当上刀架转到需要到位后(旋转90°
、180°
或270°
),数控装置发出的换刀指令使霍尔开关中的某一个选通,当磁性板与被选通的霍尔开关对齐后,霍尔开关反馈信号使电机反转,插销在弹簧力作用下进入反靠盘地槽中进行粗定位,上刀架体停止转动,电机继续反转,使其在该位置落下,通过螺母丝杆机构使上刀架移到齿盘重新啮合,实现精确定位。
刀架压紧刀架精确定位后,电机及许反转,夹紧刀架,当两齿盘增加到一定夹紧力时,电机由数控装置停止反转,防止电机不停反转而过载毁坏,从而完成一次换刀过程。
图1.1螺旋升降式四方刀架
第2节主要传动部件的设计计算
2.1蜗杆副的设计计算
自动回转刀架的动力源是三相异步电动机,其中蜗杆与电动机直联,刀架转位时蜗轮与上刀体直联。
已知电动机额定功率P1=90W,额定转速n1=1440r/min,上刀体设计转速n2=30r/min,则蜗杆副的传动比i===48。
刀架从转位到锁紧时,需要蜗杆反向,工作载荷不均匀,起动时冲击较大,今要求蜗杆副的使用寿命Lh=10000h。
(1)蜗杆的选型GB/T10085--1988推荐采用渐开线蜗杆(ZI蜗杆)和锥面包络蜗杆(ZK蜗杆)。
本设计采用结构简单、制造方便的渐开线型圆柱蜗杆(ZI型)。
(2)蜗杆副的材料刀架中的蜗杆副传递的功率不大,但蜗杆转速较高,因此,蜗杆的材料选用45钢,其螺旋齿面要求淬火,硬度为45~55HRC,以提高表面耐磨性;
蜗轮的转速较低,其材料主要考虑耐磨性,选用铸锡磷青铜ZCuSnl0P1,采用金属模铸造。
(3)按齿面接触疲劳强度进行设计刀架中的蜗杆副采用闭式传动,多因齿面胶合或点蚀而失效。
因此,在进行承载能力计算时,先按齿面接触疲劳强度进行设计,再按齿根弯曲疲劳强度进行校核。
按蜗轮接触疲劳强度条件设计计算的公式为:
1)确定作用在蜗轮上的转矩T2设蜗杆头数Z1=1,蜗杆副的传动效率取η=0.8。
由电动机的额定功率P1=90W,可以算得蜗轮传递的功率P2=P1η,再由蜗轮的转速n2=30r/min求得作用在蜗轮上的转矩:
2)确定载荷系数K载荷系数K=KAKBKV,。
其中KA为使用系数,由表6-3查得,由于工作载荷不均匀,起动时冲击较大,因此取KA=1.15;
KB为齿向载荷分布系数,因工作载荷在起动和停止时有变化,故取KB=1.15;
Kv为动载系数,由于转速不高、冲击不大,可取Kv=1.05。
则载荷系数:
K=KAKBKV=1.15×
1.15×
1.05≈1.39
3)确定弹性影响系数ZE。
铸锡磷青铜蜗轮与钢蜗杆相配时,从有关手册查得弹性影响系数。
4)确定接触系数先假设蜗杆分度圆直径d1和传动中心距a的比值,从而可查出=2.9
5)确定许用接触应力[σH]根据蜗轮材料为铸锡磷青铜ZCuSnl0P1、金属模铸造、蜗杆螺旋齿面硬度大于45HRC,查表可得蜗轮的基本许用应力[σH]′=268MPa。
已知蜗杆为单头,蜗轮每转一转时每个轮齿啮合的次数j=1;
蜗轮转速n1=30r/min;
蜗杆副的使用寿命Lh=10000h。
则应力循环次数:
N=6Qjn2Lh=60×
1×
30x10000=1.8×
107寿命系数:
许用接触应力:
[σH]=KHN[σH]′=0.929×
268Mpa≈249Mpa
6)计算中心距
查表得,取中心距,已知蜗杆头数=1,m=1.25mm,蜗杆分度圆直径d1=22.4mm。
这时0.448,从而可查得接触系数,因为,因此以上计算结果可用。
蜗杆和蜗轮主要几何尺寸计算
(1)蜗杆
分度圆直径:
d1=28mm
直径系数:
q=17.92,
蜗杆头数:
Z1=1
分度圆导程角:
γ=3°
11′38″
蜗杆轴向齿距:
PA==3.94mm;
蜗杆齿顶圆直径:
蜗杆齿根圆直径:
蜗杆轴向齿厚:
=2.512mm
蜗杆轴向齿距:
(2)蜗轮
蜗轮齿数:
Z2=45
变位系数Χ=0
验算传动比:
i=/=45/1=45
蜗轮分度圆直径:
d2=mz2=72mm
蜗轮喉圆直径:
da2=d2+2ha2=93.5
蜗轮喉母圆直径:
rg2=a-1/2da2=50-1/293.5=3.25
蜗轮齿顶圆直径:
蜗轮齿根圆直径:
蜗轮外圆直径:
当在z=1时,
2.2蜗杆轴的设计
(1)蜗杆轴的材料选择,确定许用应力
考虑轴主要传递蜗轮的转矩,为普通用途中小功率减速传动装置。
选用45号钢,正火处理,
(2)按扭转强度初步估算轴的最小直径
(2-21)
扭转切应力为脉动循环变应力,取α=0.6
抗弯截面系数W=0.1d3
取dmin=15.14mm
(3)确定各轴段的直径和长度
根据各个零件在轴上的定位和装拆方案确定轴的形状及直径和长度。
图2.1蜗杆轴
d1=d5同一轴上的轴承选用同一型号,以便于轴承座孔镗制和减少轴承类型。
d5轴上有一个键槽,故槽径增大5%
d1=d5=d1′×
(1+5%)=15.89mm,圆整d1=d5=17mm
所选轴承类型为深沟球轴承,型号为6203,B=12mm,D=40mm,
d2起固定作用,定位载荷高度可在(0.07~0.1)d1范围内,
d2=d1+2a=19.38~20.04mm,故d2取20mm
d3为蜗杆与蜗轮啮合部分,故d3=24mm
d4=d2=20mm,便于加工和安装
L1为与轴承配合的轴段,查轴承宽度为12mm,端盖宽度为10mm,
则L1=22mm
L2尺寸长度与刀架体的设计有关,蜗杆端面到刀架端面距离为65mm,
故L2=43mm
L3为蜗杆部分长度L3≥(11+0.6z2)m=38mm
圆整L3取40mm
L4取55mm,L5在刀架体部分长度为(12+8)mm,伸出刀架部分通过联轴器与电动机相连长度为50mm,故L5=70mm
两轴承的中心跨度为128mm,轴的总长为230mm
(4)蜗杆轴的校核
作用在蜗杆轴上的圆周力
(2-22)
(2-23)
其中d1=28mm
则
(2-24)
径向力(2-25)
切向力(2-26)
图2.2轴向受力分析
(2-27)
(2-28)
求水平方向上的支承反力
图2.3水平方向支承力
(2-27)
(2-28)
(2-29)
求水平弯矩,并绘制弯矩图
(2-30)
图2.4水平弯矩图
求垂直方向的支承反力
(2-31)
查文献[9]表2.2—4,,,,
其中,,
(2-32)
图2.5垂直方向支承反力
(2-33)
(2-34)
求垂直方向弯矩,绘制弯矩图
图2.6垂直弯矩图
求合成弯矩图,按最不利的情况考虑
(2-38)
(2-39)
图2.7合成弯矩图
计算危险轴的直径
查文献[9]表15—1,材料为调质的许用弯曲应力,则
所以该轴符合要求。
(5)键的选取与校核
考虑到d5=105%×
15.14=15.89mm,实际直径为17mm,所以强度足够
由GB1095-79查得,尺寸b×
h=5×
5,l=20mm的A型普通平键。
按公式进行校核
,,,。
查文献[9]表6—2,取则
(2-42)
该键符合要求。
由普通平键标准查得轴槽深t=3mm,毂槽深t1=2.3mm
2.3蜗轮轴的设计
(1)蜗轮轴材料的选择,确定需用应力
考虑到轴主要传递蜗轮转矩,为普通中小功率减速传动装置
选用45号钢,正火处理,,
(2)按扭转强度,初步估计轴的最小直径
查文献[9]表15—1,取45号调质刚的许用弯曲应力,则
由于轴的平均直径为34mm,因此该轴安全。
根据各个零件在轴上的定位和装拆方案确定轴的形状及直径和长度
即蜗轮轮芯为68mm
为蜗轮轴轴径最小部分取34mm
轴段与上刀架体有螺纹联接,牙形选梯形螺纹,根据文献表8-45
取公称直径为=44mm,螺距P=12mm,H=6.5mm
查表8-46得,外螺纹小径为31mm
内、外螺纹中径为38mm
内螺纹大径为45mm
内螺纹小径为32mm
旋合长度取55mm
L2尺寸长度为34mm,蜗轮齿宽b2当z1≤3时,b2≤0.75da1=15.6mm
取b2=15mm
2.4中心轴的设计
(1)中轴的材料选择,确定许用应力
考虑到轴主要起定位作用,只承受部分弯矩,为空心轴,因此只需校核轴的刚度即可。
选用45号钢,正火处理,,
(2)确定各轴段的直径和长度
d1=15mm,
d2与轴承配合