阳煤太化清徐化工新材料园区项目1号4号生产水脱盐处理装置工程施工组织设计方案ycgWord格式文档下载.docx
《阳煤太化清徐化工新材料园区项目1号4号生产水脱盐处理装置工程施工组织设计方案ycgWord格式文档下载.docx》由会员分享,可在线阅读,更多相关《阳煤太化清徐化工新材料园区项目1号4号生产水脱盐处理装置工程施工组织设计方案ycgWord格式文档下载.docx(47页珍藏版)》请在冰豆网上搜索。
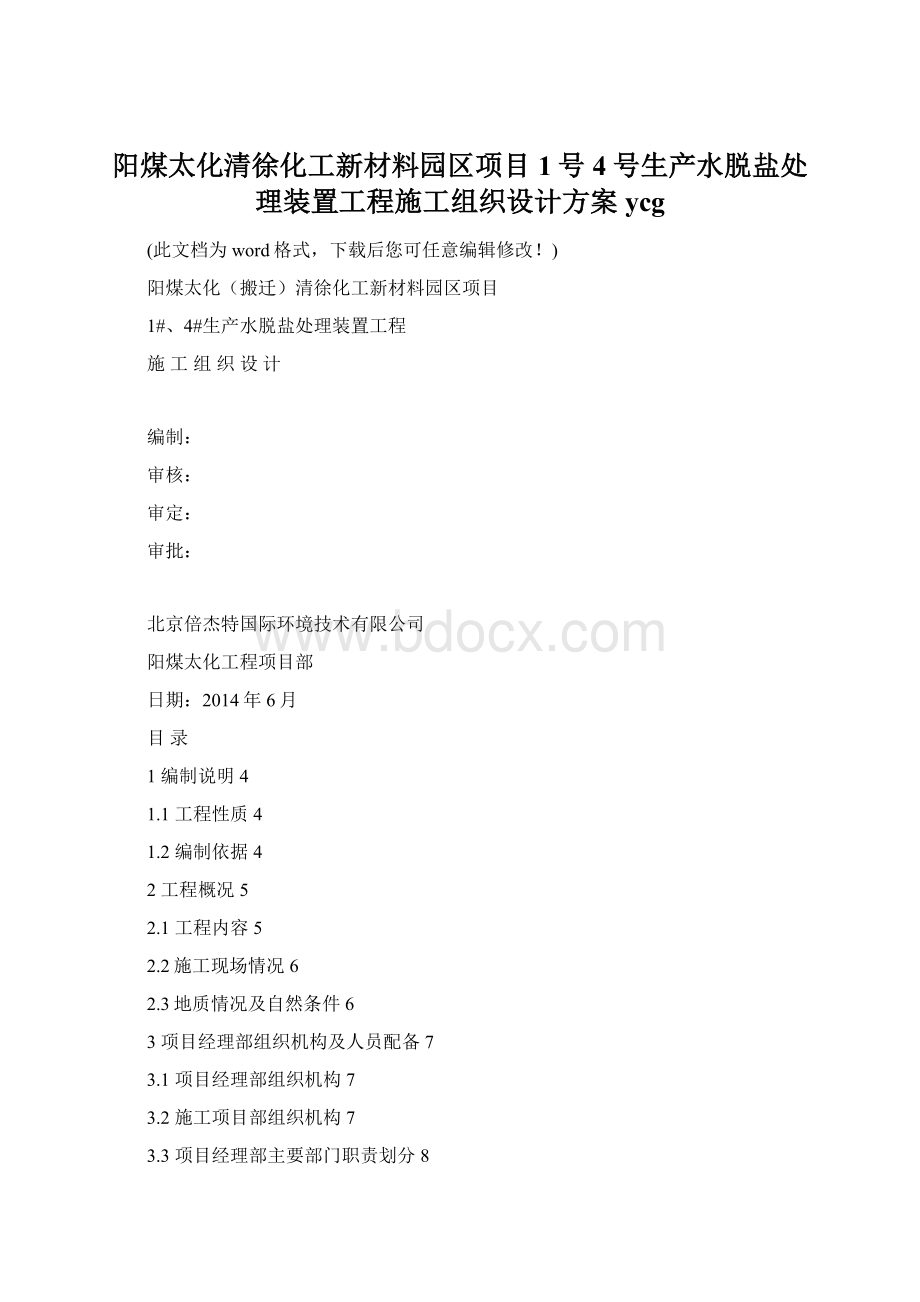
3项目经理部组织机构及人员配备7
3.1项目经理部组织机构7
3.2施工项目部组织机构7
3.3项目经理部主要部门职责划分8
4施工部署9
4.1施工总体目标规划9
4.2施工总体部署9
4.3施工资源配备计划9
4.4施工准备工作计划13
4.5施工计划安排15
5主要施工方法15
5.1设备安装工程施工方法15
5.2管道安装工程施工方法24
6施工质量保证措施35
6.1质量管理目标36
6.2质量管理体系及质量管理岗位职责36
6.3主要质量工序识别与施工控制点37
6.4关键部位质量预控对策表37
6.5主要质量工序控制程序39
6.6质量保证措施40
7进度保证措施41
7.1管理措施41
7.2劳动力保证措施42
7.3机具材料保证措施43
7.4季节性施工保证措施43
7.5资金支持措施43
8HSE管理与控制43
8.1HSE管理方针、目标43
8.2HSE管理机构及管理体系44
8.3HSE管理措施48
8.4主要安全危害辨识及预防控制措施49
8.5安全保证措施52
8.6健康保护措施53
8.7环境保护措施54
8.8文明施工及卫生、防疫管理措施55
8.9防火、保安措施57
8.10应急预案与响应计划59
8.11成品保护措施61
8.12成品保护管理制度61
9施工总体网络计划(见附页)62
10设备、材料的堆放与运输62
1编制说明
1.1工程性质
该工程由阳煤集团太原化工新材料有限公司投资新建项目,由北京倍杰特国际环境技术有限公司设计,本生产水脱盐装置设计规模:
总进水量2000m3,以壳体填料无渗漏为合格,密封试验应根据直径和压力按规定进行选取,阀门高压密封试验和上密封试验的压力为阀门公称压力1.1倍,低压密封试验压力0.6MPa,保压时间根据直径和压力按规定进行选取,以密封面不漏为合格。
2.6.6试验合格的阀门,应及时排尽内部积水,并吹干。
除需要脱脂的阀门外,密封面上应涂防锈油,关闭阀门,封闭出入口,做出明显标记,并填写阀门试验记录。
2.7材料保管
2.7.1经检查合格的管材、阀门、管件、紧固件应按现场临设平面布置进行摆放,材料摆放整齐,不得随意堆放,防止丢失或混淆。
碳钢、低温碳钢、不锈钢要分开摆放,不同型号的不锈钢也要分开摆放,不锈钢下面应垫置道木,做好底部与地面隔离以及表面防雨防晒覆盖等工作。
2.7.2不锈钢材料及防腐好的管道吊装卸装车要用软吊索。
2.7.3入库保管的管材、阀门、管件、紧固件应做好标识,注明规格、型号、材质、库存数量等。
3)管道预制
3.1管道预制前应进行下列检查
3.1.1管道图纸审查:
根据单线图、平面布置图、流程图、认真核对材料,发现问题及时提出、解决。
当管道平面布置图与管段图有差异时,应及时联系设计解决。
3.1.2检查管道材料标记、规格、型号、材质是否符合图纸要求。
无标记或标记不全、不清的材料不得使用。
3.1.3检查管道施工机具是否完好,尤其是焊接设备及计量器具应在检定周期内。
3.1.4检查管内有无石头、砂子、铁屑等杂物,若有应及时清理干净。
清理后及时封闭管口。
3.2下料
3.2.1下料前必须按图纸要求核对钢管的材质、规格及材料标记,并进行材料标记移植。
3.2.2碳钢管下料与坡口加工可用机械、砂轮机或氧-乙炔焰进行;
不锈钢管下料与坡口加工可用机械、砂轮机或等离子切割机进行。
3.2.3管子切割后,应用磨光机将管口周围的氧化物或熔渣清除干净,使之露出原金属光泽。
3.2.4管道下料后,对预制管段即可利用较长余料应封闭好。
3.2.4坡口及组对
a、管道的坡口加工形式及组对间隙见图3-1A和图3-1B。
对接坡口形式及组对间隙
图3-1A
壁厚(t)mm
坡口形状
尺寸
3≤t≤9
a′:
0-2mm
b:
θ:
35±
2.5度
9<t≤26mm
0-3mm
30±
b、角焊缝坡口形式
图3-1B
坡口形式
尺寸
a:
1.5-3mm
6.4mm或t中较小者
c、对不等厚材料,当厚度差超过1.5mm时,应按下图进行加工:
Cx=1.4T,但不大于颈部厚度
d、管道组对错边量不应超过母材壁厚的10%,且不大于2.0mm。
图3-2坡口加工图
3.4管道预制的一般规定
3.4.1φ>
16″的大口径管道组对时可采用定位卡板。
定位卡板的材质应与管道材质相同,定位卡板的切除应采用切割或磨削的方法。
3.4.2管道预制应在钢平台、管廊或水泥地面进行,不得在砂土地上组对焊接。
3.4.3预制组件应有足够的刚性,不得产生永久变形。
预制完后应及时编号、封口,妥善保管。
3.4.4管道预制应在X、Y、Z三个方向上的适当部位预留调整段或调整口,调整口的直管段宜加长50-100mm,调整段宜现场实测。
3.4.5管道上仪表接头及其它支管接头(包括临时管线接头)应在预制时一起完成,以避免管道就位后开孔及焊接,造成管内熔渣存积。
3.4.6焊接连接的阀门,在焊接时应使阀门处于开启状态。
3.4.7预制管段上法兰应置于容易拧紧螺栓的位置。
3.4.8预制管段上的焊口应躲开管架,并便于施焊和检验。
3.5支、吊架预制作
3.5.1支、吊架形式按设计图纸选用标准图。
3.5.2支、吊架的形式、材质、加工尺寸及焊接等应符合设计要求。
3.5.3焊制管托时应采取反变形措施。
3.5.4制作合格的支、吊架,应进行防锈处理,编号标记,妥善保管。
5.2.3安装方法
1管道安装的一般规定
1.1管道的安装就位应按第3.1条中所规定的原则进行。
安装前应按第4.1和第4.2条中有关条款进行检查。
1.2工艺管道的安装偏差应符合下列要求:
a、工艺管道一般法兰连接
表1-1
项目
允许偏差
备注
平行度
≤1.51000,且≯2mm
在法兰圆周任一点测量
同轴度
不超过5%d
保证螺栓能自由穿入
D:
法兰外径d:
孔径
b、与传动设备连接的管道
表1-2
设备转速·
rmin
平行度mm
同轴度mm
≤0.15
≤0.50
>
6000
≤0.10
≤0.20
c、安装允许偏差
管道安装允许偏差表4-3
项目
允许偏差mm
坐标及标高
室外
架空
15
地沟
埋地
25
室内
10
水平管弯曲
Dg≤100
11000
最大20
Dg≥100
1.51000
立管垂直度
21000
最大15
成排
管段
以同一平面上
±
5
间距
交叉
管外壁或保温层间距
1.3管道连接时,不得采用强力对口,加热管子,加偏垫或多层垫等方法来消除接口端面的空隙、偏差、错口或不同心等偏差。
1.4与设备(尤其是传动设备)连接的管道,管道与传动设备法兰连接前,应在自由状态下检查法兰的平行度和同轴度,其偏差要求应符合第4.4.1.2条。
1.5管道与设备连接前应将管内清理干净,并将管道与设备接口用带有特殊标记的临时盲板隔离。
1.6不锈钢管道安装时,不得用铁质工具敲击管道,不得用火焰直接加热调整,与管道支架之间应用氯离子含量小于40ppm的材料隔离。
1.7需反复拆装的部位,如设备进、出口、调节阀、孔板法兰、安全阀及所有水压试验吹扫中需拆除的管段法兰,应选用临时垫片,最后复位时再加装正式垫片,但加装临时垫片,应在单线图上做记录,临时垫片厚度应与正式垫片厚度一致。
1.8管道连接螺栓和螺母的螺纹上应涂以二硫化钼润滑脂,以防生锈。
1.9管道对口时应检查平直度(如图1-1),在距接口中心200mm处测量,当DN<
100mm时,允许偏差为1mm;
当DN≥100mm时,允许偏差为2mm,但全长允许偏差均为10mm。
1.10管道焊缝位置应符合下列要求:
a、直管段两环缝距离不应小于100mm。
b、焊缝距变管起弯点不得小于100mm,且不小于管径。
c、环焊缝距支、吊架的净距不小于50mm,需热处理的焊缝距支、吊架不得小于焊缝宽度的5倍,且不小于100mm。
d、在环缝上不得开孔,如必须开孔时,焊缝应经无损探伤检查合格。
e、加固圈距环缝不小于50mm。
2与传动设备的配管
2.1对传动设备,尤其是复杂的传动设备的配管要求。
a、设备的进、出口管道,特别是进口管道必须严格清扫,做到彻底无杂物、焊渣、锈皮等。
b、管道的安装不允许对主机产生任何附加应力,不得用强力拉、推、扭的方法来补偿安装偏差。
c、管道与设备应做到自由对中。
在自由状态下,管道法兰面安装偏差应符合第1.2条b的要求。
d、管道与设备连接时,应在设备联轴节处用百分表监测位移,其位移值应在0.02-0.05mm范围内。
e、管道经试压吹扫合格后,管道与设备再次连接时的偏差值应符合b及d条的规定。
若有超差则应通过调整支架等办法,使差值缩小直至合格。
2.2配管方法和步骤
a、管道法兰和设备法兰组对前,必须把密封面清理干净。
组装时先把管道法兰降低,使两密封面的间距等于垫片厚度,调整法兰相对水平偏差在0.1mm内。
同时注意螺栓孔的中心对中,使连接螺栓能在螺栓孔内自由出入。
b、管道组装过程中,所有管道支吊架应按设计位置就位。
吊架不得倾斜,弹簧支架的定荷卡板不得取下。
在管道封闭焊前,可以使用临时支、吊架或其它手段使管子就位。
从设备口延伸的管段亦可暂用螺栓与机体相连,并在弯头处设置临时支撑,避免因管道的重量引起设备轴线的偏移(位移)。
待合拢口点焊固定后,即应将所有的临时支架以及设备口法兰的螺栓拆除。
使管道在设计支架系统的支承下及设备法兰口处于自己状态下进行焊接。
焊接过程中,经常检查法兰的相对平行度和对中度,其偏差应符合第1.2条b款的规定。
否则,应采取对称焊接变形法将偏差超过部分矫正过来。
2.3管道的调整
管道因组对、焊接、焊口热处理、水压试验、吹扫等工作而产生的法兰口相对水平度和对中度误差,在设备试车前必须采取措施进行最后调整。
调整方法如下:
2.3.1在最后调整之前,应将弹簧支架的定荷卡板取下,并记下冷态负荷值和位移。
2.3.2调整方法
a、当偏差较小的情况下,一般通过调整支架达到法兰对中。
b、当偏差较大时,可以采用加热矫正的方法来消除偏差。
在管线上选择一个适当位置,对管子进行局部加热。
加热温度控制在℃(呈樱红色)。
加热区长度应视矫正量以及管线形状、加热区位置离法兰距离而定。
通常控制在两倍管径之内,但不小于200mm。
加热手段可采用电加热和中性火焰加热,对中