座体夹具 毕业设计说明书Word文档下载推荐.docx
《座体夹具 毕业设计说明书Word文档下载推荐.docx》由会员分享,可在线阅读,更多相关《座体夹具 毕业设计说明书Word文档下载推荐.docx(53页珍藏版)》请在冰豆网上搜索。
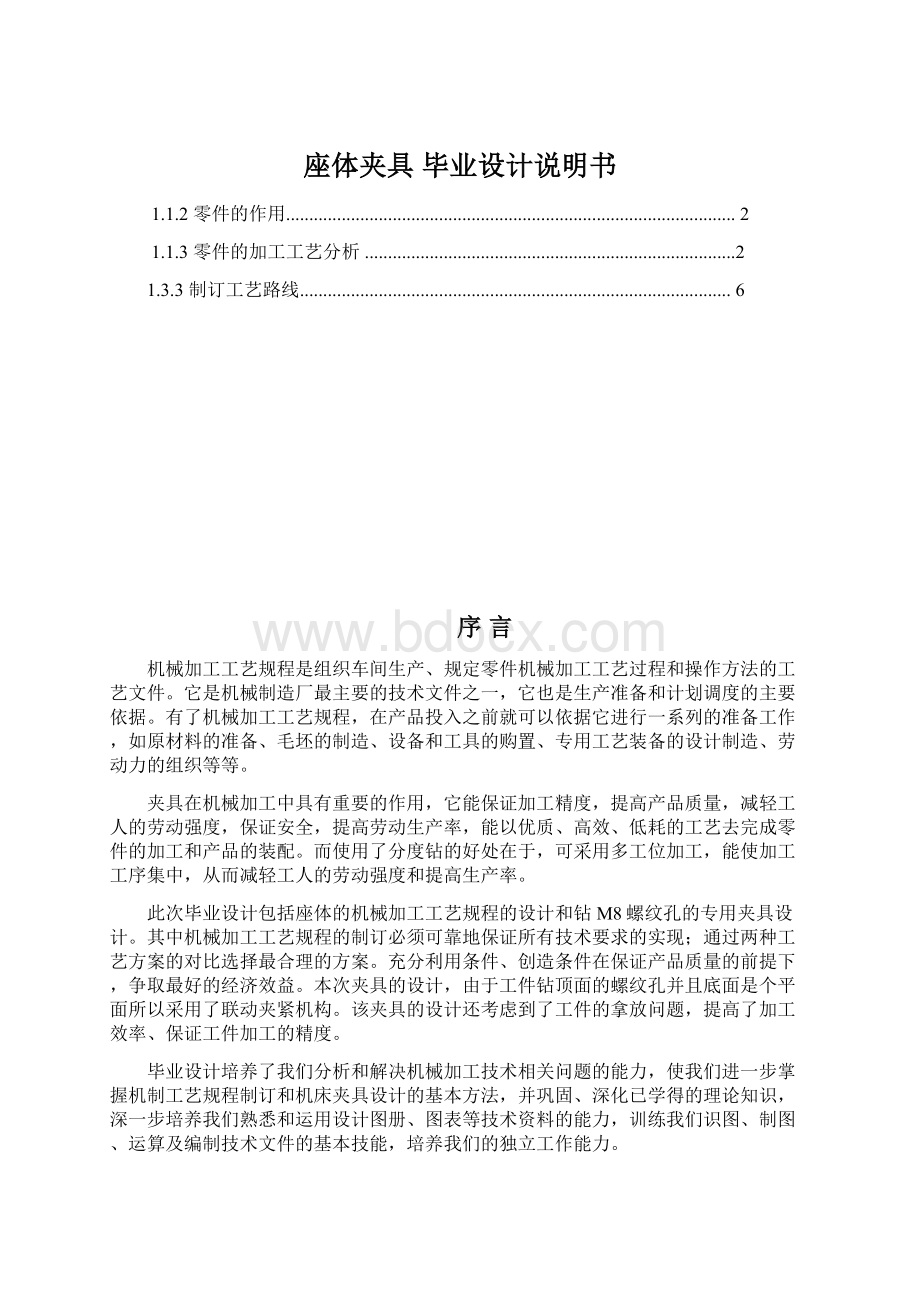
1.1.2零件的作用
课程设计题目给定的零件是座体,属于座体类零件,是汽它是用来支撑轴承的,固定轴承的外圈,仅仅让内圈转动,外圈保持不动,并且保持平衡。
1.1.3零件的加工工艺分析
零件图见图1–1。
图1–1零件图
该零件主要有平面、孔,是一个形状比较简单的零件。
(1)以工件的下表面为基准加工孔。
钻4×
Ø
9mm的孔,锪Ø
18mm的孔,钻2×
5mm销孔。
(2)以2×
9mm孔和底面为基准的加工面,这组加工面主要是Ø
42mm的两端面和Ø
24mm内孔,Ø
15mm孔端面和螺纹孔以及8×
M4螺纹孔。
1.2确定毛坯类型
1.2.1确定毛坯的成形方法
该零件材料为HT150,零件结构属于中等复杂程度,零件重要的和轮廓尺寸不是很大,故根据《铸造手册》第六卷表1–1查得采用熔模铸造。
这对提高生产率,保证加工质量也是有利的。
1.2.2确定机械加工余量、毛坯尺寸和公差
参考《机械制造技术基础课程设计指南》,铸件尺寸的公差及机械加工余量按GB/T6414-1999确定。
要确定毛坯的尺寸公差及加工余量,应先确定如下各项因素。
根据铸件的质量,零件表面粗糙度,形状复杂系数表5-4,由此查得单边余量在厚度方向为2.5mm。
即铸件各向尺寸的单边余量亦为2.5mm。
铸件中心孔的单边余量按表5-4查得为2.5mm。
(1)座体的毛坯余量由表5-4得毛坯的总尺寸为90mm
65mm
85mm
(2)铸件内孔余量由表5-4查得双边余量为5mm,取单边为2.5mm,毛坯孔径尺寸为Ø
19mm。
(3)毛坯中Ø
19mm孔,Ø
30mm孔为铸孔,其余孔均为实心。
(4)确定毛坯的热处理方式:
铸件毛坯应安排退火,降低金属材料的硬度,提高塑性,以利切削加工或压力加工,减少残余应力,提高组织和成分的均匀化。
1.3机械加工工艺过程设计
1.3.1基面的选择
基面选择是工艺规程设计中的重要工作之一,基面选择得正确合理,可以使加工质量得到保证,生产率得到提高。
否则,加工过程中会问题百出,甚至造成零件大批量报废,使生产无法正常进行。
1.粗基准的选择
由零件图可以看出零件底面上表面的粗糙度不做要求,因此可以以它作为粗精准来铣底面和加工4个沉头孔和2个销孔,其中对角的两个沉头孔需要精铰。
2.精基准的选择
主要考虑的是基准的中和问题。
当设计与工序的基准不重合时,因该进行尺寸换算。
选择底面和底面两个对角精铰的沉头孔作为精基准。
1.3.2确定机械加工方法和余量及工序尺寸
根据以上原始资料及机械加工工艺,分别确定各加工表面的机械加工余量、工序尺寸如下:
1.铣底面厚度87.5mm:
根据铣面的精度要求,参照《机械制造技术基础课程设计指南计》5-49,确定工序尺寸及余量:
粗铣:
保证厚度88mm,Z=2mm
精铣:
保证厚度87.5mm,Z=0.5mm
2.Ø
9mm,沉头Ø
18mm深2mm的孔
毛坯为实心孔,参考《机械制造技术基础课程设计指南计》表5-15,5-30确定工序尺寸及余量:
钻孔:
6.8mm
扩孔:
9mm,2Z=2.2mm,h=13mm
锪孔:
18mm,2Z=9mm,h=2mm
其中两个对顶角的孔需要精铰,因此钻—粗铰—精铰。
钻:
粗铰:
8.96mm
精铰:
9mm
18mm,2Z=9mm,h=2mm
3.钻销孔Ø
5mm:
毛坯为实心,参考《机械制造技术基础课程设计指南计》5-15,确定工序尺寸及余量:
4.8mm
4.96mm
5.00mm
4.铣Ø
42mm两端面厚度80mm:
保证厚度81mm,2Z=4mm
保证厚度80mm,2Z=1mm
5.镗Ø
24mm孔:
毛坯为Ø
19mm孔,参考《机械制造技术基础课程设计指南计》表5-15,5-30确定工序尺寸及余量:
粗镗:
23.8mm,2Z=4.8mm
半精镗:
24mm,2Z=0.2mm
6.8×
M4螺纹孔
3.3mm,2Z=3.3mm
倒C0.5倒角
攻螺纹:
M4—6H
7.铣Ø
15mm的顶面
保证厚度85.5mm,Z=2mm
半精铣:
保证厚度85mm,Z=0.5mm
8.M8螺纹孔
6.7mm
倒C1角
攻螺纹孔:
M8-6H
1.3.3制订工艺路线
见下表1-1
表1-1工艺路线图
工序号
工序名称
工序内容
1
铸造
2
时效
10
铣
粗铣底面至尺寸88mm
20
精铣底面至尺寸87.5mm
30
钻
钻底面对角2×
9mm通孔
40
钻底面对角孔至Ø
8.8mm
50
铰
粗铰对角孔至Ø
60
精铰对角孔至Ø
70
锪
锪孔Ø
18mm深度2mm
80
钻孔Ø
4.8mm孔
90
粗铰Ø
4.96mm孔
100
精铰Ø
5mm孔
110
粗铣Ø
42mm两端面至尺寸81mm
120
精铣Ø
42mm两端面至尺寸80mm
130
镗
粗镗Ø
24mm孔至Ø
23.8mm
140
半精镗Ø
24mm
150
钻M4螺纹孔底孔Ø
3.3mm
160
170
攻
攻M4螺纹
180
粗铣上顶面至尺寸85.5mm
190
半精铣上顶面至尺寸85mm
200
钻M8螺纹底孔至Ø
210
倒C1倒角
220
攻M8螺纹孔
3
去毛刺
去除全部毛刺
4
终检
按零件图样要求全面检查
1.4选择机床和工艺设备
1.4.1选择机床
根据该零件的加工特点以及考虑到经济问题,所以尽可能的选用通用机床以减少加工成本。
但为使加工方便在有些情况下也选用了专用机床对零件进行加工,基本情况如表1–2机床的选择所示。
表1–2各工序机床的选择
所选机床
X52K
Z525
组合铣床
T68
组合钻床
1.4.2选择夹具
为了提高劳动劳动生产率,保证加工质量,降低劳动强度,所以在加工该零件时所用的夹具都是专用夹具。
1.4.3选择刀具
结合各个加工表面的特点以及其加工方法,综合考虑这两者选用刀具如表1–3刀具的选择所示。
表1–3各工序刀具的选择
刀具
10、110、180
硬质合金面铣刀
直柄扩孔钻
20、130、200
镶齿三面刃铣刀
90º
直柄锥面锪钻
50、60、90、100
锥柄机用铰刀
160、210
60º
30、40、80、150、200
直柄麻花钻
170、220
细柄机用丝锥
1.5确定切削用量及基本工时
1.5.1工序10粗铣底面至尺寸88mm
1.工序切削用量及基本时间的确定
(1)切削用量
本工序为粗铣面,所选刀具为硬质合金面铣刀。
铣刀直径d=80mm,宽度L=30mm,齿数z=10。
根据《机械制造技术基础课程设计指南》表5-143选择铣刀的基本形状。
由于加工铸件的硬度在200~250HBS范围内,故选前角γ0=-10°
,后角a0=8°
。
已知铣削宽度
=65mm,铣削深度
=2mm。
机床选用X52K型立式铣床。
①确定每齿进给量
根据《机械制造技术基础课程设计指南》表5-144,X52K型立式铣床的功率为7.5kW,工艺系统刚性为中等,圆柱形铣刀加工铸铁,查的每齿进给量
=0.09~0.18mm/z。
现取
=0.09mm/z。
②选择铣刀磨顿标准及耐用度
根据《机械制造技术基础课程设计指南》表5-148,用硬质合金面铣刀粗加工铸件,铣刀刀齿后刀面最大磨损量为1.2mm;
铣刀直径d=60mm,耐用度T=120min。
③确