硅铁精炼Word文件下载.docx
《硅铁精炼Word文件下载.docx》由会员分享,可在线阅读,更多相关《硅铁精炼Word文件下载.docx(12页珍藏版)》请在冰豆网上搜索。
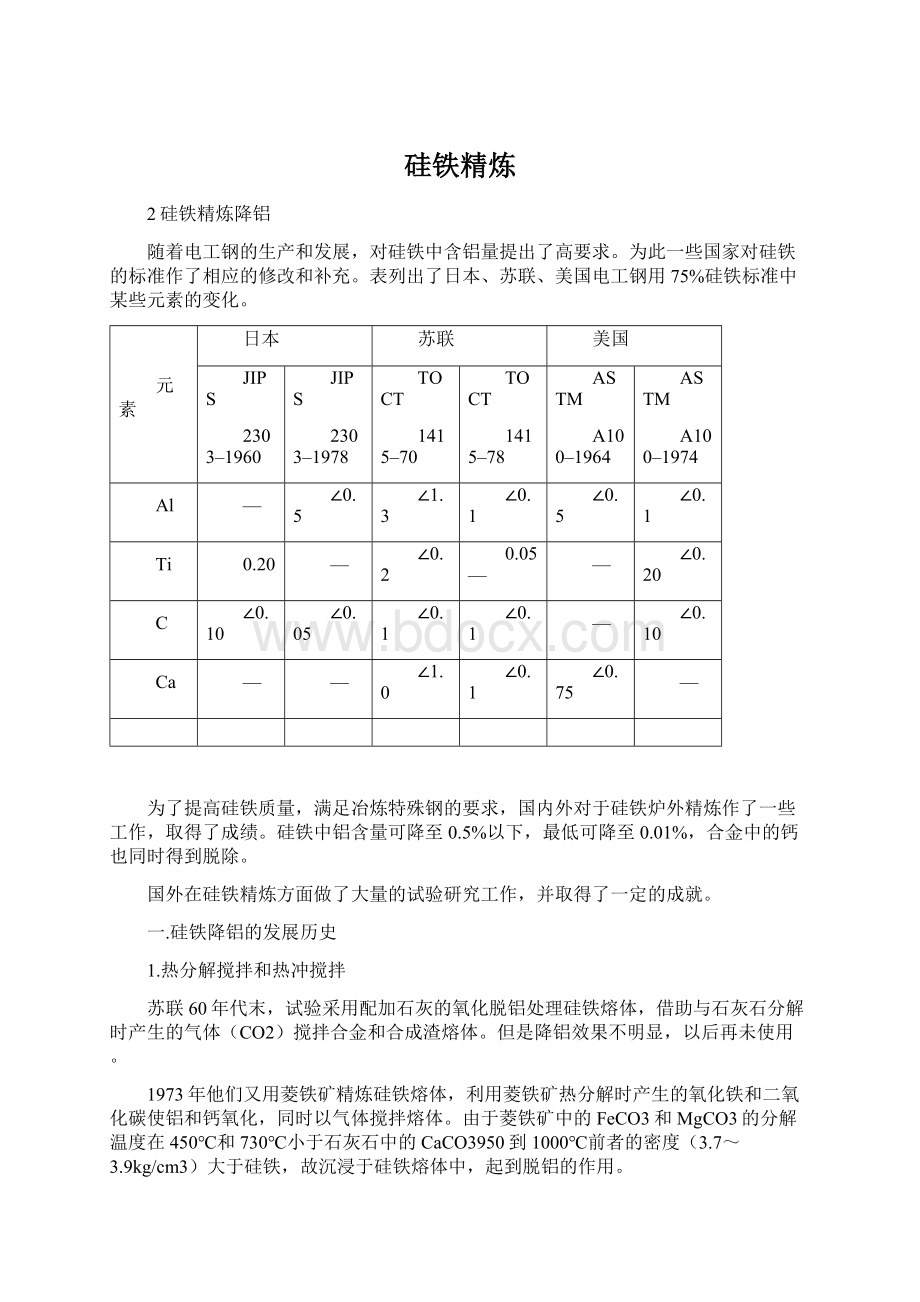
∠1.3
∠0.1
Ti
0.20
∠0.2
0.05—
∠0.20
C
∠0.10
∠0.05
Ca
∠1.0
∠0.75
为了提高硅铁质量,满足冶炼特殊钢的要求,国内外对于硅铁炉外精炼作了一些工作,取得了成绩。
硅铁中铝含量可降至0.5%以下,最低可降至0.01%,合金中的钙也同时得到脱除。
国外在硅铁精炼方面做了大量的试验研究工作,并取得了一定的成就。
一.硅铁降铝的发展历史
1.热分解搅拌和热冲搅拌
苏联60年代末,试验采用配加石灰的氧化脱铝处理硅铁熔体,借助与石灰石分解时产生的气体(CO2)搅拌合金和合成渣熔体。
但是降铝效果不明显,以后再未使用。
1973年他们又用菱铁矿精炼硅铁熔体,利用菱铁矿热分解时产生的氧化铁和二氧化碳使铝和钙氧化,同时以气体搅拌熔体。
由于菱铁矿中的FeCO3和MgCO3的分解温度在450℃和730℃小于石灰石中的CaCO3950到1000℃前者的密度(3.7~3.9kg/cm3)大于硅铁,故沉浸于硅铁熔体中,起到脱铝的作用。
苏联曾用倒包热冲精炼法实行75%硅铁炉外降铝。
出铁后加入精炼混合料,然后进行倒包热冲。
这样可是Al由1.5%~2.0%降至0.3%~0.5%;
Ca由0.25%~0.5%降至0.05%~0.1%.
2.吹气搅拌精炼
波兰先后三次发表有关压缩空气吹炼的文章。
他们主要采用黄铁矿、铁矿、萤石作精炼料,合金出炉时加于熔体中,并吹压缩空气(压力为0.2~0.5大气压)吹炼15分钟,Al降至≤0.5%脱铝率在70%左右。
苏联工业性生产含铝≤0.5%的75%硅铁是采用合成渣(铁矿、石灰、硅砂、石灰石)处理硅铁,然后再用压缩空气(余压为0.2~0.3大气压)吹炼的方法。
硅铁自炉内放入包里期间,将上述干燥的合成料(粒度为5~25mm)不断加入熔体中。
待合成料完全熔化后,将压缩空气通过石墨喷咀(插进深度为合金层的2/3)吹入熔体中。
吹炼时间为15分钟。
经过吹炼后,合金中Al含量≤0.5%.Si损失量约为1.0%(绝对值)。
1977年,日本吴本制铁公司的平敏雄提出了加合成渣吹氧精炼,并用棒状搅拌器进行硅铁脱铝的方法,经过20分钟的处理后Al从1.5~2.5%降至0.05以下。
金属回收率为96~97%。
金属中Si含量增加了1%左右。
其它杂质(Ca﹑Mg﹑C)和非金属夹杂物也得到了精炼脱除。
用SiO2-Ca-CaF2-FeO低熔点合成渣精炼处理硅铁
3.摇包法精炼
1969年,平敏雄曾提出了另一项精炼脱铝的方法。
用SiO2-Ca-CaF2-FeO低熔点合成渣精炼处理硅铁,并用摇包装置加速反应,以提高脱铝效率。
处理15~20分钟后可使Al含量降至0.05%以下。
日本的实践证明,对于矿热炉容量不大(7500~1500KVA),每炉出铁不超过2吨的情况下,使用摇包法降铝是一种简单、经济、实用的方法。
4.合成渣粉喷吹精炼
根据波兰1969年的报导,75%硅铁溶自炉内放入铁水包里,然后用压力为0.2~0.5大气压的压缩空气往包内的铁水喷吹黄铁矿和萤石粉,15分钟后Al降至<1.5%。
苏联在1968年开始进行合成渣喷吹试验,起初用压缩空气吹含Ca和Mg易熔性合成渣粉,处理结果可是铝降低70~75%,金属中最终铝含量可达<0.5%,成功率为80%。
喷吹精炼方法从力学的角度看,是炉外降铝一个比较有前途的方法。
5感应炉精炼
将矿热炉中放出的铁水直接注入低频感应炉内,并将合成渣混合粉加入其中,通过感应搅拌器使合成渣与铁水相互接触进行反应,并能保证熔体所需温度,从而脱除硅铁中的铝。
日本1977年提出用低频感应炉加细粒生石灰和硼砂混料,经感应炉加热搅拌15分钟后,合金中铝含量由初始2%左右,降至<0.05%。
捷克在1969年也提出了感应电炉加热搅拌合成渣和硅铁溶体精炼降铝方法。
这种精炼方法目前可能处于试验研究阶段,未见有用于工业生产的报道。
二.氯化精炼法
用这种方法精炼硅铁和金属硅可使Al含量降至0.01%,Ti含量可降低40~50%,C和Ca含量都可降至微量,同时非金属夹杂物可由0.8~1.2%降至0.3~0.6%
英国在1954年就提出这种方法其特点是用氯气或含氯气体(如SiC4﹑CCl4等)在惰性气体——氮气或氩气保护下,以混合气体的形式吹入硅铁熔体中。
硅铁中的铝以气态氯化物形式进入气相而除掉。
1960年,美国肯塔基州卡尔伏特城工厂采用氯气通过石墨管吹入硅铁熔体里进行精炼。
吹氯深度几乎达到铁水包的底部。
精炼每吨75%硅铁需用氯气15kg左右。
以SiCl4而损失的硅量非常少。
75%硅铁经吹氯后,Al由0.8%降至0.08%;
Ca由0.15%降至0.01%。
近年来,苏联相继发表了许多此类专利和文章,对氯化反应机理和条件选择做研究工作用氯气精炼可达到高的脱氧度,但氯气毒性太大给操作带来了许多难点,故近年来有报道都用SiC4﹑CCl4作氯化脱Al剂。
目前,硅铁精炼方法主要用合成渣氧化精炼和氯化精炼。
采用合成渣氧化精炼,操作方法较简单,成本低,但杂质的脱氧率比氯化精炼法低。
采用氯化精炼法可使硅铁中的杂质大幅度的降低,得到高纯度的硅铁。
但吹氯后排出的气体必须经过净化处理,其流程极为复杂。
因此这种氯化精炼法尚未得到工业上的广泛应用。
合成渣氧化精炼
1合成渣氧化精炼简述
合成渣氧化精炼法是,通过杂质被氧化的过程实现去除杂质的目的,其过程的本质是“选择性氧化”。
可用“氧位”的概念来讨论容硅及杂质的稳定性。
根据文献给出的热力学数据,计算出T=1773K时生成各种氧化物的△F°
值—氧位。
2Ca+O2=2CaO
△F°
=-1558745.64+370.11T
T=1773K△F°
=-902540.61J
4/3Al+O2=2/3Al2O3
=-1121225.04+214.36T
=-741164.76J
Si+O2=SiO2△F°
=-952078.32+195.94T
=-604676.7J
2Fe+O2=2FeO△F°
=-441707.4+77.87T
=-303643.89J
从上面氧位计算可以看出,在相同的氧压和温度下,钙与氧的亲和力最大,铝次之,硅再次之,而铁与氧的亲和力最弱。
所以溶剂中的氧化剂分解出来的氧化钙和铝,达到平衡后,才能氧化硅,如冶炼工业硅,又因为硅的活度aSi=1,故硅的氧化保护铁不被氧化。
2硅铁冶炼中Al2O3的还原机理
硅铁原料中的硅石和焦炭,含有一定数量的Al2O3。
硅石含Al2O3量约0.5%~1.0%,焦炭含Al2O3量达4%~6%。
Al2O3熔点高,还原性差,其软化点为1800℃,而熔点高达2030℃.
硅铁冶炼为无渣法.矿热炉内,在预热层和烧结层,Al2O3不不可能熔融,只有达到坩埚区,温度达到1800℃以上时,Al2O3与熔融的SiO2结合成Al2O3·
SiO2(其熔点为1487).进入到冶炼电弧区,Al2O3·
SiO2将与C或SiC进行复杂的物理化学反应,被还原成Al和Si.其反应式为:
2Al2O3(S)+6C=4Al(l)+6CO(g)
(1)
△G°
=612300-258.6T
T始=2367K
2Al2O3(S)+6SiC(S)=4Al(l)+6Si(l)+6CO(g)
(2)
△G°
=837000-270T
T始=3100K
由反应式
(1)﹑
(2)可以看出,Al2O3与C开始反应温度在2094℃以上,而与SiC反应则达2827℃.因此,在硅铁冶炼中,只有进入高温冶炼区中的Al2O3才可以与C或SiC反应,被还原成Al.而在炉料结构层中的炉心和炉壁料层,由于温度较低,Al2O3很难被还原,而是SiO2﹑SiC等物体结合成高熔点的难熔物,形成熔渣或假炉底和假炉壁.
由Si-Al相图可以看出Si和Al几乎完全不互溶,它们之间不能形成化合物。
而AL和Fe却能结合成a-FeAl.由于Al在硅铁液中,即可与Si互溶,也可与Fe结合,这给给硅铁炉外脱铝造成一定的空难。
新余钢铁公司的生产及资料表明,硅铁中Al含量与原料带入的Al2O3数量有关系统计资料(表1)分析表明,冶炼反应中Al2O3的还原率约70%左右。
表1硅铁中的Al含量与原料中的Al2O3数量的关系
硅铁含Al量/%
<0.5
<1.0
<1.5
<2.0
生产1t硅铁原料中的
Al2O3的量/kg
<11
<24
<37
<50
3低铝硅铁的冶炼
根据硅铁冶炼特点,在冶炼过程中,直接控制硅铁中Al含量的方法,一是控制入炉原料的Al2O3量;
二是抑制炉中Al2O3的还原。
3.1降低硅石中Al2O3的量
一般生产1t硅铁需消耗硅石1730kg。
冶炼冶炼硅铁用硅石中的Al2O3含量为0.5%~1.0%,按70%还原率计算,则Al含量达0.32%~0.64%。
因此,在选用硅石时,要求选用Al2O3的含量低的硅石。
另外硅石要筛分清洗,以除去表面的泥土和混合的杂物。
3.2选择低Al2O3的还原剂
由物料平衡可知,冶炼1t硅铁需要干焦900kg。
表2为焦炭所应控制的Al2O3量。
表2硅铁中Al含量与焦炭红Al含量的对应关系
干焦所应控制的Al2O3量/%
3.0
7.24
7.06
6.89
6.72
6.54
6.37
2.5
5.88
5.71
5.54
5.37
5.19
5.02
2.0
4.53
4.36
4.19
4.02
3.84
3.67
1.5
3.18
3.01
2.84
2.67
2.49
2.32
1.0
1.83
1.66
1.49
1.32
1.14
0.97
0.5
0.48
0.31
0.14
——
硅石含
Al2O3量/%
0.6
0.7
0.8
0.9
由表2分析可知,在硅铁生产中,硅石带入Al2O3量为原料带入的Al2O3总量的20%~30%,而还原剂带入的Al2O3总量达70%~80%。
因此要降低硅铁中Al的含量,主要应控制还原剂中的Al2O3量。
硅铁冶炼使用的还原剂有冶金焦﹑气煤焦﹑篮碳﹑石油焦﹑木炭等。
由于产地所使用煤种不同,他们所含Al2O3量也不同,一般冶金焦含Al2O3量为4.5%~6.0%;
蓝碳含Al2O3量为1.5%左右;
石油焦含Al2O3量为0.2%~0.4%;
木炭含Al2O3量最低。
我国大部分铁合金厂现在普遍采用搭配或使用气煤焦或蓝碳作为还原剂,选用低Al2O3硅石,生成含Al0.5%~2.5%的75FeSi。
而对生成含Al低于0.5%的硅铁,应选用蓝碳﹑石油焦﹑木炭做还原剂,并搭配使用。
3.3配入适量CaO,抑制Al2O3还原
抑制Al2O3还原,是降低Al含量的有效方法
Al2O3由于熔点高,不易还原,还原温度高达2094℃以上,炉内的Al2O3一部分在冶炼区与碳结合还原成Al并熔于硅铁液,另一部分与SiO2结合而形成高熔点的Al2O