基于AMESIM的ABS液压系统建模与仿真本科生毕业设计Word格式文档下载.docx
《基于AMESIM的ABS液压系统建模与仿真本科生毕业设计Word格式文档下载.docx》由会员分享,可在线阅读,更多相关《基于AMESIM的ABS液压系统建模与仿真本科生毕业设计Word格式文档下载.docx(15页珍藏版)》请在冰豆网上搜索。
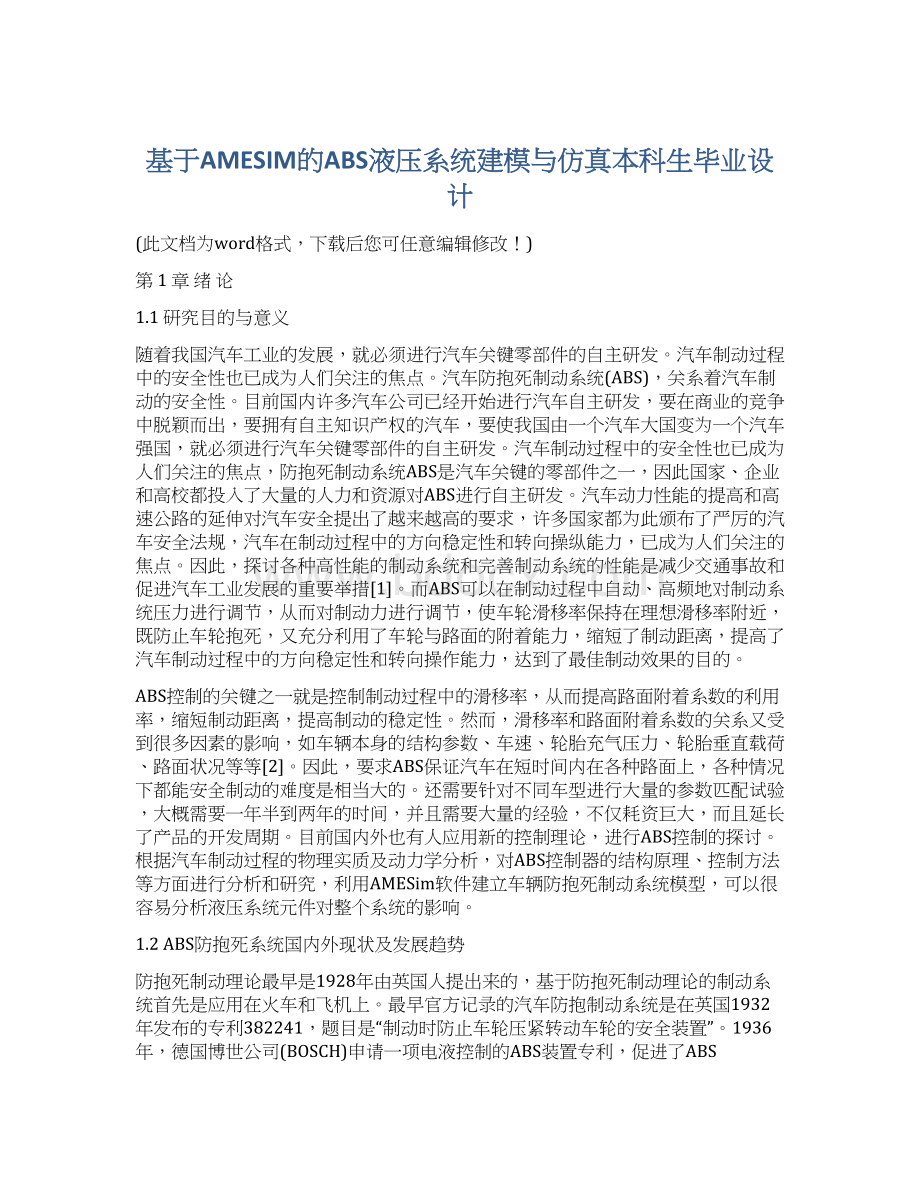
因此,探讨各种高性能的制动系统和完善制动系统的性能是减少交通事故和促进汽车工业发展的重要举措[1]。
而ABS可以在制动过程中自动、高频地对制动系统压力进行调节,从而对制动力进行调节,使车轮滑移率保持在理想滑移率附近,既防止车轮抱死,又充分利用了车轮与路面的附着能力,缩短了制动距离,提高了汽车制动过程中的方向稳定性和转向操作能力,达到了最佳制动效果的目的。
ABS控制的关键之一就是控制制动过程中的滑移率,从而提高路面附着系数的利用率,缩短制动距离,提高制动的稳定性。
然而,滑移率和路面附着系数的关系又受到很多因素的影响,如车辆本身的结构参数、车速、轮胎充气压力、轮胎垂直载荷、路面状况等等[2]。
因此,要求ABS保证汽车在短时间内在各种路面上,各种情况下都能安全制动的难度是相当大的。
还需要针对不同车型进行大量的参数匹配试验,大概需要一年半到两年的时间,并且需要大量的经验,不仅耗资巨大,而且延长了产品的开发周期。
目前国内外也有人应用新的控制理论,进行ABS控制的探讨。
根据汽车制动过程的物理实质及动力学分析,对ABS控制器的结构原理、控制方法等方面进行分析和研究,利用AMESim软件建立车辆防抱死制动系统模型,可以很容易分析液压系统元件对整个系统的影响。
1.2ABS防抱死系统国内外现状及发展趋势
防抱死制动理论最早是1928年由英国人提出来的,基于防抱死制动理论的制动系统首先是应用在火车和飞机上。
最早官方记录的汽车防抱制动系统是在英国1932年发布的专利382241,题目是“制动时防止车轮压紧转动车轮的安全装置”。
1936年,德国博世公司(BOSCH)申请一项电液控制的ABS装置专利,促进了ABS技术在汽车上的应用。
汽车上开始使用ABS始于20世纪50年代中期福特汽车公司,1954年福特汽车公司在林肯车上装配法国航空公司的ABS装置,这种ABS装置控制部分采用机械式,结构复杂,功能相对单一,只有在特定车辆和工况下,防抱死控制才有效,因此制动效果并不理想。
机械结构复杂使ABS装置的可靠性差、控制精度低、价格偏高,使ABS技术在汽车上的推广应用举步维艰。
直到70年代后期,由于电子技术的迅猛发展,为ABS技术在汽车上的应用提供了可靠的技术支持。
ABS控制部分采用了电子控制,其反应速度、控制精度和可靠性都显著提高[3],制动效果也明显改善,同时其体积逐步也变小,质量也逐步减轻,控制与诊断功能不断增强,价格也逐渐降低。
这段时期许多家公司都相继研制了形式多样的ABS装置。
进入90年代后,ABS技术不断发展成熟,控制精度、控制功能不断完善。
现在发达国家已广泛采用了ABS技术。
ABS装置制造商主要有:
德国博世公司(BOSCH),欧、美、日、韩国家的汽车采用的最多;
美国德科公司(DELCO),由美国通用及韩国大宇汽车采用;
美国本迪克斯公司(BENDIX),由美国克莱斯勒汽车采用;
还有德国戴维斯公司(TEVES)德国瓦布科(WABCO)、美国凯尔西海斯公司(KELSEYHAYES)等,这些公司的ABS产品都在广泛地应用,而且还在不断发展、更新和换代。
国内对ABS的研究工作始于八十年代初,研制单位有东风汽车公司、交通部重庆公路所、重庆宏安ABS有限公司、陕西兴平514工厂与西安交通大学等。
东风汽车公司从80年代初开始研究ABS,该公司对Wabco公司的ABS产品进行了剖析、试验、改进和消化吸收,将Wabco的ABS装在EQ-145型车上并在各种路面上进行试验。
交通部重庆公路所研制的ABS适用于中型汽车,其第一代ABS电子控制单元(ECU)采用了Z80芯片,第二代ABS产品采用了MCS-96系列8098单片机,控制软件、传感器和执行器都由自己研制,装车试验的主要问题是系统对于路况的识别不够理想。
1984年兴平814厂研制的第一代防抱制动系统的主要缺点是不能自动适应不同路况,以后该厂与西安公路交通大学合作研制了第二代防抱制动系统,增设了路面识别功能的电路,但对于长轴距的大客车则不是很理想。
宏安公司是我国批量生产ABS的厂家。
该公司于1993年投产,当年生产ABS5000套。
重型汽车研究中心1995年6月对自制的ABS系统进行了道路试验,但存在一些问题,随后,课题组重新设计了软件及硬件,所生产的ABS基本上己达到国外产品的性能。
随着车辆动力学与控制理论研究的不断深入,以及计算机技术、传感器技术、液压技术和通讯技术的不断发展,可以预测ABS技术将向以下几个方向发展。
ABS正在向小型车普及,但作为附加的安全装置,它会增加整车的重量并占据安装空间,因此要求其体积和重量尽可能小。
减小ABS体积的主要途径有优化结构设计(如减小压力调节器)及增加集成度。
目前,经过优化的ABS己可将主缸、压力调节器和电控单元集成为一体,从而大大减小了体积和成本。
由于技术的不断改进,ABS的功能在不断加强。
ABS的作用是通过控制汽车的纵向制动力来使汽车在制动过程中保持最佳的纵向附着系数和较好的横向附着系数,从而提高汽车的制动性能、方向稳定性和操纵性。
与此相类似的是汽车驱动防滑系统(ASR),其作用是防止汽车在加速过程中打滑,以保证汽车加速时的方向稳定性、操纵性,其控制机理仍然是通过控制纵向滑移率来控制纵向力,可见,ABS和ASR是密切相关的,因此常将它们结合在一起使用,构成行使安全系统。
这样,它们可共用许多电子元件和系统部件来控制汽车车轮的运动,电子控制和保护装置都被装在同一个壳体内。
Bosch公司早在1987年就推出了ABSASR防滑控制系统。
1996年,Bosch公司提出了车辆动力学系统(VDC)的概念,在ABSASR的基础上,加入侧向稳定性控制等新内容,以实现全工况内的汽车运动状态最佳[4]。
1.3汽车ABS结构与工作原理
1.3.1传感器
汽车ABS轮速传感器是ABS的信息感知元件,为了防止车轮抱死,控制程序必须知道单个车轮的实时速度。
只有取得准确的车轮速度或加速度信号,控制系统ECU才能知道什么时候下达卸压指令,什么时候下达保压指令,什么时候下达增压指令,从而使车轮不致抱死,并不断减速直到停止,如图1.1。
图1.1ABS轮速传感器
实时性ABS的防抱死控制大约在5-7ms就完成一个循环,因而对轮速处理过程的实时性要求就更高了。
系统取得轮速所花的时间分为硬件转换时间和软件计算时间。
这两者之间又以软件时间的开销为大。
最极端的情况是一个循环的时间都花在了轮速的计算上。
由于有着这样的限制,轮速算法不可能设计得很复杂。
ABS轮速的精度对其以后的轮加减速度和参考车速的计算精度影响很大。
所以轮速算法应能对轮速原始信号中的粗大误差加以识别、剔除,或者抑制粗大误差的影响。
实用的轮速算法采用测量脉冲的宽度,经过数字滤波,从而对轮速的结果进行合理性的判断修正。
1.3.2电子控制单元
ABS的电子控制单元(ElectronicControlUnit),简称ECU。
它的主要作用是接收轮速传感器等输入信号,计算出轮速、参考车速、车轮减速度、滑移率等,并进行判断,输出控制指令,控制制动压力调节器等进行工作。
ECU一般由以下几个基本电路:
轮速传感器的输入放大,整形电路、运算电路、电磁阀驱动电路、回油泵驱动电路、稳压电源、电源监控电路和故障诊断电路。
大多数电子控制单元是以微处理器为基础,采用专用集成电路,一般至少有一个微处理器来确保快速、可靠地处理数据,如图1.2。
图1.2ABS电子控制单元
1.3.3压力调节单元
压力调节单元(HydraulicControlUnit),简称HCU,是ABS中的主要执行机构,也是ABS液压系统的核心部件,如图1.3所示。
其作用接受ABS电子控制单元的指令,驱动调节器中的电磁阀动作(或油泵电机动作),实现轮缸压力的调节。
其结构原理及性能特征对ABS的控制性能产生及其重要的影响。
图1.3ABS液压调节单元内部结构
HCU要按既定的压力控制模式,有效地对制动压力实施控制,又必须满足以下基本要求:
通常助力式和动力式液压制动系的促动时间为0.36s。
ABS的促动时间应小于上述时间。
目前,典型HCU的反应时间仅为0.01s,而ECU每秒可进行200次左右计算。
一般来讲,HCU的频率为5~10次秒时,即可达到使用要求。
HCU对制动压力实施有效控制,应使增压和减压速率适当。
压力调节速率决定了制动器摩擦力矩的调节速率和控制过程中加、减速度的大小。
加、减速度绝对值小,则制动效能低下;
加、减速度绝对值大,会使ABS难以控制,此时不仅影响制动效能,而且会使车辆制动时舒适性降低。
可见压力调节速率是否得当,将影响ABS控制质量。
合理的制动压力取决于路面条件、气象条件、车辆类别及承载情况等。
制动压力波动不宜太大,否则制动摩擦力矩波动范围大,路面制动力波动范围也增大,会使车辆传动系的冲击损伤也大。
并且过大的制动压力波动会引起制动管路的震动,影响ABS的控制效果。
HCU主要有电磁阀、蓄能器、回油泵,以及一些辅助液压阀等构成。
它与ECU封装在一起。
HCU中共有4对用于防抱死制动压力调节的高速开关电磁阀。
每对高速开关阀又由一个常开阀(又称加压阀)和一个常闭阀(又称减压阀)组成。
每对电磁阀对一个控制通道进行独立防抱死制动压力控制。
4个常开阀分别设置在制动主缸两腔和液压助力室至各制动轮缸的制动管路中;
而另4个常闭阀分别设置在各个制动轮缸至蓄能器的制动液通路中。
在防抱死制动过程中,通过HCU电磁阀的开关动作来实现制动压力的调节。
通常在制动开始时,系统中的各电磁阀均不通电,常开阀和常闭阀都处于断电状态,常开阀开启,常闭阀关闭,主缸的高压制动液经常开阀进入制动轮缸而不能进入蓄能器。
HCU从结构上保证各制动轮缸的制动压力与制动踏板行程,以及制动踏板力成比例关系,随着制动压力的增加,轮速迅速降低而趋于抱死状态时,ECU根据输入的轮速信号判断出系统下一个控制周期应进入减压状态,常开阀和常闭阀都通电,常开阀关闭,常闭阀打开,轮缸内的制动液经常闭阀进入蓄能器;
随着制动压力的降低,当轮速逐渐恢复到一定值时,ECU判断出当前需要处于保压状态,常开阀通电,常开阀关闭,常闭阀断电,轮缸中的制动液被封闭在两个电磁阀之间。
回油泵的作用是将蓄能器中的制动液泵回主缸。
经过这样几个控制循环,汽车就完成制动过程,达到减速停车的目的。
1.3.4ABS工作原理
汽车在行驶过程中,车轮在路面上的纵向运动可有滚动与滑动两种形式,车轮相对于路面的滑动又可分为滑移与滑动两种形式.试验表明,当轮胎在路面上滑移时,将改变轮胎与地面间的附着系数,因而也改变了汽车的制动力。
随着制动压力的升高,在与轮速旋转相反的方向上将产生地面制动力矩,轮速开始减小,随着制动力的增加,车轮开始产生滑移,车轮滚动的成份越来越少,而滑动的成份越来越多,一般用滑移率S来描述制动时车轮的滑移程度,如公式(1.4)。
(1.4)
式中,V—汽车行驶速度;
S—滑移率;
ω—车轮的转