机械制造与模具制造工艺学.docx
《机械制造与模具制造工艺学.docx》由会员分享,可在线阅读,更多相关《机械制造与模具制造工艺学.docx(44页珍藏版)》请在冰豆网上搜索。
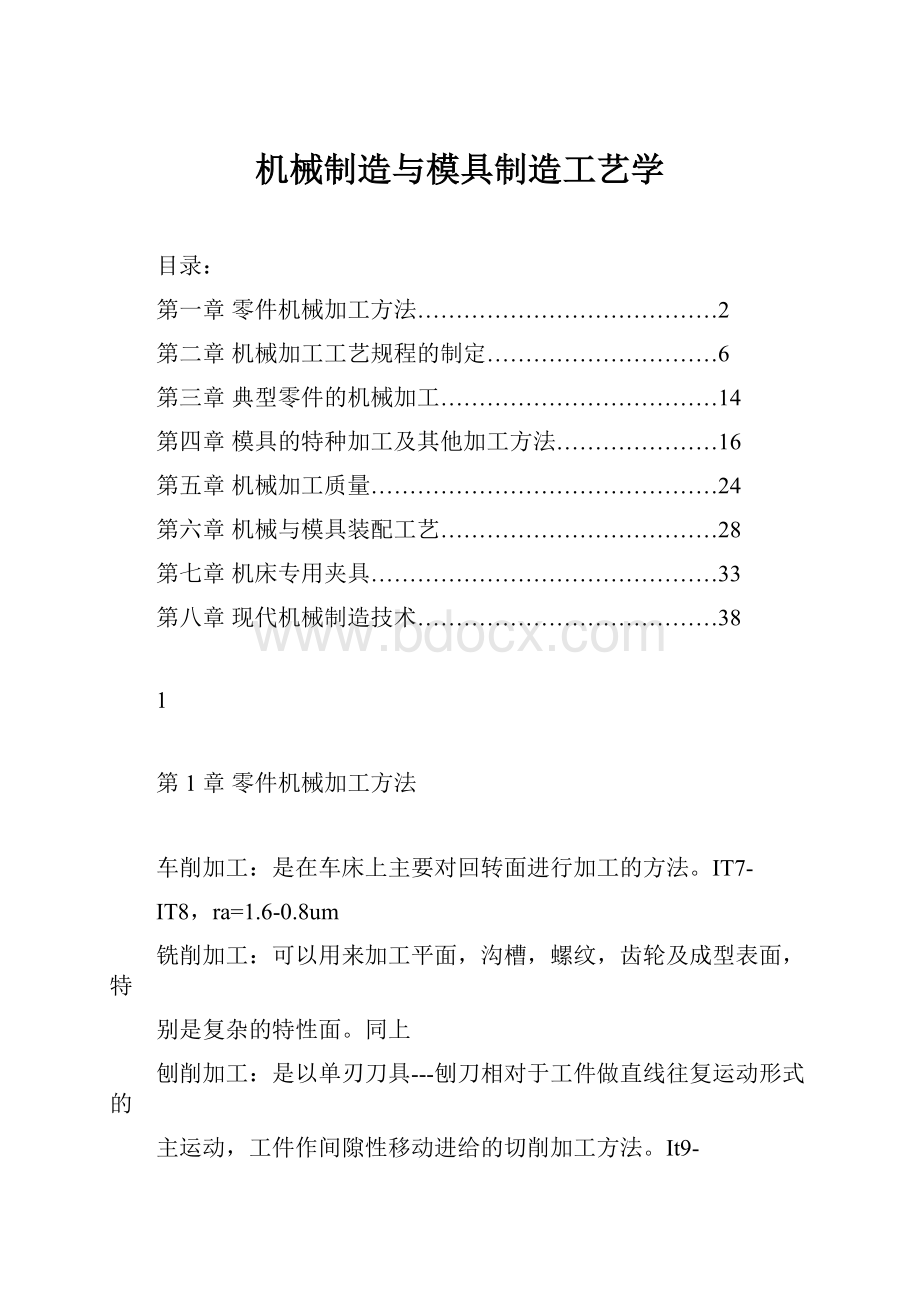
机械制造与模具制造工艺学
目录:
第一章 零件机械加工方法…………………………………2
第二章 机械加工工艺规程的制定…………………………6
第三章 典型零件的机械加工………………………………14
第四章 模具的特种加工及其他加工方法…………………16
第五章 机械加工质量………………………………………24
第六章 机械与模具装配工艺………………………………28
第七章 机床专用夹具………………………………………33
第八章 现代机械制造技术…………………………………38
1
第 1 章 零件机械加工方法
车削加工:
是在车床上主要对回转面进行加工的方法。
IT7-
IT8,ra=1.6-0.8um
铣削加工:
可以用来加工平面,沟槽,螺纹,齿轮及成型表面,特
别是复杂的特性面。
同上
刨削加工:
是以单刃刀具---刨刀相对于工件做直线往复运动形式的
主运动,工件作间隙性移动进给的切削加工方法。
It9-
7,ra=6.3-1.6
磨削加工:
可以加工外援,内孔面,平面,成型平面,螺纹及齿轮
廓形等各种表面
仿形加工:
是以预先制成的靠模为依据,加工是在一定压力作用下,
触头与靠模工作表面紧密接触,并沿其表面移动,通过仿
形机构,使刀具作同步仿形动作,从而在零件毛坯上加工
出与靠模形同型面的零件。
雕刻加工:
是对零件,模具型腔表面或型面上的图案花纹,文字和
数字的加工。
坐标镗床加工:
是在坐标镗床上,利用精密坐标测量装置,对零件
的孔及孔系惊醒高精度切削加工。
2
成形磨削:
是成形表面精加工的一种方法,磨削中常碰见的成形表
面多为直母线成形表面。
简答
车削的方法;①特形曲面的车削,包括凸轮,手柄,自动机床上的
靠模及球面等 ②多型腔零件的车削③对拼装式型腔的车
削
模具零件的立铣加工主要有:
①平面或斜面的铣削②圆弧面的铣
削 3 复杂型腔或型面的铣削 4 坐标孔的铣削
磨削加工的方法:
无心内圆磨削和行星式内圆磨削
行星式内圆磨削的原理:
磨削时,工件不动,砂轮除高速旋转外,
砂轮轴还要围绕着固定中心做旋转运动以实现圆周进给。
磨削时的横向进给由砂轮轴绕工件内孔轴线旋转半径增
大来完成,纵向进给可由工件或砂轮完成。
仿形加工的原理及加工方法:
是以预先制成的靠模为依据,加工
是在一定压力作用下,触头与靠模工作表面紧密接触,
并沿其表面移动,通过仿形机构,使刀具作同步仿形动
作,从而在零件毛坯上加工出与靠模形同型面的零件。
可以分为机械式,液压式,电控式,电液式,光电式。
液压式仿形的特点:
结构简单,体积小而输出功率大,工作适应性
强,动作灵敏度高。
3
电控式仿形的特点:
系统结构紧凑,传递信号快捷,准确,灵敏度
高,仿形触头压力小,易于实现远距离控制。
仿形铣削的切削运动路线的三种基本形式:
水平分行,垂直分行,
沿轮廓铣削。
立体靠模的制造材料:
1 非金属材料,如木材,树脂混合石膏,合
成树脂。
木材的材质要坚硬且不易变形,制成靠模后涂
漆或涂硬化树脂:
树脂混合石膏是用石膏为基本材料,
添加常温硬化性粉末树脂,以增强耐压能力:
合成树脂
的密度小,强度好,收缩性小,容易 制作,常以玻璃纤
维增强材料,用层压浇注制作靠模。
2 有色金属,如铝合
金,铜合金,锌基合金等,可用铸造法制成靠模。
3 黑色
金属,即钢或铸铁,用切削的方法制成靠模,适合于大
批生产。
常见的坐标测量装置有:
1 带校正尺的精密丝杆坐标测量装置 2 精
密刻度尺—光屏读书器坐标测量装置 3 光栅—数字显示
器坐标测量装置
光学系统的工作原理:
光源射出的光经聚光镜后为平行光束,再经
滤色器,反光镜与前物镜,投射到精密刻度尺的刻线面
上,刻度尺的刻度线经前物镜,反光镜,后物镜,反光
镜投影成像到光屏读数头的光屏上,通过目镜可以清晰
地观察到放大的像。
坐标镗削加工定位与坐标转换的基本方法:
1 以工件上的划线或
4
以外圆及内孔为定位基准,用定位角铁和光学中心测定
器找正,然后把工件正确地安装在工作台上 2 为方便工
件在机床上的加工,把零件图上按设计要求标注的孔距
尺寸换算成机床加工要求的直角坐标尺寸或极坐标尺寸。
基本磨削方法:
内孔磨削。
外圆磨削,锥孔磨削。
端面磨削,。
直
线磨削,铡磨。
成形磨削的方法:
成形砂轮磨削法,夹具磨削法。
按照砂轮的形状,成形砂轮的修磨有三种:
1 砂轮角度的修整 2
砂轮圆弧的修整 3 砂轮非圆弧曲面的修整。
夹具磨削法有:
1 正弦精密平口钳 2 正弦磁力台 3 正弦分中夹具 4
万能夹具。
万能夹具的组成:
工件装夹部分,回转部分,十字滑块,分度部分。
成形磨削工艺尺寸的换算:
首先确定磨削该工件的工艺中心,其
次确定工艺尺寸计算的坐标系,最后进行工艺尺寸计算。
成形磨削时应计算的工艺尺寸:
1 各圆弧中心的坐标尺寸 2 各平
面到相应工艺中心的垂直距离 3 各平面对 坐标轴的倾斜
角度 4 各圆弧的包角(回转角)。
5
第二章 机械加工工艺规程的制定
生产过程:
在工厂里,由原材料转化为最终产品的一系列相互关联
的劳动过程的总和成为…。
工艺过程:
生产过程中为改变生产对象的形状,尺寸,相对位置和
性质等,使其成为成品或半成品的过程成为工艺过程。
机械加工工艺过程:
采用机械加工的方法,直接改变毛坯的形状,
尺寸和表面质量等,使其成为零件的过程成为机械加工
工艺过程。
工序:
工序是一个人或一组工人,在一个工作地,对一个工件所连
续完成的那部分机械加工工艺过程。
定位:
确定工件在机床上或夹具中占有正确位置的过程成为定位。
夹紧:
工件定位后将其固定,使其在加工过程中保持定位位置不变
的操作称为夹紧。
装夹:
将工件在机床上或夹具何总定位,夹紧的过程称为装夹。
安装:
工件经一次装夹后所完成的那一部分工序内容称为安装。
工位:
为了完成一定的工序内容,一次装夹工件后,工件与夹具或
设备的可动部分一起相对刀具或设备的固定部分所占据
的每一个尾椎称为工位。
工步:
工步是在加工表面和加工工具不变的情况下,所连续完成的
那一部分工序的内容称为工步。
进给:
刀具从被加工表面切下一层金属称为一次进给。
6
生产纲领:
企业在计划期内应当生产产品产量和进度计划称为生产
纲领。
生产类型:
企业生产专业化程度的分类称为生产类型。
工艺规程:
规定产品或零部件制造工艺工程和操作方法等的工艺文
件称为工艺规程。
零件的工艺性:
是指所设计的零件在满足使用要求的前提下制造
的可行性和经济性。
工艺性审查:
在机械产品设计过程中,凡正式用于生产的零件图都
必须经过工艺性分析,生产中称为工艺性审查。
毛坯余量/加工总余量:
毛坯尺寸与零件尺寸只差。
基准:
是用来确定生产对象上级和要素间的几何关系所依据的那些
点,线,面。
设计基准:
是设计图样上所采用的基准。
工艺基准:
是在加工过程中所采用的基准。
工序基准:
在工序图上用来确定本工序所加工表面加工后的尺寸,
形状看,位置的基准称为工序基准年.
定位基准:
在加工是,为了保证工件相对于机床和刀具之间的正确
位置所使用的基准称为定位基准。
测量基准:
测量时所采用的基准称为测量基准。
装配基准:
它是装配时用来确定零件或部件在产品中的相对位置
所采用的基准。
粗基准:
机械加工的最初工序只能用工件毛坯上未经加工表面作定
7
位基准,这种定位基准称。
精基准:
用已经加工过的表面作定位基准称为精基准。
加工经济精度:
是指在正常的加工条件下所能保证的加工精度。
加工余量:
是指加工过程中所切去的金属层厚度。
工序余量:
是相邻两工序的工序尺寸只差。
加工总余量/毛坯余量:
是毛坯尺寸与零件图样的设计尺寸之差。
工序尺寸:
零件每一道工序加工规定达到的尺寸称为工序尺寸。
尺寸链:
在机器装配或零件加工过程中,由相互连接的尺寸形成封
闭的尺寸组称为尺寸链。
封闭环:
尺寸链中在装配过程或加工过程最后形成的一环。
组成环:
尺寸链中对封闭环有影响的全部环。
增环:
尺寸链中的组成环,由于该环的变动引起封闭环同向变动。
减环:
尺寸链中的组成环,由于该环的变动引起封闭环反向变动。
机械加工时间定额:
是在一定生产条件下,规定生产一件产品或完
成一道工序所需 消耗的时间。
简答
生产过程的组成:
工序,安装,工位,工步,进给。
生产类型按产量划分为:
单件生产,成批生产,大量生产。
工艺规程的作用:
在生产过程中,工艺规程是指导工人操作和用
于生产,工艺管理工作的主要技术文件,又是新产品投
8
产前进行生产准备和技术准备的依据和新建,扩建车间
或工厂的原始资料。
此外,先进的工艺规程还起着脚镣
和推广先进经验的作用。
制定工艺规程的基本原则:
是保证以最低的生产成本和最高的生
产效率,可靠地加工出符合设计要求的产品。
因此,在
制定工艺规程时,应从工厂实际条件 出发,充分利用现
有生产条件,尽可能利用国内外的先进技术和经验。
制定工艺规程的基本步骤:
1 熟悉和分析制定工艺规程的主要依
据,确定零件的生产纲领和生产类型,进行零件的结构
工艺性分析;2 确定毛坯,包括旋转毛坯类型及其制造
方法;3 拟定工艺路线;4 确定各工序的加工余量,计算
工序尺寸及其公差;5 确定各主要工序的技术要求及检
验方法;6 确定各工序的切削用量和时间定额;7 进行技
术经济分析,选择最佳方案;8 填写工艺文件。
工艺性审查的作用及内容:
是协助设计员改进零件工艺性,完善
图纸,更有利于制造;一是零件的结构组成是否适合于
切削加工,二是技术要求是否有利于切削加工。
零件的结构工艺性的要求有:
1 零件的整体结构,组成各要素的
几何形状应尽量简单统一 2 尽量减少切削加工量,减少
材料及切削刀具的消耗量 3 尽可能采用普通设备和标准
刀,量具加工,且刀具易切入,切出而顺利通过加工表
面 4 要便于装夹,装夹次数少 5 零件加工部位要有足够
9
的刚性,以减少加工过程中的变形量,提高加工精度 6
尽可能采用标准件,通用件,借用件和相似件。
毛坯的种类和选择:
机械零件常用的毛坯主要有铸件,锻件,焊
接件,各种型材及板材等,选择毛坯要综合考虑的因素:
1 零件材料及其力学性能,零件材料是铸铁,就选铸造
毛坯,材料是钢材,且力学性能要求高时,可选锻造件,
冷冲模工作零件要求材料具有足够的抗冲击韧度,一般
选用锻造毛坯,反之选用型材或铸件 2 零件材料的工艺
性,当材料具有良好的铸造性能时,应选用铸造 3 零件
的结构形状和尺寸,形状复杂的毛坯,采用铸造 4 生产
类型,大量生产选用精密铸造或特种铸造,单件生产应
用砂型铸造或自由锻 5 工厂生产条件,尽量利用工厂现
有生产设备和生产方法以求最好的经济性。
工艺基准的分类:
工序基准,定位基准,测量基准,装配基准。
粗基准的选择原则:
1 为了保证加工面与非加工面之间的位置要
求,应选非加工面为粗基准 2 为了保证各加工面都有足
够的加工余量,应选择毛坯余量小的面为粗基准 3 为了
保证重要加工面的余量均匀,应选择其为粗基准 4 粗基
准应避免重复使用,在同一尺寸方向上,通常只允许使
用一次 5 作粗基准的表面应 平整光洁,以使工件定位可
靠,夹紧方便。
精基准的选择原则:
保证加工精度和装夹可靠方便,必须满足基
10
准重合的原则,基准统一的原则,自为基准的原则,互
为基准的原则,保证工件定位准确,夹紧可靠,操作方
便的原则。
工艺路线的拟定:
工艺路线是工艺规程设计的总体布局,其主要
任务是选择零件表面的加工方法,确定加工顺序,划分
加工阶段。
根据工艺路线,可以选择各工序的工艺基准,
确定工序尺寸,设备,工装,切削用量和时间定额等。
在拟定工艺路线时应从工厂的实际情况出发,充分考虑
应用各种新工艺,新技术的可行性和经济性。
选择零件表面加工方法的主要根据:
1 零件材料性质及热处理
要求,淬火钢件的精加工采用磨削加工和特种加工 2 零
件加工表面的尺寸公差等级和表面粗糙度 3 零件的加工
表面的位置精度要求 4 零件的形状和尺寸 5 生产类型 6
具体生产条件。
机械加工工序的安排原则:
基准先行,先主后次,先粗后精,先
面后孔。
在零件切削加工工艺过程中,首先要安排加工
基准面的工序。
作为精基准表面,一般都安排在第一道
工序进行加工,以便后续工序利用该基准定位加工其他
表面。
其次安排加工主要表面。
至于次要表面则可在主
要表面加工后穿插进行加工。
当零件需要分阶段进行加
工时,即先进行粗加工,再进行精加工,最后进行精加
工和光整加工。
总之表面粗糙度值低的表面和最终加工
11
工序必须安排在最后加工,尽量避免磕碰高光洁的表面。
所有机械零件的切削加工总是先加工出平面,然后再加
工内孔。
热处理工序的安排:
1 预备热处理,目的是改善加工性能,为最
终热处理做好准备和消除残余应力 2 最终热处理,目的
是提高力学性能,如调制,淬火,渗碳淬火等。
调制,
淬火安排在半精加工之后,精加工之前,以便在精加工
磨削时纠正热处理变形 3 零件加工表面粗糙度 ra 值能否
安排淬火工序的界限,一般情况下,零件加工表面粗糙
度 ra<=0.8um 时,不得安排淬火工序。
几种典型的工艺路线:
1 调制钢件,正火或退火——加工精基准
——粗加工主要表面——调制——半精加工主要表面—
—局部表面淬火,低温回火——精加工主要表面——去
应力回火——检验。
2 渗碳钢件,正火—加工精基准—
粗,半精加工主要表面—渗碳—淬火,低温回火—精加
工主要表面—去应力退火——检验。
3 高碳钢,工具钢
件,正火—球化退火—加工精基准—粗。
半精加工主要
表面—淬火(+冷处理),低温回火—人工时效—精加工
主要表面—人工时效—检验。
4 灰口铸铁件,时效—加
工精基准—粗,半精加工主要表面—时效—精加工主要
表面—检验。
5 渗氮钢件,①精密磨具,退火或正火—
加工精基准—粗加工—调制—半精加工—稳定化处理—
12
精加工—装配—试冲模—渗氮—光整加工—检验②普通
模具,粗加工—调制—精加工—渗氮—研磨—检验。
加工阶段的划分:
1 粗加工阶段,其主要任务是切除加工表面上
的大部分余量,使毛坯的形状和尺寸尽量接近成品 2 半
精加工阶段,为主要表面的精加工作好必要的精度和余
量准备,并完成一些次要表面的加工 3 精加工阶段,是
精度要求高的表面达到规定的质量要求。
要求的加工精
度较高,各表面的加工余量和切削用量都比较小。
4 光
整加工阶段,其主要任务是提高被加工表面的尺寸精度
和减小表面粗造度,一般不能纠正形状和位置误差。
划分加工阶段的作用:
1 有利于保证产品质量 2 有利于合理使用
设备 3 便于热处理工序的安排,使热处理与切削加工工
序配合更合理 4 便于及时发现毛坯缺陷和保护已加工表
面。
划分加工阶段的依据:
主要根据零件加工表面的尺寸公差等级,
表面粗糙度,热处理要求等划分加工阶段。
工序集中具有的特点:
1 工件在一次装夹后,可以加工多个表面,
能较好地保证加工表面之间的相互位置精度,可以减少
装夹工件的次数和辅助时间,减少工件在机床之间的搬
运次数,有利于缩短生产周期 2 可以减少机床数量,操
作工人,节省车间生产面积,简化生产计划和生产组织
工作 3 采用的设备和工装结构复杂,投资大,调制和维
13
修的难度大,对工人的技术水平要求高。
工序分散具有的特点:
;机床设备及工装比较简单,调整方便,
生产工人易于掌握 2 可以采用最合理的切削用量,减少
机动时间 3 设备数量多,操作工人多,生产面积大。
第三章典型零件的机械加工
轴类零件的主要功能:
支承传动 件和传递转矩。
卧式车床主轴机械加工的定位基准:
1 最常用的是两端中心孔
作为辅助定位基准 2 采用带有中心孔的锥堵或锥套心轴
代替主轴上的中心孔定位 3 选择装配轴颈作为定位基准
4 选择主轴外圆与中心孔为定位基准
提高磨削生产率的方法:
一是缩短辅助时间,如自动装卸工件,
自动测量,数字显示尺寸,砂轮自动修整及补偿,采用
新的磨料,提高砂轮的耐用度以减少修整次数,二是改
变磨削用量以及增大磨削面积,如高速磨削,深切缓慢
进给磨削,砂带磨削,宽砂轮磨削及多片砂轮磨削等。
外圆表面的光整加工方法:
高精度磨削,超精加工,研磨,珩磨,
滚压,抛光等
高精度磨削的特点:
能够修正上道工序流线的形状误差和位置误
差,生产效率高,可配备自动测量仪,但对机床本身精
14
度要求也很高,机床回转精度与振幅须在 0.001mm 一下,
进给机构不能有低速爬行现象。
超精加工切削过程:
强烈切削阶段,正常切削阶段,微弱切削阶
段,自动停止切削阶段。
滚压加工原理:
是利用金属的塑形变形,采用硬度 比工件高的特
质的滚压工具,对半精加工后的零件表面加压,使金属
表层在外力作用下产生残余变形,从而改变其表层的物
理力学性能。
滚压加工的特点:
不能纠正上道工序留下的形状误差和位置误差,
滚压后的形位精度取决于上道工序,滚压对象是材料组
织均匀的塑形金属零件,不适合用于淬硬材料及局部有
松组织的材料,滚压生产效率高,常以滚压代替研磨,
珩磨。
深孔加工存在的问题:
1 采取工件旋转,刀具仅作进给运动的方
式,预先在工件上加工出一个与刀具直径尺寸相符的 短
导向孔,引导刀具,并且改进刀具导向结构,在刀具上
安装导向块,减少刀具的引偏 2 采用压力输送切削液冷
却刀具,强制排除切屑带走热量 3 改进刀具结构看,增
加切屑措施,有良好的分屑,断屑和卷屑功能,有利于
切屑顺利排出等。
孔的光整加工方法:
精细镗孔,内孔珩磨,内孔研磨,孔滚压。
15
箱体孔系加工方法:
1 平行孔系的加工方法,常用找正法,找正
法是工作在通用机床上利用辅助工具来找正要加工孔的
争取位置的方法,这种方法加工效率低,一般只适用于
单件小批量生产。
常见 有划线找正法,心轴和量规找正
法,样板找正法。
出息之外,还有镗模法,坐标法等。
2 同轴孔系的加工方法,在单件小批量生产中,常利用
已加工孔系作支承导向,或利用铣镗床后立柱上的导向
套支承导向,或采用调头镗。
3 交叉孔系的加工方法,
主要在卧式铣镗床上靠机床工作台上的 90 度对准装置来
控制有关孔的处置度,有时,也用心棒与百分表找正俩
帮助提高其定位精度。
第四章模具的特种加工及其他加工方法
电火花加工:
是一种电,热能加工方法,是利用工具电极和工件
电极间电火花放电时,瞬时产生的高温使电极表面
局部金属腐蚀去除而对工件进行加工。
消电离:
在一次脉冲放电结束后,使放电通道中的带电粒子复合成
中性粒子,这一过程即为。
加工速度:
电火花加工时,正极和负极同时受到不同程度的腐蚀,
单位时间内工件蚀除量成为加工速度。
极性效应:
电火花加工时,无论是正极还是负极都会受到不同程度
16
的电腐蚀。
即使两个电极的材料相同也往往出现正、
负极的蚀除速度不一样,这种现象称为极性效应。
工作液:
电火花加工一般都在液体介质进行,此液体介质称为工作
液。
二次放电:
指已加工表面上,由于电蚀产物的介入,使极间实际距
离减少或是极间工作液绝缘性能降低,而再次发生非
正常放电现象。
冲油式:
将清洁的工作液冲入放电间隙,连同电蚀产物一起从电极
侧面间隙排出。
抽油式:
从电极间隙抽出工作液,使工作液连同电蚀产物一起经过
感觉待加工表面而被排出。
电火花穿孔加工:
是利用电火花放电时的电腐蚀原理,通过工具
电极相对于工件作进给运动,而把成形电极的侧
面形状和尺寸反拷在工件上,加工所需通孔。
工件的准备:
是指完成电火花加工前的全部工序。
电规准:
是指为达到预定的工艺指标,电火花加工过程中的相互配
合的一组电参数。
电化学加工:
通过电化学反应从工件上去除或镀覆金属材料的特
种加工方法。
复制精度:
是指加工出的形状和尺寸与阴极形状和尺寸相符合的程
度。
重复精度:
是指用同一个工具阴极加工一批工件的形状和尺寸的一
17
致性。
化学加工:
利用酸、碱、盐等化学溶液与金属产生化学反应,使金
属腐蚀溶解,改变工件尺寸和形状的一种加工方法。
化学蚀刻加工:
先把工件非加工面用耐腐蚀的涂层保护起来,需
加工的表面暴露出来,侵入到化学溶液中进行腐蚀,
使金属的特定部位溶解除去,达到加工的目的。
电解抛光:
是利用在电解液中发生阳极溶解现象而对工件表面进行
腐蚀抛光的。
电铸加工:
是利用电化学过程中的阴极沉积现象来进行成型加工的。
超声波:
指高于人耳听觉频率上限的一种振动波。
超声波加工:
是利用工具端面作超声频振动,通过磨料悬浮液加
工脆硬材料的一种加工方法。
型腔挤压法:
是利用金属塑性变形原理,实现模具型腔无切削力
加工的一种方法。
开式挤压:
模具四周没受限制,金属向四周自由流动而形成型腔。
闭式挤压:
将模具坯料约束在模套内,凸模挤压模具坯料时,金属
径向流动受到限制,只能朝与挤压方向相反的方向流
动,使挤压的型腔与凸模紧密贴合,型腔轮廓清晰。
简答题
电火花加工特点:
①脉冲放电能量密度高,加工用普通机械难以
18
加工或无法加工的金属材料②加工时工具电极与
工件不直接接触,两者之间不产生明显的机械力
没有因切削力而产生的工艺问题③工具电极的此
阿里不需要比工件硬,能以弱克刚。
电火花加工的工艺指标:
加工速度、加工精度、加工表面质量及
工具电极的相对损耗。
影响电火花加工速度的主要因素:
①电参数②极性效应③工件
材料的热物理常数④工作液⑤其他因
素。
影响电火花加工精度的主要因素:
①放电间隙的大小②工具电
极的损耗③稳定性
影响电火花加工质量的主要因素:
①表面粗糙度②表面变化层(分
凝固层、热影响层)③显微裂纹④
表面层的力学性能
工作液的作用:
①具有介电性②液体介质的绝缘强度比较高,在
较小的电极间隙下击穿,可提高仿形精度③工作
液在脉冲放电作用下,急剧汽化,产生局部高压
有利于电蚀产物排出④工作液压缩火花放电通道,
使放电通道的截面积很小,电流密度很高,提高
生产率和加工精度⑤工作液冷却工具电极和工件,
防止热变形,并传散放电通道中的余热。
电火花成型加工机床组成:
脉冲电源、间隙自动进给调节系统、
19
工作液、循环过滤系统、主机
自动进给调节系统种类组成:
测量环节、比较环节、放大环节、
执行环节。
电火花自动进给调节系统按执行元件大致可分为:
电液压式,
伺服电机式,步进电机式,宽调速
力矩电机式。
工作液循环过滤系统的作用:
采用强迫循环的办法把清洁工作
液由液压泵加压,强迫冲入工具电
极与工件之间的放电间隙,将放电
间隙中的电蚀产物随同工作液一起
从放电间隙中排出,以达到稳定加
工的目的。
电火花穿孔加工加工特点:
①能加工各种高硬度、高强度、高韧
性的金属材料②能有效地加工一般
机械加工难以加工的型孔③加工表
面粗糙度 Ra 可达到 3.2-0.8um,单
面放电间隙为 0.01-0.15um④冲模的
配合间隙均匀,刃口耐磨,提高了
模具质量;而对于复杂的凹模可以
不用镶拼结构,简化了模具结构,
提高了模具强度。
电火花穿孔加工工艺方法