过程三检制度详解及流程模板.docx
《过程三检制度详解及流程模板.docx》由会员分享,可在线阅读,更多相关《过程三检制度详解及流程模板.docx(9页珍藏版)》请在冰豆网上搜索。
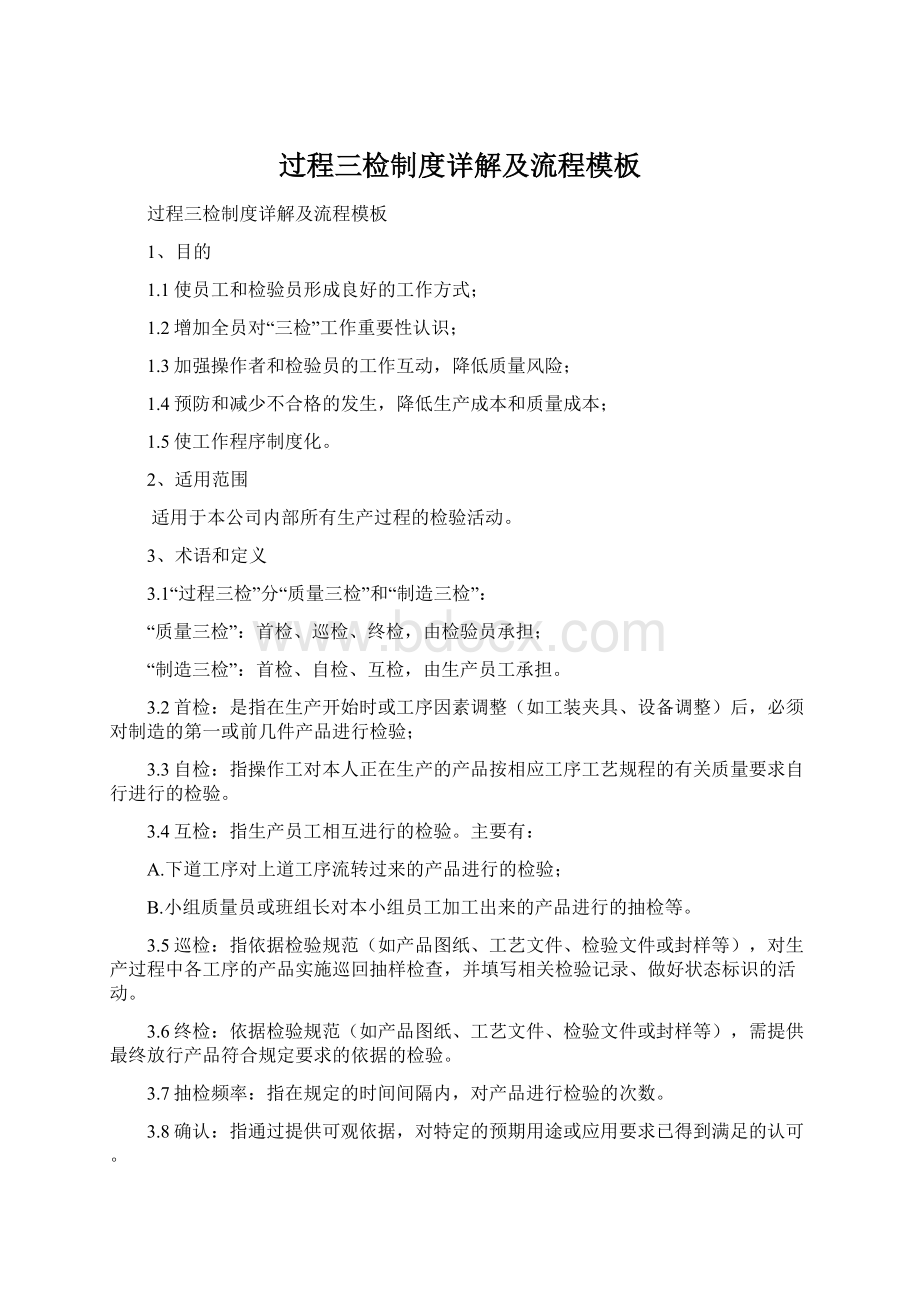
过程三检制度详解及流程模板
过程三检制度详解及流程模板
1、目的
1.1使员工和检验员形成良好的工作方式;
1.2增加全员对“三检”工作重要性认识;
1.3加强操作者和检验员的工作互动,降低质量风险;
1.4预防和减少不合格的发生,降低生产成本和质量成本;
1.5使工作程序制度化。
2、适用范围
适用于本公司内部所有生产过程的检验活动。
3、术语和定义
3.1“过程三检”分“质量三检”和“制造三检”:
“质量三检”:
首检、巡检、终检,由检验员承担;
“制造三检”:
首检、自检、互检,由生产员工承担。
3.2首检:
是指在生产开始时或工序因素调整(如工装夹具、设备调整)后,必须对制造的第一或前几件产品进行检验;
3.3自检:
指操作工对本人正在生产的产品按相应工序工艺规程的有关质量要求自行进行的检验。
3.4互检:
指生产员工相互进行的检验。
主要有:
A.下道工序对上道工序流转过来的产品进行的检验;
B.小组质量员或班组长对本小组员工加工出来的产品进行的抽检等。
3.5巡检:
指依据检验规范(如产品图纸、工艺文件、检验文件或封样等),对生产过程中各工序的产品实施巡回抽样检查,并填写相关检验记录、做好状态标识的活动。
3.6终检:
依据检验规范(如产品图纸、工艺文件、检验文件或封样等),需提供最终放行产品符合规定要求的依据的检验。
3.7抽检频率:
指在规定的时间间隔内,对产品进行检验的次数。
3.8确认:
指通过提供可观依据,对特定的预期用途或应用要求已得到满足的认可。
3.9全尺寸检验:
指对产品在设计记录上标明的所有尺寸进行完整的测量的检验。
4、作业制度
4.1首检制度
4.1.1产品实现中的首检,分为员工首检和检验员首检两种方式。
所在区域的首检必须在1小时内完成。
4.1.2每批次或每工序因素变更后生产的产品,都必须进行首检,首检应在生产员工首检合格后,方可交检验员首检。
对常规批产的产品(PPAP认可后,连续生产5个批次以上、质量稳定、工序批合格率≥90%的产品),如果生产员工首检合格、并按规定提交首检产品后,可以直接进入正常的生产阶段。
4.1.3检验员收到首检产品后,应在1小时内完成检验和确认,并将结果通知生产员工。
4.1.4检验员对检验合格的产品,应打上规定的标志,并保持到本班或本批次产品加工完了为止。
4.1.5员工首检项目仅指在生产现场可以直接检验的项目。
检验员和首检必须对所有要求项目进行检验。
4.1.6首检时,必须按生产工序顺序进行,不得错乱,并确保员工和检验员顺序一致。
同时,不得漏检、误检或不检。
4.1.7生产过程中,只要5M1E(操作者、设备、材料、方法、测量方法和环境)其中任何一个因素发生改变,则需要首检或重新检验。
4.1.8首检活动执行过程中,需做好书面的检验记录,每件产品的所有测量值应记录其中。
首检记录表应保留一份在生产现场指定的位置,以便随时核查和追查原因,直至首件发生改变为止。
4.1.9若员工首检不合格,必须立即送检验员首检并采取措施纠正,纠正到位后重新首检;检验员首检不合格时,员工应立即将已产产品隔离并全检,并采取纠正措施,确保已生产件合格或状态明确,直至首检交检验合格后方可继续生产。
4.1.10判定为合格的首检必须存放在首检区域,直至生产完成或突发性改变,产品方可取走。
4.2、自检制度
4.2.1员工应该按工艺卡等相关文件规定的频率实施自检,不得漏检或不检。
4.2.2当工艺卡没有对自检频率作出规定时,自检频率不得少于4次/班,且间隔大致相等。
4.2.3自检中,如果发现不合格,应立即停止生产,并按照时间段对产品实施全检,全检完毕后,针对不合格原因实施纠正,确认无异常后,方可继续生产。
4.2.4所有产品的外观,员工必须全部检查,保证其处于合格状态。
4.2.5自检中,必须留下记录,但可不必记录具体数据。
4.3巡检制度
4.3.1检验员应按检验文件规定的要求和频率,严格执行巡回检验,不得漏检、误检或不检。
4.3.2当检验文件没有对巡检频率作出规定时,巡检频率每班次、每工序不得少于4次,且间隔大致相等。
4.3.3员工生产时,必须按照时间顺序依次将产品排列整齐,不得混乱,以免影响巡检的质量和效果,同时便于保持对产品的追溯。
4.3.4巡检过程中,若发现不合格,检验员应立即通知操作人员,对发现的不合格产品进行标识和隔离。
分析原因和采取纠正、预防措施。
员工需针对不合格项目实施全检。
全检后,检验员必须及时对全检出的合格品和不合格品进行抽检,若抽检不合格,则员工应再次全检,直至检验员抽检合格为止。
在全检过程中,不得继续生产。
不合格品须经返工、返修合格后方可转序。
4.3.5在巡检过程中发现产品不符合要求、巡检员无法分析和处理的,应立即向车间主任或本部门主管报告,车间主任或质量部主管人员应及时分析原因并采取纠正、预防措施。
4.3.6所有巡检应当场留下检验记录。
保存数据,以便随时核查、追溯和查找原因。
4.3.7生产现场必须有合格品、不合格品的指定位置,方便对相应产品状态的存放,以免混乱和重复检验。
4.4互检制度
4.4.1生产过程中,下道工序应结合本工序的工作内容,对上道工序的产品进行检验。
4.4.2生产过程中,生产班组长应对下属员工的产品质量进行抽检。
4.4.3互检中发现的不合格,应及时通知上道工序进行纠正,并报告上道工序带班班长。
4.4.4接到互检不合格通知后,操作员应根据不合格原因,对已经生产的产品进行全检或挑选,确保产品处于合格状态。
4.4.5互检发现的不合格,应在原因查明、纠正措施到位后,方可继续生产。
4.5终检制度
4.5.1产品完工后,最终工序带班班长或授权人员应对完工产品进行自检,确认合格后提交检验员进行终检。
4.5.2检验人员依据检验规程,需对完工产品进行最终检验,并记录检验结果。
产品的装配尺寸、外形尺寸、密封性能和外观质量应作为必检项目。
4.5.3对检验合格的最终产品,检验员应加盖合格标识或印迹,并在流程卡上签字确认。
终检不合格的产品,应标明不合格原因,并通知车间进行隔离和处置。
4.5.4经返工、返修后的最终产品,必须经检验员复检合格、加盖合格标识后,方能办理入库手续。
4.5.5终检判定不合格的最终产品,分清原因和责任后,报公司统一处理。
5、管理制度
5.1生产过程中,应主观原因造成的经济损失,参照公司《员工手册》中的相关条款进行承担。
5.2若在自检或巡检中,发现重大疑问或问题时,员工或检验员应对首检合格的首检进行确认。
若确认为不合格,则重新首检。
涉及的经济损失和成本,应由检验员和员工共同承担。
检验员70%,员工30%。
5.3员工首检合格后,转让正常生产,但经检验员首检时发现不合格,则已加工不合格的损失应由员工全部承担。
5.4若因为没有巡检、自检或没按照要求巡检、自检,而连续出现不合格时,其产生的经济损失应由检验员和员工共同承担,检验员60%,员工40%。
5.5若出现批量不合格,原因已查明的,由责任人按责任大小承担相应损失。
责任不明白的,由检验员和员工各自承担40%,相关管理人员承担20%。
5.6生产过程中检验员已经发现问题并通知了员工,而员工没有及时采取纠正措施的,检验员应及时通知上级,所造成的不合格损失全部由员工承担。
5.7若员工未按操作规程等标准要求进行生产,检验员有权拒绝首检或巡检,并通知车间进行教育处罚。
5.8生产过程中,因主观原因造成的经济损失未列入本章条款的,由制造部负责查明原因、分清责任,提出处理意见,报公司批准后执行。
6.相关记录
6.1首检记录单
6.2自检记录单
6.3巡检记录单
6.4终检记录单
6.5纠正/预防措施报告
首件检查管理流程模板
质量自检管理流程模板
质量互检管理流程模板
质量巡检管理流程模板
质量专检管理流程模板