疲劳分析流程fatigue.docx
《疲劳分析流程fatigue.docx》由会员分享,可在线阅读,更多相关《疲劳分析流程fatigue.docx(25页珍藏版)》请在冰豆网上搜索。
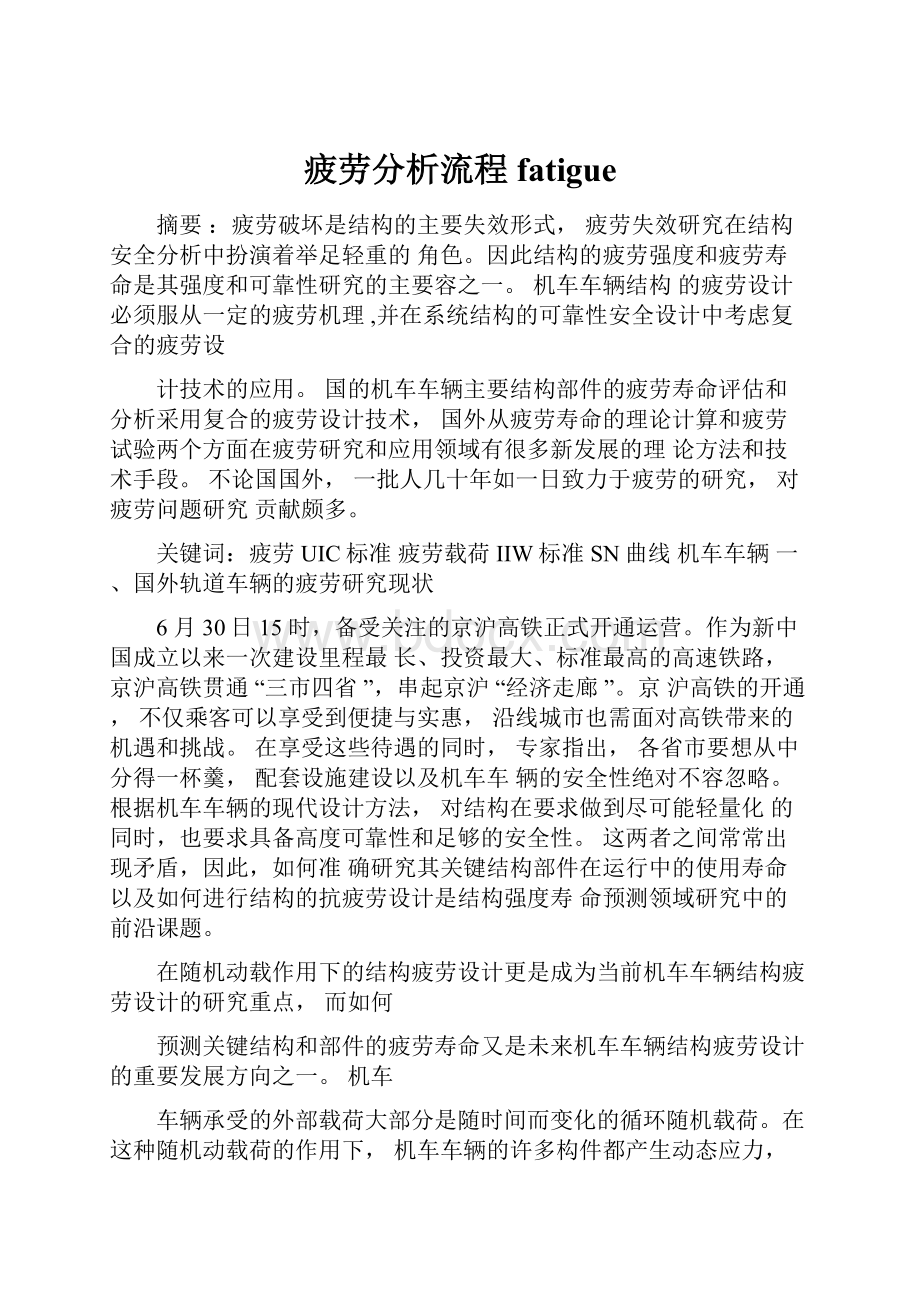
疲劳分析流程fatigue
摘要:
疲劳破坏是结构的主要失效形式,疲劳失效研究在结构安全分析中扮演着举足轻重的角色。
因此结构的疲劳强度和疲劳寿命是其强度和可靠性研究的主要容之一。
机车车辆结构的疲劳设计必须服从一定的疲劳机理,并在系统结构的可靠性安全设计中考虑复合的疲劳设
计技术的应用。
国的机车车辆主要结构部件的疲劳寿命评估和分析采用复合的疲劳设计技术,国外从疲劳寿命的理论计算和疲劳试验两个方面在疲劳研究和应用领域有很多新发展的理论方法和技术手段。
不论国国外,一批人几十年如一日致力于疲劳的研究,对疲劳问题研究贡献颇多。
关键词:
疲劳UIC标准疲劳载荷IIW标准SN曲线机车车辆一、国外轨道车辆的疲劳研究现状
6月30日15时,备受关注的京沪高铁正式开通运营。
作为新中国成立以来一次建设里程最长、投资最大、标准最高的高速铁路,京沪高铁贯通“三市四省”,串起京沪“经济走廊”。
京沪高铁的开通,不仅乘客可以享受到便捷与实惠,沿线城市也需面对高铁带来的机遇和挑战。
在享受这些待遇的同时,专家指出,各省市要想从中分得一杯羹,配套设施建设以及机车车辆的安全性绝对不容忽略。
根据机车车辆的现代设计方法,对结构在要求做到尽可能轻量化的同时,也要求具备高度可靠性和足够的安全性。
这两者之间常常出现矛盾,因此,如何准确研究其关键结构部件在运行中的使用寿命以及如何进行结构的抗疲劳设计是结构强度寿命预测领域研究中的前沿课题。
在随机动载作用下的结构疲劳设计更是成为当前机车车辆结构疲劳设计的研究重点,而如何
预测关键结构和部件的疲劳寿命又是未来机车车辆结构疲劳设计的重要发展方向之一。
机车
车辆承受的外部载荷大部分是随时间而变化的循环随机载荷。
在这种随机动载荷的作用下,机车车辆的许多构件都产生动态应力,引起疲劳损伤,而损伤累积后的结构破坏的形式经常是疲劳裂纹的萌生和最终结构的断裂破坏。
随着国铁路运行速度的不断提高,一些关键结构部件,如转向架的构架、牵引拉杆等都出现了一些断裂事故。
因此,机车车辆的结构疲劳设计已经逐渐成为机车车辆新产品开发前期的必要过程之一,而通过有效的计算方法预测结构的疲劳寿命是结构设计的重要目标。
1.1国外早在十九世纪后期德国工程师Wohler系统论述了疲劳寿命和循环应力的关系并提出了S-N曲线和疲劳极限的概念以来,国外疲劳领域的研究已经产生了大量新的研究方法和研究成果。
结构疲劳设计中主要有两方面的问题:
一是用一定材料制成的构件的疲劳寿命曲线;二是结
构件的工作应力谱,也就是载荷谱。
载荷谱包括外部的载荷及动态特性对结构的影响。
根据疲劳寿命曲线和工作应力谱的关系,有3种设计概念:
静态设计(仅考虑静强度);工作应力须低于疲劳寿命曲线的疲劳耐久限设计;根据工作强度设计,即运用实际使用条件下的载荷谱。
实际载荷因为受到车辆等诸多因素的影响而有相当大的离散性,它严重地影响了载荷谱的最大应力幅值、分布函数及全部循环数。
为了对疲劳寿命进行准确的评价,必须知道设计谱的存在概率,并且考虑实际载荷离散性,才可以确定结构可靠的疲劳寿命。
20世纪60年代,世界上第一条高速铁路建成,自那时起,一些国外高速铁路发达国家已经深入研究机车车辆结构轻量化带来的关键结构部件的疲劳强度和疲劳寿命预测问题。
其中,包括日本对车轴和焊接构架疲劳问题的研究;法国和德用试验台仿真和实际线路相结合的技术开发出试验用的机车车辆疲劳分析方法;英国和美国对转向架累计损伤疲劳方面的研究等等。
在这些研究中提出了大量有效的疲劳寿命的预测研究方法。
1.2、国
1.2.1国疲劳研究现状与方法国铁路相关的科研院所对结构的疲劳寿命也展开了大量的研究和分析,并且得到了很多研究寿命预测方法的有效成果。
疲劳寿命的估算主要分为裂纹形成阶段寿命估算和裂纹扩展阶段寿命估算两部分。
常用的疲劳寿命计算方法包括名义应力寿命法、局部应变寿命法和裂纹扩展计算法。
I.S—N方法
名义应力法,又称S—N方法,强调了长疲劳寿命和耐久性的限制,或者是假定疲劳失效不会发生时的安全应力。
它以材料或零部件的疲劳寿命曲线为基础,利用名义应力或局部应力和寿命之间的关系,主要应用在线性弹性应力的分析中。
S—N曲线也称作应力循环曲线,是说明结构疲劳过程的重要方法。
这个方法经常被用在变化的环境里,包括那些几乎没有塑性的长寿命疲劳问题,以及部件裂纹的萌生或裂纹的生长等问
题。
同时,该法主要应用在循环载荷是弹性的环境里,也就是意味着结构限制在寿命轴的疲劳
循环数量必须大于10000次,这也是为了确保结构没有大的塑性发生。
实际上在小于10000
次循环的环境,要使用S-N方程必须更加小心。
通常要使用最终的强度或者是真实的断裂应力进行分析。
应力法以循环应力作为造成疲劳的原因,寿命的预测主要是应力—循环曲线
(S—N曲线)。
它是由常幅加载试验获得的,尽管大部分情况中实际工程结构承受的多是变幅
载荷,但在疲劳寿命的估算,依然有一定的应用价值。
如果是变幅载荷,需要做出S—N曲线进
行修正。
变化的应力时间历程一般要进行计数,用累积频次分布的形式进行寿命的预测计算。
经常使用如下的公式表示整条S—N曲线:
(&A)mN=D或b=A(1+C/N)
式中:
1/m为S—N曲线的负斜率;A为材料的疲劳极限;D为材料常数;aS—N曲线的负斜率;C为材料常数。
n.E—N方法
局部应变法(也称E—N法)以局部应变为基准,局部应变或应变寿命法,通常参考裂纹萌生方法,其关注的仅仅是裂纹的萌生;结构的疲劳寿命,通常是所有的寿命(S—N或者名义应变),以及裂纹的产生或损伤误差分析之和,关注的是直到结构断裂产生的循环数。
E—N分析法使用循环应力一应变建模和Neuber弹塑性修正。
可以选择分析参数的围,包括平均应力修正模型、置信度参数、制造的细节(表面的粗糙度)以及材料的热处理。
川.裂纹扩展方法
Paris最早提出的裂纹前沿应力强度因子围AK和裂纹扩展速率da/dN之间的经验关系是计算
疲劳裂纹扩展寿命的基础[8]。
基于断裂力学的裂纹扩展寿命预测法主要用于较长裂纹的损伤容限设计,最近这种方法有被拓展到结构耐久性分析领域的趋势。
利用不同技术的这几种方法有不同的精度。
实际上预测总的寿命、裂纹萌生和裂纹扩展3
种方法很少在相同的问题上同时使用。
这是因为不同的设计理念决定了不同的分析方法。
利用这3种基本方法可以分析结构的点焊、缝焊等多种焊接方式,以及旋转结构、振动疲劳、
复合多轴等疲劳寿命的预测问题。
1.2.2国近期疲劳研究领域的发展与突破近年来,随着疲劳理论研究的进步和计算机软硬件技术的迅猛发展,在发达国家的铁路行业,产品的强度设计由原来的主要依据静强度指标和无限寿命设计发展到定量寿命设计,大大提
高了产品的使用可靠性,并且降低了产品的生产成本。
现代的抗疲劳设计中使用了“一体化
耐久管理”(IDM——IntegratedDurablityManagement)的方法,该方法包括虚拟分析和疲劳试验两个方面,下面将从这两个方面分别叙述疲劳研究和应用的新发展。
1、理论分析方法的发展——虚拟计算
所谓的“虚拟”计算就是在产品的设计阶段,使用软件建立产品有关承载构件的有限元模型,使用软件在虚拟的“新产品构件”上施加载荷进行寿命的计算并可反复调整设计方案,这种计算所需时间短,费用低,降低了产品开发周期和成本。
由于疲劳理论的发展结合计算机技术的进步.虚拟计算作为一种分析手段,也有很多新而且方便实用的方法。
主要包括3个方面,
它们分别是用S—N方法估算全寿命、用局部应力一应变估算裂纹起始寿命、用Paris公式估
算裂纹扩展寿命。
1使用PSD功率谱密度信号计算构件的全寿命
传统上人们都是使用时域信号进行寿命或损伤的计算,时域信号一般是应力、应变或载荷。
在时域中可以很方便地表示周期性的信号,若用来完全地描述一个随机过程,需要非常长的信号记录,特别是对于有上个节点的有限元模型施加几十个通道的载荷的情况下,使用时域
信号计算模型的寿命将非常困难,在这种情况下,疲劳寿命的计算可以在频域里完成。
其主要过程是:
首先对有限元模型进行频响分析,求得载荷与结构上应力的传递函数;然后,将传递函数乘以载荷的功率谱密度函数得到应力功率谱密度函数}最后使用有关的方法由应力
功率谱推算结构的寿命。
[9]
用应力PSD信号计算构件的寿命的方法有2种:
其一是直接使用PSD信号;其二是先根据
PSD信号计算出应力围的循环数,再用它估算寿命。
目前,第2种做法使用较为流行。
2预测多轴应力状态下构件的起始寿命
多数情况下,工程构件所受的载荷是多载荷的复杂组合。
这就使得构件上的某些点所受的3
个主应力处于非比例状态.主应力的方向往往也随时变化,在这种应力条件下的疲劳就称为多轴疲劳。
多轴疲劳的研究最近也有了新的进展,发展了一种新方法。
该方法不仅能够估算多轴应力情况下的寿命,还能够以损伤极坐标图的形式给出各个临界面上的损伤量。
用这一方法来估算
始裂寿命分以下几步:
第一步,在承载构件上的关键点贴上应变花测得3个应变输出,或者在有限元模型上贴虚拟应变花,求得3个虚拟的应变输出;第二步,根据3个应变输出用Mroz—Garud循环塑性模型计算该关键点的其余的应力应变分量;第三步,根据材料的疲劳寿命曲线,用有关的多轴疲劳损伤寿命模型计算寿命。
[10]
3预测形状不规则裂纹的扩展寿命
最近,有一种计算形状不规则裂纹的扩展寿命的新方法得到了发展,该方法是线弹性断裂力
学理论与有限元方法的结合。
其主要容是首先对含裂纹的构件进行三维有限元网格的划分,网格包括裂纹块和非裂纹块,裂纹块由于包含裂纹需要较细致的划分,而非裂纹块可以划分得较粗一些。
裂纹块和非裂纹块的组合可以使用多点位移约束法,使得二者的位移在其接触面上保持一致,从而使组合后的网格保持变形协调。
疲劳裂纹扩展后新网格的生成可以只对裂纹块进行,非裂纹块阿格保持不变。
网格划分完毕后,应用四分之一点位移法或者三维J积分法计算裂纹扩展前沿上的各个节点
的应力强度因子,J积分的计算方法有回路法和虚拟节点位移法。
裂纹前沿的曲线形状可以由一些离散点(节点)来定义,那么,就可以应用Paris公式分别求这些节点上的裂纹扩展量(也
就是这些节点的位移量)△,据此可以确定新的裂纹前沿。
该方法能够模拟裂纹扩展过程,跟踪裂纹形状的发展变化,大大提高了裂纹扩展寿命的预测精度。
2、疲劳试验使用软件来仿真计算虚拟“新产品”作为抗疲劳设计的一个手段,并不能代替疲劳试验,虚拟计算的目的是为了尽可能地减少疲劳试验的次数。
新产品的疲劳可靠性最终要通过疲劳试验来检验,目前国对铁道车辆零部件的疲劳试验,只能够做程序加载的疲劳试验。
如TB1959
和TB1960所规定的试验标准,用程序载荷谱加载的疲劳试验一般只能够对产品进行合格检验或产品的性能对比,不能够真正用于研究产品的寿命。
在国外,主要采用随机载荷谱加载进行疲劳试验来研究产品的寿命这样就彻底消除了程序载荷谱时高低载荷的加载次序和各加载位置载荷相位差对构件寿命的影响。
这种加载方法能够较为真实地模拟构件所承受的载荷,使所得的试验寿命能够真实地反映运用寿命在各个构件之间布置载荷传感器十分困难,而在构件上贴上应变片则很方便,所以一般不能直接采集到构件的随机载荷谱,只能够采集
到构件上某些点的应变谱。
从运用当中的构件上采集的应变谱若直接用于疲劳试验,虽然试验寿命最为接近实际的运用寿命,但试验的时间将与构件的实际运用时间相当,疲劳试验就失去了其意义。
所以,要对采集的应变谱进行一些编辑处理。
合理的疲劳编辑应该满足2个方面,其一是经过编辑后的信号与原始信号对构件的总损伤基本一致;其二是编辑前后的信号所产主的损伤分布基本一致。
过去,用线性放大载荷信号或者用“等效”的常幅载荷信号来加速疲劳试验的做法,不符合上面所提的第2个方面疲劳试验有单通道和多通道之分,疲劳编辑也有所区别.单通道编辑只编辑响应信号(应变谱),多通道编辑需要同步编辑响应信
号(应变谱)和驱动信号(随机载荷谱)。
二、CW-200转向架疲劳寿命预测实例图1是转向架焊接构架待评估位置:
图1CW-200转向架焊接构架待评估位置
2.1有限元模型
图2是CW-200转向架有限元模型
图2CW-200转向架有限元模型
有限元模型采用平面四节点单元,单元大小20mm。
疲劳试验载荷包括垂向载荷与横向载荷,垂向载荷作用在空气弹簧座上,横向载荷作用在横向减振器座上。
2.2疲劳试验载荷根据UIC标准:
――垂直力(每个侧架)(取a=0.23=0.1)
静态部分:
FZS1=FZS2=FZ准静态部分(模拟曲线中的滚动):
FZQ1=FZQ2=+-aFZ
动态部分(跳动模拟):
FZD1=FZD2=+-3FZ
——横向力(每个转向架)
准静态部分:
FYQ=+-0.25*(FZ+0.5*m+*g)动态部分:
FYD=+-0.25*(FZ+0.5*m+*g)其中,FZ=135KNm+*g=60KN
图13-UIC标准中垂向动载荷模式
图14-UIC标准中横向动载荷模式
由于产生疲劳破坏的主要为动态部分力,所以在疲劳评估时忽略静态部分和准静态部分对疲劳寿命的影响,所以需加的疲劳载荷为:
垂直力(每个侧架):
△FZ=2*(0.2*135)=54KN
横向力(每转向架):
△FY=2*[0.25*(135+0.5*60)]=82.5KN
在UIC标准中,加载分三个阶段,分别以1倍、1.2倍和1.4倍的比例关系逐段强化,每个阶段加载的循环次数分别为6e106、2e106和e106次。
图15-UIC标准中三段加载模式垂向力动态部分与横向力动态部分作用频率与相位均相同,因而视其为一个载荷事件。
2.3有限元计算
按照《UIC515-4》的实验室疲劳实验加载要求,首先将其静载到要有限元模中,然后基于动载
与静载的比例关系进行应力换算,即得动载应力厶6(任一点的Ac值都可由下图读出)
图3是部分有限元计算结果:
图3—疲劳载荷作用下应力云图
2.4S-N曲线选取
将待评估点所处的结构细部与IIW标准钢结构细部疲劳强度值表中提供的结构细部对比,选
择合适的类型FAT级别。
CW-200转向架构架各点的疲劳强度级别FAT值列入下表:
表1待评估位置FAT等级列表
编号
1
2
3
4
5
6
7
8
9
10
11
12
13
14
15
接头
管接
管接
T型
管接
T型端部
管接端部对接对接
T型
非承
载T接
头
T型
管
接
头
T型
类型
头
头
接头
头
接头接头
头
接头
接头
接头
接头
接头
接头
FAT
50
50
80
50
80
45
50
45
71
71
80
100
80
50
80
根据各点的疲劳强度级别FAT值,即可在IIW标准中(表2)查找相应的SN曲线参数,即m、
C值。
表2IIW标准中各级别S-N曲线参数(MPa)
Palmgren-Miner累积特征抗疲劳-SN曲线的修正值
最初斜率m仁3.0,循环数5e6时的常幅疲劳极限—l,x
次斜率m2=5.0,在106循环时截止
级别
循环数N<5e6,m仁3时S-N
曲线的常数C
常幅疲劳极限
循环数N>5E6,m2=5时
SN曲线的常数C
截止极限
255
2.27e13
166
6.261e17
91.1
200
1.600e13
147
3.474e17
80.9
180
1.166e13
133
2.052e17
72.8
160
8.192e12
118
1.139e17
64.8
140
5.488e12
103
5.840e16
56.7
125
3.906e12
92.1
3.313e16
50.6
112
2.810e12
82.5
1.913e16
45.3
100
2.000e12
73.7
1.086e16
40.5
90
1.458e12
66.3
6.411e15
36.4
80
1.012e12
58.9
3.558e15
32.4
71
7.158e11
52.3
1.959e15
28.7
63
5.001e11
46.4
1.078e15
25.5
56
3.512e11
41.3
5.980e14
22.7
50
2.500e11
36.8
3.393e14
20.2
45
1.823e11
33.2
2.004e14
18.2
40
1.280e11
29.5
1.112e14
16.2
36
9.331e10
26.5
6.565e13
14.6
32
6.554e10
23.6
3.643e13
13.0
28
4.390e10
20.6
1.869e13
11.3
25
3.125e10
18.4
1.060e13
10.1
22
2.130e10
16.2
5.596e12
8.9
20
1.600e10
14.7
3.474e12
8.1
18
1.166e10
13.3
2.052e12
7.3
16
8.192e9
11.8
1.139e12
6.5
14
5.488e9
10.3
5.840e11
5.7
然后就可以根据迈纳尔损伤累积理论计算疲劳寿命,这里为疲劳损伤比之和。
疲劳寿命极限;(对应i)
累计损伤率D=
计算结果列表如下:
表3CW-200焊接构架待评估点疲劳损伤比之和
标号
FAT
垂向+横向
1倍(加载6e6次)
1.2倍(加载2e6次)
1.4倍(加载2e6次)
应力围
2.5
3
3.5
SN曲线
m无C无
m无C无
m无C无
1
50疲劳寿命
无限
无限
无限
损伤比
0
0
0
累积损伤比
0
应力围
11.2
13.44
15.68
SN曲线
m无C无
m无C无
m=无C无
2
50疲劳寿命
无限
无限
无限
损伤比
0
0
0
累积损伤比
0
应力围
9.9
11.88
13.86
SN曲线
m无C无
m无C无
m无C无
3
80疲劳寿命
无限
无限
无限
损伤比
0
0
0
累积损伤比
0
应力围
16.1
19.32
22.54
SN曲线
m无C无
m无C无
m无C无
4
50疲劳寿命
无限
无限
无限
损伤比
0
0
0
累积损伤比
0
应力围
41.6
49.92
58.24
SN曲线
m=5C=3.558e15
m=5C=3.558e15
m=5C=3.558e15
5
80疲劳寿命
2.86e7
1.15e7
5.31e6
损伤比
0.21
0.174
0.377
累积损伤比
0.761
应力围
18.8
22.56
26.32
SN曲线
m=5
C=2.004e14
m=5C=2.004e14
m=5
C=2.004e14
6‘
45
疲劳寿命
8.53e7
3.43e7
1.59e7
损伤比
0.07
0.058
0.126
累积损伤比
0.254
应力围
3.1
3.72
4.34
SN曲线
m无
C无
m无
C无
m无
C无
7
50
疲劳寿命
1.58e3
无限
无限
损伤比
0
0
0
累积损伤比
0
应力围
6.6
7.92
9.24
SN曲线
m无
C无
m无
C无
m无
C无
8
45
疲劳寿命
无限
无限
无限
损伤比
0
0
0
累积损伤比
0
应力围
7.3
8.76
10.22
SN曲线
m无
C无
m无
C无
m无
C无
9
71
无限
无限
无限
疲劳寿命
损伤比
0
0
0
累积损伤比
0
应力围
11.0
13.2
15.4
SN曲线
m无
C无
m无
C无
m无
C无
10
71
疲劳寿命
无限
无限
无限
损伤比
0
0
0
累积损伤比
0
应力围
26.5
31.8
37.1
SN曲线
m无
C无
m无
C无
m=5
C=3.558e15
无限
无限
5.06e7
11
80
疲劳寿命
损伤比
0
0
0.04
累积损伤比
0.04
应力围
37.2
44.64
52.08
SN曲线
m无
C无
m=5C=1.086e16
m=5
C=1.086e16
无限
6.13e7
2.83e7
12
100
疲劳寿命
损伤比
0
0.033
0.071
累积损伤比
0.104
应力围
7.27
8.724
10.178
SN曲线
m无
C无
m无
C无
m无
C无
无限
无限
无限
13
80
疲劳寿命
损伤比
0
0
0
累积损伤比
0
应力围
8.27
9.924
11.578
SN曲线
m无
C无
m无
C无
m无
C无
14
50疲劳寿命
无限
无限
无限
损伤比
0
0
0
累积损伤比
0
应力围
4.20
5.04
5.88
SN曲线
m无
C无
m无
C无
m无
C无
15
80疲劳寿命
无限
无限
无限
损伤比
0
0