插板底座注塑模具设计与制造说明书.docx
《插板底座注塑模具设计与制造说明书.docx》由会员分享,可在线阅读,更多相关《插板底座注塑模具设计与制造说明书.docx(38页珍藏版)》请在冰豆网上搜索。
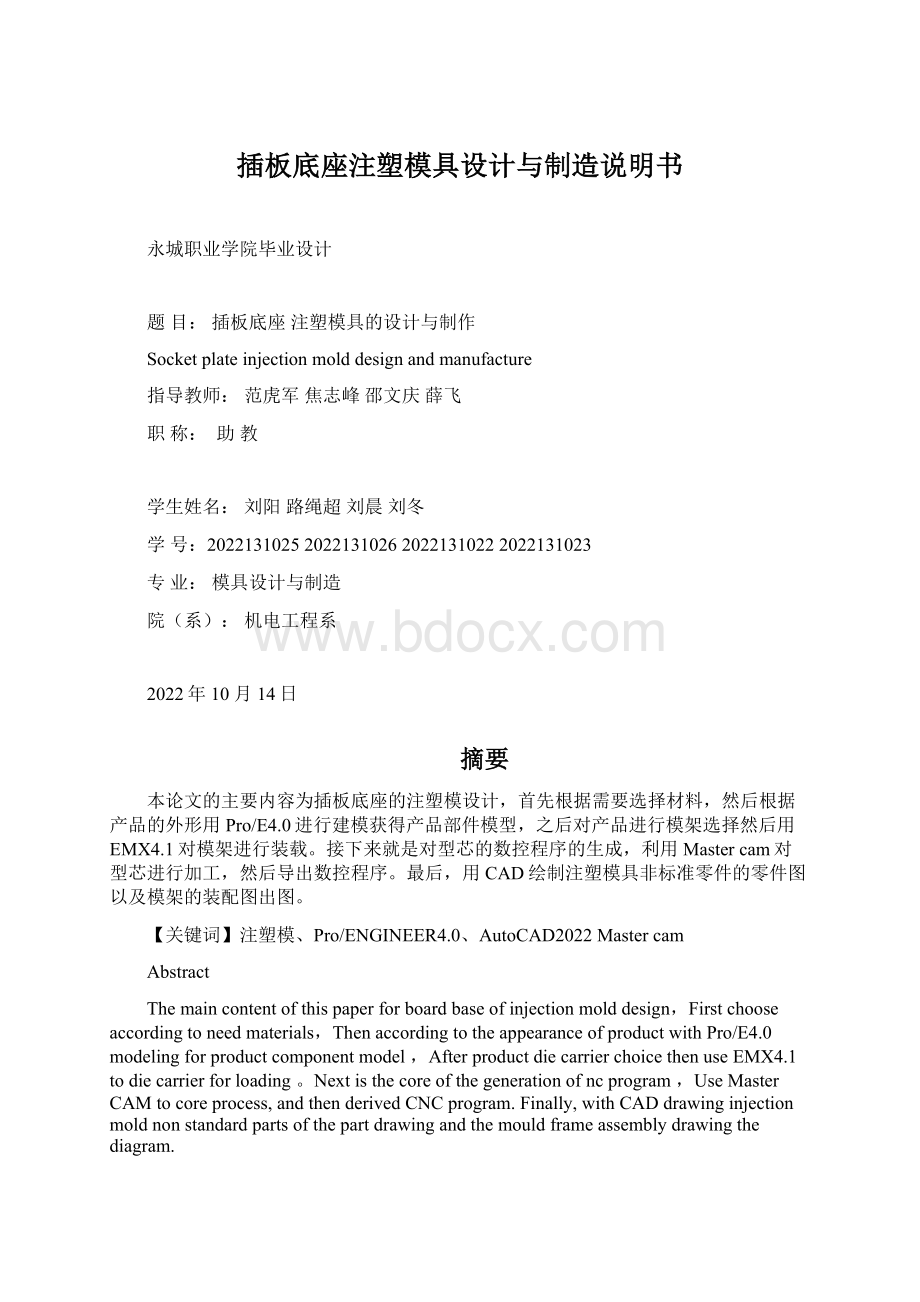
插板底座注塑模具设计与制造说明书
永城职业学院毕业设计
题目:
插板底座注塑模具的设计与制作
Socketplateinjectionmolddesignandmanufacture
指导教师:
范虎军焦志峰邵文庆薛飞
职称:
助教
学生姓名:
刘阳路绳超刘晨刘冬
学号:
2022131025202213102620221310222022131023
专业:
模具设计与制造
院(系):
机电工程系
2022年10月14日
摘要
本论文的主要内容为插板底座的注塑模设计,首先根据需要选择材料,然后根据产品的外形用Pro/E4.0进行建模获得产品部件模型,之后对产品进行模架选择然后用EMX4.1对模架进行装载。
接下来就是对型芯的数控程序的生成,利用Mastercam对型芯进行加工,然后导出数控程序。
最后,用CAD绘制注塑模具非标准零件的零件图以及模架的装配图出图。
【关键词】注塑模、Pro/ENGINEER4.0、AutoCAD2022Mastercam
Abstract
Themaincontentofthispaperforboardbaseofinjectionmolddesign,Firstchooseaccordingtoneedmaterials,ThenaccordingtotheappearanceofproductwithPro/E4.0modelingforproductcomponentmodel,AfterproductdiecarrierchoicethenuseEMX4.1todiecarrierforloading。
Nextisthecoreofthegenerationofncprogram,UseMasterCAMtocoreprocess,andthenderivedCNCprogram.Finally,withCADdrawinginjectionmoldnonstandardpartsofthepartdrawingandthemouldframeassemblydrawingthediagram.
【Keywords】
Injectionmold,Pro/ENGINEER4.0,EMX4.1,AutoCAD2022
1.前言
随着塑料工业的迅速发展,对塑料模具设计和制造技术的要求也越来越高,传统的塑料模具设计及制造技术已经无法适应当今的要求。
在注塑产品的开发过程中,模具的设计和制造决定了塑料件的最终质量和成本。
而Pro/E在注塑模具设计中的应用,为高质量模具的设计和制造提供了一条途径,使当前模具设计及制造技术呈现出新的特征,大大提高模具的制造效率和质量。
这对提高新产品开发速度作用十分的突出。
在现在工业生产中,模具是重要的工艺装配之一,它在铸造、锻造、塑料、冲压、粉末冶金,陶瓷制品等生活生产行业中得到广泛应用。
由于采用模具能提高生产效率、节约材料、降低成本,,并且可以保证一定的加工质量要求,所以,汽车、飞机、拖拉机电器、仪表、玩具和日常用品等产品的零部件很多都采用模具加工。
随着工业科学技术的工业产品的品种和数量不断增加,产品的改性换代加快,对产品质量、外观不断提出新的要求,对模具质量的要求也越来高,因此,模具设计与制造技术在国民经济中的地位是显而易见的。
2.塑件的结构及工艺分析
2.1塑件结构分析
制件的总体形状为长方体结构零件,如图1示:
图1
1.制件总体结构为长方体薄壳类产品,基本尺寸为180mm×51mm×15mm,厚度为2mm,一段有一个基本尺寸为30mm×10mm,厚度为30mm的长方体螺钉固定凸台,螺钉孔直径为5mm.4mm,其中ø5圆台向下凹1mm,另一端有一直径为8mm,12mm,和15mm厚度为2mm,长为4mm半圆形线孔,其侧有一长方体25mm×9mm的凹台,向下凹3mm,厚度为2mm,盒盖四周各有一个直径为8mm,高为8mm和长直径为6mm,高为2mm,相接的圆柱凸台其厚为2mm,盒盖内部两侧各有4个长为5mm,高为12mm,厚为2mm的三角形加强筋,内部有两个高12mm×5mm×2mm厚的圆柱孔。
。
制件具体分析如下:
①塑件的尺寸精度
该塑件的要求具有中等精度,外表无瑕疵,美观,性能可靠,重要的尺寸有180mm,51mm,15mm,查表3-1[1]可知精度为MT3级,次重要尺寸乳30mm,10mm等,精度为MT5级标注。
②塑件的表面粗糙度
查表3-3可知,ABS注射成型时,表面粗糙的范围为Ra0.2-32um,而该表面粗糙应较为高,取为Ra0.4um。
③脱模斜度
查表3-4可知,材料为ABS的塑件,其型腔脱模斜度一般为40′-1°20′,型芯脱模斜度为40′-1°20′。
而该塑件为长方体结构,故型腔脱模斜度为1°,型芯脱模斜度为1°。
④壁厚
塑件整体厚度为2mm。
⑤加强筋
因该塑件长度较大,且为薄壁塑件,强度不足,需设计加强筋。
⑥圆角
该塑件内、外表面及四周各有圆角,有利于塑件的成型。
⑦侧孔和凸台
该塑件一端螺钉定位凸台有两个定位孔,另一端有线孔,其端有一长方形凹块。
金属嵌件
该塑件无金属嵌件。
螺纹、自攻螺纹孔
该塑件的凸凹孔和侧孔皆无螺纹。
铰链
该塑件无铰链结构。
文字、符号及标记
通过上述分析,该塑件结构属于中等复杂结构,结构工艺性合理,不需对塑件的结构进行修改,塑件尺寸中等,对应的模具尺寸加工容易保证,注射时在工艺参数控制的较好的情况下,塑件的成型要求可以得到保证。
2.2塑件制品的工艺分析
ABS树脂是一种共混物,是丙烯腈-丁二烯-苯乙烯共聚物,英文名Acrylonitrile-butadine-styrene(简称ABS),这三者的比例为20:
30:
50(熔点为175℃)。
ABS为浅黄色粒状或珠状不透明树脂,无毒、无味、吸水率低,具有良好的综合物理机械性能,如优良的电性能、耐磨性,尺寸稳定性、耐化学性和表面光泽等,且易于加工成型。
缺点是耐候性,耐热性差,且易燃。
ABS是由丙烯腈、丁二烯和苯乙烯三种化学单体合成。
每种单体都具有不同特性:
丙烯腈有高强度、热稳定性及化学稳定性;丁二烯具有坚韧性、抗冲击特性;苯乙烯具有易加工、高光洁度及高强度。
ABS在比较宽广的温度范围内具有较高的冲击强度,热变形温度比PA、PVC高,尺寸稳定性好,收缩率在0.4%~0.8%范围内,若经玻纤增强后可以减少到0.2%~0.4%,而且绝少出现塑后收缩。
ABS具有良好的成型加工性,制品表面光洁度高,且具有良好的涂装性和染色性,可电镀成多种色泽。
ABS尚具有良好的配混性,可与多种树脂配混成合金(共混物),如PC/ABS、ABS/PC、ABS/PVC、PA/ABS、PBT/ABS等,使之具有新的性能和新的应用领域,ABS若与MMA掺混可制成透明ABS,透光率可达80%。
ABS是吸水的塑料,于室温下,24小时可吸收0.2%~0.35%水分,虽然这种水分不至于对机械性能构成重大影响,但注塑时若湿度超过0.2%,塑料表面会受大的影响,所以对ABS进行成型加工时,一定要事先干燥,而且干燥后的水分含量应小于0.2%。
熔融温度高,需要高料温、高压注射成型;模具流道的阻力应小,模具要加热;塑件易产生内应力,原料要干燥,顶出力要均匀,塑件需要后处理。
本制品为插板底座,要求耐高温,强度和韧性较好,耐磨、耐腐蚀,中等精度,美观、性能可靠。
使用ABS材料,产品的使用性能基本满足要求,但在成型时,要注意选择合理的成型工艺及成型前的干燥处理。
3.确定成型方式及成型工艺流程
3.1塑件成型方式
所生产制品选择ABS工程塑料,属于热塑性塑料,制品需要大批量生产。
虽然注射成型模具结构较为复杂,成本较高,但生产周期短、效率高,容易实现自动化生产,大批量生产模具成本对于单件制品成本影响不大。
而压缩成型、压注成型主要用于生产热固性塑件和小批量生产热塑性塑料;挤出成型主要用以成型具有恒定截面形状的连续型材;气动成型用于生产中空的塑料瓶、罐、盒、箱类塑件。
所以该制件应选择注射成型。
3.2注射成型工艺过程的确定
一个完整的注射成型工艺过程包括成型前准备、注射过程及塑件后处理3个过程。
①.成型前的准备。
a、对ABS原料进行外观检验:
检查原料的色泽、粒度均匀等,要求色泽均匀、细度均匀度。
b、生产开始如需要改变塑料品种、调换颜色,或发现成型过程中出现了热分解或降解反应,则应对注射机料筒进行清洗。
c、为了使塑料制件容易从模具内脱出,模具型腔或模具型芯还需要涂上脱模剂,根据生产现场实际条件选用硬脂酸锌、液体石蜡或硅油等。
②.注射过程一般包括:
加料、塑化、充模、保压补缩、冷却定型和脱模等步骤。
③.塑件后处理。
ABS易产生应力集中,严格控制成型条件,采用以下退火处理工艺。
a、烘箱
把产品放入红外线烘箱里,用烘箱以80~85℃烘2~4小时。
4.确定成型工艺参数并编制成型工艺卡片
采用螺杆式塑料注射机,螺杆转速为30~60r/min。
材料预干燥0.5h以上。
2.温度
料筒前端:
150℃~170℃,料筒中部:
180℃~190℃,料筒后端:
200℃~210℃,喷嘴:
180℃~190℃,模具:
50℃~70℃。
3.压力
注射压力:
60~100MPa,保压压力:
40~60MPa。
4.时间(成型周期)
注射时间:
2~5s,保压时间:
5~10s,冷却时间:
5~15s,成型周期:
15~30s。
5.后处理
方法:
红外线烘箱,温度;70℃~90℃,时间:
0.3~1h。
[1]
该制件的注射成型工艺卡片见下表表1
表1开关注射成型工艺卡片
塑料注射成型
工艺卡片
资料编号
车间
共1页
第1页
零件名称
插座底板
材料定额
设备型号
SYS-30
装配图号
材料牌号
ABS
每模制件数
1件
零件图号
单件质量
9.45g
工装号
材料干燥
设备
红外线烘箱
温度(℃)
70~90
时间(h)
0.3~1
料筒温度(℃)
料筒一区
150~170
料筒二区
180~190
料筒三区
200~210
喷嘴(℃)
180~190
模具温度(℃)
50~70
时间(s)
注射(s)
2~5
保压(s)
5~10
冷却(s)
5~15
压力(MPa)
注射压力
60~100
保压压力
40~60
塑化压力
2~4
后处理
温度(℃)
红外线烘箱70~90
时间额定(min)
辅助(min)
0.5
时间(min)
0.3~1
单件(min)
1~2
检验
编制
校对
审核
组长
车间主任
检验组长
编制
5.模具设计
5.1确定成型工艺设备规格
初选注射机规格通常依据注射机允许的最大注射量、锁模力及塑件外观尺寸等因素确定。
习惯上依据其中一个设计依据,其余都作为校核依据。
通常保证制品所需要注射量小于或等于注射机允许的最大注射量的80%,否则就会造成制品的形状不完整、内部组织疏松或制品强度下降等缺陷;而过小,注射机利用率偏低,浪费电能,而且塑料长时间处于高温状态可导致塑料分解和变质,因此,应注意注射机能处理的最小注射量,最小注射量通常应大于额定注射量的20%。
1单个塑件体积。
V=9(cm³)
2单个塑件质量。
M=Vp=9.45(g