支架零件的工艺规程及钻6Φ17孔的钻床夹具设计.docx
《支架零件的工艺规程及钻6Φ17孔的钻床夹具设计.docx》由会员分享,可在线阅读,更多相关《支架零件的工艺规程及钻6Φ17孔的钻床夹具设计.docx(10页珍藏版)》请在冰豆网上搜索。
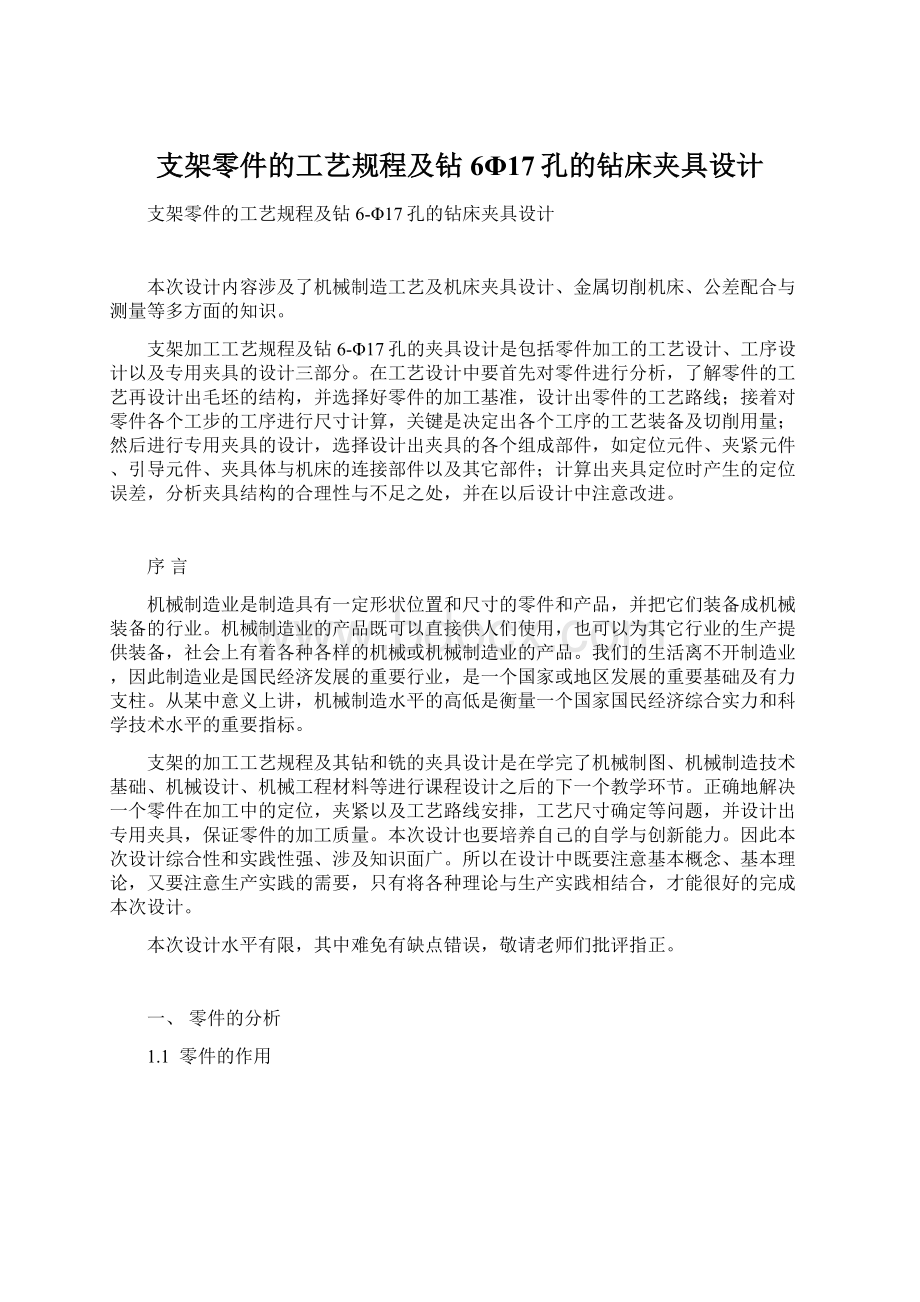
支架零件的工艺规程及钻6Φ17孔的钻床夹具设计
支架零件的工艺规程及钻6-Φ17孔的钻床夹具设计
本次设计内容涉及了机械制造工艺及机床夹具设计、金属切削机床、公差配合与测量等多方面的知识。
支架加工工艺规程及钻6-Φ17孔的夹具设计是包括零件加工的工艺设计、工序设计以及专用夹具的设计三部分。
在工艺设计中要首先对零件进行分析,了解零件的工艺再设计出毛坯的结构,并选择好零件的加工基准,设计出零件的工艺路线;接着对零件各个工步的工序进行尺寸计算,关键是决定出各个工序的工艺装备及切削用量;然后进行专用夹具的设计,选择设计出夹具的各个组成部件,如定位元件、夹紧元件、引导元件、夹具体与机床的连接部件以及其它部件;计算出夹具定位时产生的定位误差,分析夹具结构的合理性与不足之处,并在以后设计中注意改进。
序言
机械制造业是制造具有一定形状位置和尺寸的零件和产品,并把它们装备成机械装备的行业。
机械制造业的产品既可以直接供人们使用,也可以为其它行业的生产提供装备,社会上有着各种各样的机械或机械制造业的产品。
我们的生活离不开制造业,因此制造业是国民经济发展的重要行业,是一个国家或地区发展的重要基础及有力支柱。
从某中意义上讲,机械制造水平的高低是衡量一个国家国民经济综合实力和科学技术水平的重要指标。
支架的加工工艺规程及其钻和铣的夹具设计是在学完了机械制图、机械制造技术基础、机械设计、机械工程材料等进行课程设计之后的下一个教学环节。
正确地解决一个零件在加工中的定位,夹紧以及工艺路线安排,工艺尺寸确定等问题,并设计出专用夹具,保证零件的加工质量。
本次设计也要培养自己的自学与创新能力。
因此本次设计综合性和实践性强、涉及知识面广。
所以在设计中既要注意基本概念、基本理论,又要注意生产实践的需要,只有将各种理论与生产实践相结合,才能很好的完成本次设计。
本次设计水平有限,其中难免有缺点错误,敬请老师们批评指正。
一、零件的分析
1.1零件的作用
支架的作用,待查
1.2零件的工艺分析
支架有3个加工面他们相互之间没有任何位置度要求。
1:
一底面为基准的加工面,这组加工面主要是底面,上表面和6-Φ17的孔,
2:
以Φ17孔为基准的加工面,这组加工面主要是镗Φ50的孔及拉键槽
3.以Φ50孔及键槽定位,铣宽12的槽
二.工艺规程设计
2.1确定毛坯的制造形式
零件材料为45,在工作过程中经常受到冲击性载荷,采用这种材料零件的强度也能保证。
由于零件成批生产,而且零件的轮廓尺寸不大,选用锻造,锻造精度为2级,能保证锻件的尺寸要求,这从提高生产率和保证加工精度上考虑也是应该的。
2.2基面的选择的选择
粗基准选择应当满足以下要求:
(1)粗基准的选择应以加工表面为粗基准。
目的是为了保证加工面与不加工面的相互位置关系精度。
如果工件上表面上有好几个不需加工的表面,则应选择其中与加工表面的相互位置精度要求较高的表面作为粗基准。
以求壁厚均匀、外形对称、少装夹等。
(2)选择加工余量要求均匀的重要表面作为粗基准。
例如:
机床床身导轨面是其余量要求均匀的重要表面。
因而在加工时选择导轨面作为粗基准,加工床身的底面,再以底面作为精基准加工导轨面。
这样就能保证均匀地去掉较少的余量,使表层保留而细致的组织,以增加耐磨性。
(3)应选择加工余量最小的表面作为粗基准。
这样可以保证该面有足够的加工余量。
(4)应尽可能选择平整、光洁、面积足够大的表面作为粗基准,以保证定位准确夹紧可靠。
有浇口、冒口、飞边、毛刺的表面不宜选作粗基准,必要时需经初加工。
(5)粗基准应避免重复使用,因为粗基准的表面大多数是粗糙不规则的。
多次使用难以保证表面间的位置精度。
基准的选择是工艺规程设计中的重要工作之一,他对零件的生产是非常重要的。
先选取64x54的面作为定位基准,。
2.3精基准的选择
精基准的选择应满足以下原则:
(1)“基准重合”原则应尽量选择加工表面的设计基准为定位基准,避免基准不重合引起的误差。
(2)“基准统一”原则尽可能在多数工序中采用同一组精基准定位,以保证各表面的位置精度,避免因基准变换产生的误差,简化夹具设计与制造。
(3)“自为基准”原则某些精加工和光整加工工序要求加工余量小而均匀,应选择该加工表面本身为精基准,该表面与其他表面之间的位置精度由先行工序保证。
(4)“互为基准”原则当两个表面相互位置精度及自身尺寸、形状精度都要求较高时,可采用“互为基准”方法,反复加工。
(5)所选的精基准应能保证定位准确、夹紧可靠、夹具简单、操作方便。
以已经加工好的Φ17孔和一端面为定位精基准,加工其它表面及孔。
主要考虑精基准重合的问题,当设计基准与工序基准不重合的时候,应该进行尺寸换算,这在以后还要进行专门的计算,在此不再重复
2.3制定工艺路线
制订工艺路线的出发点,应当是使零件的几何形状、尺寸精度及位置精度等技术要求能得到合理的保证。
在生产纲领已确定为成批生产的条件下,可以考虑采用万能型机床配以专用夹具,并尽量使工序集中在提高生产率。
除此以外,还应当考虑经济效果,以便使生产成本尽量降下来。
制定以下两种工艺方案:
方案一
工序Ⅰ:
锻造
工序Ⅱ:
退火处理
工序Ⅲ:
铣基准面B
工序Ⅳ:
铣165X180X30的面
工序Ⅴ:
钻6-Φ17孔锪Φ28深16孔
工序Ⅵ:
铣基准面A及其对称面
工序Ⅶ:
镗Φ50孔,拉宽14键槽
工序Ⅷ:
铣宽12的槽
工序Ⅸ:
检验
方案二
工序Ⅰ:
锻造
工序Ⅱ:
退火处理
工序Ⅲ:
铣基准面B
工序Ⅳ:
铣165X180X30的面
工序Ⅴ:
铣基准面A及其对称面
工序Ⅵ:
钻6-Φ17孔锪Φ28深16孔
工序Ⅶ:
镗Φ50孔,拉宽14键槽
工序Ⅷ:
铣宽12的槽
工序Ⅸ:
检验
工艺方案一和方案二的区别在于方案一把钻孔孔放在了前面,这样我们铣面的时间就可以利用钻好的孔做为定位基准。
具体的加工路线如下
工序Ⅰ:
锻造
工序Ⅱ:
退火处理
工序Ⅲ:
铣基准面B
工序Ⅳ:
铣165X180X30的面
工序Ⅴ:
钻6-Φ17孔锪Φ28深16孔
工序Ⅵ:
铣基准面A及其对称面
工序Ⅶ:
镗Φ50孔,拉宽14键槽
工序Ⅷ:
铣宽12的槽
工序Ⅸ:
检验
2.4机械加工余量、工序尺寸及毛坯尺寸的确定
支架材料为45重量为5Kg
生产类型为大批量生产,采用锻造。
1、不加工表面毛坯尺寸
不加工表面毛坯按照零件图给定尺寸为自由度公差,由锻造可直接获得。
2、支架的底面
由于支架底面要与其他接触面接触,同时又是Φ50孔的中心线的基准。
粗糙度要求为2.5,查相关资料知余量留2.5比较合适。
3、支架的孔
锻件为空心,锻造出孔。
孔的精度要求介于IT7—IT8之间,参照参数文献,确定工艺尺寸余量为2.5mm
2.5确定切削用量及基本工时
工序Ⅴ:
钻6-Φ17孔锪Φ28深16孔
工步一:
钻6-Φ17孔
确定进给量:
根据参考文献Ⅳ表2-7,当钢的,时,。
由于本零件在加工Φ17孔时属于低刚度零件,故进给量应乘以系数0.75,则
根据Z525机床说明书,现取
切削速度:
根据参考文献Ⅳ表2-13及表2-14,查得切削速度所以
根据机床说明书,取,故实际切削速度为
切削工时:
,,,则机动工时为
总的工时:
T=6=2.658min
工步二:
锪孔
利用锪孔刀将孔扩大至深16mm,根据有关手册规定,锪孔的切削用量可根据钻孔的切削用量选取
根据机床说明书,选取
则主轴转速为,并按车床说明书取,实际切削速度为
切削工时:
,,,则机动工时为
总的工时:
T=6=3.792min
工序Ⅷ:
铣宽12的槽
加工要求:
用乳化液冷却,加工工件尺寸,宽12-0.0550mm,长L=137mm,加工余量6mm
由于此工步的设计尺寸精度要求不高,一次即可达到要求
选择刀具:
立铣刀
1)选择铣削用量
由于槽的宽度为12mm,故一次走完,ap=6mm
由《切削用量简明手册》表3.3确定f=0.5mm/r现取f=0.8mm/rfz=0.5/24=0.02mm/z
3)选择铣刀磨钝标准及刀具寿命:
根据《切削用量简明手册》表3.7,得最大磨损量为0.5由表3.8确定刀具寿命:
T=100min其中
4)确定切削速度Vc和每齿进给量:
决定切削速度Vc和每齿进给量Vf、由《切削用量简明手册》3.27的公式
Vc=(Cvxdoxqv)/(TmxapxXvxfzxyvxaexuvxZpv)·Kv
Cv=25,qv=0.2,Xv=0.1,yv=0.2,uv=0.5,pv=0.1,m=0.25,Km=1.12,
Ksv=0.8,KTv=0.82,
Kv=KmxKsvxKTv=1.12x0.8x0.82=0.79
Vc=(Cvxdoxqv)/(TmxapxXvxfzxyvxaexuvxZpv)·Kv=98.6m/min
n=1000×Vc/do=1000×98.6/3.14×100=314r/min
根据X62W型铣床说明书选nc=300r/min
实际速度Vc=donc/1000=94.2m/min
选Vfc=ncf=300X0.5=150mm/min根据X62W型铣床说明书选选Vf=150mm/min
fzc=150/300×24=0.020mm/z
5)基本工时基本工时根据《切削用量简明手册》表3.5
Tm=(L+L1+△)•i/Vf=(137+10)/150=0.98(min)L1+△=10mm
三、夹具设计
为了提高劳动生产率,保证加工质量,降低劳动强度,需要设计专用夹具。
由指导老师的分配第V道工序钻6-Φ17孔和第VIII道工序的铣宽12的槽的夹具设计。
3.1钻床夹具的设计
3.1.1问题的提出
本夹具主要用于钻6-Φ17孔,精度要求不高,和其他面没有任何为主度要求,为此,只考虑如何提高生产效率上,精度则不予考虑,。
3.1.2定位基准的选择
本道工序加工6-Φ17孔,精度不高,因此我们采用已加工好的底面和两侧面定位,因为孔径自身较小,切削力较小,因此不在采用其他的辅助定位,压板的压紧力即可以满足要求
3.1.3切削力和夹紧力的计算
由于本道工序主要完成工艺孔的钻孔加工,钻削力。
由《切削手册》得:
钻削力式(5-2)
钻削力矩式(5-3)
式中:
代入公式(5-2)和(5-3)得
本道工序加工工艺孔时,夹紧力方向与钻削力方向相同。
因此进行夹紧立计算无太大意义。
只需定位夹紧部件的销钉强度、刚度适当即能满足加工要求。
3.4定位误差分析
(1)定位元件尺寸及公差确定。
夹具的主要定位元件为一平面,一定位销,一挡销。
(2)工件的工序基准为底面,当工件底面为最大,定位销的孔径为最小时,孔心在任意方向上的最大变动量等于底面与销配合的最大间隙量。
本夹具是用来在钻床上加工,所以工件底面与夹具上的定位销保持固定接触。
此时可求出底面在接触点与销中心连线方向上的最大变动量为孔径公差多一半。
工件的定位基准为孔心。
工序尺寸方向与固定接触点和销中心连线方向相同,则其定位误差为:
Td=Dmax-Dmin
3.5钻套设计
6-Φ17孔的加工需钻,然后锪孔,因为钻后还要锪孔,为了我们钻后能及时的的锪孔。
故选用快换钻套(其结构如下图所示)以减少更换钻套的辅助时间。
根据工艺要求:
。
即先用Φ17的麻花钻钻孔,根据GB1141—84的规定钻头上偏差为零,故钻套孔径为Φ17。
再用锪孔钻锪孔。
图5.3快换钻套图
扩工艺孔钻套结构参数如下表:
表5.1扩工艺孔钻套数据表
d
H
D
公称尺寸
允差
17
20
26
-0.0