锅炉夹套水温定值控制系统设计.docx
《锅炉夹套水温定值控制系统设计.docx》由会员分享,可在线阅读,更多相关《锅炉夹套水温定值控制系统设计.docx(18页珍藏版)》请在冰豆网上搜索。
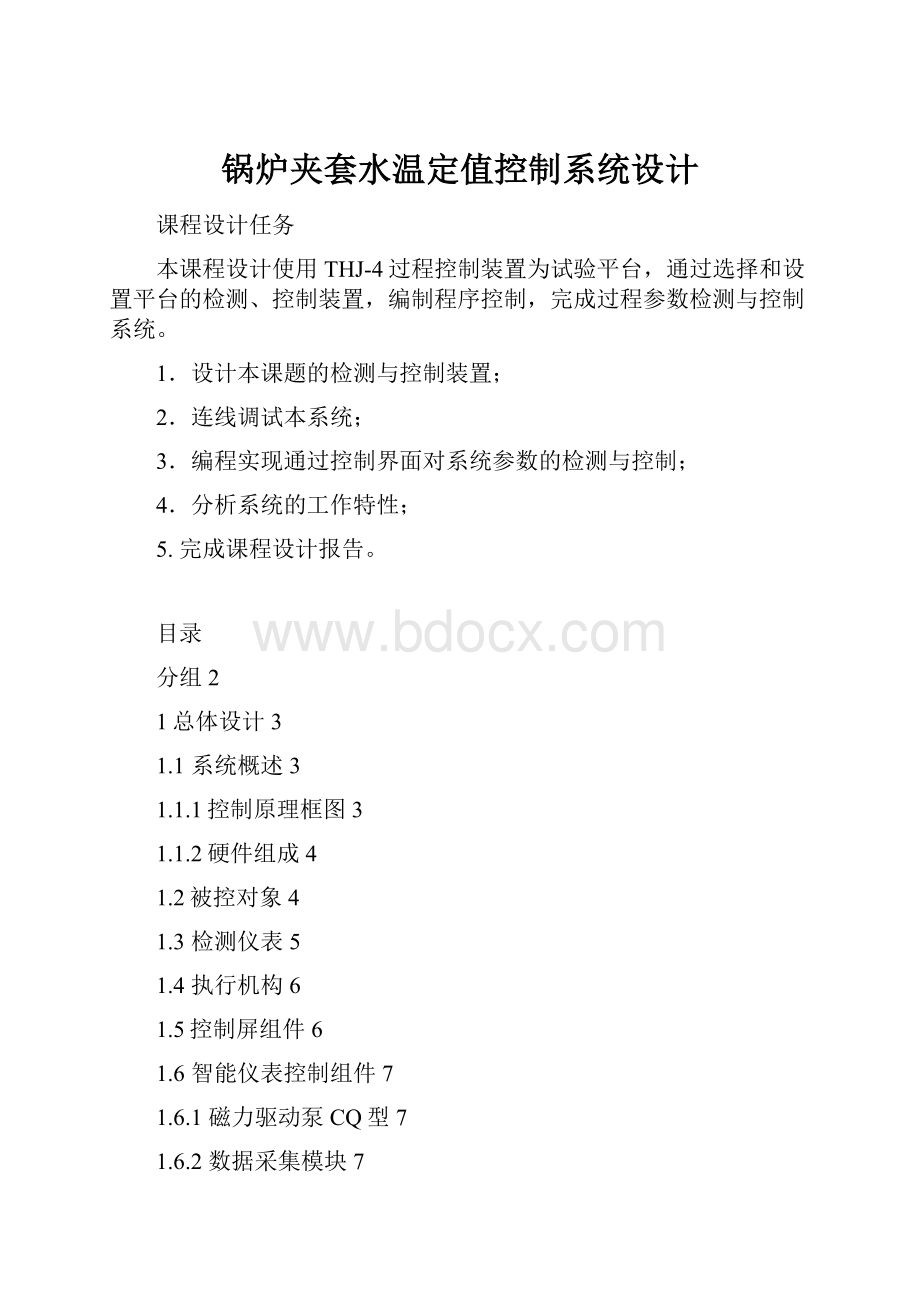
锅炉夹套水温定值控制系统设计
课程设计任务
本课程设计使用THJ-4过程控制装置为试验平台,通过选择和设置平台的检测、控制装置,编制程序控制,完成过程参数检测与控制系统。
1.设计本课题的检测与控制装置;
2.连线调试本系统;
3.编程实现通过控制界面对系统参数的检测与控制;
4.分析系统的工作特性;
5.完成课程设计报告。
目录
分组2
1总体设计3
1.1系统概述3
1.1.1控制原理框图3
1.1.2硬件组成4
1.2被控对象4
1.3检测仪表5
1.4执行机构6
1.5控制屏组件6
1.6智能仪表控制组件7
1.6.1磁力驱动泵CQ型7
1.6.2数据采集模块7
1.6.3智能调节阀8
2实验内容9
2.1实验步骤9
2.2数据采集硬件系统构件、连线9
2.2.1数据采集硬件系统构件9
2.2.2硬件系统连线10
2.3组态软件界面、逻辑、代码10
2.3.1MCGS组态软件10
2.3.2组态软件设计12
2.3.3组态软件代码14
3实验结果曲线及分析15
4心得体会17
5.参考文献19
分组
锅炉夹套水温定值控制系统
1总体设计
1.1系统概述
本设计以锅炉作为被控对象,夹套的水温为系统的被控制量。
设计目的是使锅炉夹套的水温稳定至给定量;使用MCGS组态软件结合数据采集设备来实现具体调节效果。
1.1.1控制原理框图
图1.锅炉夹套水温定值控制系统
(a)结构图(b)方框图
本实验系统结构图和方框图如图1所示。
本实验以锅炉夹套作为被控对象,夹套的水温为系统的被控制量。
本实验要求锅炉夹套的水温稳定至给定值,将铂电阻TT2检测到的锅炉夹套温度信号作为反馈信号,与给定量比较后的差值通过调节器控制三相调压模块的输出电压(即三相电加热管的端电压),以达到控制锅炉夹套水温的目的。
在锅炉夹套水温的定值控制系统中,其参数的整定方法与其它单回路控制系统一样,但由于锅炉夹套的温度升降是通过锅炉内胆的热传导来实现的,所以夹套温度的加热过程容量时延非常大,其控制过渡时间也较长,系统的调节器可选择PD或PID控制。
实验中用变频器支路以固定的小流量给锅炉内胆供循环水,以加快冷却。
图1(b)为一个单回路的锅炉夹套温度控制系统的结构框图.实验前先用磁力泵给锅炉内胆打适量的水,而锅炉夹套为动态环水,锅炉内胆组成循环供水系统。
在单回路的锅炉夹套温度控制系统中,若没有循环水加以快速热交换,散热过程相对比较缓慢,温度调节得效果受对象特性和环境的限制,在精确和稳定性上存在着一定的误差。
当增加了循环水系统以后,有利于热交换并提高散热能力。
相比与静态温度控制实验,在控制的精确性,快速性上有很大的提高。
本系统控制的被控制量锅炉夹套水温,既控制任务是控制锅炉夹套水温等于给定值,并采取工业智能PID调节。
1.1.2硬件组成
本实验装置对象主要由水箱、锅炉和盘管三大部分组成。
供水系统由三相(380V恒压供水)磁力驱动泵、电动调节阀、涡轮流量计及自动电磁阀组成、三相磁力驱动泵(220V变频调速)、涡轮流量计及自动电磁阀组成。
1.2被控对象
由不锈钢储水箱、(上、中、下)三个串接有机玻璃水箱、4.5KW三相电加热模拟锅炉(由不锈钢锅炉内胆加温筒和封闭式锅炉夹套构成)、盘管和敷塑不锈钢管道等组成。
1.水箱:
包括上水箱、中水箱、下水箱和储水箱。
水箱结构独特,由三个槽组成,分别为缓冲槽、工作槽和出水槽,进水时水管的水先流入缓冲槽,出水时工作槽的水经过带燕尾槽的隔板流入出水槽,这样经过缓冲和线性化的处理,工作槽的液位较为稳定,便于观察。
水箱底部均接有扩散硅压力传感器与变送器,可对水箱的压力和液位进行检测和变送。
上、中、下水箱可以组合成一阶、二阶、三阶单回路液位控制系统和双闭环、三闭环液位串级控制系统。
储水箱内部有两个椭圆形塑料过滤网罩,以防杂物进入水泵和管道。
2.模拟锅炉:
是利用电加热管加热的常压锅炉,包括加热层(锅炉内胆)和冷却层(锅炉夹套),可利用它进行温度实验。
冷却层和加热层都装有温度传感器检测其温度,可完成温度的定值控制、串级控制,前馈-反馈控制,解耦控制等实验。
3.管道及阀门:
整个系统管道由敷塑不锈钢管连接而成,所有的阀门均采用优质阀。
其中储水箱侧面有一个进水阀和出水阀,当水箱需要更换水时,可把球阀打开将水直接接入或排出。
1.3检测仪表
1.压力传感器、变送器:
三个液位传感器分别用来对上、中、下三个水箱的液位进行检测。
采用工业用的扩散硅压力变送器,同时采用信号隔离技术,对传感器温度漂移跟随补偿。
采用标准二线制传输方式,工作时需提供24V直流电源,输出:
4~20mADC。
2.温度传感器:
装置中采用了六个Pt100铂热电阻温度传感器,分别用来检测锅炉内胆、锅炉夹套、盘管(有3个测试点)以及上水箱出口的水温。
经过调节器的温度变送器,可将温度信号转换成4~20mA直流电流信号。
3.流量传感器、变送器:
三个涡轮流量计分别用来对由电动调节阀控制的动力支路、由变频器控制的动力支路及盘管出口处的流量进行检测。
采用标准二线制传输方式,工作时需提供24V直流电源,输出:
4~20mADC。
4.锅炉防干烧保护装置:
为保证实验效果好、不降低锅炉加热功率的前提下,本套装置配备了良好的防干烧保护系统,当锅炉内胆液位低于红色警戒水位线时,保护装置将切断调压模块输出电压,以有效保护电加热管不被干烧损坏。
1.4执行机构
1.电动调节阀:
采用智能直行程电动调节阀,用来对控制回路的流量进行调节。
电动调节阀型号为:
QSVP-16K,电源为单相220V,控制信号为4~20mADC或1~5VDC,输出为4~20mADC的阀位信号,使用和校正非常方便。
2.水泵:
本装置采用磁力驱动泵,型号为16CQ-8P。
本装置采用两只磁力驱动泵,一只为三相380V恒压驱动,另一只为三相变频220V输出驱动。
3.电磁阀:
本套装置共有17支优质电磁阀配合控制器完成所有实验项目,其阀体为黄铜材质,磁力连接栓为不锈钢榜及弹簧、弹杆、橡皮膜片,以防止生锈。
1.5控制屏组件
通讯线介绍
“THJ-4型高级过程控制系统实验平台”可以挂智能仪表、远程数据采集和S7-200PLC挂件,并可控制对象系统完成相应的实验。
屏中布有485通讯线线,从正面看控制屏时,从左边数的五个通讯口挂在一条485总线上,然后引出来一根通讯线,通讯头上标有“1”的字样;最右边的通讯口单独从控制屏后引出一个通讯头,上面标有“6”的字样。
485通讯线主要用于仪表和远程数据采集模块与计算机的通讯,485通讯方式与计算机建立通讯时需接一个转换器到计算机串口上。
THJ-4-3面板是与对象系统通过2号42芯和3号19芯电缆线相连的接口板,可取来对象上的信号,也可将控制屏上的信号通过它送出;面板上有24V开关电源的输出端子,它不但控制着面板上三路24V直流输出,而且控制着对象系统所有变送器的电源。
1.6智能仪表控制组件
1.6.1磁力驱动泵CQ型
CQ型磁力驱动泵(简称磁力泵),以静密封取代动密封,使泵的过流部件处于完全密封状态,彻底解决了其他泵机械密封无法避免的跑、冒、滴之弊病。
磁力泵具有良好的抗腐蚀性能,并可以使被输送介质免受污染。
CQ型磁力驱动泵型号意义:
CQ型磁力驱动泵安装尺寸:
图2.CQ型磁力驱动泵安装尺寸图
1.6.2数据采集模块
产品简介:
集智达R-8000系列RemoDAQ-8024/R-8024+数据采集模块,4路模拟量输出模块。
- 分辨率:
14位
- 电流输出:
0~20mA、4~20mA
- 电压输出:
0~5V、0~10V、±10V
- 分辨率:
14bit
- 输出斜率可编程
- 带ModBus通讯协议(R-8024+)
- D/A通道需外配电源供电
图3.RemoDAQ-8024
1.6.3智能调节阀
1.产品特点:
QSVP系列智能电动单座调节阀是QS智能电动调节阀系列产品之一,它由PSL智能型电动执行器与优质的国产阀门相组合构成。
2.产品参数:
电动执行机构接受4~20mA控制信号,改变阀门的开度,同时将阀门开度的隔离信号反馈给控制系统,实现对压力、温度、流量、液位等参数的调节。
3.主要特点
●配用PSL智能型直行程电动执行器,体积小、规格全、重量轻、推力大、操作方便,无调整电位器,可靠性高、噪声小。
●PSL电动执行器采用—体化结构设计,具有自诊断功能,使用和调校十分方便。
●有数字显示窗口,可看到控制信号值、阀位值。
●PSL智能型电动执行机构功能:
带断控制信号故障判断、报警及保护功能。
即断信号时可使执行机构或开;或关;或保持;或在0~100%之间予置的任意位置。
及带阀门堵转故障判断、报警及保护功能。
●TP系列采用顶端导向,单座密封结构。
与其它同类调节阀相比,具有结构简单、额定流量系数大,阀座泄露量小等突出优点。
另外,带有软密封结构的TP系列既有调节功能又有切断功能,是一种调节切断型的调节阀,也可作切断阀用。
2实验内容
2.1实验步骤
本实验选择锅炉夹套水温作为被控对象,实验之前先将储水箱中贮足水量,然后将F2-6,F2-9,F2-8打开。
给锅炉内胆和夹套贮满水,然后关闭变频器、关闭F2-8,打开F2-9,为给锅炉内胆供冷水作好准备。
2.2数据采集硬件系统构件、连线
2.2.1数据采集硬件系统构件
远程数据采集控制即我们通常所说的直接数字控制(DDC),它的特点是以计算机代替模拟调节器进行控制,并通过数据采集板卡或模块进行A/D、D/A转换,控制算法全部在计算机上实现。
在本装置中远程数据采集控制系统包括SA-21远程数据采集热电阻输入模块挂件、SA-22远程数据采集模拟量输入模块挂件、SA-23远程数据采集模拟量输出模块挂件。
采用台湾鸿格ICP7000系列智能采集模块,其中I-7017是8路模拟量输入模块,I-7024是4路模拟量输出模块,I-7033是3路热电阻输入模块。
ICP7000系列智能采集模块通过RS485等串行口通讯协议与PC相连,由PC中的算法及程序控制并实现数据采集模块对现场的模拟量、开关量信号的输入和输出、脉冲信号的计数和测量脉冲频率等功能。
图4所示即为远程数据采集控制系统框图。
图中输入输出通道即为ICP7000智能采集模块。
图4.数据采集系统框图
2.2.2硬件系统连线
图5.硬件系统连线实图
2.3组态软件界面、逻辑、代码
2.3.1MCGS组态软件
计算机技术和网络技术的飞速发展,为工业自动化开辟了广阔的发展空间,用户可以方便快捷地组建优质高效的监控系统,并且通过采用远程监控及诊断等先进技术,使系统更加安全可靠,在这方面MCGS工控组态软件发挥着重要的作用。
本装置中智能仪表控制方案、远程数据采集控制方案和S7-200PLC控制方案均采用了北京昆仑公司的MCGS组态软件作为上位机监控组态软件。
MCGS(MonitorandControlGeneratedSystem)是一套基于Windows平台的,用于快速构造和生成上位机监控系统的组态软件系统,可运行于MicrosoftWindows95/98/NT/2000等操作系统。
MCGS5.5为用户提供了解决实际工程问题的完整方案和开发平台,能够完成现场数据采集、实时和历史数据处理、报警和安全机制、流程控制、动画显示、趋势曲线和报表输出以及企业监控网络等功能。
MCGS(MonitorandControlGeneratedSystem)软件是一套几基于Windows平台的32位工控组态软件,集动画显示、流程控制、数据采集、设备控制与输出、网络数据传输、工程报表、数据与曲线等诸多强大功能于一身,并支持国内外众多数据采集与输出设备,广泛应用于石油、电力、化工、钢铁、冶金、纺织、航天、建筑、材料、制冷、通讯、水处理、环保、智能楼宇、实验室等多种行业。
MCGS组态软件由“MCGS组态环境”和“MCGS运行环境”两个部分组成。
MCGS组态环境是生成用户应用系统的工作环境,由可执行程序McgsSet.exe支持,用户在MCGS组态环境中完成动画设计、设备连接、编写控制流程、编制工程打印报表等全部组态工作后,生成扩展名为.mcg的工程文件,又称为组态结果数据库,其与MCGS运行环境一起,构成了用户应用系统,统称为“工程”。
MCGS运行环境是用户应用系统的运行环境,由可执行程序McgsRun.exe支持,以用户指定的方式运行,并进行各种处理,完成用户组态设计的目标和功能。
利用MCGS软件组建工程的过程简介:
(1)工程项目系统分析:
分析工程项目的系统构成、技术要求和工艺流程,弄清系统的控制流程和测控对象的特征,明确监控要求和动画显示方式,分析工程中的设备采集及输出通道与软件中实时数据库变量的对应关系,分清哪些变量是要求与设备连接的,哪些变量是软件内部用来传递数据及动画显示的。
(2)工程立项搭建框架:
主要内容包括:
定义工程名称、封面窗口名称和启动窗口名称,指定存盘数据库文件的名称以及存盘数据库,设定动画刷新的周期。
经过此步操作,即在MCGS组态环境中,建立了由五部分组成的工程结构框架。
(3)设计菜单基本体系:
为了对系统运行的状态及工作流程进行有效地调度和控制,通常要在主控窗口内编制菜单。
编制菜单分两步进行,第一步首先搭建菜单的框架,第二步再对各级菜单命令进行功能组态。
在组态过程中,可根据实际需要,随时对菜单的内容进行增加或删除,不断完善工程的菜单。
(4)制作动画显示画面:
动画制作分为静态图形设计和动态属性设置两个过程。
前一部分用户通过MCGS组态软件中提供的基本图形元素及动画构件库,在用户窗口内组合成各种复杂的画面。
后一部分则设置图形的动画属性,与实时数据库中定义的变量建立相关性的连接关系,作为动画图形的驱动源。
(5)编写控制流程程序:
在运行策略窗口内,从策略构件箱中,选择所需功能策略构件,构成各种功能模块,由这些模块实现各种人机交互操作。
MCGS还为用户提供了编程用的功能构件,使用简单的编程语言,编写工程控制程序。
(6)完善菜单按钮功能:
包括对菜单命令、监控器件、操作按钮的功能组态;实现历史数据、实时数据、各种曲线、数据报表、报警信息输出等功能;建立工程安全机制等。
(7)编写程序调试工程:
利用调试程序产生的模拟数据,检查动画显示和控制流程是否正确。
(8)连接设备驱动程序:
选定与设备相匹配的设备构件,连接设备通道,确定数据变量的数据处理方式,完成设备属性的设置。
此项操作在设备窗口内进行。
(9)工程完工综合测试:
最后测试工程各部分的工作情况,完成整个工程的组态工作,实施工程交接。
2.3.2组态软件设计
在开始组态工程之前,先对该工程进行剖析,以便从整体上把握工程的结构、流程、需实现的功能及如何实现这些功能。
本设计目的是通过过程控制,使内胆水温稳定为给定值,并对扰动具有一定的适应能力。
因此,夹套水温与流量参数设定、实时数据显示窗口,实时曲线与历史曲线显示窗口,计算机与工控机的通讯状态设定及显示窗口。
由上述分析可知,本系统应具有7个用户窗口:
锅炉夹套水温定值控制、实验指导、实时曲线、历史曲线、通讯状态、数据浏览、退出指示。
图6.组态软件界面一
图7.组态软件界面二
2.3.3组态软件代码
启动脚本:
control=0
q0=0
q1=0
q2=0
ei=0
ei1=0
ei2=0
mx=0
op11=0
电动阀输出=0
变频器输出=0
调压器输出=0
循环脚本:
ifalarm2<1oralarm2>31then
do12=1
do14=1
endif
夹套温度=pt1
ifcontrol=1then
ei=主设定值-pt1
q0=k1*(ei-ei1)
ifti1=0then
q1=0
else
q1=k1*0.2*ei/ti1
endif
q2=k1*td1*(ei-2*ei1+ei2)/0.2
mx=q0+q1+q2
op11=op11+mx
ifop11<0then
op11=0
endif
ifop11>100then
op11=100
endif
调压器输出=op11
ei2=ei1
ei1=ei
else
op11=调压器输出
endif
退出脚本:
do12=0
do14=0
电动阀输出=0
变频器输出=0
调压器输出=0
3实验结果曲线及分析
本实验选择锅炉夹套水温作为被控对象,实验之前先将储水箱贮足水量,将阀门F1-1、F1-2、F1-5、F1-13全开,手动调节阀门F1-3至适当开度,其余阀门关闭。
启动380伏交流磁力泵,给锅炉内胆贮一定的水量(要求至少高于液位指示玻璃管的红线位置),然后关闭阀F1-13,打开阀F1-12,给锅炉夹套注一定的水量。
1、接通控制系统电源,打开用作上位监控的PC机,进入的实验主界面。
2、在实验主界面中选择本实验项即“锅炉夹套水温PID控制实验”,系统进入正常的测试状态。
3、在上位机监控界面中点击“手动”,并将输出值设置为一个合适的值,此操作既可拉动输出值旁边的滚动条,也可直接在输出值显示框中输入。
4、合上三相电源空气开关,三相电加热管通电加热,适当增加/减少输出量,使锅炉内胆的水温稳定于设定值。
5、经验法或动态特性参数法整定调节器参数,选择PID控制规律,并按整定后的PID参数进行调节器参数设置。
6、待锅炉内胆水温稳定于给定值时,将调节器切换到“自动”状态,待水温稳定后,突增(或突减)设定值的大小,使其有一个正(或负)阶跃增量的变化(即阶跃干扰,此增量不宜过大,一般为设定值的5%~15%为宜),锅炉内胆的水温便离开原平衡状态,经过一段调节时间后,水温稳定至新的设定值。
点击实验界面下边的切换按钮,观察实时曲线、历史曲线、数据报表所记录的设定值、输出值,内胆水温的响应过程曲线将如图8所示。
图8.内胆水温的响应过程曲线
7、适量改变控制器的PID参数,重复步骤6,观察计算机记录不同参数时系统的响应曲线。
8、开始往锅炉夹套打冷水,重复步骤3~7,观察实验的过程曲线与前面不加冷水的过程有何不同。
9、采用PI控制规律,重复上述实验,观察在不同的PID参数值下,系统的阶跃响应曲线。
本实验中,得到的曲线如下:
图8.响应曲线
4心得体会
通过本次过程参数检测及仪表的课程设计,我们加深了对过程参数检测这门课程的理解同时也掌握了一定的仪表仪器使用方法和技巧,以及MCGS组态软件的应用。
本次课程设计的主要内容是锅炉夹套水温定值控制系统的设计,通过这次课程设计使我了解到团队合作、独立思考、实践动手的重要性。
本次课程设计,以我理解主要的原理是:
在锅炉内胆有加热管,内胆的热量通过热传递的形式将热量传递给夹套,通过控制夹套水流的快慢从而控制内胆的水温。
当内胆水的液位低于规定红色标定线时,出现干锅报警,此时报警灯亮。
当夹套水温大于设定的水温时,此时夹套内水流加速。
但在完成该实验的过程中,因变频器不能正常使用导致了不能有效的控制水流速度。
系统有PC机控制,主要由组态软件MCGS控制。
从数据结果中,我们发现有三条线,中间一条为一直线,是设定的夹套温度,下面一条是夹套温度,其曲线逼近与中间直线,因为夹套温度是根据内胆热传递获得的,其温度不会高于设定温度,当高于设定温度时,此时水流加速使其保持恒定,最上面的曲线是内胆温度。
内胆温度要比夹套温度高很多,但同时也是通过夹套水流速度来控制内胆温度。
故该实验结果正确。
在本实验中,我在各个环节都有涉及,包括熟知铂电阻、流量计、压力变送器、磁力泵等,熟练接线方法等。
数据采集模块主要是有个反馈环节,将测得的量经过采集模块中的AD转换等调理电路,将信号输入PC机中,由组态软件进行控制。
组态软件再将信号传递到采集模块,再通过DA转换控制相应仪器。
此外,我还在本次课程中担任了资料查找和报告书写的工作通过资料搜索到设计的书写整一个过程,让我对过去课堂当中所学到的知识进行了一次系统性的回顾和强化,相当于一次毕业设计前准备工作。
在课程设计过程中,也让我明白了思路及方法,只要努力学习总会有解决问题的方法。
5.参考文献
[1]《THJ-4过程控制装置使用说明》天煌教学仪器厂;
[2]《自动检测技术与应用》梁森等主编,机械工业出版社;
[3]《过程检测技术及仪器(第2版)》杜维等编著,化学工业出版社,2011年2月