非标塔类设备施工方案.docx
《非标塔类设备施工方案.docx》由会员分享,可在线阅读,更多相关《非标塔类设备施工方案.docx(24页珍藏版)》请在冰豆网上搜索。
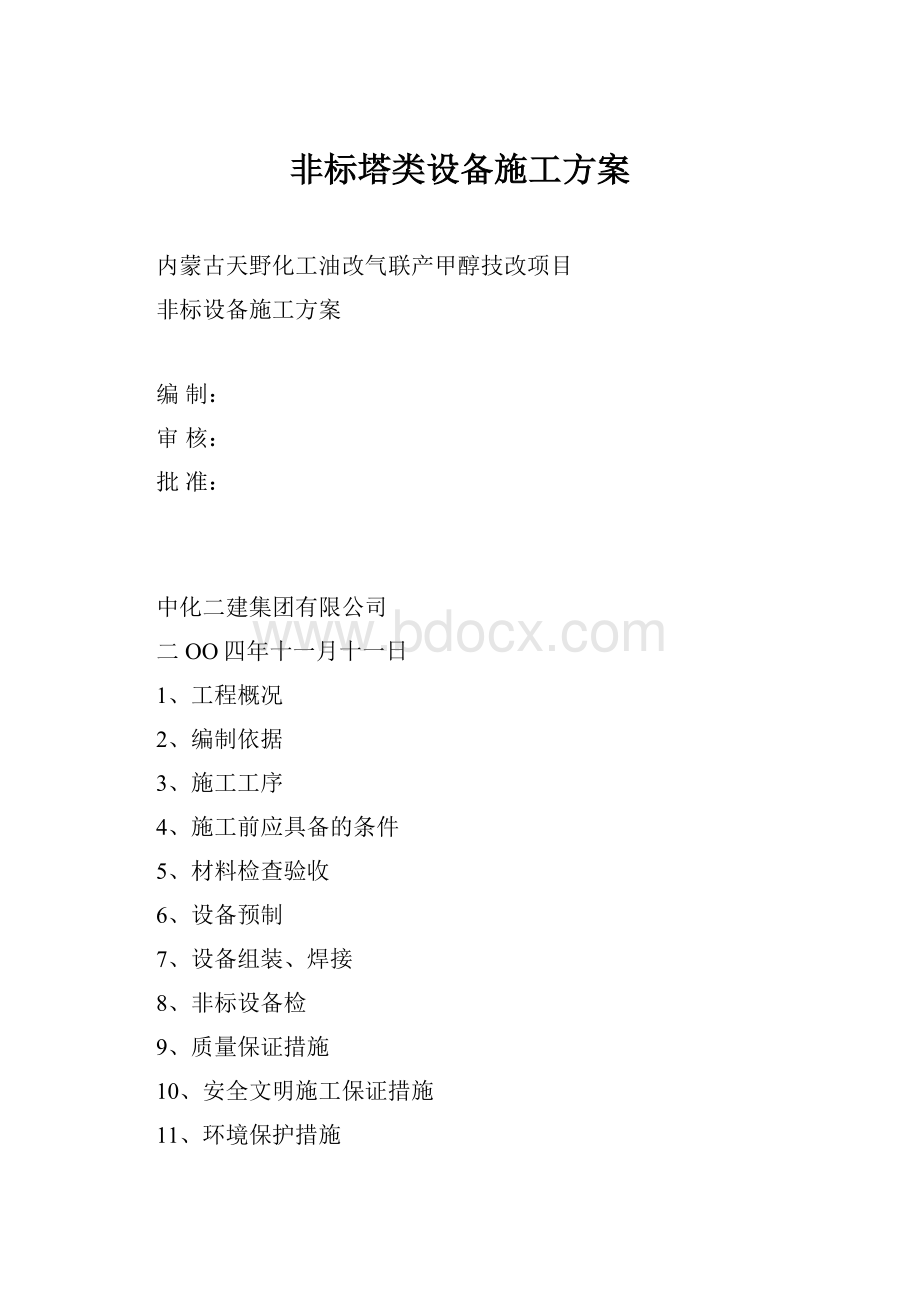
非标塔类设备施工方案
内蒙古天野化工油改气联产甲醇技改项目
非标设备施工方案
编制:
审核:
批准:
中化二建集团有限公司
二OO四年十一月十一日
1、工程概况
2、编制依据
3、施工工序
4、施工前应具备的条件
5、材料检查验收
6、设备预制
7、设备组装、焊接
8、非标设备检
9、质量保证措施
10、安全文明施工保证措施
11、环境保护措施
12、劳动力组织
13、主要施工机具
14、主要手段用料
15、施工进度计划
1.工程概况
1.1内蒙古天野化工油改气联产甲醇技改项目甲醇装置现由我单位制作非标设备16台
,其中太原基地制作7台,现场制作9台,设备主要技术参数见表一:
非标设备主要技术参数表一
序号
设备名称
型号规格
主要材质
净重(t)
数量
设计压力MPa
设计温度℃
试验压力MPa
备注
1
回收塔
φ1200×31460
16MnR
15.55
1
0.22
120
0.56(卧)
甲醇精馏
2
常压精馏塔
φ2600×40710
16MnR
37.83
1
0.31
120
0.714(卧)
甲醇精馏
3
预精馏塔
φ1900×28068
16MnR
16.52
1
0.24
95
0.52(卧)
甲醇精馏
4
加压精馏塔
φ2200×42515
16MnR
39.89
1
0.79
170
1.32(卧)
甲醇精馏
5
排污罐
φ1000×3250
16MnR
0.85
1
1.1
313
1.65
天然气转化
6
真空闪蒸罐
φ4800×17675
0Cr18Ni9
16
1
-0.1/0.3
-80
0.51(卧)
低温甲醇洗
7
溶液贮槽
φ8000×9553
Q235-A
21.03
1
常压/0.4
60/160
盛水试验/0.6
CO2回收
8
地下槽
φ2500×2000
Q235-A
1.97
1
常压/0.4
60/160
盛水试漏/0.55
CO2回收
9
杂醇油槽
φ1600×3170
Q235-A
0.97
1
常压
60
盛水试漏
甲醇精馏
10
常压塔放空水封槽
φ1150×1950
Q235-A
0.515
1
常压
60
盛水试漏
甲醇精馏
11
碱液槽
φ1000×1000
Q235-A
0.376
1
常压/0.4
60/160
盛水试漏/0.55
CO2回收
12
碱液槽
φ1400×2890
Q235-A
1.065
1
常压
60
盛水试漏
甲醇精馏
13
地下槽
φ2500×3395
Q235-B
2.45
1
常压
60
盛水试漏
甲醇精馏
14
烟气冷却塔
φ4800×22600
Q235-B
60.6
1
0.12
200
0.15
CO2回收
15
CO2吸收塔
φ4800×52616
Q235-B
133
1
0.12
80
0.15
CO3回收
16
排放槽
φ3000×8060
Q235-B
11.3
1
0.11
60
0.14
甲醇精馏
总重
361.11
1.2编制说明
根据甲醇装置非标设备制作的施工进度及本地气候条件等情况,编制此方案。
由于现场设备安装地点较分散且土建正在施工,所以外形尺寸较小的设备在钢平台制作,塔类设备在钢平台上先分段制作,待土建施工完毕运至安装地点组对。
2.编制依据
本方案依据下列施工规范进行编制
2.1《钢制压力容器》GB150-1998
2.2《钢制化工容器制造技术要求》HG20584-1998
2.3《塔器设计技术规范》HG20652-1998
2.4《钢制塔类容器》JB4710-92
2.5《钢制焊接常压容器》JB/T4735-1997
2.6《压力容器安全技术监察规程》1999
2.7《现场设备工业管道焊接工程施工及验收规范》GB50236-98
2.8五环科技股份有限公司提供的非标设备施工图。
3.施工工序
施工准备→材料检查验收→设备预制→设备组对焊接(X射线探伤)→附件焊接→设备试压
4.施工前应具备的条件
4.1施工方案和有关技术交底已编制审批完毕,并向全体施工人员进行了详细的技术交底。
4.2施工用机具已进场并按施工总平面布置图布置就绪。
4.3施工用计量器具配备齐全,并在有效期内。
4.4现场预制平台已搭设完毕。
4.5施工用材料已备齐。
5.材料检查验收
5.1所用原材料、设备附件及其原材料都必须有相应的质量证明书,当对质量合格证明书有疑问时,应对材料和设备附件进行复验,合格后方准使用。
5.2所有材料及附件的规格、型号、材质均应符合施工图纸的要求。
5.3钢板必须逐张进行外观检查,其表面不得有气孔、裂缝、夹渣、拆痕、夹层,边缘不得有重皮等缺陷。
5.4钢板表面锈蚀减薄量、划痕深度与钢板实际负偏差之和,不得超过0.8mm。
5.5设备封头外观检查应符合以下条件:
5.5.1椭圆封头直边上的纵向皱折深度不得大于1.5mm。
5.5.2封头上任一点最小壁厚不得小于设计厚度的90%。
5.5.3封头尺寸允许偏差见表二:
封头尺寸允许偏差表二
封头公称直径DN
直径允许偏差ΔDN
不圆度e
表面凹凸量c
曲面高允许偏差Δh1
800~1200
±3
≤4
≤3
±6
1300~1600
±4
≤6
≤4
±8
1700~2400
±5
≤8
≤4
±12
2600~3000
±6
≤9
≤4
±16
3200~4000
±6
≤10
≤4
±20
4200~6000
±6
≤12
≤4
±24
5.6焊条应按批号、规格、类别验收,焊条表面应无药皮脱落、偏芯、焊芯生锈、发霉等现象。
5.7油漆、保温材料应具有质量合格证,并在有效期内,如有怀疑,应检测合格后方准使用。
5.8经检查合格的材料应根据其规格及材质分类存放妥善保管。
6、设备预制
6.1钢板切割加工:
不锈钢板采用等离子加工,碳钢板、16Mn钢板采用切割加工。
6.2钢板边缘加工面应平滑,不得有夹渣、分层、裂纹及熔渣等缺陷。
火焰切割坡口产生的表面硬化层应磨除。
6.3气割坡口的表面应符合下列要求见表三:
气割坡口的表面质量要求表三
类别
定义
质量要求
平面度
表面凹凸程度
凹凸度小于等于2.5%板厚
粗糙度
表面粗糙度
Ra50(μm)
凹坑
局部粗糙度增大
凹坑宽度小于等于50mm
6.4纵向焊缝对接接头的间隙G应为0~3mm,钝边F应不大于1mm,坡口宽度W应为16~18mm,见下图:
6.5环向焊缝对接接头的坡口角度a应为45±2.5°,钝边F不应大于2mm,间隙G应为0~1mm见下图:
(其它坡口形式按图纸要求施工)
纵向焊缝坡口形式环焊缝坡口形式
6.6板材在卷制前均要压头,进料方向要垂直于滚轴,并用吊车辅助。
6.7壁板卷制后,应立置在平台上用样板检查。
垂直方向上用直样板检查,其间隙不得大于1mm;水平方向上用弧形样板检查,其间隙不得大于4mm。
6.8壁板及贮罐中幅板下料时尺寸允许偏差见下图及表四:
表四
测量部位
环向对接焊缝
板长AB(CD)≥10000m
板长AB(CD)<10000m
宽度AC、BD、EF
±1.5
±1
长度AB、CD
±2
±1.5
对角线之差|AD-BC|
≤3
≤2
直线度
AD、BC
≤1
≤1
AB、CD
≤2
≤2
AEB
CFD
7.设备组对焊接
7.1塔类设备应先分段制作时根据设备高度,确定是否需分段制作,现场组对,筒节制作应满足下列要求:
7.1.1塔类设备组装、焊接工作,应严格照设计图样及排版图确定的尺寸及焊接工艺进行。
7.1.2筒体圆弧应用弦长等于D/4且不小于500mm的样板检查壁板的弧度其间隙应小于3mm。
7.1.3筒体同一截面上任意两直径之差不得大于其直径的1%且不大于25mm。
7.1.4筒体外圆周长允许偏差应符合表五要求:
(D为筒体直径)
表五
筒体部位
不圆度
筒体
b≤1%Dg且不大于25mm
塔盘处
b≤0.5%Dg且不大于15mm
7.1.5各段筒体端面不平度偏差f应不大于1/1000Dg,且不大于2mm,见下图:
f
Dg
7.1.6塔组对时,其焊缝错边量应符合下表要求,当环焊缝两节筒体厚度不等时错边量以较薄板厚度为基准(见表六):
表六
壁厚S(mm)
纵焊缝对口错边量b允许偏差(mm)
环焊缝对口错边量b允许偏差(mm)
允许S≤6
b≤10%S且不大于3mm
b≤25%S
6<S≤10
b≤10%S且不大于3mm
b≤20%S
S>10
b≤10%S且不大于3mm
b≤10%S+1且不大于6mm
7.1.7筒体对接纵缝处形成的棱角E应小于或等于壁厚S的10%加2mm,且不大于5mm;用弦长D/6且不小于300mm的弧形样板检查。
7.1.8组装对接环焊缝时,不应采用十字焊缝,相邻筒节的纵焊缝或封头拼接焊缝与相邻筒节纵焊缝的距离应大于3倍壁厚,且不小于100mm。
7.1.9筒体分段组装后,应在内外壁上划出相隔90°的四条纵向组装线和基准圆周线作为整体组装及安装内件的依据。
7.1.10塔内件及其支承件和筒节焊接的焊缝边缘与筒体环焊缝边缘的距离应不小于筒体壁厚且不小于50mm,所有被覆盖的焊缝及塔盘、填料支承板、密封结构处防碍安装的焊缝或突出物均应磨至与母材齐平。
7.1.11裙座中心应与塔体中心线相重合,其允许偏差为±5mm。
7.1.12裙座与塔体相接处如遇到塔体拼接焊缝时,应在裙座上开出豁口,具体见下图及表七尺寸:
裙座上开出豁口尺寸表七
封头厚度δh(mm)
6~8
10~18
20~26
宽度K(mm)
70
100
120
缺口半径R(mm)
35
50
60
7.1.13裙座的底座环应垂直于底座圈(或塔体)中心线。
7.1.14塔体的底座圆,底板上地脚螺栓通孔应跨中均布,中心圆直径,相邻两孔弦长和任意弦长其允许偏差均不得大于2mm。
7.1.15塔接管的中心方位及标高允许偏差为±5mm,如接管与塔体管道有衔接时为±3mm。
7.1.16塔支撑件及梁等安装应符合下列规定:
7.1.17塔内支撑圈安装后,其上表面在300mm弦长上的局部水平度偏差不得超过1mm,总长度内允许偏差应符合表八要求:
塔内支撑圈水平度允许偏差表八
塔体内径D(mm)
允许偏差(mm)
D≤1600
≤3
1600<D≤4000
≤5
4000<D≤6000
≤6
7.1.18梁安装应符合下列规定:
7.1.19梁上表面的水平度在300mm长度内不得超过1mm,总长弯曲度允许偏差不得超过5mm。
7.1.20梁安装的中心位置与图示尺寸的偏差不得超过2mm。
7.1.21梁安装后,其上表面与支撑圈应在同一水平面上。
7.1.22当接管必须开在环焊缝上时应以开孔中心为圆心,对直径为3倍开孔直径长度的圆弧所包括的焊缝进行100%射线或超声波探伤,并符合要求。
7.1.23当外部附件与壳体主焊缝隙连接时,应在附件上开一槽口,以便使连接件焊缝跨越主焊缝。
槽口宽度应满足使连接件焊缝与主焊缝隙边缘的距离在1.5倍壳体壁厚以上。
7.2贮罐组装
7.2.1罐底组装
7.2.1.1底板铺设前应先在底板下表面涂刷防腐涂料,但每块板边缘50mm范围内不刷。
7.2.1.2边缘板对接接头的垫板应与两块底板贴紧,其间隙不得大于1mm。
7.2.1.3中幅板与边缘板之间应搭接,且中幅板应搭在边缘板上面。
7.2.1.4中幅板之间的搭接宽度为50mm,中幅板与边缘板之间的搭接宽度为60mm,其搭接宽度允许偏差为±5mm。
7.2.1.5底板搭接接头三层钢板重叠部分,应将上层钢板切角。
切角长度为100mm,宽度为33mm。
在上层底板铺设前,应先焊接上层底板覆盖部分的角焊缝。
7.2.1.6底板铺设前,应在基础上画出十字中心线,并按排板图画出底板圆周线。
底板铺设应先铺边缘板,然后再由中心向两侧铺设中幅板。
7.2.2罐顶组装
7.2.2.1罐顶组对时应设立临时支架,并提高50mm。
7.2.2.2包边角钢的半径偏差为±13mm。
7.2.2.3顶板应按画好的等分线对称组装。
7.2.2.4顶板搭接宽度允许偏差为±5mm。
7.2.3罐壁组装
7.2.3.1壁板组装前应对预制好的壁板进行复验,合格后方可组装。
当需要重新校正时,应防止出现锤痕。
7.2.3.2相邻两壁板上口允许水平偏差,不应大于2mm。
在整个圆周上任意两点允许水平偏差不应大于6mm。
壁板的铅垂度允许偏差不应大于3mm。
7.2.3.3组装焊接后,在底圈壁板1m高处,内表面任意点半径的允许偏差为±13mm。
7.2.3.4壁板安装时应保证内表面齐平,锚边量应符合表九。
罐壁对接接头错边量表九
项目
允许偏差(mm)
环向焊缝
不大于板厚的1/5,且≤3
纵向焊缝
δ≤10mm
1
δ>10mm
不大于板厚的1/10,且≤1.5
7.2.3.5组装焊接后,罐壁焊缝角变形用1m长的弧形样板检查及罐壁的局部凹凸变形应符合表十,且局部凹凸变形应平缓,不得有突然起伏。
罐壁焊缝局部凹凸变形及角变形表十
项目
允许值(mm)
罐壁局部凹凸变形
≤13
焊缝角变形
δ≤12mm
≤10
7.2.4设备焊接
7.2.4.1一般规定
a.设备施工前,应根据我公司已有的焊接工艺评定,制定出相应的作业指导书。
b.筒体等部件组装后,施焊前应将坡口表面及其内外侧边缘不小于12mm范围内的油、污垢、锈、毛刺等清除于净,不锈钢设备应在焊缝两侧50mm范围内涂白垩粉,防止飞溅沾污焊件表面。
c.塔体及吊耳、卡具等点焊或断焊,应与正式焊接工艺相同。
d.吊耳及卡具等拆除后,应对其焊缝的残留痕迹进行打磨,修整后的厚度不得小于设计要求的厚度。
e.焊接前应检查组装质量,清除坡口表面及坡口两侧各20mm范围内的泥砂、铁锈、水分和油污,并充分干燥。
f.焊接中应保证焊道始端和终端的质量。
始端采用后退起弧法,终端应将弧坑填满,多层焊的层间接头应错开。
g.罐底与罐壁连接的角焊缝焊接,应在底圈壁板纵缝焊完后施焊,并由数对焊工从罐内、外沿同一方向进行分段焊接。
初层焊道应采用分段退焊或跳焊法。
h.在底圈壁板纵缝、壁板间环缝、底圈壁板与底板间角缝焊完后,方可进行底板边缘板外缘300mm以外焊缝及收缩缝的焊接。
7.2.4.2壁板的焊接
a.壁板的焊接,应先焊纵向焊缝,后焊环向焊缝。
当焊完相邻两圈壁板的纵向焊缝后,再焊其间的环向焊缝,焊工应均匀分布,并沿同一方向施焊,力求焊接工艺一致。
b.每带壁板焊完后,焊缝X射线探伤要紧密配合。
7.2.4.3修补
a.深度超过0.5mm的划伤、电弧擦伤、焊疤等有害缺陷,应打磨平滑。
打磨修补后的钢板厚度,应不小于钢板名义厚度扣除负偏差值,缺陷深度或打磨深度超过1mm时,应进行补焊,补焊后打磨平滑。
b.返修后的焊缝,应按原规定的方法进行探伤,并应达到合格标准。
c.焊缝的修补,必须严格按照焊接工艺进行,其修补的长度,不应小于50mm。
d.同一部位的返修次数,不宜超过两次,当超过两次时,必须经施工单位技术总负责人批准。
7.3.附件安装
7.3.1开孔接管的中心位置偏差,不得大于10mm;接管外伸长度的允许偏差为±5mm。
7.3.2开孔补强板的曲率应与罐体曲率一致。
7.3.3接管法兰的密封面应平整,不得有焊瘤和划痕,法兰密封面应与接管的轴线垂直,倾斜不得大于法兰外径的1%,且不得大于3mm,法兰的螺栓孔,应跨中安装。
7.3.4罐体附件应尽量在罐体顶升前安装,以减少高空作业。
7.3.5设备操作平台应地面预制,设备安装前应焊在设备上,随同设备整体吊装;螺旋梯应地面预制,分段安装组焊。
7.3.6加热器安装
7.3.6.1加热器及其支架应在罐外预制,底圈壁板完全封堵以前运入罐内组装。
预制好的加热器应按其形状支撑放置,以防变形。
7.3.6.2加热器弯曲部位不得有拼接焊缝。
拼接用管子的最短长度为6m。
7.3.6.3罐内加热器管的拼接焊缝应100%作X射线探伤。
7.3.6.4分配管与加热器管,管堵间的焊缝必须全焊透,并作磁粉或渗透探伤。
7.3.6.5加热器组装焊接完毕后,应进行水压试验,其试验压力按图纸要求。
8.非标设备检查验收
8.1非标设备检查一般要求项目
8.1.1焊缝应进行外观检查,其表面质量应符合下列规定:
8.1.1.1焊缝表面及热影响区,不得有裂纹,气孔、夹渣和弧坑等缺陷。
8.1.1.2对接焊缝的咬边深度,不得大于0.5mm。
咬边连续长度不得大于100mm,焊缝两侧咬边的总长度,不得超过该焊缝长度的10%。
8.1.1.3设备靠近基础的T型接头内侧角焊缝应平滑过渡,咬边应打磨圆滑。
8.1.1.4罐壁纵焊缝不得有低于母材表面的凹陷;罐壁环缝表面的凹陷深度,不得大于0.5mm。
凹陷连续长度不得大于100mm,凹陷的总长度,不得大于该焊缝总长度的10%。
8.1.2焊缝无损探伤应按施工图要求比例进行。
8.1.2.1贮罐底板无损探伤
a.罐底边缘板,应对每条对接焊缝的外端300mm进行X射线探伤。
b.底板三层钢板重叠部分的搭接接头焊缝根部焊道焊完后,在沿三个方向各200mm范围内应进行渗透探伤。
全部焊完后应进行渗透探伤或磁粉探伤。
c.壁板与边缘板连接的内侧角焊缝应作100%磁粉或渗透探伤。
总体试验后再次探伤。
8.1.2.2壁板无损探伤。
a.纵向焊缝,每一焊工焊接的每种板厚,在最初焊接的3m焊缝的任意部位取300mm进行X射线探伤,以后对每种板厚,不考虑焊工人数,在每30m及其尾数内的任意部位取300mm进行X射线探伤。
探伤部位中的25%应位于丁字焊缝处,且每台罐不少于两处。
b.环向焊缝,每种板厚(以较薄的板厚为准),在最初焊接的3m焊缝的任意部位取300mm进行X射线探伤,以后对于每种板厚,在每60m焊缝及其尾数内的任意部位取300mm进行X射线探伤。
c.贮罐底圈壁板应从每条纵向焊缝中任取两个300mm进行X射线探伤检查,其中一个应靠近底板。
d.壁厚大于10mm的壁板,全部丁字缝均应进行射线探伤。
e.如果射线探伤不合格时,应在该探伤长度的两端延伸300mm作补充探伤,但缺陷部位距底片端部75mm以上者可不再延伸。
如延伸部位的探伤结果仍不合格时,应继续延伸进行检查。
8.1.2.3无损探伤的方法及合格标准
a.射线探伤执行《钢制压力容器对接接头射线照相和质量分级》(JB4730-94),并以Ⅲ级标准为合格。
b.超声波探伤应按国家现行的《锅炉和钢制压力容器对接焊缝超声波探伤》的规定进行,并应以Ⅱ级标准为合格。
c.磁粉探伤应按有关的常压钢制焊接油罐磁粉探伤技术标准的规定进行。
d.渗透探伤标准应按有关的常压钢制焊接油罐渗透探伤技术标准的规定执行。
8.1.3严密性试验
8.1.3.1贮罐底所有焊缝应采用真空箱法进行严密性试验,试验负压值不得低于53KPa,无渗漏为合格。
8.1.3.2开孔补强板焊完后,由信号孔通入100~200KPa压缩空气,检查焊缝严密性,无渗漏为合格。
8.1.4设备几何形状和尺寸检查
8.1.4.1塔类设备允许偏差范围:
a.塔高度允许偏差应符合下表要求:
塔体高度H(m)
H≤30
30<H≤60
允许偏差ΔH(mm)
±30
±40
b.筒体不直度允许偏差应符合下列要求:
筒体长度H()
筒体不直度△L(㎜)
H≤20
≤2H/1000且不大于20
20<H≤30
≤H/1000
30<H≤50
≤35
50<H≤70
≤45
8.1.4.1贮罐应满足下列要求:
a.贮罐高度允许偏差不应大于设计高度的5%,罐壁铅垂度偏差不得大于罐壁高度的4%且不大于50mm。
b.设备上的工卡具焊迹,应清除干净,焊疤应打磨平滑。
c.贮罐顶盖局部凹凸变形,应采用样板检查,其间隙不得大于10mm。
8.1.5水压试验
8.1.5.1水压试验应检查下列内容:
a.罐底严密性
b.罐壁强度及严密性
c.固定顶的强度和严密性
8.1.5.2水压试验应符合下列规定:
a.水压试验前,所有附件及其它与罐体焊接的构件,应全部完工。
b.水压试验前,所有与严密性试验有关的焊缝,均不得涂刷油漆。
c.水压试验应用洁净水,水温不得低于5℃,不锈钢设备试压用水中氯离子含量不得超过25ppm。
8.1.5.3贮罐底板严密性,应以充水试验过程中罐底无渗漏为合格。
8.1.5.4水压试验满足下列要求即为合格:
a.需加压的设备其强度及严密性试验应在设备充满水,待到壁板温度与水温大致相同时缓慢升压到规定的压力保压30分钟,对所有所有焊缝及连接部位进行检查,不渗漏,不降压,无异常变形为合格。
b.盛水试漏设备48小时后无渗漏为合格。
8.1.5.5大型塔类设备试压待设备安装完后进行,必要时只能做气压试验。
9.质量保证措施
9.1严格按施工图及规范要求执行,强化质量管理。
9.2严格执行ISO9002质量管理模式,确立用户至上,质量第一的宗旨。
9.3认真编制施工方案,做好技术交底工作。
9.4把好原材料关,做好材料检验及复验工作。
9.5严把工序质一关,上道工序不合格,不得进入下道工序,严禁不合格品出现。
9.6焊工必须持证上岗,并且在合格期内焊其合格项目。
9.7实行自检、互检、专检相结合,确保施工质量。
9.8所有检测工具,均需经校验合格后方可使用。
9.9确保施工机械完好率在95%以上,严禁带病运转。
9.10在施工过程中,严格执行A、B、C三级检查制度及时办理签字手续。
9.11施工现场应搭设防风沙、防护棚。
9.12下雪时应将罐顶接管堵住,以防水在施工时进入罐内。
雪后应将坡口上的泥砂、锈迹清理干净,并经充分干燥后方可焊接。
10.安全技术措施
10.1施工前进行安全交底,使全体施工人员做到心中有数,防患于未然。
10.2班前提出安全注意事项,班后检查安全隐患。
10.3正确使用个人防护用品,进入施工现场,必须戴安全帽,高空作业必须系安全带,并挂设安全网。
10.4脚手架要搭设牢固,不得搭探头板。
脚手架的选材和铺设应严密、牢