拐臂工艺设计说明书.docx
《拐臂工艺设计说明书.docx》由会员分享,可在线阅读,更多相关《拐臂工艺设计说明书.docx(35页珍藏版)》请在冰豆网上搜索。
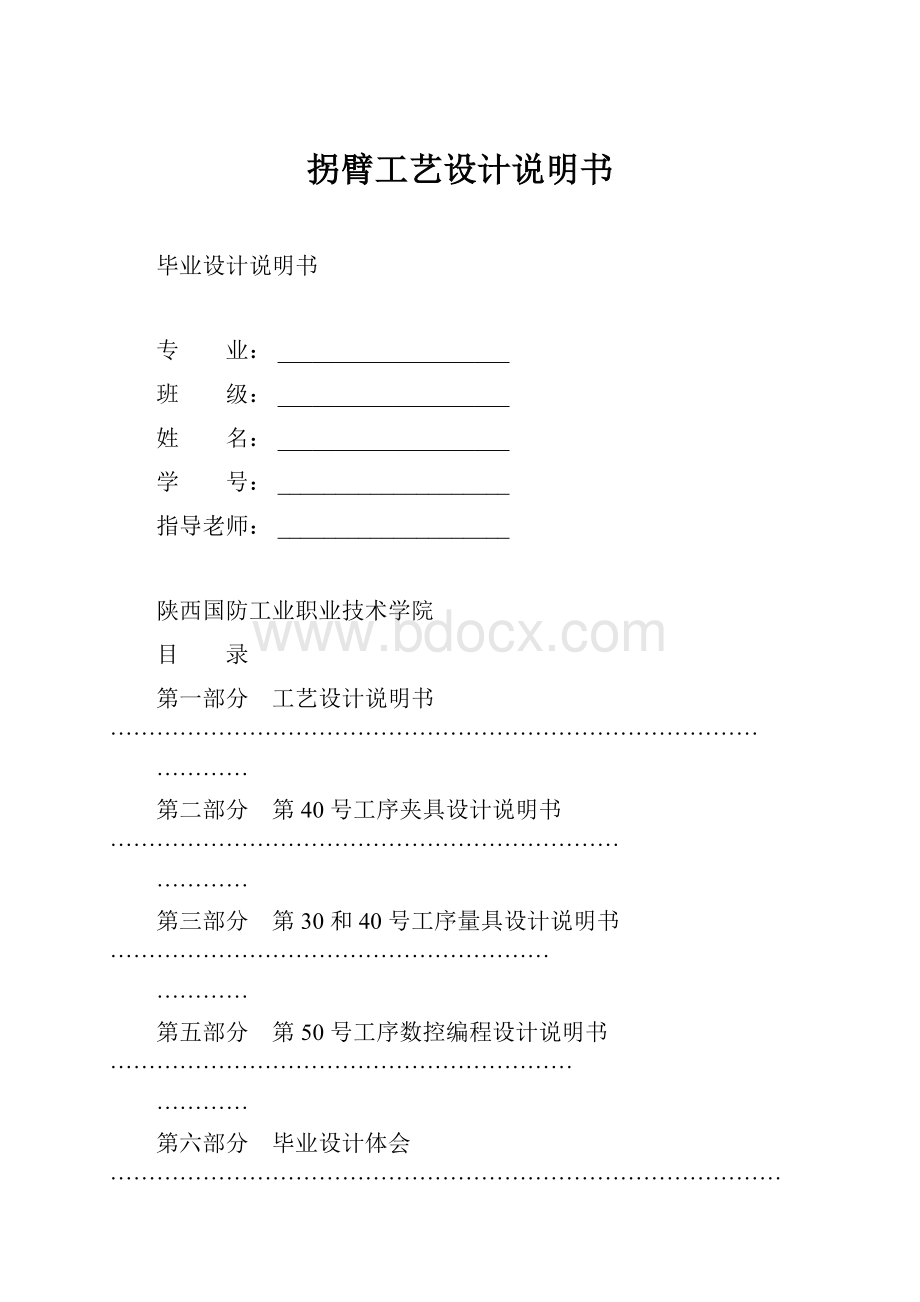
拐臂工艺设计说明书
毕业设计说明书
专 业:
____________________
班 级:
____________________
姓 名:
____________________
学 号:
____________________
指导老师:
____________________
陕西国防工业职业技术学院
目 录
第一部分 工艺设计说明书…………………………………………………………………………
…………
第二部分 第 40 号工序夹具设计说明书…………………………………………………………
…………
第三部分 第 30 和 40 号工序量具设计说明书…………………………………………………
…………
第五部分 第 50 号工序数控编程设计说明书……………………………………………………
…………
第六部分 毕业设计体会……………………………………………………………………………
…………
第七部分 参考资料…………………………………………………………………………………
第一部分 工艺设计说明书
1.零件图工艺性分析
1.1 零件结构功用分析
从标题栏可知:
该零件的名称为拐臂。
拐臂 :
是机器设备上常用的部件之一。
通过螺钉
与其它部件连接以实现连带运动等功能。
其材料为 HT200,属于轮廓类零件。
零件的结构分
析就是从设计要求和工艺要求出发,分析零件不同结构的功用。
1、从设计要求方面看,零件在机
器中,可以起到支撑、容纳、传动、配合、连接、安装和定位等功用,这是决定零件主要结构的依
据。
2、从工艺要求方面看,为了使零件的毛坯制造、加工、测量以及装配和调整工作能顺利、方
便,应设计出圆角、起模斜度、倒角等结构,这是决定零件局部结构的依据。
3、从实用和美观方
面看,不仅要求产品能使用,而且还要求经济、美观等,要从美学的角度来考虑结构形状。
1.2 零件技术条件分析
分析技术要求包括五个方面。
A.加工表面的尺寸精度;B.主要加工表面的形状精度;C.主
要加工表面的相互位置精度;D.加工表面的粗糙度和机械物理性能; E.热处理及其它要求。
分析零件技术要求的目的归结为一点,是保证零件使用性能前提下的经济合理性。
在工程实
际中要结合现有生产条件分析实现这些技术要求的可行性。
分析零件图还包括图纸的尺寸、公差和
表面粗糙度标准是否齐全。
通过对零件形状和主要表面的了解之后,就可以基本形成零件工艺流程.
1.3 零件结构工艺性分析
由零件图可知该零件图由圆弧、孔、直线等几何元素组成,各元素之间关系描述清楚、尺寸标注完
整。
基本内容有:
1.相同圆心主轴直径为 80mm 外圆以及直径为 50mm 的通孔,要求表面粗糙度为 3.2,且保
证外圆的高为 45mm。
2.要求以直径为 80mm 外圆圆心为中心,夹角为120 度,长度为 100mm 点作为圆心距。
要
求连杆两外轮廓半径为 r25,且以相同的圆心加工直径为 25mm 的通孔,其孔表面粗糙度要求
为 3.2,高度为 15mm,且两连杆圆弧连接处圆弧半径为 r25
3.注:
要求加工前划线找正确定该零件的中心,保证外圆高度为45mm 以及连杆高度为
15mm,外圆直径为 80mm 上下表面粗糙度为 3.2,其余表面粗糙度要求为 6.3
4.技术要求:
铸件不允许有裂纹,缩孔等缺陷,加工后的零件不允许有毛刺
5.零件材料为 HT200
材料分析:
材料名称:
灰铸铁
牌号:
HT200
标准:
GB9439-88
最低抗拉强度为 200MPa 的灰铸铁
铸铁级别
较高强度铸铁,基体为珠光体,强度,耐磨性,耐热性均好,减振性也良好,铸造性能较好,
需要进行人工时效处理。
2.毛坯选择
2.1 毛坯类型
毛坯种类的选择不仅影响毛坯的制造工艺及费用,而且也与零件的机械加工工艺和加工质
量密切相关。
正确选择合适的毛坯,对零件的加工质量.材料消耗和加工工时都有很大的影响。
如
果当毛坯的尺寸与零件图尺寸相近时,则就提高了工作效率,但是毛坯制造的成本就越高,所以选
择合适的毛坯需要毛坯制造和机械加工两方面的工艺人员密切配合,合理地确定毛坯的种类、结构
形状,并绘出毛坯图。
毛胚的选择:
1.毛胚种类的选择:
毛胚可分为 a 铸件:
主要用于形状复杂或尺寸较大的毛胚; b 锻件:
主要用于加工余量小,精度高,性能好的毛胚; c 型材:
型材分为热轧和冷轧。
热轧型材
尺寸较大,精度低,多用于一般零件的毛胚尺寸较 ;冷热型材小,精度较高,多用于精度
要求高的中小型零件; d 焊接件 :
通过焊,电焊,气氩弧焊等焊接方式制造毛胚,主要用于
大型零件的单间小批生产中 ;
2.毛胚选择须应考虑的因素 :
a 零件的材料及力学性能; b 零件的结构形状及外形尺寸; c 生
产纲领; d:
生产条件; e 积极推广新工艺,新技术和新材料;
根据零件图的结构形状及外形尺寸分析,该零件外形结构多为轮廓,不易与加工方便且零件
的材料为 HT200,生产批量为小批量。
综合 1(a)2(a)故选用铸件为该零件的毛胚类型。
3.选择设备:
根据零件图分析可得:
该零件属于轮廓类零件,外形结构复杂且不适于一次完成该工序所有
工步,所以故选用复合型数控加工中心
加工中心的特点:
综合加工能力较强,工件一次装夹后能完成较多的加工内容,加工精度
较高,就中等加工难度的批量工件,其效率是普通设备的5~10 倍,特别是它能完成许多
普通设备不能完成的加工,对形状较复杂,精度要求高的单件加工或中小批量多品种生产更
为适用。
在加工中心上加工零件的特点是:
被加工零件经过一次装夹后,数控系统能控制机床按不同
的工序自动选择和更换刀具;自动改变机床主轴转速、进给量和刀具相对工件的运动轨迹及
其它辅助功能,连续地对工件各加工面自动地进行钻孔、锪孔、铰孔、镗孔、攻螺纹、铣削
等多工序加工。
由于加工中心能集中地、自动地完成多种工序,避免了人为的操作误差、减
少了工件装夹、测量和机床的调整时间及工件周转、搬运和存放时间,大大提高了加工效率
和加工精度,所以具有良好的经济效益
2.2 毛坯余量确定
加工余量是指加工过程中所切去的金属层厚度。
余量有总加工余量和工序余量之分。
金属
层。
工序余量是相邻两工序的工序尺寸之差,毛坯余量是毛坯尺寸与零件图样的设计尺寸之差。
由于工序尺寸有公差,故实际切除的余量大小不等。
余量的确定有三种
(1)经验估算法。
(2)查
表修正法。
(3)分析计算法。
该零件要求表面粗糙度为 3.2,尺寸要求较严格而且公差范围较小,故余量选择较为谨慎,
根据公式确定铸件毛坯时余量为单边 2mm,由机械手册查得:
铸件单边余量为 2mm 不能达到尺寸要
求,由计算得单边余量应大于等于为 4mm,所以选择 4mm 即可.需粗加工和精加工来完成。
所以本图
采用查表修正法。
2.3 毛坯-零件合图草图
3.机加工工艺路线确定
3.1 加工方法分析确定
该零件图有圆弧、孔、直线等几何元素组成,各元素之间关系描述清楚、尺寸标注完整,拐
臂厚 40mm、中心孔为 50mm,两边为孔 Φ25,且均为通孔,表面粗糙度要求较高、公差要求严格,
零件采用工序集中,工序集中就是将零件的加工集中在少数几道工序中完成,每道工序加工内容多,
工艺路线短。
根据零件图的分析加工顺序的拟定按照基面先行,先粗后精,先面后孔,先主后次
的原则确定,根据零件图和余量的选择,故该图一面两孔的定位原则。
3.2 加工顺序的安排(宋体、加黑、小四)
方案一:
1:
粗精铣 A 平面台阶,达到精度技术要求;
2:
粗精铣 B 平面台阶,达到精度技术要求;
3:
中心钻钻内孔为直径 50 的孔,达到精度技术要求;
4:
中心钻钻内孔为直径 25 的孔,达到精度技术要求;
5:
扩 2*25 的孔,以及直径为 50 的孔;
6:
:
铰 2*25 的孔;
7:
粗精铣外轮廓;
8:
钳工去毛刺;
9:
检验;
10:
入库;
方案二:
1:
粗精铣 B 平面台阶,达到精度技术要求;
2:
中心钻钻内孔为直径 50 的孔,达到精度技术要求;
3:
扩 Φ50 的孔,达到精度技术要求;
4:
粗精铣 A 平面台阶,达到精度技术要求;
5:
中心钻钻内孔为直径 25 的孔,达到精度技术要求;
6:
扩 2*25 的孔
7:
铰 2*25 的孔
8:
粗精铣外轮廓,达到精度要求;
9:
钳工去毛刺;
10:
检验;
11:
入库;
方案三 :
1:
粗,精铣 A 面,达到精度要求;
2:
粗精铣外轮廓,达到精度要求;
3:
粗精铣外圆 80,达到精度要求;
4:
粗精铣孔 25A 表面,达到精度要求;
5:
翻身粗精铣 B 面,达到精度要求;
6:
粗精铣外圆 80,达到精度要求;
7:
粗精铣孔 25B 表面,达到精度要求;
8:
粗精铣外轮廓,达到精度要求;
9:
中心钻钻内孔为直径 50 的孔,以及 2*直径为 25 的孔;
10:
扩 2*25 的孔,以及直径为 50 的孔;
11:
铰 2*25 的孔;
12:
钳工去毛刺;
13:
检验;
14:
入库。
以上两种加工方案,根据加工理论的合理性,与一般人的加工零件的习惯等,经过对比方案一
比较合理,因为此方案遵循了基面先行,先粗后精,先面后孔的原则,同时也保证了孔的同轴度,
故选择第一种方案为加工该零件图的方案。
3.3 定位基准选择
一:
粗基准选择原则
选择粗基准时应该遵循以下几种要求:
(1)以工件中重要表面的加工余量小而均匀,则应选择该表面为粗基准。
所谓重要表面一般
是工件上加工精度以及表面质量要求较高的表面,如床身的导轨面,车床主轴箱的主轴孔,都是各
自的重要表面。
因此,加工床身和主轴箱时,应以导轨面或主轴孔为粗基准。
(2)选择不加工表面为粗基准为了保证加工面与不加工面间的位置要求,一般应选择不加
工面为粗基准。
如果工件上有多个不加工面,则应选其中与加工面位置要求较高的不加工面为粗基
准,以便保证精度要求,使外形对称等。
毛坯孔与外圆之间偏心较大,应当选择不加工的外圆为粗
基准,将工件装夹在三爪自定心卡盘中,把毛坯的同轴度误差在镗孔时切除,从而保证其壁厚均匀。
(3)选择加工余量最小的表面为粗基准在没有要求保证重要表面加工余量均匀的情况下,
如果零件上每个表面都要加工,则应选择其中加工余量最小的表面为粗基准,以避免该表面在加工
时因余量不足而留下部分毛坯面,造成工件废品。
(4)选择较为平整光洁、加工面积较大的表面为粗基准 以便工件定位可靠、夹紧方便。
(5)粗基准在同一尺寸方向上只能使用一次因为粗基准本身都是未经机械加工的毛坯面,
其表面粗糙且精度低,若重复使用将产生较大的误差。
实际上,无论精基准还是粗基准的选择,
上述原则都不可能同时满足,有时还是互相矛盾的。
二:
精基准的选择原则
当用夹具安装工件时,定位 基准的选择还会影响到夹具结构的复杂程度。
因此,定位基准的
选择是一个很重要的工艺问 题。
选择定位基准时,是从保证工件加工精度要求出发的,因此,定
位基准的选择应先选择 精基准,再选择粗基准。
选择精基准时,主要应考虑保证加工精度和工件
安装方便可靠。
其选择原则如下:
(1) 基准重合原则 即选用设计基准作为定位基准,以避免定位基准与设计基准不重合而引起
的基准不重合误差。
(2) 基准统一原则 应采用同一组基准定位加工零件上尽可能多的表面,这就是基准统一原则。
这样做可以简化工艺规程的制订工作,减少夹具设计、制造工作量和成本,缩短生产准备周期;由
于减少了基准转换,便于保证各加工表面的相互位置精度。
例如加工轴类零件时,采用两中心孔定
位加工各外圆表面,就符合基准统一原则。
箱体零件采用一面两孔定位,齿轮的齿坯和齿形加工多
采用齿轮的内孔及一端面为定位基准,均属于基准统一原则。
(3) 自为基准原则某些要求加工余量小而均匀的精加工工序,选择加工表面本身作为定位基
准,称为自为基准原则。
(4) 互为基准原则 当对工件上两个相互位置精度要求很高的表面进行加工时,需要用两个表
面互相作为基准,反复进行加工,以保证位置精度要求。
例如要保证精密齿轮的齿圈跳动精度,在
齿面淬硬后,先以齿面定位磨内孔,再以内孔定位磨齿面,从而保证位置精度。
再如车床主轴的前
锥孔与主轴支承轴颈间有严格的同轴度要求,加工时就是先以轴颈外圆为定位基准加工锥孔,再以
锥孔为定位基准加工外圆,如此反复多次,最终达到加工要求。
这都是互为基准的典型实例。
(5) 便于装夹原则 所选精基准应保证工件安装可靠,夹具设计简单、操作方便.
因此,对于对于该零件得基准选择时要考虑粗精基准的选择原则,主要保证加工精度和工件安
装方便可靠。
根据该图的零件分析其选择原则为基准重合原则。
即选用设计基准作为定位基准,以
避免定位基准与设计基准不重合而引起的基准不重合误差。
该图若采用基准不重合的定位方案,必
须控制该工序的加工误差和基准不重合误差的总和不超过尺寸和公差,这样既缩小了本道工序的加
工允差,又对前面工序提出了较高的要求,使加工成本提高,当然是应当避免的。
所以再选择定位
基准时,应当尽量使定位基准与设计基准相重合.
3.4 加工阶段的划分说明
从零件图上分析,该零件主要用于铣削加工,钻削加工。
依据机械加工工艺的基本原则:
工步的划分主要从加工精度和效率两方面考虑。
在一个工序内往往需要采用不同的刀具和切削
用量,对不同的表面进行加工。
为了便于分析和描述较复杂的工序,在工序内又细分为工步。
1)同一表面按粗加工、半精加工、精加工依次完成,或全部加工表面按先粗后精加工分开进行。
2)对于既有铣面又有镗孔的零件,可先铣面后镗孔,使其有一段时间恢复,可减少由变形引起的
对孔的精度的影响。
3)按刀具划分工步。
某些机床工作台回转时间比换刀时间短,可采用按刀具划分工步,以减少换
刀次数,提高加工生产率。
总之,工序与工步的划分要根据具体零件的结构特点、技术要求等情
况综合考虑。
另外为了保证工件通常在一次安装中,不允许将零件某一部分表面加工完毕后,再加
工零件的其他表面。
按所用刀具划分工序为了减少换刀次数,压缩空程时间,减少不必要的定位
误差,可按刀具集中工序的方法加工零件,即在一次装夹中,尽可能用同一把刀具加工出可能加工
的所有部位,然后再换另一把刀加工其他部位。
对于该零件图而言:
1 先基面后其他表面
2 先粗后精
3 先主后次
4 先面后孔
热处理工序的安排:
热处理的目的是提高材料的力学性能,消除毛胚制造及加工过程中的内应
力,改善材料的切削加工性能。
1需进行预备热处理,一般在粗加工前对含碳量大于 0.7%的碳钢和合金钢采用退火以降低硬
度;含碳量小于 0.5%的碳钢和合金钢采用正火提高材料的硬度。
在切削时切削不沾刀,工件表面
比较光滑。
2 最终热处理:
最终热处理的主要目的是提高零件的硬度和耐磨性。
还需要进行一些辅助工序的安排:
辅助工序安排包括:
检验、去毛刺、倒角、退磁、清洗和防
锈工作等。
大批量生产结构较复杂的零件,适合采用工序集中的原则,可以采用改装通用设备或采用专用
机床或多刀,多轴自动机床以提高生产率。
选择设备时应考虑的问题是:
1 机床的精度与工序要求的精度相适应。
2 机床的规格与工件的外形尺寸,本工序的切削用量相适应。
3 机床的生产效率与被加工零件或产品的生产类型相适应。
4 选择的设备应尽可能的与工厂现有的条件相适应。
3.5 主要机加工工序简图
1.粗精铣 A 平面
2.粗精加工 B 平面
3.粗精加工直径 50 孔
4.粗精加工直径 25 孔
5.粗精加工外轮廓
4.工序尺寸及其公差确定
4.1 基准重合时工序尺寸确定
工序尺寸及公
工序名称工序加工余量
/mm
加工经济精度
/mm
经济粗糙度
/um
工序基本尺寸
/mm
差
/mm
尺寸及偏差
环 名
基本尺寸
A/mm
上偏差
ES/mm
下偏差
EI/mm
→
LI
12.5
0.18
-0.18
→
L2
15
0.12
-0.12
→
L3
40
0.3
-0.3
铰孔
0.2
IT4
1.6
25
+0.0016
50 0
扩孔
0.4
IT8
3.2
24.8
+0.0032
24.8 0
镗孔
4.4
IT10
6.3
24.4
+0.0063
24.4 0
钻孔
IT12
12.5
20
+0.0125
20 0
4.2 基准不重合时工序尺寸确定
所要加工零件有圆弧和直线相交,带有角度孔,有较高的精度要求,普通铣床不容易保证精
工步号
刀具号
刀具规格名
称
数量
加工表面
备注
1
T01
铣刀
1
铣端面
2
T02
镗刀
1
镗孔
3
T03
麻花钻
1
钻孔
φ20
4
T04
扩刀
1
扩孔
5
T05
铰刀
1
铰孔
度和形状。
根据零件图分析,该零件图应该在镗铣床上依次完工,根据基面先行,先粗后精,先面
后孔,先主后次的原则,先粗精加工 AB 面,然后加工预制孔,最后粗精加工直径为 25 的孔,尺
寸要求和表面粗糙度要求,故不易在一台设备上完成,所以要选择镗床与铣床来加工。
零件加工的
机床选择 XK52k 型数控立式升降台铣床。
Xk52k 型数控立式升降台铣床的特点
(1)该铣床由端面铣刀、立铣刀、圆柱铣刀、锯片铣刀、圆片铣刀、端面铣刀及各种成形铣
刀来加工各种零件。
适于加工各种零件的平面、斜面、沟槽、孔等,是机械制造、模具、仪器、仪
表、汽车、摩托车等行业的理想加工设备。
(2)机床具备了足够的功率和刚性以及有较大的调速范围(主轴转速和进给量),因此可充分
利用硬质合金刀具来进行高速切削。
(3)铣床底座、机身、工作台、中滑座、升降滑座、主轴箱等主要构件均采用高强度材料铸
造而成,并经人工时效处理,保证机床长期使用的稳定性。
立式铣床立铣头可在垂直平面内顺、
逆回转调整±45°,拓展机床的加工范围;主轴轴承为圆锥滚子轴承,承载能力强,且主轴采用能耗
制动,制动转矩大,停止迅速、可靠。
(4)该铣床工作台 X/Y/Z 向有手动进给、机动进给和机动快进三种,进给速度能满足不同的
加工要求;快速进给可使工件迅速到达加工位置,加工方便、快捷,缩短非加工时间。
立式铣床
X、Y、Z 三方向导轨副经超音频淬火、精密磨削及刮研处理,配合强制润滑,提高精度,延长机
床的使用寿命。
(5)立式铣床润滑装置可对纵、横、垂向的丝杠及导轨进行强制润滑,减小机床的磨损,保
证机床的高效运转;同时,冷却系统通过调整喷嘴改变冷却液 流量的大小,满足不同的加工需求。
立式铣床设计符合人体工程学原理,操作方便;操作面板均使用形象化符号设计,简单直观。
夹具的选择:
加工零件外轮廓时,需要采用一面两孔进行定位装夹,需要专用夹具加工其他部分
时,通用夹具能保证加工要求。
(3)量具的选择:
由于 ø6 孔加工精度高,又是中批生产,所以选用塞规比较合适。
塞规是由自己设计。
(4)刀具的选择:
切削用量是指切削速度 、进给量 f (或进给速度 vf)和背吃刀量 ap 三者的总称,可称为切
削用量三要素。
已知加工材料为 HT200,机床为 XK52k,工件用专用夹具定位。
以粗铣时的切削用量的确
定为例:
1.确定背吃刀量总的加工余量为(45.3-40)/2=2.65MM,为精加工留 0.5MM 的余量,
则背吃刀量为 2.65-05=2.15MM。
2.确定进给量背吃刀量确定后,进给量主要受刀杆,工件及机床进给机构等的强
度,刚性的限制,一般查表得到。
F=84MM/MIN。
加工内容
主轴转速
切削速度
进给量
切削深度
进给次数
r/min
m/min
mm/r
mm
粗铣 A
800
125.6
84
3.45
2
精铣
1200
150.72
140
0.5
1
粗铣 B
800
125.6
84
3.45
2
精铣
1200
150.72
140
0.5
1
粗镗
1000
120
80
4.4
4
精镗
1500
47
50
0.45
2
扩孔
600
46.5
80
15
3
粗铰
500
39.1
69
15
1
精铰
600
47.1
105
15
1
粗铣
800
125.6
84
15
3
精铣
1200
47
50
15
1
3.确定切削速度确定了进给量和背吃刀量后,一般查表得到切削速度
V=125.6M/MIN。
所以可以得到主轴转速 n:
n=1000v/∏d=800r/min
4.效验机床功率查表背吃刀量为 2.65-
05=2.15MM,F=120MM/MIN,V=125.6M/MIN 时机床的功率为 2.0KW。
切削功率的所有修正系数之积为.17X1.0X1.0X1.0X1.13X0.8X0.65=0.687 故实际的
切削功率为 1.374KW>7.5KW(机床的额定功率),所以可以在 XK8140A 上进行加工。
其他切削用量的确定
Ti 是基本时间Tf 是辅助时间Tz 是准备与终结时间N 是件数
以精铰(ø 50)时的工时定额为例:
T=LI/FI 一般为 1
L=L1+L2+L3L1 是孔的深度 40MM,L2 是切削刃到工件的距离
2.35,L3 一般为 2-4MM,取 3MM。
T=45.35/1.2=37.79s 即约等于 38s
因为要下两次刀中间要有足够的停留时间,故大约要 2.5MIN。
7.工艺设计总结
我们这次所做的课程设计是由圆、顺逆圆弧面等几部分组成,是数控加工可选择的内容。
在数
控加工工艺课程设计指导书对加工内容的选择做了要求,因为我们的图形做特殊的表面粗糙度要求,
而一般零件取表面精度为七级精度,毛坏的选择也很重要,零件村料的工艺特性和力学性能大致决
定了毛坯的种类。
零件的结构形状与外形尺寸也是重要因素。
大型且结构简单的零件毛坯多用砂型
铸造或自由锻;轴类零件的毛坯,若台阶直径相差不大,可用棒料;若各台阶尺寸相差较大,则宜
选择锻件。
但是根据我们现在的实际情况是做课程设计及现在的我们这次课程设计让我们对以往学
习过的知识进行了再学习和巩固。
其中涉及到多门专业课。
如《机械制造》、《数控工艺》、《数
控编程》等。
通过这次课程设计我们真正学会了自主学习,独立完成作业,如何学会与自己的团队
做好协调。
因为课程设计具有实践性、综合性、探索性、应用性等特点。
本次选题的目的是数控专
业教学体系中构成数控技术专业知识及专业技能的重要组成部分,是运用数控机床实际操作的一次
综合练习。
随着课程设计的逐渐完成,使我对《数控加工工艺》这门课程以及对数控加工技术都有
了更深入的理解和掌握。
在这段时间里,我们这个小组,就是新建的团队,每个人都是一样,尽着
自己最大的努力学习,来学习和创新。
为了解决技术上的问题,我也不断地去翻阅所学的专业书籍
和各种相关的资料。
这使我真正体会到了很多,也感受到了很多,当然更重要的是学习到了以前书
本上没学