软包装行业如何有效治理VOCs.docx
《软包装行业如何有效治理VOCs.docx》由会员分享,可在线阅读,更多相关《软包装行业如何有效治理VOCs.docx(10页珍藏版)》请在冰豆网上搜索。
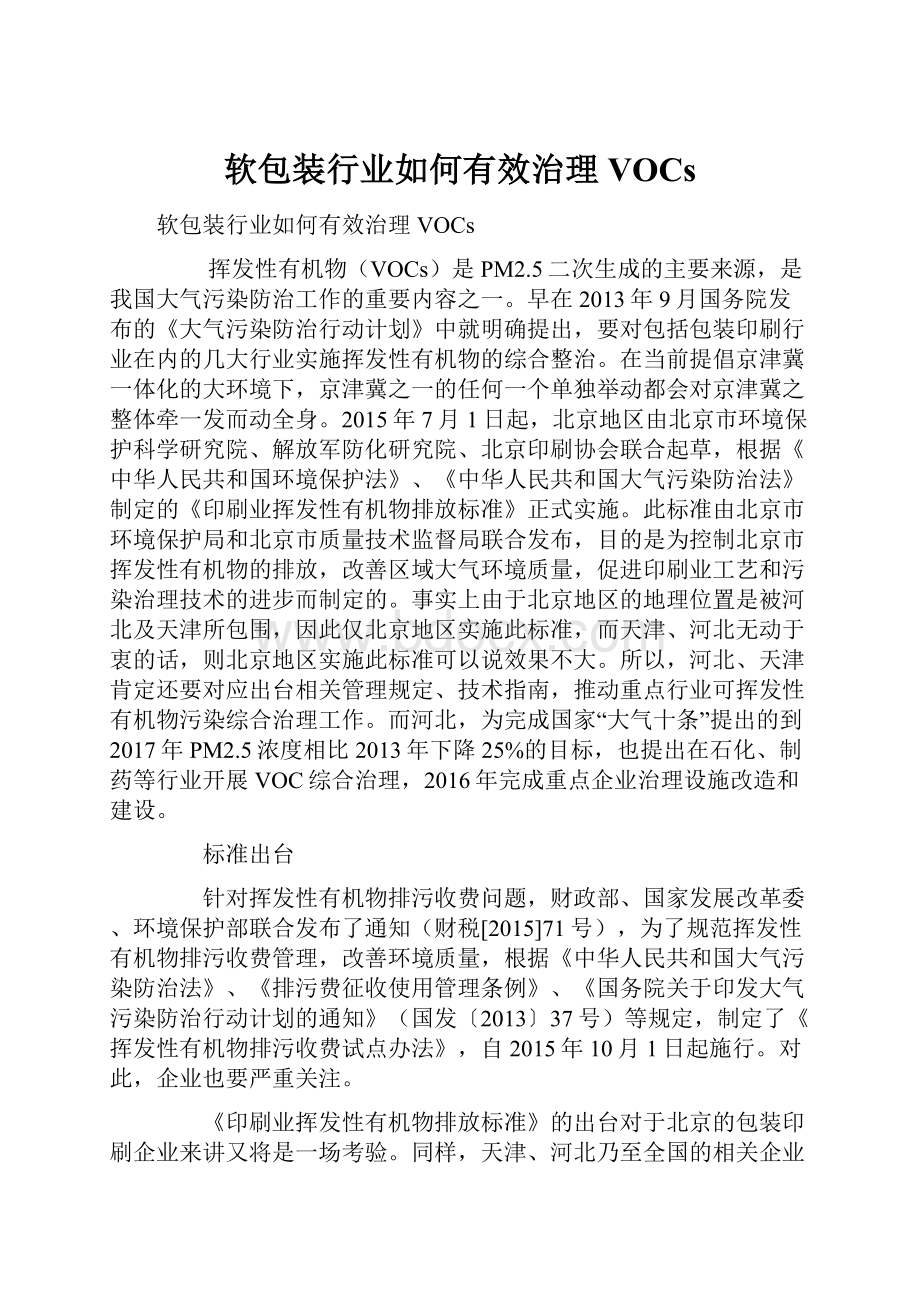
软包装行业如何有效治理VOCs
软包装行业如何有效治理VOCs
挥发性有机物(VOCs)是PM2.5二次生成的主要来源,是我国大气污染防治工作的重要内容之一。
早在2013年9月国务院发布的《大气污染防治行动计划》中就明确提出,要对包括包装印刷行业在内的几大行业实施挥发性有机物的综合整治。
在当前提倡京津冀一体化的大环境下,京津冀之一的任何一个单独举动都会对京津冀之整体牵一发而动全身。
2015年7月1日起,北京地区由北京市环境保护科学研究院、解放军防化研究院、北京印刷协会联合起草,根据《中华人民共和国环境保护法》、《中华人民共和国大气污染防治法》制定的《印刷业挥发性有机物排放标准》正式实施。
此标准由北京市环境保护局和北京市质量技术监督局联合发布,目的是为控制北京市挥发性有机物的排放,改善区域大气环境质量,促进印刷业工艺和污染治理技术的进步而制定的。
事实上由于北京地区的地理位置是被河北及天津所包围,因此仅北京地区实施此标准,而天津、河北无动于衷的话,则北京地区实施此标准可以说效果不大。
所以,河北、天津肯定还要对应出台相关管理规定、技术指南,推动重点行业可挥发性有机物污染综合治理工作。
而河北,为完成国家“大气十条”提出的到2017年PM2.5浓度相比2013年下降25%的目标,也提出在石化、制药等行业开展VOC综合治理,2016年完成重点企业治理设施改造和建设。
标准出台
针对挥发性有机物排污收费问题,财政部、国家发展改革委、环境保护部联合发布了通知(财税[2015]71号),为了规范挥发性有机物排污收费管理,改善环境质量,根据《中华人民共和国大气污染防治法》、《排污费征收使用管理条例》、《国务院关于印发大气污染防治行动计划的通知》(国发〔2013〕37号)等规定,制定了《挥发性有机物排污收费试点办法》,自2015年10月1日起施行。
对此,企业也要严重关注。
《印刷业挥发性有机物排放标准》的出台对于北京的包装印刷企业来讲又将是一场考验。
同样,天津、河北乃至全国的相关企业都要意识到印刷行业在环保问题上面临的严峻形势。
积极应对,提前做好准备,并抓紧时间研究实施治理方案。
VOCs排放国家标准制定思路主要遵循四大原则:
一是全过程控制原则:
包括源头、生产控制、末端。
源头控制即制定印刷油墨中VOCs含量限值;生产过程控制即制定印刷包装生产管理要求;末端控制即制定VOCs有组织排放和无组织排放限值。
二是差异化原则:
包括工艺、时间、技术,区域。
工艺差异即工艺之间、承印材料之间的差异;时间差异即现有企业与新建企业的差异;技术差异即源头控制与末端控制的差异;区域差异是指重点区与非重点区的差异。
其中,工艺之间的差异主要指柔印、凹印、网印以及复合工艺VOCs排放浓度限值的差异;承印材料的差异则主要指透气承印材料与不透气承印材料的差异;这直接关系到源头控制的要求,即实施水性化的可能性。
三是指向性原则:
即VOCs控制指标主要指向使用量大、毒性大和光化学反应活性强的物质,如苯、甲苯、二甲苯、总VOCs等的排放限值。
四是可行性原则:
包括最佳可行治理技术和最佳清洁生产技术。
可见,软包装行业VOCs排放控制刻不容缓。
软包装企业必须赶紧行动起来,否则只能在行业的新一轮洗牌中面临被淘汰的命运。
标准规定的VOCs排放控制要求对软包装印刷行业来说,在印刷材料方面,标准规定了挥发性有机物的含量上限,凸版和凹版油墨≤30%。
设备或车间排气筒的具体高度及距周围建筑物的距离按批复的环境影响评价文件确定,且不应低于15m。
印刷生产活动中,排气筒排放的挥发性有机物浓度要求如下表所示:
单位:
mg/m3
污染物项目I时段II时段
苯0.50.5
甲苯与二甲苯合计1510
非甲烷总烃5030
时段划分及无组织排放监控点浓度限值:
单位:
mg/m3
监控位置苯甲苯与二甲苯合计非甲烷总烃
I时段II时段I时段II时段I时段II时段
厂界0.10.10.50.22.01.0
印刷生产场所0.10.12.01.06.03.0
现有污染源,自本标准实施之日起至2016年12月31日止执行第Ⅰ时段的排放限值,自2017年1月1日起执行第Ⅱ时段的排放限值及4.2的标准要求。
新建污染源,自本标准实施之日起执行第Ⅱ时段的排放限值及4.2的标准要求。
此外,标准明确了印刷油墨挥发性有机物含量检测、排气筒监测、无组织排放监测,以及挥发性有机物测定方法。
标准的出台确实是完善了VOCs治理的相关政策,有利于环保部门监管工作的开展,推动了北京印刷业VOCs治理进入了实质性治理阶段。
在一定程度上控制了北京市挥发性有机物的排放,对改善区域大气环境质量,促进印刷行业工艺和污染治理技术的进步产生重要影响,同时对全国印刷业也产生了强大的示范带动效应。
标准的实施加速了包装印刷业的格局变换,包装印刷在生产过程中,会有废气、废液等排放对环境造成负面影响,该政策实施以后,部分规模小、技术水平落后、污染严重的企业将遇到生存危机,甚至被淘汰出局。
而那些关注绿色包装印刷、在环保方面有持续投入的印刷包装企业则不受影响,并可能获得更多发展机遇。
印刷包装企业要认识到节能、减排、创新的重要性,积极承担起企业的社会责任,下一步,不光北京,天津、河北乃至全国其它省市区或将有更多相关标准和政策出台。
解决之道
针对北京的这个标准,软包装印刷包装企业如何应对呢?
该标准属于全文强制。
其可执行性是很高的。
而且是从VOCs全过程控制出发,将排放限值和管理要求相结合,包括对有组织排放和无组织排放提出具体的工艺和管理要求,企业要做什么,企业怎么做,标准都做出了明确的要求:
如:
油墨、清洗剂、胶黏剂、有机溶剂等含挥发性有机物的原辅材料在储存和输送过程中应保持密闭,使用过程中随取随开,用后应及时密闭,以减少挥发。
使用含挥发性有机物原辅材料的生产活动(清洗、调墨等)及设备(印刷机、覆膜机、复合机等)产生的挥发性有机物应通过局部或整体集气系统导入挥发性有机物处理设备或排放管道,达标排放。
以上两点,企业可以并且必须做到。
采用非原位再生吸附处理工艺,应按审定的设计文件要求确定吸附剂的使用量及更换周期,每万m3/小时设计风量的吸附剂用量不应小于1m3,更换周期不应长于1个月。
购买吸附剂的相关合同,票据至少保存三年。
这些企业可以并必须做到。
废吸附剂应交由持有危险废物经营许可证的单位进行处置或综合利用,相关的合同、票据至少保存三年。
在这里要求国家或行业应该设立持有危险废物经营许可证的单位来处理废吸附剂。
废油墨、废清洗剂、废溶剂、沾有油墨或溶剂的棉纱抹布等废弃物应放入具有标识的密闭容器中,定期处理,并记录处理量和去向。
应做以下记录,内容必须包括但不限于:
记录中的编码规则、印刷工艺和承印物种类(金属、塑料、纸等)、每月每个工序所使用的油墨、稀释剂、胶黏剂、清洗剂等含挥发性有机物原辅材料的种类和总量、每种原辅材料中挥发性有机物的含量、烘箱温度、安装挥发性有机物处理设备的工作情况等。
并要求记录至少保存三年。
以上讨论的都是北京地区相关企业必须执行的。
那么非北京地区尤其是北京周边区域天津、河北等地如何应对呢?
要达到治本的效果,建议从以下几方面考虑:
材料方面
1.采用水性油墨,杜绝VOCS排放。
水性油墨应用主要以柔性版印刷和凹版印刷为主。
目前国内水性凹印油墨在包装纸、纸盒等产品印刷中已经很广泛.这是由于纸制品蒸发干燥和吸收干燥较好的原故。
水性油墨应用于柔版印刷,目前在国内发展也很快,水性油墨在柔印中占的比例与日俱增,但水性凹版油墨应用于塑料薄膜印刷,国内尚处于起步阶段。
塑料薄膜水性凹版印刷油墨有其特点优势:
(1)不污染大气环境
VOCs被公认为当今全球大气污染的主要污染源之一。
由于水性油墨用水作溶解载体,所以无论是在其生产过程中.还是被用于印刷时,几乎不会向大气散发挥发VOCs,这是其他油墨所无法比拟的。
对于低浓度VOCs的处理,目前只有极少数包装印刷厂采用如活性炭吸附方式处理,但投资大,运营维护成本高,回收后的溶剂含水高,处理成本高。
大多数企业都选择直接排入大气。
不仅如此,在印刷过程中,溶剂型油墨中的有机溶剂几乎完全被干燥而快速挥发出来,除了在印刷机上方的高浓度VOCs被采用如催化燃烧处理工艺处理外,弥漫在印刷车间空气中的低浓度VOCs往往被直接排入大气。
如果按照溶剂型油墨中有机溶剂所占比例为25%~35%计算,其直接排入大气环境的VOCs数量相当惊人。
而水性油墨恰恰克服了这一缺点,这一独有的对大气环境无污染的特点,正在被越来越多的印刷包装企业所看好。
(2)减少资源消耗和降低环保成本
水性油墨有一个固有的特性--固含量较高。
因此相对于溶剂型油墨。
它的涂布量(单位印刷面积所消耗的油墨量)要少一些。
经试验,与溶剂型油墨相比,水性油墨可减少约10%~30%的涂布量。
也就是说印刷相同数量和规格的印刷品,水性油墨的消耗量较溶剂型油墨减少了约10%~30%。
由于印刷时需要经常清洗印版,因此使用溶剂型油墨印刷,需要使用大量的有机溶剂清洗液,而使用水性油墨印刷,清洗的介质则主要是水。
从资源消耗的角度看,水性油墨更加经济,符合当今世界提倡的节约型社会的主题。
(3)减少印刷品表面残留毒物
水性油墨不含有机溶剂,使得印刷品表面残留的有毒物质大大减少。
这一特性在烟、酒、食品、饮料、药品、儿童玩具等卫生条件要求严格的包装印刷产品中,更体现了良好的健康安全性。
如今人类越来越重视食品安全,对包装材料和包装印刷的有害物质残留量也要求严格,因此,使用水性油墨是一个相当好的选择。
(4)提高了作业环境的安全性
有机溶剂和溶剂型油墨本身是易燃液体,有机溶剂很容易挥发,在空气中会形成爆炸性混合气体,因此,溶剂型油墨在其生产制造过程中和印刷时都相当危险。
按照中国目前的法规,溶剂型油墨的生产属于危险化学品生产。
必须具备完善的危险化学品的生产和管理条件,才能取得生产许可证。
有机溶剂特有的毒性对于生产作业人员的健康极为不利,国家卫生监督行政部门将此类作业定义为职业危害性作业。
同时,对作业现场空气中的VOCs浓度有严格规定,作业人员需定期做职业健康体检,以保障接触操作人员的健康。
而使用水性油墨印刷可有效解决这一问题,大大提高了操作工人作业环境的安全性。
通过分析水墨印刷实例,可以总结出软包装厂对凹版水性油墨的选择和要求:
水性油墨性价比要好、色浓度要高、色相稳定、高光泽、黏度要低、附着牢度要高、干燥要快、能够适应低、中、高速印刷的需要。
未来。
性价比高、能够低、中、高速印刷、印品性能优异的塑料薄膜水性凹版油墨将是替代溶剂型油墨,减少醇溶型油墨的凹版印刷发展的必然趋势。
2.采用光固化油墨。
光固化油墨以紫外线固化为特征。
其特点是:
瞬间固化,可以节省空间,缩短生产周期。
低温固化,适用于各种基材,尤其是薄膜。
高固含量,基本无溶剂,防止环境污染。
耐摩擦、耐溶剂、耐热性等均满足普遍要求。
光固化油墨的缺点是成本高,油墨储存期短。
3.采用水性黏合剂。
食品软包装用的水性黏合剂主要是以聚氨酯聚合物和聚丙烯酸为主要成分、以水为分散介质的黏合剂。
此类水性黏合剂具有良好的耐热性、耐介质性,与多数复合基材有良好的亲和性。
生产工艺复杂,技术含量高,不同厂家的产品其性能差异性比较大。
因此选用这类黏合剂时,一定要根据复合产品的具体要求,通过与黏合剂供应厂商充分沟通,对相关资料进行认真地分析研究,筛选出适合自己的品种。
在聚氨酯水性黏合剂和聚丙烯酸水性黏合剂中,以聚氨酯水性黏合剂性能更佳,不足之处是成本较高。
设备方面
采用与水性油墨配套的印刷设备。
原有凹印机不是为水性油墨准备的。
原有凹印机烘箱烘道长度为1米-1.5米,原印版均为深版,原有墨槽无法清洗。
原温控设施不配套,导致彩印厂不愿意也不容易进行改进。
现在已有多家公司正研究生产专用于水性油墨的凹印机。
环保的水性油墨与柔性版印刷,在应用在软包装印刷上尚有一些不如人意之处。
目前多数企业和软包装用户仍然青睐传统的凹印技术。
此处推荐治标的方法是,严格按照标准要求执行。
在包装设计、材料、设备、工艺等方面进行如下改进:
设计方面
改进设计理念,在软包装图案的装潢设计上,理想的方法是尽量减少印刷色数,直接的效果就是减少了油墨的用量。
工艺方面
首先可以配套溶剂回收系统。
当然这面临着回收方式众多,效果不一的问题,企业应选择最适合自己的一种。
现在有专业的投资运营公司负责投资配套吸附回收治理设备,并负责承担设备投资、运营管理、部分设备运营费用等。
企业只承担公用工程和部分设备运行费用。
其次建议采用无溶剂复合工艺,解决了干法复合造成的溶剂排放问题。
无溶剂复合工艺较之干法复合工艺具有如下主要优势:
1.节约资源显著。
不使用溶剂;没有烘道干燥过程,可节约大量能源;上胶量少,无溶剂复合单位面积黏合剂涂布量约为干法复合单位面积黏合剂干基涂布量的2/5。
2.环保适应性好。
无溶剂复合使用的黏合剂不含任何溶剂,因而在生产过程中,除停机时需要用少量溶剂对涂胶部分进行清洗之外,没有溶剂排放,生产中没有三废物质产生,不会由于大量溶剂的排放影响生产工人的身体健康,也不会对周边环境产生污染,有利于清洁化生产。
3.有助于产品质量的提高。
复合薄膜不会因残存溶剂而污染所包装的内容物,产品的卫生可靠性好;复合时,基材不会因溶剂及烘道加热而引起薄膜变形,对确保复合薄膜平整性有利;复合薄膜采用里印时,采用无溶剂复合,印刷面的油墨不会因黏合剂中的溶剂影响而导致质量下降。
4.安全、卫生性好。
无溶剂复合生产中几乎不使用可燃、易爆性有机溶剂,故安全性好;复合薄膜中不会因残余溶剂的存在导致卫生性能下降,产品卫生性能可靠性佳。
5.可明显地降低生产成本。
无溶剂复合的加工成本较之干法复合工艺明显要低,复合工序的成本可望降低到干法复合的60%左右或者更低,经济效益显著。
无溶剂复合成本低是推动无溶剂复合快速发展的强大动力。
(1)无溶剂复合单位面积上胶量少,无溶剂复合单位面积黏合剂用量约为干法复合单位面积黏合剂干基涂布量的2/5。
尽管无溶剂黏合剂较干法复合黏合剂的价格高70%左右,但无溶剂复合薄膜成本反而较干法复合薄膜成本低。
(2)无溶剂复合一次性投资少,设备回收折旧成本也比较低。
复合设备没有预干燥烘道,设备造价较低(可降低30%或者更多)。
同样因复合设备没有预干燥烘道,设备占地面积小,可明显减少车间面积。
无溶剂复合黏合剂的体积小且不用储藏溶剂,可以减小仓储面积。
(3)无溶剂复合,节能显著。
复合过程中,不需要经过烘道加热排除黏合剂中的溶剂。
每条无溶剂复合生产线较之干法复合生产线,耗用能量要少得多,较之干法复合节约能耗2/3以上。
(4)无溶剂复合生产线速度明显提高,因而可以使生产成本降低。
无溶剂复合的最高线速度高达500m/min~600m/min,一般也在300m/min左右。
(5)无溶剂复合无三废物质产生,不需治理三废,不需配置昂贵的环保装置以及相应的运行费用。
当然无溶剂复合也存在不少工艺本身所固有的问题。
由于无溶剂复合黏合剂不含溶剂,不可能通过溶剂来调节黏合剂的黏度。
要使黏合剂的黏度保持在一个较低的、适合于涂布施工的水平,所能够考虑的办法有两个,即升高涂胶温度或者降低黏合剂的分子量。
通过加热提高黏合剂的温度,可以降低黏合剂的黏度,但在高温下,会缩短黏合剂的适用期,因此复合加工时黏合剂温度的提高受到极大地限制,双组分黏合剂一般最高涂布温度仅为70℃~80℃;为了使黏合剂黏度满足涂布加工的需要,只能降低无溶剂黏合剂的分子量,而黏合剂的分子量低,会对应用带来负面影响,表现为初黏力的下降(一般无溶剂复合的初黏力仅为0.23N/15mm~0.3N/15mm或者更低),远低于干法复合的初黏力(一般在1.0N/15mm以上)。
初黏力低,复合薄膜不易收卷。
对设备的张力控制系统要求高,对操作工的技术要求也较高。
产品的初黏力低,还使薄膜在熟化以前比较难以通过薄膜的初始黏合情况对复合薄膜的最终复合牢度进行预判。
因此,无溶剂复合要求对生产过程进行严格的控制。
尽管如此,无溶剂复合无论从降低生产成本、提高经济效益的角度,还是从改善环境质量、适应环保需要以及安全生产的角度看,或者从保证产品质量、满足使用要求的角度看,它较之干式复合均具有明显的优势,是一种值得倡导的、极有实用价值的复合方法。
第三是采用多层共挤复合薄膜,部分取代多层复合薄膜,减少使用黏合剂复合的层数,相对少用了干法复合黏合剂。
阻隔性软包装材料虽然可以直接由共挤出工艺制得,然而共挤出产品的一大局限是,只能进行表面印刷而不能进行里印(因为它一次完成复合加工,没有可供进行里印的中间产品)。
在实际生产中,在许多应用领域,不仅要求复合软包装材料具有良好的物理力学性能,而且需要它具有良好的外观和印刷效果以及卫生性。
为了在充分发挥共挤出工艺的优势的同时,最大限度地克服它固有的缺点,于是利用共挤出工艺设计,开发了阻隔性复合薄膜基材,结合干法复合等其他工艺,生产阻隔性复合薄膜基材。
以五层共挤高阻隔复合薄膜基材为例。
其结构为:
复合层/黏合树脂层/EVOH/黏合树脂层/热封层。
最终产品结构为:
印刷面料层(PET或NY)/黏合剂/复合层/黏合树脂层/EVOH/黏合树脂层/热封层。
产品工艺路线有两种:
一种是生产EVOH五层共挤膜,五层进料―共挤模头―制膜―电晕处理―切边―卷取。
“五层进料”是指复合层树脂、黏合层树脂、EVOH、黏合层树脂、热封层树脂按照五层配方组合的要求,分别进入相应层喂料口,以便制成五层共挤出薄膜。
另一种是五层共挤高阻隔膜的复合,即凹版印刷―干法复合―熟化―分切或制袋。
“干法复合”使EVOH五层共挤膜与经凹版印刷的表层基膜(PET或PA)进行复合。
由于采用了共挤出复合工艺生产五层共挤高阻隔复合薄膜。
通过一次加工,得到了利用干法复合需要五次加工(三次吹塑或流延成膜、两次干法复合)才能得到的五层复合薄膜,大大缩短了生产周期,降低了生产成本。
同时,利用五层共挤高阻隔复合薄膜作为中间产品,替代单层基材生产七层[印刷面料层(PET或NY)/黏合剂/复合层/黏合树脂层/EVOH/黏合树脂层/热封层]的复合薄膜,仅用一次干法复合,就完成了全部采用单层基材时,需要三次干法复合才能完成的产品的加工,大大减少了干法复合的应用,减轻了生产过程中对环境的压力。
有利于环境保护以及降低生产成本。
总之,我们包装印刷企业所处的大环境是一样的,不同的是我们的企业规模与技术、资金的实力。
只要我们根据自己企业的实际情况,决策正确,总能够找到一条最适合自己发展的道路。