甲醇合成装置工艺说明.docx
《甲醇合成装置工艺说明.docx》由会员分享,可在线阅读,更多相关《甲醇合成装置工艺说明.docx(14页珍藏版)》请在冰豆网上搜索。
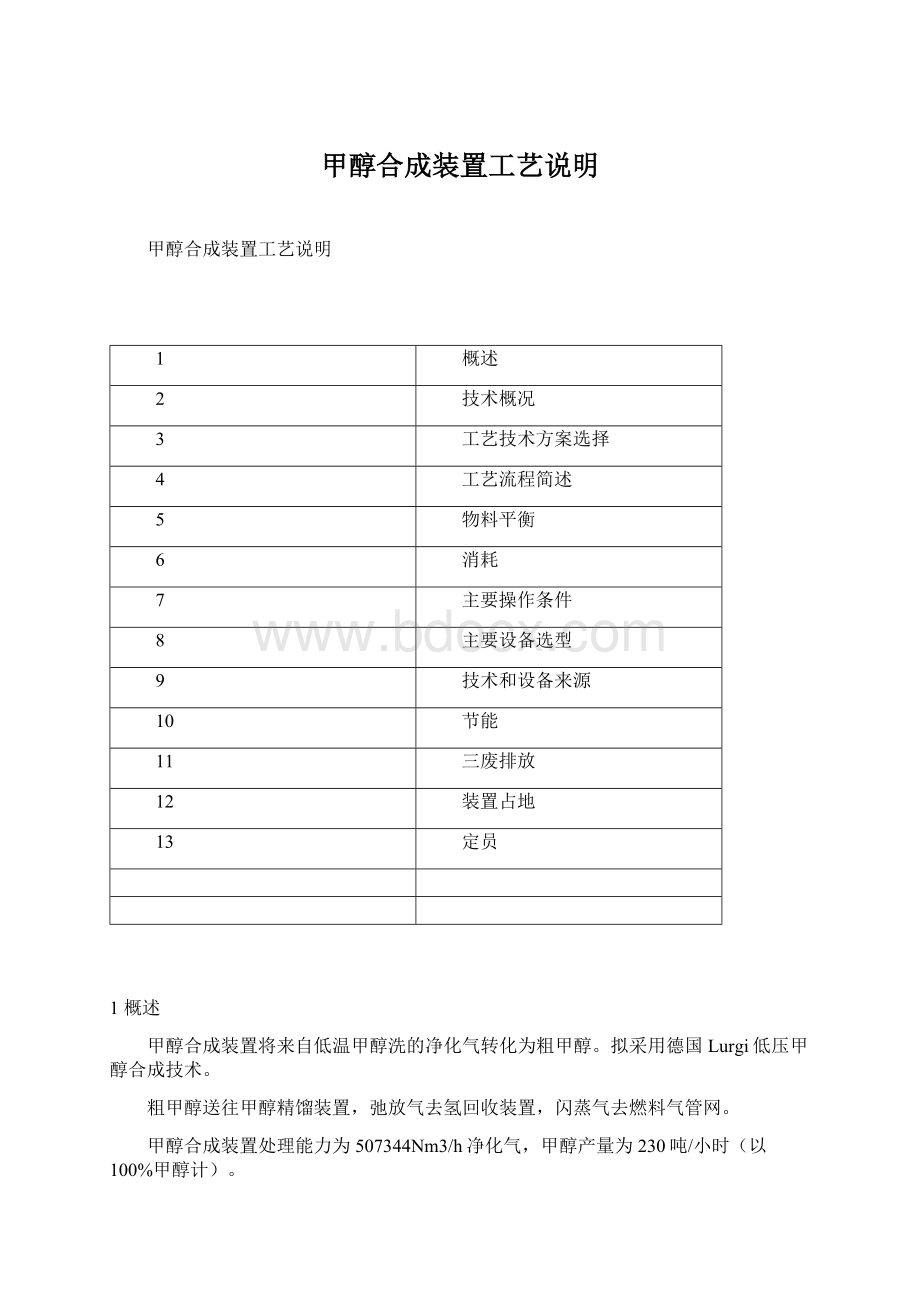
甲醇合成装置工艺说明
甲醇合成装置工艺说明
1
概述
2
技术概况
3
工艺技术方案选择
4
工艺流程简述
5
物料平衡
6
消耗
7
主要操作条件
8
主要设备选型
9
技术和设备来源
10
节能
11
三废排放
12
装置占地
13
定员
1概述
甲醇合成装置将来自低温甲醇洗的净化气转化为粗甲醇。
拟采用德国Lurgi低压甲醇合成技术。
粗甲醇送往甲醇精馏装置,弛放气去氢回收装置,闪蒸气去燃料气管网。
甲醇合成装置处理能力为507344Nm3/h净化气,甲醇产量为230吨/小时(以100%甲醇计)。
2技术概况
甲醇工业化始于20世纪初,1923年德国BASF公司首先建立了一套采用Zn-Cr催化剂、合成压力为30.0MPa、规模为300吨/年的高压法甲醇生产装置。
20世纪60年代,甲醇工业随着选择性好、低温活性高的铜基催化剂开发成功而取得重大进展。
1966年英国ICI公司研制成功Cu-Zn-Al催化剂后,推出ICI低压甲醇合成工艺,在所属Billingham工厂建立了工业化装置。
1971年德国Lurgi公司成功开发出采用活性更高的Cu-Zn-Al-V催化剂的另一著名低压法工艺-Lurgi工艺。
此后,世界各大公司竞相开发了各具特色的低压法工艺技术。
与高压法工艺相比,低压法工艺在投资和综合技术经济指标方面都具有显著优势。
以天然气为原料的甲醇厂,高压法能耗达64.8GJ/t甲醇,而大型低压法装置为29.5~31.5GJ/t甲醇。
1970年代后国外新建的大中型甲醇装置全部采用低压法,高压法渐趋淘汰。
高、低压法甲醇生产主要操作条件如下:
项目
高压法
低压法
压力
30.0MPa
5.0~10.0MPa
温度
340~380℃
210~260℃
催化剂
Zn-Cr
Cu-Zn-Al
随着1997年德国Lurgi公司大甲醇(MegaMethanol)概念的提出,甲醇技术逐渐向大型化发展,Lurgi,Davy,Topsoe等公司相继提出大甲醇技术,各种甲醇合成技术,主要体现在甲醇合成反应器的设计上。
2.1Lurgi甲醇反应器
传统的Lurgi甲醇反应器为列管等温反应器,其结构形式与管壳式换热器非常类似,列管内装填催化剂,管间为沸腾水。
原料气预热后进人反应器,反应放出的热量经管壁传给管间的沸腾水,产生蒸汽。
反应器全系统的温度条件用蒸汽压力来控制,从而保证催化剂层呈大致等温的工作状态。
Lurgi列管反应器的反应管均匀分布在沸水一蒸汽系统中,容易实现反应热的快速移除,并使反应器温度实现较均匀的分布。
可通过蒸汽压力的调节,简便地控制床层温度,使催化剂寿命延长。
其缺点是:
床层压降较大,达0.3MPa左右。
由于列管长度受到限制,放大生产一般通过增加管数的方法实现,使反应器的直径增大,给设计和制造带来很大困难,列管式反应器对材料的要求较高,如换热管要求用双相钢,设备费用大。
为了适应大规模生产的需要,Lurgi在列管式反应器的基础上开发了列管式和冷管式反应器串联的组合型合成装置。
在冷管式反应器中,壳层装填催化剂并发生甲醇合成反应,反应热由管内的冷新鲜原料气移除,同时实现对新鲜原料气的预热。
冷管式反应器的优点是催化剂装填量大;缺点是结构较复杂,对材料的要求也较高,设备费用大。
目前,采用Lurgi公司提供技术的5000t/d大规模甲醇装置已有两套成功实现了商业化运转,另有数套正在建设中。
2.2Topsoe甲醇反应器
目前.Topsoe大型甲醇技术采用的反应器为传统的水冷式列管等温反应器。
与Lurgi的水冷式反应器基本类似。
原料气经预热净化后进入合成塔管内催化剂床层反应,管外用沸腾水移热。
一般通过多个合成塔并联的方式达到大规模生产的要求。
目前,采用Topsoe公司技术的在运甲醇装置最大规模为3030t/d,有一套7500t/d装置已完成了基础工程设计
2.3Davy甲醇反应器
Davy公司近期开发了一种蒸汽上升式反应器,其主要特点是催化剂装填在壳侧,原料气从中心管进入,并从中心向两侧呈径向流动,管内用锅炉给水产生蒸汽移热。
Davy公司通过计算,比较了催化剂在管内、水在管外与催化剂在管外、水在管内两种方案。
结果表明后者所需的管子表面积仅为前者的6/7,因此选择催化剂床层在壳侧的方式。
同时,这种催化剂装填方式还具有催化剂装填量大,易于装卸等优点。
Davy反应器中,原料气进入反应器通过一垂直分布板后,横向流过催化剂床,既减少阻力降,又增加传热系数。
Davy反应器对材料的要求相对较低,因换热管内走水,在某些操作条件下换热管甚至可以采用碳钢。
大大降低了设备投资。
Davy反应器一般采用两台并联或串联,可实现年产百万吨甲醇的规模。
目前,采用Davy技术的5000t/d大规模甲醇装置已有一套投入商业运转,另有数套正在建。
2.4Casale甲醇反应器
Casale开发了一种新型IMC甲醇反应器,该反应器将换热板埋入催化剂床层内作为冷却元件,换热板内走锅炉给水,将反应热移出催化剂床层的同时产生饱和蒸汽。
这种设计结构比传统的列管式反应器换热效率更高,其催化剂装填在壳侧,装填量大,无需管板,从而提高了单台反应器的生产能力。
其缺点是结构复杂,制造难度较大,对材料的要求较高,设备投资较大。
目前.采用Casale技术的甲醇装置最大规模为3400t/d.有一套7000t/d的装置正在建设中。
2.5MGC甲醇反应器
MGC(三菱瓦斯)开发了一种超级合成塔(SPC),其主要结构特点是在传统的列管式反应器装填有催化剂的管中又增加了一根内管,原料气由塔底部的空间通过软管进入内管,用反应热预热,预热过的原料气由反应器顶部返回,然后进入催化层,催化剂置于内外两层管之间。
这样催化剂不仅被壳层中的循环水冷却,也被内管中的进料合成气所冷却。
这种特殊的换热系统使得SPC具有较好的反应温度曲线和高的一次转化率,从而提高了单台反应器的生产能力。
其缺点也是结构复杂.制造难度较大,对材料的要求较高,设备投资较大。
目前.采用MGC技术的甲醇装置最大规模为3000t/d.有一套5000t/d的装置正在建设中。
2.6国内甲醇技术
对于百万吨级的甲醇,国内杭州林达化工工程公司、华东理工大学均进行了方案设计,但都没有工业化业绩。
3工艺技术方案选择
目前国内已工业化的拥有自主知识产权的低压等温合成甲醇装置最大规模为60万吨/年。
本项目甲醇规模约为180万吨/年,如果用国内技术,按单系列设计,则存在放大风险;按照多系列设计,则投资大,能耗高,占地多。
鉴于德国Lurgi公司、英国Davy公司都有类似规模甲醇装置运行业绩,为控制项目风险,本项目暂推荐引进国外技术。
3.1工艺流程配置
由于受限于设备制造能力和运输条件的影响,180万吨级的甲醇合成往往需要数台反应器串联或者并联来实现。
3.1.1并联工艺流程
并联工艺流程是最简单的流程配置。
当一台反应器不能满足生产规模时,可采用两台或数台反应器并联来实现生产规模的增加。
从流程配置上来看,并联工艺流程仅仅是反应器数量上的叠加,对于反应器实际为多系列生产,仅在某些设备(如压缩机、汽包、主要工艺管线上)能实现共用.降低部分投资。
目前,Topsoe公司的大型甲醇技术采用的是并联工艺流程。
3.1.2串联工艺流程
Lurgi公司的大型甲醇技术采用的是典型的串联工艺流程,将列管式和冷管式反应器进行串联,原料气先进冷管式反应器,预热后气体从顶部离开。
进入列管式反应器管内装填的催化剂床层反应。
管外用沸腾水移热,出塔气返回进入冷管式反应器壳层催化剂床层继续反应,反应热对流经冷管式反应器管层的原料气进行预热,出冷管式反应器的气体回收热量、降温、分醇后,再循环。
Lurgi公司提出的这种串联工艺流程较好地在甲醇合成反应动力学与反应热力学之间进行了权衡。
从反应热力学角度来看,甲醇合成反应是放热反应。
低温有利于甲醇的生成;从反应动力学角度来看,高温可以加快反应速度,但高温对催化剂有害,并产生酮类等副产物,它们会形成共沸物,使后续的精馏更为困难。
在Lurgi的串联流程中,其列管式水冷反应器有相对较高(260℃)的出口温度,使反应较快地进行:
在此发生部分转化后,其余的转化发生在冷管式反应器,在较低温度(220~225℃)下操作,有利于甲醇的合成这种流程配置实现了较快的反应速度和较高的转化率,显著提高了反应的单程转化率,降低了循环气量,节省了循环气压缩机的功耗。
3.1.3串/并联工艺流程
Davy公司新近开发出了一种特别适合于大型甲醇装置的串/并联工艺流程。
在该流程中。
绝大部分的新鲜合成气与第二粗甲醇分离器顶部出来的循环气混合后进人第一甲醇反应器:
反应后的气体经回收热量、降温、进入第一粗甲醇分离器实现分离后,循环气与少部分新鲜合成气混合、压缩后进人第二甲醇反应器:
反应后的气体经回收热量、降温、进入第二粗甲醇分离器实现分离后,循环气与新鲜合成气混合,再进入第一甲醇反应器。
从新鲜合成气分配的角度来看,总的新鲜气量按照一定比例在两个反应器间进行分配,可视为并联流程。
从反应器出口气体的流向来看,第一反应器出口气体经过冷却、分离、压缩后进入第二反应器,可视为串联流程。
因此将这种新型的工艺流程称为串/并联工艺流程。
在该流程中,将第一反应器的出口气体进行降温、分醇后再进入第二反应器,这与两个反应器直接串联相比,第二反应器的原料气中甲醇含量很低,促使反应平衡向甲醇合成的方向移动,可显著提高甲醇转化率,降低整个合成回路的循环比。
由于单纯的反应器并联仅仅数量上的叠加,使得这种配置在投资上大大高于后面两种流程配置,不能体现出装置大型化、规模化的优点。
德国Lurgi与英国Davy技术均是为百万吨级的规模而配置,且在国内均已建设有类似规模的煤制甲醇工厂,根据它们技术特点,比较结果见下表:
Lurgi技术
Davy技术
反应器阻力降
轴向塔,压降大
径向塔,塔压降小
热回收
副产较高品味的中压蒸汽(~3.7MPa)
副产低品味蒸汽(~2.0MPa)
醇净值
高达16%
约5%左右
循环比
低至2左右
高达5以上
设备数量
少
多
催化剂装填量
~181m3
约176m3
根据以上比较结果,由于Davy技术醇净值低,循环比大,导致循环气压缩机功耗约为Lurgi技术的两倍,且受限于反应器的型式,Davy技术在热回收上劣于Lurgi技术。
再者,Davy技术相当于两个合成回路,在设备数量上多于Lurgi技术,导致设备投资高。
本项目根据国内已建设的类似规模的工厂的投资、消耗数据,进行综合比较、计算,在投资上,采用Lurgi技术的工厂比采用Davy技术的工厂约低6000万RMB;在能耗上,前者比后者约低0.2GJ/吨甲醇。
故本项目暂考虑采用德国Lurgi公司的低压甲醇合成技术。
3.2催化剂选择
由于Lurgi技术采用德国Sud-chemie(南方化学)的催化剂;Davy技术采用JohnsonMatthey(庄信万丰)的催化剂,均属于捆绑销售,因此本项目采用德国南方化学的甲醇催化剂。
4工艺流程简述
来自酸性气体脱除装置的净化气,和来自氢回收装置的氢气混合后进入压缩机,压缩到8.0MPaG后进入调温空冷器冷却,冷却到65℃与压缩机来的循环气混合后进入调温水冷器冷却。
从甲醇合成工序来的循环气压力为7.2MPaG、40℃,进入压缩机压缩到8.0MPaG,与新鲜气汇总后去甲醇合成工序。
去甲醇合成工序的合成气温度通过来自压缩机的副线流量控制。
压缩机蒸汽透平采用9.8MPaG、540℃高压蒸汽驱动,乏汽进入表面空冷器冷凝,蒸汽冷凝液由冷凝液泵送除盐水站。
从合成气压缩工序来的8.0MPaG的合成气进入气冷合成塔管侧,吸收壳侧合成反应热后升温至225℃,然后经入塔气换热器升温至240℃后从甲醇合成塔