模具设计题目及答案.docx
《模具设计题目及答案.docx》由会员分享,可在线阅读,更多相关《模具设计题目及答案.docx(19页珍藏版)》请在冰豆网上搜索。
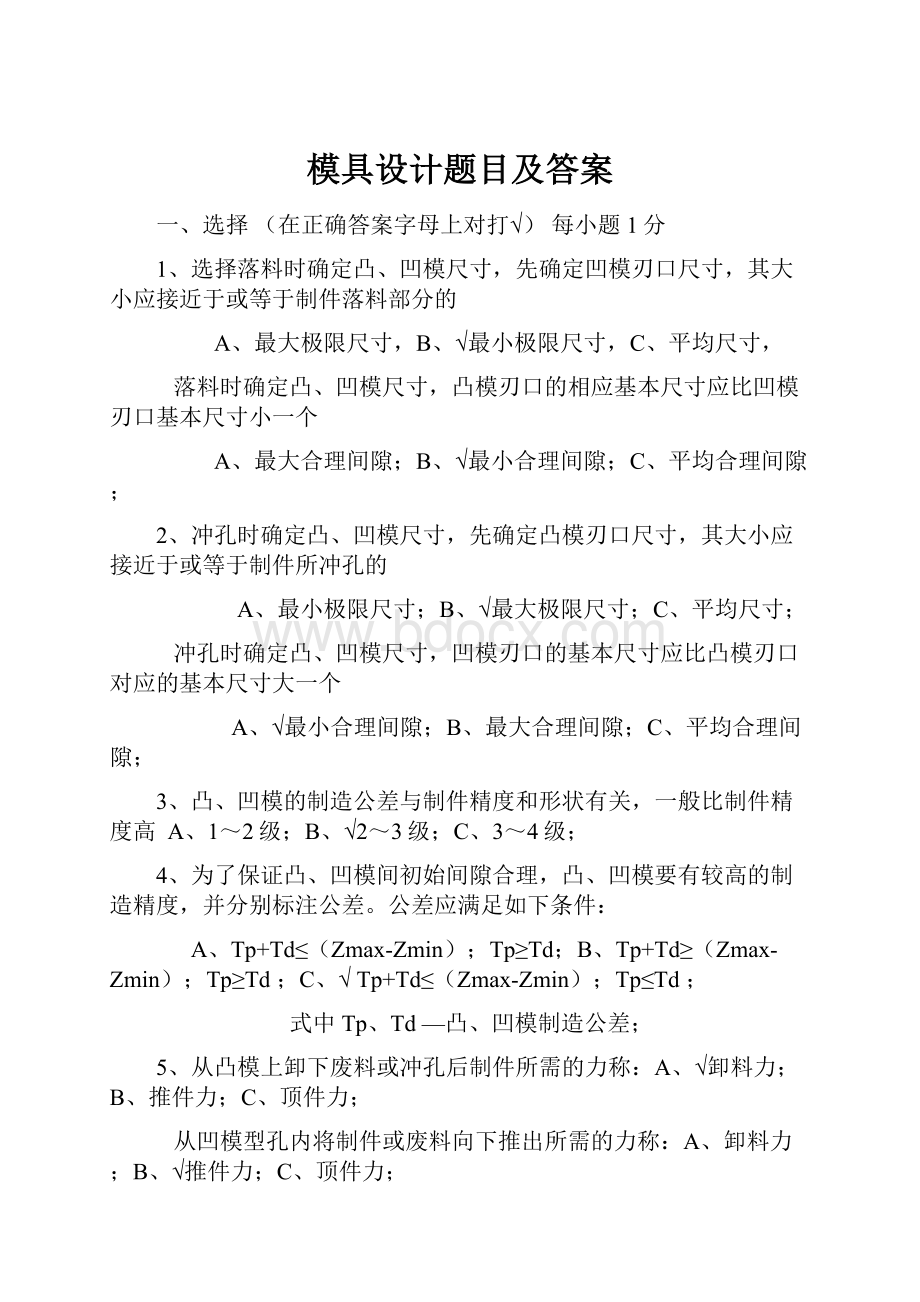
模具设计题目及答案
一、选择(在正确答案字母上对打√)每小题1分
1、选择落料时确定凸、凹模尺寸,先确定凹模刃口尺寸,其大小应接近于或等于制件落料部分的
A、最大极限尺寸,B、√最小极限尺寸,C、平均尺寸,
落料时确定凸、凹模尺寸,凸模刃口的相应基本尺寸应比凹模刃口基本尺寸小一个
A、最大合理间隙;B、√最小合理间隙;C、平均合理间隙;
2、冲孔时确定凸、凹模尺寸,先确定凸模刃口尺寸,其大小应接近于或等于制件所冲孔的
A、最小极限尺寸;B、√最大极限尺寸;C、平均尺寸;
冲孔时确定凸、凹模尺寸,凹模刃口的基本尺寸应比凸模刃口对应的基本尺寸大一个
A、√最小合理间隙;B、最大合理间隙;C、平均合理间隙;
3、凸、凹模的制造公差与制件精度和形状有关,一般比制件精度高 A、1~2级;B、√2~3级;C、3~4级;
4、为了保证凸、凹模间初始间隙合理,凸、凹模要有较高的制造精度,并分别标注公差。
公差应满足如下条件:
A、Tp+Td≤(Zmax-Zmin);Tp≥Td;B、Tp+Td≥(Zmax-Zmin);Tp≥Td;C、√Tp+Td≤(Zmax-Zmin);Tp≤Td;
式中Tp、Td—凸、凹模制造公差;
5、从凸模上卸下废料或冲孔后制件所需的力称:
A、√卸料力;B、推件力;C、顶件力;
从凹模型孔内将制件或废料向下推出所需的力称:
A、卸料力;B、√推件力;C、顶件力;
逆着冲压方向将制件或废料由凹模内顶出所需的力称:
A、卸料力;B、推件力;C、√顶件力;
6、凸模与凹模间每侧空隙的数值,称为:
A、√单边间隙,B、双面间隙,C、冲裁间隙
凹模与凸模间两侧空隙之和,称为:
A、单边间隙,B、√双面间隙,C、冲裁间隙
7、有搭边排样的材料利用率A、√较低;B、较高;C、最高;
少搭边排样的材料利用率A、较低;B、√较高;C、最高;
无搭边排样的材料利用率A、较低;B、较高;C、√最高;
8、模具冲压工作终结时,上模座的上平面至下模座的下平面间的高度称为:
A、√模具的闭合高度;B、压力机的闭合高度;C、最大闭合高度;D、最小闭合高度;
压力机的滑块在下极点位置时,连杆调至最短时的距离称:
A、模具的闭合高度;B、压力机的闭合高度;C、√最大闭合高度;D、最小闭合高度;
压力机的滑块在下极点位置时,连杆调至最长时的距离称:
A、模具的闭合高度;B、压力机的闭合高度;C、最大闭合高度;D、√最小闭合高度;
正常条件下模具与压力机闭合高度间的关系应满足如下条件:
A、√Hmax-5≥H+H1≥Hmin+10;B、Hmax–5≤H+H1≥Hmin+10;C、Hmax–5≤H+H1≤Hmin+10;
9、板料在弯曲变形时,外层纤维受拉伸长,内层纤维受压缩短。
最大切向应变在变形区
A、内表面上;B、外表面上;C、√内、外表面上;D、中心部位;
板料在弯曲变形时,r/t称为相对弯曲半径,是衡量弯曲变形程度的重要指标,r/t越小,变形程度
A、√越大;B、越小;C、不变;
10、板料在弯曲变形时,角度回弹量(回弹角)及曲率回弹量与
A、√材料的屈服极限成正比,与弹性模数E成反比;B、材料的屈服极限成反比,与弹性模数E成正比;
板料在弯曲变形时,形状复杂的弯曲件,一次弯曲成形角的数量越多,
A、√回弹量就越小;B、回弹量就越大;C、回弹量不变;
11、弯曲模设计时,当工件的相对弯曲半径r/t较小时,凸模圆角半径rp可以取
A、等于或略大于弯曲件的半径;B、√等于或略小于弯曲件的半径;C、等于弯曲件的半径;
弯曲模设计时,凹模圆角半径不能过小,以免材料表面擦伤。
凹模两边圆角半径rd应
A、等于或略小于弯曲件的半径;B、不同;C、√相同;
12、拉深过程中,最容易失去稳定而拱起,形成所谓“起皱现象”的区域是:
A、√凹模口的凸缘部分;B、凹模圆角部分;C、凸模圆角部分;D、筒壁部分;E、圆筒底部;
拉深过程中,变薄最严重的危险断面区域是:
A、凹模口的凸缘部分;B、凹模圆角部分;C、√凸模圆角部分;D、筒壁部分;E、圆筒底部;
13、拉深件的毛坯尺寸计算是以最后一次拉深成形的工件尺寸为基准,拉深前毛坯面积与拉深后的工作面积的关系是:
A、毛坯面积大于拉深后的工作面积;B、毛坯面积小于拉深后的工作面积;C、√毛坯面积等于拉深后的工作面积;
拉深工序中,除最后一次工序外,其它所有各次拉深工序中,凸模的圆角半径与凹模圆角半径
A、√应尽可能相等或略小;B、应尽可能相等或略大;C、应尽可能大于凹模圆角半径;D、应尽可能小于凹模圆角半径
14、圆筒形件的拉深系数用拉深前、后的直径比值,以m表示。
m值愈小,
A、拉深变形程度愈小;B、拉深变形程度愈大;
拉深工艺计算所得的拉深次数n,通常不会是整数,此时n的取值应:
A、四舍五入,取整数值;B、n值四舍五入,而应取较小的整数值;C、√n值不能四舍五入,而应取较大的整数值。
15、热成型可以加工薄至( )的片材。
A、0.30mm厚至数毫米;B、0.20mm厚至数毫米;C、√0.10mm厚至数毫米;
16、浇口套进口的直径d应比注射机喷嘴孔直径d1 A、小1~2mm;B、√大1~2mm;C、大2~3mm;D、小2~3mm;
17、双分型面注射模具结构较复杂,制造成本较高,零件加工困难,模具重量增加,一般
A、√不用于大型、特大型塑件成型。
B、不用于中、小型塑件的成型。
C、不用于大型、中型塑件的成型
18、通常开模后,要求塑件留在设有推出机构( )的—侧。
A、√动模;B、定模;
某些情况下,开模后塑件留在或可能留在没有推出机构的定模—侧,模具结构应设计
A、√双向推出机构;B、侧抽芯机构;C、二次推出机构;
模具设计中,如果塑件脱模力较大,模具结构应设计 A、√双向推出机构;B、侧抽芯机构;C、√二次推出机构;
19、由于塑件的特殊要求或受形状限制,开模后塑件将留在定模一侧或有可能留在定模一侧,模具结构应
A、在动模—侧设推出机构;B、在定模—侧设侧向分型抽芯机构;C、√在定模—侧设推出机构;
由于塑件的特殊要求或受形状限制,开模后塑件将留在或有可能留在定模一侧,则应在定模—侧设推出机构;
A、常选用侧向分型抽芯机构;B、√常选用定距分型推出机构;C、常选用推管推出机构;
20、注射成型机最大注射量应( )塑料制品的重量或体积。
A、√稍大于;B、等于;C、小于;
注射成型机的最大注射压力应( )塑料制品成型所需的注射压力。
A、小于;B、等于;C、√稍大于;
模具的平面尺寸应( )注射成型机模板尺寸。
A、√大于;B、等于;C、小于;
注射成型机的锁模力,应( )注射时模具分型面所产生的最大胀开力。
A、√大于;B、等于;C、小于;
21、推杆推出机构设计时,推杆与推杆孔配合间隙( )所用塑料的溢边值。
溢边值一般为0.02~0.08mm。
A、大于等于;B、√小于等于;C、大于;D、小于;
设计螺纹脱模机构时,对于塑料制品的主要要求是:
A、有脱模斜度B、有加强肋C、√有防转结构。
22、移动式压缩模结构简单,加料、开模,取件等均为机外手工操作,模具易磨损、劳动强度大。
一般重量
A、≤8kgB、≤15kgC、√≤20kg
压缩模具主要用于( )的成型。
A、热塑性塑料大型塑件;B、√热固性塑料大型塑件;C、热塑性塑料小型塑件。
D、热固性塑料小型塑件;
23、压缩模的设计中,精度要求高的尺寸 A、设计在加压方向B、√不宜设计在加压方向。
压缩模的设计中,配合环可保证凸、凹模相对位置;单边间隙一般取
A、0.25~0.75mm;B、0.05~0.1mm;C、√0.025~0.075mm;
24、压注模主浇道设计,要求在满足使用要求前提下尽量缩短主浇道长度,主浇道径向尺寸()一般的热塑性塑料注射模。
A、小于;B、等于;C、√大于;
压注模压料柱塞设计,在直径较小,柱塞与加料室单边间隙最佳值
A、0.1~0.16mm;B、0.5~0.8mm;C、√0.05~0.08mm;
二、填空:
每小题2分
1、冲裁变形过程包括:
弹性变形阶段:
塑性变形阶段:
断裂阶段:
板料经冲裁后,冲裁断面上会出现:
塌角;光亮带;断裂带;毛刺;
2、减小冲裁力的方法有:
斜刃冲裁、阶梯冲裁、加热冲裁。
3、制件在板料、条料或带料上的布置方法称为排样。
主要有:
搭边排样;少搭边排样;无搭边排样,
4、冲裁模中的挡料销分为:
固定挡料销;活动挡料销;始用挡料销;
冲裁模中的固定挡料销分为:
圆柱头挡料销;钩形挡料销;圆头挡料销;
冲裁模中的活动挡料销从功能上可分为:
回带式;隐藏式;及临时挡料销;
5、冲裁模中的卸料装置分为:
刚性卸料;弹性卸料;
冲裁模中的刚性卸料装置分为:
悬臂式;封闭式;钩形;
6、冲裁模按工艺性质分类:
落料模;冲孔模;切断模;切口模;剖切模;切边模;整修模等。
冲裁模按按工序组合分类:
单工序模(又称简单模);复合模;连续模等;
冲裁模的组成零件分类:
工作;定位;压、卸料及出件零部件;导向零件;固定零件;紧固及其它零件;
7、影响回弹因素包括:
材料的机械性能;相对弯曲半径r/t;弯曲角;弯曲件的形状;模具间隙;校正力;
弯曲件设计方面减小回弹措施:
压制加强筋;选合理相对弯曲半径;选用弹性模数大,屈服极限低,机械性能较稳定的材料。
在模具结构上减小回弹措施:
补偿法;校正法;拉弯法;软凹模弯曲 ;
8、精冲的类型:
小间隙圆角刃口精冲;负间隙冲裁;齿圈压板式精冲;往复冲裁法;
9、弯曲模中常用定位方法:
销钉定位;定位尖、顶杆、顶板定位;定位板定位;设置导向块;
10、高聚物降解主要类型:
热降解;力降解;水降解;
11、塑料的主要组成有:
树脂;填充剂;增塑剂:
着色剂;稳定剂;润滑剂;其它改善性能的助剂等;
按塑料的使用特性分为:
通用塑料;工程塑料;功能塑料。
12、注射成型特点:
成型周期短,能一次成型复杂、精密、带有嵌件的塑件,生产效率高,易于实现自动化生产,应用广泛。
压缩成型的特点:
模具结构简单,料耗少,可使用普通压力机,可成型大面积的塑料制品,生产周期长,效率低,
不易压制形状复杂和尺寸精度较高的塑料制品。
挤出成型特点:
能连续成型;生产率高;塑件截面恒定;形状简单;几乎能加工所有热塑性塑料和部分热固性塑料。
13、注射模的结构组成:
成型件;导向零件;浇注系统;推出机构;侧向分型抽芯机构;温度调节系统;排气系统;支承件;
14、注射模按加工塑料的品种分为:
热塑性塑料注射模;热固性塑料注射模;
注射模按注射机类型可分为:
卧式注射机用注射模;立式注射机用注射模;角式注射机用注射模;
压注模类型:
普通液压机用压注模;专用液压机用压注模;往复螺杆式挤出机用压注模;
15、常用分浇道的类型有:
圆形;半圆形;矩形;梯形;
16、多型腔注射模设计时,型腔在模板上的布局原则:
排列紧凑;长度最短;型腔布局力求对称;
多型腔注射模设计时,型胺数n的确定方法:
按最大注射量确定型腔数;按锁模力大小确定型腔数;按塑化量确定型腔数;
17、推出机构按动力来源分类:
手动推出机构;机动推出机构;液压与气动推出机构;
推出机构按模具结构分为:
简单;二级;双向推出机构;点浇口自动脱模机构;带螺纹塑件的推出机构等。
18、机动抽芯机构的优点:
脱模力大;劳动强度小;生产率高;操作方便等;
液压抽芯机构的优点:
脱模力大;较长的抽芯距;运动传递平稳。
19、根据热能来源,模具的加热方法有:
蒸汽加热法、电阻加热法、工频感应加热法等。
设计电阻加热装置时的基本要求有:
合理布设电热元件;各部位按需分设电热元件;各部位分别控制调节;加保温措施;
20、冷却通道的形式可分成:
直通式通道、圆周式通道、多级式通道、螺旋式通道、循环式通道及喷流式通道等
冷却装置的形式主要为:
沟道式冷却装置;管道式冷却装置;导热杆式冷却装置
模具的冷却方法有:
水冷却;空气冷却;和油冷却等;
21、挤出成型机头设计原则:
内腔应呈光滑流线型;有分流装置和适当的压缩区;有正确的断面形状;有适当的调节装置;结构紧凑;合理选材;
推出机构的设计原则:
塑件留在动模;保证塑件不因推出而变形或损坏;保证塑件良好的外观;结构应准确可靠。
22、挤出机类型,按螺杆数目分为:
单螺杆;双螺杆;多螺杆挤出机;
挤出机类型,按是否排气分为:
排气式、非排气式挤出机;
挤塑成型工艺应用的辅机组成:
机头;定型装置;冷却装置;牵引装置;切割装置;卷取装置;
23、气体辅助注射成型生产周期分为:
熔体充填;切换延迟;气体注射;保压冷却;气体释放;脱模顶出;
24、注射成型工艺过程主要包括:
成型前的准备;注射过程;制品的后处理。
注射过程包括:
加料、塑化、注射、保压、冷却、脱模等
注射成型主要工艺参数:
温度;压力;时间。
注射成型工艺过程需要控制的温度:
有料筒温度;喷嘴温度;模具温度。
25、普通浇注系统的组成:
主浇道、分浇道、浇口、冷料穴
点浇口按其形状又分为:
菱形;单点形;双点形;多点形。
三、以下各题可用于三种题型,1、是非题(全部);2、改错:
(打×的题);3、名词解释:
(打√的题)
1、是非题(错打×;对打√)每小题1分
2、改错:
(划掉错误文字,填上正确答案)每小题1分
3、名词解释:
每小题1分
1、冲压是使板料经分离或成形而得到制件的加工方法。
√
常温下进行的板料冲压加工称为冷冲压。
√
2、分离工序是使冲压件与板料沿要求的轮廓线相互分离,并获得一定断面质量的冲压加工方法。
√
塑性变形工序是使冲压毛坯在不破坏的条件下发生塑性变形,以获得所要求的形状,尺寸和精度的冲压加工方法。
√
3、剪裁:
将板材沿敞开轮廓相分离的冷冲压工序。
√
冲裁:
将板材沿封闭轮廓相分离的冷冲压工序。
√
剪裁:
将板材沿封闭轮廓相分离的冷冲压工序。
×
冲裁:
将板材沿敞开轮廓相分离的冷冲压工序。
×
4、落料:
将板材沿封闭轮廓相分离且轮廓线外为制件。
×
冲孔:
将板材沿封闭轮廓相分离且轮廓线内为制件。
5、冲裁力方向的投影尺寸之差,称为冲裁间隙。
√
6、冲裁模刃口工作尺寸计算,落料加工时,取凹模作为设计的基准件;√
冲裁模刃口工作尺寸计算,落料加工时,取凸模作为设计的基准件;×
冲裁模刃口工作尺寸计算,冲孔加工时,取凸模作为设计的基准件。
√
冲裁模刃口工作尺寸计算,冲孔加工时,取凹模作为设计的基准件。
×
7、冲裁力是指冲压时,材料对凸模的最大抵抗力。
√
冲裁力是指冲压时,材料对凸模的最小抵抗力。
×
8、模具压力中心是冲压合力的作用点。
√
模具压力中心是冲压力的作用点。
×
9、有两个对称轴的平面图形,压力中心就是它的几何中心;√
有一个对称轴的图形,压力中心位于对称轴上;√
10、直筒式刃口凹模,适用于冲裁形状复杂、精度要求较高,以及厚度较大的零件。
√
锥筒式刃口凹模,适用于冲裁精度要求低、厚度较薄、尺寸较小、形状简单的下出料零件冲裁。
√
直筒式刃口凹模,适用于冲裁精度要求低、厚度较薄、尺寸较小、形状简单的下出料零件冲裁。
×
锥筒式刃口凹模,适用于冲裁形状复杂、精度要求较高,以及厚度较大的零件。
×
11、单工序模:
压力机一次行程中只能完成一道冲裁工序的模具称为单工序模。
√
多工序模:
压力机一次行程中能完成二道以上冲裁工序的模具称为多工序模。
√
连续模:
压力机一次行程中完成的数道工序分布在坯料送进方向的不同部位。
√
12、连续模:
压力机一次行程中完成的数道工序在模具的同一部位。
×
复合模:
压力机一次行程中完成的数道工序在模具的同一部位。
√
复合模:
压力机一次行程中完成的数道工序在坯料送进方向的不同部位。
×
13、落料模装在下模的复合模称为正装复合模。
√
落料凹模装在上模的复合模称为倒装复合模。
√
落料模装在下模的复合模称为倒装复合模。
×
落料凹模装在上模的复合模称为正装复合模。
×
14、把板料、型材或管料等毛坯弯成一定角度、一定曲率,形成一定形状零件的冲压工序称为弯曲。
√
15、弯曲后工件的形状和尺寸都将发生与加载时变形方向相同的变化,从而造成弯曲件的弯曲角度和弯曲半径与模具尺寸不一致。
这种现象称为回弹,又叫弹复。
×
弯曲后工件的形状和尺寸都将发生与加载时变形方向相反的变化,从而造成弯曲件的弯曲角度和弯曲半径与模具尺寸不一致。
这种现象称为回弹,又叫弹复。
√
16、硬质合金模是指凹模或凸模为硬质合金材料,或凸模和凹模均为硬质合金的模具。
√
17、整修是一种提高冲裁件外缘或内缘尺寸精度及降低粗糙度的工艺方法。
√
18、板料在弯曲变形时,外层纤维受压缩变短,内层纤维受拉伸长,在拉伸与压缩层之间存在一层既不伸长也不缩短的其应变为零的金属层,称为应变中性层,×
板料在弯曲变形时,外层纤维受拉伸长,内层纤维受压缩短,由外层拉应力过渡到内层压应力,中间有一层纤维切向应力为零,此层称为应力中性层。
√
19、确定U形件弯曲模的凸凹模尺寸时:
当工件标注外形尺寸时,应以凸模为基准件,扩大凹模取间隙。
×
确定U形件弯曲模的凸凹模尺寸时:
当工件标注内形尺寸时,应以凹模为基准件,缩小凸模取间隙。
×
20、拉深是利用专用模具将平板毛坯制成开口空心件的一种冲压工艺方法。
√
21、拉深过程中,在保证变形区不起皱的前提下,尽量选用较小的压边力。
√
22、凸肚是将拉深件或管料的形状加以改变,使材料沿径向压缩,胀出凸起曲面的工艺方法。
×
成形,是指用各种局部变形的方法改变毛坯或半成品的形状、尺寸的一种冲压加工方法。
√
23、起伏成形是筒形毛坯的局部胀形。
×
缩口工艺是一种将已拉深好的筒形件或管坯开口端直径胀出的冲压方法。
×
翻边是在成形毛坯的平面部分或曲面部分上,使板料沿一定的曲线翻成竖立边缘的冲压方法。
√
24、整形与校平均属于修整性的成形工序,目的是为了把冲压件的尺寸、圆角半径等修整到满足工件的要求。
×
旋压是将毛坯压紧在旋压机的芯模上。
使毛坯同旋压机的主轴一起旋转,同时操纵旋轮在旋转中加压于毛坯,使毛坯逐渐紧贴芯模,从而达到工件所要求的形状和尺寸的工艺方法。
√
25、合成树脂是按照天然树脂的分子结构和特性,用人工方法合成制造的高分子聚合物。
√
高分子聚合物(高聚物)是由相对分子质量小的物质经缩聚反应而制得的相对分子质量大的物质。
×
26、如果高聚物是由一根根的分子链组成的,则称为体型高聚物;×
高聚物若是在一根根的分子链之间有一些短链把它们连起来,则称为线型高聚物;×
27、高聚物玻璃化温度(Tg):
是指非结晶型或半结晶型的高聚物从粘流态或高弹态(橡胶态)向玻璃态转变(或相反转变)
的温度,它是塑件的最高使用温度。
√
高聚物流动温度(Tf或Tm):
是指从高弹态向粘流态转变(或相反转变)的温度,它是塑料的最低成型温度。
√
高聚物热分解温度(Td):
是指聚合物在高温下开始发生分解的温度,是塑料最高成型温度。
√
28、结晶度:
是指聚合物内结晶组织的质量(或体积)与聚合物总质量(或总体积)之比。
高聚物的降解:
指聚合物的相对分子质量增加或大分子结构改变等化学变化。
×
聚合物的交联:
是指聚合物在成型过程中,由体型结构交联为线形结构的化学反应过程。
×
29、简单组分的塑料:
基本上以树脂为主要成分,不加或加入少量助剂;√
多组分的塑料:
除树脂以外,还需加入其它一些助剂。
√
30、热塑性塑料:
聚合反应得到的,在一定的温度范围内,能反复加热软化乃至熔融流动,冷却后能硬化成一定形状的
塑料。
√
热固性塑料:
缩聚反应得到的,加热温度达到一定程度后能成为不溶和不熔性物质.使形状固化下来不再变化的
塑料。
√
31、热塑性塑料特点:
在成型过程中只有化学变化,而无物理变化,因而受热后可多次成型,废料可回收再利用。
×
热固性塑料特点:
在成型受热时发生化学变化使体型分子结构转变为线形结构,废料不能再回收利用。
×
32、收缩性:
指塑件从温度较高的模具中取出冷却到室温后,其尺寸或体积发生收缩的现像。
√
塑料在一定的温度及压力作用下,允满模具型腔的能力,称为流动性。
√
33、应力开裂:
有些塑料在成型时易产生内应力而使塑件质脆易裂,塑件在不大的外力或温度作用下即发生开裂,
这种现象称为应力开裂。
×
熔体破裂:
是指具有一定熔融指数的塑料,在恒温下通过喷嘴孔时.其流速超过一定值后,
熔体表面发生明显的纵向裂纹的现象。
×
34、压缩成型是在克服压注成型的缺点并吸收注射成型的优点的基础上发展起来的一种成型方法。
×
35、气辅注射成型,即对先注射了一定量或全部注满塑料熔体的模具型腔内再注射压缩后的惰性气体,
利用气体推动熔体完成充模的新工艺。
√
热成型:
是将热塑性塑料片材加热.靠真空、压缩空气或对模的压力,使之在模具成型表面成型并冷却定型,
经修剪而制得产品的方法。
√
中空吹塑:
是将压缩空气注入处于熔融状态的型坯内部,并使之膨胀而形成中空塑件的方法。
√
压缩空气成型:
是利用真空负压气体作为工作介质,把已加热软化后的片材推向模具型面,
严密贴合后冷却定型,获取塑件的热成型方法。
×
36、泡沫塑料是以树脂为基础内部含有无数微小气孔的塑料,又称为多孔性塑料。
√
37、主浇道;指从注射机喷嘴与模具接触处开始,到有型腔进料口为止的一段料流通道。
×
分浇道:
指主浇道与型腔进料口之间的一段流道。
√
38、成型零部件:
成型塑件内外表面几何形状和尺寸的零件。
√
合模导向零件:
保证动.定模合模或其它零部件间的准确对合。
√
浇注系统:
指将熔体由注射机喷嘴引向模具型腔的通道。
√
推出机构:
在开模中,将塑件及浇注系统凝料推出或拉出的装置。
√
侧向分型抽芯机构:
推出塑件前,把成型侧