蜜饯盒盖注塑模具设计.docx
《蜜饯盒盖注塑模具设计.docx》由会员分享,可在线阅读,更多相关《蜜饯盒盖注塑模具设计.docx(26页珍藏版)》请在冰豆网上搜索。
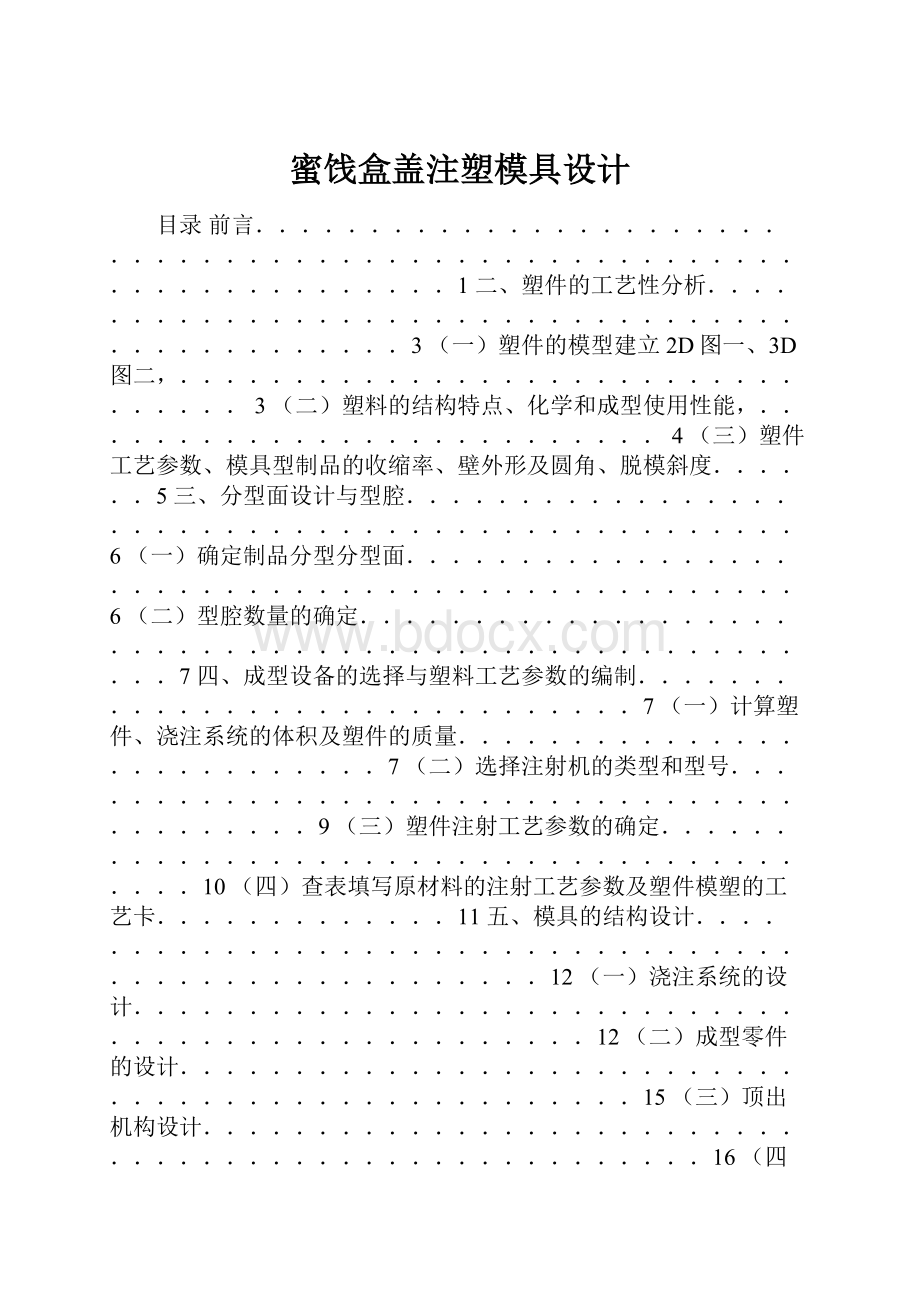
蜜饯盒盖注塑模具设计
目录前言....................................................................1二、塑件的工艺性分析...............................................3
(一)塑件的模型建立2D图一、3D图二,.................................3
(二)塑料的结构特点、化学和成型使用性能,..........................4(三)塑件工艺参数、模具型制品的收缩率、壁外形及圆角、脱模斜度......5三、分型面设计与型腔...............................................6
(一)确定制品分型分型面...............................................6
(二)型腔数量的确定....................................................7四、成型设备的选择与塑料工艺参数的编制..............................7
(一)计算塑件、浇注系统的体积及塑件的质量...........................7
(二)选择注射机的类型和型号..........................................9(三)塑件注射工艺参数的确定........................................10(四)查表填写原材料的注射工艺参数及塑件模塑的工艺卡.............11五、模具的结构设计.....................................................12
(一)浇注系统的设计..................................................12
(二)成型零件的设计..................................................15(三)顶出机构设计....................................................16(四)冷却系统设计....................................................19(五)导向机构设计....................................................22六、排气系统设计....................................................23七、模架的选择及校核...............................................24八、模具装配图和零件图............................................28致谢...................................................................29参考文献............................................................29
[摘要]通过对蜜饯盒盖注塑件进行特性分析及工艺分析等以及工艺方案的确定;根据这些分析来进行注射模具的设计,确定模具结构和成型方式,工对塑料设计与模架选择;并对成型工艺等多方面分析,制定正确工艺方案,并对模具的所有成型零部件计算进行验证及校核;最后根据结构设计出来模具进行选择注塑机以及绘制模具装配图和零件图。
[关键词]注塑模工艺分析成型尺寸注塑机
一、前言毕业设计是走上工作岗位成为正式员工的前奏,是综合运用学校学到的知识和技能进行实际工作的过程;是运用基本知识和基础理论,去分析、解决实际问题的实践锻炼过程,也是在校学习期间学习成果的综合性总结。
塑料,由于具有一系列优异的物理力学性能、化学性能和易成形加工工艺性能而在轻工、农业、国防、航天航空、机械制造、建筑材料、交通运输等部门与人们的日常生活密切相关的诸多方面都得到了非常广泛的应用。
塑料件蜜饯盒盖就是塑料运用的实例。
蜜饯盒盖是一个典型的塑料件,该零件大小适中,适合采用一模两腔的两板模生产。
通过设计该模具可较全面地熟悉塑料模具的设计过程,锻炼自己综合运用专业知识的能力。
在塑料制品的生产中,高质量的模具设计、先进的模具制造设备、合理的加工工艺、优质的模具材料和现代的成形设备等都是成形优质塑料的重要条件。
由于塑模生产领域计算机应用的独特优势,以三维模型为基础的以CAD/CAM/CAE技术为代表的模具计算机应用的集成化生产模式获得了快速的发展和进步。
模具CAD/CAM/CAE技术的广泛应用,显示了用信息技术带动和提升模具工业的优越性。
在欧美,模具CAD/CAM/CAE技术已成为模具企业普遍应用的技术。
在CAD的应用方面,已超越了甩掉图板、二维绘图的初级阶段,目前3D设计已达到了70%~89%。
PRO-E、UG、CIMATRON等软件的应用很普遍。
应用这些软件不仅可完成2D设计,同时可获得3D模型,为NC编程和CAD/CAM/CAE的集成提供了保证。
应用3D设计,还可以在设计时进行装配干涉的检查,保证设计和工艺的合理性。
CAE技术在欧美已逐渐成熟。
在塑料模设计中应用CAE分析软件,模拟塑料的充模过程,分析冷却过程,预测成形过程中可能发生的缺陷。
我在塑料件蜜饯盒盖的模具设计中,也运用了CAD绘图软件,UG三维造型软件。
二、塑件工艺分析
一)建立塑料件的模型(图1为蜜饯盒盖2D零件图、图2是蜜饯盒盖3D图)
(二)、塑料的结构特点、化学和成型使用性能
1、基本特性该塑料是仅次于聚乙烯和聚氯乙烯的第三大塑料品种。
它是无色透明、无毒无味,落地时发出清脆的金属声,密度为1.054g/cm3。
其力学性能与聚合方法,相对分子质量大小,定向度及其中的杂质量有关。
相对分子质量越大,机械强度越高。
该塑料有优良的电性能(尤其是高频绝缘性能)和一定的化学稳定性。
能耐碱、硫酸、磷酸、质量分数为10%~30%的盐酸、稀醋酸及其他有机酸,但不耐硝酸及氧化剂的作用。
对水、乙醇、汽油、植物油及各种盐溶液也有足够的抗腐蚀能力。
它能溶于苯、甲苯、四氯化碳、氯仿、酮类和脂类等。
该塑料有优良的着色性能、可染成各种鲜艳的色彩。
但耐热性能差,热变形温度一般在70~80摄氏度之间,只能在温度不太高的场合使用。
它质地硬而脆,有较高的热膨胀系数,因此,限制了它在工程上的应用。
近几十年来,发展了改性聚苯乙烯和以苯乙烯为基体的共聚物,在一定程度上克服了聚苯乙烯的缺点,同时又保留了它的优点,从而扩大了其用途。
2、成型特点该塑料的流动性和成型性能优良,成品率高,但工艺差,易于出现裂纹,要求塑料件的脱模斜度较大;因膨胀系数高,塑料件中不宜有嵌件,且壁厚应均匀;宜用高料温、高模温、低注射压力来成型并延长注射时间,以防止缩孔及变形、降低内应力。
但是料温过高,则易出现银丝;因流动性好,模具设计方面
3、模具设计方面
(1)可以使用所有常规类型的浇口。
若用点浇口,直径为0.8~1.0mm。
(2)PS性脆易开裂,设计恰当合理的顶出脱模机构,防止因顶出力过大或不均匀而导致制品开裂,选择较大的脱模斜度。
4、注塑工艺条件
(1)干燥处理:
除非储存不当,通常不需要干燥处理。
如果需要干燥,建议干燥条件为80度,2~3小时。
(2)料筒温度:
180~280度。
对于阻燃型材料其上限为250度。
(3)模具温度:
50~80度(4)注射压力:
20~60MPa。
(5)注射速度:
注射速度宜适当高些以减弱熔接痕,但因注射速度受注射压力影响大,过高的速度可能会导致飞边或出模时粘膜以及顶出时顶白顶裂等问题。
5、共混改性塑料
(1)
PS+PVC
共混成为性能较好的不燃塑料。
(2)PPO改善PPO加工性、降低吸湿性、降低成本、提高PS耐热性、冲击性。
5、主要用途聚苯乙烯在工业中可制仪表外壳、灯罩、化学仪器零件、透明模型等;在电气方面可制作绝缘性能良好的零件(如接线盒、电池盒等)。
在日常用品方面广泛地用于包装材料、各种容器、玩具等。
三)、塑件工艺参数、模具型制品的收缩率、壁外形及圆角、脱模斜度.
1、塑件工艺参数
(1)塑件的质量和精度
塑料制品的表面质量指的是塑料制品成型后的表面缺陷状态,如常见的填充不足、飞边、收缩凹陷、气孔、熔接痕、银纹、绕曲4变形,顶白,白斑,尺寸不稳定及粗糙度等。
塑料制品的表面粗糙度应遵循表3-4中GB/T14234-93《塑料件表面粗糙度标准—不同加工方法和不同材料所能达到的表面粗糙度》。
一般模具型腔粗糙度要比制品的要求低1~2级。
塑件PS公差等级为MT5,它的表面粗糙度Ra1.60~3.20。
查《塑料模具成形模具设计手册》
(2)塑件的尺寸分析
这里尺寸是指塑件的总体尺寸,而不是指壁厚,孔径等结构尺寸。
塑件的尺寸精度是指所获得的塑件与产品图中的尺寸行使程序,即所获得的尺寸的准确度。
塑料尺寸的大小与塑料的流动性有关。
注射成型的塑件尺寸还要受到注射机的注射量、锁模力和模板尺寸的限制。
2、成型收缩的形式
PS(聚苯乙烯)收缩率在0.4%~0.7%之间。
常用收缩率0.5%。
PS的流动性极好,成型加工容易。
成型收缩主要表现在以下几个方面。
(1)塑料件的线性尺寸收缩由于热胀冷缩,塑料件脱模时的弹性恢复、塑性变形等原因导致了塑料件脱模冷却到室温后其尺寸缩小。
为此,设计模具时对于型腔个尺寸必须于以补偿。
(2)收缩方向性成形时分子按照方向排列,使塑料件呈现各向异性,沿料方向的收缩大,强度高。
与料流方向相垂直,则收缩小强度低。
此外,成形时由于塑料件各部分密度及填料分布不均,故收缩也不均匀。
产生收缩差会使塑料件发生绕曲、变形、裂纹,尤其在挤塑及注射成形时,其方向性更为明显。
所以,在模具设计时,必须考虑收缩的方向性,按照塑料件的形状、料流的方向来选取收缩率为宜。
(3)后收缩性塑料件成形时,由于受成形压力、剪切应力、各向异性、密度不均、填料分布不均、模温不均、硬化不均及塑性变形等因素的影响,引起了一系列应力变化,在粘流状态时不能全部消除,故塑料在应力状态下成形时则存在着残余应力。
(4)后处理收缩根据塑料件的使用性能及工艺要求,在成形之后需要进行(时效)热处理,处理后也会导致塑料件尺寸。
因此,设计成形模具时,对高精度塑料件应当考虑后收缩及后处理收缩性能给尺寸造成偏差,并予以修正。
3、壁厚外形及圆角、脱模斜度
热塑性塑料易于成型薄壁制品,壁厚可小至0.75mm,推荐壁厚2mm。
查表3-6常用塑料的壁厚值《注射模具设计》。
圆角最小转角圆弧为0.5~0.8,PS脱模斜度50’~2°查表3-5常用塑料的脱模斜度《注射模具设计》
三、分型面设计与型腔
(一)确定制品分型分型面
为将塑件从密闭的模腔内取出,以及为了安放嵌件或取出浇注系统等,必须将模具分成两个或几个部分,一般将分开模具能取出塑件的面称为分型面。
分型面的选择受到塑件的形状、壁厚、尺寸精度、表面粗糙度、嵌件位置几其形状、塑件在模具内的成型位置、顶出方法、浇注系统的设计,模具排气,模具制造及操作等各种因素的影响。
因此,在选择时要认真分析、综合比较,从几个方案中找出一个比较合理的方案。
分型面是模具动模和定模的结合处,在塑件最大形处,是为了塑件和凝料取出而设计的。
分型面的方向尽量与注塑成型机开模方向垂直的方向,特殊情况下采用与注塑成型机开模方向平行的方向。
分型面有单分型面和双分型面之分。
分型面选择的原则:
分型面应选择在塑件外形的最大轮廓处;分型面的选取应有利于塑件的留模方式,便于塑件顺利脱模,一般都应尽可能留在动模部分;保证塑件的精度要求;满足塑件外观的要求;便于模具的制造;减少成形面积;增强排气效果。
由于本产品的分型面简单,选择塑件最大轮廓处为分型面,该塑件分型面比较简单,用单分型面。
分型面如图3所示。
二)型腔数量的确定
由于本产品塑件外观质量要求高,精度方面也有要求较高,所以采取一模两腔的方式。
多腔模具设计分布有平衡式和非平衡式排布两种,此处必须采用平衡布置分流道的方式,从主流道到分流道进入各型腔,要保持一定温度和压力平衡,在相同时间注满型腔。
也保证塑件的成形精度、形状、断面尺寸分布对称性对应相等。
非平衡式与之相反,容易造成注射时温度和压力不平衡,使模具在注射时有一定的胀行力,会加快损坏模具。
后面这种方式是不允许采取的。
此塑件的排布采用平衡式如图4。
四、成型设备的选择与塑料工艺参数的编制
一)、计算塑件、浇注系统的体积及塑件的质量
根据画出来的三维模型图,用CAD软件查询,工具/面域/质量特性可以查询到塑件的体积
V=10.5297176cm3,取V=10.53cm3而浇注系统的体积应为塑件的0.6倍,所以浇注系统的体积为V浇=0.6×10.53cm3=6.318cm3.又由于是一模两腔的方式,便一次注射所需要地塑料为V=V塑×Ni+V,所以V浇=10.53×2+6.318=27.378cm3
本产品采用PS材料,密度为1.054g/cm3,计算一个塑件的质量M=Pv塑=1.054×10.53=11.09862g
(二)选择注射机的类型和型号
我国采用注射量来表示注射机的规格成型热塑性塑料,类型和规格很多,本设计根据塑件的形状,一模两腔的方式选择卧式螺杆式注射成型设备,查《塑料成型模具设计手册》表1-3选取型号:
J54-S-200/400国产注射机,该注射机的主要技术参数如下表所示:
三)、塑件注射工艺参数的确定
(四)、查表填写原材料的注射工艺参数及塑件模塑的工艺卡.
五、模具的结构设计
(一)浇注系统的设计
浇注系统是指模具中从喷嘴开始到型腔入口为止的塑料熔体通道。
它的作用是将塑料溶体平稳地且有顺序地充填和凝固的过程中,把注射压力充分传剃到各个部位,以获得组织致密、外形清晰饱满的内在质量优良的塑件。
浇注系统其组成部分有:
主流道、分流道、浇口和冷料穴份组成。
浇注系统的设计是否合理,这对于塑料件的性能、表现质量及成形的工艺性能等都有很大的影响。
因此,浇注系统的设计要注意几个原则:
1、适应塑料注射成形的工艺特性2、有利于型腔内气体的排出3、尽量减少塑料熔体的热量损失和压力损失4、避免塑料熔体直冲细小型心或嵌件5、要便于进行拧了的修整和不影响塑料件的外观质量6、防止塑料件绕曲变形7、预测熔接痕的位置8、尽量减少成形中物料的消耗和减少模具的形状尺寸浇注系统的设计是一个非常重要的问题,模具设计者必须予以足够重视。
主流道是指紧接著设机喷嘴到分流道为止那一段锥形流道,它与注塑机喷嘴在同一轴心线上,熔融塑料进入模具时首先经过它。
其直径的大小与塑料流速及充模时间的长短有密切关系。
直径太大时,则造成回收冷料过多,冷却时间增长,而流道空气过多也易造成气泡和组织松散,极易产生涡流和冷却不足,另外,直径太大时,熔融的热量损失会增大,流动性降低,注射压力损失增大,造成成型困难;直径太小时,则增加熔体的流动阻力,同样不利于成型。
为了便于塑料从主流道中拉出,主流道设计成圆锥形,其锥角a=2°~4°,对于粘度较大的塑料熔体可以增大到6°主流道锥孔内壁粗糙度Ra应为低于0.4,主流道的始端也应设计成凹形球面状,球面半径R根据注射机喷嘴球面半径来确定,主流道要和注塑机的喷嘴紧密对接。
主流道对接处设计成半球形凹坑,其半径一般比喷嘴大1~2mm,凹坑深度常取3~5mm.主流道大端与分流道有过渡圆角,以减小塑料熔体流动转向时的阻力,其圆角半径一般取r1~3mm,或者取r=D/8(D为主流道大端的直径)。
所以需对塑件的成形过程及对选用的模架分析,选择主流道。
其衬套的固定用定位圈配合固定在模具的定模座板上。
主流道衬套和注塑机喷嘴的配合如图6所示。
连接主流道与浇口的熔体通道叫分流道,分流道起分流和转向作用。
熔融塑料沿分流道流动时,要求它尽快地充满型腔,流动中热量损失要尽可能小,流动阻力要尽可能低。
同时,应能将塑料熔体均衡地分配到各个型腔。
尽量使分流道长度最短,但是,塑料以低温成型时,为提高成型空间的压力来减少成型制品收缩凹陷时,或欲得壁厚较厚的成型制品而延长保压时间,减短流道长度并非绝对可行。
因为流道过短,则成型制品的残留应力增大,且易产生飞边,塑料的流动不均,所以流道长度应以适合成型制品的质量和结构为宜。
排位的形状分“O”形、“H”形、“X”形、“S”形,分流道截面形状有:
圆形、半圆形、梯形、“U”形、矩形和正六角形。
常用的形式有圆形、梯形和“U”形。
较小的截面周长有利于减少熔融塑料的热量散失;但截面尺寸过小时,则材料的流动阻力大,延长了充模时间,易造成充填不足、烧焦、银纹、收缩凹陷等缺陷,或者必须提高注射压力来填满,故流道截面大小应根据材料的流动性、成型制品的质量及投影面积适度确定。
设计原则:
必须保证分流道的表面积与其体积之比值最小,既在分流道长度一定的情况下,要求分流道的表面积或侧面积与其截面积之比值最小。
PS流动性好,分流道粗糙度为0.3,流道直径3.2~9.5mm,在此取6mm.分流道如图6
浇口是连接分流道与型腔之间的一段细短通道,是浇注系统的最后部分,其作用是使塑料以较快速度进入并充满型腔。
它能很快冷却封闭,防止型腔内还未冷却的熔体倒流。
设计时须要考虑产品尺寸、截面积尺寸、模具结构、成型条件及塑料性能。
浇口应尽量短小,与产品分离容易,不造成明显痕迹。
当熔融塑料通过狭窄的浇口时,流速增高,剪切速率加大,熔体温度也随之升高,这对充填型腔是有利的。
同时,狭小的浇口在适当的保压补缩后,首先凝固而封闭型腔,是型腔内的熔料在无压力状态下自由收缩、凝固成形,因而塑料件内残余应力较小,可减小塑料件的变形与破裂。
此外,狭小的浇口便于使浇道凝料与塑料件进行分离也便于修整塑料件,成形周期短。
虽然如此,但是浇口截面尺寸也不能过小。
如果浇口尺寸过小,则使注射成形时压力将增大,冷凝快、补缩困难而造成塑料件缺料、缩孔或产生真空泡等缺陷,甚至还会产生熔体破裂而形成喷射现象,使塑料件表面出现凹凸不平。
同时,浇口的截面尺寸也不能过大。
浇口尺寸过大会降低注射速率,温度降低增加,塑料件表面会产生云层现象等缺陷。
一般,浇口的尺寸很难用理论公式进行计算,通常是根据经验来确定,制作时取下限,先作得小一些,然后根据试模时塑料件所表现出的质量情况进行修正。
通常,浇口的截面面积约为分浇道截面面积的3%~8%,截面形状多为矩形或圆形,浇口的长度约为0.5~2.0mm,其表面粗糙度一般为Ra0.4~0.2um。
冷料穴是为储存因熔体与低温模具接触而在料流前锋产生的冷料而设置的,这些冷料如果进入型腔将减慢熔体填充速度,最终影响制品的成形质量。
冷料穴一般设置在主流道的末端,分流道较长时,分流道的末端也应设冷料穴。
一般情况下,主流道冷料穴圆柱体的直径为5~6mm,深度为5~6mm。
对于大型制品,冷料穴的尺寸可适当加大。
对于分流道冷料穴,其长度为1~1.5倍的流道直径。
(二)、成型零件的设计
在模具结构中,决定塑料件几何形状和尺寸的零件叫做成形零件。
塑料注射模具的成形零件包括凹模、型心(有时也叫凸模)、镶块、成形螺杆、成形螺环等成形零件工作时,直接与塑料相接触,承受塑料熔体的高压料流的冲刷;在脱模过程中还要与塑料件产生摩擦;在整个成形过程中有可能还要接触程度不同的腐蚀性气体。
因此,成形零件要求要有正确的几何形状、较高的尺寸精度、较低的表面粗糙度值和一定的耐腐蚀能力;从结构上来讲,成形零件还要求结构合理,便于加工与装配,具有较高的强度、刚度及较好的耐磨性能。
(1)型腔
型腔是成型塑件制品外表面的主要零件,按其结构不同,可分为整体式和组合式两类。
整体式凹模由整块材料加工而成,其特点是牢固,使用中不易发生变形,不会使制品产生拼接线痕迹。
而组合式凹模在使用中则出现制品产生拼接线痕迹的几率高一些。
所以,此处采用整体式凹模。
如图7
(2)型芯
型芯是成型塑件内表面的零件。
主要有主型芯和小型芯。
对于简单的容器,如壳、罩、盖之类的塑件,成型其主要部分内表面的零件称主型芯,而将成型其他小孔的型芯称为小型芯或成型杆。
按结构主型芯可分为整体式和组合式两种。
此处采用组合式。
如图8
(三)顶出机构设计
在注射模中,将冷却固化后的塑料制品及浇注系统凝料从模具中安全无损坏地推出的机构称为脱模系统,也叫推出系统或顶出系统安全无损坏是指制品被推出时制品不变形,不损坏,不粘膜,无顶白,推杆位置不影响制品美观,制品被推出时不会对人或模产生安全事故。
注射模的脱模系统包括:
1、推杆、推管、推板、推块等推出零件。
2、复位杆、复位弹簧及推杆板先复位机构等推出零件的复位零件。
3、推杆固定板和推杆底板等推出零件的固定零件。
4、高压气体推出的气阀等配件。
5、内螺纹脱模系统中的齿轮、齿条、马达、油缸等配件。
脱模系统的动作方向与模具的开模方向是一致的。
顶出机构的设计规则:
1、尽量设法使塑件留于动模;2、保证塑件不变形不损坏完整脱出;3、尽量不损坏塑件的外观;4、结构可靠;5、每副模具的推杆的直径相同,方便加工;6、塑件推出模具10mm左右,对型腔斜度较大者,顶出塑件深度2/3即可。
顶出力的计算脱模力包括如下四点:
1、制品在模具中冷却定型时,由于体积收缩,产生抱紧力;2、不带通孔壳体类制品,推出时要克服大气压力;3、脱模系统(如推杆、推管和推板等)本身运动的摩擦阻力;4、制品与模具之间的粘附力。
在开始顶出塑件的瞬间所需克服的阻力最大,称为初始顶出力,以后还需的力称为相继顶出力,后者要比前者小,所以计算顶出力时,总是计算初始顶出力。
单个塑件所需的顶出力为:
Q=Ahp(fcosa-sina)=0.363×0.018×1.2×107×(0.2-0.017)=14300N
所以两个塑件所需的顶出力为28600N
推出机构的类型分为一级顶出机构、二级顶出机构。
其中一级顶出机构又可分为顶杆顶出机构、顶管顶出机构、推板顶出机构、顶块顶出机构、气压顶出机构、成型镶件和型腔顶出。
本次设计是使用单分型面,且塑件可一次推出,所以采用一级顶出机构中的顶杆顶出机构。
顶杆顶出机构是顶出机构中最简单、最常见的一种形式。
由于顶杆截面多为圆形,制造、修配方便、顶出效果好,因此在生产中广泛应用。
有于设置推杆的自由度较大,而且推杆截面大部分为圆形,容易达到推杆与模板或型芯上推杆孔的配合精度,推杆推出时阻力小,推出动作灵活可靠。
而推出零件固定板即推杆固定板,则与推杆一起运动,将塑件顶出型芯。
单个塑件推杆的根数及直径可通过以下公式计算并校核。
(四)冷却系统设计
在塑料注射成型中,注入模腔中的熔体的温度一般在200~300度之间,熔体在模腔中成型、冷却、固化成制品,当制品从模具中取出时,温度一般在60度左右,熔体释放出的热量都传递给模具。
为保证正常生产,模具必须将这部分热量及时传递出去,是模具的温度始终控制在合理的范围内。
模具中将这部分热量及时传递出去的结构叫做冷却系统。
热传递的方式有传导、对流和辐射。
模具中热传导的介质主要是冷却水(包括常温水和冻水)冷却介质最普遍的是用水冷却,因为水的热容量大,传热系数大,成本低廉,有时也用油和铍铜。
冷却回路的设计应做到回路系统内流动的介质能充分吸收成形塑件所传导的热量,使模具成形表面的温度稳定地保持在所需的温度范围内,并且要做到使冷却介质在回路系统内流动畅通,无滞留部位。
(1)冷却回路所需的总表面积计算
经查表及计算可得,单位时间内注入模具中树脂的质量M为77.76kg/h,模具成形表面的温度θ1为50ºC,冷却水的