1#焦化.docx
《1#焦化.docx》由会员分享,可在线阅读,更多相关《1#焦化.docx(80页珍藏版)》请在冰豆网上搜索。
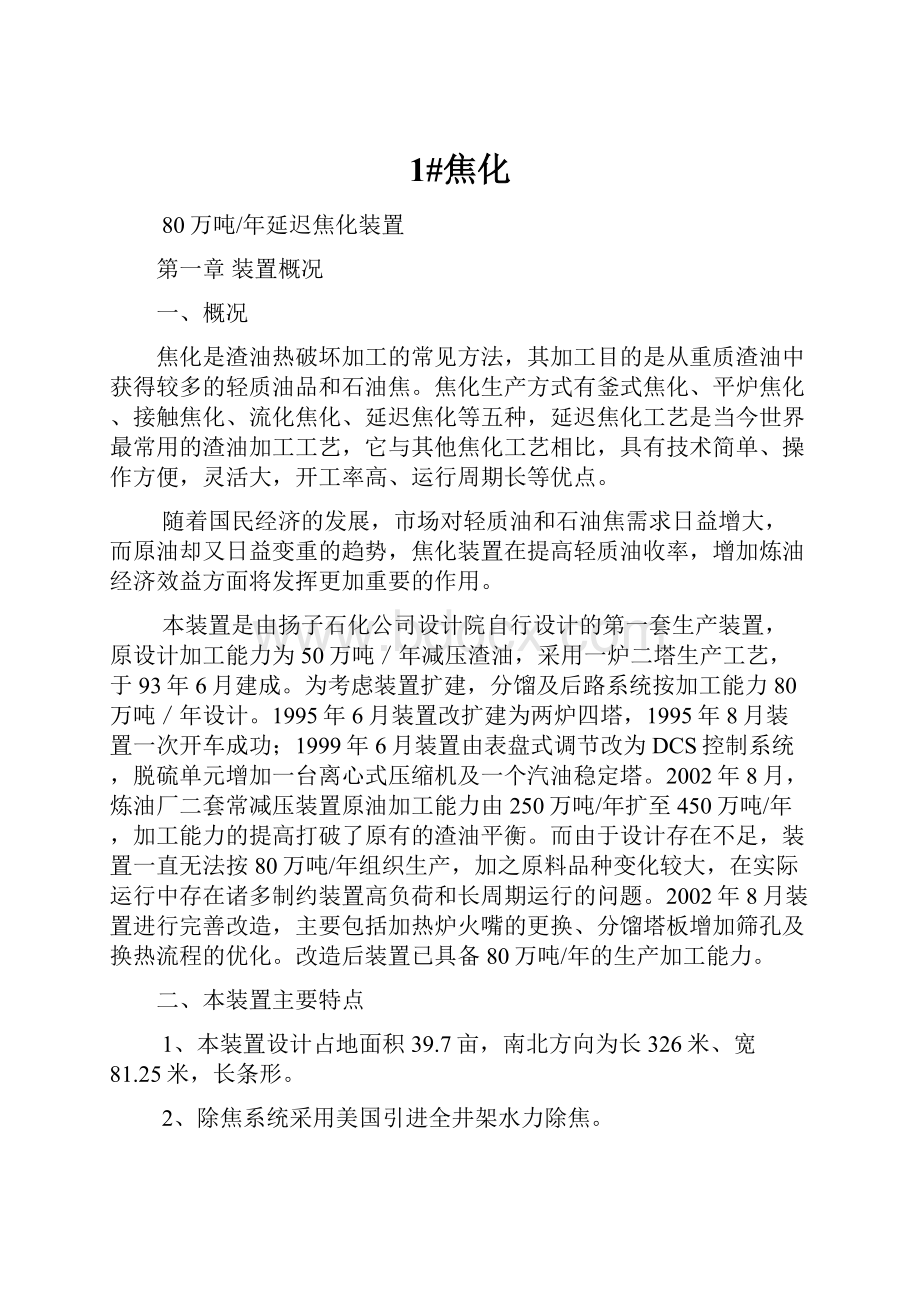
1#焦化
80万吨/年延迟焦化装置
第一章装置概况
一、概况
焦化是渣油热破坏加工的常见方法,其加工目的是从重质渣油中获得较多的轻质油品和石油焦。
焦化生产方式有釜式焦化、平炉焦化、接触焦化、流化焦化、延迟焦化等五种,延迟焦化工艺是当今世界最常用的渣油加工工艺,它与其他焦化工艺相比,具有技术简单、操作方便,灵活大,开工率高、运行周期长等优点。
随着国民经济的发展,市场对轻质油和石油焦需求日益增大,而原油却又日益变重的趋势,焦化装置在提高轻质油收率,增加炼油经济效益方面将发挥更加重要的作用。
本装置是由扬子石化公司设计院自行设计的第一套生产装置,原设计加工能力为50万吨/年减压渣油,采用一炉二塔生产工艺,于93年6月建成。
为考虑装置扩建,分馏及后路系统按加工能力80万吨/年设计。
1995年6月装置改扩建为两炉四塔,1995年8月装置一次开车成功;1999年6月装置由表盘式调节改为DCS控制系统,脱硫单元增加一台离心式压缩机及一个汽油稳定塔。
2002年8月,炼油厂二套常减压装置原油加工能力由250万吨/年扩至450万吨/年,加工能力的提高打破了原有的渣油平衡。
而由于设计存在不足,装置一直无法按80万吨/年组织生产,加之原料品种变化较大,在实际运行中存在诸多制约装置高负荷和长周期运行的问题。
2002年8月装置进行完善改造,主要包括加热炉火嘴的更换、分馏塔板增加筛孔及换热流程的优化。
改造后装置已具备80万吨/年的生产加工能力。
二、本装置主要特点
1、本装置设计占地面积39.7亩,南北方向为长326米、宽81.25米,长条形。
2、除焦系统采用美国引进全井架水力除焦。
3、焦炭塔冷焦时产生的油汽采用塔式直接接触半密闭式放空回收系统。
4、装置换热流程进行优化设计,以充分利用热源。
5、装置材质选型满足加工高硫原油需要。
第二章产品说明
一、产品用途
二、产品性质
1、液态产品
表2.1液态产品性质表(设计)
分析项目
产品
单位
延迟焦化装置
焦化
汽油
焦化
柴油
焦化
轻蜡油
焦化
重蜡油
比重
d20
0.7362
0.8311
0.8805
0.8840
胶质
mg/100ml
126
25.76
十六烷值
51
硫
%
0.74(设计)
0.76(设计)
0.66(设计)
0.70(设计)
0.50(沙轻)
1.67(沙轻)
2.63(沙轻)
溴价
g/100g
108.1
58.8
酸度
MgKOH/100ml
凝点
℃
<-15
26
30
闪点
℃
59
粘度
80℃mm2/s
0.48
5.97
7.57
100℃
0.36
5.11
6.69
氮
ug/g
4073
4609
灰份
wt%
0.002
0.004
残炭
wt%
0.039
0.017
机械杂质
wt%
0.036
0.54
重金属
ppm
V
0.5
Fe
1.8
Cu
0.1
Ni
0.1
馏程
℃
初馏
50
170
241
240
10%
85
215
304
325
50%
135
253
362
369
90%
177
294
416
418
干点
220
360
≤480
452
收率
%
16.7
23.5
25
2、焦化富气
表2.2焦化富气性质表(设计)
组份
甲烷
硫化
氢
乙烯
乙烷
丙烷
丙烯
正丁
烷
顺丁
烯
反丁
烯
碳五
以上
氢气
组成
(v/v%)
43.6
6.0
1.6
13
7.6
3.5
2.6
0.2
0.3
3.1
17.5
3、固品产品:
石油焦
表2.3石油焦性质表
序号
项目
单位
设计指标
质量分级指标
低硫焦
高硫焦
一级品
1A
1B
2A
2B
3A
3B
1
挥发份
wt%
11.5
≯12
≯12
≯14
≯17
≯18
≯20
2
灰份
wt%
0.20
≯0.3
≯0.3
≯0.5
≯0.8
≯1.2
3
含水
wt%
0.42
≯3
4
硫含量
wt%
1.51
≯0.5
≯0.5
≯0.8
≯1.0
≯1.5
≯2.0
≯3.0
3.0~6.0
5
堆积密度
t/m3
0.78
-
6
生焦密度
t/m3
0.85
-
7
真密度
g/cm3
-
2.08~2.13
报告
-
8
粉焦量
%
-
≯25
-
9
硅含量
%
-
≯0.08
-
10
钒含量
%
-
≯0.015
-
11
铁含量
%
-
≯0.08
-
4、其它产品
表2.4其它产品性质表(设计)
产品
组成
单位
指标
脱硫干气
硫化氢
ml/m3
≤100
酸性气
总烃
V%
≤2
液态烃
C2组分
V%
≤8
C5组分
V%
≤3
第三章原辅料及公用工程规格
一、原料性质
1、管输油减压渣油
表3.1管输油减压渣油性质表(设计)
比重d420
0.9653
硫含量wt%
1.09
凝点℃
37
氯含量PPM
7721
残炭wt%
12.4
灰分wt%
0.049
粘度80℃mm2/s
600~750
重金属PPM
Fe
17.9
Ni
6.9
V
3.6
2、进口原油
表3.2进口原油性质表
原油名称
沙特轻质原油
分析数据
原油类别
特性因数(K)
12.05
高硫中间基原油
密度,g/cm3,20℃
0.8565
粘度mm2/s,50℃
6.964
S含量,%
2.07
>560℃渣油
>560℃渣油
收率,%
19.3
密度,g/cm3,20℃
1.0245
粘度,mm2/s,100℃
2202
S含量,%
4.15
残炭,%
23.49
灰份,%
0.039
饱和烃,%
11.5
芳烃,%
54.0
胶质,%
27.9
沥青质,%
6.6
铁,ppm
2.41
镍,ppm
25.77
钒,ppm
93.22
铅,ppm
0.46
铜,ppm
0.20
钠,ppm
2.43
二、公用工程条件
表3.3公用工程条件一览表(设计)
名称
温度(℃)
压力(MPa)
中压蒸气MPS
240±20
1.0±0.1
低压蒸气LPS
饱和
0.35
冷却上水CWS
33
≥0.40
冷却下水CWS
43
0.25
软化水SW
30
≥0.2
工业水IW
32
≥0.40
工厂风PA
环境温度
≥0.40
氮气N2
环境温度
0.4~0.7
仪表风IA
环境温度
≥0.40
第四章物料、公用工程平衡表
一、物料平衡
本装置设计开工时数8000小时,在循环比为0.36条件下物料平衡如下。
表4.1物料平衡表(设计)
名称
比重d420
收率
(wt%)
千克/时
吨/天
万吨/年
50万吨/年
80万吨/年
50万吨/年
80万吨/年
50万吨/年
80万吨/年
原料
管输减压渣油
0.9653
100
62500
100000
1500
2400
50
80
产品
焦化富气
7.8
4875
7800
117.0
187.2
3.9
6.24
汽油
0.7362
13.2
8250
13200
198.0
316.8
6.6
10.56
柴油
0.8311
23.5
14687.5
23500
352.5
564.0
11.75
18.8
轻蜡油
0.8805
23
14375
23000
345.0
552.0
11.5
18.4
重蜡油
0.884
7
4375
7000
105.0
168.0
3.5
5.6
甩油
0.9093
1.7
1062.5
1700
25.5
40.8
0.85
1.36
焦炭
23.3
14562.5
23300
349.5
559.2
11.65
18.64
损失
0.5
312.5
500
7.5
12.0
0.25
0.4
二、公用工程消耗
公用工程消耗表(设计)
序号
项目
小时耗量
单位耗量
单位能耗
千克标油/吨
单位
数量
单位
数量
1
电
KW/h
1725
KW/t
21.86
6.56
2
燃料气
t/h
1.668
t/t
23.23
23.23
3
蒸汽
t/h
0.558
Kg/t
7.07
0.54
4
循环水
t/h
450
t/t
5.7
0.57
5
新鲜水
t/h
41.6
t/t.
0.52
0.1
6
工厂风
Nm3/h
120
Nm3/t
1.5
0.46
7
仪表风
Nm3/h
120
Nm3/t
1.5
0.46
合计
31.92
注:
不含气体脱硫系统
第五章生产方法及基本原理
一、加热、反应单元
1、任务
利用管式加热炉将重质油品加热到一定的反应温度495~505℃,使得重油在没有催化剂的情况下进行热破坏反应,反应过程复杂,主要为缩合、裂解反应,反应的结果最终生成小分子的气体化合物和大分子焦炭物质。
反应过程中加热炉提供反应热,焦炭塔提供反应场所。
2、生产原理
在高温条件下,大分子物质,诸如烷烃、环烷烃、芳香烃等物质发生c-c键断裂,生成不稳定的自由基,自由基经过重新组合和释放新的自由基,形成复杂的反应,从而生成一系列复杂的化合物。
3、主副反应方程式
3.1、烷烃
烷烃在高温下主要反应是进行裂解反应,反应产物是分子量小的烷烃和烯烃分子。
裂解反应首先发生在c-c键的断裂,因为c-c键的键能比c-H键的键能小。
以正十六烷烃为例
C16H34CH3.+C15H31.
所生成的小自由基从原料烃中夺取氢,本身变为烷烃,而把原料变为自由基。
CH3.+C16H34CH4+C16H33.
大分子自由基对热是不稳定的,在b位c-c键处很容易断裂,进而生成小分子的伯碳自由基和烯烃。
伯碳自由基进一步在b位断裂,最终生成烯烃。
C16H33.C7H14+C9H19.
↓
C2H4+C7H15.
低分子的自由基再次从原料中夺取氢,把原料烃分子变为自由基,重复以上反应,形成链反应。
两个自由基的结合,可以使链反应结束。
3.2、环烷烃
环烷烃主要是裂解和脱氢反应,裂解反应主要是侧链反应和断环。
3.3、芳香烃
芳香烃的热反应主要是断侧链和缩合反应。
3.4、烯烃
烯烃主要是各类饱和烃和烃裂解反应生成的,这些烯烃将继续发生裂解反应,同时也与其它烃类交叉进行反应。
使得反应变得极其复杂。
烯烃在热作用下的主要反应为裂解、叠合和缩合反应。
在焦化反应温度(400℃)下,主要是裂解反应,反应产物是小分子烯烃或二烯烃分子。
例如:
CH3-CH2-CH2-CH2-CH=CH2--→CH3-CH=CH2+CH3-CH=CH2
当温度高于600℃以上时,烯烃发生缩合反应,生成芳香烃和分子量大的叠合物,甚至叠合为焦炭。
3.5、胶质和沥青质
胶质和沥青质在高温下发生缩合反应生成焦炭。
减压渣油在受热时的裂解和缩合反应决非各种单体反应的综合,而是反应物之间、反应物与反应产物之间以及反应产物之间的反应,使反应变得相当复杂。
二、分馏单元
1、任务
反应单元生成的高温油气,在分馏塔的塔盘上,经过气体、液体两相接触,达到传质、传热,从而将高温油汽分离成为不同馏程范围的气体组份、液体组份。
2、基本原理
焦炭塔产生的大量油汽混合物,从分馏塔底部进入,汽流在塔内沿塔上升,在上升过程中与下降的液流在塔板上接触、传质,其中挥发份的含量逐渐增加,塔内有足够的塔板数,在升到塔顶的气流组成达到相应的分离要求。
液流在下降的过程中逐板与气流传质,将易挥发份传递给汽流,并从气流中取得难挥发份,从而使得液流达到相应的分离效果。
三、脱硫单元
1、任务
焦化反应过程中生成的低压富气含有H2S和SO2等气体,在高压低温下利用N甲基二乙醇胺脱除掉其中的H2S和SO2气体,从而得到合格的燃料气和酸性气。
2、生产原理
利用吸收与解析的反应机理,在改变操作条件的情况下达到吸收与解析的目的。
低温高压有利于吸收,高温低压有利于解析。
四、水力除焦单元
1、任务
清除焦炭塔内反应过程中生成的焦炭,为下一步生产提供反应场所。
2、原理
水力除焦利用高压水流,从水力除焦器喷射出来的动力,冲击焦炭塔内的硬质焦
炭从而使焦炭破碎脱落而清除出塔。
五、汽油吸收与稳定单元
1、任务
焦化分馏系统来的焦化富气经压缩机压缩后进入汽油吸收塔,利用粗汽油和稳定汽油吸收压缩富气中的C3、C4、C5组分,富吸收汽油进入脱吸塔(T2001)经重沸分离,分离出液态烃组分。
2、原理
基于汽-液平衡原理,汽液在汽油吸收塔内与在脱吸塔内充分传质,建立汽液平衡,达到吸收与脱吸的效果。
第六章工艺流程简述
一、焦化部份
延迟焦化装置原料为我厂常减压装置减压渣油(简称VTB),在常减压装置正常生产时,由减压塔塔底泵将热渣油送至延迟焦化装置原料缓冲罐(V101),当常减压装置停工或生产不正常时,由炼油厂罐区渣油泵送渣油至延迟焦化装置原料缓冲罐(V101)。
原料进装置缓冲罐(V101)后,由原料泵(P101)抽出,打入加热炉(F101)对流段,被加热到330℃,出对流段进入分馏塔(T102)下部换热塔盘(0#和5#)上,在此与焦炭塔(T101)来的油气接触换热。
原料油中轻组分蒸发,与焦化油气一起上升至分馏塔(T102)上段。
焦炭塔(T101A、B、C、D)来的油气与原料油接触换热后,油气温度降低,循环油全部冷凝,冷凝下来的循环油与原料油一起,流到分馏塔(T102)底,作为焦化油,温度380℃。
焦化油由辐射进料泵(P102)从分馏塔(T102)底抽出,打入加热炉(F101)辐射段,焦化油被加热到495~505℃,然后通过四通阀进入焦炭塔(T101)。
焦化油在焦炭塔(T101)内由于高温长时间发生裂解、缩合反应。
缩合反应生成的焦炭聚结在焦炭塔内。
裂解生成的油气一起自焦炭塔(T101)顶逸出,进入分馏塔(T102)底与从加热炉(F101)对流段来的原料油接触换热,换热后的油气上升到分馏段。
分馏塔底油经过滤器(X102)过滤后,由塔底循环泵(P116)抽出打回分馏塔底,建立底部循环,带出塔内焦粉。
重蜡油由重蜡油泵(P104)自六层塔板抽出,经重蜡油蒸汽发生器(E107)与脱氧水换热产出1.0MPa蒸汽,重蜡油由370℃降温至230℃,然后一部分重蜡油至分馏塔五层、八层作为回流,另一部分重蜡油进入水冷器(E110)冷却到90℃,作为燃料油出装置;装置自开工以来,一直无重蜡油抽出。
轻蜡油由轻蜡油泵(P103)自轻蜡油集油箱(十层塔板上方)抽出,一部分回分馏塔十层作热回流,另一部分至汽油脱吸塔底汽油再沸器E2002后,再送至轻蜡油蒸汽发生器(E106)发生1.0MPa蒸汽,轻蜡油温度由335℃降到210℃,然后一部分轻蜡油返回分馏塔(T102)第十、十四层作为回流,一部分至焦炭塔顶作急冷油,其余部分至轻蜡油除氧水换热器(E105)加热除氧水,降至140℃的轻蜡油送至轻蜡油空冷器(E121),再经过水冷器(E111)或重蜡油水冷器(E110)冷却到80℃后出装置。
柴油由柴油泵(P105)自柴油集油箱(二十二层塔板上方)抽出,经柴油/锅炉水换热器(E102)换热发生0.8MPa蒸汽,温度由270℃降至190℃,而后送往柴油/除氧水换热器(E103),温度降至170℃,再进入柴油/冷渣油换热器(E112)与冷渣换热,送往柴油软化水换热器(E104),温度降至145℃,再去空气预热器加热空气后去柴油空冷器(E115),温度降至80℃,一部分柴油回分馏塔二十二、二十五层作回流。
另一部分柴油经吸收柴油冷却器(E109)冷却至60℃左右送出装置。
分馏塔顶回流自分馏塔(T102)第三十五层抽出,经塔顶回流泵(P106)打入回流空冷器(E114)再经水冷器(E120)冷却至50℃返回分馏塔(T102)顶第三十八层。
分馏塔(T102)顶油气经分馏塔顶空冷器(E113),分馏塔顶冷却器(E108)冷却至40℃进入分馏塔顶油气分液罐(V102)进行油气分离及脱水。
焦化汽油由焦化汽油泵(P107)送至T201作为汽油吸收的粗汽油。
富气送本装置吸收脱硫部分或3万标米3/时气体处理装置,脱硫后干气作为燃料气;含硫污水自压至含硫污水缓冲罐(V122)进行油水分离,含硫污水由含硫污水泵(P114AB)抽出送出装置,油由(P114C)返回分馏塔顶油气分液罐(V102)。
切焦采用有井架水力除焦,切焦水用高压水泵(P115),自高位水箱(V114)抽出,打入焦炭塔顶,通过钻杆、切割器进行水力除焦,切焦水流入沉淀池,逐级沉降处理,处理后的切焦水经泵提升至高位水箱循环使用。
二、蒸汽发生部分
20~30℃,0.2~0.25MPa软化水进入装置后,进软化水罐(V119),由泵(P119)抽出,经柴油软化水换热器(E104),加热到85~90℃后,至除氧器(V121)除氧后,经锅炉给水泵(P120)抽出,一路进轻蜡油脱氧水换热器(E105)加热到150℃进入汽包(V112),产汽量约6.0t/h左右。
汽包内热水在轻、重蜡油蒸汽发生器(E106、107)内循环,汽化产生饱和蒸汽,经汽包内汽水分离器分离后,送加热炉(F101)对流段过热到240℃,送装置1.0MPa管网,供装置各部位使用。
另一路除氧水进入柴油-除氧水换热器(E103)与柴油换热后进入低压蒸汽发生器(E104),低压蒸汽发生器内热水经柴油加热,发生0.8MPa低压蒸汽送入0.6MPa蒸汽管网。
除氧用蒸汽主要由凝结水产生的二次蒸汽供给,不足部分由管网引入1.0MPa蒸汽经调节阀进除氧器。
脱硫单元,密闭放空单元,延迟焦化返回的蒸汽凝液,经凝结水管线进除氧器(V121)。
三、焦炭塔顶气密闭放空系统
焦炭塔(T101)大吹汽以及冷焦时产生的大量蒸汽及少量油气进入接触冷却塔(T204),从塔顶打入蜡油馏分在塔(T204)中洗涤下重质油,用接触冷却塔底泵(P206)由塔底抽出塔底油(300℃),经接触冷却塔底冷却器(E210)冷却至80℃,返回塔顶,部分出装置。
塔顶蒸汽及轻质瓦斯油气(150℃)经塔顶空冷器(E208),冷却至80℃,进入接触冷却塔顶汽液分离罐(V209),分出的污油由轻污油泵(P207)送至V1103,污水排入污水池(N308),不凝气经水冷器(E209)冷却后进火炬气分液罐(V211)分液后放火炬。
四、气体处理系统
粗汽油由汽油泵(P107)打入汽油吸收塔(T201)23层,与从塔(T201)底进入的高压富气逆向接触,吸收高压富气中的重组分,进入塔(T201)底,由吸收汽油增压泵(P2002)增压至2.09MPa,经汽油富吸收油换热器(E2001AB)加热到150℃,进入解析塔(T2001)中部。
富吸收汽油进入T2001底部由轻蜡油泵(P103)来的轻蜡油在E2002中加热到230℃,汽油中的液态烃组分继续上升,与V2001打来的液态烃组分接触分离,液态烃组分经塔顶冷却器(E2003)冷却后进入解析塔顶回流罐(V2001),一部分作T2001回流,一部分出装置。
T2001底稳定汽油进入E2001AB与富吸收汽油换热后,温度降至80℃,再经汽油冷却器(E2004AB)冷却至40℃,一部分至T201第25层作回流,另一部分出装置。
由分馏塔油汽分离罐(V102)来的低压富气压力为0.02-0.06MPa,温度为40℃进入低压富气分液罐(V201),由罐(V201)顶经流量调节阀HCV-116进入富气压缩机(C201C)一段,经一段压缩至0.294Mpa(表)温度升至111.6℃,进入中间气体冷却器(E-215)冷却至40℃后进入中间气液分离罐(V-251)除去凝液,除去凝液的富气进入离心式富气压缩机(C201C),经二段压缩至1.3Mpa(表),温度升至143℃,经压缩富气空冷器(E201)和压缩富气水冷器(E202)冷至40℃后进入压缩富气分液罐(V203),凝油去V102。
高压富气进入汽油吸收塔(T201)下部,与顶部下来的吸收汽油接触后,上升至塔(T201)顶部,经水冷器(E2005)冷却后进富气分液罐(V204),污油排入火炬气分液罐(V116),富气进入胺液吸收塔(T202)下部,与顶部下来的N-甲基二乙醇胺溶液进行接触,塔顶干气进入燃料气分液罐(V205),分离后燃料气送燃料气管网。
外来N-甲基二乙醇胺溶液由N-甲基二乙醇胺供给泵(P205)打入胺液混合罐(V207),废胺液由胺液混合罐底流入废胺液收集罐(V208),经氮气压出,去V103作为加热炉注水处理。
新鲜胺液用胺液补给泵(P203)由胺液混合罐(V207)抽出送胺液再生塔(T203)下部,贫胺由(T203)底经胺液循环泵(P202)抽出进入贫富胺换热器(E203)与富胺液换热,温度由114℃,降至52℃,再进入贫胺水冷器(E204和E117))冷却至40℃进入胺液过滤(X202AB)过滤杂质,再送入胺液吸收塔(T202)顶部与底部上来的压缩富气接触。
富胺液由胺液吸收塔(T202)底部压出进入贫富胺换热器(E203)与贫胺液换热后进入富胺加热器(E205)加热到102℃进入闪蒸罐(V206),闪蒸气放火炬,闪蒸后富胺进入胺液再生塔(T203)顶部,塔顶酸性气送硫磺回收装置。
目前装置所产低压富气送至3万标米3/小时气体处理装置,汽油经本装置汽油稳定塔(T2001)分离液态烃后送入加氢精制装置。
脱硫系统氮气保压,处于备用状态。
第七章工艺条件一览表
表10.1工艺卡片
序号
工艺指标名称
单位
仪表位号
控制范围
备注
一
原料性质指标
1
减压渣油粘度
mm2/S
实测
厂控
二
产品质量指标
1
汽油干点
℃
220
车间控制
2
柴油干点