工艺管道施工方案.docx
《工艺管道施工方案.docx》由会员分享,可在线阅读,更多相关《工艺管道施工方案.docx(51页珍藏版)》请在冰豆网上搜索。
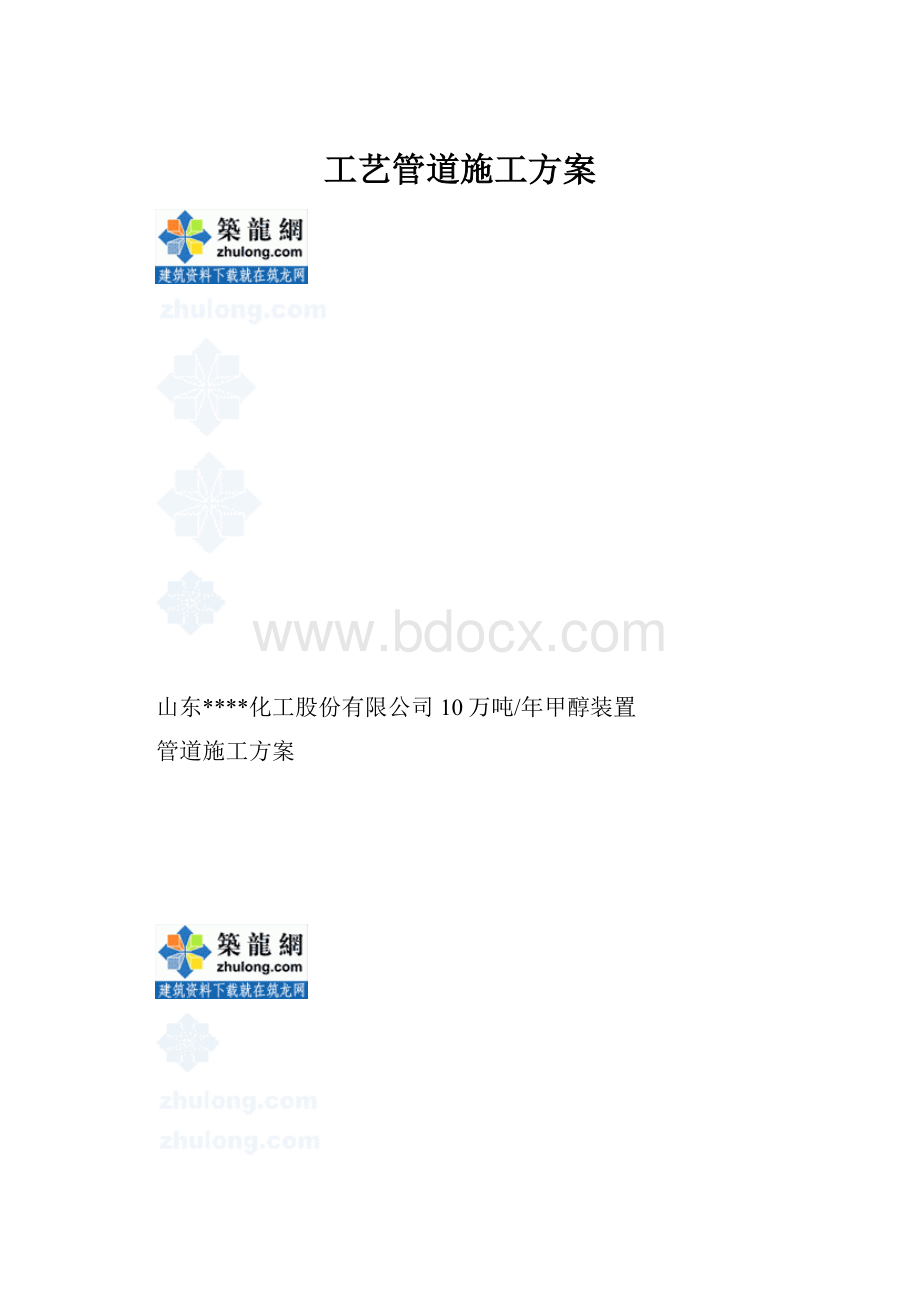
工艺管道施工方案
山东****化工股份有限公司10万吨/年甲醇装置
管道施工方案
1.编制目的
为保证工艺管道安装工程的顺利进行,安装进度和质量满足业主要求,特编制本方案作为施工指导性技术文件。
2.编制依据
2.1《工业金属管道工程施工及验收规范》(GB50235-97);
2.2《现场设备、工业管道焊接工程施工及验收规范》(GB50236-98);
2.3《管道施工手册》;
2.4《管支架标准图集》(HG/T21629-1999);
2.5我公司以往施工经验及技术资料。
3.工程概况
按我公司以往甲醇装置施工经验其工艺管道有低压管、中压管和高压管,管道材质主要有碳钢(Q235-A、20#、20G、16Mn)、不锈钢(0Cr18Ni9、00Cr17Ni14Mo2)和耐热钢(15CrMo)等。
本装置属于典型的化工装置,其管道材质多,高温、高压、有毒、易爆介质均有,因此技术和质量要求高。
同时,装置中管道布置紧凑、密集,管道形式多样,如热动力管线、传动设备管线、伴热管等,加上管道的焊接质量及探伤比例高,对施工技术和施工组织提出了较高要求。
4.主要实物量
(待详细施工图纸到齐后再行统计)
5.管道施工程序
5.1施工原则:
5.1.1先地下、后地上;先大口径管道、后小口径管道;先主要物料管道、后辅助物料管道;先主管、后支管。
但要根据设备安装情况进行合适的调整。
5.1.2管道就位前应安装好支吊架。
5.1.3伴热管线应在工艺管完成实验合格后方可安装
5.1.4管道系统试压应在焊接检验和应力清除、热处理合格后进行。
5.1.5管道上的仪表接头应在管道予制时完成。
5.2管道安装流程见图5-2
6.管道安装技术要求
6.1管道安装前一般应具备下列条件
6.1.1与管道有关的土建工程经检查合格,满足安装要求。
6.1.2与管道连接的设备找正合格,固定完毕。
6.1.3设计及其它相应技术文件齐全,施工图纸业经会审。
6.1.4施工方案业经审批,技术交底和必要的技术培训已完成。
6.1.5管道施工图纸已按施工需要进行了预处理,焊口标记明确,探伤比例已确定。
6.1.6施工执行标准、规范和验评标准已经确定。
6.1.7各种材质的焊接工艺评定合格,焊工已经资格考试。
6.1.8工程材料的检验、试验工作完成,并已作好相应材质的标记。
6.1.9施工记录和质量评定记录表格齐全。
6.1.10现场三通一评已满足施工要求,工、机具,手段用料能满足需要。
6.2材料检验
6.2.1管子、管件、阀门、紧固件及卷管板材必须有制造厂的合格证明书,其指标应符合本装置设计及其指定的规范和标准的要求。
6.2.2管子、管件、阀门在领料及使用前首先应核对其规格、型号、材质是否符合设计要求,然后进行外观检查,要求为:
a、无裂纹、缩孔、夹渣、折迭、重皮等缺陷。
b、无超过壁厚负偏差的锈蚀或凹陷。
c、验收合格后,不锈钢与碳素钢应分开贮存,不得与碳素钢接触。
6.2.3紧固件检验
6.2.3.1对所有到货的螺栓紧固件仔细进行检查,螺栓与螺母的螺纹应完整,无伤痕,毛刺等缺陷,其配合应良好,无松动,卡等现象。
6.2.3.2检查紧固件的规格、材质的标记,印记在齐全,正确,并符合设计及产品质量证明书的规定。
管架、管托预制
技术交底
方案编写
技术培训
施工技术准备
焊工培训
管工培训
图纸会审
规范及验评标准
工艺评定
管架安装
焊口热处理
焊口热处理
资格确认
试压前共检
无损检验
组
对
焊
接
现场安装
管内清扫封闭
无损检验
组对及焊接
管下料及
坡口加工
管道预制
平台铺设
试压
返修
返修
阀门检验
标记编号
标记移植
现场三通一平
劳动力、工机具等资料配置
材料检验
工程交接
联动试车
综合检查
气密试验
化学清洗
系统吹扫
材料验收
图5-2管道安装流程图
6.2.3.3合金钢螺栓、螺母应每批各取两个进行光谱检验,当有不合格时,应逐个进行检验。
6.2.3.4高压螺栓、螺母应从每批中各取两个进行硬度检验,当有不合格时,该批螺栓、螺母不能使用。
6.2.4法兰检验
6.2.4.1合金钢法兰应对每批进货(同制造厂、同规格、同型号、同时到货)进行材质复查,并应做标记。
6.2.4.2法兰验收应分清型式,其密封面应平整光洁,不得有毛刺及径向沟槽,凸凹面法兰及松套法兰应能自然嵌合。
6.2.5非金属垫片应质地柔韧,无老化分层现象,表面不应有折损,皱纹等缺陷,金属垫片的加工尺寸,光洁度和硬度应符合要求,表面不得有裂纹、毛刺、凹槽、径向划痕及锤斑等缺陷。
6.2.6阀门检验
6.2.6.1供货的阀门型号、规格、铭牌、编号、材质、压力等级等均应符合图纸设计要求。
6.2.6.2外部和可见的内部表面、螺纹、密封面应无损伤、锈蚀现象,安全阀的铅封应良好。
6.2.6.3阀门进入现场后,应按规范要求进行阀门的耐压试验,低压阀门应按每批同制造厂、同规格、同型号抽查10%,但不得少于2个,公称直径小于40的低压阀门仅做外观检查,高、中压和有毒及易燃易爆介质用的阀门应逐个进行试验。
6.2.6.4阀门的壳体试验压力不得小于公称压力的1.5倍,试验时间不少于5min,以壳体填料无渗漏为合格,密封试验室以公称压力进行,以阀瓣密封面不漏为合格。
6.2.6.5试验合格的阀门,应及时排尽内部积水,并吹干。
除需要脱脂的阀门外,密封面上应涂防锈油,关闭阀门,封闭出入口,做出明显标记,并填写阀门试验记录。
6.2.7支吊架弹簧的检验
管道支、吊架弹簧应有合格证书,其外观及几何尺寸应符合下列要求:
a、弹簧表面不应有裂纹、折迭、分层、锈蚀等缺陷。
b、尺寸偏差应符合图纸要求。
c、工作圈数偏差不应超过半圈。
d、在自由状态下,弹簧各圈节距应均匀,其偏差不得超过平均节距的10%。
e、弹簧两端支承面应与弹簧轴线垂直,其偏差不得超过自由高度的2%。
6.3管道的脱脂
本装置所有管道、阀门和管件若需脱脂处理,要求如下:
6.3.1组对前将所有需脱脂的管子、阀门和管件放入盛有四氯化碳的槽内浸泡1-1.5小时,脱脂后应将溶剂排尽。
用清洁干燥的白滤纸擦试管道及其附件的内壁,纸上应无油脂痕迹为合格。
6.3.2脱脂合格的管道应及时封闭,保证在以后的工序中不再被污染,并填写《管道系统脱脂记录》。
6.3.3脱脂后的管道组成件安装前必须进行严格检查,不得有油迹污染及二次污染。
7.管道预制
7.1管道预制程序如下:
检查
焊接
组对
坡口加工
下料
7.2管道预制前,各小组应将流程图、平面布置图与现场实际情况进行核对,确定无误后再下料。
7.3碳钢管一般用氧乙炔气割方式下料,镀锌钢管及公称直径小于或等于50mm的碳钢管用机械法切割。
不锈钢管应用机械或等离子方法切割。
7.4切口表面应平整,无裂纹、重皮、毛刺、凸凹、缩口、熔渣、氧化物、铁屑等。
切口倾斜偏差不应大于管子外径的1%,且不得超过3mm。
见下图:
7.5管道的坡口加工形式及组对间隙见图
坡口加工形式及组对间隙
项次
厚度
坡口名称
坡口形式
坡口尺寸
备注
间隙
C
钝边
d
坡口角度
α(β)°
1
3~9
V形
坡口
0~2
0~2
65~75
2
法兰角
焊接头
—
—
—
K=1.4S但不大于颈部厚度
3
承插焊
接法兰
1.6
—
—
K=1.4S且不大于颈部厚度
7.6管子、管件对接焊口的组对应做到内壁齐平,内壁错边量不宜超过壁厚的10%,且不应大于2mm。
7.7不等厚管子、管件组对时,如果内壁错边量超过上表的规定或外壁错边量大于3mm时,应按下图进行修整。
S2-S1≤10mmS2-S1≤10mm
内、外壁尺寸均不相等内壁尺寸不相等的削薄
焊件坡口形式
7.8管道预制应考虑运输和安装的方便,并留有调整活口。
预制完毕的管段应将内部清理干净,封闭管口并编好标号妥善保管。
7.9预制管道组合件应具有足够的刚性,不得产生永久性变形。
7.10煨弯
7.10.1管道煨弯可采用冷弯或热煨工艺,不锈钢管以冷弯为宜。
7.10.2弯曲半径应大于管子外径的3.5倍。
7.10.3按图并由下列公式计算出弯曲管的变形应不超过8%
椭圆度=(a-b)/D×100%
D—弯曲前管子的外径
a—弯曲后管子的长径
b—弯曲后管子的短径
7.10.4弯管前、后的壁厚之差,不得小于设计壁厚,且≤15%弯管前壁厚。
7.10.5弯管外观质量应符合下列规定:
a、不得有裂纹。
b、不得存在过烧,分层等缺陷。
c、不宜有皱纹。
7.11管道预制的一般规定
7.11.1对于大于16″的大口径管道组对时可采用定位卡板。
定位卡板的材质应
与管道材质相同,定位卡板的切除应采用切割或磨削的方法。
7.11.2管道预制应在钢平台或水泥地面进行,不得在砂土地上组对焊接。
7.11.3预制组件应有足够的刚性,不得产生永久变形。
预制完后应及时编号、封口,妥善保管。
7.11.4管道预制应在X、Y、Z三个方向上的适当部位预留调整段或调整口,调整口的直管段宜加长50-100mm,调整段宜现场实测。
7.11.5管道上仪表接头及其它支管接头(包括临时管线接头)应在预制时一起完成,以避免管道就位后开孔及焊接,造成管内熔渣存积。
7.11.6焊接连接的阀门,在焊接时应使阀门处于开启状态。
7.12支、吊架预制作
7.12.1支、吊架形式按设计图纸选用标准图。
7.12.2支、吊架的形式、材质、加工尺寸及焊接等应符合设计要求。
7.12.3焊制管托时应采取反变形措施。
7.12.4制作合格的支、吊架,应进行防锈处理,编号标记,妥善保管。
8.管道安装
8.1管道安装前应具备的条件
8.1.1与管道有关的土建工程经检验合格,满足安装要求,并办理交接手续。
8.1.2与管道连接的设备找正合格、固定完毕。
8.1.3管子、管件、阀门已按设计文件规定核对无误检验合格,内部已清理干净。
8.1.4管道安装前有关工序如清洗、脱脂等已进行完毕。
8.2管道安装
8.2.1管道上的法兰连接
·管道安装前应根据设计规定,仔细核对法兰的等级和连接尺寸以及密封垫片,并对法兰密封面及密封垫片进行外观检查,不得有影响密封性能的缺陷存在。
·法兰连接时应保持平行,其偏差不大于法兰外径的1.5/1000且≤2mm,不得用强紧螺栓的方法消除歪斜。
·法兰连接时应保持同轴,其螺栓孔中心偏差一般不超过孔径的5%,并保证螺栓自由穿入。
·管道安装时连接螺栓、螺母应使用同一规格,安装方向一致,并根据要求涂
以二硫化钼油脂。
紧固螺栓应对称均匀,松紧适应,紧固后外露长度不大于2倍螺距。
8.2.2与传动设备、静设备连接的管道
·与传动设备、静设备连接的管道安装前必须将其内部处理干净。
·与传动设备连接的管道,其固定焊口应远离设备,以避免焊接应力的影响,保证管道在无应力条件下组对、安装。
·在安装与静设备连接管道前,应对设备的敞口处采取遮盖措施。
安装管道时应在管法兰与设备法兰间加设临时盲板,避免焊渣和杂物进入设备内,加设临时盲板应做好标识和记录。
·安装管道过程中,不要随意敲击设备,更不要在设备附近随意加热,以避免设备局部受热、受损。
8.3管道对口时应检查平直度,其技术要求见表
项目
允许偏差
备注
水平度
±1‰
全长允许偏差<10mm
垂直度
±1‰
8.4管道安装的允许偏差应符合表
项目
允许偏差
坐标
室外
25
室内
15
标高
室外
±20
室内
±15
水平管道平直度
DN≤100
2L‰,最大50
DN>100
3L‰,最大80
立管铅垂度
5L‰,最大30
成排管道间距
15
交叉管的外壁
或绝热层间距
20
L-管子有效长度DN-管子公称直径
8.5管道的坡向、坡度应符合设计规定,管道的坡度可用支座下的金属垫片、板调整,吊架可用吊杆螺栓调整,垫片应与预埋件或钢结构焊接。
8.6蒸汽伴热管安装
8.6.1蒸汽伴管的安装范围、材料、长度按设计规定执行。
8.6.2水平管道的伴热管设在被伴管道的下方;垂直管道的伴管者为二根时应均匀分布,若为一根可安装在被伴管便于安装的一侧。
伴管内的蒸汽流向应与被伴管道内的介质流向相反。
8.6.3伴管表面包扎非石棉绝热带用镀锌铁丝固定在主管上,直伴管绑扎点间距为1米。
8.7阀门安装
8.7.1法兰或螺纹连接的阀门应在关闭状态下安装。
8.7.2对焊阀门与管道连接焊缝层宜采用氩弧焊施焊,保证内部清洁,焊接时阀门不宜关闭,防止过热变形。
8.7.3安装阀门前,应按设计核对型号,并按介质流向确定其安装方向。
8.7.4安装安全阀时,必须按下列规定进行
·安全阀应垂直安装。
·管道投入试运时,应及时进行调校。
·开启和回座压力应符合设计文件的规定。
8.8支、吊架安装
8.8.1管道支、吊架制作标准应按设计要求的标准图进行制作。
8.8.2管道安装时应及时进行支、吊架的固定和调整工作。
支、吊架的位置应正确安装平整牢固与管子接触良好。
支架底板及支、吊架的工作面应平整。
8.8.3无热位移的管道其吊杆应垂直安装,有热位移的管道吊点应设在位移的相反方向,按位移值1/2偏位安装两根热位移方向相反或位移值不等的管道,不得使用同一吊杆。
8.8.4导向支架或滑动面应洁净平整,不得有歪斜和卡涩现象。
其安装位置应从支承面中心向位移反方向偏移,偏移量应符合设计文件规定。
8.8.5管道安装时不宜使用临时支、吊架,当使用临时支、吊架时不得与正式支、吊架位置冲突,并应有明显标记,在管道安装完毕后应予拆除。
8.8.6支、吊架的焊接应由合格焊工施焊,并不得有漏焊、欠焊或焊接裂纹等缺
陷。
管道与托架焊接时,管子不得有咬边,烧穿等现象。
8.8.7制作合格的支、吊架应进行除锈刷漆。
8.8.8安装U型和Ω型补偿器,应按设计规定值在两个固定支架间的管道安装完毕之后进行预拉伸或预压缩工作,其允许误差为±10mm。
8.9静电接地的安装
8.9.1液氧、氧气和含有CO(一氧化碳)、甲醇、HAC等易燃易爆物料管道,以及进出个工段的管道始末端均应采取静电接地,接地电阻<100欧姆,接地引线采用焊接形式。
8.9.2用作静电接地的材料或零件,安装前不得刷油,导电接触面必须除锈或妥善连接,导电良好。
安装完毕后应进行测试,并填写《管道静电接地测试记录》。
9.管道焊接及检验
本装置焊接工程量大,材料种类较多,焊接难度大,质量要求高。
因此,必须严格执行方案规定的技术要求和焊接工艺。
9.1焊材选用
焊材选用表
管道材料
焊条
焊丝
20#、20G、16Mn
E4303或E4315、E5015
Ho8Mn2SiA
0Cr18Ni9
EO-19-10-16
HoCr21Ni10
00Cr17Ni14Mo215CrMo
EO-18-12Mo2-16
热307
HoCr19Ni12Mo2
热3.7
0Cr18Ni12Mo2Ti
EO-18-12Mo2No-16
HooCr19Ni12Mo2
0Cr18Ni9Ti
E1-23-13-16
H1Cr24Ni13
0Cr17Ni14Mo2316L
EO-23-13-16
H1Cr24Ni13
9.2焊接工艺程序
技术准备
技术准备
管道下料、组对
材料检验
技术准备
焊接工艺评定
焊接
资料整理
焊口热处理
无损检验
返修
焊接
预热
9.3焊接方法选择
工艺管道对焊全部采用手工氩弧焊打底,手工电弧焊盖面;承插焊全部采用手工电弧焊。
不锈钢管道对接焊时,采用管内充氩保护。
9.4焊接技术要求
9.4.1焊工施焊前应按照焊接工艺指导书的要求通过资格考试,合格后方可上岗操作。
9.4.2严格执行焊材的入库、保管、发放、回收制度。
9.4.3焊条使用前必须按规定进行烘干、恒温,随用随取。
9.4.4当现场环境出现以下任一情况时,应采取防护措施方可进行焊接。
a、雨、雪天;
b、风速超过8m/s
c、环境温度在5℃以下。
当环境湿度超过90%时,应停止进行焊接作业。
9.4.5焊前准备
9.4.5.1焊前应将坡口表面及其边缘内、外侧20mm范围内的油漆、锈、垢等杂物清除干净。
焊丝表面亦应进行清理。
9.4.5.2定位焊前是应仔细检查坡口角度,钝边厚度、组对间隙、错边量等是否合乎要求,禁止强力组对。
9.4.5.3定位焊应采取与正式焊相同的工艺。
定位焊长度为10-15mm,间距不大
于150mm。
9.4.5.4预热可按《焊接工艺评定》规定进行,但当环境温度低于0℃时,不锈钢低于5℃时,所有管子均应适当进行焊前预热,预热温度以80℃左右为宜。
9.4.5.5合金钢法兰与碳钢管或管件组对施焊前均应预热,预热温度100℃~150℃左右。
9.4.5.6加热可采用电加热,石油液化气或其它燃油喷灯。
预热范围为焊缝两侧各不小于75mm内,应保证焊件温度均匀、稳定。
9.4.6焊接工艺要求
9.4.6.1焊接应严格按焊接工艺指导书进行。
9.4.6.2焊接中应确保起弧及收弧处的质量,收弧时应将弧坑填满,多层焊的层间接头应相互错开。
9.4.6.3不锈钢管焊接时,应在焊口两侧各50mm范围内涂上防护膏,白垩粉或石灰粉,以防止熔合性飞溅损伤管子表面。
9.4.6.4焊接完毕后,应及时将焊缝表面的熔渣及附近的飞溅物清理干净。
9.4.6.5对于大口径的管子焊口宜采取双人对称焊接,以减少变形。
9.4.6.6大口径管子(24″以上)的焊接可采用手工电弧焊打底盖面,并从内面进行封底焊,但其固定焊口仍应氩弧焊打底,手工电弧焊盖面。
封底焊后应将焊渣、药皮、飞溅处理干净,办理管线清理记录。
9.4.6.7焊前预热和焊后热处理
9.4.6.7.1对于高压过热蒸汽管道焊口,由于其管道介质温度高,压力大,且管道材质均为20G钢,因此应进行焊前预热和焊后后热,预热温度150℃左右,后热温度150-200℃,测温用测温笔监测,加热用液化石油气进行。
9.4.7.2在进行水平管道加热时,焊口两侧各500mm处应垫以支撑,以免在长时间的高温操作下管道发生变形。
当进行垂直管道焊口热处理时,先在焊口下部上好管卡,然后用倒链或其它工具拉起,以免升温后管道负荷使焊口变形。
9.4.7.3对焊接阀门的焊口进行加热时,应使阀门处于开启状态。
阀门焊口可用火焰加热的方法进行热处理,但恒温时间应适当缩短。
9.4.7.4法兰焊口加热时,缠绕式垫片和金属环型垫片应取下,阀门应尽量拆
下,以免过热损坏。
9.4.7.5焊口加热应作好测温和温度控制工作,并作好记录。
9.4.7.6焊口加热工作必须与管道施工密切配合,对已处理过的焊口要及时进行明确的标记,防止遗漏和重复处理。
9.4.8冬雨季焊接技术
A、统筹安排施焊作业计划,遵循先高层后低层,先室外后室内的原则,尽量减少冬季施焊面。
B、碳素钢、低合金钢、耐热钢、不锈钢、低温钢冬季焊接的环境温度及予热要求见下表:
材质
工件厚度(mm)
环境温度()
预热温度(℃)
环境温度要求
碳素钢
<16
-20以下
100~200
不低于-20℃
16-30
-10~-20
100~200
>30
0~-20
150~200
低合金钢
<16
-5~-10
150~200
不应低于-10℃
16~24
0~-10
150~200
耐热钢
<24
0~-10
250~400
不应低于-10℃
不锈钢
>16
0~-5
80~100
不应低于-5℃
低温钢
<24
0~-5
100~150
不应低于-5℃
C、当环境温度低于上表规定而施焊时,必须搭设活动小棚,棚内采用加热措施,以提高环境温度,焊接电流提高10%。
D、每道焊缝应一气呵成,以确保焊接的层间温度。
E、对无预热要求的钢材,在低于0℃焊接时,在始焊的100mm范围内加热到50℃以上,再开始焊接。
F、焊接时应避风、雨、雪的影响,相对湿度不高于90%。
必要时应搭设小棚,以防直接影响。
9.5焊接检验
9.5.1外观检查
9.5.1.1焊缝成型美观,焊波均匀,外形尺寸符合设计要求。
无裂纹、未溶合、
气孔、溶合性飞油、烧穿、未焊透,焊边缘与母材圆滑过渡,咬边应符合规范要求。
9.5.1.2外观检查结果应记入质量控制表,并由质检员、甲方确认。
9.5.1.3典型焊缝缺陷见下图(图9-5-1)
(b)相邻焊道间欠熔合
焊道与基底金属之间欠熔合
(a)侧壁欠熔合
仅一侧底部未填满
(c)因内部未对准而渗透不全
底部未填满
(d)焊口渗透不全
外切
根部焊缝熔合到两边内表面但根心稍低于管子内表面(渗透不全)
(a)凹根表面(上吸)
内切
(c)切口
图9-5-1典型的焊缝缺陷
9.5.2无损检测
9.5.2.1本装置无损检验方法和验收标准按GB3323-87执行。
9.5.2.2无损检测的比例遵照设计文件要求执行。
9.5.2.3无损检验时间要求
射线探伤、超声波伤应在焊后24小时后进行,着色渗透及磁粉探伤应在焊后48小时进行。
9.5.2.4当抽样检查未发现需返修的焊缝缺陷时,则抽样检验所代表的一批焊缝应认为全部合格;当抽样检查发现需要返修的焊缝缺陷时,除返修该焊缝外,还应用原规定办法进一步检验。
a、每出现一道不合格焊缝应再检验两道该焊工所焊的同一时间同一批焊缝,如果这两道合格,则应认为检验所代表的这一批焊缝合格。
b、如果这两道焊缝又出现不合格,每道不合格焊缝应现再检查该焊工同期同批焊缝两道,当再次检验的焊缝均合格时,则可认为检验所代表的一批焊缝合格。
c、当再次检验又出现不合格时,应对该焊工同期同批焊缝进行全部检验,该焊工需重新考试合格后上岗。
注:
同期同批焊缝指一个阶段内同一条线的焊缝。
9.5.2.5不合格焊缝应进行质量分析,采取措施及时返修并重新探伤。
同一焊缝返修次数不得超过两次。
9.5.3焊口返修
9.5.3.1表面缺陷返修
9.5.3.1.1表面缺陷可用打磨方法消除。
9.5.3.1.2打磨消除缺陷后,如需补焊,应将沟槽打磨成适于焊接的形状,两端斜度不少于1/3,补焊层数不少于两道,补焊长度不少于50mm。
9.5.3.1.3表面缺陷修复后应进行表面打磨,并进行磁粉探伤或着色探伤。
9.5.3.2内部缺陷的修复
9.5.3.2.1根据返修通知单,确定缺陷