GG50 气缸盖工艺及夹具设计 毕业设计说明书.docx
《GG50 气缸盖工艺及夹具设计 毕业设计说明书.docx》由会员分享,可在线阅读,更多相关《GG50 气缸盖工艺及夹具设计 毕业设计说明书.docx(78页珍藏版)》请在冰豆网上搜索。
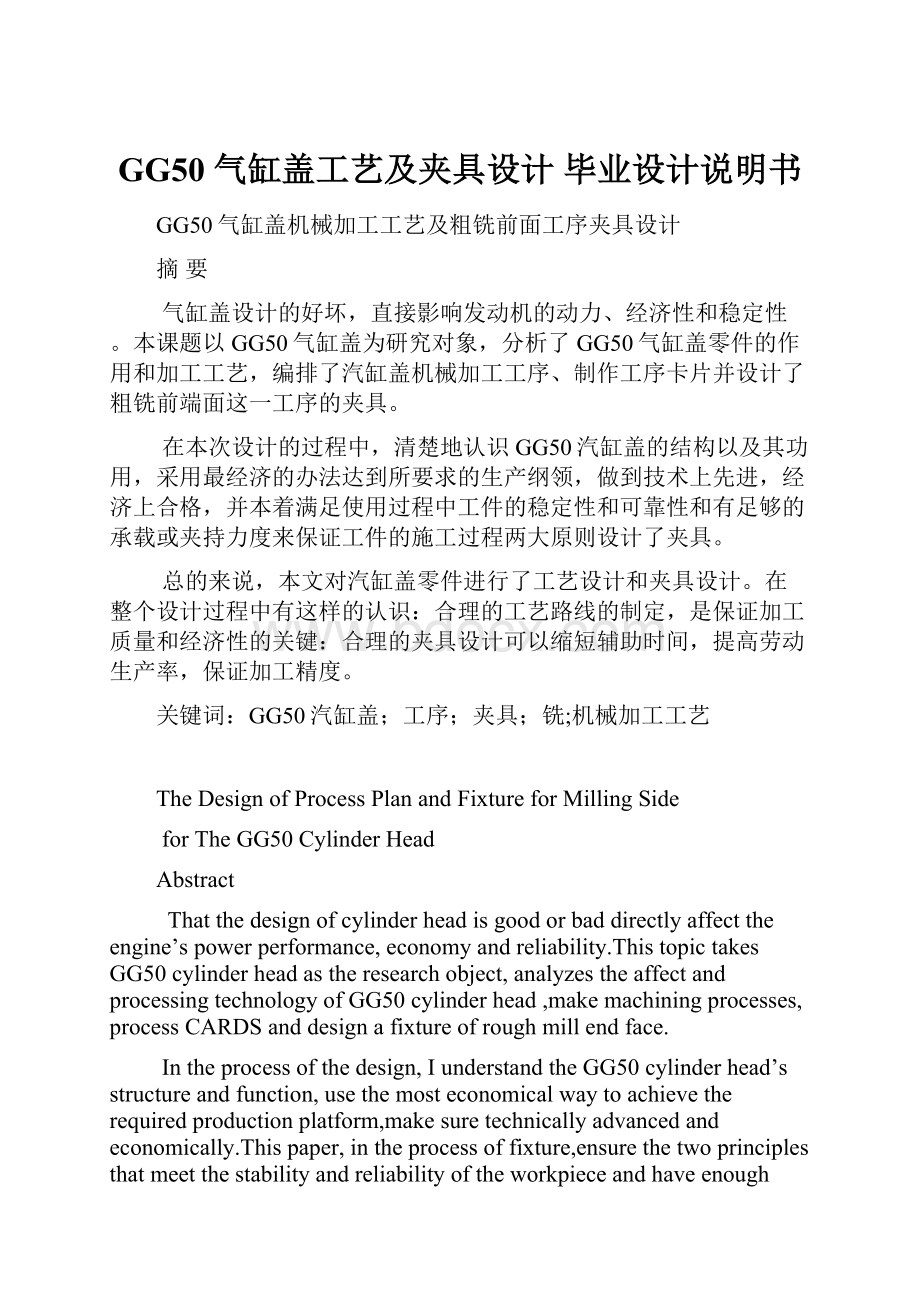
GG50气缸盖工艺及夹具设计毕业设计说明书
GG50气缸盖机械加工工艺及粗铣前面工序夹具设计
摘要
气缸盖设计的好坏,直接影响发动机的动力、经济性和稳定性。
本课题以GG50气缸盖为研究对象,分析了GG50气缸盖零件的作用和加工工艺,编排了汽缸盖机械加工工序、制作工序卡片并设计了粗铣前端面这一工序的夹具。
在本次设计的过程中,清楚地认识GG50汽缸盖的结构以及其功用,采用最经济的办法达到所要求的生产纲领,做到技术上先进,经济上合格,并本着满足使用过程中工件的稳定性和可靠性和有足够的承载或夹持力度来保证工件的施工过程两大原则设计了夹具。
总的来说,本文对汽缸盖零件进行了工艺设计和夹具设计。
在整个设计过程中有这样的认识:
合理的工艺路线的制定,是保证加工质量和经济性的关键:
合理的夹具设计可以缩短辅助时间,提高劳动生产率,保证加工精度。
关键词:
GG50汽缸盖;工序;夹具;铣;机械加工工艺
TheDesignofProcessPlanandFixtureforMillingSide
forTheGG50CylinderHead
Abstract
Thatthedesignofcylinderheadisgoodorbaddirectlyaffecttheengine’spowerperformance,economyandreliability.ThistopictakesGG50cylinderheadastheresearchobject,analyzestheaffectandprocessingtechnologyofGG50cylinderhead,makemachiningprocesses,processCARDSanddesignafixtureofroughmillendface.
Intheprocessofthedesign,IunderstandtheGG50cylinderhead’sstructureandfunction,usethemosteconomicalwaytoachievetherequiredproductionplatform,makesuretechnicallyadvancedandeconomically.Thispaper,intheprocessoffixture,ensurethetwoprinciplesthatmeetthestabilityandreliabilityoftheworkpieceandhaveenoughcarryingorholdingtoensuretheconstructionprocessofworkpiecetodesign.
Ingeneral,thispaperdesigntheprocessplanandfixtureofcylindercover.Throughoutthedesignprocesstohavesuchunderstanding:
theestablishmentofreasonabletechnologyrouteisthekeytoensuremachiningqualityandefficiency,reasonablefixturedesigncanshortentheauxiliarytime,improvelaborproductivity,ensurethemachiningaccuracy.
Keywords:
GG17Cylinder-head;process;fixturedesign;milling;Mechanicalprocessingtechnology
插图清单
表格清单
引言
机械加工工艺和机床的夹具设计以及夹具的制造技术已经是生产、国际竞争、产品革新的一种重要手段,所有国家都在寻求、获得、开发和利用它。
它正被看做是现在国家经济上获得成功的重要因素。
气缸盖是发动起最复杂最重要的零件之一,气缸盖设计的好坏,直接影响发动机的质量。
传统的机械制造业在新时代的背景下已经不能满足时代的要求,因此机械制造业要在吸收新成果的基础之上成为一个新兴技术行业,实现机械制造业地环保化,节能化,经济化的目标。
我国自从改革开放以来机械制造工业取得了很大的发展,已近成为工业产品门类比较齐全、具有相当规模和一定技术基础的产业部门之一。
但是与国外的机械制造行业相比,我国机械制造工业存在资源利用率低,环境污染高,自主创新能力差等特点。
虽然夹具的设计也有较大的发展,但是与工业发达国家相比,我们在这方面的水平还存在着阶段性的差距,主要表现在机械产品和水平不够高,加工工艺不合理,夹具的应用比较少,使其加工工人的劳动强度大,加工的产品不理想。
这些问题对机械制造工业的长远发展不利,因此我国要实现机械工业的现代化必须要加大机械制造行业的资金和技术投入比例,实现我国机械制造工业的成功转型。
目前我国机械制造处于高速发展阶段,一些先进的机械制造工业已经应用于机械制造行业。
但是由于我国机械技术水平相对来说较地,在机械制造工业方面没有充分的经验,因此,我国的机械制造工业与发达国家存在着很大的差距,主要表现在计算机管理水平低,管理方法落后,仍处于机械加工工艺的研发和单自动化阶段。
随着科学技术的不断进步,夹具已从一种辅助工具发展成为门类齐全的工艺装备。
现代生产要求企业所制造的产品品种经常的更新换代,以适应市场的需求和竞争,然而一般的企业都仍习惯于大量的采用传统的专用夹具,一般在具有中等生产能力的工厂里拥有上千甚至近万套夹具;另一方面,在多品种生产的企业中,每隔3-5年就要更新50-80%左右的专用夹具,而夹具的实际磨损仅为10-20%左右。
本文以GG50汽缸盖为研究对象,分析了其加工工艺并对粗铣前端面这一工序进行夹具设计,保证了加工质量和经济性,尽可能地缩短辅助时间,提高了劳动生产率并且降低对工人的技术要求。
第1章绪论
1.1本课题的研究意义
本课题研究的是GG50气缸盖机械加工工艺及指定工序夹具设计。
机械加工工艺就是在流程的基础上,改变生产对象的形状、尺寸、相对位置和性质等,使其成为成品或半成品,是每个步骤,每个流程的详细说明。
编制汽缸盖加工工艺规程,用以指导汽缸盖的实际加工生产,达到提高生产效率、获得较好的经济效益和较高的产品质量的目标。
夹具是在机械制造过程中用来固定加工对象,使之占有正确的位置,以接受施工或检测的装置。
在工艺过程中的任何工序,都用来迅速、方便、安全地安装工件的装置。
夹具的好坏直接影响工件加工表面的位置精度,所以机床夹具是装备设计中的一项重要工作,关系到生产效率和产品质量的提高。
1.2本课题的研究现状
目前,缸盖加工工艺已在我国得到了应用与推广,主要在汽车发动机,航天航空,武器制造,机械工程,仪器仪表等等。
但是从目前我国的情况来看,缸盖加工工艺主要在汽车制造业和飞机制造业中应用较为广泛,但是也只是停留在初步应用阶段,在其他行业应用较少,主要是在专业研究机构和高校研究机构中应用,可见我国对于缸盖加工工艺的应用领域和技术水平还很低,但是却有很大的提升空间。
现代生产要求企业所制造的产品品种经常更新换代,以适应市场的需求与竞争。
然而,一般企业都仍习惯于大量采用传统的专用夹具,一般在具有中等生产能力的工厂里,约拥有数千甚至近万套专用夹具;另一方面,在多品种生产的企业中,每隔3-4年就要更新50-80%左右的专用夹具,而夹具的实际磨损量仅为10-20%左右。
所以,老式的夹具已经不能满足生产需要了,更经济化,高效化的夹具也就慢慢的发展出来。
1.3本课题的发展趋势
机械制造工艺的发展分为三个趋势。
第一,数字化趋势,机械制造加工的发展最重要的推动者就是计算机技术的普遍应用,机械制造工艺的重要发展方向就是数字化。
数字化包括机械制造中设计环节数字化,数字化生产过程的实现和实现生产过程的数字化管理。
第二,精细化趋势,机械制造工艺的发展不可或缺的是材料进步和加工手段的提升,即加工的精密化不断提高。
在未来随着纳米技术的不断提升,机械制造工艺也将完全进入到纳米时代。
第三,集成化的发展趋势,集成化的发展是高度自动化带来的产物,即机械制造的工艺由原来的分散型逐渐加工,转化为完整的集成化、连续性加工和生产。
现在的集成主要是设备、技术的集成,即利用机电一体化、工艺连续性来一次性完成某个部件的生产,而未来的集成化将是整个成品的集成化生产,那是将使设计、生产、装配、成品检验、出厂的全过程在一个自动化系统内完成。
现代夹具的发展方向主要表现为标准化、精密化、高效化和柔性化四个方面。
夹具在机械加工生产过程中起着重大的作用,夹具的发展是为了满足当代机械加工工艺的需要,可以说是社会的发展、生产的需要带动着夹具的发展,其发展过程是必然的。
第2章零件分析
2.1生产纲领要求
年产8000台,单班制。
属于大批量生产,适合用工序集中生产。
2.2汽缸盖的工艺分析
2.2.1汽缸盖的材料
由零件图技术要求,GG50气缸盖的材料为ZL101(铝合金),根据铝合金的特点,我们在设计工艺过程和选定切削参数的时应有所注意。
2.2.2缸盖毛坯的要求
对于缸盖毛坯的技术要求是:
毛坯应采用重力铸造或低压浇铸成型,铸件内外表面不得有缩孔、毗缝、疏松等现象。
2.2.3确定待加工部位
上平面的待加工部位:
粗铣上平面、钻9×Φ13通孔、钻Φ10深70通孔、钻Φ10深88通孔、钻3×Φ18通孔、钻8×Φ5深18通孔、钻2×Φ12.5通孔、钻扩铰2×Φ15深16孔、钻2×Φ14通孔、钻扩铰Φ15深16.3孔、钻Φ13孔、铣槽、钻扩铰Φ20深23.8孔、加工SR12.5球面、钻扩铰Φ25深23孔、钻扩铰Φ32孔、锪Φ32至顶面4、铣槽、钻扩铰10×Φ12深60.7孔、成形车刀加工、镗5×Φ27.3孔、镗5×Φ30.8孔、镗5×Φ33孔、镗5×Φ37孔。
下平面的待加工部位:
粗铣下平面、钻扩铰Φ14、锪Φ24至顶面3、钻扩铰8×Φ8.5深7.3孔,攻丝8×M8-6H、粗精镗3×Φ302×Φ47Φ32、镗10×Φ33距顶面60.7、粗精镗10×Φ35。
前平面的待加工部位:
粗铣前端面、攻丝19×M8-6H深14.5、攻丝M6-6H深12、钻扩铰2×Φ12深12孔。
后端面的待加工部位:
粗铣后端面、钻Φ10深9孔、钻2×Φ5深18孔、钻5×Φ6.75深20孔、攻丝2×M6-6H深14、攻丝5×M8-6H深16、钻Φ7.9孔、钻Φ10.7深14孔、攻丝5×M12×1.25-6H攻深11、镗Φ32孔。
左端面的待加工部位:
粗铣左端面、钻Φ4通孔、钻Φ5深17孔、钻Φ6.75深19孔、钻Φ8.5通孔、钻孔铰Φ24深10孔、攻丝M6-6H深10、攻丝M8-6H深16孔、攻丝NPT1/8-27。
右端面的待的加工部位:
粗铣右端面、钻Φ6.75深19孔、钻Φ6.75深22孔、钻Φ9深19孔、攻丝2×M8-6H深16、攻丝M10×1-6H深15、钻扩铰Φ24、锪Φ28深3.5、钻Φ10.3深19、攻丝ZM12深15、锪Φ12.8距顶面2.5。
钻斜孔:
钻5×Φ13孔、钻5×Φ20.7、钻5×Φ22、攻丝5×M24×2-6H深16,钻5×Φ28、钻扩铰Φ20.7、钻Φ4.5、钻扩铰Φ5.4、钻4×Φ4.3、钻4×Φ5深27、钻扩铰Φ16
第3章确定GG50汽缸盖机械加工工艺
3.1确定毛坯的制造形式
气缸盖的材料是铝合金,考虑到在汽车中的受力情况,所以毛坯采用铸造的形式。
3.2制定工艺规程的原则
汽缸盖属于箱体类零件,所以应遵守箱体类加工原则。
加工顺序为先面后孔,箱体类零件的加工顺序为先加工面,已加工好的平面定位,再来加工孔。
因为箱体孔精度要求高,加工难度大先以孔基准加工好平面,再以平面为精基准加工孔,这样既能为孔的加工提供稳定可靠的精基准,同时可以使孔的加工余量均匀。
工序间安排时效处理箱体毛坯比较复杂,铸造内应力较大。
为了消除内应力减小变形,保证精度的稳定铸造之后要安排人工时效处理(加热500~550℃,加热速度50~120℃/h,保温4~6h,冷却速度≤30℃/h,出炉温度≤200℃)。
箱体人工时效的方法,除了加工保温方法外,也可采用振动时效来达到消除残余应力的目的。
3.3基准的选择
在设计工序基准时,首先考虑用设计基准作为工序基准,其次所选工序基准应尽可能用于工件的定位和工序尺寸的检验,但当采用设计基准为工序基准有困难时,可另选工序基准,但必须可靠地保证零件的设计尺寸和技术要求。
正确选择定位基准是制订机械加工工艺规程和进行夹具设计的关键。
定基准分为精基准和粗基准。
在起始工序中,只能选用未经加上过的毛坯表面作为定位基准,这种基准称为粗基准。
用加工过的表面所作的定位基准称为精基准。
在设计工艺规程的过程中,当根据零件工作图先选择精基准、后选粗基准。
结合整个工艺过程要进行统一考虑,先行工序要为后续工序创造条件。
对于汽缸盖的加工基准选择应遵循如下原则:
基准重合原则、基准统一原则、自为基准原则、互为基准原则、便于装夹的原则等。
3.4确定机械加工工艺
方案一
10.铸造毛坯
20.热处理
30.粗铣下端面
40.粗精铣上端面
50.钻上端面上所有的通孔及粗加工上端面所有阶梯孔
60.粗镗排气孔中Φ27.3Φ33Φ37Φ30.8Φ37Φ41钻Φ11孔
70.精铣下端面
80.粗加工下端面所有阶梯孔、打螺纹底孔以及粗镗底面孔
90.粗铣前端面
100.钻前端面螺纹底孔并钻Φ11孔
110粗铣后端面
120.钻M8-6HM6-6HM12x1.25-6H螺纹底孔以及Φ32和Φ10孔
130.粗铣左侧面
140.钻Φ4孔,钻Φ22孔,加工M6-6HM8-6HNPT1/8-27螺纹底孔
150.粗铣右端面
160.钻M8-6HM10x1-6H螺纹底孔,粗加工O-ON-N阶梯孔
170.钻扩铰上端面所有阶梯孔
180.精镗排气孔中Φ27.3Φ33Φ37Φ30.8Φ37Φ41扩铰Φ11孔至Φ12
190.精加工下端面所有阶梯孔
200.攻下端面所有螺纹
210.精镗底面孔
220.攻前端面所有螺纹孔
230.攻后端面所有螺纹孔
240.加工Φ24孔
250.攻丝M6-6HM8-6HNPT1/8-27螺纹
260.攻丝M8-6HM10x1-6H螺纹
270.钻扩铰加工O-ON-N阶梯孔
280.钻扩铰斜孔
290.清洗
300.检查入库
方案二
10.铸造毛坯
20.热处理
30.粗铣下端面
40.粗、精铣上端面并钻、扩、铰上端面所有的通孔,加工A-A阶梯孔,钻、扩、铰Φ15深16.3孔,加工C-C阶梯孔、倒角、铣槽,钻、扩、铰Φ20深23.8孔,加工E-E阶梯孔、用成形车道加工Φ25球面并铣槽,钻扩铰Φ12孔
50.粗精镗排气孔中Φ27.3Φ33Φ37Φ30.8Φ37Φ41
60.精铣下端面并加工F-F阶梯孔,加工M8-6H螺纹孔,钻扩铰Φ8.5孔
70.粗铣、半精铣凸轮轴孔
80.镗Φ33孔,粗精镗Φ35孔
90.粗铣前端面、加工前端面M8-6H及M6-6H,钻扩铰Φ12孔并倒角
100.粗铣后端面,加工M8-6HM6-6HM12x1.25-6H螺纹以及Φ32和Φ10孔
110.粗铣左侧面,钻Φ4孔,钻扩铰Φ24孔,加工M6-6HM8-6HNPT1/8-27螺纹
120.粗精铣右端面,加工M8-6HM10x1-6H螺纹加工O-ON-N阶梯孔
130.钻斜孔
140.精铣凸轮轴孔
150.清洗
160.检查入库
方案一再选择设备时选择了组合机床,而方案二几乎所有机床均选用加工中心加工。
由于气缸盖的结构及其复杂,选择加工中心能使工序集中,加快加工效率,故更加合理。
方案一很好地遵循了保证相互位置要求的原则、保证加工表面加工余量合理分配的原则、粗基准不重复使用的原则和便于工件装夹的原则等。
所以选择方案二。
第4章确定切削用量及工时
4.1概述
在粗加工是要尽可能达到较高的金属切除率,同时又要保证必要的刀具耐用度,在背吃刀量的选择上,应根据工件的加工余量确定,粗加工时,除留下必要的精加工余量外,应尽量使余量能一次或少数几次切除完。
在进给量的选择上,要根据机床、工件、刀具的具体条件和断屑情况选择,机床、工件和刀具刚性好的可选性大些;反之,则选小些。
切削速度就根据T度的要求,针对不同刀具材料和工件材料选用合适的Vc。
精加工时首先应保证获得必要的加工精度和表面质量,同时又要考虑得到必要的刀具耐用度和生产率。
背吃刀量的选择就根据粗加工留下的余量确定,在进给量的选择上,为降低表面粗糙度,应采用较小的f。
切削速度可以在保证合理的刀具耐用T的情况下合理选择。
4.2各工序切削参数及工时的确定
工序10.铸造毛坯
工序20.热处理
工序30.粗铣下端面
机床:
卧式铣床
刀具:
硬质合金端铣刀(面铣刀)d0=400mm齿数Z=20ae=240mm
每齿进给量af:
由文献[8]知,取af=0.25mm/z
铣削速度V:
由文献[8]知,取V=80m/min
机床主轴转速n:
n=1000v/лd0=64r/min
走刀量f:
f=af×z=0.25×20=5mm/r
进给量Vf=f×n0=af×z×n=0.25×20×60=300mm/min
工作台每分钟进给量fm:
fm=Vf=300mm/min
被切削长度l:
由毛坯尺寸可知l=518mm
刀具切入长度l1:
l1=0.5[D-(D2-a2e)1/2]+(1~3)=42mm
刀具切出长度l2:
l2=1~3mm,取l2=2mm
走刀次数为5次
机动时间t1=(l+l1+l2)/fm=1.87min
工序40.粗、精铣上端面并钻、扩、铰上端面所有的通孔,加工A-A阶梯孔,钻、扩、铰50深16.3孔,加工C-C阶梯孔、倒角、铣槽,钻、扩、铰Φ20深23.8孔,加工E-E阶梯孔、用成形车道加工Φ25球面并铣槽,钻扩铰Φ12孔
(1)粗铣上端面
每齿进给量af:
由文献[8]知,取af=0.25mm/z
铣削速度V:
由文献[8]知,取V=80m/min
机床主轴转速n:
n=1000v/лd0=64r/min
走刀量f:
f=af×z=0.25×20=5mm/r
进给量Vf=f×n0=af×z×n=0.25×20×60=300mm/min
工作台每分钟进给量fm:
fm=Vf=300mm/min
被切削长度l:
由毛坯尺寸可知l=518mm
刀具切入长度l1:
l1=0.5[D-(D2-a2e)1/2]+(1~3)=42mm
刀具切出长度l2:
l2=1~3mm,取l2=2mm
走刀次数为1次
机动时间t1=(l+l1+l2)/fm=1.87min
(2)精铣上端面
铣削深度ap=0.5mm
每齿进给量af=0.20mm/z
铣削速度V=120m/min(由文献[8]知)
机床主轴转速n=1000v/лd0=95.5r/min
走刀量f=af×z=0.20×20=4mm/r
进给量Vf=f×n0=af×z×n=0.2×20×95.5=382mm/min
被切削长度l:
由毛坯尺寸可知l=518mm
刀具切入长度l1:
l1=0.5[D-(D2-a2e)1/2]+(1~3)=42mm
刀具切出长度l2:
l2=1~3mm,取l2=2mm
走刀次数为1次
机动时间t1=(l+l1+l2)/fm=1.47min
(3)钻9个Φ13孔
机床:
加工中心
刀具:
高速钢麻花钻
切削深度ap=6.5mm
钻削速度V=28m/min(由文献[8]知)
机床主轴转速n=1000v/лd0=857r/min
进给量f:
由文献[8]知f=0.18mm/r
进给速度fm=fn=857×0.18=154.3mm/min
被切削长度l:
由毛坯尺寸可知l=65mm
刀具切入长度l1:
l1=(D×ctgkr)/2+(1~2)=4.5mm
刀具切出长度l2:
l2=0mm
走刀次数为1次
机动时间t1=(l+l1+l2)/fm=0.45min
(四)钻Φ10深70孔
切削深度ap=5mm
钻削速度V=22m/min(由文献[8]知)
机床主轴转速n=1000v/лd0=700r/min
进给量f:
由文献[8]知f=0.14mm/r
进给速度fm=fn=700×0.14=98mm/min
被切削长度l:
由毛坯尺寸可知l=70mm
刀具切入长度l1:
l1=(D×ctgkr)/2+(1~2)=5mm
刀具切出长度l2:
l2=0mm
走刀次数为1次
机动时间t1=(l+l1+l2)/fm=0.76min
(五)钻Φ10深88孔
切削深度ap=5mm
钻削速度V=22m/min(由文献[8]知)
机床主轴转速n=1000v/лd0=700r/min
进给量f:
由文献[8]知f=0.14mm/r
进给速度fm=fn=700×0.14=98mm/min
被切削长度l:
由毛坯尺寸可知l=88mm
刀具切入长度l1:
l1=(D×ctgkr)/2+(1~2)=5mm
刀具切出长度l2:
l2=0mm
走刀次数为1次
机动时间t1=(l+l1+l2)/fm=0.95min
(6)钻3个Φ18孔
切削深度ap=9mm
钻削速度V=32m/min(由文献[8]知)
机床主轴转速n=1000v/лd0=566r/min
进给量f:
由文献[8]知f=0.20mm/r
进给速度fm=fn=566×0.20=113.2mm/min
被切削长度l:
由毛坯尺寸可知l=86mm
刀具切入长度l1:
l1=(D×ctgkr)/2+(1~2)=5.3mm
刀具切出长度l2:
l2=0mm
走刀次数为1次
机动时间t1=(l+l1+l2)/fm=0.81min
(7)钻8个Φ5孔
切削深度ap=2.5mm
钻削速度V=20m/min(由文献[8]知)
机床主轴转速n=1000v/лd0=1274r/min
进给量f:
由文献[8]知f=0.12mm/r
进给速度fm=fn=1274×0.12=152.9mm/min
被切削长度l:
由毛坯尺寸可知l=18mm
刀具切入长度l1:
l1=(D×ctgkr)/2+(1~2)=3.5mm
刀具切出长度l2:
l2=0mm
走刀次数为1次
机动时间t1=(l+l1+l2)/fm=0.14min
(八)钻2个Φ12.5孔
切削深度ap=6.25mm
钻削速度V=28m/min(由文献[8]知)
机床主轴转速n=1000v/лd0=713.4r/min
进给量f:
由文献[8]知f=0.18mm/r
进给速度fm=fn=713.4×0.18=128.4mm/min
被切削长度l:
由毛坯尺寸可知l=58mm
刀具切入长度l1:
l1=(D×ctgkr)/2+(1~2)=4.3mm
刀具切出长度l2:
l2=0mm
走刀次数为1次
机动时间t1=(l+l1+l2)/fm=0.49min
(八)钻2个Φ14通孔
切削深度ap