燕山石化生产实习报告.docx
《燕山石化生产实习报告.docx》由会员分享,可在线阅读,更多相关《燕山石化生产实习报告.docx(25页珍藏版)》请在冰豆网上搜索。
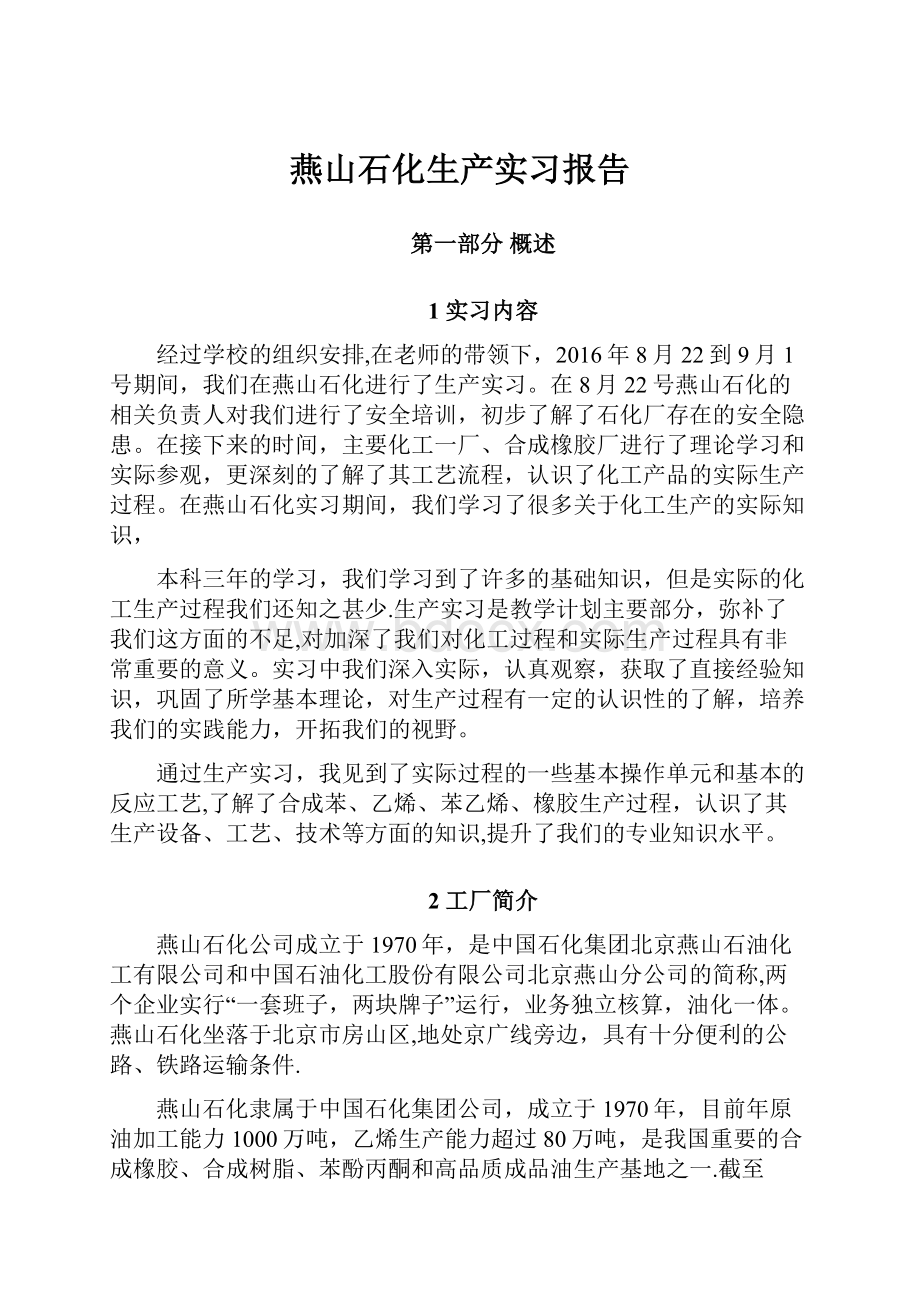
燕山石化生产实习报告
第一部分概述
1实习内容
经过学校的组织安排,在老师的带领下,2016年8月22到9月1号期间,我们在燕山石化进行了生产实习。
在8月22号燕山石化的相关负责人对我们进行了安全培训,初步了解了石化厂存在的安全隐患。
在接下来的时间,主要化工一厂、合成橡胶厂进行了理论学习和实际参观,更深刻的了解了其工艺流程,认识了化工产品的实际生产过程。
在燕山石化实习期间,我们学习了很多关于化工生产的实际知识,
本科三年的学习,我们学习到了许多的基础知识,但是实际的化工生产过程我们还知之甚少.生产实习是教学计划主要部分,弥补了我们这方面的不足,对加深了我们对化工过程和实际生产过程具有非常重要的意义。
实习中我们深入实际,认真观察,获取了直接经验知识,巩固了所学基本理论,对生产过程有一定的认识性的了解,培养我们的实践能力,开拓我们的视野。
通过生产实习,我见到了实际过程的一些基本操作单元和基本的反应工艺,了解了合成苯、乙烯、苯乙烯、橡胶生产过程,认识了其生产设备、工艺、技术等方面的知识,提升了我们的专业知识水平。
2工厂简介
燕山石化公司成立于1970年,是中国石化集团北京燕山石油化工有限公司和中国石油化工股份有限公司北京燕山分公司的简称,两个企业实行“一套班子,两块牌子”运行,业务独立核算,油化一体。
燕山石化坐落于北京市房山区,地处京广线旁边,具有十分便利的公路、铁路运输条件.
燕山石化隶属于中国石化集团公司,成立于1970年,目前年原油加工能力1000万吨,乙烯生产能力超过80万吨,是我国重要的合成橡胶、合成树脂、苯酚丙酮和高品质成品油生产基地之一.截至2015年底,燕山石化累计加工原油3。
13亿吨,生产乙烯2034。
7万吨,累计实现销售收入11103.39亿元,上缴利税1278亿元,为我国石化工业发展和首都经济社会建设做出了重要贡献。
作为地处首都的石化企业,燕山石化一直致力于提供清洁能源,1997年率先实现了汽油无铅化;2007年完成1000万吨炼油系统改造,油品质量升级到欧IV标准,兑现了中国政府向国际奥委会的郑重承诺;2012年,燕山石化成为我国第一家生产京标V标准(相当于欧V标准,后统一为“国V标准")清洁油品的千万吨级炼油基地。
新世纪以来,燕山石化保持了持续健康发展的良好局面,先后荣获全国五一劳动奖状、中央企业先进基层党组织、全国企业文化示范基地、全国“安康杯"示范企业、中华环境友好企业、中国节能减排功勋企业、国家职业卫生示范企业、“中华宝钢环境奖"等荣誉称号。
第二部分71万吨/年乙烯生产装置
1车间概况
1.1车间概况
1973年8月29日,装置动工建设,1976年5月8日开车成功,生产出合格的乙烯。
装置一轻柴油为原料,经过裂解、急冷、压缩、分离等工艺过程,生产出高纯度的乙烯、丙烯、氢气、液化气、碳四、碳五裂解汽油、裂解燃料油等副产品,为下游生产装置提供原料。
为了进一步提高装置的生产能力,降低成本,提高经济效益,将30万吨/年的乙烯装置进行大规模的技术改造与建设,生产能力扩大到45万吨/年.设计负责人依然是美国和日本的两个公司,与1994年9月22日试车成功。
1999年3月18日进行第二次改造,2001年9月26日试车成功,达到了71万吨每年的产量,实产76万吨/年,而且生产的产品也逐渐变得多样.
1。
2原料与能耗
(1)主要原料
裂解炉的原料主要包括石脑油、中柴油、尾油、烃(乙烷、丙烷).原料经过预热系统.分子量大的时候就降低预热温度,分子量较小的话,就升高预热温度。
进入裂解炉裂解出口温度科大800℃.
(2)能耗水平
由于采用的是高温裂解,所以主要能耗集中在反应装置上,高温裂解的反应装置是SRT-IV型炉,该装置也是有鲁姆斯公司(LUMMUS)设计的。
动力消耗有蒸汽、锅炉给水、循环冷却水、电、仪表风、杂用风和氮气。
其中高压蒸汽:
压力11.28MPa,温度520℃;中压蒸汽:
新区压力1。
6MPa,温度290℃,老区压力1.6MPa,温度300℃;低压蒸汽压力0.3MPa,温度197℃。
1。
3产品
燕化乙烯装置主要以炼厂来的加氢尾油(HVGO)、重柴油(HGO)和石脑油(NAP)为原料,经过高温蒸汽裂解、急冷、压缩、分离等工艺过程,生产出高纯度的乙烯、丙烯产品和氢气、液化气、碳四、碳五、裂解汽油、裂解轻柴油、裂解燃料油等副产品,为下游的聚乙烯、聚丙烯、丁二烯装置、芳烃装置等提供原料。
因此,乙烯装置处于石油化工装置生产链的核心位置.
2生产工艺、运行与维护
2.1工艺流程说明
2.2主要工艺指标与技术先进性
工艺流程总图格局呈“两头一尾”。
采用管式炉蒸汽裂解、顺序分离流程。
装置全部采用DCS控制,压缩机采用电子调速控制,全装置实现APC先进改造的裂解炉采用KT16万吨/年的CK—V型裂解炉,新建裂解炉为中石化和其合作开发的10万吨裂解炉(SL—I型)。
在世界乙烯工业中首次采用了二元制冷技术和催化精馏脱除MAPD技术。
在裂解气压缩机上采用了注水工艺,在制冷压缩机上采用了干气密封技术。
2.3运行与控制
全场信息化应用系统中应用到了APC控制,APC控制系统是由ASPEN公司出品的一种控制系统。
APC控制系统根据原料不同提供最优断裂条件,直接写入DMC控制系统。
本装置采用DMCplus多变量预估计控制技术为主的先进控制,并使用符合线性规划CLP进行最大化优化.
该现场控制系统与Technip的裂解炉深度计算软件SPYRO线连接,SPYRO实时计算裂解深度作为裂解炉DMCplus控制系统的输入。
下面是裂解炉的控制结构图和SPYROforAPC结构图.
2。
4维护与检修
化工一厂的装置每四年维护检修一次,一次历时一个月左右。
主要检修阀门的泄漏,装置中残留的物质等,以降低在生产过程中发生故障和事故的可能。
乙烯高温裂解装置的维护和检修。
高温裂解炉在正常情况下,可以保证连续工作130天,长时间工作后,会在反应炉内结垢,其主要原因是:
柴油和石脑油等在高温条件下反应可能会产生焦炭或碳的氧化物与管壁的金属材料中的镍或其他金属材料形成结合台的金属盐.清灰的方式是,进一步将结构烧成灰,然后将灰尘吹出,用水清洗管内。
3主要设备原理与参数
3。
1主要化学反应设备
SRT-IV裂解炉
管式裂解炉是当今乙烯生产中占主导地位的技术,它具有高温,短停留,低烃分压等特点,可以实现乙烯工业生产中的高选择性和长转运周期.管事裂解炉其特点主要有:
(1)被加热物质在管内流动,故仅限于加热气体和液体.而且,这些气体或液体通常都是易燃易爆的烃类物质,同锅炉加热水和蒸汽相比,危险性大,操作条件要苛刻得多.
(2)加热方式为直接受火式,加热温度高,传热能力大.
(3)加热气体或液体燃料。
(4)长周期连续运转,不断操作,便于管理。
SRT—IV裂解炉炉管
SRT-IV型炉管排列为8421(或8411),即第一程为8根直径为67毫米炉管,而后两两合并为4根直径为89毫米的第二程管,再两两合并成两根直径为121毫米的第第三管程炉管,最后合并成一根直径为165毫米的第四程管.炉管材质为Cr25%、Ni35%、Nb1。
4%、W1.4%。
采用离心浇筑的方法进行制造。
3。
2主要分离设备
分离设备主要是塔器设备,在该套乙烯生产装置中一共有34台塔器设备.本装置就其分离方法而言属于深冷顺序分离过程,因为采用了—100℃的冷冻系统。
利用混合气体中各种烃的相对挥发度的不同,而利用精馏法在低温下将裂解气中除了氢和甲烷意外的其它烃全部冷凝下来,同时用精馏法在适当的温度、压力下将各烃逐一加以分离,从而得到高纯的乙烯、丙烯产品。
精馏原理是根据物料中各组分的相对挥发度的不同,利用汽液相平衡原理,经过多次部分冷凝,部分气化而获得高纯度产品的过程。
分离系统主要包括一系列的精馏塔:
脱甲烷塔、脱乙烷塔、脱丙烷塔、脱丁烷塔、脱戊烷塔、乙烯精馏塔、丙烯精馏塔。
第三部分8。
4万吨/年苯乙烯生产装置
1原理
1.1烷基化反应
在一定温度压力下,乙烯和苯在酸性催化剂上进行烷基化反应生成乙苯,同时乙苯与乙烯进一步反应生成多乙苯,化学反应式如下
C6H6+C2H4C2H5C6H5
C6H6+nC2H4(C2H5)nC6H6—n
以上这些反应都是快速不可逆反应,反应器中的反应物通过催化剂上的微孔扩散至催化剂活性中心并进行反应,然后反应产物通过微孔扩散到物流中。
1.2烷基转移反应
烷基转移反应是在一定的温度压力条件下,在酸性催化剂的作用下多乙苯转化为乙苯的反应,主要反应为
C6H6+(C2H5)2C6H42C6H5C2H5
C6H6+(C2H5)3C6H3C6H5C2H5+(C2H5)2C6H4
烷基转移反应在催化剂上的催化剂活性中心反应,是可逆的二级反应.除生产苯乙烯外,还生产重质化合物,因此要尽可能的减少副产物的生产,通过维持苯过量,以提高转化率和选择性。
1。
3苯乙烯脱氢
乙苯脱氢制苯乙烯主反应:
C6H5-CH2CH3C6H5CH=CH2+H2
乙苯脱氢制苯乙烯主要副反应:
C6H5—CH=CH2C6H5C=CH+H2
即使没有催化剂的存在乙苯也能发生脱氢反应生产苯乙烯,工业上首次生产苯乙烯就是用这种方式进行的,但乙苯转化率很低(10-15%),苯乙烯选择性也只有50%左右。
.现在使用催化剂的工艺中,主要副产物是苯和甲苯,同时也会转化为较高级的复杂化合物。
副反应在600.C时还不明显,但温度高于655.C时,副反应的总收率有着不可估量的影响。
2装置构成
本装置主要有烷基化和烷基转移单元、乙苯精馏单元、脱氢反应单元、苯乙烯精馏单元和中间罐区五个单元构成。
其中烷基化和烷基转移单元包括烷基化反应器、烷基转移反应器、预分馏塔,乙苯精馏单元包括苯回收塔、乙笨精馏塔、多乙苯塔、脱非芳塔,脱氢反应包括乙笨脱氢反应器、氧化反应器、尾气压缩系统,苯乙烯精馏包括乙苯/苯乙烯分离塔、乙苯回收塔、苯乙烯精馏塔、苯/甲苯分离塔。
工艺流程大致为:
3工艺流程
3。
1烷基化与烷基转移单元
烷基化为强放热反应,这部分热量应从反应系统中除去,因此采用部分反应物循环到反应器入口,通过调节循环量,来控制催化剂床层的温度升高,同时保证乙烯在液相中完全溶解。
另外采用苯过量的方法,但大量的苯将使精馏系统内耗过大。
烷基化反应在两台串联的绝热反应器中进行,控制反应压力使反应在全液相进行.烷基化反应的进料包括乙苯精馏单元的回收苯和新鲜苯,从预分馏塔出来的苯进入第一台烷基化反应器。
来外界的乙烯经乙烯压缩机增压后,被分成相等的两部分,分别进入第一和第二台烷基化反应器的底部与苯进行烷基化反应,两台反应乙烯的转化率为100%,在第一烷基化反应器另有一部分进料来自第二反应器的出料,经循环泵增压后进入第一反应器的入口。
烷基化反应为强放热反应,因此在两台反应器之间设置出料冷却器,将第一台烷基化反应器的出料冷却到一定温度,并产生低压蒸汽,第二台烷基化反应器的出料先预热烷基转移反应器的进料,以充分利用热能,然后送到乙苯精馏工段。
烷基转化器的原料包括来自来自多乙苯塔的多乙苯,以及原料苯罐的回收苯。
混合物料在烷基转移预热器与来自烷基化反应器的产物换热后,温度升高,进入烷基转化反应器进行烷基转移反应,反应产物与烷基化反应器产物一起进入乙苯精馏单元,分离出乙苯等物质。
3。
2乙苯精馏单元
乙苯精馏单元有预分馏塔、苯塔、乙苯塔、多乙苯塔和脱非芳塔,将烷基转移反应物分离成苯、乙苯、多乙苯塔和重物质,同时除去循环苯中的轻烃组分和水.
预分馏塔用于循环回收苯,烷基化化和烷基转移反应产物中的苯大部分在预分馏塔塔顶回收,塔项蒸汽部分冷凝产0。
3lMPa蒸汽。
冷凝液一部分作为预分馏塔回流,纯苯返回到烷基化反应器.从预分馏塔侧线抽出的部分苯与苯塔回收的苯,作为烷从转移反应苯进料。
罐区区来的新鲜苯直接被送到预分馏塔项罐。
预分馏塔顶罐中未冷凝的气体直接送入脱非芳塔底部,脱非芳塔顶塔顶蒸汽用冷却水却.轻烃(不凝气体)排入火炬,水从脱非芳塔的集水格中被分离出来,冷凝液凝液大部分作为塔的回流,少量排到罐区。
预分馏塔塔底物料送到苯塔继续回收剩余的苯,苯塔项蒸汽冷凝后,部分作为回流,一部分送去烷基化反应器,侧线采出物料大部分是苯送去烷基转移反应器。
苯塔塔底物料送到乙苯塔,乙苯塔塔项蒸汽冷凝后,一部分作为回流,另一部分作为合格的乙苯产品采出,送去下一单元生产苯乙烯。
乙苯塔塔底釜液进一步送到多乙苯塔,从塔顶回收多乙苯。
多乙苯塔为减压塔,塔顶蒸汽用冷却水冷凝,凝液一部分回流到塔顶,另一部分送去烷基化反应器,进行烷基转移反应。
塔底产物多为高沸点的残油,经冷却后送到残油储槽。
3.3乙苯脱氢单元
乙苯脱氢部分的工艺流程如图,乙苯在水蒸气存在下催化脱氢生成苯乙烯,是在段间带有蒸汽再热器的两个串联的绝热径向反应器内进行,反应所需热量由来自蒸汽过热炉的过热蒸汽提供。
在蒸汽过热炉中,水蒸气在对流段内预热,然后在辐射段的A组管内过热到880℃。
此过热蒸汽首先与反应混合物换热,将反应混合物加热到反应温度.然后再去蒸汽过热炉辐射段的B管,被加热到815℃后进入一段脱氢反应器。
过热的水蒸气与被加热的乙苯在一段反应器的入口处混合,由中心管沿径向进入催化剂床层。
混合物经反应器段间再热器被加热到631℃,然后进入二段脱氢反应器。
反应器流出物经废热锅炉换热被冷却回收热量,同时分别产生3.14MPa和0。
039MPa蒸汽。
反应产物经冷凝冷却降温后,送入分离器,不凝气体(主要是氢气和二氧化碳)经压缩去残油洗涤塔用残油进行洗涤,并在残油汽提塔中用蒸汽汽提,进一步回收苯乙烯等产物。
洗涤后的尾气经变压吸附提取氢气,可作为氢源或燃料。
反应器流出物的冷凝液进入液相分离器,分为烃相和水相.烃相脱氢混合液即粗苯乙烯送至分离精馏部分,水相送工艺冷凝汽提塔,将微量有机物除去,分离出的水循环使用.
1—蒸汽过热炉;2(Ⅰ、Ⅱ)—脱氢绝热径向反应器;3,5,7—分离罐;4—废热锅炉;6—液相分离器;8,12,13,15—冷凝器;9,17—压缩机;10—泵;11—残油汽提塔;14—残油洗涤塔;16—工艺冷凝汽提塔
3.4苯乙烯精馏单元
苯乙烯的分离与精制部分,由四台精馏塔和一台薄膜蒸发器组成。
其目的是将脱氢混和液分馏成乙苯和苯,然后循环回脱氢反应系统,并得到高纯度的苯乙烯产品以及甲苯和苯乙烯焦油副产品。
本部分的工艺流程如图所示。
脱氢混合液送入乙苯—苯乙烯分馏塔,经精馏后塔顶得到未反应的乙苯和更轻的组分,作为乙苯回收塔的加料。
乙苯—苯乙烯分馏塔为填料塔,系减压操作,同时加入一定量的高效无硫阻聚剂,使苯乙烯自聚物的生成量减少到最低,分馏塔底物料主要为苯乙烯及少量焦油,送到苯乙烯塔.苯乙烯塔也是填料塔,它在减压下操作。
塔顶为产品精苯乙烯,塔底产物经薄膜蒸发器蒸发,回收焦油中的苯乙烯,而残油和焦油作为燃料。
乙苯-苯乙烯塔与苯乙烯塔共用一台水环真空泵维持两塔的减压操作。
在乙苯回收塔中,塔底得到循环脱氢用的乙苯,塔顶为苯—甲苯,经热量回收后,进入苯—甲苯分离塔将两者分离。
本流程的特点主要是采用了带有蒸汽再热器的两段径向流动绝热反应器,在减压下操作,单程转化率和选择性都很高;流程设有尾气处理系统,用残油洗涤尾气以回收芳烃,可保证尾气中不含芳烃;残油和焦油的处理采用了薄膜蒸发器,使苯乙烯回收率大大提高.在节能方面采取了一些有效措施,例如进入反应器的原料(乙苯和水蒸气的混合物)先与乙苯—苯乙烯分馏塔顶冷凝液换热,这样既回收了塔顶物料的冷凝潜热,又节省了冷却水用量.
1—乙苯—苯乙烯分馏塔;2—乙苯回收塔;3—苯—甲苯分离塔;4—苯乙烯塔;5—薄膜蒸发器;6,7,8,9—冷凝器;10,11,12,13—分离罐;14—排放泵
4主要生产设备
4。
1反应器
烷基化反应器是两台串联的绝热反应器,控制反应压力使反应在全液相进行.烷基转移反应器主要完成烷基转移反应,在催化剂作用下进行反应.乙苯脱氢反应器也是两台串反应器。
4。
2主要分离设备--精馏塔
精馏塔是进行精馏的一种塔式汽液接触装置,又称为蒸馏塔,有板式塔与填料塔两种主要类型,根据操作方式又可分为连续精馏塔与间歇精馏塔。
蒸气由塔底进入,与下降液进行逆流接触,两相接触中,下降液中的易挥发的轻组分不断地向蒸气中转移,蒸气中的难挥发重组分组分不断地向下降液中转移,蒸气愈接近塔顶,其易挥发组分浓度愈高,而下降液愈接近塔底,其难挥发组分则愈富集,达到组分分离的目的。
由塔顶上升的蒸气进入冷凝器,冷凝的液体的一部分作为回流液返回塔顶进入精馏塔中,其余的部分则作为馏出液取出。
塔底流出的液体,其中的一部分送入再沸器,热蒸发后,蒸气返回塔中,另一部分液体作为釜残液取出。
精馏原理蒸馏的基本原理是将液体混合物部分气化,利用其中各组份挥发度不同的特性,实现分离目的的单元操作。
4。
3泵
液泵开动前,先将泵和进料管灌满液体物料,泵运转后,在叶轮高速旋转而产生的离心力的作用下,叶轮流道里的液体被甩相四周,压入蜗壳,叶轮入口形成真空,液池的水在外界大气压力下沿吸液管被吸入补充了这个空间,继而吸入的液体物料又被叶轮甩出经蜗壳而进入出料管。
由此可见,若离心泵叶轮不断旋转,则可连续吸液、压液,液体物料便可源源不断地从低处扬到高处或远方。
综上所述,离心泵是由于在叶轮的高速旋转所产生的离心力的作用下,将液体物料提相高处的,故称离心泵。
所有离心泵均设有备用的另一台泵。
气体输送泵的原理与水泵相似,通过离心力的作用,增加气体的压力完成输送过程.
4。
4压缩机
为了增加气体的压力以达到所需求的压力,必须使用压缩机。
离心式压缩机的工作原理与输送液体的离心泵类似,气体从中心流入叶轮,在高速旋转的叶轮的作用下,随叶轮作高速旋转并沿半径方向甩出,叶轮在驱动机械的作用对气体作功。
因此,气体在叶轮内流动过程中,一方面由于受旋转离心力的作用增加了气体的本身压力,另一方面又得到了很大的速度能。
气体离开叶轮后,这部分速度能在通过叶轮的扩压器、回流器弯道的过程中转变为压能,进一步使气体的压力得到升高。
在活塞式压缩机中,气体是依靠在气缸内往复运动的活塞来进行压缩的。
其压缩气体共分为三个过程:
吸气过程、压缩过程、排气过程。
相配套的有缓冲器和冷却器,要达到高压状态,往往需要进行多级压缩。
4。
5换热器
换热器,是将热流体的部分热量传递给冷流体的设备,又称热交换器,换热器是化工、石油、动力、食品及其它许多工业部门的通用设备.在化工生产中换热器可作为加热器、冷却器、冷凝器、蒸发器和再沸器等,应用更加广泛。
换热器种类很多,但根据冷、热流体热量交换的原理和方式基本上可分三大类即:
间壁式、混合式和蓄热式,在三类换热器中,间壁式换热器应用最多,最为常见的就是管壳式换热器。
换热器是实现化工生产过程的重要设备,也是能量综合利用的主要设备,在生产中占有重要地位。
第四部分合成橡胶厂生产装置
1关于橡胶
*SBS(热塑性丁苯橡胶)*公路沥青内含有5-6%,使其耐磨、降噪、且夏天不化,冬天不裂.
*丁基橡胶*汽车轮胎的内胎,及吊瓶瓶塞.
*顺丁橡胶*汽车轮胎胎侧,具有弹性好的特点。
2顺丁橡胶的合成装置
顺丁橡胶的合成装置共分五个部分,分别是抽提、聚合、凝聚、后处理和回收装置。
总的操作流程为:
原料C4---抽提装置-—-聚合装置———胶液罐储存—--凝聚装置——-后处理.由凝聚过程分离出的粗溶剂,先到罐区储存,在到回收装置进行回收,最后打回反应釜内再利用。
2.1抽提装置
2.1.1抽提目的
顺丁橡胶、SBS等橡胶产品的原料均为聚合级丁二烯。
但原料为多种碳四组分的混合物,由于碳四原料中大部分组分与丁二烯-1,3之间的沸点较为接近,而且相互之间有共沸物产生,这样采用一般的精馏方法很难进行分离开,所以为了得到目标产品(丁二烯)就必须采用特殊分离方法——萃取精馏.萃取精馏的原理就是:
向被分离物料碳四原料中加入一种新的组分-—萃取溶剂,它的加入使得原来物料中各组分之间的相对挥发度发生明显变化,从而使物料中难以用普通精馏方法分离的组分如:
顺丁烯-2和反丁烯—2等组分在第一萃取精馏塔分离出来,乙基乙炔和乙烯基乙炔等组分在第二萃取精馏塔分离出来。
抽提后的丁二烯浓度可达到99.5%以上.
2。
1.2抽提方法
1、DMF(二甲基甲酰胺)法
DMF法抽提丁二烯装置所用原料为化一裂解副产物碳四组分及炼油厂蒸馏装置生产的碳四组分,其中丁二烯含量在50%左右,产品为纯度达99。
5%以上的聚合级丁二烯。
DMF抽提装置的主要构成
DMF抽提丁二烯装置可分为两个部分:
萃取部分和精馏部分。
萃取部分包括第一萃取精馏系统和第二萃取精馏系统,碳四原料中的丁烷、丁烯等在第一萃取精馏系统中脱除,乙烯基乙炔、一部分乙基乙炔等组分在第二萃取精馏系统中脱除;精馏部分包括丁二烯净化和溶剂精制两系统,除去其中的二甲胺、甲基乙炔、水、顺丁烯—2等杂质,得到丁二烯成品;而溶剂精制系统是将循环溶剂中的水分,二聚物等轻组分及焦油等重组分除去,保持循环溶剂的质量。
DMF抽提主要设备
1、减温减压器:
就是将高温高压蒸汽降为低压低温蒸汽(可为过热蒸汽)的设备。
装置中的减温减压器为套管式的结构,管内走高压高温蒸汽,管间走冷却水.内管管壁上开有许多小孔。
其目的有两个:
一是由于高速蒸汽流过管子会产生很大噪音,这种结构可以消除噪音(与消音器结构类似)。
二是高速蒸汽在流过管内使会使管内形成负压区,由此,管间冷却水即可有管壁上的小孔进入内管,以加快蒸汽冷却。
至于减温则是通过调整阀门开度,通过节流来达到。
一般情况均为先减压后减温。
此装置用减温减压器将3.5MPa,240℃的水蒸气降至1MPa,180℃.
2、屏蔽泵:
屏蔽泵是一种无密封泵,泵和驱动电机都被密封在一个被泵送介质充满的压力容器内,此压力容器只有静密封,并由一个电线组来提供旋转磁场并驱动转子。
这种结构取消了传统离心泵具有的旋转轴密封装置,故能做到完全无泄漏。
因此,屏蔽泵主要被选用为输送易燃、易爆、有毒等石油化工液体.
结构:
屏蔽泵是用同一根轴将电机的转子和泵的叶轮固定在一起,然后用屏蔽套将这一组转子屏蔽住.而电机的定子围绕在屏蔽套的四周,屏蔽套是由金属制成的,因此动力可以通过磁力场传递给转子.而整个转子都在被泵送液体中运转.而屏蔽的端部靠法兰或焊接的结构实现静密封。
屏蔽套实际上是一个压力容器。
除了屏蔽套之外,还有一个部件是循环管.利用泵送液体对轴承润滑与冷却,有时也对电机冷却都起到非常重要的作用.
定子的内表面和转子的外表面装有耐腐蚀金属薄板制造的定子屏蔽套和转子屏蔽套。
各自端面用耐腐蚀金属薄板与它们焊接。
与被输送液体分隔,使定子绕组铁芯和转子铁芯不受浸蚀。
循环管一般是从泵排出口引入少部分被输送液体(约1%~3%总流量),经过滤后,通过循环管,先润滑冷却后轴承,然后再通过定子屏蔽套与转子屏蔽套之间的间隙进行冷却,然后再润滑冷却前轴承,最后经叶轮平衡孔回流到叶轮进口眼。
屏蔽泵的屏蔽套,即定子屏蔽套与转子屏蔽套,用来防止输送介质浸人定子绕组和转子铁芯.但由于屏蔽套的存在,使电机定子和转子之间的间隙加大,造成屏蔽套中产生涡流,造成电机性能下降,功率损耗加大.
为了减少功率损耗,屏蔽电机定子内径通常比较小,屏蔽套壁厚尽可能薄,屏蔽套材料选用非导磁材料.所以屏蔽电机通常是细长式结构.屏蔽套材料多为304、304L、316,316L不锈钢。
钛材料虽然涡流损失小,但成本高,因此较少被选用.屏蔽套厚度一般为0。
2~1mm。
3、单级离心泵:
一般选用弹性膜片式联轴器,采用双端面密封。
PS.只要是泵一般均在出口处设有压力表.
4、电机:
电机在无负