第3篇锂离子电池隔膜的技术和产业发展资料.docx
《第3篇锂离子电池隔膜的技术和产业发展资料.docx》由会员分享,可在线阅读,更多相关《第3篇锂离子电池隔膜的技术和产业发展资料.docx(21页珍藏版)》请在冰豆网上搜索。
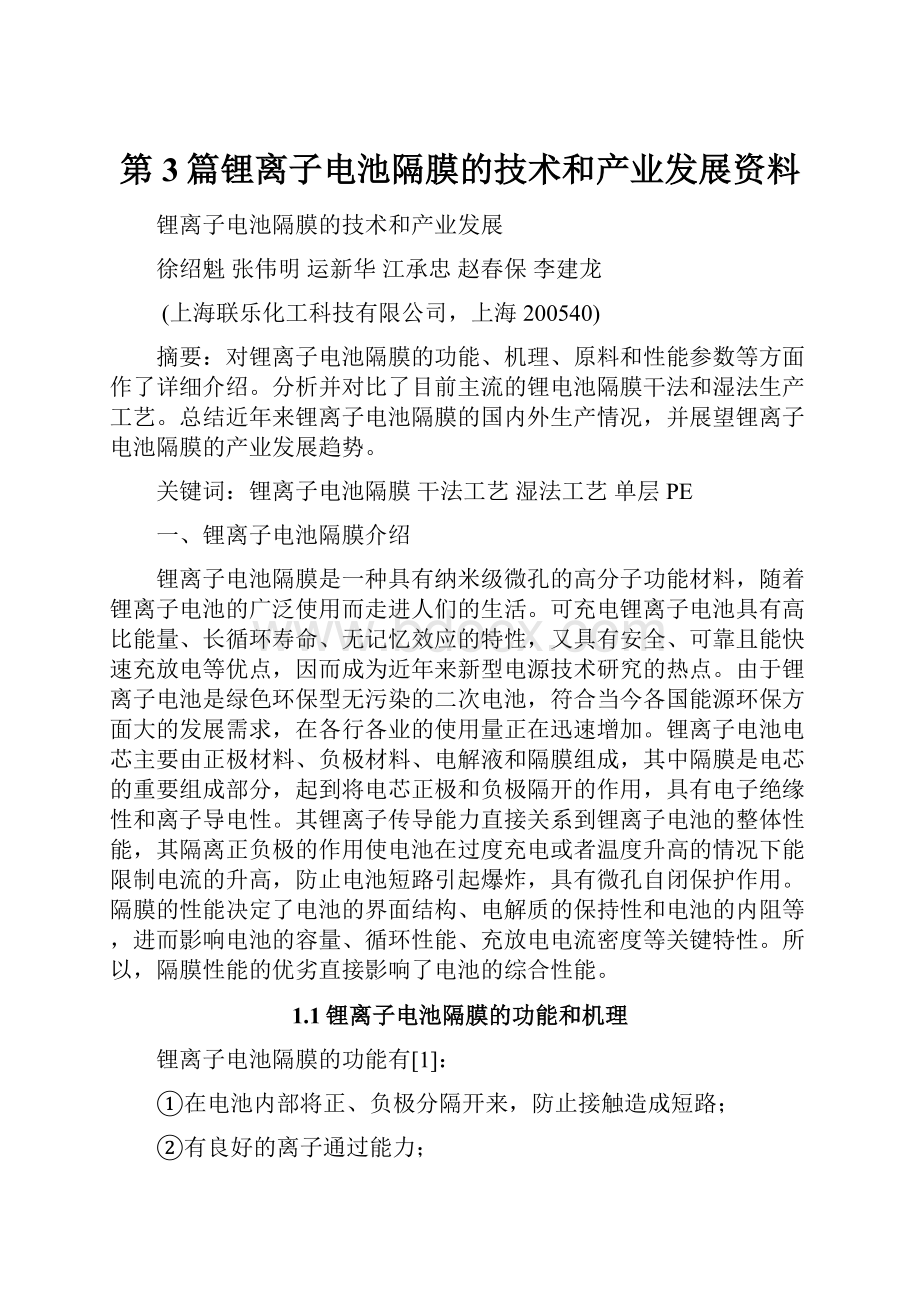
第3篇锂离子电池隔膜的技术和产业发展资料
锂离子电池隔膜的技术和产业发展
徐绍魁张伟明运新华江承忠赵春保李建龙
(上海联乐化工科技有限公司,上海200540)
摘要:
对锂离子电池隔膜的功能、机理、原料和性能参数等方面作了详细介绍。
分析并对比了目前主流的锂电池隔膜干法和湿法生产工艺。
总结近年来锂离子电池隔膜的国内外生产情况,并展望锂离子电池隔膜的产业发展趋势。
关键词:
锂离子电池隔膜干法工艺湿法工艺单层PE
一、锂离子电池隔膜介绍
锂离子电池隔膜是一种具有纳米级微孔的高分子功能材料,随着锂离子电池的广泛使用而走进人们的生活。
可充电锂离子电池具有高比能量、长循环寿命、无记忆效应的特性,又具有安全、可靠且能快速充放电等优点,因而成为近年来新型电源技术研究的热点。
由于锂离子电池是绿色环保型无污染的二次电池,符合当今各国能源环保方面大的发展需求,在各行各业的使用量正在迅速增加。
锂离子电池电芯主要由正极材料、负极材料、电解液和隔膜组成,其中隔膜是电芯的重要组成部分,起到将电芯正极和负极隔开的作用,具有电子绝缘性和离子导电性。
其锂离子传导能力直接关系到锂离子电池的整体性能,其隔离正负极的作用使电池在过度充电或者温度升高的情况下能限制电流的升高,防止电池短路引起爆炸,具有微孔自闭保护作用。
隔膜的性能决定了电池的界面结构、电解质的保持性和电池的内阻等,进而影响电池的容量、循环性能、充放电电流密度等关键特性。
所以,隔膜性能的优劣直接影响了电池的综合性能。
1.1锂离子电池隔膜的功能和机理
锂离子电池隔膜的功能有[1]:
①在电池内部将正、负极分隔开来,防止接触造成短路;
②有良好的离子通过能力;
③有保持电解液的能力;
④有一定的保护电池安全的能力。
隔膜中具有大量曲折贯通的微孔,电解液中的离子载体可以在微孔中自由通过,在正负极之间迁移形成电池内部导电回路,而电子则通过外部回路在正负电极之间迁移形成电流,供用电设备利用。
1.2锂离子电池隔膜的主要原料
隔膜使用的聚烯烃材料主要是聚丙烯(PP)、聚乙烯(PE)两类。
聚烯烃材料具有强度高、耐酸碱腐蚀性好、防水、耐化学试剂、生物相容性好、无毒性等优点,在众多领域得到了广泛的应用。
当前,商品化的液态锂离子电池大多使用微孔聚烯烃隔膜,因为聚烯烃化合物在合理的成本范围内可以提供良好的机械性能和化学稳定性,而且具有高温自闭性能,更加确保了锂离子二次电池在日常使用上的安全性。
以日本旭化成公司为例[4~5],该公司采用三元体系生产的大孔径薄膜,其组分为:
聚烯烃含量20~50%,增塑剂30~60%,二氧化硅10~40%。
在聚烯烃中包含HDPE(M=28~50万)、LLDPE(M=10~30万)和UHMWPE(M=200~230万)。
在聚烯烃中,三种聚乙烯的含量均控制在10~50%,例如其中一份专利给出50%:
40%:
10%的质量组成比例。
1.3锂离子电池隔膜的性能参数
锂离子电池隔膜的主要性能参数[6]有:
厚度、孔隙率、孔径及分布、透气度、吸液率、抗穿刺强度、热收缩率、闭孔及破膜温度等。
1.3.1厚度
在同样大小的电池中,隔膜厚度越厚,能卷绕的层数就越少,相应容量也就会降低;但是另一方面,较厚的产品,抵抗穿刺的性能会稍高,安全性会高一些,同时同样孔隙率的情况下,越厚的产品,其透气率会稍差,使得电池的内阻会高一点。
而厚度小电阻小,占据空间少,在限定空间中可以使用更长的电极。
所以在考虑电池隔膜厚度的时候需要在容量指标和安全性之间寻找一个平衡。
一般厚度控制在≤25
,动力锂电池隔膜厚度约40
。
1.3.2孔隙率
孔隙率是材料中孔隙体积占总体积的比例,反映隔膜内部微孔体积占比多少。
孔隙率的大小影响电池的内阻,但不同种隔膜之间的孔隙率的绝对值无法直接比较。
孔隙率与隔膜的透过能力有一定关系,孔隙率较大有利于锂离子通过,但孔隙率大并不代表隔膜的透过性好,因为透过性取决于微孔的导通率和孔径大小。
另外,对于一定的电解质,具有高孔隙率的隔膜可以降低电池的阻抗,但也不是越高越好,但是孔隙率过大则影响机械强度和闭孔性能,目前商用隔膜孔隙率一般在40%~60%之间。
1.3.3孔径及分布
锂电池隔膜上面要求有微孔,便于锂离子通过。
一般隔膜的孔径在纳米级,双拉方式生产的隔膜的孔接近圆形,干法隔膜的孔为长条形。
从现有的工艺水平来看,湿法隔膜的孔径在0.01~0.1um,干法隔膜的孔径在0.1~0.3um,孔径的大小与隔膜的透过能力有关,过小的孔径会抑制锂离子通过,过大的孔径有可能导致隔膜穿孔形成电池微短路导致电池自放电过快。
孔的分布不均匀有可能导致电池内部电流密度不一致,工作时会形成局部电流过大,长期使用中锂离子可能沉积形成枝晶状刺穿隔膜。
总体来看,隔膜的孔径直接影响电池的内阻和短路率。
1.3.4透气度
透气度又叫Gurley数,反映隔膜的透过能力。
即一定体积的气体,在一定压力条件下通过6.45cm2面积的隔膜所需要的时间,气体的体积量一般为100ml。
透气度是由隔膜的孔径大小、孔径分布、孔隙率和开孔率等决定的,透气率从一定意义上来讲,和用此隔膜装配的电池内阻成正比,即该数值越大,则内阻越大。
然而,对于不同类型、厚度的隔膜,该数字的直接比较没有任何意义。
因为锂离子电池中的内阻和离子传导有关,而透气率和气体传导有关,两种机理是不一样的。
换句话说,单纯比较两种不同隔膜的Gurley数是没有意义的,因为可能两种隔膜的微观结构完全不一样;但同一种隔膜的Gurley数的大小能很好的反应出内阻的大小,因为同一种隔膜相对来说微观结构是一样的。
干法隔膜典型的透气度在300~400秒/100ml。
1.3.5吸液率
吸液率反映隔膜吸收电解液的能力,是衡量隔膜与电解液相容性的指标,影响锂电池的内阻和容量。
吸液率不仅受隔膜材料与电解液的浸润性能影响,还受隔膜的孔隙率、开孔率、孔径的影响。
吸液率测试方法是把干式样称重后浸泡在电解液中,直至吸收平衡,再取出湿隔膜擦干表面电解液称重,计算单位积吸收电解液的重量。
直观来看,为了保证电池的内阻不是太大,要求隔膜是能够被电池所用的电解液完全浸润,但是目前这方面没有一个公认的检测标准。
当前市场上通用的衡量标准是:
取一定面积的隔膜完全浸泡在电解液中,看隔膜吸收电解液的重量(常用单位是g/m2)。
同样厚度的隔膜,吸收的重量越大,浸润效果越好。
浸润度一方面与隔膜材料本身有关,还与隔膜的表面及内部微观结构密切相关,另一方面与电解液的配方也有很大关系。
1.3.6机械强度
锂离子电池对隔膜机械强度的要求较高。
电池中的隔膜直接接触有硬表面的正极和负极,而且当电极上的毛刺、带尖角的大颗粒物质、甚至电池内部形成枝晶,都会引起隔离膜被穿破而引起电池短路或微短路,因此要求隔离膜的抗穿刺强度尽量高。
抗穿刺强度指标反映隔膜抗外力穿刺的能力,影响电池的短路率和安全性。
在微结构一定的情况下,相对来说抗穿刺强度高的,其装配不良率低。
但是单纯追求高穿刺强度,也必然导致隔膜的其他性能下降。
一般对产品都会做穿刺实验验证隔膜的可靠性。
抗穿刺强度的测试方法是用环状物体将隔膜固定,取一定直径的针,要求针尖无锐边缘,以一定的速度垂直刺过隔膜,将隔膜刺破最大力就是隔膜的抗穿刺力。
对于湿法工艺一般要求穿刺强度大于300g/20um。
此外对隔膜的拉伸强度也有一定要求。
单轴拉伸的隔膜在拉伸方向与垂直拉伸方向强度不同,而双轴拉伸制备的隔膜强度在两个方向上基本一致。
尽管如此,在实际应用中双向拉伸并没有性能上的优势。
因为电池卷绕的受力方向是纵向;横向拉伸会导致垂直方向的收缩,这种收缩在高温下会导致电极之间的相互接触。
一般而言孔隙率、透气性较高时,尽管其阻抗较低,但其机械强度却要下降,因此在调节隔膜其中一项或几项性能指标的同时,要兼顾微孔膜的其他各项性能指标,以获得最佳的使用性能。
拉伸强度(纵/横向)的测试方法是隔膜在一定方向上、通过拉伸夹具以一定的试验速度拉伸直至断裂所表现出的承载能力。
对于湿法工艺一般要求拉伸强度大于1200kg/cm2。
1.3.7热收缩率
热收缩率反映隔膜在受热时的尺寸稳定性。
隔膜是一种高分子材料,经过拉伸取向后,在高温条件下,拉伸方向都或多或少会产生热收缩。
单轴拉伸的产品在纵向热收缩会偏大,横向基本不产生热收缩。
双轴拉伸的隔膜在两个方向上均会产生热收缩。
通常隔膜的热收缩是在自然松弛状态下测试得到。
对于卷绕形式的电芯来说,由于纵向有支撑和固定,隔膜纵向的实际热收缩没有那么大,对电池基本没有影响,主要影响产生在隔膜的横向收缩。
除了隔膜需要在电池使用的温度范围内(-20~60℃)保持尺寸稳定外,还有一个就是在电池生产过程中由于电解液对水份非常敏感,大多数厂家会在注液前进行85~90℃的长时间烘烤,所以要求在这个温度下隔膜的尺寸也应该稳定,否则会造成电池在烘烤时,隔膜收缩过大,极片外露造成短路;另外在电池使用过程中也有可能遇到电池内部由于电化学反应产生高温导致隔膜收缩,因此设计电芯采用隔膜的宽度时应当准确了解和要求隔膜的横向收缩率。
以湿法隔膜为例,一般要求90℃条件下加热2小时条件下,纵向<5.0%,横向<3.0%。
1.3.8闭孔温度和破膜温度
自动关断保护性能是锂离子电池隔膜的一种安全保护性能,是锂离子电池内部防止由于短路、过充等原因造成温度失控的有效方法。
隔膜的闭孔温度和破膜温度是该性能的主要参数。
材料的熔点决定了隔膜的闭孔温度、破膜温度的高低。
闭孔温度和破膜温度是反映隔膜耐热性能和热安全性能的最重要参数,闭孔温度是指达到这一温度后,隔膜能够在热作用下关闭孔隙,从而在电池内部形成断路,防止电池内部温度由于内部电流过大进一步上升,造成安全隐患。
这一特性可以为锂离子电池提供一个额外的安全保护。
破膜温度是造成电池破坏的极限温度,在此温度下,隔膜完全融化收缩,电极内部短路产生高温直至电池解体或爆炸。
由于非正常情况下电池短路使电池内部温度升高,当温度到达隔膜的闭孔温度时,隔膜内的微孔会坍塌,阻断电流通过,但热惯性会使温度进一步上升,有可能达到破膜温度而造成隔膜熔体破裂,造成电池内部短路。
因此,闭孔温度和破膜温度相差越大越好(即安全窗口温度越高越好),此时电池的安全性越好。
破膜温度-闭孔温度反映了隔膜的温度安全区间,(闭孔温度与材料本身的熔点密切相关)以单层PE膜为例,闭孔温度在128~135℃,破膜温度一般大于145℃,温度保护区间为145-135=10℃。
PP隔膜的闭孔温度在150~160℃,破膜温度在170℃左右。
闭孔温度和熔融破裂温度的测试方法是:
在不断升温的情况下测试隔膜分隔的极板之间的电阻,随着温度升高,电阻突然增大,此时的温度即闭孔温度。
再继续升温,电阻会突然变小,此时的温度即破膜温度。
1.4锂离子电池对隔膜的要求
隔膜性能决定了电池的内阻和界面结构,进而决定了电池容量、安全性能、充放电电流密度和循环性能等特性,因此需满足如下一些性能:
(1)化学稳定性—电解液为有机溶剂体系,耐有机溶剂;
(2)机械性能—隔膜的拉伸强度高,穿刺强度高;
(3)热稳定性—收缩率低,具有较低的闭孔温度和较高的破膜温度;
(4)透过率好—孔隙率高,孔径分布均匀、透气性好;
(5)表面无静电—不吸尘、易分离;
(6)电解液浸润性—与电解液相容性好,吸液率高;
(7)均匀性—厚度、透过率、热收缩等。
二、锂离子电池隔膜工艺技术
目前市场上主流的锂电池隔膜生产工艺包括两种,即干法工艺(熔融拉伸)和湿法工艺(热致相分离),其中干法工艺又可细分为干法单向拉伸工艺和干法双向拉伸工艺,两种方法都包括至少一个取向步骤使薄膜产生孔隙并提高拉升强度。
2.1干法工艺
干法工艺原理[2]是先将高聚物原料熔融,之后高聚物熔体挤出时在拉伸应力下结晶,形成垂直于挤出方向而又平行排列的片晶结构,并经过热处理得到硬弹性材料。
具有硬弹性的聚合物膜经过拉伸环节之后,发生片晶之间的分离而形成狭缝状微孔,再经过热定型制得微孔膜。
该工艺对过程精密控制要求高,尤其是拉伸温度高于聚合物的玻璃化温度而低于聚合物的结晶温度。
目前主要包括干法单向拉伸和双向拉伸工艺。
干法工艺的主要难点在于过程控制精度要求严格,孔隙率控制较难把握,拉伸比较小(约1~3),低温拉伸容易隔膜穿孔。
图1.干法生产工艺的主要步骤
从技术源头来看,干法单向拉伸工艺源自美国Celgard公司,该方法主要是在在熔融挤出成膜后经退火结晶处理形成半结晶PP/PE/PP,单向拉伸出微裂纹(银纹),孔隙率在30-40%。
该工艺经过几十年的发展在美国、日本已经非常成熟,美国Celgard公司拥有干法单向拉伸工艺的一系列专利,日本UBE公司则通过购买Celgard的相关专利使用权进行生产。
采用干法单向拉伸方法生产的隔膜,具有扁长的微孔结构。
从性能上看,没有横向拉伸步骤有利有弊:
由于只进行单向拉伸,隔膜的横向强度比较差,但正是由于没有进行横向拉伸,横向几乎没有热收缩。
干法双向拉伸技术源自中科院化学所,该所是我国最早从事锂电池隔膜研究的单位,后又得到国家863计划的支持。
该技术通过在聚丙烯中加入具有成核作用的β晶型改进剂,利用聚丙烯不同相态间密度的差异,在拉伸过程中发生晶型转变形成微孔,用于生产单层PP膜。
尽管中科院化学所拥有专利技术,但是其集大成者却是美国Celgard公司。
2001年,中科院化学所将其在美国、英国和日本申请的干法双向拉伸专利权转让给美国Celgard公司。
国内的新乡格瑞恩公司以及新时科技的技术就来自于中科院化学所,采用的是干法“双向拉伸”技术生产单层PP膜,其中新乡格瑞恩已经成功实现产业化。
2.2湿法工艺
湿法制备微孔膜的热力学基础是聚合物-溶剂体系的相图。
通过调节体系的温度和浓度,使得聚合物直接从体系中结晶析出。
影响膜孔结构形态因素:
✧冷却速率
✧聚合物溶液的初始浓度
✧聚合物分子量
✧溶剂分子的运动与结晶能力
✧成核剂--成核剂能更好地控制微孔的尺寸和分布
和干法相比,湿法需要有机溶剂,其基本过程是指在高温下将聚合物溶于高沸点、低挥发性的溶剂中形成均相液,使溶剂相连续贯穿于聚合物相形成的连续固态相中,然后降温冷却,导致溶液产生液-固相分离或液-液相分离,再选用挥发性试剂将高沸点溶剂萃取出来,经过干燥获得一定结构形状的高分子微孔膜。
在隔膜用微孔膜制造过程中,可以在溶剂萃取前进行单向或双向拉伸,萃取后进行定型处理并收卷成膜;也可以在萃取后进行拉伸。
用这种方法生产的超高分子量聚乙烯微孔膜具有良好的机械性能。
在目前湿法隔膜制造过程中,通常将液态烃或一些小分子物质与聚烯烃树脂混合,加热熔融后,形成均匀的混合物,然后降温进行相分离,压制得膜片,再将膜片加热至接近熔点温度,进行双向拉伸使分子链取向,最后保温一定时间,用易挥发物质洗脱残留的溶剂,可制备出相互贯通的微孔膜材料。
和干法相比,湿法的制膜过程相对容易调控,可以较好地控制孔径、孔径分布和孔隙率。
但制备过程中需要大量的溶剂,容易造成环境污染,而且与干法熔融拉伸法相比工艺相对复杂。
目前日韩厂商采用湿法工艺的公司较多,主要有日本旭化成、东燃化学、三菱化学、韩国SK化学和美国Entek等。
图2.湿法生产工艺的主要步骤
2.3湿法工艺环节难点
2.3.1投料和配料
投料和配料的稳定性直接关系到挤出过程的稳定性,并且对厚片和薄膜的厚度产生重要的影响,从而影响到后续加工和产品的性能和质量,例如主料和成孔剂的比例是锂离子电池隔膜微孔孔径的大小及分布的影响因素之一。
所以,投料和配料必须要得到比较高的精度保证,一般需要安装电脑精密控制的在线实时计量系统。
2.3.2挤出和混合
该环节需要满足如下的要求:
(1)能够具备较强的剪切塑化能力,让主料快速、均匀的塑化;
(2)能够具备很好的混合效果,让主料与成孔剂均匀混合;(3)能够让物料与挤出机之间不打滑、不倒流、能够稳定进料。
该环节对混合的均匀性以及进料的稳定性计量要求严格。
2.3.3铸片冷却
将模头出来的熔体经过冷辊冷却成固态厚片。
该环节需要满足如下的要求:
(1)冷却熔体,形成厚片;
(2)急冷熔体,降低厚片结晶度,防止球晶的形成;(3)急冷“塑料-成孔剂”混合物熔体,使成孔剂与聚烯烃产生热致性相分离;(4)急冷厚片表面,使已产生相分离的大部分成孔剂被锁在厚片里面,使成孔剂不容易流走和渗出。
该环节对温度控制和冷却速度的控制要求精度很高。
2.3.4拉伸
拉伸系统是薄膜生产的另一个核心环节。
目的是使分子链在拉伸的过程中产生取向,从而改善和提高产品的应用性能。
经过双向拉伸后的油膜,分子链得到了纵横两个方向取向,而成孔剂也均匀地分布在发生了取向的分子链之间,形成了特殊的“网-油”混合结构。
从热力学角度来看,这时锂离子隔膜的微孔或微孔形状已经形成,只是成孔剂还仍然占据了孔的位置,堵住了隔膜的孔眼,使得微孔还没有呈现出来。
2.3.4洗涤烘干
该环节是湿法锂离子隔膜生产特有的工序过程。
因为经上一道工序加工后的薄膜虽然主料膜网与成孔剂基本上已经产生了相分离,但成孔剂还仍然分布在产生了双向取向的分子链之间。
洗涤烘干系统的作用就是将成孔剂从油膜的孔隙中赶出来或萃取出来,形成(准确的讲应该是“呈现出”)能让锂离子通过的微孔结构。
洗涤过程要求快速以适应高速生产,要求萃取能力高,以满足锂离子隔膜低成孔剂残留量的要求。
2.4干法湿法工艺比较
干法和湿法两种工艺方法的比较如表1和表2所示。
表1.不种生产工艺的特点比较
表2.干法和湿法两种工艺方法的比较
比较方法
干法工艺
湿法工艺
工艺比较
工序
简单
复杂
固定资产
相对低
高
工艺控制
难度高
低
产品比较
单层膜
可以
可以
多层膜
可以
不能够
原料
PP
可以
不能够
PE
可以
可以
原料特性
流动性好、分子量低
不流动、分子量高
产品性能
成本
低
高
使用范围
小功率、低容量电池
大功率、高容量电池
安全性
低
高
热关闭温度
低(135oC)
高(180oC)
热收缩性
高
比较低
孔径
比较大
纳米级
环境
友好
污染
2.5动力用锂离子电池隔膜新工艺技术
现有的聚烯烃隔膜耐热性不足,在高于聚合物熔点10~20℃即发生熔融破裂,在170℃发生非常严重的收缩,很难应用于汽车用动力锂离子电池中。
因此目前国外普遍研究的课题是通过各种技术手段提高隔膜的耐热性能,以下是目前主要采用的研究方法。
2.5.1涂层技术
涂层技术是指以聚烯烃隔膜作为基膜,在其表面涂覆一层或几层耐热材料而制备的微孔膜。
基膜要求具有较低的闭孔温度,聚乙烯隔膜以其优越的电流关闭性能成为首选;在聚烯烃隔膜表面涂覆耐热材料时,很难避免不堵塞隔膜的微孔,所以选用的聚乙烯隔膜通常要具有很好的孔径分布和孔隙率。
耐热材料通常选用无机物或无机有机混合物,可以选用的无机材料有SiO2、Al2O3、MgO等。
日立麦克赛尔公司利用其磁带制造等方面积累的技术,在聚烯烃微孔膜表面涂布板状的无机粒子,用来研制动力电池隔膜。
日本帝人公司利用其芳纶纤维方面的技术优势,将氧化铝和芳纶纤维混合溶解后制成浆料,涂覆在聚乙烯隔膜表面,具有很好的耐高温性能。
2.5.2湿法共混技术
湿法共混技术是目前技术难度较高的一种电池隔膜制备技术,主要是在湿法聚乙烯配方体系中混入无机粒子,然后通过双螺杆挤出机熔融挤出、流延铸片、拉伸成膜、萃取干燥等工艺,从而制得耐高温锂离子电池隔膜。
该技术的难点是物料体系在双螺杆挤出机中的熔融混合,螺纹组合的排布对塑化效果影响显著。
在此领域比较有代表性的公司有日本旭化成和东燃化学,但由于这些隔膜价格高昂,目前国内很少有厂家使用。
2.5.3干法多层技术
干法多层技术指目前市场上使用较广的干法PP/PE/PP三层隔膜。
由于此类隔膜的耐热性能仅靠外层的聚丙烯来提供,而聚丙烯的熔点只有160℃左右,所以该类隔膜不能保证170℃以上的熔破温度。
2.5.4Separion隔膜
德国Degussa公司结合无纺布的柔性和无机物良好热稳定性的特点,在纤维素无纺布上复合Al2O3或其他无机物,形成了Separion隔膜的产业化。
该隔膜熔融温度可达到230℃,在200℃下不会发生热收缩,具有较高的热稳定性。
2.5.5静电纺丝
以静电纺丝技术制备非织造布膜,是近年来最新的研究方法。
静电纺丝主要以耐热材料PVDF做为基体,所制得的纤维最主要的特点是纤维直径很细,具有高的比表面积,且所得亚微米级纤维堆积而成的层状膜,具有较高的孔隙率和优异的离子电导率。
中科院理化技术研究所、清华大学等都做了大量的工作并申请了专利,但还没有关于产业化的信息。
三、锂离子电池隔膜的国内外生产情况
在锂离子电池的四种关键材料—正极、负极、隔膜、电解液中,隔膜问题最为突出,我国锂离子电池隔膜产业正处于起步阶段,隔膜材料严重依赖进口,目前世界上只有日本、美国等少数国家拥有聚合物生产技术和相应的规模化产业。
国内外主要锂离子电池隔膜公司总体情况见表3(截止2014年,粗略统计锂离子电池隔膜国内公司目前已有22家)。
表3.国内外主要锂电池隔膜公司总体情况一览表
厂商名称
技术来源
结构组成
加工工艺
产能
美国Celgard
拥有干法单拉的系列专利并受让中科院化学所干法双拉专利
单层PE
单层PP
多层PP/PE/PP
干法单拉+干法双拉
8980万m2/年
美国Entek
自有技术
单层PE
湿法
1800万m2/年
日本宇部兴产(Ube)
购买美国Celgard干法单拉专利
多层PP/PE/PP
干法
3000万m2/年
日本旭化成(Asahi)
自有技术
单层PE
湿法
17000万m2/年
日本东燃(Tonen)
自有技术、基体材料有美孚研发力量支撑
单层PE
湿法
8340万m2/年
日本住友(Sumitomo)
自有技术
单层PE
湿法
1600万m2/年
韩国SK化工
自有技术
单层PE
湿法
2900万m2/年
深圳星源材质
引进湿法技术
单层PE
单层PP
多层PP/PE/PP
干法+湿法
现有5000万m2/年,引进德国一条湿法生产线,产能3000万m2/年,总产能8000万m2/年
佛山金辉高科
自主研发
单层PE
湿法
一期产能1200万m2/年
二期增加产能4500万m2/年
三期拟增加产能4500万m2/年
新乡格瑞恩
与中科院化学所合作研发干法双拉
单层PP
干法双拉
12条干法双拉工艺生产线,产能8000万m2/年。
目前引进韩国湿法生产线1条,产能8000万m2/年。
计划引进德国湿法生产线,产能6000万m2/年,未来总产能近2亿m2/年
沧州明珠
自主研发,与BOPP工艺具有一定的技术相通性
单层PP膜、多层复合膜
干法单拉
现有产能4000万m2/年,涂布能力1000万m2/计划引进湿法生产线,产能3000万m2/年,未来总产能7000万m2/年
苏州捷力
引进日本技术
单层PE
湿法
现有产能2000万m2/年
河南义腾
未知
干法双拉
现有产能4000万m2/年
南通天丰
自主研发,同时拥有干法单拉和干法双向同步拉伸工艺
单层PP
双层PP/PE、多层PP/PE/PP
干法单向+双向
现有产能4000万m2/年
天津东皋
自主研发,拥有自主知识产权的“超临界萃取”工艺
单层PE
湿法
现有产能3000万m2/年
纽米科技
四川大学湿法技术
单层PE
湿法
现有产能3000万m2/年
大东南
自主研发
单层PE
单层PP
干法+湿法
干法双向拉伸PP隔膜生产线4条