叉杆毕业设计.docx
《叉杆毕业设计.docx》由会员分享,可在线阅读,更多相关《叉杆毕业设计.docx(19页珍藏版)》请在冰豆网上搜索。
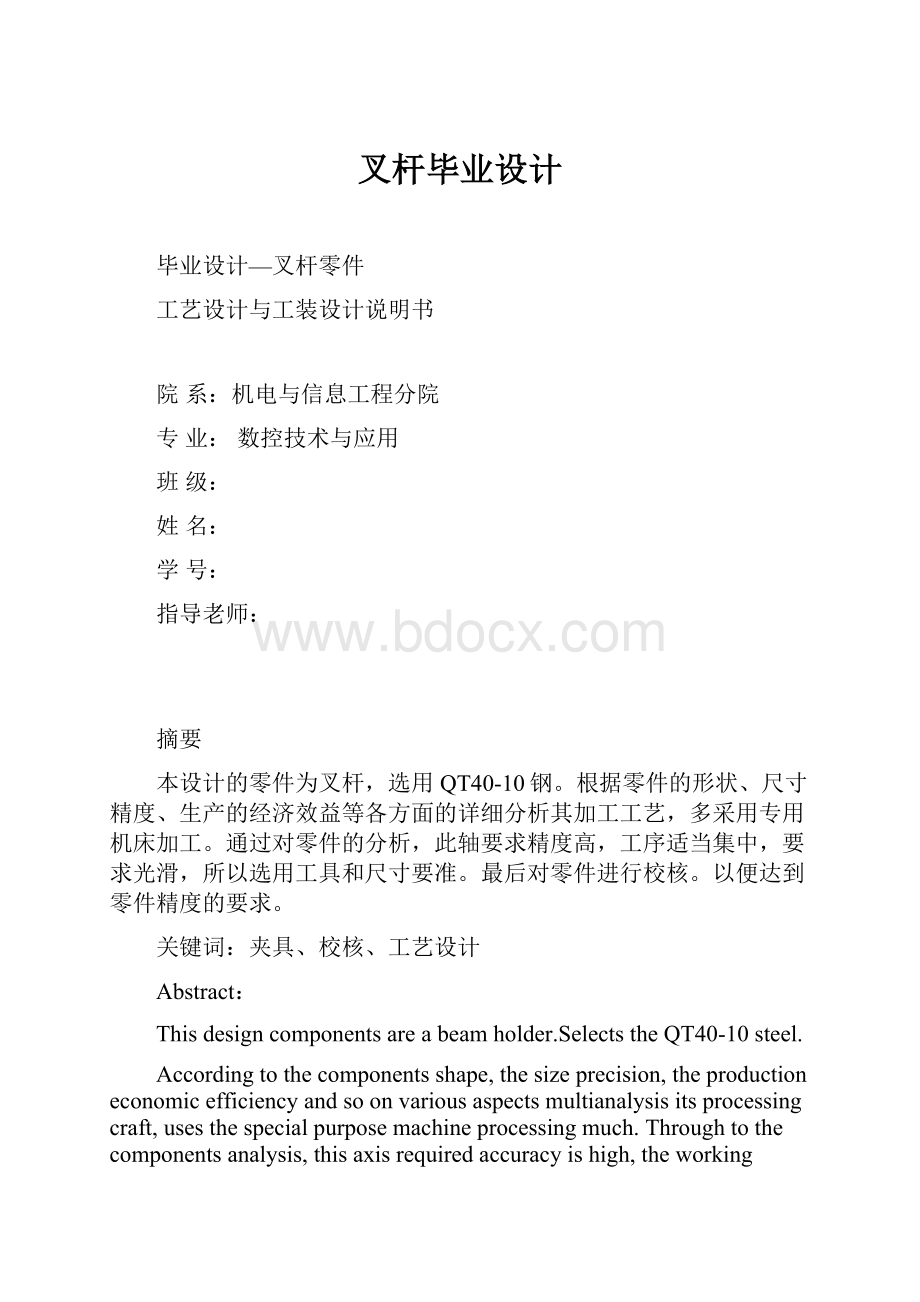
叉杆毕业设计
毕业设计—叉杆零件
工艺设计与工装设计说明书
院系:
机电与信息工程分院
专业:
数控技术与应用
班级:
姓名:
学号:
指导老师:
摘要
本设计的零件为叉杆,选用QT40-10钢。
根据零件的形状、尺寸精度、生产的经济效益等各方面的详细分析其加工工艺,多采用专用机床加工。
通过对零件的分析,此轴要求精度高,工序适当集中,要求光滑,所以选用工具和尺寸要准。
最后对零件进行校核。
以便达到零件精度的要求。
关键词:
夹具、校核、工艺设计
Abstract:
Thisdesigncomponentsareabeamholder.SelectstheQT40-10steel.
Accordingtothecomponentsshape,thesizeprecision,theproductioneconomicefficiencyandsoonvariousaspectsmultianalysisitsprocessingcraft,usesthespecialpurposemachineprocessingmuch.Throughtothecomponentsanalysis,thisaxisrequiredaccuracyishigh,theworkingproceduresuitablecentralism,therequestissmooth,thereforeselectsthetoolandthesizewants.Finallycarriesontheexaminationtothecomponents.Inordertoachievethecomponentsprecisiontherequest.
Keyword:
Jig,examination,technologicaldesign
目录
前言----------------------------------------------------------------------------------------------4
1、绪言---------------------------------------------------------------------------------------5
1.1、课程设计的目的--------------------------------------------------5
2、机械制造工艺要求的基本任务和要求----------------------------5
2.1、基本任务--------------------------------------------------------6
2.1.1、工艺设计的基本任务------------------------------------------------------------------6
2.1.2、夹具设计的基本任务------------------------------------------------------------------6
2.2、设计要求--------------------------------------------------------7
2.2.1、工艺设计的设计要求-------------------------------------------------------------------7
2.2.2、夹具设计的设计要求------------------------------------------------------------------7
3、机械制造工艺课程设计的方法和步骤------------------------------------------7
3.1生产纲领的计算与生产类型的确定-----------------------------------------------------7
3.2零件材料的分析-----------------------------------------------------------------------------7
3.3分析零件图----------------------------------------------------------------------------------7
3.4确定毛坯--------------------------------------------------------------------------------------8
3.5加工工艺路线--------------------------------------------------------------------------------9
3.6确定工序尺寸及其公差------------------------------------------------------------------10
3.7确定切削用量------------------------------------------------------------------------------11
3.8机床及工艺设备---------------------------------------------------------------------------11
3.9制作工艺卡片------------------------------------------------------------------------------11
3.10零件的程序编制-------------------------------------------------------------------------12
4、夹具设计------------------------------------------------------------------------------13
4.1夹具设计的目的和要求------------------------------------------------------------------13
4.2夹具设计步骤-----------------------------------------------------------------------------13
4.3夹具零件图--------------------------------------------------------------------------------14
结论:
-------------------------------------------------------------------------------------------15
致谢:
-------------------------------------------------------------------------------------------16
参考文献--------------------------------------------------------------------------------------17
前言
随着科技技术的不断进步,生产都向着自动化、专业化和大批量化的方向发展。
这就要求企业的生产在体现人性化的基础上降低工人的生产强度和提高工人的生产效率,降低企业的生产成本。
现代的生产和应用设备多数都采用机电一体化、数字控制技术和自动化的控制模式。
在这种要求下叉杆越发体现出其广阔的应用领域和市场前景。
特别是近年来与微电子、计算机技术相结合后,使叉杆进入了一个新的发展阶段。
又因需求的增加,所以生产也步入大批量化和自动化。
为适应机械设备的要求,对叉杆的设计要求和技术领域的拓展还需要不断的更新。
1.毕业设计的目的
(1)培养工程意识
(2)训练基本技能
(3)培养质量意识
(4)培养规范意识
2、机械制造工艺要求的基本任务和要求
2.1、基本任务
2.1.1、工艺设计的基本任务
(1)绘制零件工作图一张
(2)绘制毛坯-零件合图一张
(3)编制机械加工工艺规程卡片一套
(4)编写设计说明书一份
2.1.2、夹具设计的基本任务
(1)收集资料,为夹具设计做好准备
(2)绘制草图,进行必要的理论计算和分析以及夹具的结构方案
(3)绘制总图和主要非标准件零件图,编写设计说明书
(4)编制夹具的使用说明或技术要求
2.2、设计要求
2.2.1、工艺设计的设计要求
(1)保证零件加工质量,达到图纸的技术要求
(2)在保证加工质量的前提下,尽可能提高生产效率
(3)要尽量减轻工人的劳动强度,生产安全
(4)在立足企业的前提下,尽可能采用国内技术和装备
(5)工艺规程应正确.清晰,规范化,标准化的要求
2.2.2、夹具设计的设计要求
(1)保证工件的加工精度
(2)提高生产效率
(3)工艺性好
(4)使用性好
(5)经济性好
3、机械制造工艺课程设计的方法和步骤
3.1、零件分析
1.首先在对加工零件进行充分的工艺分析,确定零件的编程坐标系,计算零件的几何元素坐标参数。
确定钻孔或扩孔、镗孔和锪孔的中心坐标,铣面时的起点坐标和终点坐标,两端点坐标。
2.其次零件加工工艺路线或加工顺序。
根据零件图、零件的制造材料、零件的质量要求确定主运动的启动、停止、方向、变速;进给运动的速度大小;选择刀具的参数及冷却液开、关等辅助装置的动作。
3.根据零件的形状和加工位置设计制造其专用夹具,适合于工件的大批量生产。
4.零件的图形、尺寸及公差、形位公差、表面粗糙度、材料、热处理及其他技术要求要表示的清晰明了。
5.要做到加工效率高、加工质量符合要求、加工费用低等要求。
基本尺寸
考虑材料力学性能:
强度、塑性、硬度、冲击韧性、疲劳强度;
内外表面质量
十字接头此零件用于两轴,杆之间连接传递,扭力或运动的中
间联接器所以对韧性和强度耐磨度有一定的要求.如零件图所示该零件主要加工表面及技术要求分析如下.
1.零件整体在未注尺寸公差为IT14级.这对一般的铣削加工都不难打到.
2.零件的形位公差要求也不高.它是GBIT1184-1996K级也较容易达到.
3.T1.T2.T3.T4.T5.T6表面
3.2、选材
接头的许用应力和安全系数的关系:
[σ]=σ°/n=96.67MPa~113.33MPa(极限应力σ°,n=3)脆性材料的σ°=σb。
安全系数n反映了构件的强度储备。
脆性材料的n=2~3.5或是3~9。
[σ]=290/3=96.67MPa
拉伸的强度计算:
σ=N/A≤[σ]=96.67
N=σ*Aaz
N≤[σ]*A
材料为QT500
3.3、材料特性
牌号
抗拉强度Бβ
屈服硬度Б
延伸率δ%
布氏硬度HB
N/uu2(cФ/uu2)
N/mm(kgf/mm2)
QT400-18
400
250
18
130-18
QT400-15
400
250
12
130-18
QT400-10
450
310
10
160-210
QT500-7
500
320
7
170-230
QT600-3
600
370
3
190-270
QT700-2
700
420
2
225-305
QT800-2
800
480
2
245-335
QT900-2
900
600
2
280-360
3.4、毛坯
根据零件材料确定毛坯为铸件,根据其结构形状、尺寸大小和材料性能毛坯的铸
造方法选用----低压铸造
毛坯公差等级---IT8级
球墨铸铁:
在铁水(球墨生铁)浇注前加一定量的球化剂(硅,镁)使铸铁中石
墨球化,由于碳以球状存在于铸件基体中,改善其对基体的割裂作用,球墨铸铁
的抗拉强度,屈服强度,塑性,冲击韧性大大提高,并且有耐磨,减震。
工艺性
能好,成本低等优点
因为零件要求无砂眼,所以在毛坯铸造时要注意气孔的产生
气孔原因:
1.空气夾杂在熔汤中
.2.气体的来源:
熔解时、在料管中、在模具中、离型剂
改善方法:
1.适当的慢速
2.检查流道转弯是否圆滑,截面积是否渐減
3.检查逃气道面积是否够大,是否有被阻塞,位置是否位於最后充填的地方
4.检查离型剂是否噴太多,模温是否太低
5.使用真空.
3.5、零件图的分析:
要求:
表面清晰,无毛刺,尺寸精度如上图。
表面粗糙度要求高。
3.6加工工艺路线
1.定位基准的选择
正确地选择定位基准是设计工艺过程的一向重要内容,也是保证加工精度的关键。
定位基准分为精基准和粗基准。
对于无合适定位面的零件可在毛坯上另外
专门设计或加工出定位表面,称为辅助基准。
(机械制造基础P254)
2.拟定工艺路线
<1>.确定各表面的加工方法
工件各加工表面的加工方法和加工次数是拟定工艺路线的重要内容。
主要依据零件各加工表面本身的技术要求确定,同时还要综合考虑生产类型、零件的结构形状和加工表面的尺寸、工厂现有的设备情况、工件材料性质和毛坯情况等。
各种加工方法的经济精度和粗糙度如下:
表面加工的经济精度与表面粗糙度
序号
加工方法
经济精度(IT)
表面粗糙度
Ra(um)
适用范围
1
粗铣
11~13
25~6.3
适用于淬火钢以外的各种金属
2
粗铣→半精铣
8~10
6.3~3.2
3
粗铣→半精铣→精铣
6~9
1.6~0.8
4
粗铣→半精铣→精铣→抛光
6~8
0.2~0.025
5
粗铣→半精铣→精铣→磨削
6~8
0.8~0.4
适用于淬火钢、未淬火钢
6
粗铣→半精铣→粗磨→精磨
5~7
0.4~0.1
7
粗铣→半精铣→粗磨→精磨→超精加工
5~6
0.1~0.012
8
粗铣→半精铣→精铣→精磨→研磨
5级以上
<0.1
9
粗铣→半精铣→精铣→精磨→超精磨
5级以上
<0.05
10
粗铣→半精铣→精铣→抛光
5~6
0.2~0.025
适用于有色金属
<2>加工顺序的安排
在确定了零件各表面的加工方法之后,就要安排加工的先后顺序。
零件加工顺序是否合适,对加工质量、生产率和经济性有着较大的影响。
1.机械加工顺序的安排
在安排机械加工顺序时,一般遵循先粗后精、先面后孔、先主后次、基准先行的原
则。
对于工序内容复杂的零件则视具体情况采取工序集中与分散的原则处理。
2.加工阶段的划分
对于精度和表面质量要求较高的零件,应将粗、精加工分开进行。
为此,一般将整个工艺过程划分阶段,按加工性质和作用不同,一般划分为粗加工阶段、半精加工阶段、精加工家段和光整加工阶段。
这对于保证零件加工质量、合理使用机床设备、及时发现毛坯缺陷及合理安排热处理工序等有很大好处。
3.热处理工序的安排
热处理工序主要用来改善材料的性能及消除应力。
热处理的方法、次数和在工艺路线中的位置,应根据零件材料和热处理的目的而定。
如图1-4所示为热处理工序安排图。
毛坯-------→粗加工-------→半精加工-------→精加工-------→抛光
4.合理安排辅助工序
辅助工序种类很多,主要包括检验、划线、去毛刺、清洗、平衡、退磁、防锈、包装等,根据工艺需要穿插在工序中。
3.7确定工序尺寸及其公差
工序顺序确定后,就要计算各个工序加工时所应达到的工序尺寸及其公差。
工序尺寸公差一般按经济加工精度确定,但就其性质和特点而言,一般可以归纳为两类:
1.基准重合时(定位基准或工序基准重合)工序尺寸的计算
当确定了各个工序间余量和工序所能达到的加工精度后,将余量一层层叠加在被加工表面上,计算顺序是从最后一道工序开始,由后往前推,就
可计算出每道工序的工序尺寸。
2.基准不重合时工序尺寸的计算
在零件的加工过程中为了加工和检验的方便可靠,或由于零件表面的多次加工等原因,往往不能直接采用设计基准作定位基准,会出现基准不重合的情况。
形状复杂的零件在加工过程中需要多次转换定位基准,这时工艺尺寸的计算微比较复杂,应利用尺寸链原理进行分析和计算,并对工序余量进行必要的验算(是否够切)以确定工序尺寸及其公差。
3.8确定切削用量
在单件小批生产中,各工序的切削用量一般又操作工人根据具体情况自己确定,以简化工艺文件。
在大批大量生产中则应科学地、严格地选择切学用量,以充分发挥高效率设备的潜力和作用。
切学用量的选用与下列因素关:
生产率,加工质量(主要是表面粗糙度),切削力所引起的工艺系统的弹性变形,工艺系统的振动,刀具的耐用度,机床功率等。
在综合考虑上诉因素的基础上,使背吃刀量ap,进给量f,切削速度v的乘积最大。
一般应先尽量取大ap,其次尽量取大f,最后取合适的v。
3.8机床及工艺设备的选择
(1)选择机床
选择机床和工艺装备的总原则是根据生产类型与加工要求使所选择的机床及工艺装备既能保证加工质量,又经济合理。
基于次原则本叉杆设计所选机床如下:
数控机床、铣床、钻床、磨床等(具体铣床类型及型号请看工艺卡片)。
(2)选择夹具
①粗铣、半精铣可采用压板对底面进行固定。
②红金控可以用直径10mm的铣刀直接铣出。
(3)选择量具
①粗加工、半精加工可选用通用量具。
Ⅰ大端面工序尺寸中无高公差,而查参考文献知计量器具不确定度允许值为0.012mm,故选择分度值为0.01mm的游标卡尺,其不确定度值为0.006mm,可满足要求。
Ⅱ仿形铣工序中轴向尺寸Ф32f6其上偏差为-0.025,下偏差为-0.041,查表并根据有关公式计算得,计量器具不确定度允许值为0.045mm,查参考文献选择分度值为0.02mm的游标卡尺,其不确定值可满足要求。
Ⅲ精加工工序为零件完工尺寸,精度要求高,若用通用量具,需选用比较仪、指示表,使用不便。
故宜选用专用量具。
⑴内圆测量宜采用卡规,测量时要注意从相互垂直的两个方向测量。
4、夹具设计
4.1夹具设计的目的和要求
目的
1.保证加工精度
2.提高劳动生产率
3.改善工人劳动条件
4.降低生产成本
5.扩大机床工艺范围
要求
1.保证工件的加工精度
2.提高生产效率
3.工艺性好
4.使用性好
5.经济性好
4.2夹具设计步骤
1.夹具类型的选择
根据本叉杆加工要求及其工艺性,在铣孔时所用夹具为专用夹具,故无须浪费人力、物力设计新夹具。
由于该工件生产为中批量生产,且工件体积小,结构不复杂,从经济耐用的要求考虑,本工序加工家具不适宜太复杂,自动化声度不宜太高。
故拟定选用简单的V形块定位螺旋压板夹紧机构。
2.定位装置的设计
(1)定位方案的确定
(2)定位误差分析
3.夹紧装置设计
(1)夹紧机构
根据该产品不是批量生产,因此夹具的夹紧机构不用太过复杂
,自动化程度也不能太高,采用螺旋压板夹紧机构,采用M12螺栓作为夹具夹紧螺栓。
(2)夹紧力的计算
根据理论力学的力平衡理论,夹紧摩擦力矩应与铣削力矩平衡,即M摩=M切。
铣削力矩M切的计算和夹紧力的计算
3、工件的夹紧方式,计算夹紧力并设计夹紧装置
夹紧机构应保证工件夹紧可靠.安全.不破坏工件的定位及夹压表面的精度和粗糙度。
在设计夹紧装置时必须合理选择夹紧力的方向和作用点,必要时还应进行夹紧力的估算。
(1)切削力的计算(Ca吃刀量f进给量v切削速度k修正系数)
0.750
Fz=9.81Cafvk=9.81×180×0.2×4×10×(300/190)×0.55×1.8=1561.18N
0.90.750
Fy=9.81Cafvk=9.81×94×0.2×4×10×(300/190)×1.3×1.63=1795.36N
1.20.650
Fx=9.81Cafvk=9.81×54×0.2×4×10×(300/190)×1.1×0.7=1092.82N
222
故总的切削力F=【〔Fz_+Fy+Fx〕】开平方根=2618.27N
(2)夹紧力的计算
Fwk=KM/LF(Fwk实际夹紧力,M切削力矩,L压板长度,F进给量)
=0.1×2618.27×20/50×0.2=523.65N
在确定夹紧力的大小时,为简化计算,通常将夹具和工件看成一个刚性系统。
根据工件所受切削力。
夹紧力(大型工件还应考虑重力,惯性力等)的作用情况,找出加工过程中对夹紧最不利的状态,按静力平衡原理计算出理论夹紧力,最后再乘以安全系数。
4.3夹具零件图
此叉杆夹具图形如下:
结论
经过两个月的分析零件、查阅资料、绘图、计算、等复杂的步骤,最终完成了止动块的模具设计。
在此期间本人遇到了不少的疑难问题,通过网上查询、请教师、跟同学讨论之后得到了解决问题的办法。
经过这次毕业设计,让我巩固了以前所学的知识,也为我以后的工作打下了很好的基础。
这篇毕业设计虽然已经完成了,但由于本人缺少实际经验,在实际利用中次设计肯定还存在不少的问题,需要改进。
希望老师能给我提点意见和建议。
接下来的时间本人会在公司里好好学习,以提高自己的水平,为将来的工作打下更坚实的基础。
致谢
在这里,在这本设计即将完成之际,我要感谢我们宁波摩多卡汽铣配件有限公司的领导,是他们给了我设计的空间;我还要感谢一直帮助我的杨伟超、廖飞军两位导师,他们在我的设计中给了我很多的指导,在一些对我来说比较艰深,比较把握不了方向的地方,给予了我指明,帮我除去了许多不必要的麻烦;在此我还要感谢我们公司技术课的同仁,是他们不遗余力的帮助,才使我有充足的时间来完成本设计,谢谢,谢谢你们,因为有你们才有本设计的实现,谢谢!
!
!
参考文献
[1]、吴兆祥,《机械制造技术课程设计》,浙江大学出版社,2005.1
[2]、蒋建强,《数控加工技术与实训》,北京:
电子工业出版社,2003.8
[3]、李启炎,《计算机绘图(初级)AUTOCAD2004版》,同济大学出版社,2004.7
[4]、夏凤芳,《数控机床》,高等教育出版社,2002.7
[5]、廖兆荣,《数控几双电气控制》,高等教育出版社,2005.1
[6]、《机械工程手册》工程材料,1996年第二版
[7]、成大先,《机械设计手册》北京:
机械工业出版社
[8]、甘永立,《几何量公差与检测》上海:
上海科学技术出版社,1993