炼钢厂技术操作规程全.docx
《炼钢厂技术操作规程全.docx》由会员分享,可在线阅读,更多相关《炼钢厂技术操作规程全.docx(59页珍藏版)》请在冰豆网上搜索。
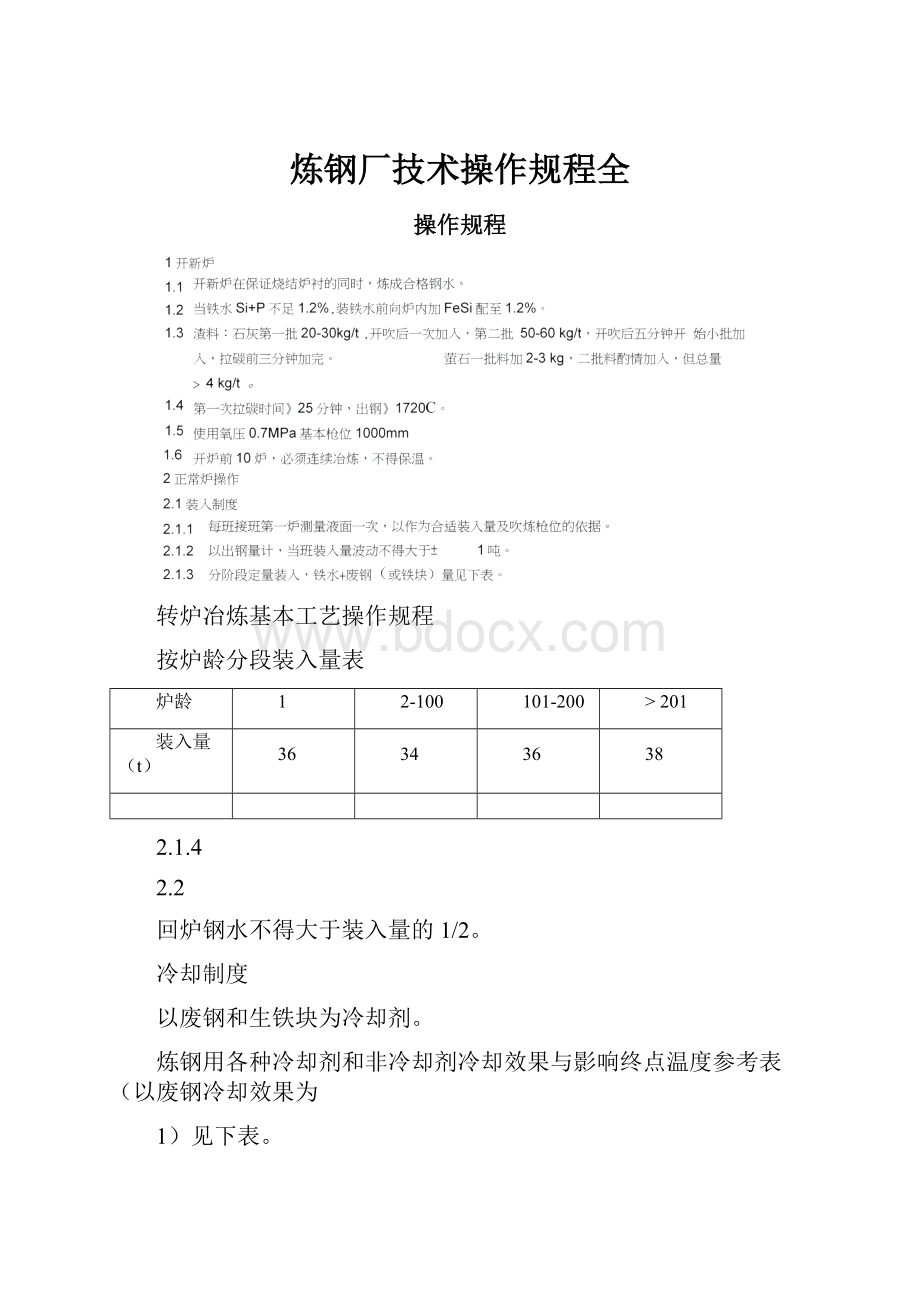
炼钢厂技术操作规程全
操作规程
转炉冶炼基本工艺操作规程
按炉龄分段装入量表
炉龄
1
2-100
101-200
>201
装入量(t)
36
34
36
38
2.1.4
2.2
回炉钢水不得大于装入量的1/2。
冷却制度
以废钢和生铁块为冷却剂。
炼钢用各种冷却剂和非冷却剂冷却效果与影响终点温度参考表(以废钢冷却效果为
1)见下表。
冷却剂和非冷却剂的冷却效果参考表
冷却剂
废钢
石灰
铁皮
铁块
白云石
冷却效果
1
1
3
0.5
1.5
每炉加100kg影响
终点温度「C)
4-5
4-5
12-15
2-2.5
6-7.5
2.3
2.3.1
供氧制度
采用分期定压、恒压变枪位操作。
氧压低于0.4MPa不得吹炼。
炉龄
1
2-50
>50
氧压(MPa)
0.7
0.9-1.0
1.0-1.1
各阶段氧压参考表
枪位控制
基本枪位900-1100mm波动枪位800-1200mm枪位调整要做到勤动少动。
正常情况应控制〉200mm次。
以基本枪位为主要吹炼枪位,为迅速成渣,在开始吹炼时或炉渣返干时允许适当提高枪位。
严禁过高枪位操作。
冶炼末期要采取低枪位操作,时间最少不少于60秒。
2.3.3采用三孔喷头吹炼,喷头参数©27X3-11,氧枪漏水时应及时换枪。
2.4造渣制度
要求吹炼全程化渣
2.4.1除后吹炉次外,均采用留渣操作工艺。
即出完钢后,先向炉内加入石灰、白云石混合物,稠化炉渣,后吹炉次必须倒净炉渣,不得先加石灰,后倒渣。
2.4.2铁水Si>0.8%寸应采用双渣操作。
炼钢用废钢、生铁要求和石灰、白云石、萤石、氧化铁皮技术要求另见原材料标准。
2.4.3散状料加入量
2.4.3.1石灰加入量=〖2.2(Si+P)%R〗/CaO%效】X1000kg/t铁终渣碱度R:
普通钢2.8-3.5,优质钢3.5-4.0,
R=CaO/(SiO2+P2O),CaO%效=石灰CaO%RX石灰S©%
萤石加入量〉2kg/t钢,补炉后第一炉〉3kg/t钢。
硬线钢〉4kg/t钢。
视铁水温度和化渣需要适量使用铁皮和白云石。
终渣MgO7-11%。
终渣FeO含量W18%
渣料加入方式:
头批渣料在开吹时加入,为总量的1/2-1/3,以后每次少量加入,提倡多批少量,应在拉碳前3分钟加完,在非正常炉次,需在末期加入冷却剂或造渣剂调整时,应经过补吹或点吹方可作为终点。
2.5终点控制及出钢
要求合理控制过程温度,化好过程渣,提高终点命中率,使钢水的成分、温度同时达到终点。
2.5.1终点温度:
吹炼终点必须测温。
2.3.2
2.4.3.2
2.4.3.3
2.4.3.4
2.4.3.5
5.4.4
终点温度控制表
钢种
第一包
连浇炉次
普碳钢
1700r-1720C
1660r-1690r
低合金钢
1720r-1740r
1680r-1710r
2.5.2终点成分:
普碳钢、低合金钢
C>0.08%,S>0.040%,P>0.025%(普碳钢),P>0.020%(低合金钢)
2.5.3严重后吹炉次,出钢前炉内需加铁块预脱氧。
2.5.4转炉实行挡渣出钢,挡渣球比重3.2-3.5克/厘米3,出钢1/2-2/3时,投入炉内出钢口附近;钢包钢水必须加保温剂保温。
2.5.5实行红包出钢,出钢前检查钢包,不使用带渣盖钢包,以防托浮合金料。
2.5.6钢包内钢水在含碳量偏低时,允许普碳钢及低合金钢加碳化硅(低品位)增碳,加入量应V1.5kg/t钢。
2.5.7禁止出钢过程下渣,出钢时间V1.5分钟时须修补或更换出钢口。
2.5.8冶炼其它品种钢时,执行《分钢种规程》。
以上或其它钢种如有新规程时,执行新规程。
2.6
2.6.1
脱氧合金化
合金加入量(kg/炉)
=〖(成品成分中限一钢中残余成分)/(合金元素含量X吸收率)〗x1000X钢水量普碳镇静钢吸收率:
FeMn85-95%;FeSi70-80%。
2.6.2
2.6.3
;硅铝铁的加入量:
普碳镇静钢0.4-0.8kg/t,根据钢水氧化性酌情调整。
丨合金料加入时间及顺序
出钢1/4后开始加合金料,顺序为FeMn^FeSi-FeAISi(由弱到强),出钢至3/4时合金料加完,严禁预先加入包底。
-冶炼普碳钢时,CaSi加入量0.5-1.0kg/t钢。
.冶炼其它品种钢时,按《分钢种规程》执行。
钢包精炼制度
普碳钢必须取样观察脱氧情况,包内允许加合金微调成分:
普碳钢W2kg/t钢,低合金钢W4kg/t钢,应尽量采用喂丝微调成分。
2.7.2炉炉测包温,吹氩后包温控制见下表
钢种
第一包
连浇炉次
普碳钢
1640r-1660r
1610r-1640r
低合金钢
1640r-1660r
1610r-1640r
包温高时,包内可加同钢种废钢或同钢种浇余微调至控制范围。
2.7.3镇静钢必须吹氩处理。
顶吹氩压力0.17-0.22MPa;吹氩枪插入深度:
枪头距包底
200-250mm吹氩时间:
普碳钢镇静钢》1.5分钟,低合金钢》2分钟,底吹氩按底吹氩规程执行。
2.7.4若需微调成分和温度,先进行微调处理,而后吹氩处理,吹氩时间应延长30秒,吹氩处理后,不得进行成分、温度微调。
2.7.5其它品种钢按《分钢种规程》执行,如由新规程执行新规程。
2.8补炉
2.8.1炉容量达33吨时开始补炉(可根侵蚀情况提前或退后),根据侵蚀情况决定补炉具体时间、次数和补炉位置。
2.8.2采取铁水、浇余助烧结。
烧结时间:
补大面60分钟,补小面及贴喷补70分钟,补炉底70分钟。
老炉阶段根据炉衬侵蚀情况及时补炉。
煤气回收操作
新炉前10炉、贴补炉第1炉、停吹3小时第1炉及浇余》10吨不回收煤气。
正常炉次开吹3分钟降罩,第4分钟开始回收,回收时间7分钟。
i氧压V0.75MPa降罩开始及回收时间延长1分钟,及时调整喉口开度,保证煤气质量。
氧压V0.6MPa不得回收。
2.9.4铁水[Si]>0.80%或[S]>0.070%时,降罩与回收时间延长1分钟。
2.9.5回收时保证炉口微正压。
转炉炉衬砖修砌要点
1.保护砖修砌
1.1保护砖必须竖砌、靠实挤严,砖后要灌泥浆。
1.2熔池修砌两圈镁碳保护砖。
1.3熔池以上余下部位修砌小镁砖。
2.炉衬修砌
2.1高档砖由第四层起砌至炉内上卡板,合计38层,出钢口部位砌宽20块,高13层高档砖。
2.2出钢口部位的高档砖必须层层打胶泥。
2.3杈豁必须打胶泥,在大面部位杈豁,搂砖不许>40mm即背后只能加一块40板的厚度)。
3.接底泥料卤水加入量适当,接好销钉、销板后,落炉底车,在炉底下东南、东北二点垫销子板,再顶炉底车,将销子板打实。
4.销子打实后,炉内炉底接缝应砌好保护砖。
5.摇炉后要重新打实各销子板(打第二遍),然后将销子板与销钉点焊牢固。
1.中间包的修砌与准备
1.1中间包修砌
1.1.1
炼钢厂连铸基本工艺技术规程
中间包包衬由永久层、填充层、工作层组成。
1.1.2
1.1.3
中间包永久层为浇注料浇注成型,脱胎后要根据浇注料要求进行烘烤。
装水口座砖:
装座砖时中间包放置于水口对中台架上,中间包内外的残钢残渣,将别是方眼和包底水口处的粘钢必须清理干净,座砖要放平、放正,保证水口位置偏差小于5mm同时保证水口砖下端面突出包底大于10mm然后四周用专用泥料夯实。
1.1.4修砌工作层(绝热板)
⑴砌绝热板时,先砌底板,后砌壁板。
底板从水口座砖处开始修砌,以保证绝热板水口孔与座砖对中。
壁板从冲击区开始修砌,三期连铸还要注意将挡墙夹紧。
⑵装板时先在板子接缝处均匀抹好胶泥,装好后板缝V2mm用胶泥抹好所有接缝并用
©12mn〜©16mm圆钢支撑,或用卡子卡牢,不得有扭曲,然后用专用填砂将绝热板与永久层间填实。
最后将中间包内清扫干净。
1.2中间包准备
1.2.1安装上水口砖
1.2.1.1安装上水口砖前,将中间包内及座砖孔内垃圾清除干净。
1.2.1.2安装上水口砖时,座砖孔与上水口砖周围应均匀带泥,旋转放入,做到平、正、紧,且突出包底大于10mm然后清除多余泥浆。
1.2.2
清除包盖上的残渣、残钢,包盖严重变形者要更换。
吊放中间包盖要平稳,严禁撞击塞杆。
包盖必须盖正,位置偏差〉20mm
盖中间包包盖
1.2.2.1
1.2.2.2
1.2.2.3
1.2.3
中间包车升至烘烤位置,将上下烧嘴分别与中间包盖孔及水口对准。
先点水口烘烤器(小烧嘴),听通知点燃大烧嘴,大烧嘴烘烤时间30〜60min。
中间包烘烤完毕停火到开浇时间〉5min。
烘烤所用转炉煤气CO45%小于45%寸,要适当延长烘烤时间。
中间包烘烤。
1.2.3.1
1.2.3.2
1.2.3.3
1.2.3.4
2.开浇准备
2.1认真检查所属设备,正常后方准送引锭,同时检查风、水、电、氧、乙炔、液压等动力源符合工艺要求,各项必备工具和辅料准备就绪。
2.1.1开通结晶器冷却水,确认符合下列技术条件:
水量90〜110m3/h,水压0.4〜0.6MPa,
进水温度W40C。
开通结晶器冷却水,各水咀正常喷水,无缺、堵现象,水条对中,发现问题及时处理。
结晶器内腔表面光洁,无划痕及损伤,不得有渗漏现象。
凡连续两次发生裂纹漏钢或连续两炉铸坯有裂纹、菱变缺陷的结晶器必须更换。
结晶器振动应平稳无摆动,振幅和频率符合工艺要求。
对振动参数有特殊要求的钢种
执行分钢种操作规程。
2.1.6冷却水的水位应处于正常状态,事故水塔要保证发生停电停水事故时结晶器供水压力<0.2MPa,且不间断供水15min以上。
2.2送引锭
2.2.1引锭头应清洁干燥,不得潮湿或粘有废钢。
2.2.2送引锭前,二操工要认真检查所属机械、电气及液压设备正常,拉矫辊升降自如,剪机工作正常。
然后,同一操工取得联系,将铸机状态选择开放拨至“送引锭”位置。
2.2.3送引锭时,先提升拉矫辊至最大开口度,并把拉矫液压缸压力切换到送引锭状态。
2.2.4将引锭杆用升降装置送至拉矫机后,防下拉矫辊,启动拉矫机。
引锭头进入二冷室后,出浇钢工安装引锭钩头,以0.6m/min的速度点动进入结晶器内200mn后,再向下拉至距下口80mn位置,然后,再向上送至距离结晶器下口200mm
2.2.5送引锭时,操作人员应随时注意引锭杆的运动有无阻碍,要随时准备停止引锭杆行走,保证设备安全。
2.2.6浇钢工用石棉绳塞好引锭头与结晶器壁之间的缝隙,并在引锭头四周撒上适量的铁屑(铁屑厚度以15〜20mm为宜),最后放入适量冷钢。
2.2.7引锭头塞好后盖好结晶器上口,以防异物落入。
拉矫机、振动电机断电,开浇前浇钢工应检查引锭是否下滑,如果引锭下滑,需重新送引锭。
3.连铸对钢水的基本要求
3.1钢水成分符合相关标准及作业文件要求,脱氧正常,流动性良好。
连浇炉次必须为同钢种,浇钢过程中严禁向钢包内和中间包内追加合金料调成分。
3.2连铸钢水到平台温度要求执行分钢种操作规程。
4.中间包浇注
4.1钢包吊上座架(或回转台并转到浇钢位置)后无异常,中间包停止烘烤并迅速开到浇钢位置,将中间包水口与结晶器对中。
4.2中包液面上升到80mm时开始起步,正常情况下,中间包开浇到起步的时间(出苗时间)
及起步拉速参考下表:
铸坯断面(m2)
165X280
165X225
150X150
起步时间(S)
30
45
30
起步拉速(m/min)
0.5
0.6
0.8
遇钢水温度过高或过低时,应适当延长或缩短起步时间。
起步的同时开始加和保护渣,保护渣应均匀覆盖液面,勤加少加,以液面不亮为准,渣条长大时及时捞出。
起步正常后,将中包降下,控制水口浸入深度为50〜80mm。
中间包开浇前由机长通知一操工,一操通知配水人员,各方面确认后方可开浇。
中间包采用带长水口开浇(钢水温度偏低时,可先开浇后上长水口)。
要保证长水口垂直且对中,长水口在使用前应放在中间包盖下预热不少于半小时。
中间包液面达到200mn左右,加入中包覆盖剂。
中间包液面达到400mm后,进行测温并开浇。
正常温度或偏下限温度应大流开浇,钢水温度较高时,大包可直接用中小流开浇,不得断流。
当引锭头拉到脱引锭位置时,将脱头辊压下,引锭头与铸坯脱离,然后立即将拉矫辊压力调整到正常拉坯压力。
正常浇注过程中,钢包开浇5min时测量一次中间包钢水温度,以后间隔10〜15min测量一次,一操工做好时间与温度记录。
浇注过程中钢包或中间包不得调温。
4.10浇注过程中结晶器液面控制在距上口50mn以下,禁止液面超高。
4.11一般情况下,一个中间包只允许浇注同一钢种,不同钢种连浇必须更换中间包。
如有特殊试验钢,同一中间包需浇注不同钢种时,须有公司技术主管部门出具的质量计划。
4.12更换中间包时需将结晶器内残余保护渣捞净,并迅速插入吊攀。
中间包停浇至大包开浇的时间间隔不得超过10min。
4.13操作过程中应尽量稳定拉速,拉速控制执行分钢种操作要点。
5.主控室操作
5.1从第一包钢水上连铸平台至浇钢结束,应准确做好原始记录,发生事故应将时间、原因、现象、后果等情况如实填写,字迹应工整,不得有涂改。
5.2每次钢包开浇,立即将炉号通知三操工。
6.配水操作
6.1
4.3
4.4
4.5
4.6
4.7
4.8
4.9
6.2
6.3
6.4
6.5
6.6
6.7
开浇前检查所属设备,仪表、各进出水阀门工作是否正常,检查各水、气管路有无漏水、漏气现象,并作相应处理。
检查结晶器、二冷段冷却水量、压力、温度是否正常,检查二冷水条、喷嘴、过滤器等,若发现脱落堵塞等,必须及时处理。
结晶器进水总管压力0.4〜0.6MPa
钢包开浇前10min必须打开结晶器冷却水,确认供水符合技术要求后,方可开浇。
开浇后,随钢坯移动逐段打开冷却水,配水由计算机自动进行。
配水量的控制应保证铸坯在二冷段均匀降温,使矫直温度控制在900〜1000r
使用自动配水时,若连续出现坯温异常,必须查明原因,并切换为手动调节二冷水量。
浇注中遇突然停车或更换中间包时,要及时关闭二冷水及拉矫机喷淋水,待起步后再逐
段开启。
6.8浇注结束后延时15min关结晶器冷却水,铸坯通过后,适时关闭各流各段二冷区冷却水。
6.9生产时设备冷却水应不喷到铸坯表面。
不得随意停设备冷却水,并且保证冷却水压力不小于0.4MPa停浇后,红坯离线15min后,每天更换一次各分支过滤网。
6.10每周必须清理或更换一次总管过滤网,每天更换一次各分支过滤网。
7.拉矫剪切操作
7.1
7.2
7.3
7.4
7.5
7.6
7.7
7.8
送引锭前,检查所属机械、液压、电气、仪表等设备是否正常。
检查定尺装置,保证定尺精度。
引锭头光滑无凸出、耳刺,钩槽边部最薄部位不小于15mm检查引锭节各销钉无凸出,
引锭杆不得有严重下弯。
开浇后,当引锭头拉到脱引锭位置时,将压辊压下,使引锭头与铸坯脱离,此时将拉矫机切换到正常拉坯压力。
铸坯表面温度低于750r时,不得使用液压剪切机剪切。
正常拉坯过程中连铸机拉矫辊压力要求2.0〜2.7MPa泵出口压力3.0〜3.5MPa在送引锭或拉“换中间包衔接坯”时,拉矫机各辊压力可按上值提高0.8MPa控制,在红坯进入拉矫机后应立即恢复到正常压力。
液压站操作工在交接班以后每隔2小时检查一次拉矫辊压力并做好记录。
火焰切割机正常工作参数如下:
(单位MPa)
咼压风
冷却水
氧气
丙烷气
0.45〜0.6
0.4〜0.6
1.2〜1.4
0.08〜0.12
切割枪点火、熄火操作详见设备操作规程。
7.9
开浇后剪头坯不小于500mm尾坯不小于1m至缩孔切净为止。
7.10浇注结束,当尾坯离开拉矫机后,停机并将拉矫机上辊抬起,拉矫机操作结束。
8.冷床控制操作
8.1
8.2
8.3
开浇前,检查所属机械、电气、仪表等设备应正常。
生产过程中操作工应密切注意钢坯运行情况,发现问题及时通知有关人员进行处理。
当主控室通知换炉号以后,上、下炉铸坯应严格分开,并按规定点好混坯。
钢包吹氩工艺操作要点
1.
2.
出钢后,吹氩前,钢水在钢包内要静置镇静玄1-2分钟,使钢包充分吸热。
吹氩时间:
2-3分钟(不少于2分钟,使钢水充分搅拌均匀
吹氩压力:
要保证钢包内钢水液面有波动,但不翻腾,不得裸露钢水液面,
(防止钢
4.
5.
6.
7.
水二次氧化)。
若吹氩时加废钢调温,应将吹氩时间延长1-2分钟;若吹氩后加废钢调温,应再补
吹氩不少于3分钟,(以使废钢充分熔化和均温)。
吹氩后,迅速覆盖碳化稻壳或钢包覆盖剂保温。
调温废钢尺寸:
(①20-①30)X500或165X225X(>100),约28kg/块。
调温废钢应洁净、干燥、无油污、无孔洞,不得有密闭的中空容器或可爆炸物。
废钢应有专人准备,并堆放于指定位置,便于调温使用。
一般不允许在连铸平台向大包内吊入废钢调温,严格禁止向大包吊入尾坯调温。
S08钢冶炼操作要点(试行)
1.化学成分控制
2.终点控制及配料方案
2.1
2.2
化学成分控制目标:
C
Mn
S
P
Si
<0.08%
0.20〜0.35%
<0.035%
<0.035%
0.10〜0.20%
终点碳W0.06%,控制目标:
0.04〜0.06%。
当终点碳》0.05%时,不允许加碳化硅;用硅锰合金配锰,加入量按5kg/1钢左右控制;当
Si不足时,用Si-Fe找齐,加入量按1.5kg/t钢左右控制。
2.3
3.事宜执行普碳钢工艺技术规程。
用脱氧剂和Si-AI-Ba-Ca做好脱氧。
HRB400技术操作规程
1.化学成份(%)
C
Mn
S<
P<
Si
V
0.17〜0.25
1.2〜1.6
0.045
0.045
0.2〜0.8
0.04〜0.12
2.转炉冶炼
2.1转炉前十炉,补炉后第一炉不得冶炼该钢种。
2.2终点控制
2.2.1终点成分控制
O0.06%;S<0.025%;P<0.020%.
2.2.2终点温度控制
第一包:
1690〜1740r;连铸炉次:
1650〜17000
2.3脱氧及合金化
2.3.1脱氧剂加入量》1.0kg/t钢。
2.3.2用MnSi合金配锰,用FeSi和SiC配硅,碳不足时用碳剂补齐。
2.3.3钒铁加入参考量:
0.7〜0.8kk/t钢。
2.4连铸平台温度控制
第一包:
1650〜16800;连浇炉次:
1610〜16300
3.连铸
3.1浇铸165X225伽方坯,合格铸坯头部涂白色。
3.2采用低合金保护渣,拉速控制参照低合金钢。
3.3配水同低合金钢。
4.未尽事宜执行基本工艺技术规程。
硅钢(10Si2Mn)操作要点(暂行)
1.化学成分
C
Mn
S
P
Si
V
<0.10
0.25-0.50
<0.045
<0.045
1.00-1.50
0.02-0.05
2.4
2.5Si不足部分用低铝硅铁按1.3%补足,参考量:
22kg/t钢。
2.6出钢后吹氩时间》2.5min。
2.7挡渣出钢。
3.连铸
3.1老包及小修包不得使用,尽可能红包出钢。
3.2包温控制
浇钢操作基本工艺规程
1钢包包衬的浇注成型工艺操作
1.1钢包包衬的修砌与浇注成型
1.1.1包底永久层的砌筑:
将包壳内的钢、渣及其它杂物清除干净后,用打结料打结包底,并以法兰为准找平(50mm厚),然后砌一层二等高铝标准砖。
1.1.2
1.1.3
1.1.4
砌包底砖用泥料:
采用1#泥料。
包壁永久层的砌筑:
沿包壁砌一圈A9粘土砖。
砌包壁砖用泥料:
镁砂+(9-11%)卤水,和成粘稠状。
1.1.5
1.1.6
打包底前将座砖摆正。
工作层的浇注成型:
采用铝-镁浇注料浇注成型,先浇注包底,而后浇注包壁。
1)包底用料3.5吨(厚350mm)分两次打结。
2)号在包壁永久层上贴硅酸铝纤维毡(8mm厚);浇注胎具安放在与钢包同心位置;当头批料浇至300mn高时,启动振动器,至浇到帽口后继续振动5分钟。
3)调和工作层浇注打结料时,一定要按配料的比例投料,使用搅拌机混料,每2.6吨混
合料为一批,搅拌时间》5分钟,包衬铝镁料配比如下表:
名称
高铝骨料
高铝细粉
镁粉
水玻璃
水
比例%
60
28
12
5-7
10-15
※水玻璃模数>2.4
1.1.7脱胎与养护
1)浇注好的钢包内衬,在自然干燥12小时后,包衬材料有一定强度方可脱出胎具。
脱胎时,要将模具吊正,切忌斜拉猛吊。
脱模后要对损坏的地方进行修补。
2)脱胎后的钢包静置24小时后方可进行烘烤。
烘烤要求如下:
前期低温烘烤(<400C)8小时,中期中温烘烤(400-800C)8小时,后期高温烘烤(>800C)24小时。
2.浇钢前准备
2.1钢包准备
2.1.1钢包使用前应认真检查包衬侵蚀情况和滑动机构有无损坏,侵蚀严重或有损坏时要停止使用或修复后再投入使用。
使用粘钢钢包应事先通知炼钢工,由炼钢工决定是否使用。
包内渣子清净,渣盖捅掉,保持包内清洁。
按要求加引流剂,摆包时严禁滑动机构、连杆与钢包车碰撞。
优质钢与特殊钢对钢包的要求按《分钢种操作要点》执行。
安装滑动水口工艺操作
选砖:
凡不符合标准(外形、尺寸等)的砖均不得使用,滑板间隙大、滑板、水口有裂
纹或残缺禁用。
2.2.2下滑板与下水口用磷酸火泥预装,烘烤》24小时方能使用。
2.2.3安装前,将上滑板槽内,上水口内及上水口接口处,滑盒内的残渣、残钢、残泥清理干净。
2.2.4上水口砖一定要装平,确保水口眼在正中央;上滑板上正,上水口与上滑板泥缝W2mm上滑板应高出安装板6-9mm清理干净残泥,新包、凉包将泥料烘烤后使用。
2.2.5水口使用:
上、下水口,上、下滑板均使用①50mmi勺型号。
2.3FLK滑动机构的使用
2.3.1上、下滑板工作面涂抹润滑油后,立即关门,再同时用力锁紧左右肘关节。
2.3.2接上油缸试滑动,从侧面观察上、下滑板接触是否良好。
如发现缝隙必须打开重装,并检查上、下滑板的两孔是否同心。
2.3.3弹簧使用前必须进行检查,起其高度在63.0-63.5mm,检测压力>5Mpa为合格品。
2.3.4
大包浇钢工艺操作
钢包到达连铸平台3分钟内必须测量钢水温度,温度符合工艺要求者方可浇注,若一次测温不合格,在补测1-2次确认,以三次中两次接近的温度为准。
钢包未使用引流剂