熔炼系统冶金计算相关知识.docx
《熔炼系统冶金计算相关知识.docx》由会员分享,可在线阅读,更多相关《熔炼系统冶金计算相关知识.docx(25页珍藏版)》请在冰豆网上搜索。
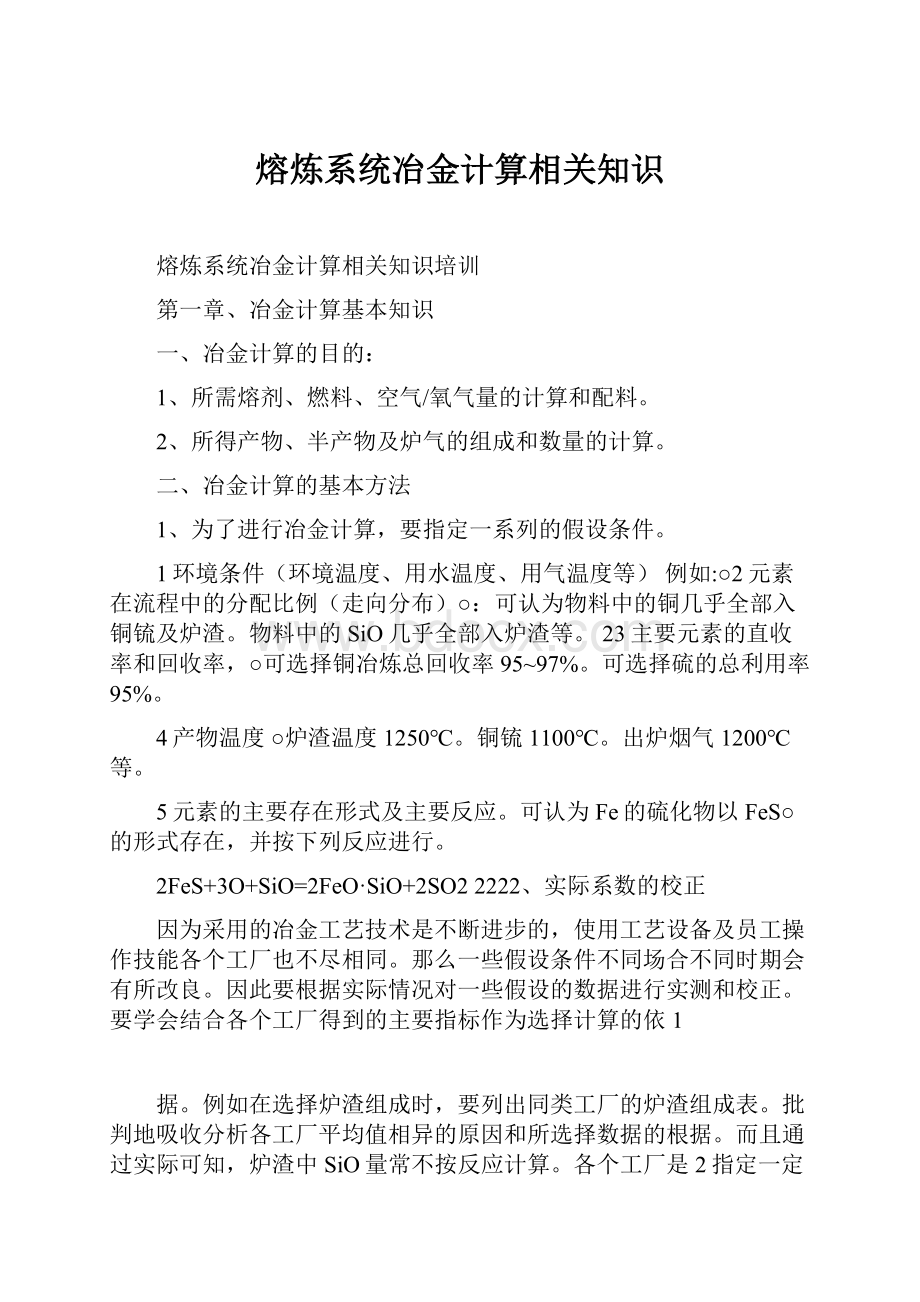
熔炼系统冶金计算相关知识
熔炼系统冶金计算相关知识培训
第一章、冶金计算基本知识
一、冶金计算的目的:
1、所需熔剂、燃料、空气/氧气量的计算和配料。
2、所得产物、半产物及炉气的组成和数量的计算。
二、冶金计算的基本方法
1、为了进行冶金计算,要指定一系列的假设条件。
1环境条件(环境温度、用水温度、用气温度等)例如:
○2元素在流程中的分配比例(走向分布)○:
可认为物料中的铜几乎全部入铜锍及炉渣。
物料中的SiO几乎全部入炉渣等。
23主要元素的直收率和回收率,○可选择铜冶炼总回收率95~97%。
可选择硫的总利用率95%。
4产物温度○炉渣温度1250℃。
铜锍1100℃。
出炉烟气1200℃等。
5元素的主要存在形式及主要反应。
可认为Fe的硫化物以FeS○的形式存在,并按下列反应进行。
2FeS+3O+SiO=2FeO·SiO+2SO22222、实际系数的校正
因为采用的冶金工艺技术是不断进步的,使用工艺设备及员工操作技能各个工厂也不尽相同。
那么一些假设条件不同场合不同时期会有所改良。
因此要根据实际情况对一些假设的数据进行实测和校正。
要学会结合各个工厂得到的主要指标作为选择计算的依1
据。
例如在选择炉渣组成时,要列出同类工厂的炉渣组成表。
批判地吸收分析各工厂平均值相异的原因和所选择数据的根据。
而且通过实际可知,炉渣中SiO量常不按反应计算。
各个工厂是2指定一定的炉渣组成并加以实际校正:
在富氧熔炼体系,入炉物料中铁一部分以FeS的形式入锍相,一部分以2FeO·SiO形式2造渣(此时Fe/SiO大约1.7)。
另一部分以FeO形式存在于冰423铜和渣中,而这些分布随不同的反应条件而变化,也要根据实际检测加以整理、分析和校正。
3、绘制物料处理流程图
在着手进行任何一种冶金计算时,首先必须确定所处理的是一些什么物料。
应该进行哪些过程。
所要进行的工序将得到哪些产物。
4、物料平衡计算
计算进入该过程的全部物料(加入)及产出的全部产物、半成品(产出)的重量之和。
不仅是按物料类别,而且还要按主要组成(Cu、Fe、S、SiO等)来进行。
25、热平衡计算
热平衡是计算该过程中全部热收入(燃料燃烧、放热反应、各种物料的显热等)和全部热支出(吸热反应、产物带走热、炉子散热等)。
其目地是为了验算热的支出和更深入的分析过程,以发现热量损失的主要原因和使用或节省燃料的可能性和有效途径。
同时可考虑余热回收的实效性。
6、选定计算的基准
2
物料平衡计算一般按100Kg或100t混合精矿(或入炉物料)进行;也有的按100Kg或100t最终产品进行。
热平衡一般按每小时该过程的热量支出和收入。
单位一般为MJ/h(或GJ/h).
第二章、混合精矿的初(粗)配
一、混合精矿的粗配是根据生产调度给定的抓配单,将各库存铜精矿,自产渣精矿或搭配金精矿按一定的抓斗数比例在堆配仓内进行抓配而成。
有的冶炼厂一般一次堆配料保证一天的处理量(1000t左右)。
以尽量保证一天的操作不发生大的波动。
当然,如果原料充足,配矿不复杂多变,场地不受限制,也可以加大堆配量。
二、选择的冶金工艺不同,处理的精矿性质亦有所差异(即对原料的适应性不同)。
我们选择富氧底吹造锍捕金新工艺,加之逐步完善的收砷技术,可处理含砷相对较高的混合铜精矿。
混合矿含砷试验已做到2.2%,同时含铜可低到7.5%.(这样会影响Cu、Au、Ag的回收率),实际中应根据各种情况,以效益优先的原则尽量提高混合矿含铜品位。
混合铜精矿一般要求如下:
Cu/S≤1、Fe+S≥50%As≤2.2%
3.1.6~1.8g/cm由于铜精矿与金精矿的堆积密度差别较大,前者三、3.所以g/cm而金精矿的堆积密度随品位变化较大,高的可达3.0
在进行抓配时要特别注意,灵活掌握。
而且要经常性的测量并掌握各种不同物料的堆积密度。
四、每堆料要求至少抓配三次以上,首先是按一定顺序和抓斗比3
抓料堆放。
抓完后进行两次翻料,要求堆配料无明显分层且颜色均匀。
每批料根据要求抓配完成,经值班领导检查认可后,应马上取样送快速分析Cu、Fe、S、SiO、As、Pb、Zn、CaO、MgO2和测定水分,便于及时调整和进行下一道工序配料计算。
第三章、冶金计算实例
一、处理物料组成(%)
1、混合精矿组成
CuFeSSiOAsPb
Zn
CaO+MgO其它23.5
9.5
6.5
28
18
2.2
32
1.121.56
2、熔剂(石英石)组成SiO(90)Fe(3.5)2二、产物成份的假定(%)
1、铜锍组成选择
CuFeSO其它22.8
18.2
22.6
55
1.4
2、熔炼炉渣的选择
假定炉渣温度是1250℃,选择渣相(2FeO·SiO)的2Fe/SiO=1.7。
此时各冶炼厂渣含SiO.一般20~26%,计算时选2222%(参照国外诺兰达炉实测数据),那么以2FeO·SiO存在的2Fe约38%。
另可设入炉物料中Fe有25%~30%变为FeO入炉渣43(少许铜锍)。
此时炉渣中30%~40%的Fe以FeO形式存在。
43三、系统物料处理流程图
氧气空气混合炉料
4
富氧底吹
铜锍炉渣烟气
(吹炼)(选矿)余热锅炉
锅炉烟尘
电收尘
电尘灰
骤冷塔
布袋收砷器
砷尘
高温风机
四、配料计算(制酸)
1、以100kg混合精矿为计算基准
2、假设条件:
假设入炉物料中的铜全部入铜锍和炉渣,物料
的SiO全入渣,物料中的铁亦全入铜锍和炉渣。
23、设加石英石xKg、产铜锍yKg
1、入炉物料含Cu:
18那么:
○入炉物料含Fe:
28
入炉物料含SiO:
6.5+0.9x
2:
2、铜锍含Cu:
0.55yFe:
0.182y○炉渣含SiO:
22%Fe:
38%(与SiO造渣的22Fe)
3铜平衡○5
炉渣产量:
(6.5+0.9x)÷22%
入渣铜量(6.5+0.9x)÷22%×3.5%(假设炉渣含铜3.5%)
由于入炉物料含Cu(18)等于铜锍含量(0.55y)加上入渣铜量那么
118=0.55y+(6.5+0.9x)÷22%×3.5%-------○4Fe/SiO=1.7关系○2设25%入炉Fe以FeO的形式存在,那么75%的入炉43铁进入铜锍和造渣,即
入渣(2FeO·SiO)铁:
28×75%-0.182y2入渣SiO6.5+0.9x
22显然有(28×75%-0.182y)/(6.5+0.9x)=1.7-------○解这两个方程式得:
x=2.5kgY=30kg
即处理100kg精矿,需加石英石2.5kg。
同时产铜锍30kg
产炉渣:
(6.5+0.9×2.5)÷22%=40kg
FeO总含量:
28×25%×232/168=9.7kg
43冰铜中FeO量:
43假设冰铜中的O(1.4%)以FeO形式存在,那么冰铜中FeO44332含量:
30×1.4×232/64=1.52kg
那么进入渣中的FeO9.70-1.52=8.18kg43
渣中FeO含量:
8.18/40×100%=20.45%43炉渣组成(%)
SOFeCu
Fe
SiO其它CaO+MgO4326
5.8
8.752220.451.53.538
开炉料单4
物料名称混合精矿
比例100
Cu18
Fe28
S32
OSiAs26.52.2
Pb1.12
Zn1.561.561.52
石英混合料
2.5102.5
0.08751828.0875
32
2.258.752.2
1.12
2.15
8.54
%
17.56
1.1
31.2227.4
其10.620.1510.7710.51
烟尘计算五、元素在冶炼产物中的分配比例如As、Pb、Zn1、假设物料中的)下:
(%
物料名称3Nm其它名称100
18
28
32
6.5
2.2
1.12
1.56
10.62
混合矿
2.50.08752.30.15
石英石
102.51828.0875328.82.21.121.5610.77
加入合计炉渣带走热
8260q
Zn6705480
Pb7450
570Q
As878522430100
136铜锍1367炉渣27
74
烟尘3.00
33.20
24.40
2.60
36.80
%配料量炉体散热q
74%=0.83kg1.12×、进入烟尘中的2Pb:
85%=1.87kg
2.20×As:
1.025kg
1%)即、锅炉尘(锅炉尘率取入炉混合料的35%=0.05125kg
×Pb:
1.025含3.5%=0.036kg
×:
1.025As0.83-0.05125=0.778kgPb:
含4、电尘:
40=1.94kg
0.778÷电尘灰量:
6%=0.116kg
×As量:
1.94电尘含As64.18%折合成)85%.OAs、布袋尘:
5(含321.87-0.036-0.116=1.717kg
As进入布袋尘量:
7
布袋灰尘量:
1.717÷64.18%=2.68kg
6、总烟尘量:
1.025+1.94+2.68=5.645kg
7、烟尘率:
5.645/102.5×100%=5.5%
8、返尘率(返熔炼系统):
(1.025+1.94)/102.5×100%=2.9%
9、AsO尘率:
5.5%-2.9%=2.6%
32六、氧料比计算
底吹炉下料是混合料,氧料比指每吨入炉料所需氧气量。
那么计算基准可取100kg入炉混合料
1、产铜锍30÷102.5×100=29.27kg
铜锍含S量:
29.27×22.6%=6.215kg
含铁量:
29.27×18.2%=5.327kg
应脱去S量:
31.22-6.215=24.6kg
氧化总Fe:
27.4-5.32=22.075kg
其中:
氧化成FeO的Fe:
27.4×75%-5.327=20.552-5.32=15.245
kg
氧化成FeO的Fe:
22.075-15.245=6.83kg432、耗氧单元:
3
22.4=17.22Nm×÷32耗氧:
a:
S24.63
Nm×22.4=4.4151/222.075氧耗÷56×Fe-FeO:
b
-c:
FeO-FeO耗氧:
43O=Fe3FeO+1/2O4238
322.4=0.46Nm1/2×1.025÷232×9.7÷311.2=0.284Nm94%÷65××d:
Zn耗氧:
1.523÷207×11.2=0.052Nme:
Pb耗氧:
1.1×87%3×22.4=0.44Nm2.15×92%÷74×3/4f:
As耗氧:
g:
总耗氧量317.22+4.415+0.46+0.284+0.052+0.44=22.87Nm33/t22.87Nm/100kg=228.7Nm入炉混合料H:
总氧料比:
I:
工业用氧料比,,空气含氧20.05%,氧站氧浓度设氧枪出口富氧浓度65%100%/空比求氧(65%-21%)/(100%-65%)=1.275
)体积比反过来空/氧比=0.784(33工业氧→含氧气100Nm100Nm3316.07Nm78.4Nm空气→含氧气3×100/115.57入炉总氧气量115.57Nm中,工业氧占的比例14%100%=86%,空气中氧气占的比例料比工业用氧那么/为33×228.7Nm86%=入炉料197Nm/t33那么每吨入炉物料耗氧气站氧气197Nm156Nm,耗空气约,那么以湿物量8%以上计算的是干量。
如果混合精矿含水份为控制氧料比为3197/t92%=182Nm×湿料(工业用氧)9
3
182Nm每吨入炉湿物料耗氧站工业氧气:
3
143Nm耗空气约七、处理量计算
399.5%)含氧不小于10000Nm/h(制氧站产氧设计达量可入为炉氧气氧利用率,那么可认按95%的平均3(纯氧)9500Nm/h33/t=48t/h198Nm/h÷那么每小时可处理炉料:
9500Nm)
100=47t/h(干(其中混合精矿48÷102.5×47t/h=1070t/d
95%(作业率)×日可处理混合精矿24×八、烟气成份(以每小时计算)
3/h
9500Nm1、入炉氧气:
3/h9500×0.784=7448Nm2、入炉空气(氧枪):
3/h
2100Nm3、下料口漏入空气假设:
3/h
9500+(74448+2100)×20.5%=11460Nm4、入炉总氧气量:
3O,那么烟气含570Nm假设氧气利用率95%:
23/h)×入炉总氮气量:
(7448+210078%=7450Nm5、水蒸气量:
1○8%O为:
H物料带入水量,假设物料含23/h
22.48%48(干)÷92%×÷18××1000=5200Nm32)(设湿空气含水量空气带入水量,○0.023940g/m3/h×1822.4=280Nm÷×(7448+2100)0.023943/h
总水蒸气量:
5200+280=5480Nm10
6、SO气量23/h×1000/100=8260Nm48×17.22CO气量:
7、2CO气体:
CaCO、MgCO等碳酸盐分解产生混合精矿中各种2333.5%
设(在精矿中的含量)CaO+MgO3/h1000=670Nm×22.4×那么Vco=3.5%×48÷562
、烟气成份表(炉口处,不含炉口漏风)8
3
NmCOOHO∑NSO22222
九、开炉生产物料平衡表
CuFe
SSiAsPbZn2产出30铜锍6.785.4616.5
40熔炼渣0.622.6275
8.8
1.4
24.62
24.62烟气含硫
5.650.1烟尘
1.2损失
28.0875
18102.5
8.832
产出合计说明:
11
、1的7.4275kg熔炼渣中22.6275kgFe包括FeO,342、熔炼返尘及返冷料加入与产出相同,可不参与平衡计算。
(如转炉烟尘等非本系统含铜、正常生产配料计算根据实际3物料)调整。
十、热平衡计算、富氧底吹炉界面热量流通图1q烟气带走热入炉物料显热Q
水份蒸发吸热q、硫化物、碳酸盐分解吸热q、化学反应放热铜锍带走热q
入炉气体显热Q
2、假设条件:
计算基准:
每小时处理48吨入炉混合料,设炉渣温度1250℃,铜锍温度1100℃,烟尘气1200℃,炉子容积热强度800—3。
·m1300MJ/hGJ/h()3、热收入QS)○(硫的燃烧热9286KJ/kg·、S燃烧放热:
148×24.6%×1000×9286=109.65GJ/h
、Fe氧化放热:
○(Fe的氧化热4258KJ/kg·Fe)(上述是指2氧化成FeO的放热,进一步氧化成FeO的忽略不计)4348×22.075%×1000×4258=45012GJ/h。
精矿中其它元素如Pb、Zn、As等的氧化放热忽不计。
12
、造渣热○32FeO+SiO2FeO·SiO(放热Q=762KJ/kgSiO)
=222渣含Fe40×38%÷102.5×100=14.83kg(100kg混合料)
硅酸铁中SiO量=14.83×60.1/111.7=7.98kg
2生成硅酸铁渣放热7.98×1000/100×48×762=2.92GJ/h
CaO+SiO=CaO·SiO(放热Q′=1436KJ/kg·SiO)222渣含SiO=40×22%÷1.025=8.6kg.(100kg混合矿)2硅酸钙渣中SiO=0.78kg
2生成硅酸钙渣放热:
0.78×1000/100×48×1436=0.54
总的造渣热Q=2.92+0.54=3.46GJ/h
渣、入炉空气显热(氧气温度低不计显热)○4320℃1.3KJ/Nm·℃温度取空气热容20=0.25GJ/h
1.3×(7448+2100)×Q=气○入炉物料显热5入炉混合物料热焓取12.6kJ/kg
Q=48×1000×12.6=0.6GJ/h
料、总的热收入Q○6∑Q=109.65+45.12+3.46+0.25+0.6=159.0GJ/h∑4、热支出q(GJ/h)
、铜锍带走热(铜锍比热0.856KJ/kg·℃)○aq=48×30%÷1.025×1000×0.856×11001=13.23GJ/h
13
炉渣带走热(炉渣比热1.172KJ/kg·℃)○bq=48×40%÷1.025×1000×1.172×12502=27.44GJ/h
、烟气带走热○c3·℃)热容:
2.28KJ/Nm带走热(令SOSO221200=22.60GJ/h
××2.28826032.28.气体热容为热容:
2.28KJ/Nm·℃,XOCO带走热(令CO2221200=1.83GJ/h
×670×2.283气体热容1.77Kg/Nm·℃HO蒸气带走热(HO221200=11.64GJ/h×1.77×54803·℃N气带走热(N气热容1.42Kg/Nm221200=12.70GJ/h×7450×1.423·℃O热容1.40Kg/NmO带走热(221200=0.96GJ/h
××1.40570=49.73GJ/h
烟气带走总热q烟气○(烟尘比热、烟尘带走热1.13KJ/kg·℃)dq=5.5%×48×1000×1.13×1200=3.58GJ/h
尘水到1200℃气体蒸发吸收热:
○e物料中水份量:
48÷92%×8%×1000=4174Kg/h
3=229Kg/h0.02394Kg/Nm7448+2100)×(空气中水份量:
=4403Kg/h
总入炉水份量=1.47GJ/h
100-204.184********水从℃上升到℃吸热××()14
水在100℃的汽化潜热
4403Kg/h×539Kcal/kg×4.127KJ/kcal=9.94GJ/h
100℃水蒸汽到1200℃水蒸汽吸热:
1·V-t·c]·q=[tc气1001200120010054801.5)×1200×1.77-100×=(=10.82GJ/h
=22.23GJ/h
℃气体吸收总热量q水到1200水○碳酸盐分解吸热f设精矿中3.5%的含量以CaCO形式计算CaO+MgO3那么CaCO=CaO+CO↑23
10056
炉料中碳酸钙量为:
3.5%÷1.025×100/56=6.10%
碳酸钙分解吸热量为1583KJ/Kg.CaCO3那么分解吸热=48×1000×6.10%×1583=4.64GJ/h
黄铜矿的分解吸热○g假设精矿中的铜(18%)60%以CuFeS形态存在2则CuFeS含硫量:
18%×60%=10.8%2其分解放热量为:
1675kJ/kg·S
那么放热量为:
48×1000×10.8%÷1.025×1675=8.47GJ/h
、黄铁矿分解吸热○h假设精矿中的硫(32%)以CuFeS和FeS两种形态存在:
22那么以FeS形态存在的S量=32%-10.8%=21.2%
215
FeS—S22
55.84+6464
55.84?
64=39.70%
则精矿中×FeS含量=21.22
641FeS=FeS+S的分解吸热量为561KJ/kg·FeS222
2那么黄铁矿的分解吸热量:
48×1000×39.7%÷1.025×561=10.43GJ/h
、炉子散热损失○i炉子热损失诺兰达炉取9.8%,本炉型结构与诺兰达炉相似取10%,那么炉子热损失为:
159×10%=15.9GJ/h.
、总的热支出○j13.23+27.44+49.73+3.58+22.23+4.64+8.47+10.43+15.9=155.65GJ/h
、Q-q=159-155.65=3.35GJ/h>0说明:
○1支出收入炉子热收入大于热支出,熔炼过程不需外加热量能够自热熔炼。
3○、炉子热强度:
炉膛体积,V=165m2159GJ/h3=965MJ/m炉子容积热强度·=h符合要求,
3165m与诺兰达炉接近。
、热平衡5
热收入渣精锍氧化放热
热量GJ/hCuFe45.12
比例%SiOAsS28.38
热支出Pb炉渣带走热
CaO+MgOZn
热量30.67
GJ/h其它
比例9.518.45
硫燃烧热矿113.45kg砷尘造渣热
109.653.0102.520.8431.1233.192.63.46
68.961.01.022.2101.122.18
铜锍带走热1.56烟气带走热
13.233.552.34
8.329.631.48
锍氧化放热吹炼%入炉物料显热
45.1229.2627.4318.371.63
28.388.81.940.48
炉渣带走热1.381.0烟尘带走热
27.443.103.47
17.268.692.01
造渣热入炉物料显0.75尘烟气
3.460.850.340.1130.85
2.180.480.070.19碳酸盐分解吸热
烟气带走热烟尘带走热水蒸发吸热
49.733.5821.414.60
31.552.2512.882.77
热13.98
水蒸发吸热22.23
0.9x—x
石英—113.45
合计11.20
硫化物分解吸热18.78
%
16
3.71碳酸盐分解吸4.64
热11.89硫化物分解吸18.9
热1015.9炉子散热
1.043.35其它
100
159
合计159合计100
正常生产下的冶金计算第四章
%一、投入产出物料组成:
混合精矿(铜精矿和金精矿)1、CaO+MgOPb
Zn
SiOFeSAs
Cu其它21.56
6.5
2.21.123.5
18
9.5
28
30
、渣经矿:
2CaO+MgOFeSSiOCu
2SiOFeSCu210
45
2