换热器的结构.docx
《换热器的结构.docx》由会员分享,可在线阅读,更多相关《换热器的结构.docx(38页珍藏版)》请在冰豆网上搜索。
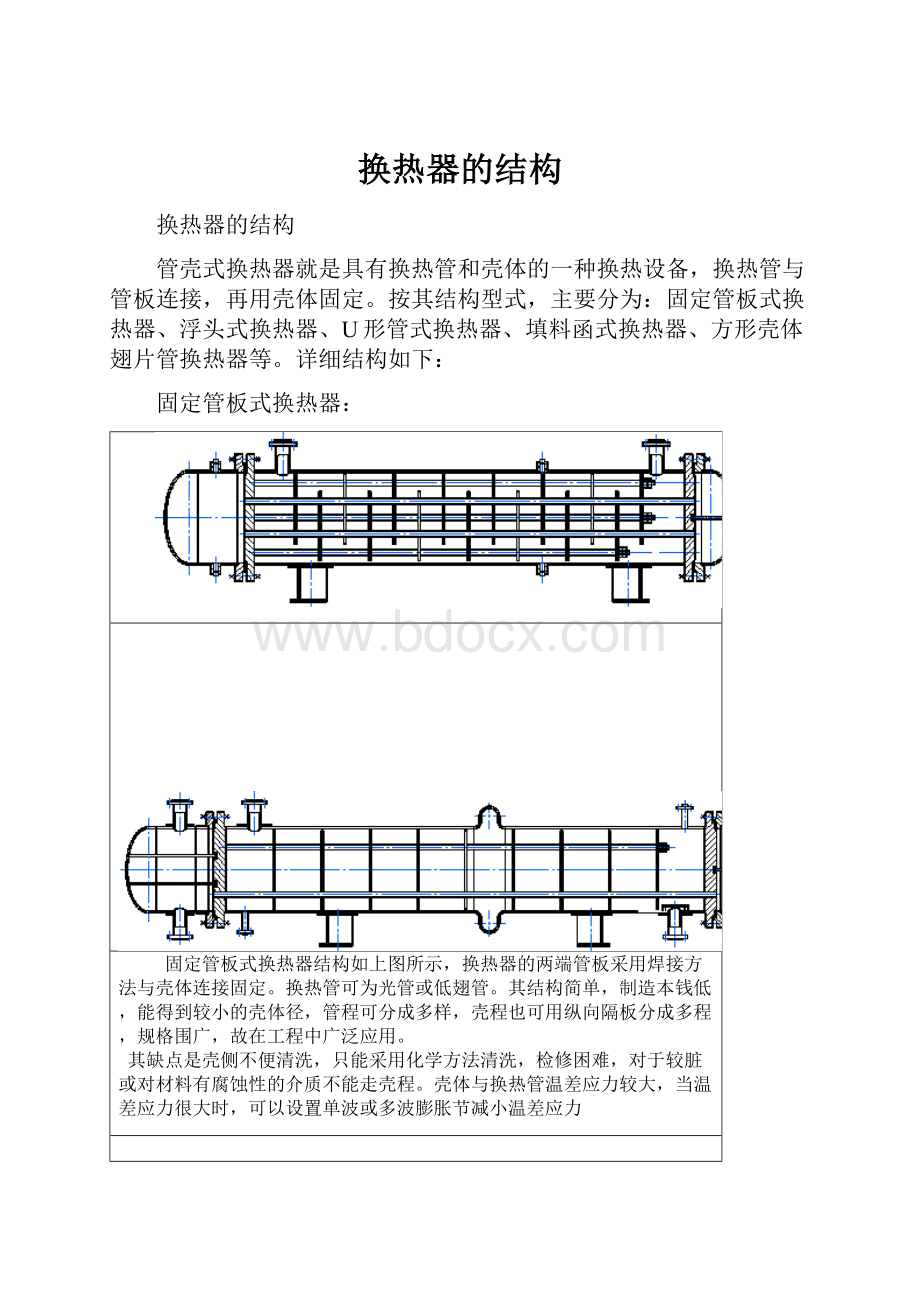
换热器的结构
换热器的结构
管壳式换热器就是具有换热管和壳体的一种换热设备,换热管与管板连接,再用壳体固定。
按其结构型式,主要分为:
固定管板式换热器、浮头式换热器、U形管式换热器、填料函式换热器、方形壳体翅片管换热器等。
详细结构如下:
固定管板式换热器:
固定管板式换热器结构如上图所示,换热器的两端管板采用焊接方法与壳体连接固定。
换热管可为光管或低翅管。
其结构简单,制造本钱低,能得到较小的壳体径,管程可分成多样,壳程也可用纵向隔板分成多程,规格围广,故在工程中广泛应用。
其缺点是壳侧不便清洗,只能采用化学方法清洗,检修困难,对于较脏或对材料有腐蚀性的介质不能走壳程。
壳体与换热管温差应力较大,当温差应力很大时,可以设置单波或多波膨胀节减小温差应力
浮头式换热器
浮头式换热器结构如下图,其一端管板与壳体固定,而另一端的管板可以在壳体自由浮动。
壳体和管束对热膨胀是自由的,故当两种介质的温差较大时,管束与壳体之间不会产生温差应力。
浮头端设计成可拆结构,使管束可以容易地插入或抽出,这样为检修和清洗提供了方便。
这种形式的换热器特别适用于壳体与换热管温差应力较大,而且要求壳程与管程都要进展清洗的工况。
浮头式换热器的缺点是结构复杂,价格较贵,而且浮头端小盖在操作时无法知道泄漏情况,所以装配时一定要注意密封性能
U形管式换热器
上图为双壳程U形管式换热器。
U形管式换热器是将换热管弯成U形,管子两端固定在同一块管板上。
由于换热管可以自由伸缩,所以壳体与换热管无温差应力。
因U形管式换热器仅有一块管板,所以结构较简单,管束可从壳体抽出,壳侧便于清洗,但管清洗稍困难,所以管介质必须清洁且不易结垢。
U形管式换热器一般用于高温高压情况下,尤其是壳体与换热管金属壁温差较大时。
壳程可设置纵向隔板,将壳程分为两程(如图中所示)。
填料函式换热器
上图为填料函式双管程双壳程换热器,填料函式换热器的换热管束可以自由滑动,壳侧介质靠填料密封。
对于一些壳体与管束温差较大,腐蚀严重而需经常更换管束的换热器,可采用填料函式换热器。
它具有浮头换热器的优点,又克制了固定管板式换热器的缺点,结构简单,制造方便,易于检修清洗。
填料函式换热器的缺点:
使用直径小;不适于高温、高压条件下;壳程介质不适于易挥发、易燃、易爆、有毒等介质
方形壳体翅片管换热器:
方形壳体翅片管换热器的壳体为方箱形(如上图所示),其换热管为带翅片的翅片管。
换热管可为单排或多排换热管。
翅片材料可采用碳钢、不锈钢、铝或铜材等。
翅片的翅高、翅距和翅片厚度可根据实际工况而定。
这种形式的换热器因为采用了翅片管,可大大强化传热面积,所以特别适用于给热系数较低的流体。
壳程流通面积可设计较大,流动阻力较小,所以对于压力较低和对压力降要求较小的流体特别适用。
在实际生产中,常常用这种换热器来加热或冷却低压空气。
其缺点:
因为壳体为方箱形,虽然管程可承受高压介质,但壳程只能承受较低压力的介质。
这种换热器的金属消耗量大,制造本钱较高。
在实际生产装置中,为提高壳程的耐压能力,往往将壳体做成圆形,而管束采用方形布管。
结构可参见下面附图
左图为我厂设计制造的空气段间冷却器的剖视图。
该换热器的管束采用方形排列的翅片管,管束长度为3.7m。
为提高壳体的承压能力,壳体采用圆筒形,直径900mm。
换热管为紫铜整体轧制翅片管,翅片外径36mm,翅片根径为20mm,换热管径16mm,翅片间距2.5mm,翅片厚度为0.5mm,换热总面积为440m2。
空气条件:
流量:
30000Nm3/h 温度:
100-40ºC 工作压力:
0.1MPa
压降:
150mm水柱 总热负荷:
597000kcal/h
管壳式换热器主要由换热管束、壳体、管箱、分程隔板、支座等组成。
换热管束包括换热管、管板、折流板、支持板、拉杆、定距管等。
换热管可为普通光管,也可为带翅片的翅片管,翅片管有单金属整体轧制翅片管、双金属轧制翅片管、绕片式翅片管、叠片式翅片管等,材料有碳钢、低合金钢、不锈钢、铜材、铝材、钛材等。
壳体一般为圆筒形,也可为方形。
管箱有椭圆封头管箱、球形封头管箱和平盖管箱等。
分程隔板可将管程与壳程介质分成多程,以满足工艺需要。
管壳式换热器在结构设计时,必须考虑许多因素,例如传热条件、材料、介质压力、温度、管壳程壁温温差、介质结垢情况、流体性质以与检修和清洗条件等等,从而确定一种适合的结构形式。
对于同一种形式的换热器,由于各种不同工况,往往采用的结构并不一样。
在工程设计中,应按其特定的条件进展分析设计,以满足工艺需要。
换热面积的计算
在管壳式换热器的设计中,确定了一种换热器的结构形式后,首先必须确定的一个重要因素是有效换热面积,换热面积的多少决定了换热器的大小。
如果换热面积太小,使工艺过程不能实现,使换热器介质出口温度不能得到有效控制。
如果换热面积太大,不仅造成材料的浪费,增加投资,而且增大了换热器的体积,使其占据过多的空间。
计算换热面积的一个重要参数是总传热系数,它包括冷热介质的给热系数、介质的污垢系数和金属壁的传热系数。
其中计算较为复杂的是介质的给热系数。
介质的给热系数不仅与介质的物性有关,而且与介质的流动状态有关。
介质的流动状态是由换热器的结构决定的,如果换热器的结构作很小改动,将引起介质流动状态作较大的变化。
在一个换热器中,同一种介质的温度是不断变化的,所以在换热器中的不同位置,同一种介质的热力学数据因温度的不同而不同。
在实际计算中,往往将一种介质分成许多个温度区域,在不同的温度区域,对介质的热力学数据作相应的计算。
在换热器的设计过程中,换热面积确实定是最为关键的一步,它不仅需要计算方确严密,而且各种参数必须十分准确。
换热器的分析计算过程是一个动态的计算过程,往往须不断地调整换热器的结构参数。
而管壳式换热器的结构参数很多,其中一项的改变将会使计算结果产生很大变化,所以需要不断的反复,不仅要使换热面积满足需要,而且还应兼顾到其它许多因素,例如介质阻力情况等等。
流体阻力的计算
在管壳式换热器的分析设计中,流体的阻力计算是极为重要的,流体的阻力对于工艺过程是较为关键的参数,它不仅影响到整个系统的压力平衡,而且对于节能降耗也起到重要的作用。
在实际生产中,常常由于流体阻力不适而使工艺过程难以实现。
在管壳式换热器中,流体的阻力包括壳程流体的阻力与管程流体的阻力。
壳程流体阻力包括介质进口管、出口管、换热管间、折流板缺口等处阻力。
介质进出口管阻力可以通过改变进出口管的大小来进展调节。
换热管间的介质阻力可以通过改变换热管间的介质流通面积来进展调节,例如改变换热管的布管形式,改变壳体直径,改变折流板间距等。
折流板缺口处的介质阻力可以通过改变折流板缺口高度来进展调节。
管程流体的阻力包括介质进出口管、换热管、管箱等处阻力。
介质进出口管阻力可以通过改变进出口管的大小来进展调节。
换热管的介质阻力可以通过改变换热管的数量,换热管的长度,换热管的直径以与管程数等来进展调节。
管箱处的介质阻力可以通过改变管箱处的介质流通面积来进展调节。
换热器中流体的阻力计算,应分别计算出换热器部各处的流体阻力。
只有掌握了介质阻力的分布情况,才能够通过有效调整换热器各处的结构尺寸来改变介质的阻力,从而满足工艺要求。
管束震动分析
对于管壳式换热器,一个容易被无视的问题是换热管的振动。
而换热管束的振动往往是换热管破坏的主要原因,使换热器过早报废。
引起换热管振动的因素很多,也较复杂。
当介质流量接近使换热管产生共振的临界流量时,将引起换热管束产生较大的振动。
另外换热器部介质的局部湍流、涡流也会引起换热管振动。
换热管振动的位置较广,可以是某两个折流板间的所有换热管同时产生振动,或只有几排换热管产生振动。
也可能是在介质进口或出口端的某些换热管产生振动。
总之,换热管的振动可能发生在换热管束的任何一处或多处。
换热器的管束振动分析,就是要确定换热管的振动位置以与振动性质,了解引起换热管产生振动的原因,从而消除换热管的振动。
消除换热管振动的方法有很多,可以通过改变换热器的结构尺寸来改变换热管束的固有频率或流体的流动状态,从而消除换热管的振动。
或者在换热管束的振动部位增加局部支撑板,来约束换热管的振动。
换热器网络分析
在一个工程系统中,往往不是对单一的某台换热器进展分析,常常是对由多个换热器组成的网络进展联合计算,其间还有一些其它设备〔例如:
阀门、混合、别离等设备〕。
下列图为一个简单的换热器网络。
对一个换热器网络应进展综合的考虑并进展系统的分析。
在一个工程系统中,往往不是对单一的某台换热器进展分析,常常是对由多个换热器组成的网络进展联合计算,其间还有一些其它设备〔例如:
阀门、混合、别离等设备〕。
下列图为一个简单的换热器网络。
对一个换热器网络应进展综合的考虑并进展系统的分析。
换热器强度计算
确定了换热器的结构与尺寸以后,必须对换热器的所有受压元件进展强度计算。
因为管壳式换热器一般用于压力介质的工况,所以换热器的壳体大多为压力容器,必须按照压力容器的标准进展计算和设计,对于钢制的换热器,我国一般按照GB150<<钢制压力容器>>标准进展设计,或者美国ASME标准进展设计。
对于其它一些受压元件,例如管板、折流板等,可以按照我国的GB151<<管壳式换热器>>或者美国TEMA标准进展设计。
对于其它材料的换热器,例如钛材、铜材等应按照相应的标准进展设计。
下面提供一氮气冷却器的受压元件强度计算,以供参考。
该换热器为U形管式换热器,壳体直径500mm,管程设计压力3.8MPa,壳程设计压力0.6MPa。
详细强度计算如下:
1.壳程筒体强度计算:
氮气冷却器(U形管式换热器)筒体计算
计算条件
筒体简图
计算压力Pc
0.60
MPa
设计温度t
100.00
C
径Di
500.00
mm
材料
16MnR(热轧)(板材)
试验温度许用应力
170.00
MPa
设计温度许用应力t
170.00
MPa
试验温度下屈服点s
345.00
MPa
钢板负偏差C1
0.00
mm
腐蚀裕量C2
1.00
mm
焊接接头系数
0.85
厚度与重量计算
计算厚度
==1.04
mm
有效厚度
e=n-C1-C2=7.00
mm
名义厚度
n=8.00
mm
重量
481.06
Kg
压力试验时应力校核
压力试验类型
液压试验
试验压力值
PT=1.25P=0.7500
MPa
压力试验允许通过
的应力水平T
T0.90s=310.50
MPa
试验压力下
圆筒的应力
T==31.95
MPa
校核条件
TT
校核结果
合格
压力与应力计算
最大允许工作压力
[Pw]==3.99014
MPa
设计温度下计算应力
t==21.73
MPa
t
144.50
MPa
校核条件
t≥t
结论
合格
2.前端管箱筒体强度计算
氮气冷却器前端管箱筒体计算
计算条件
筒体简图
计算压力Pc
3.80
MPa
设计温度t
100.00
C
径Di
500.00
mm
材料
0Cr18Ni9(板材)
试验温度许用应力
137.00
MPa
设计温度许用应力t
137.00
MPa
试验温度下屈服点s
205.00
MPa
钢板负偏差C1
0.80
mm
腐蚀裕量C2
0.00
mm
焊接接头系数
0.85
厚度与重量计算
计算厚度
==8.29
mm
有效厚度
e=n-C1-C2=11.20
mm
名义厚度
n=12.00
mm
重量
75.76
Kg
压力试验时应力校核
压力试验类型
液压试验
试验压力值
PT=1.25P=4.7500
MPa
压力试验允许通过
的应力水平T
T0.90s=184.50
MPa
试验压力下
圆筒的应力
T==127.53
MPa
校核条件
TT
校核结果
合格
压力与应力计算
最大允许工作压力
[Pw]==5.10266
MPa
设计温度下计算应力
t==86.72
MPa
t
116.45
MPa
校核条件
t≥t
结论
合格
3.前端管箱封头强度计算
氮气冷却器前端管箱封头计算
计算条件
椭圆封头简图
计算压力Pc
3.80
MPa
设计温度t
100.00
C
径Di
500.00
mm
曲面高度hi
125.00
mm
材料
0Cr18Ni9(板材)
试验温度许用应力
137.00
MPa
设计温度许用应力t
137.00
MPa
钢板负偏差C1
0.80
mm
腐蚀裕量C2
0.00
mm
焊接接头系数
1.00
厚度与重量计算
形状系数
K==1.0000
计算厚度
==6.98
mm
有效厚度
e=n-C1-C2=11.20
mm
最小厚度
min=0.75
mm
名义厚度
n=12.00
mm
结论
满足最小厚度要求
重量
32.23
Kg
压力计算
最大允许工作压力
[Pw]==6.06962
MPa
4.后端壳程封头强度计算
氮气冷却器后端壳程封头计算
计算条件
椭圆封头简图
计算压力Pc
0.60
MPa
设计温度t
100.00
C
径Di
500.00
mm
曲面高度hi
125.00
mm
材料
16MnR(热轧)(板材)
试验温度许用应力
170.00
MPa
设计温度许用应力t
170.00
MPa
钢板负偏差C1
0.00
mm
腐蚀裕量C2
2.00
mm
焊接接头系数
1.00
厚度与重量计算
形状系数
K==1.0000
计算厚度
==0.88
mm
有效厚度
e=n-C1-C2=6.00
mm
最小厚度
min=0.75
mm
名义厚度
n=8.00
mm
结论
满足最小厚度要求
重量
19.61
Kg
压力计算
最大允许工作压力
[Pw]==4.05567
MPa
结论
合格
5.管板强度计算
氮气冷却器管板计算
设计条件
壳程设计压力
0.60
MPa
管程设计压力
3.80
MPa
壳程设计温度
100.00
C
管程设计温度
100.00
C
壳程筒体壁厚
8.00
mm
管程筒体壁厚
12.00
mm
壳程筒体腐蚀裕量C
1.00
mm
管程筒体腐蚀裕量C
0.00
mm
换热器公称直径
500.00
mm
换热管使用场合
一般场合
管板与法兰或圆筒连接方式(abcd型)
a型
换热管与管板连接方式(胀接或焊接)
焊接
材料(名称与类型)
0Cr18Ni9
名义厚度
70.00
mm
管
强度削弱系数
0.40
刚度削弱系数
0.40
材料泊松比
0.30
隔板槽面积
210.00
mm2
换热管与管板胀接长度或焊脚高度l
3.50
mm
设计温度下管板材料弹性模量
191000.00
MPa
设计温度下管板材料许用应力
137.00
MPa
许用拉脱力
68.50
MPa
壳程侧结构槽深h1
0.00
mm
板
管程侧隔板槽深h2
4.00
mm
壳程腐蚀裕量
0.00
mm
管程腐蚀裕量
0.00
mm
材料名称
0Cr18Ni9
换
管子外径d
19.00
mm
热
管子壁厚
2.00
mm
管
U型管根数n
138
根
换热管中心距S
25.00
mm
设计温度下换热管材料许用应力
137.00
MPa
垫片材料
软垫片
压紧面形式
1a或1b
垫
垫片外径Do
565.00
mm
片
垫片径Di
515.00
mm
a型
垫片厚度g
mm
垫片接触面宽度
mm
垫片压紧力作用中心园直径DG
547.11
mm
(c型)
管板材料弹性模量
0.00
MPa
(d型)
管板材料弹性模量
0.00
MPa
(bd型)
管箱圆筒材料弹性模量
0.00
MPa
(bc型)
壳程圆筒材料弹性模量
0.00
MPa
(cd型)
管板延长局部形成的凸缘宽度
0.00
mm
(c型〕
壳体法兰或凸缘厚度
0.00
mm
(d型)
管箱法兰或凸缘厚度
0.00
mm
参数计算
管板布管区面积
三角形排列
正方形排列
一根换热管管壁
金属横截面积
=106.81
mm2
管板开孔前抗
弯刚度
bcd型
0.00
N·mm
管板布管区当
量直径
436.43
mm
a型
其他
系数
0.80
系数
按和查图得:
=0.000000
系数
按和查图得:
=0.000000
ad型
=0
bc型
0.00
a,c型
=0
b,d型
0.00
a型
=0
其他
0.00
旋转刚度无量
刚系数
0.00
系数
0.2696
按和0.0713
0.0000
管板厚度或管板应力计算
a
管板计算厚度
取、大值
61.345
mm
型
管板名义厚度
66.000
mm
管板中心处径
向应力
=0
MPa
=0
MPa
b
c
d
布管区周边处
径向应力
=0
MPa
型
=0
MPa
边缘处径向应
力
=0
MPa
=0
MPa
管板应力校核单位:
MPa
|r|r=0=
b
工况
|r|r=Rt=
c
|r|r=R=
d
|r|r=0=
型
工况
|r|r=Rt=
|r|r=R=
换热管轴向应力计算与校核:
MPa(单位)
计算工况
计算公式
计算结果
校核
只有壳程设计压力,
管程设计压力=0:
|-1.59|
≤
合格
只有管程设计压力,
壳程设计压力=0:
=
|6.29|
≤
合格
壳程设计压力,管程
设计压力同时作用:
|4.69|
≤
合格
换热管与管板连接拉脱力校核
拉脱力q
3.21≤[q]
MPa
校核
合格
重量
64.89
Kg
6.管程设备法兰强度计算
氮气冷却器管箱法兰强度计算
设计条件
简图
设计压力p
3.800
MPa
计算压力pc
3.800
MPa
设计温度t
100.0
°C
轴向外载荷F
0.0
N
外力矩M
0.0
N.mm
壳
材料名称
0Cr18Ni9
体
许用应力
137.0
MPa
法
材料名称
#
许用
[s]f
137.0
MPa
兰
应力
[s]tf
137.0
MPa
材料名称
40Cr
螺
许用
[s]b
212.0
MPa
应力
[s]tb
189.0
MPa
栓
公称直径dB
24.0
mm
螺栓根径d1
20.8
mm
数量n
24
个
Di
500.0
Do
660.0
垫
结构尺寸
Db
615.0
D外
565.0
D
515.0
δ0
16.0
mm
Le
22.5
LA
31.5
h
35.0
δ1
26.0
材料类型
软垫片
N
25.0
m
2.00
y
11.0
压紧面形状
1a,1b
b
8.94
DG
547.1
片
b0≤6.4mmb=b0
b0≤6.4mmDG=(D外+D)/2
b0>6.4mmb=2.53
b0>6.4mmDG=D外-2b
螺栓受力计算
预紧状态下需要的最小螺栓载荷Wa
Wa=πbDGy=169119.0
N
操作状态下需要的最小螺栓载荷Wp
Wp=Fp+F=1127044.1
N
所需螺栓总截面积Am
Am=max(Ap,Aa)=5963.2
mm2
实际使用螺栓总截面积Ab
Ab==8117.5
mm2
力矩计算
操
FD=0.785pc
=745750.0
N
LD=LA+0.5δ1
=44.5
mm
MD=FDLD
=33185876.0
N.mm
作
FG=Fp
=233573.5
N
LG=0.5(Db-DG)
=33.9
mm
MG=FGLG
=7928625.5
N.mm
Mp
FT=F-FD
=147150.2
N
LT=0.5(LA+d1+LG)
=45.7
mm
MT=FTLT
=6728066.0
N.mm
外压:
Mp=FD(LD-LG)+FT(LT-LG);压:
Mp=MD+MG+MTMp=47842568.0
N.mm
预紧Ma
W=1492550.6
N
LG=33.9
mm
Ma=WLG=50664460.0
N.mm
计算力矩Mo=Mp与者Mo=50664460.0
N.mm
螺栓间距校核
实际间距
=80.5
mm
最小间距
56.0(查GB150-98表9-3)
mm
最大间距
158.4
mm
形状常数确定
89.44
h/ho=0