第二章 硅的提纯.docx
《第二章 硅的提纯.docx》由会员分享,可在线阅读,更多相关《第二章 硅的提纯.docx(25页珍藏版)》请在冰豆网上搜索。
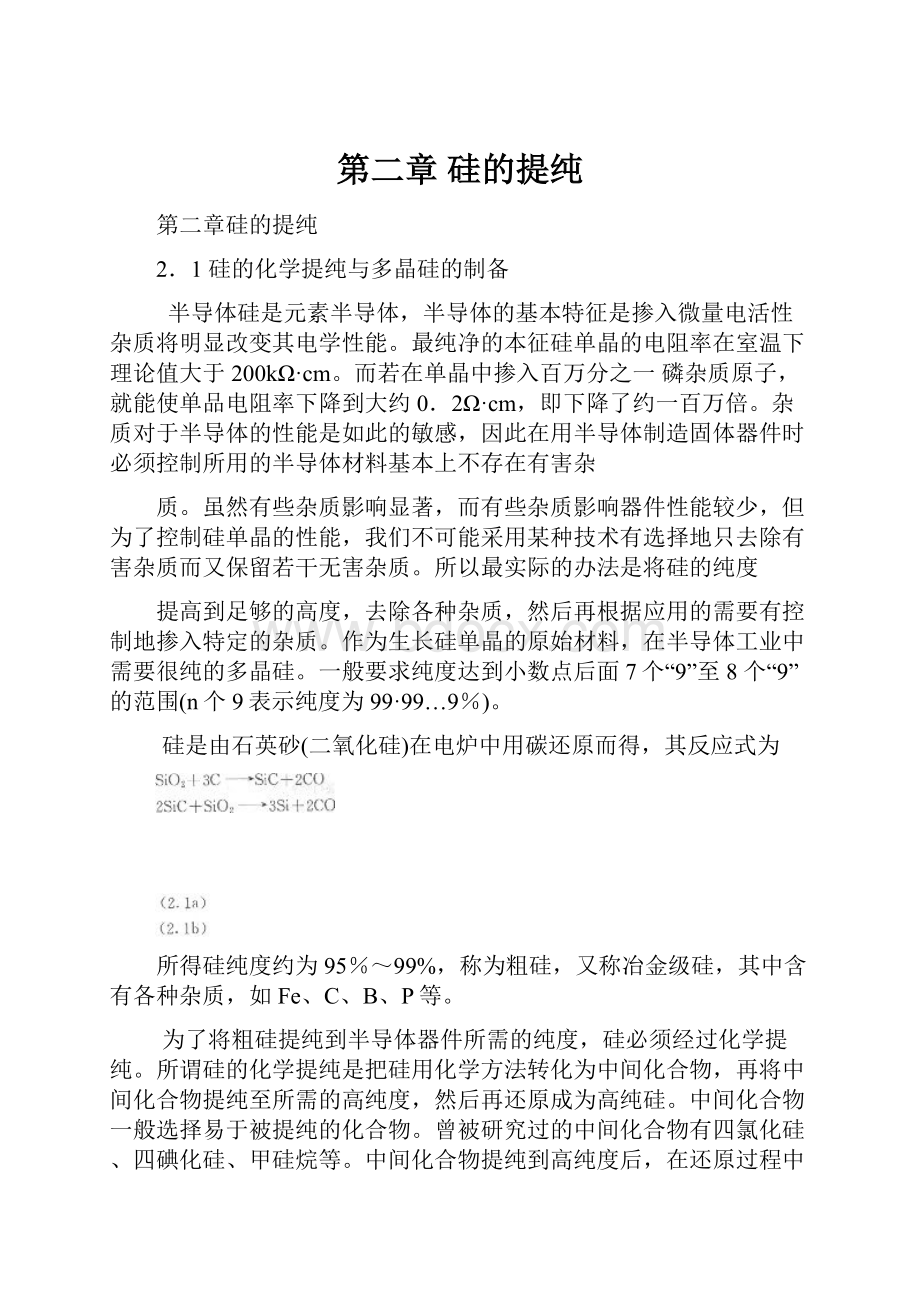
第二章硅的提纯
第二章硅的提纯
2.1硅的化学提纯与多晶硅的制备
半导体硅是元素半导体,半导体的基本特征是掺入微量电活性杂质将明显改变其电学性能。
最纯净的本征硅单晶的电阻率在室温下理论值大于200kΩ·cm。
而若在单晶中掺入百万分之一磷杂质原子,就能使单品电阻率下降到大约0.2Ω·cm,即下降了约一百万倍。
杂质对于半导体的性能是如此的敏感,因此在用半导体制造固体器件时必须控制所用的半导体材料基本上不存在有害杂
质。
虽然有些杂质影响显著,而有些杂质影响器件性能较少,但为了控制硅单晶的性能,我们不可能采用某种技术有选择地只去除有害杂质而又保留若干无害杂质。
所以最实际的办法是将硅的纯度
提高到足够的高度,去除各种杂质,然后再根据应用的需要有控制地掺入特定的杂质。
作为生长硅单晶的原始材料,在半导体工业中需要很纯的多晶硅。
一般要求纯度达到小数点后面7个“9”至8个“9”的范围(n个9表示纯度为99·99…9%)。
硅是由石英砂(二氧化硅)在电炉中用碳还原而得,其反应式为
所得硅纯度约为95%~99%,称为粗硅,又称冶金级硅,其中含有各种杂质,如Fe、C、B、P等。
为了将粗硅提纯到半导体器件所需的纯度,硅必须经过化学提纯。
所谓硅的化学提纯是把硅用化学方法转化为中间化合物,再将中间化合物提纯至所需的高纯度,然后再还原成为高纯硅。
中间化合物一般选择易于被提纯的化合物。
曾被研究过的中间化合物有四氯化硅、四碘化硅、甲硅烷等。
中间化合物提纯到高纯度后,在还原过程中如果工艺技术不恰当,还会造成污染而降低产品纯度。
因此,还原也是重要的工艺过程。
高纯多晶硅的生产方法大多数分为三个步骤:
①中间化合物的合成;②中间化合物的提纯;③还原成纯硅。
历史上,人们研究或应用过各种高纯多晶硅的制造方法。
最早实现的是四氯化硅锌还原法,由于在还原时锌的沾污,产品还要经过区域提纯(物理提纯)才能达到电子级的要求,整个过程不经济所以已被淘汰。
用四碘化硅作为中间化合物也曾被重视,因为四碘化硅能用各种方法提纯,如精馏、萃取、区域提纯等方法均可用于提纯四碘化硅,但由于结果并不经济,纯度也不优于其他方法而被淘汰。
现代大量用于生产的是四氯化硅氢还原法、二氯二氢硅还原法、三氯氢硅氢还原法和甲硅烷热分解法。
尤其是后两者,在国际上占主导地位。
现分述如下。
2.1.1三氯氢硅氢还原法
三氯氢硅氢还原法最早由西门子公司研究成功,有的文献上称此法为西门子法。
三氯氢硅氢还原法可分为三个重要过程:
一是中间化合物三氯氢硅的合成,二是三氯氢硅的提纯,三是用氢还原三氯氢硅获得高纯硅多晶。
1.三氯氢硅的合成
三氯氢硅(SiHCl3)由硅粉与氯化氢(HCl)合成而得。
化学反应式为
上述反应要加热到所需温度才能进行。
又因是放热反应,反应开始后能自动持续进行。
但能量如不能及时导出,温度升高后反而将影响产品收率。
反应除了生成SiHCl3外,还有SiCl4或SiH2Cl2等氯硅烷以及其他杂质氯化物,如BCl3、PCl3、FeCl3、CuCl、TiCl3等。
合成设备可以是固定床,也可以是沸腾床,以沸腾床为优,可连续生产且效率高。
影响产率的重要因素是反应温度与氯化氢的含水量。
产出率与含水量的关系可粗略地由图2.1中的曲线表示。
此外,硅粉粗细对反应也有影响。
因此,对硅粉的粒度要有适当选择。
2.三氯氢硅的提纯
三氯氢硅的提纯是硅提纯技术的重要环节。
在精馏技术成功地应用于三氯氢硅的提纯后,化学提纯所获得的高纯硅已经可以免除物理提纯(区域提纯)的步骤直接用于拉制硅单品,符合器件制造的要求。
精馏是近代化学工程有效的提纯方法,可获得很好的提纯效果。
三氯氢硅精馏一般分为两级,常把前一级称为粗馏,后一级称为精馏。
完善的精馏技术可将杂质总量降低到10-7~10-10量级。
精馏对于各种中间化合物有共同的提纯原理,将在2.2.1节中介绍讨论。
3.氢还原三氯氢硅
用氢作为还原剂还原已被提纯到高纯度的三氯氢硅,使高纯硅淀积在1100~1200℃的热载体上。
载体常用细的高纯硅棒,通以大电流使其达到所需温度。
化学反应式为
用于还原的氢必须提纯到高纯度以免污染产品。
如氢与三氯氢硅的克分子比值按理论配比则反应速度慢,硅的收率太低。
氢与三氯氢硅的配比在生产上通常选在20~30之间。
还原时氢通人SiHCl3液体中鼓泡,使其挥发并作为SiHCl3的携带气体。
还原时SiHCl3反应仍不完全,因此必须回收尾气中的SiHCl3以减少损失。
三氯氢硅氢还原工艺系统原理图如图2.2所示。
2.1.2硅烷热分解法
硅烷实际上是甲硅烷的简称。
甲硅烷作为提纯中间化合物有其突出的特点:
一是甲硅烷易于热分解,在800~900℃下分解即可获得高纯多晶,还原能耗较低。
二是甲硅烷易于提纯,在常温下为气体,可以采用吸附提纯方法有效地去除杂质。
缺点是热分解时多晶的结晶状态不如其他方法好,而且易于生成无定型物。
高纯硅烷气又是外延单晶、多晶、非晶硅薄膜的重要原材料。
1.硅烷的制备
曾被研究的甲硅烷的制备方法有多种,如用氢化铝锂在乙醚溶液中与四氯化硅作用可生成甲硅烷。
化学反应式如下
过量的氢化铝锂有很好的去硼提纯作用。
氢化铝锂与氯化硼作用的化学反应如下
类似的方法还有用氢化钠代替氢化铝锂在醚或四氢呋喃中与四氯化硅反应。
以上方法价格高,又不安全,易引起爆炸。
日本小松电子金属公司在20世纪60年代末开始采用硅烷法生产多晶硅,用硅化镁与氯化铵反应生成甲硅烷,化学反应如下
反应在液氨作为溶剂下进行。
该方法的甲硅烷产率可达60%~70%,化学反应进行稳定。
80年代美国联合碳化物公司研究成功采用催化剂,使氯硅烷产生歧化反应转化为甲硅烷的方法,化学反应如下
该方法大大降低了甲硅烷制备的成本,并已进行大规模生产。
2.硅烷的提纯
硅烷法在提纯方面有许多优点,首先是有特殊的去硼技术可以采用,如上述的过量氢化铝锂的去硼作用。
在液氨作为溶剂下,用硅化镁与氯化铵反应生成甲硅烷也有很好的去硼效果。
NH3与B2H6会发生化学反应,生成稳定的化合物并溶于液氨中。
化学反应式如下
而在硅的提纯中硼是被去除的首要对象。
由于各种金属杂质不能生成类似的氢化物或者其他挥发性化合物,使得在硅烷生成的过程中,粗硅中的金属杂质先被大量除去。
因此,在以后的提纯过程中,提纯对象是余下的施主杂质和碳化物。
硅烷提纯的主要技术是精馏和吸附。
硅烷在常温下为气体,精馏必须在低温或低温非常压下进行。
因此,硅烷精馏比其他的精馏方法复杂。
但是硅烷气体却易于用吸附法提纯。
我国的高纯硅烷气多采用浙江大学研究的分子筛吸附提纯方法生产。
在液氨作为溶剂下用硅化镁与氯化铵反应制备的硅烷气中的硼含量已经降到很低水平,分子筛吸附提纯能有效地去除PH3,使施主和受主杂质都降到很低水平。
3.硅烷的热分解
不需用氢还原,甲硅烷可以热分解为多晶硅是硅烷法的一大优点。
化学反应式如下
甲硅烷的分解温度低,在850℃时即可获得好的多晶结晶。
而目.硅的收率达90%以上。
但在500℃
以上甲硅烷就易于分解为非晶硅。
非晶硅易于吸附杂质,已达到高纯度的非晶硅也难于保持其纯度,因此在硅烷热分解时不能允许无定型硅的产生。
改进硅烷法多晶质量,可以使用加氢稀释热分解等专利技术,甲硅烷热分解时多晶硅就淀积在加热到850℃的细硅棒(硅芯)上。
2.1.3其他方法
四氯化硅氢还原法虽然陈旧,但仍有工厂保留这种方法进行生产。
美国的海姆洛克公司采用二氯二氢硅(SiH2C12)代替三氯氢硅生产硅多晶,优点是SiH2Cl2比SiHCl3稳定性小、易于分解,多晶沉积速度快,转换效率可达35%,产量高而能耗低。
化学反应式如下
颗粒状多晶硅是80年代出现的硅多晶新产品。
已提纯的中间化合物不是在硅棒上还原淀积,而是淀积在硅细粉上。
反应在流化床中进行。
由于硅细粉相对于硅棒的淀积热载体表面积的增加,使硅的收率增高而能耗降低,其成本较低。
生长直拉硅单晶时在石英坩埚中装多晶料,如果将块状硅与颗粒状硅混合使用,可增加填充系数,给装料带来方便,并目.最适用于连续拉晶工艺的加料。
颗粒状硅的应用将会不断增加,很有发展前途。
颗粒状硅的缺点是不能用于区熔方法中,且结晶状态较差。
2.2超提纯技术及其原理
2.2.1精馏提纯
在化学提纯中,精馏是极为有效的重要方法之一,在硅的提纯过程中,不论是SiCl4,SiHCl3,SiH2Cl2还是SiH4均可以采用精馏技术进行提纯。
精馏是利用不同组分有不同沸点,在同一温度下各组分具有不同蒸气压的特点进行的。
精馏过程实质上属于物理提纯过程。
但是硅的化学提纯包括把硅变为中间化合物而后进行精馏,精馏是作为化学提纯过程中的一个步骤。
1.1.气液两相的相平衡与蒸馏
一个物系可由一个或多个相互问处于平衡状态的相组成,这种状态称为相平衡状态。
随温度、压力不同,相平衡状态随之改变。
以下用完全互溶的A、B双组分的溶液与其混合蒸气所组成的相平衡体系为例进行说明。
在盛有A、B溶液的密闭容器内,在一定温度下A、
B两组分同时逸出液面,形成蒸气。
这一系统由气相
和液相这两相组成。
当各组分从液相进入气相与从
气相返回液相的速率相等时,此两相达到平衡,液
相与气相中的组分保持一定。
在一定压力下,随温
度的不同,相平衡下的组分各异。
组分随温度的变
化可用温度-组分图(T-X-Y图)表示,如图2.3所示。
在图2.3中,横坐标表示组分(X表示液相的组分,
Y表示气相的组分),纵坐标T表示温度,Ta,Tb分
别表示纯A、B组元的沸点。
下面一条曲线称为液相线,
上面一条曲线称为气相线。
这两条曲线把T-X-Y图分为
三个区域,液相线以下为液相区,气相线以上为气相区,
两
线之间为气液共存区。
对组分为XF的某溶液,温度从低到高上升到T1时,遇到液相线(J点)。
这时,正好产生第一个气泡,故液相线又称为泡点曲线。
该组分气从高温下降温度遇到气相线(H点),则产生第一个液滴,相应的温度为T3,即露点,故气相线又称为露点曲线。
溶液的组元不同时,T一X—Y曲线也各异,可由实验测定而得。
从图2.3可见,在任一温度下,气相中易挥发组分B的含量总是高于液相中易挥发组分B的含量。
所以将双组分溶液进行简单蒸馏,加热溶液到沸点,用冷凝器将所产生的蒸气冷凝并收集馏出液,进行一段时间就把原液分成了含易挥发组分较多的馏出液和含难挥发组分较多的残留液。
蒸馏是一种简单的分离手段,虽有分离提纯作用,但效果不够理想。
精馏则是一种很有效的提纯技术。
2.精馏原理——多次部分气化,部分冷凝
如图2.3所示,某双组分溶液加热到(J点),液体开始沸腾,产生的蒸气组成为Y1,Y1与XF平衡,这时Y1中的易挥发成分B大于XF中的B成分。
温度若再继续升温到t3(H点),液相终将消失,这时蒸气的组成与溶液的最初组成XF相同。
但在JH之间加热时,却进行着部分气化和部分冷凝,使溶液分成为不同成分的液体和蒸气。
如图2.4所示,XF加热到了T2时,气、液两相共存,液体组成为X2,蒸气组成为Y2。
如分别收集,就可得到组分不同的物质。
所以,部分气化和冷凝能使成分得到改变。
如让X2,y2成分再进行部分气化和部分冷凝,一步一步地蒸馏和冷凝的过程如图2.4所示的箭头方向,终将使A与B
两种组元完全分离。
这是不切实际的很不经济的方法,不过这一原理促成了精馏技术的发展。
3.精馏技术
精馏是实现多级部分气化和多级部分冷凝的实用技术。
精馏塔是实现精馏技术的工具,图2.5是塔板塔示意图。
底部为塔釜,对塔底部的液体加热。
顶部有冷凝器,把上升的气体冷凝为液体并使其中一部分回流,回流液自塔顶逐板下降,在塔板上气液相遇进行部分气化和部分冷凝。
塔内上升蒸气每经一块塔板,就与该板上的蒸气接触一次,进行一次部分冷凝,其易挥发组分的含量就增加一次,所以上升蒸气中易挥发组分逐板提浓。
而塔内下降的液体每经一塔板就与上升蒸气接触一次,进行一次部分气化,使液相中易挥发组分逐板减少,即难挥发组分逐板提浓。
在塔板数足够多的情况下,精馏可以把挥发性不同的组分分离。
精馏塔一般由中部进料,上段称为精馏段,下段称为提馏段。
回流是保证精馏操作的重要措施。
为达到精馏的提纯效果,必须保持一定回流比。
如塔顶冷凝馏出液为D,回馏液的量为L,则R=L/D称为回馏比。
回馏比是精馏操作的重要参数,也是设计精馏塔的重要参数。
在设计考虑中,理论板是一个很重要的概念。
所谓理论板,是假设在该塔板的蒸气和液体达到平衡,离开它的蒸气组成Yn与液体组成Xn呈平衡状态。
因为达到平衡状态时,一个塔板所能取得的分离效果是最好的,因此它是作为衡量塔板分离效果的最高标准。
在设计中,可依分离的需要求得最少理论塔板数。
塔的效率,对于某种提纯常常有实际数据可依。
所需的实际塔板数就可以估算了。
板式塔有多种形式,其中较重要的塔型有泡罩塔、筛板塔和浮阀塔,其他新型塔板多是在这三种塔板的基础上改进而成的。
除板式塔外,还有填料塔。
填料塔内没有塔板,但装有填料,在运行时组分是连续变化的,而不像板式塔那样是呈阶梯形的。
填料塔结构上不存在一层层塔板,但理论塔板数是一样的。
计算时,引入另一概念——理论板当量高度或等板高度,它是指相当于一块理论塔
板的分离能力所需要的某填料的高度,即所需填料高度等于理论塔板数与等板高度的乘积。
有关精馏技术及其设计问题的细节,可参阅有关化工原理书籍。
2.2.2吸附提纯
当流体与固体两相组成一个体系时,在两相的相界面处的组分与相内部不同,在固相表面产生了流体相的浓缩,这种现象称为吸附。
吸附现象的存在,使得能够利用某种固体有选择地凝聚溶液中的特定组分,使它得到分离,达到提纯的目的。
吸附提纯在工业中应用很广泛。
在硅材料工业中,吸附是重要的超提纯技术,如用于提纯甲硅烷、高纯氢等气体,可获得很好的提纯效果。
用来吸附流体组分的固体称为吸附剂,被吸附组分称为吸附质,不被吸附的组分称为惰性组分。
1.物理吸附与化学吸附
吸附可分为物理吸附和化学吸附两类。
物理吸附时并不发生任何化学变化,是由气相或液相分子与固体表面分子问的吸引力造成的,又称为“范德瓦尔吸附”,是一种可逆过程。
随着温度的升高或气压的降低,被吸附物质的分压与气相中分压达到平衡时,被吸附分子就不易再吸附而可能逸出列气相中去。
利用这种现象,可以进行脱附或对吸附剂进行再生操作。
在工业应用中,吸附和再生是可逆的循环过程。
化学吸附是由吸附质与固体间化学键作用引起的,这种吸附力大大超过物理吸附的范德瓦尔力,放出的吸附热也比物理吸附所放出的热大得多。
这类吸附多数是不可逆的,脱附以后原先的物质已发生化学变化。
2.工业中应用的吸附剂
广泛地讲固体表面都有吸附作用,但实际上只有多孔性物质由于有很大表面积,才具有明显的吸附效应。
作为工业用的吸附剂有活性碳、硅胶、活性氧化铝等。
近半个世纪以来,合成沸石迅速发展,它又称为分子筛,是具有特定均匀孔径的吸附剂。
成分可表为(M2+,M+)O·Al2O3·mSi02·nH2O,是含水的硅酸盐。
上式中,M表示K、Na、Ca等。
分子筛的孔径有3Ǻ,4Ǻ,5Ǻ等,分别称为3Ǻ,4Ǻ,5Ǻ分子筛等。
其实合成沸石有上百个种类,这些只是其中常用的几种。
由于分子筛晶体内有许多孔径均匀的孔道和排列整齐的孔穴,提供了大量的比表面,并有筛选分子的选择吸附作用。
分子筛又具有极性,对极性分子具有较强的亲和力。
分子筛的发展使吸附分离技术大大向前推进了一步。
3.吸附操作和设备
吸附操作可分为:
间歇操作:
流体和固体吸附剂同时置于一容器内,待充分吸附后吸附剂才与流体分离。
此方法只适宜于试验或小规模生产中。
半连续操作:
流体经过固定吸附床进行吸附,一定时间后吸附剂饱和,必须停止吸附,吸附剂经再生后,还可再进行吸附提纯。
连续操作:
流体和固体并向或逆向连续均匀地输入到移动床中,使其相互接触进行吸附,并分别连续地输出。
半连续操作使用的设备是固定床吸附器,连续操作使用的设备是移动床吸附器。
4.吸附平衡与吸附等温线
由于吸附剂表面引力场的作用,吸附质分子停留在吸附剂表面,但这并不意味着被吸附的分子不动。
由于分子的热运动,吸附质分子可沿着吸附剂表面扩散运动,同时也会发生脱附,脱附速率随吸附量的增大而增加,达到平衡时吸附的速率与脱附的速率相等,称为吸附平衡。
吸附物质的多少用吸附量c表示,在一定温度下吸附量c与吸附质相对压力变化P/P0的关系曲线称为吸附等温线,如图2.6所示。
其中P0为该吸附质的饱和蒸气压。
吸附等温线形状的不同表示了吸附能力变化的情况,这是重要的参考数据。
温度对吸附等温线
影响很大,因吸附是放热过程,温度越低吸附量越大,温度越高吸附量越小。
对于不同的吸附剂和吸附质,根据实验结果可得到不同的吸附等温线,图2.6所示为几种典型的吸附等温线。
5.固定床吸附器的传质过程
用固定床进行吸附,当流体进入吸附器时,吸附质首先在进口端吸附剂上被吸附。
由于吸附不可能瞬时完全完成,因此形成了吸附前沿,而且这一前沿不断向前移动,如图2.7所示。
吸附剂可分为三个区,即饱和区、传质区和未用区。
随着吸附过程的进行,未用区不断缩小。
当传质区前沿到达固定床出口时,未用区消失,这时吸附器已达到工作极限,失去吸附提纯的作用。
吸附前沿的形状与吸附等温线的形状密切相关。
如图2.8所示,等温线段(a)的传质区较窄,而等温线段(c)的传质区较宽。
所以等温线(a)称为优惠型吸附等温线,等温线(c)称为非优惠型吸附等温线,等温线(b)称为线性吸附等温线。
可见优惠型等温线可获得更为经济有效的吸附工艺过程。
前面列举的几种类型等温线中,有的可以分成若干段,有的段属于优惠型而有的段属于非优惠型。
因此,在固定床的设计和操作中应尽可能按优惠型来安排。
优惠型线段不但与吸附剂、吸附质的种类有关,还与所要分离的混合气体或溶液的状态有关,与相对压力有关。
6.吸附转效曲线
吸附转效曲线又称穿透曲线。
固定床中的吸附质浓度分布难以通过实验确定,通常是测定出口气的浓度变化间接地反映固定床的吸附能力,以床层出口流出气的吸附质浓度作为总体的衡量。
经再生过的床内仍残留少量吸附质x0,与之平衡的气相浓度为y0,如未经过吸附的气体中吸附质的浓度为ya,经过吸附后出口的气体应为y0。
只要在传质区还在固定床内,吸附前沿未达到出口之前,出口气的y0不变。
但当前沿到达出口后,吸附质的浓度开始从y0向ya增加。
固定床出口的吸附质浓度变化情况由穿透曲线表示,如图2.9所示。
图中B点为系统的突破点,D点为床层饱和点,时间tb称为穿透时间,它表示该固定床可供工作的时间。
对于同一种吸附质,选用不同吸附剂可以有不同的吸附转效曲线。
斜率较大的转效曲线对应的传质区短,而吸附速度较快。
关于吸附床的设计计算问题的细节请参阅有关化工原理书籍。
7.固定床的脱附与再生
物理吸附的最大优点是其为一种可逆的过程,吸附剂经脱附(再生)后可循环使用,不必每次更换吸附剂。
脱附操作主要有两种方法:
升温脱附:
吸附等温线随温度而改变,高温时平衡吸附量减少,因此吸附饱和的吸附剂在高温时可以脱附。
固定床在加热脱附的同时必须通入吹扫气体以带走脱附下来的吸附质,以免降温后重新吸附。
加热的方式有两种:
一种是先加热吹扫气体,用热的气体吹扫脱附。
吹扫气体应为惰性组分。
第二种加热方式是在床内装有加热设备,再生时加热吸附剂,并同时吹入气体。
降压脱附:
降压脱附是沿着等温线进行的,降低压力是为了降低吸附质的分压,通过吸附质的分压下降使平衡的吸附量下降而达到脱附的目的。
如在高压下吸附,可在常压下脱附。
如在常压下吸附,可以真空脱附。
通常把采用降压脱附的整个吸附操作称为变压吸附。
变压吸附具有能耗低、脱附时间短、一次能去除多种杂质、操作方便等优点。
有的吸附操作必须综合上述脱附方式进行。
例如用5Ǻ分子筛吸附提纯甲硅烷时,主要分离的对象是磷化氢。
在脱附时不允许立即加热,因为这些固定床中充满大量甲硅烷,加热会分解而阻塞孔隙使分子筛失效。
这时,必须在常温下用真空脱附一段时间,而后再加热并用氢气吹扫,达到深度再生的目的。
2.3物理提纯
物理提纯技术的提高几乎与半导体科学技术的发展并驾齐驱。
区域提纯方法最成功地用于锗元素的提纯上,使得高纯锗小数点后达到了8个“9’’以上的纯度。
在半导体技术中,物理提纯不是泛指各种物理方法的提纯技术,而是专指由分凝现象而实现的提纯技术——区域熔化提纯和正常凝固提纯。
2.3.1分凝现象
完全互溶的二元系的固液相图如图2.10所示。
某一p组分的材料熔化为液体后,温度缓慢降低冷却至T1温度,正好与液相线接触,在达到平衡的状态下开始凝固。
由图2.10可知,在T1温度下与p组分的液相平衡的是q组分的固相。
由此可见固熔体熔化后再结晶时,凝固出来的固相中所含
组分与原先的组分不同。
原先p组分的液相中B的含量大而新凝固的q组分的固相中B的含量小。
这种现象称为分凝现象。
对微量杂质的分凝,在物理化学中表达为分配定律:
互相平衡的单元二相系中加入少量另一成分,实验指出在一定温度下这种成分在两相内的浓度比保持恒定。
关于分配定律的导出,见第三章3.1.6节。
从图2.10的相图可知,当组分接近于单一组分时,液相线和固相线可近似为直线段,如图2.11所示。
因此,成分B在固相中的成分与在液相中的成分的比值为一定,可表达为
为方便起见,液相中的杂质浓度用平均值计算,以CL0表示。
引入有效分凝系数
代替
的关系由图2.12可知对于k0<1的情形有效分凝系数keff>k0。
有效分凝系数的具体数值随凝固过程的参数和条件而变,它将在晶体生长原理及基本技术一章中予以深入讨论。
2.3.2正常凝固
将材料全部熔化为液体,然后由一点开始结晶,逐渐扩展,而后全部凝固,切氏法等晶体生长方法可以简化为这样的过程。
具有这样一种特征的凝固过程,称为正常凝固过程。
如图2.13所示,令锭长为1、截面面积为l,正常凝固的杂质分布可从求解杂质分布微分方程而得。
设沿固体锭的杂质浓度分布为Cs(z),在固液界面移动达到z点时,界面继续前进dz,凝固到固体中的杂质为Csdz,液相中杂质的变化为(CL一Cs)dz,同时可写为(1一z)dCL,方程式为
2.3.3区域提纯
正常凝固的提纯只能进行一次,第二次再熔化时只作上一次结晶的重复,得到的仍然是同样的结果。
区域熔化是熔化锭条的一部分,熔化的部分称为熔区。
当熔区从头到尾移动一次后,杂质随熔区移到尾部。
利用这种方法不只可以进行一次提纯,而且可以进行多次提纯,一次一次地移动熔区以达到很好的提纯效果,该方法称为区域熔化提纯,简称为区域提纯。
1.一次区域提纯
如图2.14所示,材料截面为l,长度为l,熔化区域长度为l,凝固部分长度为z。
设熔区前进dz,液区中杂质含量增加了新熔化部分的杂质C0dz,减少了凝固出去的杂质Csdz,净增(C0-Cs)dz。
由此可得
利用
可得
边界条件
求得
对于k《1的杂质,在大部分固体中符合
这可视为杂质几乎全部留在液体中,末凝固部分体积为(1一z),液相中的杂质浓度为
乘以k
即得固相浓度,只在很接近尾部时才偏离此值。
即
求解得
式中,A为常数。
边界条件为
2.多次区域提纯
多次区域提纯能够得到更高的纯度,但也不可能把纯度无限提高。
对于一定熔区宽度l,有一极限分布。
若已达到这一极限分布后再进行区域提纯,熔区经过后固体中的杂质分布将仍然不变。
设达到极限的分布为C(ξ),如果继续进行区域提纯,在x处的熔区把x—x+l范围熔化,熔区