材料工程系模具设计与制造专业11.docx
《材料工程系模具设计与制造专业11.docx》由会员分享,可在线阅读,更多相关《材料工程系模具设计与制造专业11.docx(17页珍藏版)》请在冰豆网上搜索。
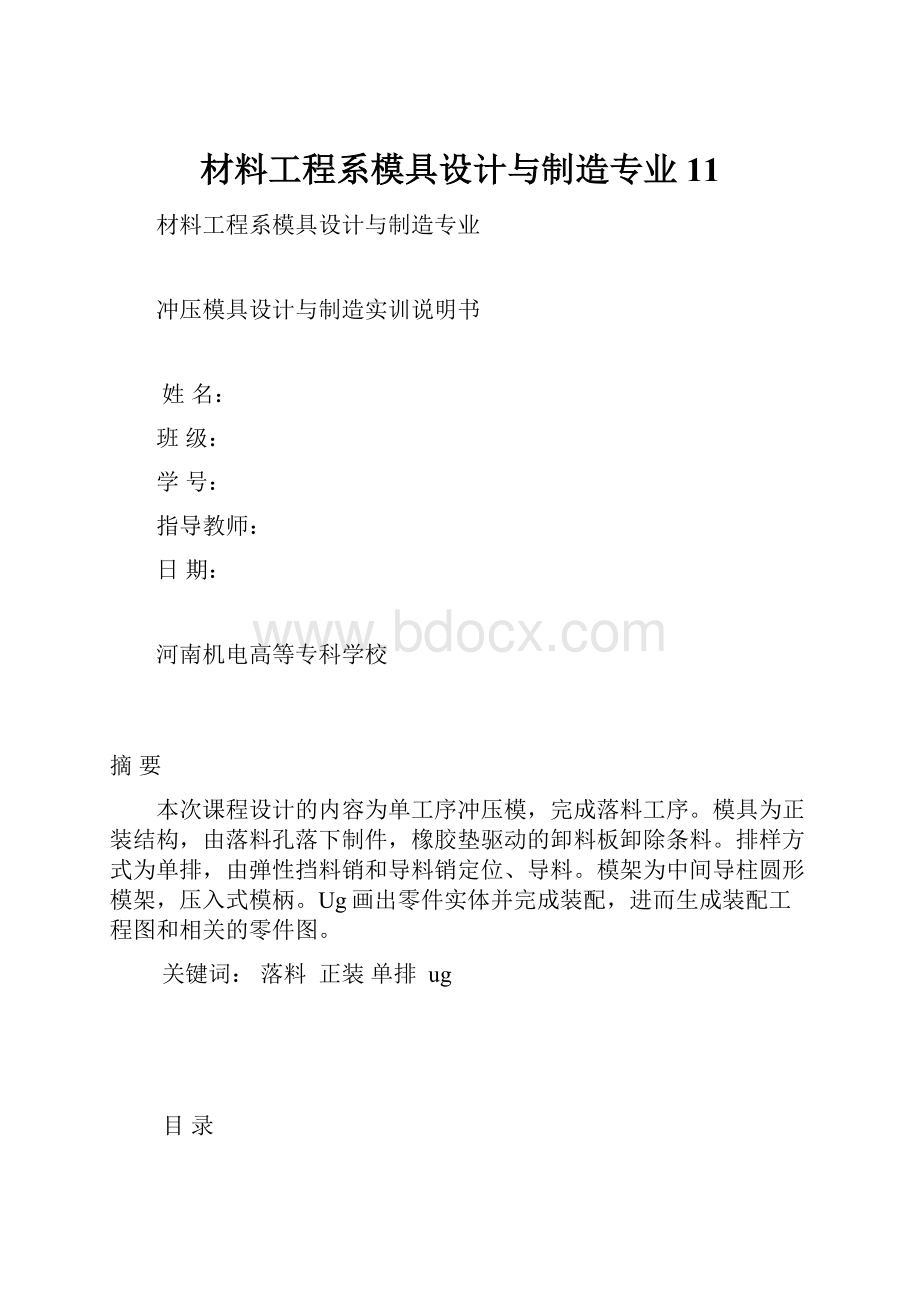
材料工程系模具设计与制造专业11
材料工程系模具设计与制造专业
冲压模具设计与制造实训说明书
姓名:
班级:
学号:
指导教师:
日期:
河南机电高等专科学校
摘要
本次课程设计的内容为单工序冲压模,完成落料工序。
模具为正装结构,由落料孔落下制件,橡胶垫驱动的卸料板卸除条料。
排样方式为单排,由弹性挡料销和导料销定位、导料。
模架为中间导柱圆形模架,压入式模柄。
Ug画出零件实体并完成装配,进而生成装配工程图和相关的零件图。
关键词:
落料正装单排ug
目录
一、零件工艺性分析。
。
。
。
。
。
。
。
。
。
。
。
。
。
。
。
。
。
。
。
。
。
。
。
。
。
。
。
。
。
。
。
。
。
。
。
。
。
。
。
。
。
。
。
。
。
。
。
。
。
。
。
。
。
。
。
。
。
。
。
。
。
。
。
。
。
。
。
。
。
。
。
。
。
。
。
。
1、材料分析。
。
。
。
。
。
。
。
。
。
。
。
。
。
。
。
。
。
。
。
。
。
。
。
。
。
。
。
。
。
。
。
。
。
。
。
。
。
。
。
。
。
。
。
。
。
。
。
。
。
。
。
。
。
。
。
。
。
。
。
。
。
。
。
。
。
。
。
。
。
。
。
。
。
。
。
。
。
。
。
。
。
。
。
。
。
2、结构分析。
。
。
。
。
。
。
。
。
。
。
。
。
。
。
。
。
。
。
。
。
。
。
。
。
。
。
。
。
。
。
。
。
。
。
。
。
。
。
。
。
。
。
。
。
。
。
。
。
。
。
。
。
。
。
。
。
。
。
。
。
。
。
。
。
。
。
。
。
。
。
。
。
。
。
。
。
。
。
。
。
。
。
。
。
。
3、精度分析。
。
。
。
。
。
。
。
。
。
。
。
。
。
。
。
。
。
。
。
。
。
。
。
。
。
。
。
。
。
。
。
。
。
。
。
。
。
。
。
。
。
。
。
。
。
。
。
。
。
。
。
。
。
。
。
。
。
。
。
。
。
。
。
。
。
。
。
。
。
。
。
。
。
。
。
。
。
。
。
。
。
。
。
。
。
二、工艺方案确定。
。
。
。
。
。
。
。
。
。
。
。
。
。
。
。
。
。
。
。
。
。
。
。
。
。
。
。
。
。
。
。
。
。
。
。
。
。
。
。
。
。
。
。
。
。
。
。
。
。
。
。
。
。
。
。
。
。
。
。
。
。
。
。
。
。
。
。
。
。
。
。
。
。
。
。
。
。
。
。
。
三、工艺计算
1、压力中心及冲裁力的计算。
。
。
。
。
。
。
。
。
。
。
。
。
。
。
。
。
。
。
。
。
。
。
。
。
。
。
。
。
。
。
。
。
。
。
。
。
。
。
。
。
。
。
。
。
。
。
。
。
。
。
。
。
。
。
。
。
。
。
。
。
。
。
。
。
。
。
。
。
。
。
。
。
2、卸料力及推件力的计算。
。
。
。
。
。
。
。
。
。
。
。
。
。
。
。
。
。
。
。
。
。
。
。
。
。
。
。
。
。
。
。
。
。
。
。
。
。
。
。
。
。
。
。
。
。
。
。
。
。
。
。
。
。
。
。
。
。
。
。
。
。
。
。
。
。
。
。
。
3、凸凹模刃口尺寸的计算。
。
。
。
。
。
。
。
。
。
。
。
。
。
。
。
。
。
。
。
。
。
。
。
。
。
。
。
。
。
。
。
。
。
。
。
。
。
。
。
。
。
。
。
。
。
。
。
。
。
。
。
。
。
。
。
。
。
。
。
。
。
。
。
。
。
。
。
。
。
。
。
。
。
。
。
。
。
。
。
。
。
4、排样、计算条料宽度、确定步距及材料利用率的计算。
。
。
。
。
。
。
。
。
。
。
。
。
。
。
。
。
。
。
。
。
。
。
四、模具总体设计。
。
。
。
。
。
。
。
。
。
。
。
。
。
。
。
。
。
。
。
。
。
。
。
。
。
。
。
。
。
。
。
。
。
。
。
。
。
。
。
。
。
。
。
。
。
。
。
。
。
。
。
。
。
。
。
。
。
。
。
。
。
。
。
。
。
。
。
。
。
。
。
。
。
。
。
。
1、模具类型的选择。
。
。
。
。
。
。
。
。
。
。
。
。
。
。
。
。
。
。
。
。
。
。
。
。
。
。
。
。
。
。
。
。
。
。
。
。
。
。
。
。
。
。
。
。
。
。
。
。
。
。
。
。
。
。
。
。
。
。
。
。
。
。
。
。
。
。
。
。
。
。
。
。
。
。
。
。
。
。
。
。
。
。
。
。
2、操作方式。
。
。
。
。
。
。
。
。
。
。
。
。
。
。
。
。
。
。
。
。
。
。
。
。
。
。
。
。
。
。
。
。
。
。
。
。
。
。
。
。
。
。
。
。
。
。
。
。
。
。
。
。
。
。
。
。
。
。
。
。
。
。
。
。
。
。
。
。
。
。
。
。
。
。
。
。
。
。
。
。
。
。
。
。
3、卸料、出件方式。
。
。
。
。
。
。
。
。
。
。
。
。
。
。
。
。
。
。
。
。
。
。
。
。
。
。
。
。
。
。
。
。
。
。
。
。
。
。
。
。
。
。
。
。
。
。
。
。
。
。
。
。
。
。
。
。
。
。
。
。
。
。
。
。
。
。
。
。
。
。
。
。
。
。
。
。
。
。
。
。
。
。
。
。
。
4、确定送料方式。
。
。
。
。
。
。
。
。
。
。
。
。
。
。
。
。
。
。
。
。
。
。
。
。
。
。
。
。
。
。
。
。
。
。
。
。
。
。
。
。
。
。
。
。
。
。
。
。
。
。
。
。
。
。
。
。
。
。
。
。
。
。
。
。
。
。
。
。
。
。
。
。
。
。
。
。
。
。
。
。
。
。
。
。
。
。
。
。
。
。
5、确定导向方式。
。
。
。
。
。
。
。
。
。
。
。
。
。
。
。
。
。
。
。
。
。
。
。
。
。
。
。
。
。
。
。
。
。
。
。
。
。
。
。
。
。
。
。
。
。
。
。
。
。
。
。
。
。
。
。
。
。
。
。
。
。
。
。
。
。
。
。
。
。
。
。
。
。
。
。
。
。
。
。
。
。
。
。
。
。
。
。
。
。
五、标准模具零部件设计及选择。
。
。
。
。
。
。
。
。
。
。
。
。
。
。
。
。
。
。
。
。
。
。
。
。
。
。
。
。
。
。
。
。
。
。
。
。
。
。
。
。
。
。
。
。
。
。
。
。
。
。
。
。
。
。
。
。
。
。
。
。
。
。
。
。
。
。
。
。
。
。
。
。
。
。
。
。
1、工作零部件的设计。
。
。
。
。
。
。
。
。
。
。
。
。
。
。
。
。
。
。
。
。
。
。
。
。
。
。
。
。
。
。
。
。
。
。
。
。
。
。
。
。
。
。
。
。
。
。
。
。
。
。
。
。
。
。
。
。
。
。
。
。
。
。
。
。
。
。
。
。
。
。
。
。
。
。
。
。
。
。
。
。
。
。
。
。
。
2、定位零部件的设计。
。
。
。
。
。
。
。
。
。
。
。
。
。
。
。
。
。
。
。
。
。
。
。
。
。
。
。
。
。
。
。
。
。
。
。
。
。
。
。
。
。
。
。
。
。
。
。
。
。
。
。
。
。
。
。
。
。
。
。
。
。
。
。
。
。
。
。
。
。
。
。
。
。
。
。
。
。
。
。
。
。
。
。
。
。
3、压料、卸料零部件的设计。
。
。
。
。
。
。
。
。
。
。
。
。
。
。
。
。
。
。
。
。
。
。
。
。
。
。
。
。
。
。
。
。
。
。
。
。
。
。
。
。
。
。
。
。
。
。
。
。
。
。
。
。
。
。
。
。
。
。
。
。
。
。
。
。
。
。
。
。
。
。
。
。
。
。
。
4、支撑零部件的设计。
。
。
。
。
。
。
。
。
。
。
。
。
。
。
。
。
。
。
。
。
。
。
。
。
。
。
。
。
。
。
。
。
。
。
。
。
。
。
。
。
。
。
。
。
。
。
。
。
。
。
。
。
。
。
。
。
。
。
。
。
。
。
。
。
。
。
。
。
。
。
。
。
。
。
。
。
。
。
。
。
5、导向零部件的设计。
。
。
。
。
。
。
。
。
。
。
。
。
。
。
。
。
。
。
。
。
。
。
。
。
。
。
。
。
。
。
。
。
。
。
。
。
。
。
。
。
。
。
。
。
。
。
。
。
。
。
。
。
。
。
。
。
。
。
。
。
。
。
。
。
。
。
。
。
。
。
。
。
。
。
。
。
6、紧固零部件的选择。
。
。
。
。
。
。
。
。
。
。
。
。
。
。
。
。
。
。
。
。
。
。
。
。
。
。
。
。
。
。
。
。
。
。
。
。
。
。
。
。
。
。
。
。
。
。
。
。
。
。
。
。
。
。
。
。
。
。
。
。
。
。
。
。
。
。
。
。
六、压力机的选择。
。
。
。
。
。
。
。
。
。
。
。
。
。
。
。
。
。
。
。
。
。
。
。
。
。
。
。
。
。
。
。
。
。
。
。
。
。
。
。
。
。
。
。
。
。
。
。
。
。
。
。
。
。
。
。
。
。
。
。
。
。
。
。
。
。
。
。
。
。
。
。
。
。
。
。
。
。
。
。
七、绘制总装配图。
。
。
。
。
。
。
。
。
。
。
。
。
。
。
。
。
。
。
。
。
。
。
。
。
。
。
。
。
。
。
。
。
。
。
。
。
。
。
。
。
。
。
。
。
。
。
。
。
。
。
。
。
。
。
。
。
。
。
。
。
。
。
。
。
。
。
。
。
。
。
。
。
。
。
。
。
。
。
。
。
。
。
。
八、各个零件图及排样图。
。
。
。
。
。
。
。
。
。
。
。
。
。
。
。
。
。
。
。
。
。
。
。
。
。
。
。
。
。
。
。
。
。
。
。
。
。
。
。
。
。
。
。
。
。
。
。
。
。
。
。
。
。
。
。
。
。
。
。
。
。
。
。
。
。
。
。
。
。
。
。
。
。
。
。
。
九、工艺卡、工序卡。
。
。
。
。
。
。
。
。
。
。
。
。
。
。
。
。
。
。
。
。
。
。
。
。
。
。
。
。
。
。
。
。
。
。
。
。
。
。
。
。
。
。
。
。
。
。
。
。
。
。
。
。
。
。
。
。
。
。
十、说明书。
。
。
。
。
。
。
。
。
。
。
。
。
。
。
。
。
。
。
。
。
。
。
。
。
。
。
。
。
。
。
。
。
。
。
。
。
。
。
。
。
。
。
。
。
。
。
。
。
。
。
。
。
。
。
。
。
。
。
。
。
。
。
十一、参考文献。
。
。
。
。
。
。
。
。
。
。
。
。
。
。
。
。
。
。
。
。
。
。
。
。
。
。
。
。
。
。
。
。
。
。
。
。
。
。
。
。
。
。
。
。
。
。
。
。
。
。
。
。
。
。
。
。
。
。
。
。
。
。
。
。
。
。
。
。
。
。
。
。
。
。
。
。
。
。
。
。
。
。
。
一、零件工艺性分析
1、材料分析(摘自GB699-1999)
该制件材料为08钢,属于合金结构钢,冷变形时塑性高、低温时性能良好,其厚度t为2mm。
于相应含碳量的碳钢相比,其淬透性较高,但热处理时有过热、脱碳敏感性及回火脆性倾向。
热处理工艺:
对于直径或厚度小于25mm的钢材,正火保温时间不少于10min.空冷;淬火推荐保温时间不少于10min;回火保温时间不少于0.5h。
查参考文献1,其化学成分(%):
碳C:
0.05~0.11,硅Si:
0.17~0.37,锰Mn:
0.35~0.65,铬Cr≦0.30,硫S≦0.025,镍Ni≦0.30,铜Cu≦0.25。
查参考文献2表1.3,其力学性能:
抗剪强度
260~360MPa,抗拉强度σb215~410MPa,屈服强度σs为200MPa,断面收缩率60%,伸长率不小于27%,未热处理硬度不大于131HB。
2、结构分析
该零件为十字形件,为本次设计内容。
3、精度分析
图1-1
图示1-1零件未标注尺寸公差要求,按GB/T15055的m级可查得尺寸公差为±0.40mm,普通冲裁可以达到零件的精度要求。
由以上分析可知,该零件的冲裁性能好,冲裁加工能够达到设计要求。
二、工艺方案确定
该零件的工序有三道,有:
落料、卸料、送料。
其工艺路线有一条:
方案为:
落料、卸料、送料。
三、工艺计算
1、压力中心及冲裁力的计算
模具压力中心是指冲压时各个冲压部分冲压力合力的作用点。
为了确保压力机和模具正常工作,应使冲模的压力中心与压力机滑块的中心相重合。
对于带有模柄的冲压模,压力中心应通过模柄的轴心线。
否则会使冲模和压力机滑块产生偏心载荷,使滑块和导轨之间产生过大的磨损,模具导向零件加速磨损,降低模具和压力机的使用寿命。
冲模的压力中心,可按下述原则来确定:
(1)对称形状的单个冲裁件,冲模的压力中心就是冲裁件的几何中心。
冲裁直线段时,其压力中心位于直线段的中点。
(2)工件形状相同且分布位置对称时,冲模的压力中心与零件的对称中心相重合。
(3)冲裁形状复杂的零件或多凸模的零件时,其压力中心可以通过解析计算法求出。
现在需要落料的零件是一个十字形件,其压力中心就是其几何中心。
其压力中心的坐标为(Xo,Yo);
坐标公式为
;
Y
;
经计算得其压力中心为(29,26)。
用普通平刃口模具冲裁时,其冲裁力F一般按下式计算:
F=K×L×t×
式中F——冲裁力;
L——冲裁周边长度;
t——材料厚度;
—材料抗剪强度;K——系数。
系数K是考虑到实际生产中,模具间隙值的波动和不均匀、刃口的磨损、板料力学性能和厚度波动等因素的影响而给出的修正系数。
一般取K=1.3。
为计算简便,也可按下式估算冲裁力:
F≈K×L×t
在材料抗剪强度为260MPa时,其冲裁力Fa=1.3×220×2×260=148720N=148.72KN;
在材料抗剪强度为360MPa时,其冲裁力Fb=1.3×220×2×360=205920N=205.92KN;
故其冲裁力在148.72KN~205.92KN,选其冲裁力为200KN。
2、卸料力推件力的计算
冲裁后,由于板料的弹性恢复,由于冲裁后板料的弹性恢复,使条料紧卡在凸模上,需要把条料从凸模上卸下来的力称卸料力Fx。
此处所设计的模具为落料模,通过卸料板将卡在凸模上的条料卸下来,故有卸料力存在。
采用的凹模刃口为阶梯式,在冲裁是会有冲裁件卡在凹模中,又需要推件力。
由于所冲完的冲裁件是直接从凹模落下,所以不需要在凹模下设置顶件装置,故不存在顶件力。
查参考文献2表2-7得卸料力系数Kx=0.02-0.05mm,取0.045mm,推件力系数Kt=0.045mm,卡在凹模内冲裁件的个数n。
查参考文献2表3-2,得冲裁凹模洞口的直刃壁高度h﹥8~10mm,取h=8mm。
卸料力:
Fx=KxF=0.045×200=9KN;
卡在凹模内冲裁件的个数:
n
=4;
推件力:
Ft=nKtF=4×0.045×200=36KN;
冲裁时,压力机的公称压力必须大于或等于各种冲压力的总和
。
在此次模具设计中采用弹压卸料装置和下出料的方式
=F+Fx+Ft
经计算得
=245KN。
图1-2
3、凸凹模刃口尺寸的计算
凸模和凹模的刃口尺寸和公差,直接影响冲裁件的尺寸精度。
模具的合理间隙也靠凸、凹模的刃口尺寸及其公差来保证。
由于模具加工方法不同,凸模与凹模刃口部分尺寸的计算公式与制造公差的标注也不同,刃口尺寸的计算方法可分为两类,一个是凹模与凸模分别加工法,另一个是凹模与凸模配合加工法。
分别加工法是指凸模和凹模分别按图纸标注的尺寸和公差进行加工,冲裁间隙由凸模、凹模刃口尺寸和公差来保证,需要分别标注凸模和凹模刃口尺寸与制造公差(凸模δp、凹模δd)。
其优点是具有互换性,但受到冲裁间隙的限制,它适用于圆形或简单规则形状(方形或矩形)的冲压件。
落料凸凹模刃口计算
查参考文献2:
表2-4得Z
=0.640mmZ
=0.460mm,
表2-5得δ凹=+0.030mm,δ凸=-0.020mm,
表2-6得x=0.5
落料
=
=
=
mm;
=
=
=
mm;
=
=
=
mm;
=
=
=
mm;
=
=
=
mm;
=
=
=
mm;
校核间隙|δ凹|+|δ凸|=(0.020+0.030)mm=0.050mm﹤Znax-ZMIN﹦(0.640-0.460)=0.18mm,故符合条件。
4、排样、计算条料宽度、确定步距、材料利用率
1)排样方式的选择
方案一:
有废料排样沿冲件外形冲裁,在冲件周边都留有搭边。
冲件尺寸完全由冲模来保证,因此冲件精度高,模具寿命高,但材料利用率低。
方案二:
少废料排样因受剪切条料和定位误差的影响,冲件质量差,模具寿命较方案一低,但材料利用率稍高,冲模结构简单。
方案三:
无废料排样冲件的质量和模具寿命更低一些,但材料利用率最高。
通过上述三种方案的分析比较,综合考虑模具寿命和冲件质量,该冲件的排样方式选择方案一为佳。
考虑模具结构和制造成本有废料排样的具体形式选择直排最佳。
2)计算条料宽度
搭边的作用是补偿定位误差,保持条料有一定的刚度,以保证零件质量和送料方便。
搭边过大,浪费材料。
搭边过小,冲裁时容易翘曲或被拉断,不仅会增大冲件毛刺,有时还有拉入凸、凹模间隙中损坏模具刃口,降低模具寿命。
搭边值通常由表2.9(文献2)所列搭边值和侧搭边值确定。
根据零件形状,查表2.9,并考虑到工件的切边,工件之间搭边值a=2.5mm,工件与侧边之间搭边值取a1=2.8mm,条料是有板料裁剪下料而得,为保证送料顺利,规定其上偏差为零,下偏差为负值—△
B0△=(Dmax+2a1)0△
式中Dmax—条料宽度方向冲裁件的最大尺寸;
a1---工件与侧边之间搭边值取。
△—板料剪裁下的偏差;(其值查表2.91)可得△=0.8mm。
B0△=52.04+2×2.8
=
mm
故条料宽度为47.68mm。
表2.9搭边值和侧边值的数值
材料厚度t(mm)
圆件及类似圆形制件r>2t
矩形或类似矩形制件边长≤50
矩形或类似矩形制件边长>50
工件间a
侧边a1
工件间a
侧边a1
工件间a
侧边a1
≤0.25
1.8
2.0
2.2
2.5
2.8
3.0
>0.25~0.5
1.2
1.5
1.8
2,0
2.0
2.5
>1.6~2.0
1.2
1.5
1.8
2.5
2.0
2.2
>2.0~2.5
1.5
1.8
2.0
2.2
2.2
2.5
>2.5~3.0
1.8
2.2
2.2
2.5
2.5
2.8
>3.0~3.5
2.2
2.5
2.5
2.8
2.8
3.2
表2.91普通剪床用带料宽度偏差△(mm)
条料厚度t(mm)
条料宽度b(mm)
≤50
>50~100
>100~200
>200
≤1
0.4
0.5
0.6
0.7
>1~2
0.5
0.6
0.7
0.8
>2~3
0.7
0.8
0.9
1.0
>3~5
0.9
1.0
1.1
1.2
3)步距的确定
送料步距S:
条料在模具上每次送进的距离称为送料步距,每个步距可冲一个或多个零件。
进距与排样方式有关,是决定侧刃长度的依据。
条料宽度的确定与模具的结构有关。
进距确定的原则是,最小条料宽度要保证冲裁时工件周边有足够的搭边值;最大条料宽度能在冲裁时顺利的在导料板之间送进条料,并有一定的间隙。
级进模送料步距S
S=Dmax+a1
Dmax零件横向最大尺寸,a1搭边
S=58.04+2.5
=60.54mm
排样图如图3-1所示。
图3-1排样图
4)材料利用率的计算
冲裁件的实际面积与所用板料面积的百分比叫材料的利用率,它是衡量合理利用材料的重要指标。
一个步距内的材料利用率
η=A/BS×100%
式中 A—一个步距内冲裁件的实际面积;
B—条料宽度;
S—步距;
由此可之,η值越大,材料的利用率就越高,废料越少。
废料分为工艺废料和结构废料,结构废料是由本身形状决定的,一般是固定不变的,工艺废料的多少决定于搭边和余量的大小,也决定于排样的形式和冲压方式。
因此,要提高材料利用率,就要合理排样,减少工艺废料。
排样合理与否不但影响材料的经济和利用,还影响到制件的质量、模具的的结构和寿命、制件的生产率和模具的成本等指标。
因此,排样时应考虑如下原则:
1)、提高材料利用率(不影响制件使用性能的前提下,还可以适当改变制件的形状)。
2)、排样方法使应操作方便,劳动强度小且安全。
3)、模具结构简单、寿命高。
4)、保证制件质量和制件对板料纤维方向的要求。
一个步距内冲裁件的实际面积,运用CAD软件,工具-查询-面积:
A=2760mm2
所以一个步距内的材料利用率
Η=A/BS×100%
=2760/60.54×57.64×100%
=79.09%
根据计算结果知道选用直排材料利用率可达79.09%,满足要求。
四、模具总体设计
1、模具类型的选择
由冲压工艺分析可知,采用单工序模冲压,所以模具类型为单工序模。
2、操作方式
零件的生产批量为大批量,但合理安排生产可用手动送料方式,既能满足生产要求,又可以降低生产成本,提高经济效益。
3、卸料、出件方式
1)卸料方式
刚性卸料与弹性卸料的比较:
刚性卸料是采用固定卸料板结构。
常用于较硬、较厚且精度要求不高的工件冲裁后卸料。
当卸料板只起卸料作用时与凸模的间隙随材料厚度的增加而增大,单边间隙取(0.2~0.5)t。
当固定卸料板还要起到对凸模的导向作用时卸料板与凸模的配合间隙应该小于冲裁间隙。
此时要求凸模卸料时不能完全脱离卸料板。
主要用于卸料力较大、材料厚度大于2mm且模具结构为倒装的场合。
弹压卸料板具有卸料和压料的双重作用,主要用于料厚小于或等于2mm的板料由于有压料作用,冲件比较平整。
卸料板与凸模之间的单边间隙选择(0.1~0.2)t,若弹压卸料板还要起对凸模导向作用时,二者的配合间隙应小于冲裁间隙。
常用作落料模、冲孔模、正装复合模的卸料装置。
工件平直度较高,料厚为2mm相对较薄,卸料力较小,弹压卸料模具比刚性卸料模具方便,操作者可以看见条料在模具中的送进动态,且弹性卸料板对工件施加的是柔性力,不会损伤工件表面,所以采用弹性卸料。
2)出件方式
因采用连续模生产,故采用向下落料出件。
4、确定送料方式
因选用的冲压设备为开式压力机且垂直于送料方向的凹模宽度B小于送料方向的凹模长度L故采用横向送料方式,即由前向后送料。
5、确定导向方式
方案一:
采用对角导柱模架。
由于导柱安装在模具压力中心对称的对角线上,所以上模座在导柱上滑动平稳。
但上下配合度不好。
方案二:
采用后侧导柱模架。
由于前面和左、右不受限制,送料和操作比较方便。
因为导柱安装在后侧,工作时,偏心距会造成导套导柱单边磨损,严重影响模具使用寿命,且不能使用浮动模柄。
方案三:
四导柱模架。
具有导向平稳、导向准确可靠、刚性好等优点。
常用于冲压件尺寸较大或精度要求较高的冲压零件,以及大量生产用的自动冲压模架。
方案四:
中间导柱模架。
导柱安装在模具的对称线上,导向平稳、准确。
常用于纵向送料的落料模、复合模。
根据以上方案比较并结合模具结构形式和送料方式,为提高模具寿命和工件质量,该级单工序模采用中间导柱模架的导向方式,即方案四最佳。