稀油站控制系统改造中的经验总结互联网+.docx
《稀油站控制系统改造中的经验总结互联网+.docx》由会员分享,可在线阅读,更多相关《稀油站控制系统改造中的经验总结互联网+.docx(6页珍藏版)》请在冰豆网上搜索。
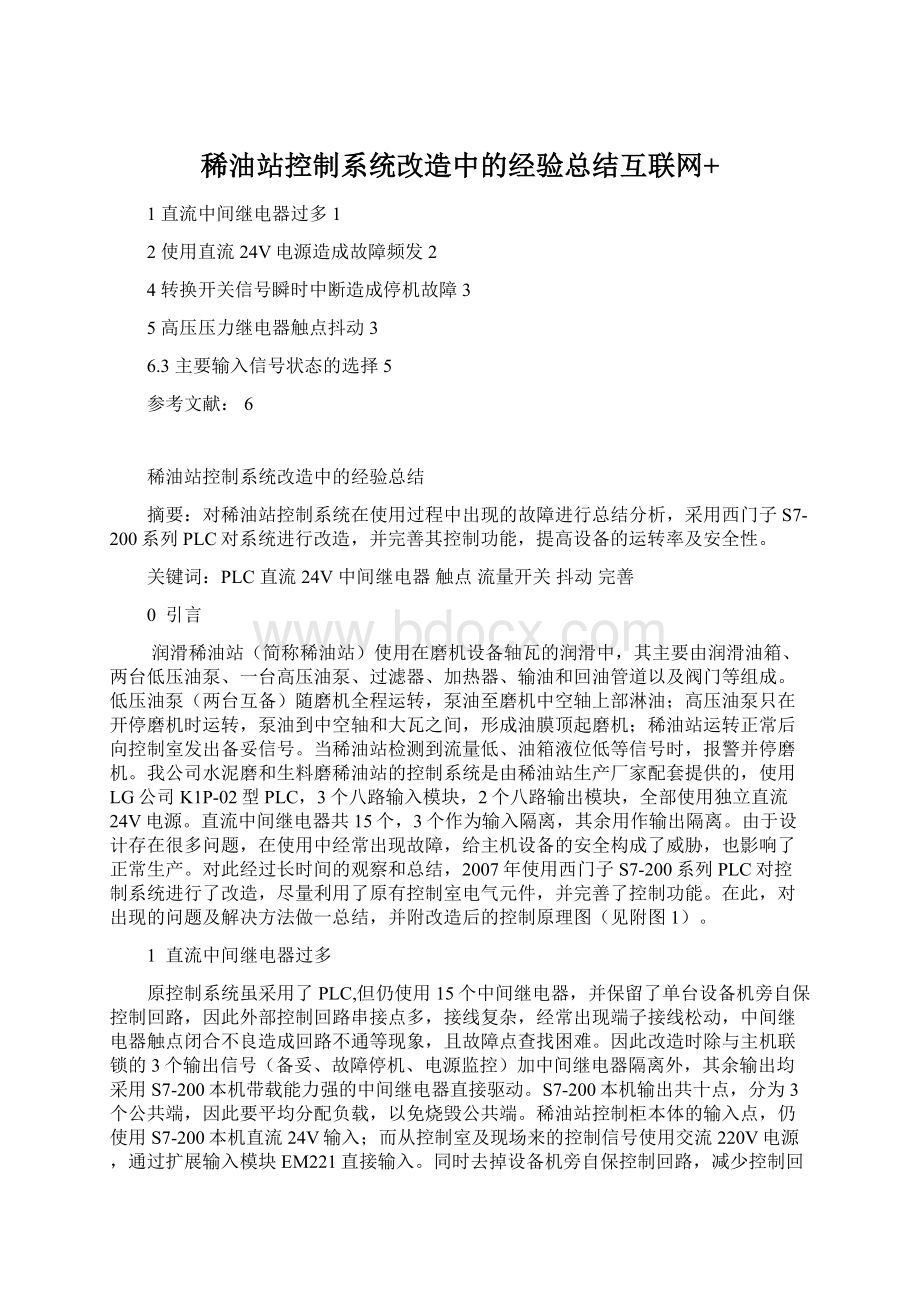
稀油站控制系统改造中的经验总结互联网+
1直流中间继电器过多1
2使用直流24V电源造成故障频发2
4转换开关信号瞬时中断造成停机故障3
5高压压力继电器触点抖动3
6.3主要输入信号状态的选择5
参考文献:
6
稀油站控制系统改造中的经验总结
摘要:
对稀油站控制系统在使用过程中出现的故障进行总结分析,采用西门子S7-200系列PLC对系统进行改造,并完善其控制功能,提高设备的运转率及安全性。
关键词:
PLC直流24V中间继电器触点流量开关抖动完善
0引言
润滑稀油站(简称稀油站)使用在磨机设备轴瓦的润滑中,其主要由润滑油箱、两台低压油泵、一台高压油泵、过滤器、加热器、输油和回油管道以及阀门等组成。
低压油泵(两台互备)随磨机全程运转,泵油至磨机中空轴上部淋油;高压油泵只在开停磨机时运转,泵油到中空轴和大瓦之间,形成油膜顶起磨机;稀油站运转正常后向控制室发出备妥信号。
当稀油站检测到流量低、油箱液位低等信号时,报警并停磨机。
我公司水泥磨和生料磨稀油站的控制系统是由稀油站生产厂家配套提供的,使用LG公司K1P-02型PLC,3个八路输入模块,2个八路输出模块,全部使用独立直流24V电源。
直流中间继电器共15个,3个作为输入隔离,其余用作输出隔离。
由于设计存在很多问题,在使用中经常出现故障,给主机设备的安全构成了威胁,也影响了正常生产。
对此经过长时间的观察和总结,2007年使用西门子S7-200系列PLC对控制系统进行了改造,尽量利用了原有控制室电气元件,并完善了控制功能。
在此,对出现的问题及解决方法做一总结,并附改造后的控制原理图(见附图1)。
1直流中间继电器过多
原控制系统虽采用了PLC,但仍使用15个中间继电器,并保留了单台设备机旁自保控制回路,因此外部控制回路串接点多,接线复杂,经常出现端子接线松动,中间继电器触点闭合不良造成回路不通等现象,且故障点查找困难。
因此改造时除与主机联锁的3个输出信号(备妥、故障停机、电源监控)加中间继电器隔离外,其余输出均采用S7-200本机带载能力强的中间继电器直接驱动。
S7-200本机输出共十点,分为3个公共端,因此要平均分配负载,以免烧毁公共端。
稀油站控制柜本体的输入点,仍使用S7-200本机直流24V输入;而从控制室及现场来的控制信号使用交流220V电源,通过扩展输入模块EM221直接输入。
同时去掉设备机旁自保控制回路,减少控制回路中间环节。
改造后,隔离中间继电器由15个减少至3个,极大的简化了电路,降低了故障的发生次数。
2使用直流24V电源造成故障频发
24V信号的问题首先是易受干扰。
稀油站控制柜到控制室的控制电缆约100米长,整个磨系统设备的电缆在一个电缆沟内,使得有些控制线感应电压值经测量高达100V,对直流24V信号有很大的干扰;而且两种不同电压的控制线接在控制室操作台的一排端子上,处理故障时易混淆。
其次是直流24V电源的导通性不好。
从现场采集的压力、温度等信号,虽然相应继电器达到设定值动作,触点已闭合,但由于现场粉尘大,直流24V信号无法导通送至PLC,因此程序不能输出应有的动作,导致发生设备事故;有时虽然使用工具吹净粉尘,又因压力表触点氧化,也会造成上述现象。
所以改造时采用S7-200的EM221扩展输入模块采集上述信号,交流220V电压信号直接输入,不用隔离中间继电器,这样既提高了信号抗干扰能力,又克服了因粉尘大、触点氧化致使信号导通性差的缺点。
3低压压力继电器工作不可靠
稀油站低压压力的大小原来是通过低压管道末端出口阀门调节的,因此岗位工有时刻意的关闭阀门以达到要求的压力值而忽略供油量,造成供油少时磨瓦润滑状况不佳,或供油多时油从瓦盒外溢的现象。
由于磨瓦设备正常运转的条件是20L/Min的供油量,而不是0.4MPa的低压压力。
因此改造时将低压压力继电器更换为密封性较好的流量开关,再加上信号电源采用交流220V直接输入EM221扩展模块,这样使得信号采集准确可靠,调节供油量方便无误。
4转换开关信号瞬时中断造成停机故障
由于原稀油站控制柜的远驱\机旁、低压泵选择等转换开关在任一选择状态下,相对应的PLC输入通道都有信号输入,因此在远驱状态主机设备运转时易出现信号瞬时中断致使稀油站不工作,因而停磨主机。
而且这样的故障比较隐蔽,易误导工作人员的思路。
造成这种故障的原因是粉尘大、触点氧化、意外振动、接线虚等。
因此,改造中在设计电路时把远驱\机旁选择开关的远驱状态及低压泵选择转换开关的主泵状态设定为信号不输入,即图1中SA1、SA2所示,就可消除此种故障的发生。
5高压压力继电器触点抖动
高压压力继电器安装在高压供油管路上,油泵的机械振动造成触点抖动;夏季油温高,回油落差产生的油沫、气泡造成供油不稳,也会出现这个现象。
触点抖动使得高压压力的信号采集不稳定,造成信号保持达不到PLC程序设定时间,备妥继电器无驱动,延误开停主机。
改造中,在PLC内部程序加高压低报警延时2s,同时信号电压改为交流220V,高压压力继电器增加适当的防尘措施,如安装表盖时加装一个密封垫,接线出口用自粘带缠绕密封,即可防止灰尘进入表体内部,保证触点稳定可靠的导通。
6PLC控制功能的完善
6.1单台设备报警功能的实现
设备报警信号与输入信号(备妥、驱动和应答)的逻辑关系是:
报警信号是应答信号与驱动信号“异或“后,和备妥信号进行“或”运算的结果,即Y=R1+(D⊕R2)。
`
报警信号与输入信号的真值表如表1:
表1
备妥R1
驱动D
应答R2
报警Y
0
0
0
1
0
0
1
1
0
1
0
1
0
1
1
1
1
0
0
0
1
0
1
1
1
1
0
1
1
1
1
0
在实际应用中,因驱动、应答信号之间有小的时间差,会导致系统立即误发出设备报警信号,所以还应在两信号“异或”后加一定的延时。
另外,延时时间不能设定太长,一般设为1-2s,以防止设备过载故障时撤掉了应答信号但程序无法执行仍保持驱动输出。
6.2PLC工作电源断电无法停主机
稀油站控制柜的电源由配电所独立空气开关供电,运转中PLC检测到稀油站的故障后驱动故障停机中间继电器(图1中的ZJ1),闭合主机故障跳闸回路。
但若供电电缆短路或稀油站控制柜内线路故障等原因致使供电空气开关跳闸,则PLC不能及时闭合跳闸回路停主机,造成重大设备事故。
因此选用S7-200内部特殊状态位SM0.0驱动PLC继电器,将电源监控继电器(图1中的ZJ3)常闭点与故障跳闸回路并联,即可实现断电保护功能。
6.3主要输入信号状态的选择
稀油站输入PLC的监控信号中,高压压力及流量信号的准确无误是保障设备安全运转的关键,而信号状态的选择起决定作用。
实际使用中,主要考虑PLC采集不到真实的设备运转状况,执行相应的动作来保护设备的安全。
造成的因素诸如触点导通差、电缆断线、接线松动等。
选择不同的开关触点动作状态来传输信号,并相应命名一个信号名称。
见下表2:
表2
表结果中,选择B或C最佳,使用时依个人不同思维方法及编程习惯选用。
我们在此稀油站高压压力及流量信号使用中选择了C类。
7结论
此次稀油站控制系统的改造运行一年多来,因油站故障停主机次数由原来的月平均7次降低至1-2次,解决了因原控制上的缺陷可能造成磨瓦损坏或翻瓦的事故发生。
在改造中尽量简化外部电路,充分发挥PLC的优点;考虑到现场的使用环境,选择了合适的控制电压;并深入了解设备工况要求及可能发生的特殊情况,进一步完善系统的控制功能。
参考文献:
1西门子公司SIMATICS7-200系统手册2003
2刘介才工厂供电书号7-111-05927-1机械工业出版社
3白公怎样阅读电气工程图书号7-111-08699-62007.1
机械工业出版社
图1改造后的控制原理图