挡条套塑料模具方案设计书与制造.docx
《挡条套塑料模具方案设计书与制造.docx》由会员分享,可在线阅读,更多相关《挡条套塑料模具方案设计书与制造.docx(17页珍藏版)》请在冰豆网上搜索。
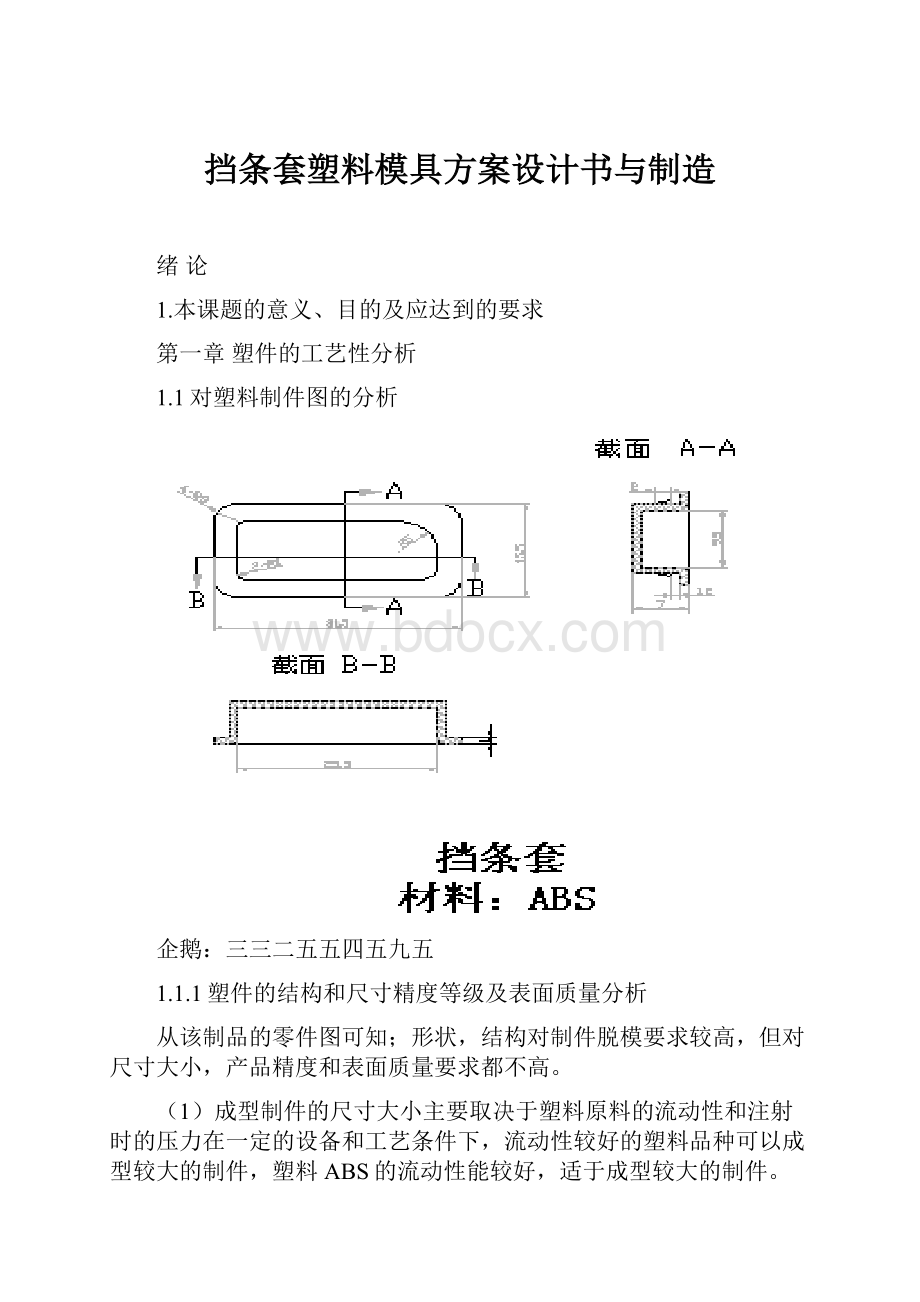
挡条套塑料模具方案设计书与制造
绪论
1.本课题的意义、目的及应达到的要求
第一章塑件的工艺性分析
1.1对塑料制件图的分析
企鹅:
三三二五五四五九五
1.1.1塑件的结构和尺寸精度等级及表面质量分析
从该制品的零件图可知;形状,结构对制件脱模要求较高,但对尺寸大小,产品精度和表面质量要求都不高。
(1)成型制件的尺寸大小主要取决于塑料原料的流动性和注射时的压力在一定的设备和工艺条件下,流动性较好的塑料品种可以成型较大的制件,塑料ABS的流动性能较好,适于成型较大的制件。
在这里排水管头注塑模具的尺寸较小,注塑时的压力要求不太大,一般的注塑压力就能满足。
(2)制品的精度等级;塑料制件的尺寸精度主要取决于塑料收缩率的波动和模具制造误差,此处塑料件未注公差,由于该制件的原材料为ABS,而ABS的制件公差等级较低为MT5级,该塑件的精度等级较低。
(3)制品的表面质量;塑料制件的精度等级较低,我们所要获得的制件对制品的表面质量除要求无缺陷,毛刺,无特殊要求,一般的模具制造工艺和注塑工艺就能满足要求。
(4)制品的形状结构;制品的壁厚均匀为3mm。
符合ABS的最小壁厚原则,制件的四周有四个小凸台,需要考虑侧向分型,增加了模具设计的难度,需由于制件的尺寸较小,ABS的强度较大不需增设加强筋。
1.1.2制件所用塑料的性能分析
本制件所用的材料是ABS,ABS的性能如下:
(1)吸湿性强。
成型前须充分干燥要求其含水量小于1%,对于表面光泽要求较高的制品,需长时间干燥。
(2)流动性较好(溢边值为0.04mm左右)易于充模,粘度对剪切速率较敏感,同时还与注射温度和注射压力有关,其中注射压力影响较为显著,因此提高流动性要从提高注射压力入手。
(3)成型难度大,须采用较高的料温和模温。
对于耐热抗冲击性和中抗冲击性制件,应在允许的范围内料温取较大值。
(4)精度对之制件影响较大,有破坏ABS橡胶相的倾向,通常ABS在250℃左右变色,270℃开始分解。
(5)若制件精度要求较高模温宜采取50~60℃,若制件表面要求具有光泽模温宜取60~80℃。
(6)注射压力应比聚苯乙烯较大,采用螺杆式注塑机料温可取160~220℃,注射压力可取70~90MPa。
(7)模具设计过程中注意事项,浇注系统流动阻力应尽可能小,浇口位置及形式应合理并能防止熔接痕的产生,同时要考虑模具制造的经济性和加工的合理性。
1.2计算塑料制件的体积和质量
计算塑件的体积和质量是为了选用注塑机及确定模具型腔数量。
计算塑料制件的体积:
V=2041㎜3
塑件质量计算:
W=V×ρ
=2041×
×1.1
=2.25g
(在这里为大致计算,其中圆角和凸台的尺寸可不预考虑,在选取注塑机时适当放缩。
)
查《模具设计与制造简明手册》知ABS塑料密度为ρ=1.02~1.16g/㎜3
1.3ABS塑料注射成型的工艺参数。
(注塑工艺卡)
(试模时,可根据实际情况作适当调整)
注射温度包括料筒温度和喷嘴温度
料筒温度:
后段温度t1选用150~170℃
中段温度t2选用165~180℃
前段温度t3选用180~200℃
注塑压力:
选用55~65Mpa
注塑时间:
选用0~5s
保压压力:
选用65Mpa
保压时间:
选用10s
冷却时间选用15s
喷嘴温度:
180~190℃
1.4塑料成型设备的选取
根据计算及原材料的注射成型参数,考虑塑件的外形尺寸,注塑时所需压力和工厂现有设备等情况,初选注塑机为xs-zy-125.查文献[7]可知xs-zy-125型的主要参数:
理论注射量(最大):
125㎝3
螺杆直径:
42㎜
注射压力:
119KN
注射行程:
115㎜
注射时间:
1.6s
注射方式:
螺杆式
锁模力:
900KN
最大成型面积:
320㎝2
模板行程:
300㎜
模具最大高度:
300㎜
模具最小高度:
200㎜
1.5注射成型工艺条件
注射成型过程中需要控制的温度有料筒温度、喷嘴温度和模具温度等。
塑化物料的温度(塑化温度)和从喷嘴注射出来的熔体温度(注射温度)主要取决于料筒和喷嘴两部分的温度,热塑性塑料在受热时的变化曲线如下图所示:
图中,A、B、C、D四区分别对应塑料的玻璃态、高弹性态、可塑态和分解态,料筒温度应参照C区的流动温度和分解温度来确定。
喷嘴温度通常略低于料筒的温度,以防止在直通式喷嘴口发生“流涎现象”。
第二章注射模的结构设计
2.1分型面的确定
制品在模具中的位置,直接影响到模具结构的复杂程度。
选择分型面的原则是:
塑件脱出方便、模具结构简单、型腔排气顺利、确保塑件质量、无损塑件外观、设备利用合理。
本制件为挡条套,内表面的粗糙度要求高,再加上对脱模机构的考虑,选择A—A分型面比较合理。
如下图所示:
以A—A为分型面,即可降低模具的复杂程度,减少模具加工难度,也有利于脱模,塑件成型后,由于四个小凸台的作用,塑件没有包紧型芯,而是留在型腔中,型腔设置在动模部分,较易推出。
2.2型腔数量的确定
根据注射机的注射能力,以每次注射量不超过注射机最大注射量的80%来求型腔数量N.
N=(0.8G-w)W
=(0.8×0.1375-0.05)÷0.00225
=26
其中:
G——注射机的公称注塑量(㎏)
W——成型件的重量(㎏)
w——流道和浇口的总质量(㎏)
实际生产中根据工厂的情况和生产批量的要求,本设计中选用一模四腔的设计方法。
2.3浇注系统的设计
2.3.1主流道设计
主流道截面积的大小最先影响塑料熔体的流速和充模时间。
如果截面直径过小,熔体在流动过程中的冷却面积相对增大,热量损失大,导致粘度升高,压力损失增大,流动性降低,因此成型困难。
如果截面直径过大,则流道容积增大,塑料
2.3.2主流道衬套设计
主流道是浇注系统的第一个组成部分,这部分的具体设计都集中在浇口套上,模具工作时,浇口套直接与注射机喷嘴接触,浇口套本身的工作条件比较苛刻,所以应选用较好的钢材来制造,并应有50~55HRC的硬度。
浇口套与注射机喷嘴的接触部分有两种形式,一种为平面接触,另一种为球面接触。
平面接触的优点是:
接触面积较大,密封较好,塑料不易外溢。
其缺点是:
若注射机的精度不高,容易造成塑料外溢,但由于它能自动调整注射机的偏差,所以在注射机精度不高的情况下,亦能正常使用。
通过综合考虑,本设计采用球面接触的浇口套,在正常情况下,浇口套端部的球面半径应大于注射机喷嘴的球面半径,浇口套锥孔的小端直径应大于注射机喷嘴孔径。
为了提高模具的寿命在模具与注塑机频繁接触的地方设计为可更换的主流道衬套形式,在这里我们设计的模具较小,可以将主流道衬套与定位环设计为一个整体。
选取材料为T10A,热处理以后的硬度为53~57HRC,主流道衬套和定模的配合形式为H7/m6的过渡配合。
衬套的长度应与定模配合部分厚度一致主流到出口处的端面部的突出在分型面上,否则不仅会造成溢料还会压坏模具。
2.3.3分流道的设计
分流道是指连接主流道与浇口的塑料通道。
单腔注塑模通常不用分流道,但多腔注塑模必须开设分流道。
本设计是一模四件,需要开设分流道。
本设计中采用梯形截面的分流道,梯形截面分流道容易加工,且熔体的热量散发和流动阻力都不大,截面尺寸由文献[2]表6-2查得:
h=5㎜b=7㎜
第三章成型零部件的设计
3.1型芯的结构设计及其计算
本制件采用一模四件的结构形式,考虑加工的难易程度和材料的价值利用等因素。
型芯拟采用整体式结构,整体式型芯形状比较简单,便于机械切削加工。
ABS的收缩率为0.4%~0.9%.
由文献[4],按平均收缩率计算模具成型零件工作尺寸的公式表查得:
型芯的径
第四章侧向分型与抽芯机构的设计
4.1抽芯距的确定
抽芯距是指将侧型芯从成型位置推至不防碍塑件推出时的位置所需的距离,一般抽芯距等于塑件侧孔深度或凸台高度另加2~3㎜的安全距离。
S=h+(2~3)㎜
=0.5+2.5
=3㎜
S----抽芯距(㎜)
h----塑件侧孔深度或凸台高度(㎜)
4.2抽芯机构的确定
本制件中凸台较小,选用顶出抽芯机构比较合理。
顶出抽芯是利用顶出元件直接顶推塑件同时进行抽芯。
本设计利用成型顶杆顶出抽芯,成型顶杆见下图:
V=WQ1/Pc1(T1-T2)
=82600/60×1/1000×4.2×(30-20)
=58㎝3
由上述计算可知,因为模具每分钟所需的冷却水量很小,故在这里我们可以初选水管直径为Ф8mm的孔,水冷即可。
经试模以后根据塑料制件的质量问题然后修正冷却系统的水管直径,小的话可以通过机械加工增加孔的直径。
第六章结构与辅助零部件设计
6.1合模导向机构
合模导向机构的功能是保证动、定模部分能够准确对合。
使分别加工在动模和定模上的成型表面在模具闭合后形成形状和尺寸准确的腔体,从而保证塑件形状、壁厚和尺寸的准确。
导柱对合导向在注塑模中应用最普遍,本设计中也选择导柱对合导向,导柱可以安装在动模一侧,也可以安装在定模一侧,本设计中导柱安装在动模一侧。
因为作为成型零件的型芯安装在定模一侧,导套和型芯安装在同一侧,在合模时可起保护作用。
设计中选用的是直形导柱,直形导柱是一种除安装部分的凸肩外,长度的其余部分直径相同的导柱,这种导柱便于加工,导柱的前端设计成锥形,便于导向,导柱可以在工作部分带有储油槽。
带储油槽的导柱可以储存润滑油,延长润滑时间。
导套采用带肩导套。
导柱安装时模板上与之配合的孔径公差按H7确定,安装沉孔直径视导柱直径可取D+(1~2)㎜,导柱长度尺寸应能保证位于动、定模两侧的型腔和型芯开始闭合前导柱已经进入导孔的长度不小于导柱直径。
导柱和导套材料选用T10A钢,形状如下图:
6.2复位杆的设计
复位杆的形状和尺寸如下图所示:
6.3支承块的设计
支承块又称支架,可以和动模固定底板设计为一体,这时又将支承块称为模脚,也可以单独设计为一个零件。
单独设计为一个零件时又称为垫块。
对于外形为圆形的模具,单独设计为一个零件比较经济。
对于方形模具,与动模固定底板设计为一体的结构更常采用。
本设计采用单独设计为一个零件.
第七章注射机的校核
本设计选用的是具有液压-机械式合模机构XS-ZY-125型注射机,其最大开模行程是由肘杆机构的最大行程所决定的,而不受模具厚度的影响,当模具厚度变化时可由其调模装置调整。
故校核时只需使注射机最大开模行程大于模具所需的开模距离。
即Smax≥S
300≥83
式中Smax------------------------------注射机最大开模行程.㎜
S-------------------模具所需开模距离.㎜
第八章模具闭合高度的确定
由标准模架可知:
定模座板选用25mm
定模板选用16mm
定模垫板选用9㎜
动模板选用30mm
动模垫板选用10mm
动模座板选用25mm
根据推出行程和推出结构的结构尺寸确定垫块的高度为:
63mm
因而模具的闭合高度:
H=25+16+9+30+10+25+63
=178mm
第九章模具总装图及其工作原理
工作过程:
模具打开,由于凸台的作用塑件留在型腔中。
动模后退,当后退到一定的程度,顶杆垫板21碰到注射机顶杆,在注射机顶杆的作用下,带动顶杆固定板4把塑件和成型顶杆一起顶出。
继续顶出,成型顶杆和塑件分离,取出塑件,顶杆由复位杆复位,模具闭合,进行下一次注射。
第十章模具的安装和调试
10.1模具的安装
(1)清理模板平面定位孔及模具安装面上的污物、毛刺。
(2)因本模具外形尺寸不大,故采用整体法安装法。
先在机器下面两根导轨上垫好木板,模具从侧面进入机架间,定模入定位孔,并放正,慢速闭合模板,压紧模具,然后用压板或螺钉压紧定模,并初步固定动模,然后慢速开闭模具,找正动模。
应保证开闭模具时平衡、灵活、无卡住现象,然后固定动模。
(3)调节锁模机构,保证有足够开模距及锁模力,使模具闭合适当。
(4)慢速开启模板直至模板停止后退为止,调节顶出装置,保证顶出距离。
开闭模具观察顶出机构运动情况,动作是否平衡、灵活、协调。
(5)模具装好后,等料筒及喷嘴温度上升到距预定温度20~30℃,即可校正喷嘴与浇口套的相对位置及弧面接触情况,可用一纸片放在喷嘴与浇口套之间,观察两者接触印痕,检查吻合情况,须使松紧合适,校正后拧紧注射座定位螺钉,紧固定位。
(6)开空车运转,观察模具各部分运行是否正常,然后才可注射试模。
10.2模具的调试
通过试模塑件上常会出现各种弊病,为此必须进行原因分析,排除故障。
造成次废品的原因很多。
有时是单一的,但经常是多方面综合的原因。
需按成形条件、成形设备、模具结构及制造精度、塑件结构及形状等因素逐个分析找出其中主要矛盾,然后再采取调节成形调节、修整模具等方法加以解决。
试模中出现的问题及解决办法
缺陷名称
注塑机或成型条件问题
模具或材料(塑料原料)问题
解决办法
填充不满
1.注塑机的注塑力不够
2.加料量不够
3.注塑压力太低
4.注塑速度太慢
1.浇口平衡不好
2.模具温度太低
3.排气不良
4.塑料原料的流动性不好
提高注射压力和速度;增加浇口尺寸和加料量提高模具和料筒温度
溢边
1.注塑压力太大
2.锁模压力不够
3.加料量太大
4.料温过高
1.模具配合面不严
2.成型期间塑料原料粘性太低
降低模具温度和料筒温度;减少保压时间和浇口尺寸;增大锁模力
熔接线
1.料温太低
2.注射压力过低
3.注塑速度过慢
4.注塑机喷嘴温度低
1.模具温度较低
2.浇口的数目与位置不对
3.塑料原料干燥不够
4.塑料原料流动性差
提高注射速度;增加模具温度和料筒温度
龟裂
1.注射压力过高
2.料温太低导致流动不好
3.保压压力过高
1.模具温度过低
2.型腔设计不良
3.塑料原料粘性不良
4.塑料原料退火不良
降低注射压力和保压压力;提高模具温度;改良型强设计
总结
经过近段的努力,在老师和同学们的指导和帮助下,我顺利地完成了这次的毕业设计任务。
经过这次的设计任务,使我对模具设计,特别是模具的设计过程有了进一步地了解;对模具的基本结构、组装、调试、加工制造等方面有了深刻理解。
在设计的过程中,通过对制件的分析和对模具的设计的研究时,能够较好地将课本上的理论知识应用与设计当中,并且能够从整体,宏观上去研究、分析、考虑设计问题。
同时,在这次的设计过程中,还很大地程度上锻炼了自己的动手能力,如:
亲自去收集和查找有关资料,并从中又学会了一门新的课程《如何查找资料和文献》;其次,通过搜寻大量的资料,还大大地锻炼了自己的画图、看图、排版等方面的能力。
最重要的是,经过这次毕业设计,使我真正地感受到了集体的力量和学习方法。
在设计过程中,难免会遇到技术或其他方面的难题,但是通过老师的指导和与同学们的交流和虚心地请教都得到了解决,使我最终顺利地完成设计。
由于本人的水平有限,经验不足,在设计当中如有不妥之处,还恳请各位老师指导更正。
致谢
经过一段时间的紧张工作,今日终于顺利完成毕业设计。
在这里,我要衷心地感谢一些在我的设计工作中给予我很大帮助的老师和同学。
首先:
我最要感谢的是我的指导老师--杨安民老师,感谢杨老师在设计期间多次对我的指导和有关设计中错误的更正。
还要感谢丁老师和尚老师,他们虽然不是我的指导老师,但在设计过程中同样给了我耐心的指导和热心的帮助。
在这里一并感谢。
其次:
我要深深感谢的是我的专业课老师们,没有您们耐心的教诲和专业课知识的传授,我不会完成今天的设计,在这里我同样说声谢谢!
最后:
我还要感谢我的同学们,在设计过程中遇到技术问题,通过与他们的商讨和帮助,查阅资料,一一攻破难关,助我顺利地完成设计。
参考文献
【1】刘昌祺塑料模具设计北京:
机械工业出版社.1998
【2】杨占尧塑料注射模结构与设计北京:
清华大学出版社.2004
【3】宋玉恒塑料注射模具设计实用手册北京:
航空工业出版社.1998
【4】唐志玉塑料模具设计师指南北京:
国防工业出版社.1999
【5】奚永生塑料橡胶成型模具设计手册北京:
中国轻工业出版社.2000
【6】王孝培塑料成型工艺及模具简明手册北京:
机械工业出版社.2000
【7】翟德梅模具制造技术北京:
化学工业出版社.2005
【8】阎亚林塑料模具图册北京:
高等教育出版社.2002
【9】黄虹塑料成型加工与模具北京:
化学工业出版社.2003
【10】中国标准出版社第三编辑室塑料模具标准汇编
北京:
中国标准出版社.1997
【11】ThomaspetersTolerancefittingandtechnologyofmeasuringPublishinghouseofthemechanicalindustry1999