铅酸蓄电池的生产工艺.docx
《铅酸蓄电池的生产工艺.docx》由会员分享,可在线阅读,更多相关《铅酸蓄电池的生产工艺.docx(11页珍藏版)》请在冰豆网上搜索。
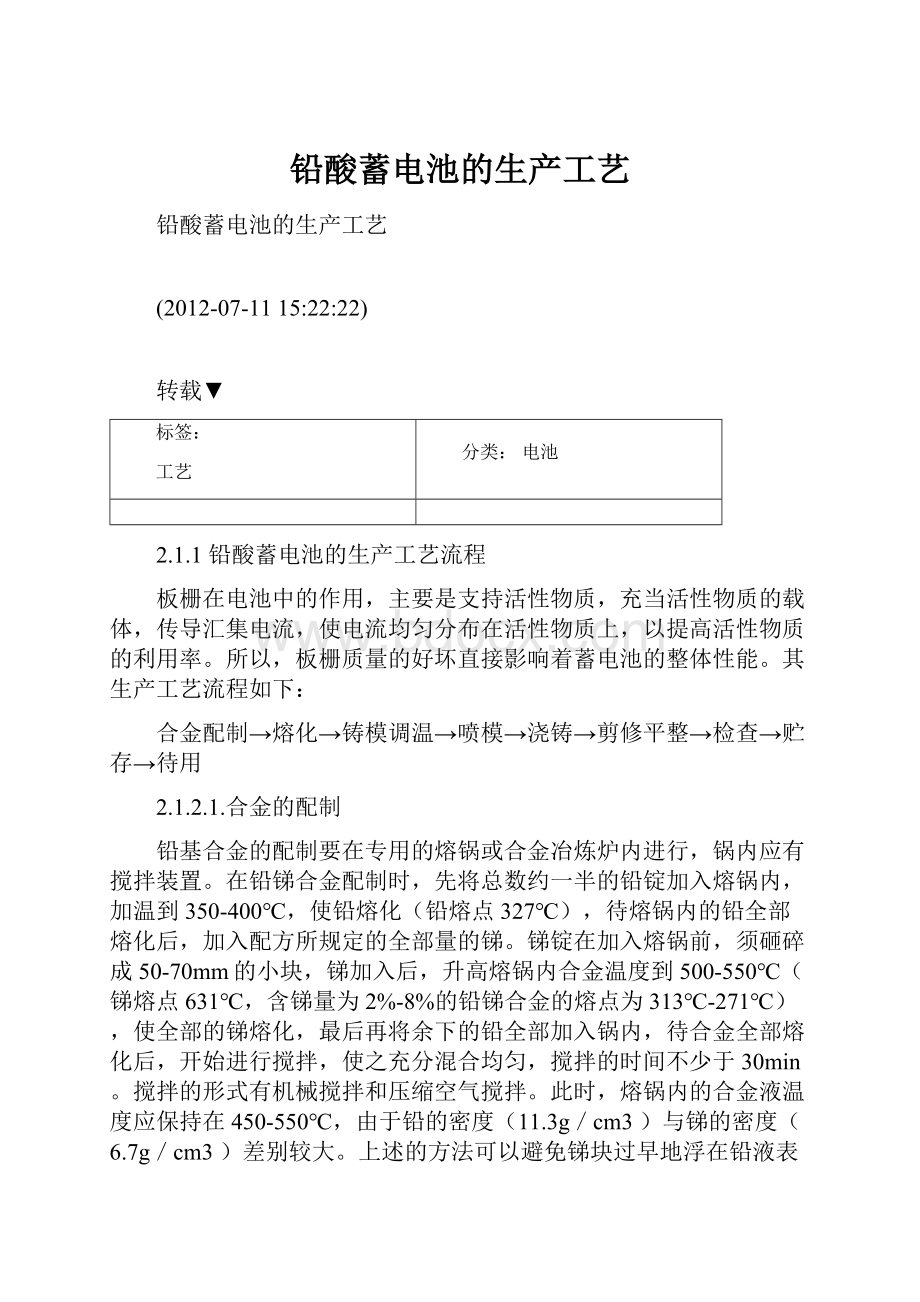
铅酸蓄电池的生产工艺
铅酸蓄电池的生产工艺
(2012-07-1115:
22:
22)
转载▼
标签:
工艺
分类:
电池
2.1.1铅酸蓄电池的生产工艺流程
板栅在电池中的作用,主要是支持活性物质,充当活性物质的载体,传导汇集电流,使电流均匀分布在活性物质上,以提高活性物质的利用率。
所以,板栅质量的好坏直接影响着蓄电池的整体性能。
其生产工艺流程如下:
合金配制→熔化→铸模调温→喷模→浇铸→剪修平整→检查→贮存→待用
2.1.2.1.合金的配制
铅基合金的配制要在专用的熔锅或合金冶炼炉内进行,锅内应有搅拌装置。
在铅锑合金配制时,先将总数约一半的铅锭加入熔锅内,加温到350-400℃,使铅熔化(铅熔点327℃),待熔锅内的铅全部熔化后,加入配方所规定的全部量的锑。
锑锭在加入熔锅前,须砸碎成50-70mm的小块,锑加入后,升高熔锅内合金温度到500-550℃(锑熔点631℃,含锑量为2%-8%的铅锑合金的熔点为313℃-271℃),使全部的锑熔化,最后再将余下的铅全部加入锅内,待合金全部熔化后,开始进行搅拌,使之充分混合均匀,搅拌的时间不少于30min。
搅拌的形式有机械搅拌和压缩空气搅拌。
此时,熔锅内的合金液温度应保持在450-550℃,由于铅的密度(11.3g/cm3)与锑的密度(6.7g/cm3)差别较大。
上述的方法可以避免锑块过早地浮在铅液表面,同时,为了合金均匀,必须进行充分的搅拌。
以上铅锑合金配制过程的时间大约为4h。
在开始铸锭前必须检查合金的锑含量。
如不符合规定,应加适量的铅或适量的锑进行调整,符合工艺规定的合金液,除掉表面氧化残渣后,开始铸锭。
铸模要干燥无水,铸锭时要注意避免合金液溅出烫伤。
铸锭后标号存放。
在铅锑合金的配制过程中,熔渣损失约为1.0%-2.0%,烧减损失约为0.2%-0.6%。
2.1.2.2合金的熔化
板栅浇铸时,需先将配制好的合金熔化,熔化后的合金液温度对板栅浇铸时的成型关系很大,合金液温度过高或过低都不能浇铸出良好的板栅。
一般情况下,合金液温度应控制在450-550℃的范围,但工厂在实际中应根据具体情况摸索出最佳的合金液浇铸温度。
2.1.2.3浇铸模具的温度调整
浇铸使用的模具在浇铸前都应进行预热和温度调整,铸板机通过由加热预热,手工模具通过电加热或合金液预铸预热,其目的是为了保证在浇铸过程中合金液的冷却速度,铸模温度过高或过低或不均匀都会对板栅的成型影响很大,特别是对于手工铸板显得更为重要。
2.1.2.4喷模、刮模
在浇铸时由于模具是金属制成,故存在散热快的特点,加入模具内腔沟槽比较窄浅,使得熔锅状态下的合金液难以充满模具。
为了保证浇铸板栅的成型率,必须在模具表面和浇铸合金之间喷涂脱模剂。
目前,在蓄电池厂一般使用由软木粉、硅酸钠和水配制的脱模剂,喷涂在模具内腔,主要起保温、隔热、润滑,确保合金液充满模具的作用。
同时,对板栅的厚度均匀性起调整作用。
脱模剂的配制方法如下:
取8Kg左右的水和密度为1.35g/cm3的硅酸钠(水玻璃)450mL左右,放入加温锅内(可用铝锅)混合均匀后放在炉子上加热烧煮。
待硅酸钠水溶液煮沸后,即将1kg细度为180-200目的软木粉缓慢地倒入锅内,充分搅拌均匀,再加入8kg左右的水小火煮沸30min,冷却后用60-80目筛子过滤后装入容器内待用。
以上配制出的脱模剂使用的有效期为2-3小时,如在上述配方中加入25mL左右的磷酸铝(含铝36.4%)或400g左右的膨润土,有效期可延长至6-8小时。
在使用中,如果脱模剂发粘,可适当减少硅酸钠量或适当增加用水量,如果脱模剂稀,喷模时容易从模具表面脱落,可适当增加硅酸钠量或适当减少水用量。
脱模剂稀稠要合适,太稀粘附力差,太稠脱模剂在模具表面堆积太厚,因此,可以根据实际使用情况和板栅要求的厚薄程度进行调整。
2.1.3铅粉的制造
铅粉是制造铅酸蓄电池极板的活性物质,是表面覆盖一层PbO的金属铅的粉粒状物。
它是由纯铅经过特定的热氧化过程形成的。
铅粉的颜色,由颗粒中氧化铅的含量、颗粒结构和尺寸的大小等因素来决定,随着氧化度的增加,粉末由黑色逐渐转变为黄绿色或灰黄色。
铅粉的制造有两种方法:
一是球磨法;二是气相氧化法。
此处选用球磨法,其生产工艺流程如下:
铅锭→熔铅锅→铅球→球磨机→沉淀分离→除尘过滤→存贮→输送
铅粉对铅膏及极板性能影响很大,其特性主要有氧化度,视密度,吸水率,筛析和吸酸值等。
氧化度高的用于正极板,氧化度低的用于负极板。
PbO以两种形态存在,特点如下述:
t-PbO(tetragonal-)
四方晶系、红色
低温低压下稳定,但在较高温度下会发生晶形转化,转化温度为486~489℃,热效应为1.35kJ/mol
O-PbO(Orthorhomb-)
正交晶系、黄色
快速冷却时,它可能保持不变或继续在低温下存在,但最终会在外来特理作用的影响下,缓慢地转化成t-PbO
Barton法可生产氧化度为70%~80%的铅粉。
在较高的反应温度下,氧化物几乎完全是O-PbO。
在低温下,t-PbO和O-PbO一同生成。
t-PbO是电池工业最可取的氧化物。
因为氧化必须在低于多晶转化温度(486℃)下进行,反应锅被保持的温度范围为460~470℃。
在这种情况下,可形成少量的(约<15%)O-PbO,这对随后的电池参数实际上无多大影响。
2.1.3.1铸球
将符合要求的铅锭加入熔铅锅内加热至400-500℃,使铅锭全部熔化,并在铅液表面覆盖一层木炭以防止铅氧化及保持铅液温度,点燃煤气烧热排铅管,使凝固在排铅管内的铅完全熔化后,熔铅锅的排铅管阀门打开,使铅液自动流入回转圆盘式铸球机内,铸成一定规格的铅球或使铅液自动流入回转圆盘式铸块机,铸成铅条后拉出,通过自动切刀将铅条切成一定规格的铅块。
制成的铅球或铅块通过提升机输送到贮存斗内贮存6小时以后输送到铅粉机内制粉。
2.1.3.2制粉
球磨法制铅粉是在滚筒式铅粉机(又称岛津式铅粉机)中完成的,铅粉机的筒体内并无任何的研磨体,铅粉是靠铅球或铅块在随筒体的转动过程中的相互撞击和摩擦而形成的。
这种铅粉机有两种形式,一种是分选式铅粉机,另一种是筛选式铅粉机,这两种铅粉机的工作原理基本一样,所不同的是出粉的方式不同,风选式铅粉机是通过吹入空气而把铅粉带出,而筛选式铅粉机则是通过筛网来出粉的。
目前,在我国蓄电池企业大多采用风选式铅粉机。
制粉过程:
将铅球或铅块由输送器按负载量送入球磨机,同时通过鼓风机给铅粉机内输入定量的预热空气。
球磨机由传动机构带动,以一定的转速旋转,由于离心力的作用,铅粉机内的铅球或铅块也随着铅粉机筒体一道转动,当被带到一定高度时,铅球或铅块又借自身的重量自由落下,在这个过程中有三个现象:
(1)铅球或铅块与筒体摩擦产生热量。
(2)铅球或铅块与铅球或铅块摩擦产生热量。
(3)铅球或铅块的相互撞击和摩擦使得铅球或铅块表面晶粒发生变形和滑动位移。
由于铅粉机内铅球或铅块相互摩擦和撞击产生大量的热量,使得筒体内的温度增加,在给铅粉机输入的有一定温度和相对湿度的空气气流中氧的作用下,铅球或铅块发生位移的晶面边缘受到氧化而生成了氧化铅。
反应方程式如下:
2Pb+O2→2PbO+Q(热量)
由于铅的氧化反应是放热反应,放出的热量又使得铅粉机筒体内达到较高的温度。
在这个摩擦、撞击、晶体变形位移、氧化的过程中,铅球或铅块表面被氧化的部分就与铅球或铅块整体之间发生裂缝。
随着裂缝的逐渐深入,金属氧化层在撞击和摩擦力的作用下,逐渐从球体或块体上脱落下来,续而进一步磨碎、研细而形成了覆盖一层PbO2的细颗粒状铅粉。
铅粉的技术指标
⑴ 氧化度:
是指铅粉中氧化铅(PbO)所占的百分数。
实践表明,氧化度在70~80%之间最好,氧化度太低,电池初期容量很小;氧化度太高,电池初期容量大,但寿命短。
一般正铅膏铅粉氧化度在70~75%之间,负铅膏铅粉氧化度在75~80%之间。
⑵ 铁含量:
铅粉中的含铁量要小于0.0007%,铁含量超标会引起电池的自放电速率加大。
⑶ 筛析度:
铅粉中的筛析度主要是分析铅粉颗粒的大小。
一般要求铅粉过100目筛的剩余物要少于7%。
因为铅粉的颗粒度太小会使电池的初期容量增大使电池寿命缩短。
⑷ 视密度:
也就单位体积的重量,视密度与颗粒度和氧化度有关,一般讲氧化度越高、颗粒度越细的铅粉,其视密度越小。
视密度的测量方法:
使铅粉通过振动筛自由落在容积为100ml的量筒内,刮平后称重,即可得到铅粉的视密度。
铅粉的视密度一般控制在1.5~1.8g/cm3范围内。
⑸ 吸水率:
是指每kg铅粉吸水量的毫升数,铅粉的吸水率与铅粉的孔隙度或孔率有关。
它表明了铅粉在制膏过程中吸水或吸酸能力的大小。
一般要求吸水率在95~100ml/kg之间。
⑹ 吸酸率:
是指铅粉与硫酸反应的程度,一般规定每kg铅粉吸收的稀硫酸为在5~15g(稀硫酸的密度为1.1g/cm3)。
将一定量的铅粉加入到密度为1:
100的稀硫酸中,置于25℃的恒温槽中充分振动,用过滤纸过滤,取出一部分滤液,用1mol/dm3的NaOH滴定,通过反应前后的NaOH浓度差,计算出1g铅粉所吸收的硫酸克数,并以此值来吸酸程度。
一般来说,吸酸值愈大,表示铅粉氧化度愈高;反之表示铅粉氧化度低。
铅粉的性质对电池性能的影响
生产初实践经验已经证明,氧化铅的特性对电池正极工作性能的影响程度远远大于负极板。
例如,电池正极板的比电特性明显依赖于氧化铅的相组成和颗粒大小的分布。
Chang和Brown证明:
以不同粉末制备的正极板,当深度电循环时,其正极板容量的变化有很大的差别。
图中数据表明,以O-PbO制得的正极板与t-PbO制得的正极板比较,只具有较短的循环寿命和较低的极板容量。
因此,电池制造中,最好采用t-PbO作为制备极板的原材料。
颗粒的大小对铅酸电池的初始性能起着十分重要的影响。
如果粉末太细,其初始容量虽然相对较高,但在第20次循环之后,容量开始下降。
反之,当铅粉为较粗的颗粒,初始循环时,容量较低,随后逐渐增加到一最大值,此后开始进一步下降。
平均粒度大小为5~50μm的铅粉和t-PbO的氧化物相组成可确保电池深放电循环时具有相当于50%理论容量的实际容量以及最长的循环寿命。
2.1.3.3铅膏的制造
铅膏的合制过程就是在和膏机内将铅粉,纯水,硫酸及一些添加剂均匀地混合成有塑性的膏状物质的过程,其工艺流程如下:
配料→干混→加水→加酸→混合→检查→出膏
具体操作如下:
1.将符合质量指标要求的铅粉按工艺条件规定的数量加入到和膏机内,启动和膏机。
2.将符合质量指标要求的各类粉状添加剂按规定的用量加入和膏机内干搅拌3-5min(不加粉状添加剂和制的正极用铅膏不需此程序)。
3.将符合要求的短纤维按规定的用量放入符合质量要求的定量的去离子水中(具有一定得温度),使其在水中充分均匀分散,然后在1min左右的时间内将水加入到和膏机内,搅拌8min左右。
4.打开和膏机冷却系统,将符合质量要求的稀硫酸按规定的用量在15-20min的时间内加入到和膏机内,在搅拌20min左右。
5.停机取少量铅膏测视密度和稠度,如果视密度过高,则加适量的调节水重新开机搅拌5min左右的时间,在停机取样测量,符合要求后放出铅膏。
6.铅膏视密度对电池的影响:
视密度是指单位体积铅膏的重量,它与铅膏中水和硫酸的用量有直接的关系。
水和酸越多,视密度越低。
一般正膏的视密度为4.05-4.20g/cm3,负膏的视密度为4.25-4.40g/cm3。
视密度对正极铅膏影响较大,视密度越低,孔率越高,其利用率也高,初期容量也高;但活性物质容易脱落,对寿命不利。
一般正极铅膏的视密度不得低于3.80g/cm3。
视密度对负极铅膏影响不大,负极视密度高于正极主要是多涂些活物质。
7.铅膏中的含酸量一般以3%~5%为宜,含酸量高,电池初期容量好,但寿命不好;含酸量低,寿命好,但初期容量低。
另外,合膏温度超过40℃主要生成四碱式硫酸铅(4PbO·PbSO4),合膏温度低于40℃主要生成三碱式硫酸铅(3PbO·PbSO4·H2O);出膏温度不宜超过40℃。
铅膏的搅拌时间通常是加入硫酸后搅拌20min结束,搅拌时间太短,铅膏组份不均匀;搅拌时间太长,会产生过多的四碱式硫酸铅,使铅膏发硬。
铅膏的加酸速度一般控制在20min加完,加酸太快或太慢都对铅膏质量有影响。
2.1.3.4涂膏或灌粉
涂板是指铅膏与板栅形成涂膏式极板的过程,即将铅膏按照规定的数量均匀地涂填到板栅格体内,使铅膏与板栅良好结合的过程。
灌粉(或挤膏)是指铅粉(或铅膏)与铅芯套管体形成管式极板的过程,即将铅粉(或铅膏)灌入(或挤入)铅芯套管体,使铅粉(或铅膏)与铅芯良好结合的过程。
极板是蓄电池电化学反应的主体部分,极板分为正极板和负极板。
涂膏即是将正负极活性物质均匀涂填到板栅的过程。
其工艺流程如下:
涂填→检查板面膏量→压实→淋酸或浸酸→表面干燥→检查水量→存放
涂板分为手工涂板和机械涂板。
现在大多生产厂家多是机械涂板,机械涂板是通过涂板机来完成极板的涂填、压实及淋酸的整个过程。
涂板后的极板进行表面干燥的目的有两个方面:
一方面是要充分除去极板活性物质的水分,防止收板时极板粘连。
另一方面是要保证极板内部铅膏含有一定量的水分以利于极板固化时铅膏内金属铅的氧化。
而极板的淋酸目的是为了在生极板的表面形成一层薄的硫酸铅,防止干燥后出现裂纹。
淋酸后的极板立即进入表面干燥窑,表面干燥窑的温度一般控制在100~120℃,干燥时间为2~5min,使表面失去一部分水,以避免在下面的操作中极板表面互相粘连。
极板在出表面干燥窑时铅膏含水率应控制在8%~11%,以利于后面的固化工序。
2.1.3.5极板的固化干燥
固化干燥即硬化脱水,涂填后的极板其一方面水分过多,另一方面铅膏组织不稳定,因此要经过固化干燥工艺来使其硬化脱水,在完成铅膏的硬化脱水的过程的同时要实现铅膏中游离铅的氧化,铅膏与板栅的腐蚀结合,铅膏中碱式硫酸铅的再结晶以及多孔电极的形成等一系列的物化反应的目的。
在这个过程中极板发生的反应有:
一、铅膏中游离铅进一步氧化成氧化铅,二、极板板栅表面生成腐蚀层,三、碱式硫酸铅的再结晶,四、铅膏的脱水硬化及多孔电极的形成。
其作用有:
1.使铅膏中的铅进一步氧化,在正、负极中残余的铅分别减小到2.5%和5.0%(质量分数)左右,化成后可望获得坚固的活性物质和良好的外观;2.在固化过程中,铅膏物质继续进行碱式硫酸铅的结晶过程,在较低温度下生成3PbO·PbSO4·H2O,温度高于80℃时有利于4PbO·PbSO4·H2O的生成;3.通过固化使板栅表面生成氧化铅的腐蚀膜,增强板栅与活性物质的结合力。
⑴ 固化的目的:
使极板中的铅膏进一部氧化,固化前铅膏中的游离铅含量约15%,固化后游离铅含量在2.5~5%,这样化成后活物质的强度好、外观好。
固化时极板继续进行碱式硫酸铅结晶过程,在较低的温度下生成三碱式硫酸铅;在温度高于80℃时,有利于四碱式硫酸铅。
另外,固化过程也使板栅表面生成PbO腐蚀膜,可使活物质与板栅结合得更好,所以说固化不好的极板容易脱粉。
⑵ 固化中湿度对铅膏氧化的影响:
铅膏中保持7~8%的水份时,铅的氧化速度最高。
湿度越大铅的氧化速度越快。
因此,固化过程的开始阶段湿度最好为100%。
在固化过程中铅的氧化和失水是在最初20h内完成的。
⑶ 固化中温度对铅膏氧化的影响:
在温度为30℃时铅的氧化速率最大。
⑷ 固化条件:
固化条件分为高温高湿固化和低温高湿固化,它们都要求固化室湿度高。
这是因为碱式硫酸铅的再结晶要在极板含水量为5~6%的条件下才能显著进行,因而在固化过程中极板必须在较长时间内保持含水量在5%以上,所以固化室的环境湿度要达到95%以上。
三碱式硫酸铅和四碱式硫酸铅为相互交联的纤维状结构,对极板的强度起着重要的作用,所以说固化不好的极板容易脱粉。
⑸ 高温高湿固化特点:
固化后的物相主要四碱式硫酸铅(4PbO·PbSO4),它初期容量低,但寿命长。
动力电池主要采用这种固化方式,以保证电池的使用寿命。
⑹ 低温高湿固化特点:
固化后的物相主要三碱式硫酸铅(3PbO·PbSO4·H2O),它初期容量大,寿命适中。
⑺ 干燥:
生极板经过干燥后,含水量小于2%,正极板中的金属铅含量小于2.5%,负极板中的金属铅含量小于5%。
由于游离铅的氧化需要氧气,所以在固化过程中要不断向固化室补充适当的空气。
干燥温度60℃,干燥时间24~30h。
2.1.3.6极板的化成
极板化成是指利用化学和电化学反应转化成具有电化学特性的正、负极板的过程。
化成方式主要有两种:
一是槽式化成,也叫外化成,即将极板放在专门的化成槽中,多片正、负极相间的连接起来,与直流电源相接,灌入稀硫酸通电;另一种为电池化成,也叫内化成,即不需要专门的化成槽,而是用生极板装配成极群组,放在电池壳体中装成电池组后,灌满电解液再通直流电化成。
电池化成避免了生极板在化成槽中化成时析出气体携带酸雾造成的污染,以及减少了化成后的洗涤干燥等工序,具有明显的优越性。
化成反应:
“化成”即“转化而成”之意。
生极板从浸入化成槽与稀硫酸接触就开始进行化学反应,其反应式为:
PbO+H2SO4─→PbSO4+H2O
PbO+PbSO4+H2SO4─→2PbSO4+H2O
3PbO+PbSO4+H2O+3H2SO4─→4PbSO4+4H2O
这个时间长达6~7h,时间长短还取决于硫酸的浓度和电解液温度。
另一个反应是电化学反应,即正极板上的硫酸铅被氧化成二氧化铅,负极板上的硫酸铅还原成海绵状铅。
反应式:
正极板PbSO4─→PbO2;负极板PbSO4─→Pb。
化成的第一阶段以化学反应为主导,第二阶段以电化学反应为主导。
2.1.3.7装配
上述蓄电池的各个步骤完成以后,就可以把其组装起来,即装配。
其工序为:
1.起动电池和管式动力电池组装工艺流程:
焊极群→插隔板→装槽→穿壁焊→盖子热封→气密性检测→焊端子→加酸充电(干荷电电池不需此工序)→测试→包装
2.阀控密封式电池组装工艺流程:
包板→焊极群→装槽→焊接→封盖→焊端子→极柱密封→气密性检测→加酸充电→测试→包装。