超临界直流锅炉说明书.docx
《超临界直流锅炉说明书.docx》由会员分享,可在线阅读,更多相关《超临界直流锅炉说明书.docx(41页珍藏版)》请在冰豆网上搜索。
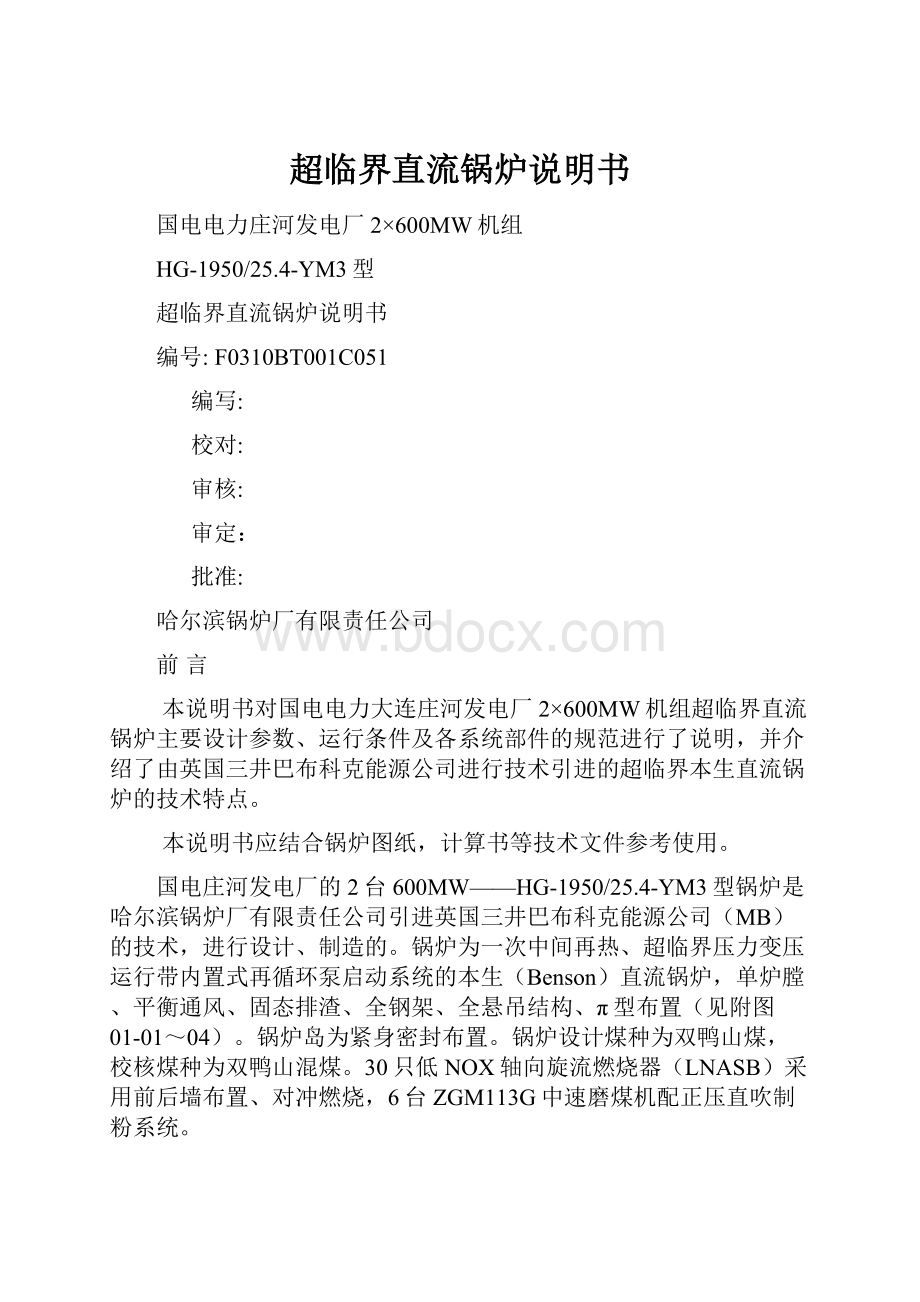
超临界直流锅炉说明书
国电电力庄河发电厂2×600MW机组
HG-1950/25.4-YM3型
超临界直流锅炉说明书
编号:
F0310BT001C051
编写:
校对:
审核:
审定:
批准:
哈尔滨锅炉厂有限责任公司
前言
本说明书对国电电力大连庄河发电厂2×600MW机组超临界直流锅炉主要设计参数、运行条件及各系统部件的规范进行了说明,并介绍了由英国三井巴布科克能源公司进行技术引进的超临界本生直流锅炉的技术特点。
本说明书应结合锅炉图纸,计算书等技术文件参考使用。
国电庄河发电厂的2台600MW——HG-1950/25.4-YM3型锅炉是哈尔滨锅炉厂有限责任公司引进英国三井巴布科克能源公司(MB)的技术,进行设计、制造的。
锅炉为一次中间再热、超临界压力变压运行带内置式再循环泵启动系统的本生(Benson)直流锅炉,单炉膛、平衡通风、固态排渣、全钢架、全悬吊结构、π型布置(见附图01-01~04)。
锅炉岛为紧身密封布置。
锅炉设计煤种为双鸭山煤,校核煤种为双鸭山混煤。
30只低NOX轴向旋流燃烧器(LNASB)采用前后墙布置、对冲燃烧,6台ZGM113G中速磨煤机配正压直吹制粉系统。
锅炉以最大连续出力工况(BMCR)为设计参数。
在任何5磨煤机运行时,锅炉能长期带额定负荷(BRL)。
1.锅炉容量及主要参数
名称
单位
BMCR
BRL
过热蒸汽流量
t/h
1950
1789.9
过热器出口蒸汽压力
MPa(g)
25.4
25.2
过热器出口蒸汽温度
oC
571
571
再热蒸汽流量
t/h
1653.4
1516.8
再热器进口蒸汽压力
MPa(g)
4.75
4.35
再热器出口蒸汽压力
MPa(g)
4.56
4.17
再热器进口蒸汽温度
oC
321
311
再热器出口蒸汽温度
oC
569.0
569.0
省煤器进口给水温度
oC
285
279
2.
设计依据
2.1燃料
名称及符号
单位
设计煤种(双鸭山煤)
校核煤种(双鸭山混煤)
工
业
分
析
收到基全水分Mar
%
8.14
10.50
收到基灰分Aar
%
24.48
25.07
可燃基挥发分Vdaf
%
43.80
42.00
收到基低位发热量Qnet,ar
kJ/kg
21230
19800
哈氏可磨系数HGI
51
50
元
素
分
析
收到基碳Car
%
54.37
50.68
收到基氢Har
%
3.75
3.04
收到基氧Oar
%
8.27
0.75
收到基氮Nar
%
0.81
9.70
收到基全硫St,ar
%
0.18
0.26
灰
熔
融
性
变形温度DT
℃
1200
1180
软化温度ST
℃
1270
1250
半球温度HT
℃
1310
1330
流动温度FT
℃
1350
1370
灰
分
分
析
二氧化硅SiO2
%
54.25
54.30
三氧化二铝Al2O3
%
27.80
21.94
三氧化二铁Fe2O3
%
4.48
6.89
氧化钙CaO
%
4.72
7.03
氧化镁MgO
%
1.27
1.98
二氧化钛TiO2
%
0.84
0.85
三氧化硫SO3
%
1.50
1.46
氧化钠Na2O
%
0.44
2.49
氧化钾K2O
%
1.42
1.11
二氧化锰MnO2
%
0.18
0.23
其它
%
3.10
1.72
2.2点火及助燃油
油种:
#0轻柴油
运动粘度(20℃时):
3.0~8.0mm2/s
凝固点:
小于0℃
闭口闪点:
不低于65℃
机械杂质:
无
含硫量:
≤0.2%
水份:
痕迹
灰份:
≤0.02%
密度:
0.825t/m3
低位发热值Qnet,ar41800kJ/kg
2.3自然条件
多年平均气压1012.6hPa
多年平均气温8.8℃
多年平均最高气温13.9℃
多年平均最低气温4.4℃
多年极端最高气温36.0℃
多年极端最低气温-26.6℃
多年一日最大降水量151.6mm
多年最大积雪深度280mm
多年最大实测风速27.0m/s(10分钟10m高)
多年平均相对湿度69%
多年平均风速2.8m/s
多年平均降水量796.2mm
全年主导风向:
NW、NE向频率为11%
夏季主导风向:
SE、S向频率为10%
冬季主导风向:
NW向频率为15%
厂址所在的庄河地区地震烈度为VI度。
厂区位于相对稳定部位,适于建厂。
主厂房位于挖方部位,可做天然地基,其他位于填方部位的建筑物基础需作适当处理。
3锅炉运行条件
锅炉运行方式:
带基本负荷并参与调峰。
制粉系统:
采用中速磨煤机直吹式制粉系统,每炉配6台磨煤机(5台运行,1台备用),煤粉细度按200目筛通过量为75%。
煤粉均匀性系数为1.1。
给水调节:
机组配置2×50%B-MCR调速汽动给水泵和一台30%B-MCR容量的电动调速给水泵。
空气预热器进风加热方式:
一二次风采用暖风器加热。
空预器结构保证在各种负荷和环境温度下不出现冷端腐蚀。
4锅炉设计规范和标准
可执行下列标准:
AISC美国钢结构学会标准
AISI美国钢铁学会标准
ASME美国机械工程师学会标准
ASNT美国无损检测学会
ASTM美国材料试验标准
AWS美国焊接学会
EPA美国环境保护署
HEI热交换学会标准
NSPS美国新电厂性能(环保)标准
IEC国际电工委员会标准
IEEE国际电气电子工程师学会标准
ISO国际标准化组织标准
NERC北美电气可靠性协会
NFPA美国防火保护协会标准
《多燃烧器锅炉炉膛防爆/内爆标准》
PFI美国管子制造商协会标准
SSPC美国钢结构油漆委员会标准
DIN德国工业标准
BSI英国标准
JIS日本标准
GB中国国家标准
SD(原)水利电力部标准
DL电力行业标准
JB机械部(行业)标准
原电力部《火力发电厂基本建设工程起动及竣工验收规程》1996版
原电力部《火力发电厂劳动安全和工业卫生设计规程》DL5053-1996
原电力部《电力建设施工及验收技术规范》(锅炉机组篇)DL/T5047-95
原电力部《火电工程起动调试工作规定》
原电力部《电力工业锅炉压力容器监察规程》DL612-1996
劳动部《蒸汽锅炉安全技术监察规程》1996版(与电力部《电力工业锅炉压力容器监察规程》有矛盾者,以电力部的为准)
原能源部《防止火电厂锅炉四管爆漏技术守则》1992版
国家电力公司《火力发电厂设计技术规程》DL5000-2000
劳动部《压力容器安全技术监察规程》1999版
原电力部《火力发电厂燃煤电站锅炉的热工检测控制技术导则》DL/T589-1996
国家标准《水管锅炉受压组件强度计算》GB9222-88
国家标准《钢结构设计规范》GBJ17-88
5锅炉性能计算数据表(设计煤种)
名称
单位
负荷工况
BMCR
TRL
75%THA
过热器出口蒸汽流量
t/h
1950
1789.9
1209.9
过热器出口压力
MPa.g
25.40
25.20
19.66
过热器出口温度
℃
571
571
571
过热器系统压降
MPa
1.76
1.61
1.01
过热蒸汽温度控制负荷
%BMCR
35
再热器出口蒸汽流量
t/h
1653.4
1516.8
1054.5
再热器进口压力
MPa.g
4.75
4.35
3.03
再热器出口压力
MPa.g
4.56
4.17
2.91
再热器进口温度
℃
321
311
306
再热器出口温度
℃
569.0
569.0
569.0
再热器系统压降
MPa.g
0.19
0.18
0.12
再热蒸汽温度控制负荷
%BMCR
50
给水压力
MPa.g
28.9
28.2
21.64
给水温度
℃
285
279
257
预热器进口烟气温度
℃
362
349
316
预热器出口排烟温度(修正前)
℃
128
124
108
预热器出口排烟温度(修正后)
℃
123
119
103
预热器进口一/二次风温
℃
23/23
23/23
23/31.1
预热器出口一/二次风温
℃
301/318
294/311
272/283
省煤器出口过量空气系数
——
1.19
1.19
1.26
燃煤耗量
t/h
259.4
242.0
173.5
锅炉计算热效率(按低位热值)
%
93.83
93.91
94.01
6锅炉的特点
6.1技术特点
本锅炉是采用三井巴布科克能源公司技术设计、制造的超临界燃煤本生直流锅炉。
1951年三井巴布科克从西门子公司获得了本生直流锅炉的技术许可证,并于1960年设计、制造了第一台超临界本生直流锅炉。
经过半个世纪的发展和研究,其超临界锅炉已在中国、英国、比利时、菲律宾、丹麦、荷兰、芬兰、日本等国家投入使用,可适用于各种变压工况运行,具有较高的锅炉效率和可靠性。
其技术特点如下:
1)良好的变压、备用和再启动性能
锅炉下部炉膛水冷壁及灰斗采用螺旋管圈,在各种负荷下均有足够的冷却能力,并能有效地补偿沿炉膛周界上的热偏差,水动力特性稳定;采用四只启动分离器,壁厚较薄,温度变化时热应力小,适合于滑压运行,提高了机组的效率,延长了汽机的寿命。
2)燃烧稳定、温度场均匀的墙式燃烧系统
墙式燃烧系统的旋流燃烧器具有自稳燃能力和较大的调节比,在炉膛中布置的节距较大,相邻的燃烧器之间不需要相互支持;墙式燃烧系统的燃烧器布置为对称方式,沿炉膛宽度方向的热量输入均匀分布,因而在上炉膛及水平烟道的过热器、再热器区域的烟气温度也更加均匀,避免高温区受压元件的蠕变和腐蚀,有效抑制结渣。
3)经济、高效的低NOX轴向旋流燃烧器(LNASB)
三井巴布科克公司已有2000多只LNASB燃烧器在全球各地使用,其不仅能够高效、稳定地燃烧世界各地的多种燃煤,而且已经作为一种经济实用的手段来满足日益严格的降低NOX排放的需要。
4)高可靠性的运行性能
三井巴布科克有丰富的变压运行本生直流锅炉设计、制造经验,在燃烧等方面的研究和应用上进行了大量工作,并对已投运的机组积累了大量的调试和研究数据。
本工程的炉型为三井巴布科克公司标准化的典型设计,具有成熟的设计和制造经验,机组的可用率和可靠性高,能满足用户的各种技术要求。
6.2结构特点
1)本锅炉中、下部水冷壁采用螺旋管圈,上部水冷壁采用一次上升垂直管屏,二者之间用过渡集箱连接。
螺旋管圈的同一管带中的各管子以相同方式从下到上绕过炉膛的角隅部分和中间部分,水冷壁吸热均匀,管间热偏差小,使得水冷壁出口的介质温度和金属温度非常均匀。
因此,螺旋管圈水冷壁更能适应炉内燃烧工况的变化。
2)在螺旋管圈水冷壁部分采用可膨胀的带焊接式张力板垂直刚性梁系统,下部炉膛和冷灰斗的荷载传递给上部垂直水冷壁,保证锅炉炉膛自由向下膨胀。
3)布置于上炉膛的屏式过热器采用膜式管屏末端技术,使管屏平整防止结焦、挂渣。
4)省煤器为H型鳍片管省煤器,传热效率高,受热面管组布置紧凑,烟气侧和工质侧流动阻力小,耐磨损,防堵灰,部件的使用寿命长。
5)燃烧器喉口设计采用水冷壁让管加强喉口冷却,并采用高导热性的、光滑的碳化硅砖敷设喉口表面,以降低燃烧器喉部耐火层表面温度,抑制燃烧器区域的结焦。
6)高温受热面采用小集箱和短管接头的结构型式,集箱口径小,壁厚薄,降低了热应力和疲劳应力,提高了运行的可靠性。
7)锅炉尾部采用双烟道,根据再热汽温的需要,调节省煤器出口烟道的烟气挡板来改变流过低温再热器和低温过热器的烟气量分配,从而实现再热汽温调节。
烟气调温挡板为垂直布置,轴向受力,不易变形、卡涩,动作灵活。
7锅炉整体布置
本锅炉采用π型布置,单炉膛,尾部双烟道,全钢架,悬吊结构,燃烧器前后墙布置、对冲燃烧。
炉膛断面尺寸为22.187m宽、15.632m深,水平烟道深度为5.322m,尾部前烟道深度为5.52m,尾部后烟道深度为8.28m,水冷壁下集箱标高为8.0m,顶棚管标高为67.750m。
锅炉的汽水流程以内置式启动分离器为界设计成双流程,从冷灰斗进口一直到标高46.459m的中间混合集箱之间为螺旋管圈水冷壁,再连接至炉膛上部的水冷壁垂直管屏和后水冷壁吊挂管,然后经下降管引入折焰角、水平烟道底包墙和水平烟道侧墙,再引入汽水分离器。
从汽水分离器出来的蒸汽引至顶棚和包墙系统,再进入低温过热器中,然后再流经屏式过热器和末级过热器。
再热器分为低温再热器和高温再热器两段布置,中间无集箱连接,低温再热器布置于尾部双烟道中的前部烟道,高温再热器布置于水平烟道中逆、顺流混合与烟气换热。
水冷壁为全膜式焊接水冷壁,下部水冷壁及灰斗采用螺旋管屏,上部水冷壁为垂直管屏,螺旋管屏和垂直管屏的过渡点在标高46.659m处,转换比为1:
3。
从炉膛出口至锅炉尾部,烟气依次流经上炉膛的屏式过热器、折焰角上方的末级过热器、水平烟道中的高温再热器,然后至尾部烟道中烟气分两路:
一路流经前部烟道中的立式和水平低温再热器、省煤器,另一路流经后部烟道的低温过热器、省煤器,最后进入下方的两台三分仓回转式空气预热器。
锅炉的启动系统为带再循环泵式启动系统,内置式启动分离器布置在锅炉的前部上方,其进口为水平烟道侧墙出口和水平烟道对流管束出口连接管,下部与贮水箱相连。
在直流负荷(30%BMCR)以下,汽水混合物在启动分离器中分离,蒸汽从分离器顶部引出到顶棚包墙和过热器中,分离下来的水经分离器进入贮水箱中。
当贮水箱中的水位在正常范围内,水经再循环泵排入到省煤器入口的主给水管道中,进行再循环;当水位高于正常水位时,通过打开溢流管的溢流调节阀将水排至疏水扩容器中。
过热器采用两级喷水减温器,一级减温器布置在低温过热器和屏式过热器之间,二级减温器布置在屏式过热器和末级过热器之间,每级两点。
再热蒸汽采用尾部烟气挡板调温,并在再热器入口管道备有事故喷水减温器。
制粉系统采用中速磨正压直吹系统,每炉配6台磨煤机,在5台磨煤机运行时能带额定负荷(ECR工况)。
每台磨煤机供布置于前墙或后墙同一层的LNASB燃烧器,前后墙各3层,每层布置5只。
在煤粉燃烧器的上方前、后墙各布置1层燃烬风,每层有5只风口。
锅炉布置有98只炉膛吹灰器、56只长伸缩式吹灰器、8只半伸缩式吹灰器,4只空气预热器吹灰器,吹灰器由程序控制。
炉膛出口两侧各装设一只烟气温度探针,右侧设置炉膛监视闭路电视系统的摄像头用于监视炉膛燃烧状况。
锅炉除渣采用一台刮板式捞渣机,装于炉膛冷灰斗下部。
8汽水系统(汽水流程图见附图01-05~10)
8.1.给水管道
从高加出口引来的锅炉主给水管道布置在锅炉构架内的右侧、26.893m的标高处,规格为φ508mm×60mm,材料为WB36。
在给水操纵台上的主给水管道上布置有一只18”的电动闸阀和一只止回阀,电动闸阀并联有一只10”的调节阀,调节阀的通流能力为35%BMCR,满足锅炉启动和最低直流负荷(本生负荷)的需要。
此调节阀主要用于锅炉启动阶段在未达到直流负荷之前的给水调节。
当主给水闸阀全开后,调节阀关闭。
阀门在关闭时仍有3%BMCR的通流量,保证省煤器和水冷壁在任何情况下均有适当的冷却。
在给水操纵台后的主给水管道上有过热器减温水总管、循环泵过冷管、省煤器再循环管路的接头和一只用于测量省煤器入口水流量的长颈喷嘴。
长颈喷嘴用来测量进入省煤器中给水和再循环的总流量,这个流量一直等于或大于本生流量(30%BMCR),因此测量的精度可以得到保证。
这样,本生流量的测量来自一个单独的流量测量装置,而没有必要将来自两个流量测量装置(给水流量和再循环流量)的信号相加,测量和控制方法简单。
此外,在锅炉启动初期,给水流量很小,测量的给水流量精确性差。
主给水管道在标高30.300m通过三通变为φ356×42水平横向布置的管道,管道的两端再通过三通向上分别与前、后烟道中的各一只φ324mm×42mm的省煤器入口集箱相连接。
8.2.省煤器及出口连接管
在尾部的前、后烟道内低温再热器和低温过热器下均布置有省煤器管组。
省煤器采用H型双肋片管。
肋片间节距均为25mm,基管规格为φ44.5mm×6MWTmm,材质为SA-210C;肋片尺寸为3mm×90mm×195mm,材质为酸洗碳钢板。
低温过热器出口烟道省煤器采用顺列布置,纵向节距为100mm,纵向排数为14排,管组高度为1300mm;横向节距为104mm,横向排数为212排,管组宽度为21944mm;管组有效深度为7630mm。
低温再热器出口烟道省煤器同样采用顺列布置的结构形式,纵向节距为100mm,纵向排数为14排,管组高度为1300mm;横向节距为104mm,横向排数为212排,管组宽度为21944mm;管组有效深度为4730mm。
两组省煤器均采用悬吊结构的方式,每组吊板悬吊在省煤器出口集箱下,分别悬挂两排省煤器管束。
吊板采用16mm厚的钢板,材料为12Cr1MoV。
两组省煤器连接出口集箱的管束,均加装瓦形防磨罩,其材料为1Cr6Si2Mo,厚度为3mm;两组省煤器的最上排均加装梳形防磨罩,其材料为SUS304,厚度为1.5mm。
两组省煤器管组与烟道前后墙及两侧墙间均布置烟气阻流隔板,隔板材料为12Cr1MoV,厚度为6mm。
在吹灰器工作范围内省煤器管布置防吹损的护板。
每组省煤器管组均有两只φ273×50、材料为SA-106C的出口集箱,每只集箱上引出95根悬吊管,再热器侧吊挂管为φ51×10MWT,过热器侧吊挂管为φ57×13MWT,材料为15CrMoG。
前后烟道中的4排悬吊管不仅承担省煤器管组的重量,其从下至上穿过尾部烟道,还用以吊挂水平低温再热器和水平低温过热器,并穿过后烟道顶棚管与各自的悬吊管出口集箱连接。
悬吊管出口集箱均设有放气管,然后合并成一根φ76×8.5MWT的放气总管与分离器入口的一根引入管相连接,总管上设置有一只电动截止阀。
当任何燃烧器点火时此阀门关闭,当炉膛内无火焰时此阀门立即打开,该管路除用于锅炉上水时排放空气外,另一目的是在锅炉点火之前将省煤器中产生的蒸汽排出,避免蒸汽进入水冷壁管中影响水动力的安全。
4只φ273×50悬吊管出口集箱的两端分别连接至烟道包墙两侧的φ508×70过渡集箱,过渡集箱再通过φ406×60的连接管在标高46.456m处汇集成一根φ559×80的下降管。
此下降管上接出两根φ38×6.5MWT的管路,一根连接至省煤器再循环管,作为循环泵停运时的暖泵管路;另一根与贮水箱溢流管相连,作为溢流管的暖管管路,一直将水引至溢流阀的上游,保持管路的暖态,避免当贮水箱突然产生水位而使管路受到热冲击。
这两路暖管管路引入的水最后都会进入到贮水箱中,并被蒸发进入过热器系统。
φ559×80的下降管在标高11.5m处又分成两根φ406×60的小下降管,并分别引至炉膛冷灰斗处的两侧与φ559×75分配集箱连接。
每根下降管分配集箱引出16根φ114×20的连接管分别与水冷壁入口前、后集箱连接。
8.3.水冷壁、折焰角和水平烟道包墙
水冷壁、折焰角和水平烟道包墙均为管子加扁钢焊接成的膜式管屏。
给水经省煤器加热后进入规格为φ219×45mm、材料为SA-106C的水冷壁下集箱(其标高为8.0m),经水冷壁下集箱再进入水冷壁冷灰斗。
冷灰斗的角度为55°,下部出渣口的宽度为1426.72mm。
灰斗部分的水冷壁由前、后水冷壁下集箱引出的436根直径φ38mm、壁厚为6.5MWT、材料为15CrMoG、节距为53(52.79)mm的光管组成的管带围绕成。
经过灰斗拐点(标高为18.144m)后,管带以17.893°的螺旋倾角继续盘旋上升。
在炉膛的四角,螺旋管屏以250mm的弯曲半径进行弯制。
螺旋管屏上升过程中,将绕过前后墙各三层的煤粉燃烧器和各一层的燃烬风喷口形成喷口管屏,燃烬风喷口布置在煤粉燃烧器上方,每层燃烧器为5只,每层燃烬风喷口为5只。
螺旋管圈水冷壁在标高46.459m处通过规格为φ219×60、材料为SA-335P12的中间集箱转换成垂直管屏。
相邻的中间集箱均用1根φ89×16的压力平衡管连接。
垂直管屏由1312根φ31.8×5.5MWT、材料为15CrMoG、节距为57.5mm的管子组成。
前、后墙垂直管屏各由385根管子组成,两侧墙管屏各由271根管子组成。
前墙和两侧墙垂直管屏上升并与位于顶棚上方的出口集箱相连接,后墙垂直管屏上升与标高52.061m的φ273×60后水吊挂管入口集箱相接,此集箱引出95根φ76×12.5MWT的吊挂管至标高68.8m的吊挂管出口集箱。
在水动力分析完成后,为保证四面水冷壁的流量分配均衡,防止吊挂管在低负荷时发生流动停滞,在所有后水吊挂管入口段均加装了节流短管,用以增加管屏的流动阻力。
在运行过程中为监控水冷壁的壁温,在螺旋水冷壁管出口装设了73个壁温测点,在前、侧墙垂直管屏和后水吊挂管出口共装设了87个壁温测点。
前、侧垂直管屏出口集箱和吊挂管出口集箱分别引出12根、14根和10根共36根φ168×35的引出管与上炉膛两侧的各1根φ559的下降管相连。
下降管向下再向后在折焰角后标高52.506m处汇合成折焰角入口汇集集箱。
从折焰角入口汇集集箱引出42根φ114×22和6根φ168×30的连接管分别与φ273×60折焰角入口集箱和φ219×52水平烟道侧包墙入口集箱相接。
折焰角由385根φ44.5×6.3MWT、节距为57.5mm的管子组成,其穿过后水吊挂管形成水平烟道底包墙,然后形成纵向4排节距为100mm、横向95排节距为230mm的水平烟道管束与出口集箱相连。
水平烟道侧墙由92根φ44.5×6.3MWT、节距为115mm的管子组成,其φ273×60的出口集箱与φ219×52的水平烟道管束出口集箱共引出24根φ168×30的连接管与4只启动分离器相连接。
8.4.启动系统
启动系统为内置式带再循环泵系统。
锅炉负荷小于30%B-MCR直流负荷时,分离器起汽水分离作用,分离出的蒸汽进入过热器系统,水则通过连接管进入贮水箱,根据贮水箱中的水位由再循环泵排到省煤器前的给水管道中或经溢流管排到疏水扩容器中。
锅炉负荷在30%BMCR以上时,分离器呈干态运行,只作为一个蒸汽的流通元件。
启动系统按全压设计。
启动系统由如下设备和管路组成:
1)启动分离器及进出口连接管;2)贮水箱;3)溢流管及溢流阀;4)疏水扩容器;5)再循环泵及再循环管路;6)最小流量管路;7)过冷管;8)循环泵暖管管路;9)溢流管暖管管路;10)压力平衡管路。
启动分离器为立式筒体,共4