金相制备整理资料.docx
《金相制备整理资料.docx》由会员分享,可在线阅读,更多相关《金相制备整理资料.docx(35页珍藏版)》请在冰豆网上搜索。
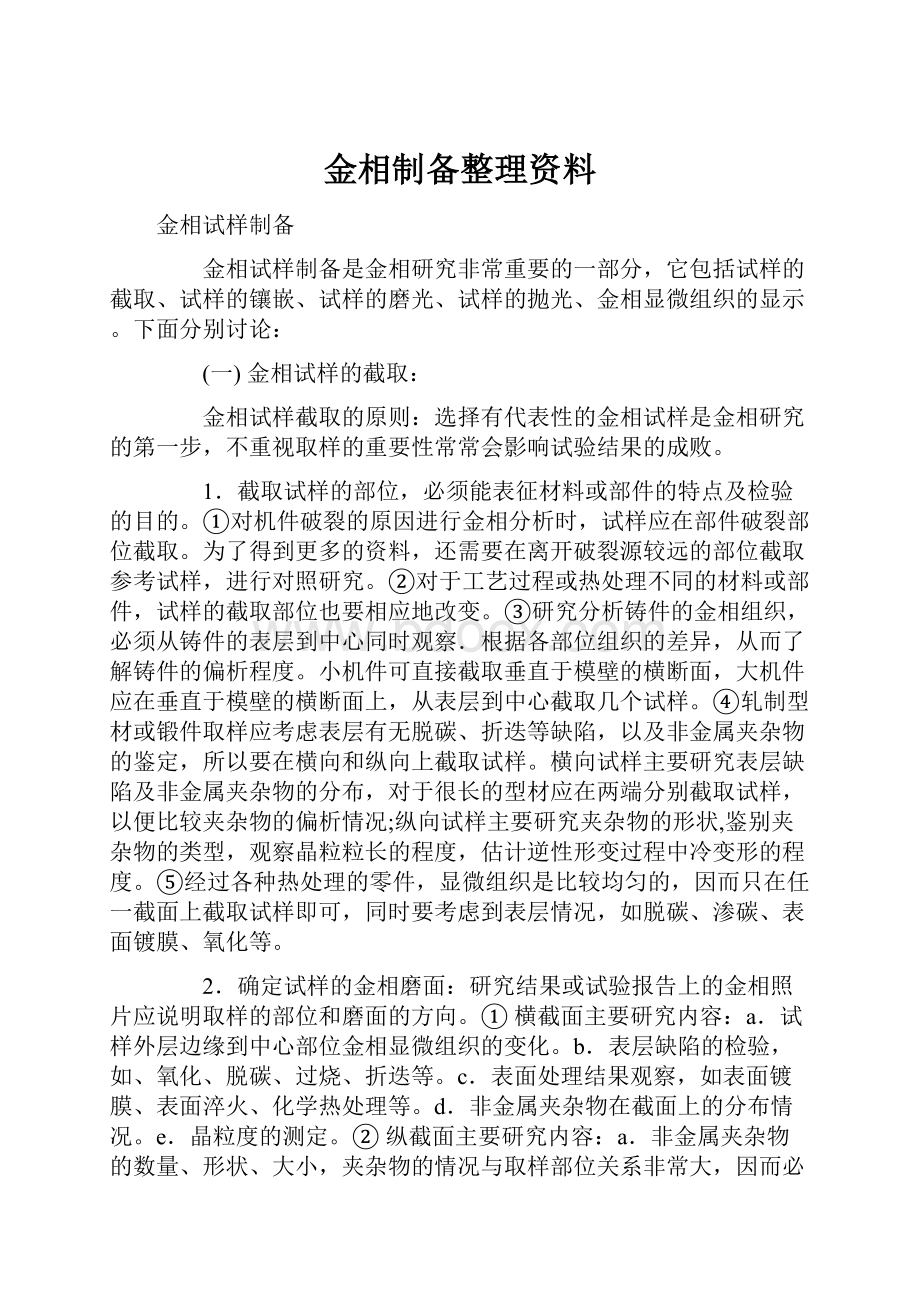
金相制备整理资料
金相试样制备
金相试样制备是金相研究非常重要的一部分,它包括试样的截取、试样的镶嵌、试样的磨光、试样的抛光、金相显微组织的显示。
下面分别讨论:
(一)金相试样的截取:
金相试样截取的原则:
选择有代表性的金相试样是金相研究的第一步,不重视取样的重要性常常会影响试验结果的成败。
1.截取试样的部位,必须能表征材料或部件的特点及检验的目的。
①对机件破裂的原因进行金相分析时,试样应在部件破裂部位截取。
为了得到更多的资料,还需要在离开破裂源较远的部位截取参考试样,进行对照研究。
②对于工艺过程或热处理不同的材料或部件,试样的截取部位也要相应地改变。
③研究分析铸件的金相组织,必须从铸件的表层到中心同时观察.根据各部位组织的差异,从而了解铸件的偏析程度。
小机件可直接截取垂直于模壁的横断面,大机件应在垂直于模壁的横断面上,从表层到中心截取几个试样。
④轧制型材或锻件取样应考虑表层有无脱碳、折迭等缺陷,以及非金属夹杂物的鉴定,所以要在横向和纵向上截取试样。
横向试样主要研究表层缺陷及非金属夹杂物的分布,对于很长的型材应在两端分别截取试样,以便比较夹杂物的偏析情况;纵向试样主要研究夹杂物的形状,鉴别夹杂物的类型,观察晶粒粒长的程度,估计逆性形变过程中冷变形的程度。
⑤经过各种热处理的零件,显微组织是比较均匀的,因而只在任一截面上截取试样即可,同时要考虑到表层情况,如脱碳、渗碳、表面镀膜、氧化等。
2.确定试样的金相磨面:
研究结果或试验报告上的金相照片应说明取样的部位和磨面的方向。
①横截面主要研究内容:
a.试样外层边缘到中心部位金相显微组织的变化。
b.表层缺陷的检验,如、氧化、脱碳、过烧、折迭等。
c.表面处理结果观察,如表面镀膜、表面淬火、化学热处理等。
d.非金属夹杂物在截面上的分布情况。
e.晶粒度的测定。
②纵截面主要研究内容:
a.非金属夹杂物的数量、形状、大小,夹杂物的情况与取样部位关系非常大,因而必须注意取样部位能代表整块材料。
b.测定晶粒拉长的程度,了解材料冷变形的程度。
c.鉴定钢的带状组织以及热处理消除带状组织的效果。
3.金相试样截取截面方法:
试样的截取必须采用合适的方法,避免因切割加工不当而引起显微组织的变化。
引起组织变化的可能性有两方面必须注意:
①逆性变形使金相组织发生变化。
如低碳钢、有色金属中晶粒受力压缩拉长或扭曲,多晶锌晶粒内部形变挛晶的出现,奥氏体类钢晶粒内部滑移线的增加等都是容易发生的毛病。
尤其某些低熔点金属{锡、锌等),由于它们的再结晶温度低于室温,如果试样发生逆性变化,将同时伴随有再结晶过程,使原来的组织、晶粒大小发生根本改变。
②材料因受热引起的金相组织变化.如淬火马氏体组织,往往因磨削热影响,使马氏体回火.产生回火马氏体。
③根据材料的硬度不同,采用不同方法截取试样。
a.对软性的材料可用手锯或锯床等截取。
b.极硬的合金材料,如淬火钢及硬质合金等,可用砂轮片,金相试样切割机截取。
c.硬脆合金一般用锤击,挑选合适的碎块,然后镶嵌成规整的试样。
d.斜面截取法对表层金相组织的分析研究是一种有效的方法,在很多情况下表层厚度极薄,在一般试样截面上是一条极细的线条,无法观察到清晰的组织。
但采用斜面截切法可扩大观察范围,如表面镀层、拜尔培层的研究。
(二)金相试样的镶嵌适用于对不是整形、不易于拿的微小金相试样进行热固性塑料压制,如线材、细小管材、薄板、锤击碎块等。
在磨光时不易握持,用镶嵌方法镶成标准大小的试块,然后进行切割、抛光等。
常用的镶嵌法有低熔点合金镶嵌法、塑料镶嵌法。
实验室金相试样制备过程大概如下:
正确地检验和分析金属的显微组织必须具备优良的金相样品。
制备好的试样应能观察到真实组织、无磨痕、麻点与水迹,并使金属组织中的夹物、石墨等不脱落。
否则将会严重影响显微分析的正确性。
金相样品的制备分取样、磨制、抛光、组织显示(浸蚀)等几个步骤。
1、取样
选择合适的、有代表性的试样是进行金相显微分析的极其重要的一步,包括选择取样部位、检验面及确定截取方法、试样尺寸等。
(1)取样部位及检验面的选择
取样的部位和检验面的选择,应根据检验目的选取有代表性的部位。
例如:
分析金属的缺陷和破损原因时,应在发生缺陷和破损部位取样,同时也应在完好的部位取样,以便对比;检测脱碳层、化学热处理的渗层、淬火层、晶粒度等,应取横向截面;研究带状组织及冷塑性变形工件的组织和夹杂物的变形情况时,则应截取纵向截面。
(2)试样的截取方法
试样的截取方法可根据金属材料的性能不同而异。
对于软材料,可以用锯、车、刨等方法;对于硬材料,可以用砂轮切片机切割或电火花切割等方法;对于硬而脆的材料,如白口铸铁,可以用锤击方法;在大工件上取样,可用氧气切割等方法。
在用砂轮切割或电火花切割时,应采取冷却措施,以减少由于受热而引起的试样组织变化。
试样上由于截取而引起的变形层或烧损层必须在后续工序中去掉。
(3)试样尺寸和形状
金相试样的大小和形状以便于握持、易于磨制为准,通常采用直径ф15~20mm、高15~20mm的圆柱体或边长15~20mm的立方体。
2.磨制:
分粗磨和细磨两步。
试样取下后,首先进行粗磨。
如是钢铁材料试样可先用砂轮粗磨平,如是很软的材料(如铝、铜等有色金属)可用锉刀锉平。
在砂轮上磨制时,应握紧试样,使试样受力均匀,压力不要太大,并随时用水冷却,以防受热引起金属组织变化。
此外,在一般情况下,试样的周界要用砂轮或锉刀磨成圆角,以免在磨光及当抛光时将砂纸和抛光织物划破。
但是,对于需要观察表层组织(如渗碳层,脱碳层)的试样,则不能将边缘磨圆,这种试样最好进行镶嵌。
细磨是消除粗磨时产生的磨痕,为试样磨面的抛光做好准备。
粗磨平的试样经清水冲洗并吹干后,随即把磨面依次在由粗到细的各号金相砂纸上磨光。
常用的砂纸号数有01、02、03、04号4种,号小者磨粒较粗,号大者较细。
磨制时砂纸应平铺于厚玻璃板上,左手按住砂纸,右手握住试样,使磨面朝下并与砂纸接触,在轻微压力作用下把试样向前推磨,用力要均匀,务求平稳,否则会使磨痕过深,且造成试样磨面的变形。
试样退回时不能与砂纸接触,这样“单程单向”地反复进行,直至磨面上旧的磨痕被去掉,新的磨痕均匀一致为止。
在调换下一号更细的砂纸时,应将试样上磨屑和砂粒清除干净,并转动90°角,使新、旧磨痕垂直。
金相试样的磨光除了要使表面光滑平整外,更重要的是应尽可能减少表层损伤。
每一道磨光工序必须除去前一道工序造成的变形层(至少应使前一道工序产生的变形层减少到本道工序生产的变形层深度),而不是仅仅把前一道工序的磨痕除去;同时,该道工序本身应尽可能减少损伤,以便进行下一道工序。
最后一道磨光工序产生的变形层深度应非常浅,应保证能在下一道抛光工序中除去。
磨制铸铁试样时,为了防止石墨脱落或产生曳尾现象,可在砂纸上涂一薄层石墨或肥皂作为润滑剂。
磨制软软的有色金属试样时,为了防止磨粒嵌入软金属内和减少磨面的划损,可在砂纸上涂一层机油、汽油、肥皂水溶液或甘油水溶液作润滑剂。
金相试样还可以用机械磨制来提高磨制效率。
机械磨制是将磨粒粗细不同的水砂纸装在预磨机的各磨盘上,一边冲水,一边在转动的磨盘上磨制试样磨面。
配有微型计算机的自动磨光机可以对磨光过程进行程序控制,整个磨光过程可以在数分钟内完成。
3.抛光:
目的为去除金相磨面上因细磨而留下的磨痕,使之成为光滑、无痕的镜面。
金相试样的抛光可分为机械抛光、电解抛光、化学抛光三类。
机械抛光简便易行,应用较广。
(1)机械抛光
机械抛光是在专用的抛光机上进行的,抛光机主要是由电动机和抛光圆盘(Ф200~300mm)组成,抛光盘转速为200~600r/min以上。
抛光盘上铺以细帆布、呢绒、丝绸等。
抛光时在抛光盘上不断滴注抛光液。
抛光液通常采用Al2O3、MgO或Cr2O3等细粉末(粒度约为0.3~1μm)在水中的悬浮液。
机械抛光就是靠极细的抛光粉末与磨面间产生相对磨削和液压作用来消除磨痕的。
操作时将试样磨面均匀地压在旋转的抛光盘上,并沿盘的边缘到中心不断作径向往复运动。
抛光时间一般为3~5min。
抛光后的试样,其磨面应光亮无痕,且石墨或夹杂物等不应抛掉或有曳尾现象。
这时,试样先用清水冲诜,再用无水酒精清洗磨面,最后用吹风机吹干。
(2)电解抛光
电解抛光是利用阳极腐蚀法使试样表面变得平滑光高的一种方法。
将试样浸入电解液中作阳极,用铝片或不锈钢片作阴极,使试样与阴极之间保持一定距离(20~30mm),接通直流电源。
当电流密度足够时,试样磨面即由于电化学作用而发生选择性溶解,从而获得光滑平整的表面。
这种方法的优点是速度快,只产生纯化学的溶解作用而无机械力的影响,因此,可避免在机械抛光时可能引起的表层金属的塑性变形,从而能更确切地显示真实的金相组织。
但电解抛光操作时工艺规程不易控制。
(3)化学抛光
化学抛光的实质与电解抛光相类似,也是一个表层溶解过程。
它是一种将化学试剂涂在试样表面上约几秒至几分钟,依靠化学腐蚀作用使表面发生选择性溶解,从而得到光滑平整的表面的方法。
4.组织显示:
由于金属中合金成分和组织的不同,造成腐蚀能力的差异,腐蚀后使各组织间、晶界和晶内产生一定的衬度,金属组织得以显示。
常用的金相组织显示方法有:
(1)化学浸蚀法;
(2)电解浸蚀法;(3)金相组织特殊显示法,其中化学浸蚀法最为常用。
经抛光后的试样若直接放在显微镜下观察,只能看到一片亮光,除某些非金属夹杂物(如MnS及石墨等)外,无法辨别出各种组成物及其形态特征,必须使用浸蚀剂对试样表面进行“浸蚀”,才能清楚地看到显微组织的真实情况。
钢铁材料最常用的浸蚀剂为3%~4%硝酸酒精溶液或4%苦味酸酒精溶液。
最常用的金相组织显示方法是化学浸蚀法,其主要原理是利用浸蚀剂对试样表面的化学溶解作用或电化学作用(即微电池原理)来显示组织。
对于纯金属单相合金来说,浸蚀是一个纯化学溶解过程。
由于金属及合金的晶界上原子排列混乱,并有较高的能量,故晶界处容易被浸蚀而呈现凹沟。
同时,由于每个晶粒原子排列的位向不同,表面溶解速度也不一样,因此,试样浸蚀后会呈现出轻微的凹凸不平,在垂直光线的照射下将显示出明暗不同的晶粒。
对于两相以上的合金而言,浸蚀主要是一个电化学腐蚀过程。
由于各组成具有不同的电极电位,试样浸入浸蚀剂中就有两相之间形成无数对“微电池”。
具有负电位的一相成为阳极被迅速浸入浸蚀剂中形成凹洼;具有正电位的另一相则为阴极,在正常电化学作用下不受浸蚀而保持原有平面。
当光线照射到凹凸不平的试样表面时,由于各处对光线的反射程度不同,在显微镜下就能看到各种不同的组织和组成相。
浸蚀方法是将试样磨面浸入浸蚀剂中,或用棉花沾上浸蚀剂控试表面。
浸蚀时间要适当,一般试样磨面发暗时就可停止。
如果浸蚀不足,可重复浸蚀。
浸蚀完毕后,立即用清水冲诜,接着用酒精冲洗,最后用吹风机吹干。
这样制得的金相试样即可在显微镜下进行观察和分析研究。
如果一旦浸蚀过度,试样需要重新抛光,甚至还需在04号砂纸上进行磨光,再去浸蚀
、
提高T12钢强韧性并获得板条马氏体优化方案
quanmuyi
(材料成型07-2)
摘要常规T12钢热处理为直接淬火回火工艺,获得组织硬度高韧性差,本实验采用等温淬火工艺获得下贝氏体和板条马氏体组织具有高韧性和高强度,采用低温淬火工艺过程简单获得大量板条马氏体是材料强韧性能提高
关键词T12钢强韧性板条马氏体
1引言
既有高强度又有高韧性、耐疲劳又能经受多次冲击的位错型板条马氏体形态的利用,已大大超出了低碳钢的范畴,改变热处理工艺参数,可以在中碳及高碳钢已获得以板条马氏体为主的淬火组织,显著改善中碳钢及高碳钢的强韧性,这种控制淬火组织一形态的方法已经成为中、高碳钢强韧性的一条重要途径。
对高碳钢,为减少因塑性、韧性低而产生的折断报废,应设法保存较多的未溶渗碳体以降低奥氏体含碳量,从而生成较多甚至全部板条马氏体,如低温、快速、短时奥氏体化淬火。
本实验利用这些原理对传统生产工艺进行参数优化和方案优化。
2实验材料、实验设备
钢号
C%
Si%
Mn%
S%
P%
T12
1.13
0.23
0.23
0.105
0.021
用10吨万能材料试验机进行拉伸试验,用NMT-3型显微硬度计和洛氏硬度硬度计测定试样表面硬度,用透射电镜和NEOPHT型卧式显微镜拍照金相组织。
加热用SG-5-10电阻炉将试样放入钢管内,填木碳保护。
等温淬火用自制外热式盐炉,盐浴成分为55%KNO3+45%NaNO2,用UJ-37电位差计、水银温度计和调压器联合控制等
温温度。
误差控制在±3℃内。
3原理:
1高碳钢要获得优异的强韧性,其组织应具备下列特点:
1)球化组织中的碳化物要均匀、细小、圆整,因此淬火后的剩余碳化物也应均匀、细小、圆整。
2)马氏体针要均匀、细致,板条马氏体的份额要高。
为此,应细化奥氏体晶粒,先形成适量下贝氏体,以细化后形成马氏体的伸展空间。
碳化物颗粒应均、细小以及微区化学成分不均匀等,都可细化马氏体。
有时同时能增加板条马氏体的份额。
2高碳钢获得板条马氏体的途径:
马氏体的形态与奥氏体的含碳量有关。
奥氏体的含碳量低于0.5%时,淬火后基本上是板条马氏体组织;含碳量高于1.0%时,淬火后基本上是片状马氏休组织;含碳量为0.5%-1.0%时,淬火后是板条马氏体组织与片状马氏体组织的混合组织,而且随着含碳量的增加,板条马氏体组织减少。
既有高强度又有高韧性、耐疲劳又能经受多次冲击的位错型板条马氏体形态的利用,已大大超出了低碳钢的范畴,改变热处理工艺参数,可以在中碳及高碳钢已获得以板条马氏体为主的淬火组织,显著改善中碳钢及高碳钢的强韧性,这种控制淬火组织一形态的方法已经成为中、高碳钢强韧性的一条重要途径。
对高碳钢,为减少因塑性、韧性低而产生的折断报废,应设法保存较多的未溶渗碳体以降低奥氏体含碳量,从而生成较多甚至全部板条马氏体,如低温、快速、短时奥氏体化淬火。
3等温淬火:
等温淬火是将奥氏体化的工件淬入等温淬火的显著特点是保证有较高硬度的同时,还保持有很高的韧性。
淬火变形小。
4低温淬火:
低温淬火将正常加热温度压低20-30度,可获得体积分数为50%以上的板条马氏体的淬火组织,孪晶马氏体也较细可以提高模具韧性。
4试验方法:
(—)1预备热处理
(1)正火920度(小工件保温15min大工件保温1h,细化过热钢的晶粒和消除过共析钢的网状碳化物)
(2)球化退火780(小工件保温20min大工件保温数h改善钢材的可加工性和热处理工艺性)
(3)去应力退火650度(保温一小时空冷)
2淬火
(1)大工件(预热500-600度)
(2)加热到800度水淬火
(3)在345度等温淬火
3回火
300度回火(在300度回火使马氏体中过饱和碳原子沉淀析出弥散分布的Ɛ-相既提高钢的韧性,又保持较强的强度、硬度和耐磨性。
),大工件两次回火。
)
(二)1预备热处理
(1)正火920度(小工件保温15min大工件保温1h,细化过热钢的晶粒和消除过共析钢的网状碳化物)
(2)球化退火780度(小工件保温20min大工件保温数h改善钢材的可加工性和热处理工艺性)
(3)调质。
(4)去应力退火650度(保温一小时空冷)
2淬火
(4)大工件(预热500-600度)
(5)加热到760度水淬火
3回火
300度回火(在300度回火使马氏体中过饱和碳原子沉淀析出弥散分布的Ɛ-相既提高钢的韧性,又保持较强的强度、硬度和耐磨性。
,大工件两次回火。
图示为T12钢等温淬火的机械性能
T12虽然在低温区295℃;300℃有ɸk的峰值,但
数值较低,350℃虽有ɸk的峰值,但却是下贝氏体和上贝氏体的过渡温度,所以取345℃是合
理的。
T12钢仪表元件常规工艺与等温淬火模具寿命比较
热处理工艺
硬度HRC
寿命/次
失效形式
备注
常规工艺
780淬火+300回火
>55
5500
根部断裂
报废
等温淬火工艺
780加热+345等温淬火
53.5-55
19730
刃口钝
刃磨后可再用
5结论:
1)高碳钢经过等温淬火有效提高了强韧性。
2)高碳钢采用调质加低温淬火工艺简单使组织获得大量板条马氏体,材料韧性提高较大。
3)低温、快速、短时奥氏体化淬火,生成较多板条马氏体,使高碳钢强韧性增强。
6参考文献:
1、热处理工艺及设计上海交大出版社彭其凤丁洪太主编
2、实用热处理技术及应用机械工业出版社马博龙王建林编著
3、热处理工作者手册机械工业出版社
4、新版工具钢金像热处理机械工业出版社蔡美良丁惠麟孟卢龙编著
5、板条马氏体淬火在模具强韧化处理中的应用长沙航空职业技术学院机电工程系(湖南长沙410124)刘劲松《模具制造》2003.No.8总第25期
6、碳钢等温淬火最佳参数的研究内蒙古工业大学学报第17卷 第2期燕来生1 张伟华
零件热处理裂纹的分析与对策
(1)
哈尔滨第一工具厂(黑龙江 150020)祝国华 战祥丽
零件在热处理过程中产生的裂纹是最严重的热处理缺陷之一。
这种缺陷通常是无法补救的,零件只能报废,因而它引起了热处理工作者的特别重视。
1.零件热处理裂纹产生的原因
零件在热处理过程中会产生很大的内应力(组织应力和热应力),当这些应力超过钢的屈服强度时,会引起零件的变形;当应力更大,超过钢的抗拉强度时,则会造成零件的开裂。
作用在零件上的应力有两种:
压应力和拉应力。
淬火时形成的拉应力是引起淬火裂纹的主要原因。
但是当钢的塑性较高时,即使有较大的拉应力也不会引起零件的开裂,比如没有发生组织转变的去应力退火,获得较多残留奥氏体的等温淬火等。
只有在应力较大,又具备了高硬度、脆性大的组织时,才容易造成零件的开裂。
故淬火裂纹的形成必须同时存在两个条件:
一是具有脆性组织;二是拉应力超过了此时钢的抗拉强度(当然其他情况也能促使零件裂纹发生,比如原材料缺陷、设计及机械加工不当造成的缺陷等)。
2.关于裂纹的类型
裂纹的分类方法各种各样。
按裂纹的方向分,有纵向裂纹、横向裂纹、弧形裂纹和网状裂纹(又称龟裂)等;按裂纹发生的位置分,有表层裂纹(或称表面裂纹)和内部裂纹;按裂纹发生在不同的工序分,有锻造裂纹、焊接裂纹、淬火裂纹、回火裂纹、冷处理裂纹、酸洗裂纹及磨削裂纹等。
零件在热处理过程中以淬火裂纹为最多。
3.裂纹的分辨方法
如何区分究竟是淬火裂纹、回火裂纹、锻造裂纹还是磨削裂纹等是很重要的,这样便于准确查找裂纹发生在哪一工序,有利于分析裂纹产生的原因。
第一,注意淬火裂纹和磨削裂纹形态的不同。
对于淬火时未发现而在磨削后才发现的裂纹,要区别是淬火裂纹还是磨削裂纹。
在裂纹未附着污染物时比较容易,此时注意裂纹的形态,特别是裂纹发展的方向,磨削裂纹是垂直于磨削方向的,呈平行线形态(如图1所示),或呈龟甲状裂纹(如图2所示)。
磨削裂纹的深度根浅,而淬火裂纹一般都比较深 比较大,与磨削方同无关,多呈直线刀割状开裂。
图l 平行线状磨削裂纹 图2 龟甲状磨削裂纹
第二,注意裂纹发生的部位。
尖锐的凹凸转角处、孔的边缘处、刻印处、打钢印处及机械加工造成的表面缺陷等部位,在这些部位发生的裂纹多属淬火裂纹。
第三,通过观察零件的裂断面来区分是淬火裂纹还是淬火前的锻造裂纹或其他情况造成的裂纹。
若裂纹断面呈白色或暗白色或浅红色(水淬时造成的水锈),均可断定为淬火裂纹,若裂纹断面呈深褐色,甚至有氧皮出现,那就不是淬火裂纹,系淬火前就存在的裂纹,是零件经过锻造或压延时形成的裂纹,这些裂纹都会因淬火而被扩大。
因淬火裂纹基本上是在MS点以下时形成的,其断面是不会被氧化的。
第四,在显微组织中,淬火裂纹是沿晶界断裂,若不是沿晶界断裂,而是沿晶内断裂,则属于疲劳裂纹。
第五,如果裂纹周围有脱碳层存在,那就不是淬火裂纹,而是淬火前就存在的裂纹,因为淬火裂纹是淬火冷却时产生的,绝不会发生脱碳现象。
4.检查裂纹的方法
检查零件有无裂纹,最简单、最常用的方法是将零件喷砂后用肉眼直接观察,或使用放大镜观察零件的表面即可。
当用眼睛或放大镜看不到裂纹时,还可用浸油探伤法检查。
即将零件浸入到煤油、汽油等油中,稍后取出零件用棉纱擦拭干净,再涂以石灰粉或其他白粉,如有裂纹,则在白色部分有油渗出。
有经验的检查人员还可以用敲击的方法检查出是否有裂纹,即用小锤等轻轻敲击零件,如果发出清晰的金属声音,尾音比较长,即可掣。
为没有裂纹;反之,若发出重浊的声名,就出现了裂纹。
还可以采用磁力探伤法及荧光探伤法检查零件是否有裂纹。
5.淬火过热与淬火裂纹
零件被加热到高出工艺规定的某一淬火加热温度并在一定的加热时间里,便会造成工件的淬火过热。
过热温度会因钢种的不同而不同。
工件一旦过热,则奥氏体晶粒粗化,生成的马氏体针也粗大。
容易产生马氏体微裂纹。
这种马氏体的微裂纹是淬火裂纹的激发源,并发展成为淬火裂纹。
过热使钢的性能变坏,强度与塑性大大降低。
生产现场中淬火过热引起的淬火裂纹在工具钢中最为常见,特别是高速工具钢因淬火过热造成工件裂纹的事例最多,这是由于高速钢的淬火加热温度接近其熔点,因此稍有不慎即可引起过热,甚至过烧。
某厂在热处理一批W18Cr4V钢制模数为m=12、外径为Φ170mm的盘形齿轮铣刀时,工艺规定的淬火加热温度为1270℃,但由于控温仪表失灵,表指温度比实际炉温低35℃,幸亏操作者发现炉温的变化,立即采取终止生产进行重新测温的措施,避免了大批过热产品的发生,但仍有少量齿轮铣刀出现了过热引起的裂纹,如图3所示。
金相检查发现淬火晶粒粗大,裂纹均发生于网状碳化物处,由此可见裂纹系加热温度过高所致。
因过热形成的共晶碳化物沿晶界呈网状分布,在晶界上形成一层硬壳使钢产生了很大的脆性,阻碍了钢的塑性变形,在淬火冷却时产生的极大应力作用下引起淬火裂纹。
图3 m=12、外径为Φ170mm的W18Cr4V钢盘形齿轮铣刀上的裂纹
防止零件因淬火过热而产生裂纹的主要措施是:
①工艺员要制定正确合理的加热温度和加热方法。
如对一些大规格碳化物偏析较严重的高速钢刀具,应采取高速钢下限的淬火加热温度,为保证加热充分,可适当延长加热时间,对一些带尖角的零件应离炉内加热体远一些,在盐浴炉中工件距电极盼距离不得小于50mm,以免引起尖角过热。
②对测温仪表和控温仪表要定期检查校对和维修,保证仪表始终在运转正常的条件下使用。
仪表员要保证测温、定温、调温时准确无误。
③淬火工要随时观察炉温的情况,发现炉温有异常变化时,及时找工艺员或仪表员等有关人员解决,必要时立即停产,重新测温,待炉温恢复正常后再进行生产。
④设备要保证工艺要求。
零件热处理裂纹的分析与对策
(2)
哈尔滨第一工具厂(黑龙江 150020)祝国华 战祥丽
6.加热速度过快、加热不均匀与淬火裂纹
零件加热速度过快和加热不均匀会使应力增加,尤其是合金元素较多、导热性较差和尺寸较大的高合金钢工件,在淬火加热前若不进行充分的预热,则在淬火时会因加热速度过快和加热不均而很可能导致产生裂纹。
生产中高速钢工件多采用550~600℃和850~900℃的两段预热,以减缓高速钢工件的加热速度,并使其得到充分均匀地加热,从而减少加热时的应力,同时也可缩短高