晋城二化合成氨原料气净化工艺路线的选择与应用.docx
《晋城二化合成氨原料气净化工艺路线的选择与应用.docx》由会员分享,可在线阅读,更多相关《晋城二化合成氨原料气净化工艺路线的选择与应用.docx(11页珍藏版)》请在冰豆网上搜索。
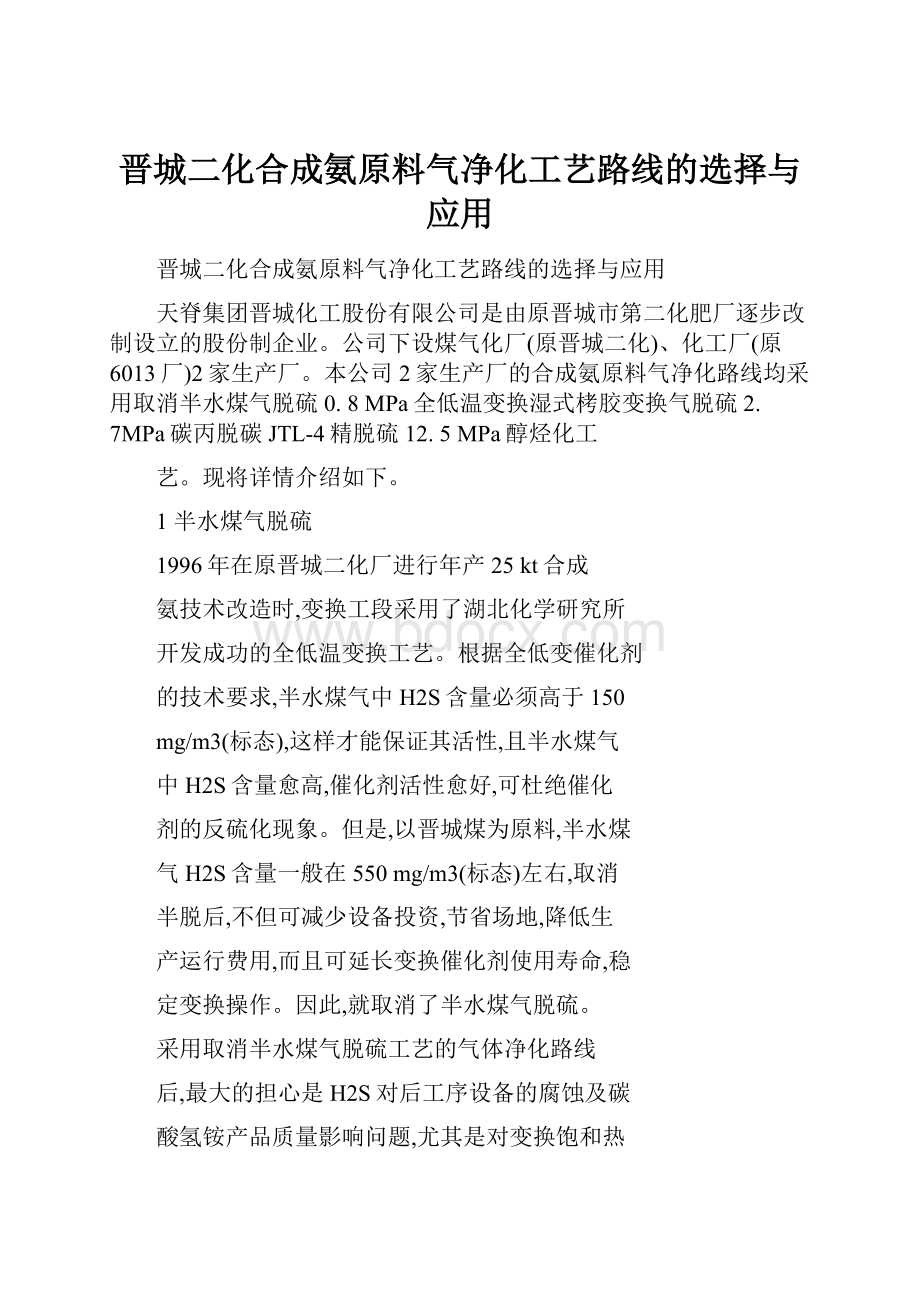
晋城二化合成氨原料气净化工艺路线的选择与应用
晋城二化合成氨原料气净化工艺路线的选择与应用
天脊集团晋城化工股份有限公司是由原晋城市第二化肥厂逐步改制设立的股份制企业。
公司下设煤气化厂(原晋城二化)、化工厂(原6013厂)2家生产厂。
本公司2家生产厂的合成氨原料气净化路线均采用取消半水煤气脱硫0.8MPa全低温变换湿式栲胶变换气脱硫2.7MPa碳丙脱碳JTL-4精脱硫12.5MPa醇烃化工
艺。
现将详情介绍如下。
1半水煤气脱硫
1996年在原晋城二化厂进行年产25kt合成
氨技术改造时,变换工段采用了湖北化学研究所
开发成功的全低温变换工艺。
根据全低变催化剂
的技术要求,半水煤气中H2S含量必须高于150
mg/m3(标态),这样才能保证其活性,且半水煤气
中H2S含量愈高,催化剂活性愈好,可杜绝催化
剂的反硫化现象。
但是,以晋城煤为原料,半水煤
气H2S含量一般在550mg/m3(标态)左右,取消
半脱后,不但可减少设备投资,节省场地,降低生
产运行费用,而且可延长变换催化剂使用寿命,稳
定变换操作。
因此,就取消了半水煤气脱硫。
采用取消半水煤气脱硫工艺的气体净化路线
后,最大的担心是H2S对后工序设备的腐蚀及碳
酸氢铵产品质量影响问题,尤其是对变换饱和热
水塔的腐蚀。
但是,从生产运行情况来看,以上问
题基本不存在。
1998年技改时拆开1台1400
mm饱和热水塔进行内部检查,除饱和塔热水进
口管及其分布器损坏外,塔壁无腐蚀现象;2003
年对1998年更换的2200mm饱和热水塔进行
全面检查,也是饱和塔热水进口管及其分布器损
坏,筒体气液接触部分有麻点,可以认为在气液接触部位有可能产生化学腐蚀和气流冲刷腐蚀。
2003年在化工厂新建1套180kt/a全低变装置
时,并为避免上述现象,将饱和塔上部气液接触部
位及封头、湿煤气出口U形管、热水进口L形管
(长度各1.5m)采用不锈钢材质。
关于对变换热
交换器的腐蚀问题,采取增设不锈钢预腐蚀器来
保护热交的方式。
关于H2S对碳化系统设备的
腐蚀问题,由变换气带过来的H2S在碳化液中与
Fe2+反应生成FeS。
由于FeS的存在,在设备内
壁形成了具有防腐作用的保护膜。
关于对化肥质
量影响的问题,H2S与NH3反应生成白色结晶硫
化铵,或夹带部分FeS使化肥颜色呈浅灰色。
从
农作物生长所需的十大营养元素C、H、O、N、P、
K、Ca、Mg、S、Fe来看,S、Fe也在其中。
S是构成
蛋白质和酶的主要成分,对促进植物根系生长有
良好的作用。
Fe是叶绿素形成不可缺少的条件,
其能促进作物呼吸,加速生理的氧化。
氨加工成
尿素,增加变换气脱硫之后,气体H2S含量[10
mg/m3(标态),不但对后工序没有影响,而且可将
硫泡沫回收加工成高品位硫磺。
20.8MPa全低温变换
从1996年开始将15kt/a合成氨装置由中串
低变换工艺改造成全低温变换工艺后,合成氨生
产能力不但达到了30kt/a,而且各种消耗大幅度
降低,为企业取得了较好的经济效益和社会效益。
在初次尝到变换新工艺应用带来的好处后,对装
置不断地进行技改和完善,合成氨生产能力最终
达到60kt/a。
此后,分别于2001年、2002年在所
属的煤气化厂和化工厂各新建1套60kt/a合成
氨装置,也采用全低变工艺。
2003年为建设化工
厂240kt/a合成氨、300kt/a大颗粒尿素工程的需要,又新建1套合成氨能力为180kt/a的全低
温变换系统,同年10月投入运行。
9年来,公司2
家厂共有4套全低温变换系统相继建成投运,总
合成氨生产能力已达360kt/a。
2.1典型工艺流程简述
由压缩来的半水煤气经半水煤气冷却器降温
后送至丝网除油过滤器滤掉气体中夹带的油分,
再进入饱和热水塔的饱和段。
在塔内气体与塔顶
喷淋而下的热水逆流接触,进行物热的传递。
经
提温增湿后的半水煤气进入湿煤气水分离器,分
离掉夹带的液滴后,气体进入预热交换器、主热交
换器提温,混合煤气温度升到180~200e进入变
换炉一段(原中变炉一、二段),在变换炉一段,通
过催化剂保护剂(可用旧催化剂)将气体中的杂
质进一步过滤,再通过抗毒剂除氧后进入变换炉
的一段催化剂床层。
经一段变换反应后,气体升
温至380e左右,CO含量由28%降到12%引出,
进入增湿净化炉,在此高热气体与大量的冷凝水
接触,在填料的表面上进行物质与热量的传递。
液相全部被蒸发,增加了气体中的水蒸气含量。
增湿降温至200e左右的气体进入变换炉的二段
催化剂床层,继续进行CO的变换反应。
出二段
催化剂床层约280e、CO含量~6%的气体进入
主热交换器、预热交换器换热降温至180e左右,
进入变换炉三段催化剂床层(原2#低变炉),继续
进行CO的变换反应。
经三段催化反应的变换气
CO含量达到4.0%(联醇)或1.5%离开变换炉。
合格的变换气经一水加热器、饱和热水塔的热
水段回收热量后,变换气温度约为70e。
为进一
步回收变换工段的低位热能,变换气去软水冷却器
换热,回收的热水送锅炉。
进一步降温后的变换气
去变换冷却器用循环水冷却至常温,再经变换气水
分离器分离掉夹带的液滴后送入下一系统。
2.2全低变工艺的优点
(1)全低变工艺对原料气中的H2S含量,只
有下限要求,而上限要求较宽,原料气中的H2S
含量可达到2g/m3(标态),因此可不设半水煤气
脱硫,只设变脱,可节省基建投资,减少占地面积,
降低消耗。
低变催化剂对有机硫的转化率高,可
更有效地净化气体,尤其适用于联产甲醇。
(2)催化剂的使用寿命长,一般在3年以上。
(3)节能效果明显,吨氨耗蒸汽150kg左右,
低变后气体中CO含量比传统的中变、中串低变
低2%~3%,从而减轻了铜洗的净化负荷,同时
由于变换率提高,合成氨的产量可相对增加。
(4)流程简单,方便管理和操作。
由于采用
喷水增湿净化流程,温度调节灵敏、可靠、安全。
2.3全低变工艺设备的选择
随着对全低变工艺的不断完善,也要不断地
对设备结构进行优化,以提高换热效果和降低系
统阻力。
主要采取了以下措施:
(1)变换系统的预腐蚀器(预热交换器)、水
加热器、热交换器、调温水加热器等换热设备都容
易腐蚀,除采取一定的防腐措施外,应加强对半水
煤气的除沫,因此在工艺流程中,用丝网除油器代
替原来的焦炭过滤器,设备内装2层不锈钢丝网
除沫器。
为了降低入口煤气冷却器、丝网除油器的阻
力,及时将分离出的油、水、灰尘清除掉,在煤气冷
却器换热管内和丝网除油器内每层丝网的上部增
加热水冲洗管,定时用热水冲洗换热管和丝网,并
及时将冲洗的油、水、灰尘等排入地沟。
(2)饱和热水塔由填料塔改为垂直筛板塔。
提高了饱和热水塔的换热效果,气、液在塔内充分
接触,提高了煤气的温度和湿度,提高了气汽比,
降低了补充蒸汽量,充分回收变换气的余热。
同
时热水塔出口变换气的温度降至70~80e,充分
回收低位热能。
(3)用折流杆式换热器代替折流板式换热
器,提高换热器的换热效率,减少换热面积和缩小
设备体积,降低流体阻力。
(4)喷水增湿净化炉内使用新型喷头,其雾化
度高,极大地提高了水、气之间的传热、传质效率。
(5)采用板式换热器,具有很高的传热系数,
在同样气量的情况下,换热器的面积小、阻力小,
即节约冷却水、又能降低系统阻力。
30.8MPa变换气栲胶法脱硫
从2000年煤气化厂改产大颗粒尿素开始,变
换气脱硫采用湿式加压栲胶法脱硫至今,在2家
生产厂已有3套装置运行,通过5年生产使用证
明,该工艺具有设备少、工艺流程简单、投资少,且操作方便、运行稳定、物料消耗低、脱硫效率高等
特点。
栲胶法脱硫用在高H2S含量的变换气脱
硫效果也很好,在取消半水煤气脱硫经变换后,变
换气H2S质量浓度在500~700mg/m3(标态)状
态下,可保证脱硫后气体中H2S质量浓度[10
mg/m3(标态),脱硫效率为99%,H2S吸收容量
达到0.106kg/m3,达到国内同行目前栲胶法脱硫
较好水平,从没有发生过液泛、堵塔现象,变脱系
统运行状态良好。
典型工艺流程为:
变换气经过变换气分离器
后,从下部进入变脱塔,自下而上与栲胶溶液逆流
接触,然后由顶部出来经分离器分离水分后回高压
机三段进口。
栲胶溶液由贫液泵打入变脱塔,由上
而下吸收H2S后,出变脱塔,经过喷射器进入再生
槽,减压解析出H2S并自吸空气再生,再生好的溶
液溢流至贫液槽,经贫液泵加压进入变脱塔循环使
用。
硫泡沫从再生槽的上部分离出来后溢流至硫
泡沫槽。
所有塔、泵的排出液均回收至地下槽,由
地下泵加压送入贫液槽,进行系统内循环。
栲胶法
变脱物料消耗很低,吨氨纯碱消耗0.17kg(1.8
元/kg)、栲胶0.02kg(15元/kg)、五氧化二钒
0.0025kg(160元/kg),吨氨耗栲胶溶液物料费仅
1.01元。
吨氨可回收硫磺1.8kg,约可收入1.44
元,足以弥补变脱化学物料消耗费用。
42.7MPa碳酸丙烯酯(PC)脱碳
氮肥行业所应用的主要有PC、MDEA、NHD
及PSA等脱碳法,应该讲这几种脱碳方法各有优
缺点,应用于合成氨生产其净化度及解吸CO2纯
度均能满足合成氨和尿素生产要求。
通过5年生
产运行证明,PC脱碳方法具有流程短、无需加热
和氨冷、能耗低等优点。
目前2家厂3套PC脱碳
装置运行稳定,2800mm脱碳塔、3800mm再
生塔系统合成氨生产能力已超120kt/a,3200
mm脱碳塔、5000mm再生塔系统合成氨生产
能力已超150kt/a。
脱碳选用2.7MPa压力PC
法,该压力下气体净化度较高、不耗热量和冷量、
富液能量可回收、气液比大、运行成本低、装置投
资相对较少。
工艺流程:
来自压缩的2.7MPa变换气,经进
口分离器分离掉其中油水后,自脱碳塔下部导入,然后经分离器,再在净化气洗涤段经脱盐水洗涤
回收所夹带碳丙雾沫后去压缩机五段进口;碳丙
液由脱碳泵打入冷却器后,从脱碳塔顶部导入,吸
收碳丙后经涡轮机组及闪蒸塔、再生塔的常解、真
解、气提段后循环使用。
碳丙液的再生无需加热
及氨冷,采用四段式分解再生(闪蒸、常解、真解
和气提)及对四气(净化气、闪蒸气、混解气、气提
气)夹带的碳丙进行洗涤回收。
5JTL-4精脱硫
为保护醇烃化甲醇铜系催化剂,在综合比较
的基础上,择优选用湖北省化学研究院的JTL-4
精脱硫工艺,从2002年11月投运至今已运行3
年多。
精脱硫后的净化气采用HC-2微量硫分
析仪进行检测,至今监测数据仍测不出。
原设计
生产规模为220kt/a,实际氨醇生产能力可达860
t/d。
可保证出口总硫(H2S+COS+CS2)[0.1
mg/m3(标态)、Cl-[0.01@10-6的指标要求。
其
工艺流程简单,操作方便,为合成氨系统的稳定运
行发挥了重要作用。
工艺流程:
来自脱碳工段的净化气首先经过
气液分离器进行气液分离,防止碳丙液夹带到精
脱工段,对脱硫剂使用造成影响。
分离后的气体
从第一脱硫塔顶部进入,首先通过T102型精脱硫
剂脱除H2S,由第一脱硫塔底部出来从第二脱硫
塔顶部进入,通过上段的ET-3型精脱氯剂脱除
净化气中微量氯。
经过上述两步净化的气体,再
通过T104常温转化吸收型精脱硫剂,将气体中有
机硫脱除后送出本系统。
工艺特点:
(1)工艺流程简单,只有3台设备,不需要加
热、降温,节省蒸汽、冷却水。
(2)2台脱硫塔气相均为上进下出流程,可避
免开、停车时气流冲击脱硫剂床层或带出脱硫剂。
(3)脱硫剂支撑采用驼峰分布器与20mm
瓷球铺底,气体分布效果好。
(4)不需设专人操作,可由脱碳或变换岗位
操作员兼职管理操作即可。
6醇烃化原料气精制
我公司化工厂在实施/18#300工程中,合成氨原料气精制采用湖南安淳高新技术有限公司新
开发的醇烃化工艺。
该工艺具有原料气精制度
高、操作简单、运行稳定、物耗少、工作环境清洁及
消除传统铜洗工艺对水、气污染等优点。
更重要
的是可提高资源利用率,将少量的(CO+CO2)全
部转化为甲醇,为企业增加了产品品种,并可根据
市场需求,对氨醇比进行适当调整。
本装置有2
套2000mm甲醇合成塔,设计能力为220kt/a
醇氨,可副产甲醇30~50kt/a。
2005年该装置共
生产氨醇261.3k,t超出设计能力,精制原料气微
量(CO+CO2)<10@10-6。
醇烃化精制工艺设
计为三塔流程,即A、B醇化塔和烃化塔。
A醇化
塔以净化为主,B醇化塔以产醇为主,提高醇氨
比,B、A塔串联运行。
醇烃原料气精制工艺流程如下:
压缩机六段
(12.5MPa)来原料气首先经系统油分离,再并联
分别进入A、B预热器及A、B醇化塔,出塔热气返
至预热器换热,然后进入A、B水冷和A、B醇分。
醇分离后气体合并可循环或不循环串联进入烃化系统;经过烃化预热器、烃化塔及预热器,再至水
冷、氨冷、烃分离送入合成系统,烃化气可进行单
系统循环亦可入醇化系统大循环。
7结语
通过5年的生产运行证明,所选用的合成氨
工艺原料气净化路线工艺技术先进,设备选型合
理。
同时,该装置通过积极选用国家近几年大力
推广的新技术、新工艺、新材料、新设备,集大、中、
小化肥先进技术之优点,充分体现出其能耗低、资
源综合利用率高、投资省、见效快的特点。
山西天
脊晋城化工公司目前正在建设1套/30#400(年
产240kt合成氨联产60kt甲醇、400kt大颗粒尿
素)工程,经过多次考察论证,合成氨原料气净化
工艺基本还是采用上述工艺路线,只是变换、变
脱、脱碳系统压力统一为2.2MPa,为避免因变换
压力升高对材料腐蚀影响,增设了半水煤气脱硫
装置。