榨汁机设计.docx
《榨汁机设计.docx》由会员分享,可在线阅读,更多相关《榨汁机设计.docx(52页珍藏版)》请在冰豆网上搜索。
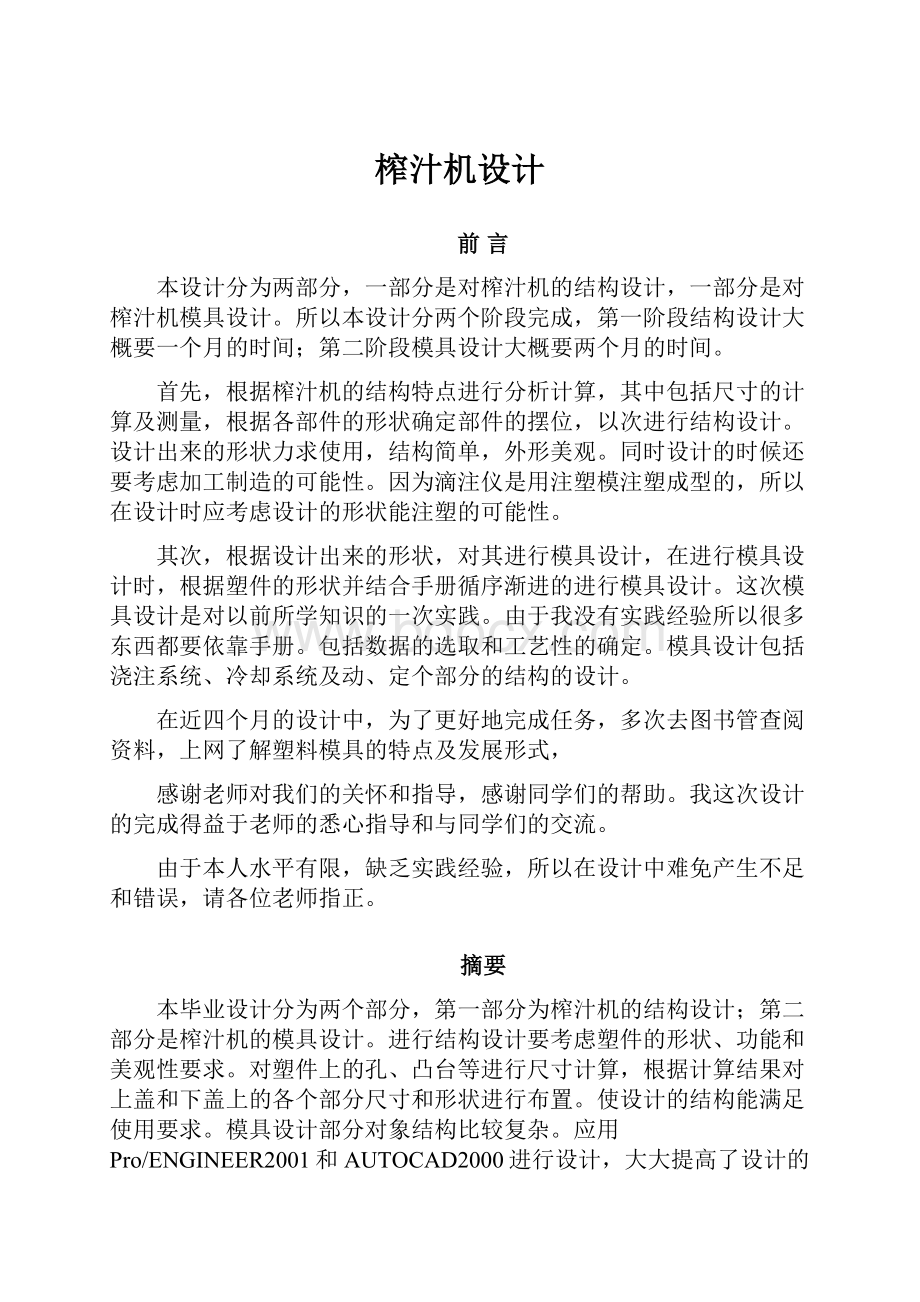
榨汁机设计
前言
本设计分为两部分,一部分是对榨汁机的结构设计,一部分是对榨汁机模具设计。
所以本设计分两个阶段完成,第一阶段结构设计大概要一个月的时间;第二阶段模具设计大概要两个月的时间。
首先,根据榨汁机的结构特点进行分析计算,其中包括尺寸的计算及测量,根据各部件的形状确定部件的摆位,以次进行结构设计。
设计出来的形状力求使用,结构简单,外形美观。
同时设计的时候还要考虑加工制造的可能性。
因为滴注仪是用注塑模注塑成型的,所以在设计时应考虑设计的形状能注塑的可能性。
其次,根据设计出来的形状,对其进行模具设计,在进行模具设计时,根据塑件的形状并结合手册循序渐进的进行模具设计。
这次模具设计是对以前所学知识的一次实践。
由于我没有实践经验所以很多东西都要依靠手册。
包括数据的选取和工艺性的确定。
模具设计包括浇注系统、冷却系统及动、定个部分的结构的设计。
在近四个月的设计中,为了更好地完成任务,多次去图书管查阅资料,上网了解塑料模具的特点及发展形式,
感谢老师对我们的关怀和指导,感谢同学们的帮助。
我这次设计的完成得益于老师的悉心指导和与同学们的交流。
由于本人水平有限,缺乏实践经验,所以在设计中难免产生不足和错误,请各位老师指正。
摘要
本毕业设计分为两个部分,第一部分为榨汁机的结构设计;第二部分是榨汁机的模具设计。
进行结构设计要考虑塑件的形状、功能和美观性要求。
对塑件上的孔、凸台等进行尺寸计算,根据计算结果对上盖和下盖上的各个部分尺寸和形状进行布置。
使设计的结构能满足使用要求。
模具设计部分对象结构比较复杂。
应用Pro/ENGINEER2001和AUTOCAD2000进行设计,大大提高了设计的质量和效率。
本设计结合了结构设计和模具设计,在进行结构设计的时候要考虑模具设计的可能性,每一部分都不能单独进行。
关键词:
结构设计;模具设计;注塑模;Pro/E。
ABSTRACT
Thisgraduationdesigncontainstwosections,thefirstsectionisconfigurationdesignofinstillationinstrumentwireless-controlmainframeandthesecondisaboutthemolddesignoftheinstillationinstrumentwireless-controlmainframe’sbottomcover.Whenmakingdesignfortheinstillationinstrumentwireless-controlmainframe,weshouldthinkovertheshape、thefunctionandtheartisticoftheplasticparts.calculatethesizesofthoseholesandflanges.Onthebasisoftheresultwecanlayouteverypartsoftheuppercoverandbottomcoveringoodsizeandshape.Whichwillfulfilqualityrequirements.Thepartofmolddesignisjustfortheinstillationinstrumentwireless-controlmainframe’sbottomcoverandincludespin-pointgate,lateralcore-pullingandtheconstructionisverycomplex.UsingPRO/ENGINEER2001andAutoCAD2000canimprovethequantityandefficiencyofmolddesign.Thedesigncombinedtheconfigurationdesignandmolddesign.Viewinwhole,whenmakingconfigurationdesignweshouldtakethemolddesigninourmind.Nooneofthemcanbeignored.
Keywords:
configurationdesign;molddesign;injectionmold;Pro/E.
不要删除行尾的分节符,此行不会被打印
第1章文献综述
1.1模具及其在材料加工工业中的重要地位
人类在劳动中学会了制造工具和使用工具,人们正是利用工具创造了巨大的精神文明和物质文明,生产工具三发展和不断改进代表着人类社会的进步,而模具是人类社会发展到一定程度所产生的一种先进的生产工具,人们用它制造了成千上万种生活用品和生产用品。
在近代工业中模具工业以成为工业发展的基础。
国民经济中一些重大的工业部门,如机械、电子、冶金、交通、建筑、轻工、食品等行业都大量地使用着各种各样的模具,它已成为这些工业发展的支柱和脊梁。
例如一部汽车,其构成零件的90%以上都是通过模具来成型的。
95%以上的塑料制品也是通过模具来成型的。
在今天,绝大多数新产品的开发和、生产、升级换代首当其冲的就是模具的开发、更新、换代。
因此,在近代工业中模具工业已成为工业发展的基础。
模具工业已纳入国家基础工业的范畴。
应该看到,并不时所有的模具都是最先进的,模具有不同的档次和高低不等的水平,又原始的低水平的模具,也有高效率、自动化、用计算机进行操作控制的模具。
模具水平的高低影响着生产效率的高低,同时还直接决定了所生产制品质量水平的高低。
一个国家模具总体水平三优劣也反映了一个国家工业化水平的高低。
用模具成型制品与采用机床分布加工生产制品的方法相比具有以下优点。
(1)生产效率高。
于采用多台机床多个工序的机械加工相比生产同一个制品采用模具能一次成型,生产效率可以三机械加工效率的几倍、几十倍或上百倍。
因此它特别适合也大批量、高速度地生产各种制品。
(2)用模具成型的制品质量高。
这是因为用模具成型制品三一致性好,即在精密的成型条件下,制品的尺寸精度和形位精度都比较高,互换性良好,另一方面在一定条件下用模具哟用成型真皮的物理力学性能比机械加工的更好,例如玻璃纤维增强塑料制品如采用机械加工的方法成型,玻璃纤维会被切断,而且大量得暴露的制品的表面,不但外观难看,而且影响使用性能,而且模具通过注射或压制成型的增强塑料制品,制品表面光滑,不但外观好,性能也好。
(3)用模具成型制品原料材料的利用率高。
用机械加工的方法,毛坯的40%或更多都回在加工中成为废屑,废屑即使回收再加工,也只能降低使用,或者只能放弃。
采用模具成型是少废料、少无切削的方法,可大大节约原材料,节省能源。
(4)正是由于上述原因,用模具成型的制品比用别的方法获得的制品成本低,经济效益好。
由于生产效率高,可大大节省机时费,由于废料少可节省材料费。
(5)用模具成型操作简便。
由于制品的形状,尺寸、公差都是通过模具和成型机械老保证的,无须人为控制,因此生产操作简便,生产工人不需要都
是很高文化程度和操作技术水平
综上所述,模具已成为当代工业生产中的重要手段,特别适用于各类产品的制造和生产,传统的用机械加工等方法自由成型的零件,很多都逐渐改成了永模具成型,如自由锻改成了模锻、切削成型零件改成了压铸成型零件等,可以认为模具成型是成型是成型工业发展的一个方向。
模具可以按成型材料种类的不同而分为不同的种类,如金属成型模具(最常见有冲压模、锻压模、铸造模、压铸模)、陶瓷成型模具、玻璃成型模具、塑料成型模具等。
模具在世界各国国民经济中扮演着十分重要的角色,美、日等先进工业国家近十年来模具生产和出口的增长率都超过其机床生产和出口的增长率。
实际上无论是机械产品、家用电器、汽车、飞机、轻工产品的质量都在相当程度上依赖模具工业,没有高水平的模具工业就没有高水平的机电工业,产品的革新首先是模具的革新,产品水平的高低在很大程度上取决于其成型摸具水平的高低。
世界各国分别制定了扶植摸具工业的政策。
1989年中国国务院颁布了当前产业政策要点的决定,把摸具工业列为机电工业中技术改造序列的第一位,生产基本建设序列的第二位(第一位是大型发输电设备),这就确定了摸具工业在我国国民经济中的重要地位。
这说明政府部门非常重视我国摸具工业的振兴和发展。
1.2国内外塑料摸具技术现状及发展趋势
塑料制品的质量和生产效率与塑料摸具的技术水平关系十分密切。
摸具的结构、型腔的精度、表面粗糙度、分型面位置、脱模方式对塑件的尺寸精度、形位精度、外观质量影响很大。
摸具的温度控制、充模速度、浇口位置、排气槽大小对塑件内分子取向、结晶形态等凝聚态结构以及由它们决定的力学性能、残余应力水平、光学、电学性能以及气泡、凹陷、烧焦、冷疤、银纹等各种制品缺陷有重要的关系。
摸具的脱摸机构和抽芯机构的驱动方式、动作繁简、运动速度、冷却快慢对成型效率有决定性的影响。
从摸具制造的角度出发,要求模具零件经久耐用,它的加工工艺性能好,选材合理,制造容易,造价低廉。
由于模具的制造费用十分昂贵它的成本对产品的价格影响很大。
综上所述可以看出,对于一副模具的要求是多方面的,在各种产品的制造行业,人们对上述各个方面都进行了深入的研究,使模具的产量和水平发展十分的迅速,高效率、自动化、大型、精密、长寿命模具在模具总产量中所占比例不短增大。
从模具设计和制造两方面来看,模具发展趋势可归纳为以下几个方面。
(1)高速、高效自动化模具现在的塑料成型模具基本上都能实现自动脱出产品、自动脱出浇注系统、自动坠落,大型制品或不能自动坠落的制品则采用机械手或机器人取出制品,对有侧型芯或带螺纹的制品多采用自动抽侧型芯或自动旋出螺纹型芯的结构。
采用热流道模具的结构由于不需要脱出浇注系统使模具更容易实现全自动操作,为了缩短成型周期,注射模具采用各种高效冷却结构,典型的有热管冷却、逻辑密封冷却等,必须强调的是高效自动化的模具必须配合以高速运动全自动操作的成型设备,同时采用先进合理的工艺条件,才能稳定的提高产品质量,提高生产效率,降低生产成本。
(2)高精密注射模具能否生产出高精密的塑件取决于模具、机器、原料、工艺、环境五大因素影响,只有当成型机械精度高、工艺稳定、环境不变,原料收缩率小,特别是模具精度高时,才能生产出高精度的塑件。
普通塑件的精度很难达到金属切屑零件的TI8或TI7级精度要求,特别是大型制件,但在某些特殊的使用场合有必须采用精密塑件,这时就不得不采用精密注射成型模具。
(3)大型塑件模具随着塑件制品应用的日益扩大,在建筑、机械、汽车、仪器、仪表、家用电器上采用了许多大型塑件制品,如汽车保险杠,洗衣机桶,大周转箱,甚至汽车车体,这就相应的需要大型模具,特别是大型注塑模具。
大型注塑模具物料流程长,弹性变形大,自重大,目前最重以达60吨,因此它是设计、安装、使用都有特殊之处。
例如高压下型腔壁的弹性变形很容易超差,应进行仔细的校核计算。
(4)计算机技术于模具技术的完美结合模具计算机辅助设计、辅助工程是20世纪70年代迅速发展起来的,到80年代已进入实用化。
不同软件可分别用于挤塑、注塑、压制、压铸、中空等模具的设计和对模具结构产品质量进行分析。
它由计算机硬件和专用软件组成。
CAD软件的主要功能是几何造型技术,采用Pro/E、UG等软件将制品图形立体地、精确的显示了屏幕上,完成制件设计的绘图工作,对制品或模具进行力学分析,而过程软件中充模流动软件可模拟熔体在模体的流动和熔接痕形成大等过程,冷却分析软件可模拟熔体冷却凝固过程和在模内温度的变化,使温度分布尽可能均匀,并提高冷却效率。
计算机能大量储存和方便地查找各种设计数据和标准件的图形,并能绘制出模具的零件图和装配图,使设计质量提高,设计速度加快许多倍
(3)模具制造新工艺的进展塑料模具制造中最困难的部分莫过于型腔特别是异形复杂型腔的切屑加工。
按传统方式进行机械加工费时费工,且难以保证质量。
为缩短制模周期,提高模具精度,减少钳工等手工操作工作量,采用各种坐标机床、仿形机床,光控机床和数控机床等。
特别是尽年来发展起来的计算机辅制造使模具制造技术取得了突破性的发展,它采用计算机程序来控制数字机床的刀具和工件运动轨迹和加工程序,来完成模具型腔的加工过程。
数控机床有加工中心、数控铣床、数控车床等。
采用注射模CAM后,模具的质量大大的提高,而且成本降低了10%~30%加工周期缩短了20%~50%。
电加工技术的进步给塑料模具型腔加工带来了巨大方便,特别是对高硬度]、高强度的制造的型腔可在淬火后直接加工,最常见的电加工技术有电火花、线切割、电强化、电抛光等。
用计算机程序控制电火化加工是一项正在发展的高效率、高精度型腔加工的新技术,估计它将取代很大一部分型腔的继续切屑加工的工作量。
将模具的计算机辅助设计、辅助工程和辅助制造连成一体的设计和制造系统是在模具型腔结构和尺寸经CAE软件优化后,将用CAD系统建造的型腔几何模型直接生成型腔加工的数控程序单,并指挥相关机床完成型腔的数控加工。
采用CAD/CAMCAE技术可以使模具型腔达到±0。
0001%的重复和±0.002%的准确性。
(6)简易制模工艺的研究为了及时的更新产品的花色品种,降低成本和适应小批量产品的要求,开展了简易制模工艺的研究。
其所用的材料有木材、石膏、陶瓷、塑料等非金属,也有铸钢、铜金属、铝合金、易熔合金。
制模方法有浇铸、喷涂交联固化等。
例如采用锌合金浇铸制模,以铝粉、细钢丝等填充增强的环氧树脂制模,聚氨酯弹性体制模,这些模具虽然精度较差,寿命不长,但制模周期短,成本低,有一定的适用范围。
(7)目击标准化目前发达国家模具标准化程度达到模具加工工作量的30%以上,并有完善的标准系列,包括零件标准和模架标准,国标标准化组织已制定了国标模具系列标准,标准件品种多,规格全,质量高,而且均以商品化。
近年来我过模具标准化工作有了很大进展,基本上配齐了各种主要模具类别的零件标准。
在塑料模具方面有塑料注塑模零件标准、塑料注塑模零件技术条件、塑料注塑模模架标准、塑料注塑模技术条件等,其中零件标准包括模板、垫块、推杆、导柱、导套等十余种零件,现以有不少专业厂成套生产标准模架,成批生产各种标准模具零件,并作为商品出售。
对于顶杆、导柱等常用模具的标准零件已深入人心,由于采用它即节省时间、金钱、又提高了质量,目前厂家非常乐于采用,而大小模具的标准模架人们已习惯向有关厂家订购,然后再进行型腔、型芯等的加工。
模具标准化为塑料模具设计和制造都带来了极大的方便,由于标准件可直接购买,因此模具设计制造者只需精心设计和加工型腔,这使得塑料模具的设计和制造周期大为缩短,成本降低,质量得到保证,当前我国模具标准化程度还不高,尚需大力推广,充实完善,扩大模具标准件新系列。
(8)特种塑料成型模具的研制例如随着成型工艺不断发展而出现的气体辅助注塑成型模具、低发泡制品注塑模具、反应注塑成型模具、多层多腔注塑模具、多色注塑模具以及低发泡挤出机头、多层复合机头等。
此外在模具制造上采用特殊的模具专用钢材,采用特殊的表面处理技术如离子注入、物理沉积、喷镀、刷镀等提高模具的使用寿命,表面花纹加工新技术可提高塑件外观质量等。
1.3塑件的结构设计
1.3.1功能结构设计
塑件设计的核心问题,是要保证其使用功能要求。
在充分分析塑件使用功能的基础上确定塑件的整体结构、各组成部分几何形状、尺寸、材质和外观要求及强度等。
塑件的结构,应在满足其功能要求的前提下,力求简单、明快、可靠。
因为简单的塑件结构容易满足其功能要求,达到经济、适用、安全的目的。
在设计塑件时,应当了解它是单独使用,还是与其它零件组合起来使用,在使用过程中它的主要功能和辅助功能是什么。
如果它是与其它零件组合起来使用,那么它的哪些部分、结构形状、尺寸受其它零件制约、不可变动,哪些部分可通过直观判断、试验后加以修正。
塑件各部分的强度可以通过选材、合理地分配材料、必要的强度和刚度计算、模拟或实用实验等方法予以确认。
根据使用要求不同,在设计某些塑件时还要计算容积、重量、伸长,决定某些几何参数,有的塑件要采用金属嵌件,如齿轮、轴承一类塑件。
为了提高刚度,例如对于玻璃纤维增强的塑件,应尽量不设计成平面而设计成曲面,恰当地利用筋、皱折、凸起部、夹层结构和有方向性的玻璃纤维基材。
为了保证更好地发挥塑件的功能作用,例如在设计仪表壳体、仪表板件等时,要考虑到在其上要安装与运转操作、情报传达、安全警报、娱乐快适应等有关的各种零件,因此在设计板面零件布局时要考虑操作者的视认性、操作性和安全性等。
1.3.2工艺结构设计
再塑件功能结构设计的基础上,为实现加工制造的可能性和简捷性,必须进行工艺结构设计。
因此,在设计塑件时,要选择合适的材料,以保证在使用过程中的可靠性及加工过程中的可行性,用以确定成型方法及成型工艺对塑件提出的工艺结构要求。
塑件工艺结构设计的主要内容如下:
塑件内外侧壁应有恰当的脱模斜度,内外表面结合处,即角隅处,加强筋端部和根部等以及所有能允许设计圆角的地方均应设计成圆角。
塑件壁厚要均匀,加强筋、凸台、支撑面、边缘、底部形状的设计要保证其强度,利于其成型和脱模。
金属嵌件要满足塑件使用功能要求,与塑件连接牢固性要求,成型时便与在模具中装固,成型后容易从模具中脱出。
塑件表面的花纹、图案、文字、符号等的设计要考虑成型与脱模、使用中的损伤、模具加工等问题。
此外处于塑件外形轮廓最大部分得分型线痕迹,不影响其工作特性及表观质量。
因此在塑件工艺结构设计时,要充分了解其在使用中的机能,又要熟悉材料的性能特点,成型工艺过程及特点。
只有正确的工艺结构设计,才能保证塑件顺利成型、脱模,确保塑件质量,避免塑件在成型中出现裂纹、凹陷、气孔、银纹、疏松、污斑等一系列成型缺陷,增强塑件的使用中的可靠性及持久性。
除以上所述外,还应对塑件的焊接、铆接、电镀、涂装、印刷、压花、机械加工等后续工序加以考虑,并在塑件结构设计上采取相应的措施,借以保证这些加工的顺利进行,并确保加工质量。
1.3.3造型结构设计
工业制品的结构设计,是一门技术与艺术相结合的多元交叉科学。
塑件制品种类繁多,有像光盘、磁带、薄膜、人造革、电影胶片、编织带、地毯、地板等一类平面状制品;有像餐具、玩具、家用电器、仪表等立体状制品,还有塑料花、仿大理石、仿玉石制品,仿生制品等艺术品。
对于这些制品,都要通过外部造型设计加以装饰美化。
因为人们通常都是在满足功能要求下,总是喜欢购置外形美观的制品。
塑件造型设计系指按照美的法则,如对比与调合、概括与简单、对称与平衡,安定与轻巧、尺寸与比例、主从、比拟、联想等对塑件外观形状、图案、色彩及其相互的结合进行设计,通过视觉给人以美的感觉。
对于单独使用的塑件或壳体制品,一定要认真的进行造型设计,以满足其使用机能要求,是现代制品设计的根本目的,满足人的心理需要是制品使用功能设计的根本依据。
“实用、经济、美观”是制品造型设计的基本原则。
在造型设计中还要体现环境、时代的要求,正确地使用水平线、垂直线、弧线等所形成的几何构型、比例尺度、起伏、棱角、机理、色彩等,使人们在使用塑件时有一种美的享受,同时又能保证使用者在使用它时感到方便、安全、可靠、舒适。
1.3.4塑件尺寸、精度及表面粗糙度
1.尺寸塑件尺寸的大小取决于塑件的流动性.流动性差,塑件不可过大,以免不能充满型腔或形成熔接痕,影响塑件外观和强度,此外成型设备,模具尺寸及脱模距离等也会影响塑件的大小。
2.精度影响塑件精度的因素很多,除与模具制造精度和模具磨损有关外,还与塑料收缩率的波动、成型时工艺条件有关,所以素件的尺寸精度一般不高。
3.壁厚塑件的壁厚主要取决于塑件的使用要求,但壁厚的大小对塑件的成型影响很大。
壁厚过小,成型时流动阻力大,难以充型;壁厚过大则浪费材料,还易产生气泡,缩孔等缺陷,因此必须合理选择塑性壁厚。
同一塑件壁厚应尽可能一致,否则会因冷却或固化速度不均而产生内应力,影响塑件的使用。
4.孔的设计a.通孔:
通孔设计时深度不能太大,压缩成形时应注意,通孔深度应不超过孔径的3.75倍。
b.盲孔:
盲孔只能用一端固定的型芯来成形,因此其深度浅于通孔。
注射成形或压注成形时,孔深不超过孔径的4倍。
压缩成形时,平行于压制方向的孔深一般不超过直径的2.5倍,垂直于压制方向的孔深不超过直径的2倍。
直径小于1.5mm的孔或深度太大(大于以上值)的孔最好采用成形后机械加工的方法获得。
c.异形孔:
当塑件为异形孔(斜孔或复杂形孔)时,常常采用拼合的方法成形,这样可以避免侧向抽芯。
1.4Pro/ENGINEER软件的集成制造技术
模具CAD/CAE/CAM系统的集成关键是建立单一的图形数据库、在CAD、CAE、CAM,各单元之间实现数据的自动传递与转换,使CAM、CAE阶段完全吸收CAD阶段的三维图形,减少中间建模的时间和误差;借助计算机对模具性能、模具结构、加工精度、金属液体在模具中的流动情况及模具工作过程中的温度分布情况等进行反复修改和优化,将问题发现于正式生产前,大大缩短制模具时间,提高模具加工精度。
Pro/ENGINEER软件采用面向对象的统一数据库和参数化造型技术,具备概念设计、基础设计和详细设计的功能,为模具的集成制造提供了优良的平台。
Pro/ENGINEER的并行工程技术在模具中应用
模具是面向定单式的生产方式,属于单性生产,制造过程复杂,要求交货时间短。
如果利用CAD、CAM单元技术制造模具,制造精度低、周期长,为了解决上述难题,我们将并行工程技术引入到模具制造过程中。
所谓并行工程是设计工程师在进行产品三维零件设计时就考虑模具的成型工艺、影响模具寿命的因素,并进行校对、检查,预先发现设计过程的错误。
在初步确立产品的三维模型后,设计、制造及辅助分析部门的多位工程师同时进行模具结构设计、工程详图设计、模具性能辅助分析及数控机床加工指令的编程,而且每一个工程师对产品所做的修改可自动反映到其他工程师那里,大大缩短设计、数控编程的时间。
在实际生产过程中,应用Pro/ENGINEER软件,将原来模具结构设计→模具型腔、型芯二维设计→工艺准备→模具型腔、型芯设计三维造型→数控加工指令编程→数控加工的串行工艺路线改为由不同的工程师同时进行设计、工艺准备的并行路线,不但提高了模具的制造精度,而且能缩短设计、数控编程时间达40%以上。
要实施并行工程关键要实现零件三维图形数据共享,使每个工程师使用的图形数据是绝对相同,并使每个工程师所做的修改自动反映到其他有关的工程师那里,保证数据的唯一性和可靠性。
Pro/ENGINEER软件具有的单一数据库、参数化实体特征造型技术为实现并行工程提供了可靠的技术保证。
第2章榨汁机的结构设计
2.1塑件材料的选择
塑料的选择主要考虑材料成型后的强度以及注塑过程中塑料的流动性。
pvc在工业上应用很广泛,工业上很多塑料结构件都使用ABS,如鼠标、显示器、仪表盘等外壳都使用ABS,ABS能满足强度要求,并且注塑性能也相当好。
所以榨汁机可以选用ABS。
2.2pvc的性能和成型特点
PVC=Polyvinylchloridepolymer,中文称作聚氯乙烯。
聚氯乙烯的最大特点是阻燃,因此被广泛用于防火应用。
但是聚氯乙烯在燃烧过程中会释放出氯化氢和其他有毒气体,例如二恶英。
它稳定;不易被酸、碱腐蚀;对热比较耐受。
正是由于其防火耐热作用,聚氯乙烯被广泛用于电线外皮和光纤外皮。
此外也常被制成手套、某些食物的保鲜纸。
聚氯乙稀具有原料丰富(石油、石灰石、焦炭、食盐和天然气)、制造工艺成熟、价格低廉、