复合材料成型工艺.docx
《复合材料成型工艺.docx》由会员分享,可在线阅读,更多相关《复合材料成型工艺.docx(15页珍藏版)》请在冰豆网上搜索。
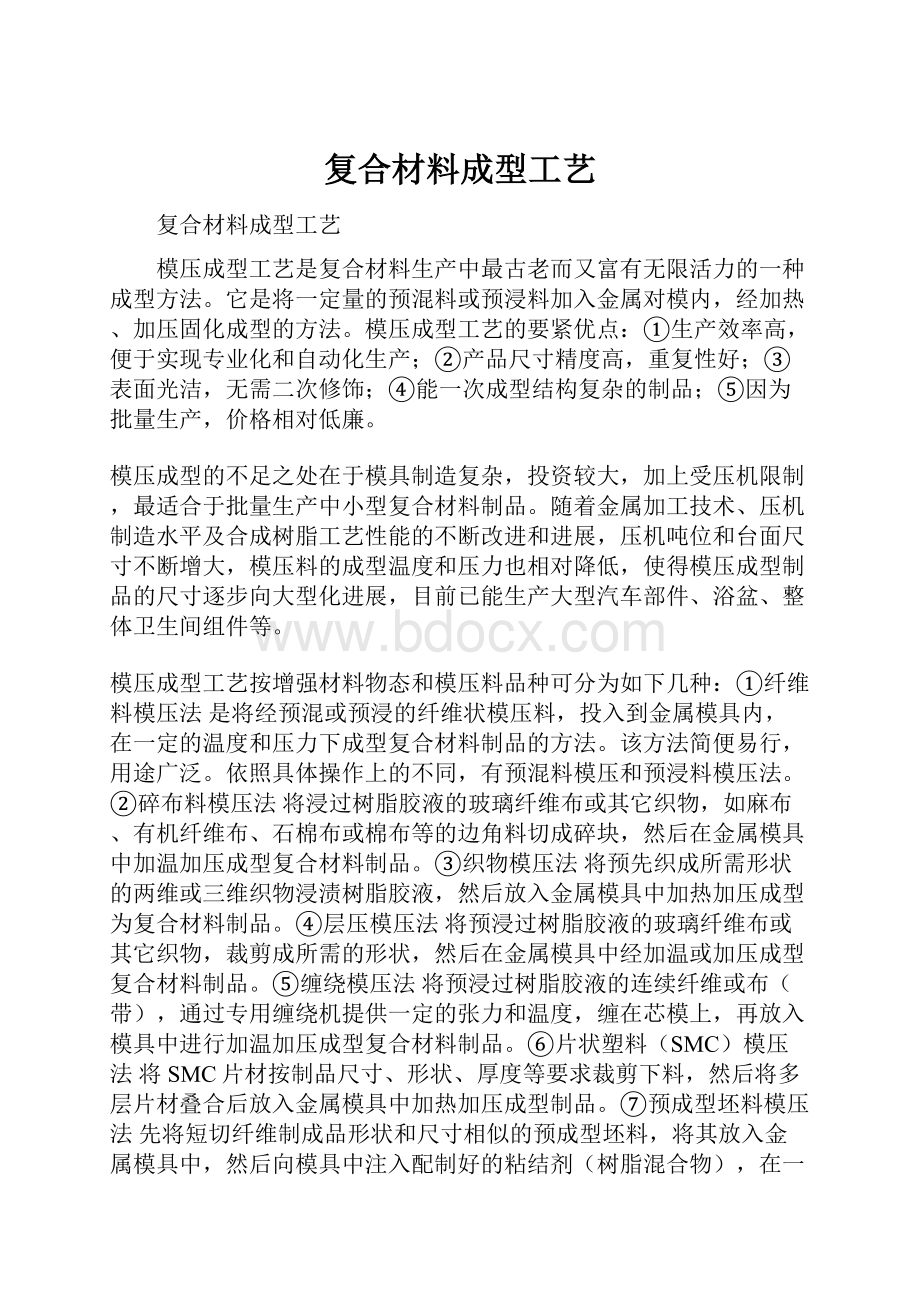
复合材料成型工艺
复合材料成型工艺
模压成型工艺是复合材料生产中最古老而又富有无限活力的一种成型方法。
它是将一定量的预混料或预浸料加入金属对模内,经加热、加压固化成型的方法。
模压成型工艺的要紧优点:
①生产效率高,便于实现专业化和自动化生产;②产品尺寸精度高,重复性好;③表面光洁,无需二次修饰;④能一次成型结构复杂的制品;⑤因为批量生产,价格相对低廉。
模压成型的不足之处在于模具制造复杂,投资较大,加上受压机限制,最适合于批量生产中小型复合材料制品。
随着金属加工技术、压机制造水平及合成树脂工艺性能的不断改进和进展,压机吨位和台面尺寸不断增大,模压料的成型温度和压力也相对降低,使得模压成型制品的尺寸逐步向大型化进展,目前已能生产大型汽车部件、浴盆、整体卫生间组件等。
模压成型工艺按增强材料物态和模压料品种可分为如下几种:
①纤维料模压法是将经预混或预浸的纤维状模压料,投入到金属模具内,在一定的温度和压力下成型复合材料制品的方法。
该方法简便易行,用途广泛。
依照具体操作上的不同,有预混料模压和预浸料模压法。
②碎布料模压法将浸过树脂胶液的玻璃纤维布或其它织物,如麻布、有机纤维布、石棉布或棉布等的边角料切成碎块,然后在金属模具中加温加压成型复合材料制品。
③织物模压法将预先织成所需形状的两维或三维织物浸渍树脂胶液,然后放入金属模具中加热加压成型为复合材料制品。
④层压模压法将预浸过树脂胶液的玻璃纤维布或其它织物,裁剪成所需的形状,然后在金属模具中经加温或加压成型复合材料制品。
⑤缠绕模压法将预浸过树脂胶液的连续纤维或布(带),通过专用缠绕机提供一定的张力和温度,缠在芯模上,再放入模具中进行加温加压成型复合材料制品。
⑥片状塑料(SMC)模压法将SMC片材按制品尺寸、形状、厚度等要求裁剪下料,然后将多层片材叠合后放入金属模具中加热加压成型制品。
⑦预成型坯料模压法先将短切纤维制成品形状和尺寸相似的预成型坯料,将其放入金属模具中,然后向模具中注入配制好的粘结剂(树脂混合物),在一定的温度和压力下成型。
模压料的品种有专门多,能够是预浸物料、预混物料,也能够是坯料。
当前所用的模压料品种要紧有:
预浸胶布、纤维预混料、BMC、DMC、HMC、SMC、XMC、TMC及ZMC等品种。
1、原材料
(1)合成树脂复合材料模压制品所用的模压料要求合成树脂具有:
①对增强材料有良好的浸润性能,以便在合成树脂和增强材料界面上形成良好的粘结;②有适当的粘度和良好的流淌性,在压制条件下能够和增强材料一道平均地充满整个模腔;③在压制条件下具有适宜的固化速度,同时固化过程中不产生副产物或副产物少,体积收缩率小;④能够满足模压制品特定的性能要求。
按以上的选材要求,常用的合成树脂有:
不饱和聚酯树脂、环氧树脂、酚醛树脂、乙烯基树脂、呋喃树脂、有机硅树脂、聚丁二烯树脂、烯丙基酯、三聚氰胺树脂、聚酰亚胺树脂等。
为使模压制品达到特定的性能指标,在选定树脂品种和牌号后,还应选择相应的辅助材料、填料和颜料。
(2)增强材料模压料中常用的增强材料要紧有玻璃纤维开刀丝、无捻粗纱、有捻粗纱、连续玻璃纤维束、玻璃纤维布、玻璃纤维毡等,也有少量特种制品选用石棉毡、石棉织物(布)和石棉纸以及高硅氧纤维、碳纤维、有机纤维(如芳纶纤维、尼龙纤维等)和天然纤维(如亚麻布、棉布、煮炼布、不煮炼布等)等品种。
有时也采纳两种或两种以上纤维混杂料作增强材料。
(3)辅助材料一样包括固化剂(引发剂)、促进剂、稀释剂、表面处理剂、低收缩添加剂、脱模剂、着色剂(颜料)和填料等辅助材料。
2、模压料的制备
以玻璃纤维(或玻璃布)浸渍树脂制成的模压料为例,其生产工艺可分为预混法和预浸法两种。
(1)预混法先将玻璃纤维切割成30~50mm的短切纤维,经蓬松后在捏合机中与树脂胶液充分捏合至树脂完全浸润玻璃纤维,再经烘干(晾干)至适当粘度即可。
其特点是纤维松散无定向,生产量大,用此法生产的模压料比容大,流淌性好,但在制备过程中纤维强度缺失较大。
(2)预浸法纤维预浸法是将整束连续玻璃纤维(或布)通过浸胶、烘干、切短而成。
其特点是纤维成束状,比较紧密,制备模压料的过程中纤维强度缺失较小,但模压料的流淌性及料束之间的相容性稍差。
树脂基复合材料成型工艺介绍
(2):
层压及卷管成型工艺
1、层压成型工艺
层压成型是将预浸胶布按照产品形状和尺寸进行剪裁、叠加后,放入两个抛光的金属模具之间,加温加压成型复合材料制品的生产工艺。
它是复合材料成型工艺中进展较早、也较成熟的一种成型方法。
该工艺要紧用于生产电绝缘板和印刷电路板材。
现在,印刷电路板材已广泛应用于各类收音机、电视机、机和移动机、电脑产品、各类操纵电路等所有需要平面集成电路的产品中。
层压工艺要紧用于生产各种规格的复合材料板材,具有机械化、自动化程度高、产品质量稳固等特点,但一次性投资较大,适用于批量生产,同时只能生产板材,且规格受到设备的限制。
层压工艺过程大致包括:
预浸胶布制备、胶布裁剪叠合、热压、冷却、脱模、加工、后处理等工序,如图所示:
2、卷管成型工艺
卷管成型工是用预浸胶布在卷管机上热卷成型的一种复合材料制品成型方法,其原理是借助卷管机上的热辊,将胶布软化,使胶布上的树脂熔融。
在一定的张力作用下,辊筒在运转过程中,借助辊筒与芯模之间的摩擦力,将胶布连续卷到芯管上,直到要求的厚度,然后经冷辊冷却定型,从卷管机上取下,送入固化炉中固化。
管材固化后,脱去芯模,即得复合材料卷管。
卷管成型按其上布方法的不同而可分为手工上布法和连续机械法两种。
其差不多过程是:
第一清理各辊筒,然后将热辊加热到设定温度,调整好胶布张力。
在压辊不施加压力的情形下,将引头布先在涂有脱模剂的管芯模上缠上约1圈,然后放下压辊,将引头布贴在热辊上,同时将胶布拉上,盖贴在引头布的加热部分,与引头布相搭接。
引头布的长度约为800~1200mm,视管径而定,引头布与胶布的搭接长度,一样为150~250mm。
在卷制厚壁管材时,可在卷制正常运行后,将芯模的旋转速度适当加快,在接近设计壁厚时再减慢转速,至达到设计厚度时,切断胶布。
然后在保持压辊压力的情形下,连续使芯模旋转1~2圈。
最后提升压辊,测量管坯外径,合格后,从卷管机上取出,送入固化炉中固化成型。
3、预浸胶布制备工艺
预浸胶布是生产复合材料层压板材、卷管和布带缠绕制品的半成品。
(1)原材料预浸胶布生产所需的要紧原材料有增强材料(如玻璃布、石棉布、合成纤维布、玻璃纤维毡、石棉毡、碳纤维、芳纶纤维、石棉纸、牛皮等)和合成树脂(如酚醛树脂、氨基树脂、环氧树脂、不饱和聚酯树脂、有机硅树脂等)。
(2)预浸胶布的制备工艺预浸胶布的制备是使用经热处理或化学处理的玻璃布,经浸胶槽浸渍树脂胶液,通过刮胶装置和牵引装置操纵胶布的树脂含量,在一定的温度下,通过一定时刻的洪烤,使树脂由A阶转至B阶,从而得到所需的预浸胶布。
通常将此过程称之为玻璃的浸胶。
树脂基复合材料成型工艺介绍(3):
缠绕成型工艺
缠绕成型工艺是将浸过树脂胶液的连续纤维(或布带、预浸纱)按照一定规律缠绕到芯模上,然后经固化、脱模,获得制品。
依照纤维缠绕成型时树脂基体的物理化学状态不同,分为干法缠绕、湿法缠绕和半干法缠绕三种。
(1)干法缠绕干法缠绕是采纳通过预浸胶处理的预浸纱或带,在缠绕机上经加热软化至粘流态后缠绕到芯模上。
由于预浸纱(或带)是专业生产,能严格操纵树脂含量(精确到2%以内)和预浸纱质量。
因此,干法缠绕能够准确地操纵产品质量。
干法缠绕工艺的最大特点是生产效率高,缠绕速度可达100~200m/min,缠绕机清洁,劳动卫生条件好,产品质量高。
其缺点是缠绕设备贵,需要增加预浸纱制造设备,故投资较大此外,干法缠绕制品的层间剪切强度较低。
(2)湿法缠绕湿法缠绕是将纤维集束(纱式带)浸胶后,在张力操纵下直截了当缠绕到芯模上。
湿法缠绕的优点为:
①成本比干法缠绕低40%;②产品气密性好,因为缠绕张力使余外的树脂胶液将气泡挤出,并填满间隙;③纤维排列平行度好;④湿法缠绕时,纤维上的树脂胶液,可减少纤维磨损;⑤生产效率高(达200m/min)。
湿法缠绕的缺点为:
①树脂白费大,操作环境差;②含胶量及成品质量不易操纵;③可供湿法缠绕的树脂品种较少。
(3)半干法缠绕半干法缠绕是纤维浸胶后,到缠绕至芯模的途中,增加一套烘干设备,将浸胶纱中的溶剂除去,与干法相比,省却了预浸胶工序和设备;与湿法相比,可使制品中的气泡含量降低。
三种缠绕方法中,以湿法缠绕应用最为普遍;干法缠绕仅用于高性能、高精度的尖端技术领域。
纤维缠绕成型的优点①能够按产品的受力状况设计缠绕规律,使能充分发挥纤维的强度;②比强度高:
一样来讲,纤维缠绕压力容器与同体积、同压力的钢质容器相比,重量可减轻40~60%;③可靠性高:
纤维缠绕制品易实现机械化和自动化生产,工艺条件确定后,缠出来的产品质量稳固,精确;④生产效率高:
采纳机械化或自动化生产,需要操作工人少,缠绕速度快(240m/min),故劳动生产率高;⑤成本低:
在同一产品上,可合理配选若干种材料(包括树脂、纤维和内衬),使其再复合,达到最佳的技术经济成效。
缠绕成型的缺点①缠绕成型适应性小,不能缠任意结构形式的制品,专门是表面有凹的制品,因为缠绕时,纤维不能紧贴芯模表面而架空;②缠绕成型需要有缠绕机,芯模,固化加热炉,脱模机及熟练的技术工人,需要的投资大,技术要求高,因此,只有大批量生产时才能降低成本,才能获得较的的技术经济效益。
1、原材料
缠绕成型的原材料要紧是纤维增强材料、树脂和填料。
(1)增强材料缠绕成型用的增强材料,要紧是各种纤维纱:
如无碱玻璃纤维纱,中碱玻璃纤维纱,碳纤维纱,高强玻璃纤维纱,芳纶纤维纱及表面毡等。
(2)树脂基体树脂基体是指树脂和固化剂组成的胶液体系。
缠绕制品的耐热性,耐化学腐蚀性及耐自然老化性要紧取决于树脂性能,同时对工艺性、力学性能也有专门大阻碍。
缠绕成型常用树脂要紧是不饱和聚酯树脂,也有时用环氧树脂和双马来酰亚胺树脂等。
关于一样民用制品如管、罐等,多采纳不饱和聚酯树脂。
对力学性能的压缩强度和层间剪切强度要求高的缠绕制品,则可选用环氧树脂。
航天航空制品多采纳具有高断裂韧性与耐湿性能好的双马来酰亚胺树脂。
(3)填料填料种类专门多,加入后能改善树脂基体的某些功能,如提高耐磨性,增加阻燃性和降低收缩率等。
在胶液中加入空心玻璃微珠,可提高制品的刚性,减小密度降低成本等。
在生产大口径地埋管道时,常加入30%石英砂,借以提高产品的刚性和降低成本。
为了提高填料和树脂之间的粘接强度,填料要保证清洁和表面活性处理。
2、芯模
成型中空制品的内模称芯模。
一样情形下,缠绕制品固化后,芯模要从制品内脱出。
芯模设计的差不多要求①要有足够的强度和刚度,能够承担制品成型加工过程中施加于芯模的各种载荷,如自重、制品重,缠绕张力,固化应力,二次加工时的切削力等;②能满足制品形状和尺寸精度要求,如形状尺寸,同心度、椭圆度、锥度(脱模),表面光洁度和平坦度等;③保证产品固化后,能顺利从制品中脱出;④制造简单,造价廉价,取材方便。
芯模材料缠绕成型芯模材料分两类:
熔、溶性材料和组装式材料。
熔、溶性材料是指石蜡,水溶性聚乙烯醇型砂,低熔点金属等,这类材料可用浇铸法制成空心或实心芯模,制品缠绕成型后,从开口处通入热水或高压蒸汽,使其溶、熔,从制品中流出,流出的溶体,冷却后重复使用。
组装式芯模材料常用的有铝、钢、夹层结构、木材及石膏等。
另外还有内衬材料,内衬材料是制品的组成部分,固化后不从制品中取出,内衬材料的作用要紧是防腐和密封,因此也能够起到芯模作用,属于这类材料的有橡胶、塑料、不锈钢和铝合金等
3、缠绕机
缠绕机是实现缠绕成型工艺的要紧设备,对缠绕机的要求是:
①能够实现制品设计的缠绕规律和排纱准确;②操作简便;③生产效率高;④设备成本低。
缠绕机要紧由芯模驱动和绕丝嘴驱动两大部分组成。
为了排除绕丝嘴反向运动时纤维松线,保持张力稳固及在封头或锥形缠绕制品纱带布置精确,实现小缠绕角(0°~15°)缠绕,在缠绕机上设计有垂直芯轴方向的横向进给(伸臂)机构。
为防止绕丝嘴反向运动时纱带转拧,伸臂上设有能使绕丝嘴翻志的机构。
我国60年代研制成功链条式缠绕机,70年代引进德国WE-250数控缠绕机,改进后实现国产化生产,80年代后我国引进了各种型式缠绕机40多台,通过改进后,自己设计制造成功微机操纵缠绕机,并进入国际市场。
机械式缠绕机类型
(1)绕臂式平面缠绕机其特点是绕臂(装有绕丝嘴)围绕芯模做平均旋转运动,芯模绕自身轴线作平均慢速转动,绕臂(即绕丝嘴)每转一周,芯模转过一个小角度。
此小角度对应缠绕容器上一个纱片宽度,保证纱片在芯模上一个紧挨一个地布满容器表面。
芯模快速旋转时,绕丝嘴沿垂直地面方向缓慢地上下移动,现在可实现环向缠绕,使用这种缠绕机的优点是,芯模受力平均,机构运行平稳,排线平均,适用于干法缠绕中小型短粗筒形容器。
(2)滚翻式缠绕机这种缠绕机的芯模由两个摇支承,缠绕时芯模自身轴旋转,两臂同步旋转使芯模翻动一周,芯模自转一个与纱片宽相适应的角度,而纤维纱由固定的伸臂供给,实现平面缠绕,环向缠绕由附加装置来实现。
由于滚翻动作机构不宜过大,故此类缠绕机只适用于小型制品,且使用不广泛。
(3)卧式缠绕机这种缠绕机是由链条带动小车(绕丝嘴)作往复运动,并在封头端有瞬时停歇,芯模绕自身轴作等速旋转,调整两者速度能够实现平面缠绕、环向缠绕和螺旋缠绕,这种缠绕机构造简单,用途广泛,适宜于缠绕细长的管和容器。
(4)轨道式缠绕机轨道式缠绕机分立式和卧式两种。
纱团、胶槽和绕丝嘴均装在小车内,当小车沿环形轨道绕芯模一周时,芯模自身转动一个纱片宽度,芯模轴线和水平面的夹角为平面缠绕角α。
从而形成平面缠绕型,调整芯模和小车的速度能够实现环向缠绕和螺旋缠绕。
轨道式缠绕机适合于生产大型制品。
(5)行星式缠绕机芯轴和水平面倾斜成α角(即缠绕角)。
缠绕成型时,芯模作自转和公转两个运动,绕丝嘴固定不动。
调整芯模自转和公转速度能够完成平面缠绕、环向缠绕和螺旋缠绕。
芯模公转是主运动,自转为进给运动。
这种缠绕机适合于生产小型制品。
(6)球形缠绕机球形缠绕机有4个运动轴,球形缠绕机的绕丝嘴转动,芯模旋转和芯模偏摆,差不多上和摇臂式缠绕机相同,第四个轴运动是利用绕丝嘴步进实现纱片缠绕,减少极孔外纤维堆积,提高容器臂厚的平均性。
芯模和绕丝嘴转动,使纤维布满球体表面。
芯模轴偏转运动,能够改变缠绕极孔尺寸和调剂缠绕角,满足制品受力要求。
(7)电缆式纵环向缠绕机纵环向电缆式缠绕机适用于生产无封头的筒形容器和各种管道。
装有纵向纱团的转环与芯模同步旋转,并可沿芯模轴向往复运动,完成纵向纱铺放,环向纱装在转环两边的小车内,当芯模转动,小车沿芯模轴向作往复运动时,完成环向纱缠绕。
依照管道受力情形,能够任意调整纵环向纱数量比例。
(8)新型缠管机新型缠管机与现行缠绕机的区别在于,它是靠管芯自转,并同时能沿管长方向作往复运动,完成缠绕过程。
这种新型缠绕机的优点是,绕丝嘴固定,为工人处理断头、毛丝以及看管带来专门大方便;多路进纱可实现大容量进丝缠绕,缠绕速度快,布丝平均,有利于提高产品重量和产量。
树脂基复合材料成型工艺介绍(4):
连续成型工艺
复合材料制品的连续成型工艺,是指从投入原材料开始,通过浸胶、成型、固化、脱模、切断等工序,直到最后获得成品的整个工艺过程,差不多上在连续不断地进行。
依照生产的产品不同,连续成型工艺分为连续拉挤成型工艺、连续缠绕成型工艺和连续制板工艺三种。
连续缠绕成型工艺要紧用于生产不同口径的玻璃钢管和罐身。
连续缠绕机的特点是:
生产效率高、产品质量稳固、劳动强度低、节约原材料、减少芯模数量等,但这种工艺技术含量高、设备投资大、变径难度大。
另一种工艺是将塑料管挤出技术和纤维缠绕工艺相结合,塑料内衬玻璃钢管,挤出的塑料管同时起到芯模和防腐内衬两个作用。
拉挤成型工艺要紧用于生产各种玻璃钢型材,如玻璃钢棒、工字型、角型、槽型、方型、空腹型及异形断面型材等。
目前最大的拉挤成型机,能够生产断面为800mm×800mm的空腹玻璃钢型材。
新型拉挤成型技术不断涌现,如RIM拉挤成型机,弯曲形型材拉挤工艺等。
连续制板工艺要紧是用玻璃纤毡、布为增强材料,连续不断地生产各种规格平板,波浪板和夹层结构板等。
连续成型工艺的共同特点:
①生产过程完全实现机械化身自动化,生产效率高;②生产过程不间断,制品长度不限;③产品无需后加工,生产过程中边角废料少,节约原料和能源;④产品质量稳固,重复性好,成品率高;⑤操作方便,省人力、劳动条件好;⑥成本低
树脂基复合材料成型工艺介绍(5):
拉挤成型工艺
拉挤成型工艺是将浸渍树脂胶液的连续玻璃纤维束、带或布等,在牵引力的作用下,通过挤压模具成型、固化,连续不断地生产长度不限的玻璃钢型材。
这种工艺最适于生产各种断面形状的玻璃钢型材,如棒、管、实体型材(工字形、槽形、方形型材)和空腹型材(门窗型材、叶片等)等。
拉挤成型是复合材料成型工艺中的一种专门工艺,其优点是:
①生产过程完全实现自动化操纵,生产效率高;②拉挤成型制品中纤维含量可高达80%,浸胶在张力下进行,能充分发挥增强材料的作用,产品强度高;③制品纵、横向强度可任意调整,能够满足不同力学性能制品的使用要求;④生产过程中无边角废料,产品不需后加工,故较其它工艺省工,省原料,省能耗;⑤制品质量稳固,重复性好,长度可任意切断。
拉挤成型工艺的缺点是产品形状单调,只能生产线形型材,而且横向强度不高。
(1)拉挤工艺用原材料
①树脂基体在拉挤工艺中,应用最多的是不饱和聚酯树脂,约占本工艺树脂用量的90以上,另外还有环氧树脂、乙烯基树脂、热固性甲基丙烯酸树脂、改性酚醛树脂、阻燃性树脂等。
②增强材料拉挤工艺用的增强材料,要紧是玻璃纤维及其制品,如无捻粗纱、连续纤维毡等。
为了满足制品的专门性能要求,能够选用芳纶纤维、碳纤维及金属纤维等。
不论是哪种纤维,用于拉挤工艺时,其表面都必须通过处理,使之与树脂基体能专门好的粘接。
③辅助材料拉挤工艺的辅助材料要紧有脱模剂和填料。
(2)拉挤成型模具
模具是拉挤成型技术的重要工具,一样由预成型模和成型模两部分组成。
①预成型模具在拉挤成型过程中,增强材料浸渍树脂后(或被浸渍的同时),在进入成型模具前,必须通过由一组导纱元件组成的预成型模具,预成型模的作用是将浸胶后的增强材料,按照型材断面配置形式,逐步形成近似成型模控形状和尺寸的预成型体,然后进入成型模,如此能够保证制品断面含纱量平均。
②成型模具成型模具横截面面积与产品横截面面积之比一样应大于或等于10,以保证模具有足够的强度和刚度,加热后热量分布平均和稳固。
拉挤模具长度是依照成型过程中牵引速度和树脂凝胶固化速度决定,以保证制品拉出时达到脱模固化程度。
一样采纳钢镀铬,模腔表面要求光洁,耐磨,借以减少拉挤成型是的摩擦阻力和提高模具的使用寿命。
(3)拉挤成型工艺
拉挤成型工艺过程是由送纱、浸胶、预成型、固化定型、牵引、切断等工序组成。
无捻粗纱从纱架引出后,通过排纱器进入浸胶槽浸透树脂胶液,然后进入预成型模,将余外树脂和气泡排出,再进入成型模凝胶、固化。
固化后的制品由牵引机连续不断地从模具拔出,最后由切断机定长切断。
在成型过程中,每道工序都能够有不同方法:
如送纱工序,能够增加连续纤维毡,环向缠绕纱或用三向织物以提高制品横向强度;牵引工序能够是履带式牵引机,也能够用机械手;固化方式能够是模内固化,也能够用加热炉固化;加热方式能够是高频电加热,也能够用熔融金属(低熔点金属)等。
(4)其它拉挤成型工艺
拉挤成型工艺除立式和卧式机组外,尚有弯曲形制品拉挤成型工艺,反应注射拉挤工艺和含填料的拉挤工艺等。
树脂基复合材料成型工艺介绍(6):
其它成型工艺
聚合物基复合材料的其它成型工艺,要紧指离心成型工艺、浇铸成型工艺、弹性体贮存树脂成型工艺(ERM)、增强反应注射成型工艺(RRIM)等。
1、离心成型工艺
离心成型工艺在复合材料制品生产中,要紧是用于制造管材(地埋管),它是将树脂、玻璃纤维和填料按一定比例和方法加入到旋转的模腔内,依靠高速旋转产生的离心力,使物料挤压密实,固化成型。
离心玻璃钢管分为压力管非压力管两类,其使用压力为0~18MPa。
这种管的管径一样为φ400~φ2500mm,最大管径或达5m,以φ1200mm以上管径经济成效最佳,离心管的长度2~12m,一样为6m。
离心玻璃钢管的优点专门多,与一般玻璃钢管和混凝土管相比,它强度高、重量轻,防腐、耐磨(是石棉水泥管的5~10倍)、节能、耐久(50年以上)及综合工程造价低,专门是大口径管等;与缠绕加砂玻璃钢管相比,其最大特点是刚度大,成本低,管壁能够按其功能设计成多层结构。
离心法制管质量稳固,原材料损耗少,其综合成本低于钢管。
离心玻璃钢管可埋深15m,能随真空及外压。
其缺点是内表面不够光滑,水力学特性比较差。
离心玻璃钢管的应用前景十分宽敞,其要紧应用范畴包括:
给水及排水工程干管,油田注水管、污水管、化工防腐管等。
(1)原材料
生产离心管的原材料有树脂、玻璃纤维及填料(粉状和粒状填料)等。
树脂应用最广的是不饱和聚酯树脂,可依照使用条件和工艺要求选择树脂牌号和固化剂。
增强材料主工是玻璃纤维及其制品。
玻纤制品有连续纤维毡、网格布及单向布等,制造异形断面制品时,可先将玻纤制成预制品,然后放入模内。
填料填料的作是用增加制品的刚度、厚度、降低成本,填料的种类要依照使用要求选择,一样为石英砂、石英粉、辉绿岩粉等。
(2)工艺流程
离心制管工艺流程如下:
离心制管的加料方法与缠绕成型工艺不同,加料系统是把树脂、纤维和填料的供料装置,统一安装在可往复运动的小车内。
(3)模具
离心法生产玻璃钢管的模具,要紧是钢模,模具分整体式和拼装式两种:
小于φ800mm管的模具,用整体式,大于φ800mm管的模具,能够用拼装式。
模具设计要保证有足够的强度和刚度,防止旋转、震动过程中变形。
模具由管身、封头、托轮箍组成。
管身由钢板卷焊而成,小直径管身可用无缝钢管。
封头的作用是增加管模端头的强度和防止物料外流。
托轮箍的作用是支撑模具,传递旋转力,使模具在离心机上高速度旋转,模具的管身内表面必须平坦,光滑,一样都要精加工和抛光,保证顺利脱模。
2、浇注成型工艺
浇注成型要紧用于生产无纤维增强的复合材料制品,如人造大理石,钮扣、包埋动、植物标本、工艺品、锚杆固定剂、装饰板等。
浇注成型比较简单,但要生产出优质产品,则需要熟练的操作技术。
(1)钮扣生产工艺
用聚酯树脂浇注的钮扣,具有硬度高,光泽好,耐磨、耐烫、耐干洗、花色品种多及价格低等优点,目前在国内外已差不多取代了有机玻璃钮扣,占钮扣市场80%以上。
生产钮扣的原料要紧是不饱和聚酯树脂、固化剂(引发剂采纳过氧化甲乙酮)和辅助材料(包括色浆、珠光粉、触变剂等)。
聚酯钮扣采纳离心浇注式棒材浇注法生产,先制成板材或棒材,然后经切板、切棒制成钮扣,再经热处理、刮面、刮底、铣槽、打眼、抛光等工序制成钮扣。
(2)人造石材生产工艺
人造石材是用不饱和聚酯树脂和填料制成的。
由于所选用的填料不