第五章硅质硅酸铝质及刚玉质耐火材料讲解.docx
《第五章硅质硅酸铝质及刚玉质耐火材料讲解.docx》由会员分享,可在线阅读,更多相关《第五章硅质硅酸铝质及刚玉质耐火材料讲解.docx(72页珍藏版)》请在冰豆网上搜索。
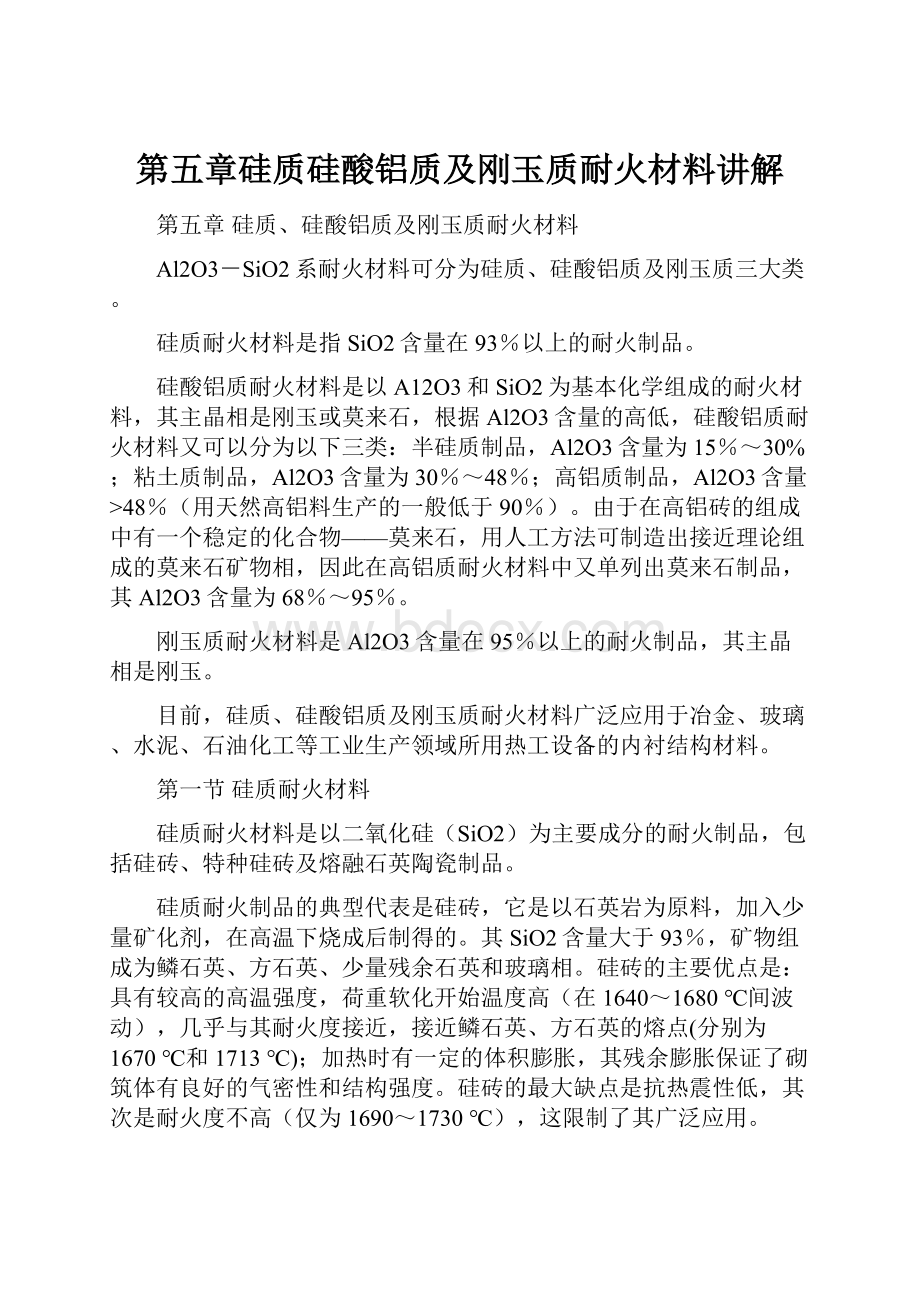
第五章硅质硅酸铝质及刚玉质耐火材料讲解
第五章硅质、硅酸铝质及刚玉质耐火材料
Al2O3-SiO2系耐火材料可分为硅质、硅酸铝质及刚玉质三大类。
硅质耐火材料是指SiO2含量在93%以上的耐火制品。
硅酸铝质耐火材料是以A12O3和SiO2为基本化学组成的耐火材料,其主晶相是刚玉或莫来石,根据Al2O3含量的高低,硅酸铝质耐火材料又可以分为以下三类:
半硅质制品,Al2O3含量为15%~30%;粘土质制品,Al2O3含量为30%~48%;高铝质制品,Al2O3含量>48%(用天然高铝料生产的一般低于90%)。
由于在高铝砖的组成中有一个稳定的化合物——莫来石,用人工方法可制造出接近理论组成的莫来石矿物相,因此在高铝质耐火材料中又单列出莫来石制品,其Al2O3含量为68%~95%。
刚玉质耐火材料是Al2O3含量在95%以上的耐火制品,其主晶相是刚玉。
目前,硅质、硅酸铝质及刚玉质耐火材料广泛应用于冶金、玻璃、水泥、石油化工等工业生产领域所用热工设备的内衬结构材料。
第一节硅质耐火材料
硅质耐火材料是以二氧化硅(SiO2)为主要成分的耐火制品,包括硅砖、特种硅砖及熔融石英陶瓷制品。
硅质耐火制品的典型代表是硅砖,它是以石英岩为原料,加入少量矿化剂,在高温下烧成后制得的。
其SiO2含量大于93%,矿物组成为鳞石英、方石英、少量残余石英和玻璃相。
硅砖的主要优点是:
具有较高的高温强度,荷重软化开始温度高(在1640~1680℃间波动),几乎与其耐火度接近,接近鳞石英、方石英的熔点(分别为1670℃和1713℃);加热时有一定的体积膨胀,其残余膨胀保证了砌筑体有良好的气密性和结构强度。
硅砖的最大缺点是抗热震性低,其次是耐火度不高(仅为1690~1730℃),这限制了其广泛应用。
硅质制品属于酸性耐火材料,对酸性炉渣抵抗力强,但受碱性渣强烈侵蚀,易被含Al2O3、K2O、Na2O等氧化物作用而破坏,对CaO、FeO、Fe2O3等氧化物有良好的抵抗能力。
目前,硅砖主要用于焦炉、玻璃熔窑、高炉热风炉以及其他热工设备。
一、硅砖生产的物理化学原理
硅石原料和硅砖的主要成分均为SiO2。
由于SiO2在不同温度下以不同的晶型存在,并在一定条件下可以互相转变,同时在晶型转变时伴随体积变化而产生应力,因此了解SiO2各种晶型的性质和它们之间的转换条件,以及矿化剂对其晶型转化的影响,对硅砖的制造、生产和使用均有重要意义。
(-)SiO2的同质多晶转变
SiO2在常压下有7个变体和1个非晶型变体,即β-石英,α-石英,γ-鳞石英,β-鳞石英,α-鳞石英,β-方石英,α-方石英,以及石英玻璃。
SiO2各种变体的性质和稳定存在温度范围见表5-1。
SiO2各晶型间的转变温度以及体积变化值见图5-1。
表5-1SiO2各种变体的性质和稳定存在温度范围
变体
晶系
真密度,g·cm-3
稳定温度范围,℃
β-石英
三方晶系
2.65
>573
α-石英
六方晶系
2.53
573~870
γ-鳞石英
斜方晶系
2.37~2.35
<117
β-鳞石英
六方晶系
2.24
117~163
α-鳞石英
六方晶系
2.23
870~1470
β-方石英
斜方晶系
2.31~2.32
<180~270
α-方石英
等轴晶系
2.23
1470~1723
石英玻璃
无定形
2.20
<1713(急冷)
从图5-1中可看出,SiO2各变体间的转变可分为两类:
第一类是高温型转变,即石英、鳞石英、方石英之间的转变。
由于它们在晶体结构和物理性质方面差别较大,因此转变所需的活化能大,转变温度高而缓慢,并伴随有较大的体积效应。
有矿化剂存在时可显著加速转变,无矿化剂时实际上不能转变。
第二类是低温型转变,即石英、鳞石英、方石英本身的α、β、γ型的转变,由于它们在结构和性质方面差别很小,因此转变温度低,转变速度快,而且转变是可逆的,所伴随的体积效应也比高温型的小。
由于SiO2各种变体的晶体结构不同,其密度不同,因此它们在转变过程中有体积效应产生。
由图5-1中给出的体积变化值可以看出,SiO2各种变体在转变时所产生的体积变化是不一样的:
快速转变时所发生的体积变化比慢速转变时所发生的体积变化小,其中鳞石英型转变时的体积变化较小,方石英型的较大。
图5-1SiO2的晶型转变及体积变化值
由于方石英的熔点是1728℃,鳞石英是1670℃,而石英是1600℃,因此,从提高制品的耐火度方面考虑,方石英是比较有利的;但从体积稳定性来看,鳞石英具有较高的体积稳定性;同时鳞石英具有矛头状双晶相互交错的网络状结构,可使硅砖具有较高的荷重软化温度及高温结构强度。
当硅砖中有残余石英存在时,由于它在使用中会继续进行晶型转变,体积膨胀较大,易引起砖体结构松散而降低制品的使用性能。
综上所述,一般希望烧成后硅砖中含大量鳞石英,方石英次之,而残余石英愈少愈好。
在硅砖生产中,石英的转变程度可用硅砖的真密度来衡量。
硅砖的密度一般应小于2.38g·cm-3,优质硅砖的密度在2.32~2.36g·cm-3之间。
另外,由于硅砖生坯在烧成升温过程中,发生α-石英→α-鳞石英→α-方石英的晶型转变,体积膨胀较大;而在冷却过程中,发生α型→β型→γ型的晶型转变,体积收缩较小,因此烧成后硅砖的体积要大于生坯的体积。
砖质制品烧成时的体积膨胀程度取决于原料性质、结构、转化程度、烧成时间和温度等多种因素。
实际上,由于制品内SiO2转化不完全,硅质制品烧成时的膨胀率在3%~4%之间。
(二)矿化剂的作用及原理
矿化剂的作用是促进石英在烧成时转变为低密度的变体(鳞石英和方石英)而不显著降低其耐火度。
它还能防止砖坯烧成时因发生急剧膨胀而产生的松散和开裂。
石英转变为鳞石英或方石英时,在矿化剂很少或几乎没有时,α-石英就形成α-方石英,这种转变称为“干转化”。
在干转化时,由于砖体的不均匀的体积膨胀很大,而又无液相缓冲应力,因而会引起制品结构松散和开裂,不可能制得良好性能的制品。
而当有足够数量矿化剂存在时,β-石英在573℃转变为α-石英,在1200~1470℃范围内,α-石英很快转变为亚稳定方石英,同时α-石英、亚稳定方石英和矿化剂及杂质等相互作用形成液相,并侵入到石英颗粒在形成亚稳定方石英时出现的裂纹中,促进α-石英和亚稳定方石英不断地溶解于所形成的液相中,使之形成硅氧过饱和溶液,然后以稳定的鳞石英形态不断地从液相中结晶出来。
这个转变速度取决于所加矿化剂的性质和数量。
同时,所形成的液相还能缓冲由于转变过程中体积膨胀所产生的应力,提高砖坯的加热体积稳定性和强度,防止焙烧过程中制品的松散和开裂现象。
在硅砖泥料中加入矿化剂,能促进石英在高温下转变成鳞石英和方石英。
但矿化剂对对制品性能也有不利的一面,即降低制品的耐火度。
因此在硅砖制造过程中,对矿化剂的选择是很重要的,要求既能促进石英在烧成时转变为鳞石英和方石英,又不能显著降低制品的耐火性能,而且比较经济和容易获得。
不同物质对石英转化程度的影响见表5-2。
表5-2不同物质对石英转化程度的影响
物质名称
真密度/g·cm-3
石英转化量/%
无矿化剂
TiO2
Al2O3
BaO或Cr2O3
CaO
MnO2
Fe2O3
FeO
Na2SiO3
Na2CO3
K2CO3
2.650
2.625
2.615
2.605
2.585
2.580
2.550
2.530
2.390
2.350
2.325
-
0
3
6
12
14
23
29
72
85
92
由表中可看出,促进石英转化最有利的物质是K2CO3、Na2CO3、Na2SiO3,其次是FeO、Fe2O3、MnO2和CaO,其他物质的矿化作用不大。
虽然K2CO3、Na2CO3和Na2SiO3能强烈地促进石英的转化,但实际生产中不采用这类物质作矿化剂。
因为它们对硅砖的耐火性能影响很大,加入少量就会显著降低耐火度;此外,这些物质干燥时会析出到砖坯表面上来,造成砖坯内部和表面矿化剂含量不同,导致内外的晶型转变不一致而造成制品开裂。
在生产中厂泛采用的矿化剂有石灰CaO,CaO对硅质原料的耐火度降低不大,并有足够的矿化作用,同时它还起到结合剂的作用,使泥料具有结合性和可塑性,从而使砖坯干燥后具有一定强度。
为了进一步提高石英的转变程度,减少砖坯烧成时的膨胀和松散,以及减少制品的裂纹,还与石灰一起加入铁鳞(FeO+Fe2O3)。
因为加入铁氧化物可以显著降低液相出现温度和粘度。
目前硅砖生产中广泛采用石灰一铁鳞作为矿化剂。
矿化剂的加入量应根据原料特性,制品的性能要求和使用条件来确定,通常加入量不应超过3%~4%。
二、硅砖的生产流程及工艺要点
(一)制造硅砖的生产流程
硅砖的生产工艺流程与其他砖种的相似,不同点在于增加了矿化剂(铁鳞粉和石灰乳)的制备系统。
制造硅砖的工艺流程如图5-2所示。
图5-2国内某厂的硅砖生产工艺流程
(二)对原料的技术要求和加工
1.对硅石原料的技术要求
(1)硅石
我国生产硅砖所用硅石主要是天然硅石。
耐火材料用硅石分为GS-98.5、GS-98、GS-97、GS-96四个牌号,其理化指标应符合本书第四章中表4-7的要求,其粒度应符合表5-3的要求。
同时还要求制砖用硅石原料中不得混入废石、角烁状硅石、风化石等,硅石表面不允许有直径大于5%的各种有害物包裹体。
(2)废砖
制造硅砖可以掺入部分废硅砖作原料,其理化性能需达到以下要求:
SiO2含量≥94%,耐火度≥1690℃。
用于制砖生产的废砖,要求其表面不能附着火泥及碱性杂质侵蚀物,而且砖表面因金属物造成的显著变色部分应<15mm,超过时需经过处理后方可使用。
表5-3对硅石原料的粒度要求(YB/T5268-1999)
粒度范围/mm
最大粒度/mm
最大粒度的含量/%
下限
上限
20~40
50
10
8
40~60
70
10
8
60~120
140
10
5
120~160
170
10
8
160~250
260
8
6
2.原料的洗涤
由于硅石中经常混入泥土和夹杂物,对原料和制品高温性能的影响很大,所以使用前必须进行挑选和洗涤。
目前一般采用在板式输送机、运输车辆、料槽中进行冲洗的简易措施。
3.原料的加工
硅石、干燥废坯和烧成废砖一般采用颚式破碎机进行破碎。
破碎后的块度一般要求在40mm以下。
破碎后的硅石进入短头圆锥破碎机、双辊式破碎机、干碾粉碎机中进行粉碎。
粉碎后的硅石料、废坯和废砖采用单层筛(或振动筛)进行筛分,其中<0.5mm的颗粒不是很多(通常在30%~45%范围内),特别是<0.088mm的细粉过少,所以还需采用筒磨机进行细磨,管磨机出料口一般采用lmm的筛网。
粉料在皮带运输过程中应用电磁铁(或磁铁)除铁,并选出料中杂质。
硅石细粉中<0.088mm的含量一般控制在85%~90%,对硅石细粉的细度要求列于表5-4。
表5-4国内一些硅砖生产厂对硅石粉料的粒度要求
生产厂
粉碎设备
粉料的粒度要求
粒度/mm
含量/%
A厂
圆锥破碎机
≥2
0.5~0.1
<0.1
8~18
20~25
35~40
筒磨机
<0.1
≥97
B厂
筒磨机
<0.088
≥90
C厂
筒磨机
<0.1
≥90
D厂
筒磨机
<0.1
≥92
(三)粒度组成的选择
硅质坯体加热时的松散和烧结能力取决颗粒组成中粗细两种粒度的性质和数量。
粗颗粒转变在很大程度上发生在细颗粒转变和砖体开始形成(烧结)之后。
所以粗颗粒转变时体积膨胀是砖体趋于松散以至开裂的基本因素。
烧成时转变程度愈高,粗颗粒的松散作用也愈大。
相反,细颗粒多处于颗粒堆积的孔隙中,不仅细颗粒本身的膨胀对砖坯的膨胀影响小,而且在高温下它与矿化剂作用使烧结能力增强。
特别是小于0.088mm的细颗粒是促进砖坯烧结具有最大活性的部分。
因此希望在砖坯中有足够的细颗粒含量,以提高砖坯的烧结性。
采用细颗粒组成的砖坯时,在烧成时有利于减少膨胀,减少砖膨胀与颗粒组成的体的裂纹和体积变化,提高成品率,还可提高制品中鳞石英的含量,但泥料颗粒过细,也将导致硅砖气孔率的提高。
砖坯的密度及其烧结能力是决定硅砖的致密度的两个主要因素。
但最致密的砖坯不一定制得最低气孔率的硅砖。
在加入物不变的情况下,粒度系数,即<0.088mm的细粉含量与临界粒度颗粒含量的比值,决定了砖坯的烧结能力。
实践证明,当临界粒度为3mm时,粒度系数,即<0.088mm与3~1mm颗粒的含量比为0.75~1.00的条件下,硅砖的气孔率、密度和外观质量都较好。
临界粒度不同时,砖坯烧成时烧结而不松散的粒度系数值不同。
它随临界粒度的增大而提高。
所以临界粒度增大时,坯体内应含有较多的细颗粒。
实验证明,硅砖烧成时会产生裂纹松散倾向,而且砖密度随临界粒度的减小而降低。
因此,为了提高砖的鳞石英化程度,减少体积变化和裂纹产生,提高成品率,采用较小的临界粒度是有利的。
一般硅砖的临界粒度以2~3mm为宜。
以脉石英为原料时,多采用2mm为最大颗粒。
硅砖泥料粒度组成的要求如表5-5所示。
表5-5硅砖泥料的粒度组成要求
砖种
粒度组成(质量分数)/%
>3mm
<0.5mm
<0.088mm
标型砖及一般砖
≤3
55~65
28~35
焦炉砖
≤3
55~65
30~35
注:
对于某些手工成型的大型和特异型砖,泥料中<0.088mm细粉的含量可增至35%~40%。
(四)结合剂的选择和石灰乳的制备
1.结合剂的选择
制造硅砖用的结合剂有纸浆废液和石灰。
用石灰(CaO)作结合剂时,一般以石灰乳的形式加入配料中。
它起着塑化剂的作用,结合砖坯内的石英颗粒,在干燥过程中增加砖坯的强度,而在烧成时则成为矿化剂,促进石英的转化。
因此采用石灰的质量在很大程度上决定着砖坯的性质。
制造硅砖用的石灰要求活性CaO含量≥90%,未分解的CaCO3+MgCO3含量不应超过5%,杂质Al2O3+Fe2O3+SiO2的含量不超过5%。
当石灰乳中含有大的欠烧CaCO3颗粒和过烧石灰时,烧成时会在成品中产生熔洞,影响制品质量,因此去必须除去或在球磨机中将其磨碎。
石灰的块度应≥50mm,小块(<5mm)的含量不超过5%,大块内部的颜色应与表面相同,不应掺有熔渣、灰分等杂质。
也可采用硅酸盐水泥代替石灰作结合剂使用。
配料时石灰加入量应换算成CaO,通常波动在1.5%~2.5%,确切值应根据制品用途(如耐火度及使用温度等因素)、泥料的颗粒组成和原料中CaO杂质含量而定,如表5-6所示。
表5-6石灰乳中的CaO含量
浓度波美度
密度/g·cm-3
CaO含量
浓度波美度
密度/g·cm-3
CaO含量/
g/L
%
g·L-1
%
18
19
20
21
22
23
24
25
26
1.143
1.152
1.161
1.170
1.180
1.190
1.200
1.210
1.220
181
193
206
218
229
242
255
268
281
15.85
16.75
17.72
18.61
19.40
20.34
21.25
22.15
23.03
27
28
29
30
32
34
36
38
40
1.230
1.241
1.252
1.262
1.285
1.308
1.332
1.357
1.384
295
309
324
339
371
407
445
489
525
23.96
24.90
25.87
26.84
28.99
31.23
33.56
35.89
38.41
为了进一步提高泥料的可塑性和砖坯的干燥强度,石灰乳还需与亚硫酸纸浆废液混合加入,纸浆加入量应小于1%。
2.石灰乳的制备
石灰乳的制备方法,在机械化生产厂中,将石灰经转筒消化器和球磨机消化和粉碎。
从球磨机流出的浆料经1~1.5mm筛孔的筛网过滤,然后将料浆抽到搅拌筒(立式浆叶式搅拌机)中贮存一定时间,再将其送人另一搅拌机内,并调整至要求浓度,最后经过储存桶和计量桶送至混合设备使用。
使用前须经过0.1~4mm筛孔的检验筛,要求筛余量不超过5%,石灰乳的比重应为1.20~1.25。
用人工方法制备石灰乳时,可将石灰和水加入一组开口的铁槽(或木槽)内,先制取浓浆,然后在另一槽内搅拌,调整浓度,再送到另一槽内贮存待用。
根据石灰的消化速度,石灰可分为:
快速消化石灰(在l0min内消化完毕);中速消化石灰(10~30min消化完);慢速消化石灰(30min以上消化完)。
在硅砖生产中,希望采用快速消化石灰,它可以用冷水消化,而慢速消化石灰须用50~60℃的热水进行消化。
制备好的石灰乳应是充分消化和细分散的,呈油脂状。
经充分消化的石灰乳,具有强的可塑性和结合性。
石灰乳中不应含有粗粒石灰,否则会使制品干燥时开裂或烧成时产生熔洞废品。
粗分散的石灰乳因矿化作用不够,会导致制品强度低,断面组织结构不良。
消化石灰时,应将石灰倒人多量水中,以增加灰浆量,并制得细分散的石灰乳。
为了掌握石灰乳的浓度,保证成型泥料具有必要的水分和一定数量的石灰,可以用比重计直接测其比重来表示石灰乳浓度。
实际操作时,首先从比重计的刻度上读出波美度数,然后从表5-7中查出CaO含量。
(五)矿化剂的选择
在实际生产中,采用的矿化剂为轧钢皮(也叫铁鳞)、平炉渣、硫酸渣和石灰乳等。
其中以采用轧钢皮和石灰乳的为多。
在这种情况下,石灰乳不仅是矿化剂,而且还是结合剂。
采用轧钢皮作矿化剂时,要求FeO十Fe2O3的含量>90%。
轧钢皮进厂后须经筛选和烘烤,并且不得混有铁块、油脂等杂物。
为使轧钢皮在泥料中均匀分布并达到良好的矿化效果,必须在球磨机中磨碎。
磨细后的轧钢皮粒度要求如下:
>0.5mm的不准有,<0.1mm的≥97%。
矿化剂的加入量一般不应超过3%~4%。
因为矿化剂的含量过多会强烈地降低硅砖的耐火度。
增加矿化剂中CaO的含量可以降低硅砖的气孔率和真密度,提高硅砖砖坯和制品的强度及成品率。
目前,我国生产硅砖泥料内加入的矿化剂数量如表5-7所示。
表5-7焦炉砖泥料内矿化剂加入量
使用原料及生产厂家
加入量(质量分数)/%
Fe+Fe2O3
CaO
石门硅石(AG厂)
五台硅石(TG厂)
铁门硅石(LY厂)
0.5~0.8
0.5
1.0
2.0~3.0
1.8~2.5
2.0~2.5
(六)废硅砖加入量
硅砖生产过程中产生的烧成废硅砖可作为原料使用。
由于烧成废硅砖已经过烧成膨胀,用其制砖可以减少砖坯的烧成膨胀与产生的应力,从而减少硅砖的裂纹,降低烧成废品。
尤其是形状复杂的大型和特异型制品,更需要加入较多的废硅砖以提高成品率。
一般质量<25kg的异型砖可加入20%的废硅砖,>25kg的可加入30%,特异型和大型制品可加入40%。
但加入废砖会降低制品的耐火度和机械强度,提高气孔率(见表5-8)。
因此废硅砖加入量通常控制在20%左右。
表5-8废硅砖加入量对硅砖制品性能的影响
废硅砖加入量/%
砖坯体积密度/g·cm-3
成品指标
显气孔率/%
耐压强度/MPa
0
2.26
22
54
10
2.16
23
39
20
2.14
24
32
30
2.11
25
28
40
2.04
26
25
(七)配料及混合
1.配料
硅砖配料多采用重量配料法配料。
其配料中临界粒度一般为2~3mm,细粉(<0.088mm=加入量为10%~20%(手工成型可配到30%~40%),废硅砖加入量为10%~20%(单重较大或异型砖可加入到30%~40%)。
结合剂、矿化剂的加入量按生产条件来定。
硅砖的配料组成如表5—9所示。
表5-9国内一些厂家生产硅砖的配料组成
生产厂
砖种
配料组成/%
结合剂与矿化剂的配比及加入方式
硅石
废砖粉
A厂
机压焦炉砖
机压一般砖
手工成型砖
90
85
80
10
16
20
纸浆废液,石灰乳、氧化铁粉以混合液形式加入,其中Fe2O39%~12%,CaO≥24%,纸浆废液5%~6%。
B厂
机压一般砖
振动成型砖
手工成型砖
90
80
70
10
20
30
纸浆废液、石灰乳以混合液形式加入,混合液比重不低于1.2,外加铁粉1%。
C厂
机压一般砖
机压焦炉砖
90
90
10
10
纸浆与石灰乳以混合液形式加入,其中CaO不低于28%,纸浆15%,外加氧化铁粉0.5%~0.8%。
另外,生产中常常采用不同产地的硅石混合配料。
这样可以利用它们各自不同的结晶性能和晶型转化速度来改善砖坯在烧成过程中的转化特性,使制品的鳞石英化程度提高,残余石英含量下降,减少烧成裂纹,从而得到优质硅砖。
2.混合
泥料的混合质量与配料的粒度级别、配料比、混合设备、加料顺序等因素有关。
一般通过控制混合料的粒度组成和水分来保证混合质量。
常用的混合设备有湿碾机,混砂机,单、双轴搅拌机,强制式搅拌机等。
加料顺序:
将各种硅石粉和废硅砖粉按一定配比加入湿碾机中,先干混2~3min,然后再加入纸浆废液、石灰乳及铁鳞粉的混合液,根据制品的用途和成型方法的要求,再混合8~17min,总混练时间不得少于20min。
补加水或石灰乳应在出料前10min进行。
泥料混合时间太长,会影响砖坯和制品的强度。
混合时间长短取决于碾轮的重量及形状、碾盘转数、原料加入量、原料硬度、泥料的颗粒组成及成型方法等。
特异型砖和手工成型泥料比机械成型的泥料要求有较长的混合时间。
一些耐火厂硅砖泥料的混合时间见表5-10。
在湿碾机中混合的缺点是颗粒再粉碎,这种再粉碎作用,在混合初始几分钟最明显。
再粉碎程度取决于泥料的湿度、硅石的硬度,湿度大的料或软质硅石的再粉碎程度大些。
再粉碎时,细颗粒数量会增加,粗颗粒会减少,而中间颗粒则几乎不变。
增加混合料层厚度,调整碾轮与刮板的位置和碾轮与碾盘距离及角度,都可以控制和减少颗粒再粉碎的程度。
硅砖泥料的水分一般控制在5%~9%。
其中手工成型的为7%~9%,而机压成型的为5%~6%。
混合好的硅砖泥料,以颗粒组成、水分、碱度三项作为硅砖泥料的检验指标。
硅砖泥料的混合制度如表5-10所示。
表5-10一些硅砖生产厂家的硅砖泥料混合制度
生产厂
混合
设备
成型方式
混合
时间/min
粒度组成(质量分数),%
泥料碱
度1)/%
泥料水分/%
>3
mm
3~2
mm
<0.5
mm
<0.1
mm
<0.088
mm
A厂
湿碾
机
机压
手工
11
11
<2
<2
13~20
<14
55~59
58~62
30~38
32~36
1.4~1.7
2.0~3.0
5~5.6
8~8.5
B厂
湿碾
机
机压
振动
≥15
≥20
≤3
≤1
<10
35±5
20~302)
18~252)
30~40
35~45
2.0~2.5
4.5~5.3
8.5~9.5
C厂
湿碾
机
机压
振动
≥15
≥20
8~