叶军毕业设计1.docx
《叶军毕业设计1.docx》由会员分享,可在线阅读,更多相关《叶军毕业设计1.docx(54页珍藏版)》请在冰豆网上搜索。
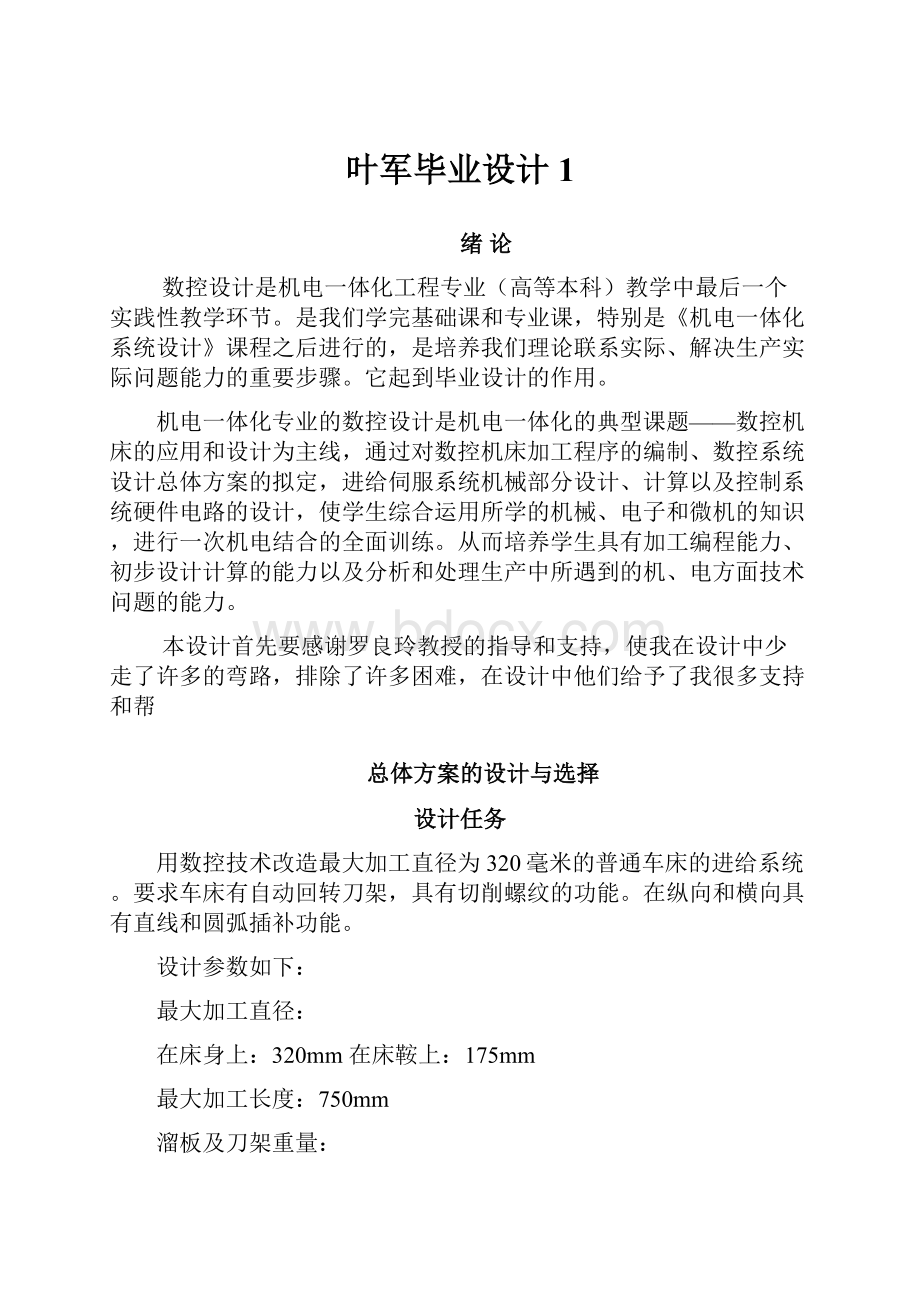
叶军毕业设计1
绪论
数控设计是机电一体化工程专业(高等本科)教学中最后一个实践性教学环节。
是我们学完基础课和专业课,特别是《机电一体化系统设计》课程之后进行的,是培养我们理论联系实际、解决生产实际问题能力的重要步骤。
它起到毕业设计的作用。
机电一体化专业的数控设计是机电一体化的典型课题——数控机床的应用和设计为主线,通过对数控机床加工程序的编制、数控系统设计总体方案的拟定,进给伺服系统机械部分设计、计算以及控制系统硬件电路的设计,使学生综合运用所学的机械、电子和微机的知识,进行一次机电结合的全面训练。
从而培养学生具有加工编程能力、初步设计计算的能力以及分析和处理生产中所遇到的机、电方面技术问题的能力。
本设计首先要感谢罗良玲教授的指导和支持,使我在设计中少走了许多的弯路,排除了许多困难,在设计中他们给予了我很多支持和帮
总体方案的设计与选择
设计任务
用数控技术改造最大加工直径为320毫米的普通车床的进给系统。
要求车床有自动回转刀架,具有切削螺纹的功能。
在纵向和横向具有直线和圆弧插补功能。
设计参数如下:
最大加工直径:
在床身上:
320mm在床鞍上:
175mm
最大加工长度:
750mm
溜板及刀架重量:
纵向:
800N横向:
400N
刀架快移速度:
纵向:
2m/min横向:
1m/min
最大进给速度:
纵向:
0.8m/min横向:
0.4m/min
最小分辨率:
纵向:
0.01mm横向:
0.005mm
定位精度:
0.02mm
主电机功率:
3KW
起动加速时间:
25ms
总体方案的确定
系统运动方式与伺服系统的选择
由于改造后的经济型数控车床应具有定位、直线插补、顺、逆圆弧插补、暂停、循环加工、公英制螺纹加工等功能,固应选择连续控制系统。
考虑到属于经济型数控机床加工精度要求不高,为了简化结构、降低成本,采用步进电机开环控制系统,步进电机采用混合式步进电机。
计算机系统
根据机床要求,采用8位微机。
由于MCS-51系列单片机具有集成度高,可靠性强、功能强、速度快、抗干扰能力强,具有很高的性能价格比等特点,决定采用MCS-51系列的8051单片机扩展系统。
控制系统由微机部分、键盘及显示器、I/O接口及光电隔离电路、步进电机功率放大电路等组成。
系统的加工程序和控制命令通过键盘操作实现,显示器采用数码管显示加工数据及机床状态等信息。
机械传动方式
为实现机床所要求的分辨率,采用步进电机经齿轮减速再传动丝杆,为保证一定的传动精度和平稳性,尽量减小摩擦力,选用滚珠丝杆螺母副。
同时,为提高传动刚度和消除间隙,采用有预加负荷的结构。
齿轮传动也要采用消除齿轮侧间隙的结构。
系统总体方案框图
经济型数控车床进给伺服系统方案框图2-1
数控车床机械的计算
和选型
切削力的计算
纵车外圆
N切削功率=KηN额
=1×0.8×3=2.4(KW)
式中取K=1∽1.25间断时间越长K值越大;
η=0.7∽0.85;N额=3KW
主切削力Fz(N)按经验公式估算(取为η=0.8)
Fz=60000×N切削功/V线=60000×2.4÷90=1600N
式中取V线=90m/min
按切削力各分力比
Fz:
Fx:
Fy=1:
0.5:
0.6可得:
Fx=Fz×0.5=1600×0.5=800N
Fy=Fz×0.6=1600×0.6=960N
横切端面时
主切削力Fz´(N)取纵切力的1/2
Fz´=0.5×Fz=0.5×2400=800N
Fx´=1200×0.5=400N
Fy´=1440×0.5=400N
滚珠丝杠螺母副的计算和选型
纵向进给丝杠
计算进给牵引力Fm(N)Fm=KFx+f(Fz+G)
=1.15×800+0.17(1600+800)
=1328N
式中K=1.15三角形导轨/综合导轨(滑动导轨)
f=0.15∽0.18为滑动导轨摩擦系数。
铸铁对钢铁导轨f取0.17计算;
G:
为溜板及刀架重力,取800N
选择导程(L)
选择合适的导程,使马达的最大转速和最大快速移动度能满足下式:
=
=4(mm)
Vmax快速移动速度mm/min
Nmax驱动马达min-1
本例选择L=5mm
螺母的设计
必需的基本额定动态负载(C)当导程为5mm时计算得出如下结果:
C=
Fmfw
Lh寿命(h)(15000h为一个单位)
C基本额定动态负载(N)
Fm平均轴向负载(N)
Nm平均转速(min-1)
fw负载因子(由运动情况决定的系数)
无冲击平滑运转 fw=1.0~1.2
普通状态下的运转 fw=1.2~1.5
有冲击和振动情况下的运转 fw=1.5~2.0
Nm=1000Vs/L0
=1000×0.8×0.5÷5
=80
Fm=1328N
C=
Fmfw
=
×1328×1.5
=8287
校核必需的基本额定动态负载和允许的转速(DmN值)
〈导程为5的情况〉
纵向进给时:
Fm=1328(N)Nm=80(min-1)C=8287(N)
直径20,导程5和2.5圈1个回路
这时,DmN值为:
DmN=20.8×500=10400≤50000符合设计要求
[研磨滚珠丝杠]DmN≤70000[轧制滚珠丝杠]DmN≤50000
这里:
Dm:
丝杠直径(mm)+A
N:
最大转数(min-1)
表3-1
滚珠直径
0.8
1.0
1.5875
2.0
2.3812
3.175
3.9688
4.7625
6.35
7.1438
7.9375
9.525
A
0.24
0.3
0.3
0.4
0.6
0.8
0.8
1.0
1.8
2.0
2.0
2.4
表明该型号螺母满足允许值。
选择GR2005DS-AALR插管式单螺母(表3-2)
丝杠直径d
导程L
滚珠直径Db
根径
回路数
基本额定动态负载C
基本额度静态负载Co
刚性KNS
Pm/mm
外径D
总长Lt
檫洗器
没有檫洗器E
厚度T
20
5
3.1750
17.5
2.5×1
8350
17500
140
40
48
L
5
12
外径D1
类型
X
Y
B
油孔Q
PCD
直径
沉孔
深度
68
A
40
60
21
M6
53
6.6
11
6.5
丝杠的设计
校核丝杠的总长(l)、允许轴向负载(P0)和临界速度(Nc)。
假定:
L=最大行程+螺母长度+余量+两轴端的尺寸
=700+50+70+180=1000
为了获得允许轴向负载,应校核弯曲负载。
假定受力点之间的距离L1=800,
弯曲负载P0
P0=
=
=58501.78N
P0=58501.78(N)
这里:
P0:
开始发生弯曲变形时的负载(N)
l:
负载点之间的距离(mm)
E:
弹性模量(2.06×105N/mm2)
I:
滚珠丝杠轴截面的最小二次力矩(mm4)
I=(π/64)×d4
d:
丝杠根径(mm),参见尺寸表
图3-1
n:
由滚珠丝杠的支撑方式决定的系数
支撑—支撑 n=1
固定—支撑 n=2
固定—固定 n=4
固定—自由 n=0.25
滚珠丝杠的刚度
滚珠丝杠的刚度(Ke)
假定轴承端面之间的的距离L3=1005,由于在l3/2处轴的变形量最大,
所以在该处进行计算。
下面的公式
Kl
=257.57(N/μm)
E:
弹性模量(2.06×105N/mm2)
d:
丝杠的根径(mm)
螺母的刚度(Knw)
任何大小预压下的刚度是指在预压力(PL)为最大的1/3时的值,
Knw=Kns
=140×
=1142(N/μm)
精度选择
参考下表格定(表3-3)
位精度选择±0.018/700<0.02,允许偏差(ec)选择C3(ec=±0.013)
GE2005DS-AALR-1005×925C3S型滚珠丝杠
横向进给丝杠的计算
进给牵引力Fm´(选导轨为燕尾形)
Fm´=KFy´+f´(Fz´+2Fx´+G)
式中K=1.4;f´=0.2;G=400N
所以Fm´=1.4×480+0.2(800+2×400+400)=1072N
计算最大动负载C´
C=
Fmfw
=
×1072×1.5
=5309.06N
丝杠螺母副的选择(次处具体计算参考纵向选择)
选择GR2004ES-AALR插管式双螺母
丝杠直径d
导程L
滚珠直径Db
根径
回路数
基本额定动态负载C
基本额度静态负载Co
刚性KNS
Pm/mm
外径D
总长Lt
檫洗器
没有檫洗器E
厚度T
20
4
2.3812
18.1
2.5×2
8600
23400
250
40
49
L
3
10
外径D1
类型
X
Y
A
油孔Q
PCD
直径
沉孔
深度
64
A
49
60
5.5
M6
51
5.5
9.5
5.4
选择GE2004ES-AALR-0605×525-C4S 丝杠
丝杠名称代号意义参见附表1
齿轮传动比的计算
纵向进给齿轮箱传动比的计算
已确定纵向进给脉冲当量为δp=0.01;滚珠丝杠导程L0=5mm,选不进电动机的步距角θb=0.6º。
可计算传动比i为:
i=360δQ/L0/θb=360×0.01÷0.6÷5=1.2
可选定齿轮数为Z1=20,Z2=24模数m取2。
滚珠丝杠的几何参数
参数名称
符号
关系式
GE2005DS
GE2004ES
螺纹
滚导
公称直径
d0
20
20
导程
L0
5
4
接触角
β
3º39¹
3º39¹
钢球直径
dq
3.175
2.381
滚导法面半径
R
R=0.52dq
1.651
1.238
偏心距
е
е=(R-dq/2)sinβ
0.0404
0.0158
螺纹伸角
γ
γ=arctan(L0/л/d0)
4º33¹
3º39¹
螺杆
大径
d
d=d0-(0.2∽0.25)dq
19.36
19.52
底经
d1
d1=d0+2е-2R
16.779
15.269
接触直径
dz
dz=d0-dqcosβ
16.831
17.634
螺母
螺纹直径
D
D=d0-2е+2R
23.221
22.444
内径
D1
D1=d0+(0.2∽0.25)dq
20.635
20.476
横向进给齿轮箱传动比的计算
横向进给脉冲当量δp´=0.005,滚珠丝杠导程取L0´=4mm,选步进电动机的步距角为θb´=0.6º 计算总传动比:
i´=360δQ´/L0´/θb´=360×0.005÷0.6÷4=0.75
Z1=40Z2=30
因进给运动齿轮受力不大,模数m取2。
其参数见下表表
传动齿轮几何参数
齿数
Z
40
30
分度圆
d=mz
80
60
齿顶圆
da=d+2m
84
64
齿根圆
df=d-2×1.25m
75
65
齿宽
(6∽10)m
20
20
中心距
A=(d1+d2)/2
70
步进电动机的计算和选型
纵向进给步进电机的计算和选型
初选步进电机
进电机负载转矩Tm
Tm=36Fmδp/(2πθbη)=(36×0.01×1832)÷(2×3.14×0.6×0.98×0.99×0.94)=191.83N·cm
式中δp为脉冲当量取0.01mm/sep;
Fm为进给牵引力,取1832N;
θb为电动机的步距角,选双拍制为0.6º
η为电动机—丝杠的传动效率,为齿轮,轴承,丝杠的
效率之积,分别取0.98,0.99,0.99和0.94;
估算步进电机的起动转矩Tq
Tq=Tm/(0.3∽0.5)=191.83÷0.3=639.42N·cm
计算最大静转矩Tmax
步进电动机的其动转矩和最大静转矩的关系
步进
电机
相数
三相
四相
五相
六相
拍数
3
6
4
8
5
10
6
12
λ=Tq/Tmax
0.5
0.866
0.707
0.707
0.809
0.951
0.866
0.866
取三相6拍,则:
Tjmax=Tq/0.866=537.5÷0.866=738.36N·cm
计算步进电动机运行频率fe和最高起动频率fk
fe=1000Vs/60δp=1000×0.8÷60÷0.01=1333.3Hz
fk=1000Vmax/60δp=1000×2÷60÷0.01=3333.3Hz
式中Vs为最大切削进给速度,取0.8m/min;
Vmax为最大快速移动速度,取2m/min;
δp为脉冲当量,取0.01mm/step。
选步进电动机的型号
根据估算出的最大静转矩在下表可查出110BYG350M型的最大静转矩为1000N·cm>Tjmax可以满足要求。
因数控机床有较大的切削用量,应选稍大一点转矩的步进电动机,以保证有一定的余量。
校核步进电动机转矩
等效转动惯量的计算
传动系统折算到电动机轴上的总的转动惯量J∑可以由下式计算:
J∑=JΜ+J1+(Z1/Z2)²[(J2+JZ)+G/g×L0²/(2π)²]
这里:
L0 丝杠导程(mm)J∑:
施加于马达的转动惯量(kg·cm2)
J1:
小齿轮的转动惯量(kg·cm2)
J2:
齿轮的转动惯量(kg·cm2)
JZ:
滚珠丝杠的转动惯量(kg·cm2)
JM:
马达转子的转动惯量(kg·cm2)
参考同类型的机床,应选的步进电动机为110BYG350M型,
其转子的转动惯量JΜJΜ=5.6kg·cm²
圆柱形的转动惯量,如滚珠丝杠和齿轮,可由下述公式计算
这里:
D:
圆柱体的外径(cm)L:
圆柱体的长度(cm)
:
材料的密度
=7.8×10-3(kg/cm3)
J1=0.784kg·cm²
J2=2.032kg·cm²
JZ=1.231kg·cm
G=800N(g为重力加速度 9.8kg/s2)
代入上式可得:
J∑=44.55kg·cm²
因步进电动机与传动系统的惯量应相匹配:
JΜ/J∑=0.125<0.25不满足设计的匹配要求。
重新选择110BYG350B型号的混合式步进电机,JΜ=12.6kg·cm²
最大静转矩为1800N·cm>Tjmax可以满足要求0.25电动机转矩的计算
快速空载起动转矩M
在快速空载起动时,加速转矩占的比例较大,其计算公式为:
M=Mamax+Mf+M0
式中Mamax=J∑ε=J∑×2π×10ˉ²nmax/60taN·cm
nmax=υmaxθb/360º/δp=2000÷0.01×0.6÷360º=333.3r/min
起动加速时间ta=25ms
所以Mamax=622N·cm
折算的电机轴上的摩擦转矩为Mf
Mf=F0L0i/2π/η=f´(Fz+G)L0i/2π/η
式中f´=0.16,G=800N,i=1.2
所以Mf=0.16×(1600+800)×0.5×1.2÷2÷π÷1.2=45.84N·cm
附加摩擦转矩M0:
M0=Fp0L0i×(1-η0²)/2π/η
=1328÷3×0.5×1.2×(1-0.9²)÷2÷π÷0.8
=10.04N·cm
式中Fp0=Fm/3=442.67N;
故空载起动转矩M=Mamax+Mf+M0=677.88N·cm
快速移动时需要的转矩M´
M´=Mf+M0=55.88N·cm
最大切削负载时的转矩M´´
M´´=Mf+M0+Mt=Mf+M0+FxL0i/2π/η=151.37N·cm在三种情况下,快速空载起动所需的转矩最大,即按此转矩来校核步进电动机。
在表1-4中查出,当步进电动机为三相6拍时λ=M/Mjmax=0.866,则最大静转矩为Mjmax
Mjmax=M/0.866N·cm=174.79N·cm
查出110BYG350B型步进电动机最大转矩为180N·cm,大于所需的最大静转矩,满足要求。
校核步进电动机的起动距频特性和运行距频特性。
前面已经计算出此车床纵向最大快速移动时的所需的步进电动机的最高起动频率为3333.3Hz,切削进给时所需步进电动机的运行频率为1333.33Hz。
可查出110BYG350B型步进电动机允许的最大空载起动频率为3000Hz,运行频率为16000Hz,查得110BYG350B型的步进电动机的起动矩频特性和运行矩频特性曲线。
可以看出步进电动机满足空载起动转矩而不产生失步现象
横向进给步进电动机
初选步进电动机
计算步进电动机负载转矩Tm
Tm´=36Fm´δp´/(2πθb´η)
=(36×0.005×1072)÷(2×3.14×0.6×0.98×0.99×0.94)
=93.59N·cm
(式中参数与前面取相同值)
估算步进电动机的起动转矩
Tq´=Tm´/(0.3∽0.5)=187N·cm
计算最大静转矩Tjmax´
查表取三相6拍,则:
Tjmax´=Tq´/0.866
=187÷0.866
=196.81N·cm
计算步进电动机的运行频率fe´和最高空载频率fk´
fe´=1000υs´/60δp´=1000×0.4÷60÷0.005=1333.3Hz
fk´=1000υmax´/60δp´=1000×1÷60÷0.005=3333.3Hz
选电机的型号
根据估算出的最大静转矩在表可查出110BYG350型的最大静转矩为1000N·cm>Tjmax=262.88N·cm可以满足要求。
因数控机床有较大的切削用量,应选稍大一点转矩的步进电动机,以保证有一定的余量。
此步进电机的最高空载起动频率为3800Hz满足fk´=3333.3Hz的要求。
校核步进电动机转矩
等效转动惯量的计算
传动系统折算到电动机轴上的总的转动惯量J∑可以由下式计算:
J∑=JΜ´+J1+(Z1/Z2)²[(J2+Js´)+G/g×L0²/(2π)²]
式中JΜ´为步进电动机转子的转动惯量(kg·cm²);
J1´,J2´为齿轮的转动惯量(kg·cm²);
Js´为滚珠丝杠的转动惯量(kg·cm²)。
参考同类型的机床,应选的步进电动机为110BYG350型,其转子的转动惯量JΜ´:
JΜ´=5.6kg·cm²
J1´=0.0165kg·cm²
J2´=0.0489kg·cm²
Js´=0.185kg·cm²
G´=400N
代入上式可得:
J∑´=15.06kg·cm²
因步进电动机与传动系统的惯量应相匹配:
0.25电动机转矩的计算
1)快速空载起动转矩M´
在快速空载起动时,加速转矩占的比例较大,其计算公式为:
M´=Mamax´+Mf´+M0´
式中Mamax´=J∑´ε=J∑´×2π×10ˉ²nmax/60ta´N·cm
nmax=υmax´θb´/360º/δp´
=1000÷0.005×0.6º÷360º=333.52r/min
起动加速时间t=25ms
所以Mamax´=21.03N·cm
折算的电机轴上的摩擦转矩为Mf´
Mf´=F0´L0´i´/2π/η=f´(Fz´+G´)L0´i´/2π/η
式中f´=0.16,G´=400N,π=3.14,i´=0.75;
所以Mf´=0.16×(800+400)×0.75×0.4÷2÷3.14÷0.8=11.5N·cm
附加摩擦转矩M0:
M0´=Fp0´L0´i´×(1-η0²)/2π/η
=357.3×0.4×0.75×(1-0.9²)÷2÷3.14÷0.8
=2.59N·cm
式中Fp0´=Fm´/3=357.3N;
故空载起动转矩M2´=Mamax´+Mf´+M0´=35.127N·cm
2)快速移动时需要的转矩M1´
M1´=Mf´+M0´=14.09N·cm
3)最大切削负载时的转矩M1´´
M1´´=Mf´+M0´+Mt´=Mf´+M0´+Fx´L0´i´/2π/η=37.98N·cm
在三种情况下,快速空载起动所需的转矩最大,即按此转矩来校核步进电动机。
在表查出,当步进电动机为三相6拍时:
λ=M2´/Mjmax´=0.866,则最大静转矩为Mjmax´
Mjmax´=M2´/0.866N·cm=43.85N·cm
从表中查出110BYG350型步进电动机最大转矩为100N·cm,大于所需的最大静转矩,满足要求。
校核步进电动机的起动距频特性和运行距频特性。
前面已经计算出此车床横向最大快速移动时的所需的步进电动机的最高起动频率为3333.3Hz,切削进给时所需步进电动机的运行频率为1000Hz。
可查出110BYG350型步进电动机允许的最大空载起动频率为3800Hz,运行频率为16000Hz,查得110BYG350型的步进电动机的起动距频特性和运行距频特性曲线如图右所示
数控系统的硬件电路
80c51引脚图管脚图及各引脚功能简介
Vss(20脚):
接地
VCC(40脚):
主电源+5V
XTAL1(19脚):
接外部晶体的一端。
在片内它是振荡电路反相放大器的输入端。
在采用外部时钟时,对于HMOS单片机,该端引脚必须接地;对于CHMOS单片机,此引脚作为驱动端。
XTAL2(18脚):
接外部晶体的另一端。
在片内它是一个振荡电路反相放大器的输出端,振荡电路的频率是晶体振荡频率。
若需采用外部时钟电路,对于HMOS单片机,该引脚输入外部时钟脉冲;对于CHMOS单片机,此引脚应悬浮。
RST(9脚):
单片机刚接上电源时,其内部各寄存器处于随机状态,在该脚输入24个时钟周期宽度以上的高电平将使单片机复位(RESET)
PSEN(29脚):
在访问片外程序存储器时,此端输出负脉冲作为存储器读选通信号。
CPU在向片外存储器取指令期间,PSEN信号在12个