PVC木塑发泡制品生产技术精华总结.docx
《PVC木塑发泡制品生产技术精华总结.docx》由会员分享,可在线阅读,更多相关《PVC木塑发泡制品生产技术精华总结.docx(28页珍藏版)》请在冰豆网上搜索。
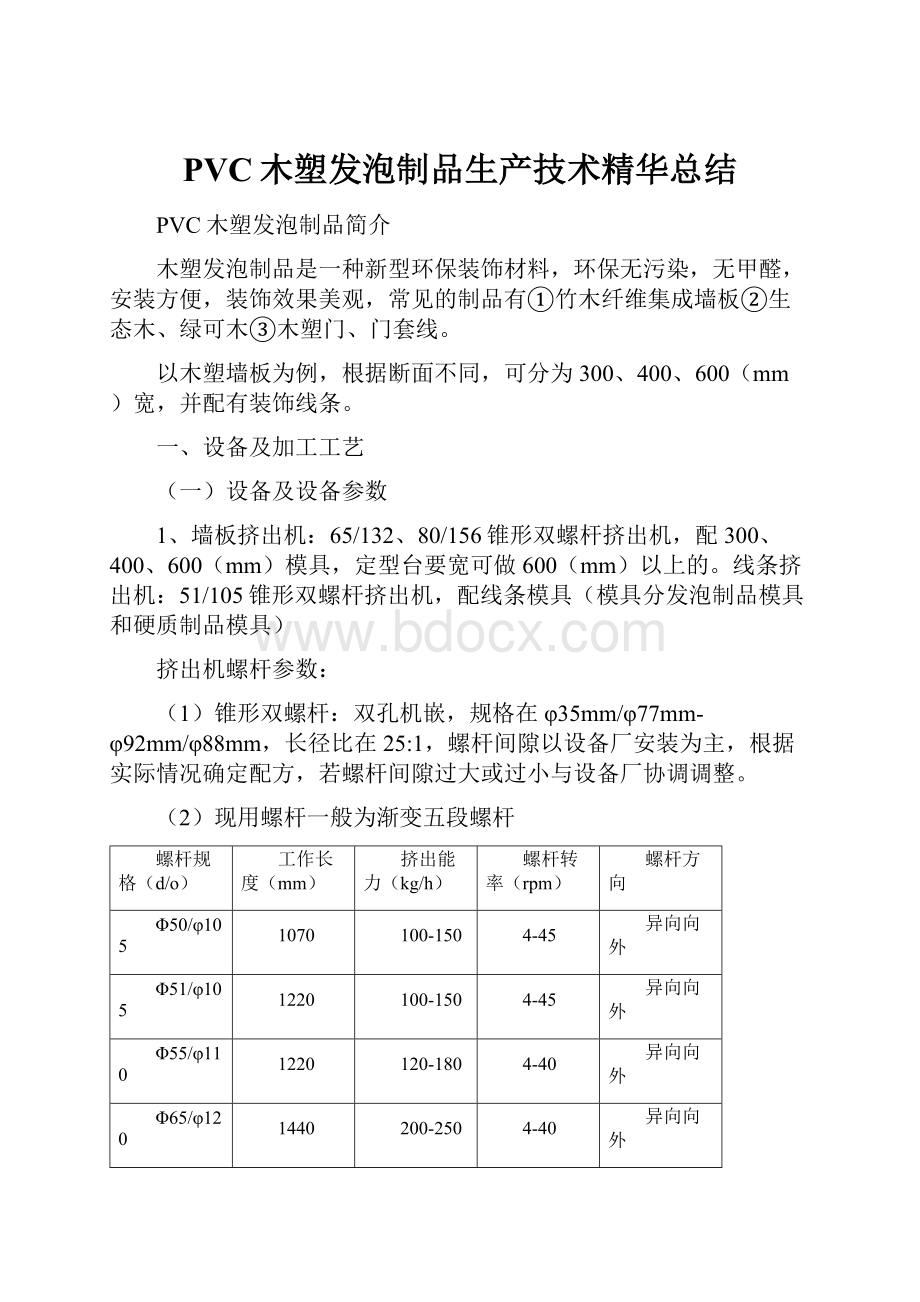
PVC木塑发泡制品生产技术精华总结
PVC木塑发泡制品简介
木塑发泡制品是一种新型环保装饰材料,环保无污染,无甲醛,安装方便,装饰效果美观,常见的制品有①竹木纤维集成墙板②生态木、绿可木③木塑门、门套线。
以木塑墙板为例,根据断面不同,可分为300、400、600(mm)宽,并配有装饰线条。
一、设备及加工工艺
(一)设备及设备参数
1、墙板挤出机:
65/132、80/156锥形双螺杆挤出机,配300、400、600(mm)模具,定型台要宽可做600(mm)以上的。
线条挤出机:
51/105锥形双螺杆挤出机,配线条模具(模具分发泡制品模具和硬质制品模具)
挤出机螺杆参数:
(1)锥形双螺杆:
双孔机嵌,规格在φ35mm/φ77mm-φ92mm/φ88mm,长径比在25:
1,螺杆间隙以设备厂安装为主,根据实际情况确定配方,若螺杆间隙过大或过小与设备厂协调调整。
(2)现用螺杆一般为渐变五段螺杆
螺杆规格(d/o)
工作长度(mm)
挤出能力(kg/h)
螺杆转率(rpm)
螺杆方向
Φ50/φ105
1070
100-150
4-45
异向向外
Φ51/φ105
1220
100-150
4-45
异向向外
Φ55/φ110
1220
120-180
4-40
异向向外
Φ65/φ120
1440
200-250
4-40
异向向外
Φ65/φ132
1440
200-250
4-40
异向向外
Φ80/φ143
1800
300-360
4-35
异向向外
Φ80/φ156
1660
300-360
4-35
异向向外
Φ92/φ188
2000
400-500
4-35
异向向外
(3)螺杆技术指标
氮化层深度:
0.5-0.8mm
氮化硬度:
950-1020HV
氮化脆度:
≤一级
表面粗糙度:
Ra0.4μm
螺杆直线度:
0.015mm
双合金硬度:
HRc55-62
双合金深度:
>2mm
(4)选用材料和工艺
优质38CrMoA1A
优质双向不锈钢
优质粉末冶金材料
冷热喷涂硬金属工艺
先进渗氮工艺
双金属加工制造工艺
(5)螺杆基体采用38CrMoA1A的加工,①热处理②渗氮处理③电镀硬铬层④高频淬火⑤喷涂双金属合金层
2、混料机:
300/600、500/1000、600/1200、1000/2000混料机,
混料机的正确选择:
(1)按生产能力要求选择混料机的容积
(2)热混机的工作容积一般是70-80%以内
(3)能够自动的排气
(4)密封要好,严防物料的渗出
(5)浆叶的耐磨损要强,混合时搅拌剪切要均匀无死角
(6)对温度能够自动控制并能准确显示
(7)便于维护、维修
(8)冷混锅的体积最好是热混锅的三倍
(9)冷混设备的冷却要均匀一致,内壁不能够结露
(10)冷混搅拌也要均匀一致,密封要好,也要便于维修和维护
3、刀式/锤式破碎机、磨粉机:
根据实际产量订购相应型号的破碎机和磨粉机
4、包覆机、3D打印机等表面处理设备以及包覆膜的分切机、胶水(热胶、冷胶等)
(二)设备加工工艺
第一部分:
PVC加工工艺简述
PVC的实际加工分为六部分,这六部分缺一不可,这六部分没有说那一部分重要那一部分不重要,对于PVC产品来说是同等重要的,这六部分主要分为以下:
1、原材料的作用(包括原材料的物理性能、化学性能、机械性能及在PVC当中的作用);
2、PVC的配方;
1)协同反应的配方:
两种原材料放在一起在配方中能起到三种、四种、五种等作用,效率明显增高。
2)加合反应:
两种原材料放在一起效率没有增高也没有降低。
3)对抗反应:
两种原材料放在一起添加到配方中它的效率不但没增高反而降低,相当于一种或者低于一种的效果,所以它的效果明显降低,实际上对抗反应就是一种化学反应,按照最粗略得讲就是化学中的酸碱反应;
3、混料工艺:
就是把配方所做成的原材料放到一个装置中加温混合;起到预塑化的作用;
4、挤出机的结构及挤出工艺;
5、模具;
6、员工的操作技术及责任感。
以上六部分是脱离不开的,脱离任何一部分产品都不会做好,不要忽略任何部分,技术不懂不会,好产品照样做坏,相反的技术好了,对于不是很好的配方也可做到极善完美。
责任感就是人为的部分。
这六部分同等重要,在PVC加工中配方占了一个产品的30~40%,挤出机的结构和挤出工艺占25%,混料工艺占20%,员工的操作技术和职能也占了10~15%。
第二部分:
挤出机的结构和挤出工艺:
1、挤出机的结构(以单螺杆为例)
挤出机是由电动机(即驱动装置),减速箱(减速器),分配箱,机筒、螺杆(机筒螺杆是一部分),加热冷却装置,电控装置组成。
挤出机结构的核心部分是机筒和螺杆,其它的都是辅助装置,但没有这些装置也不行,这些装置属于固定的易损件。
物料及混合好的干粉料,通过喂料机设到一定的转速向机筒的料槽里进行推进,这个料就自然推到机筒螺杆中。
2、挤出机机筒螺杆各部的作用:
一区(预塑化区):
在整台挤出机的电控加热和挤出过程中一区的作用是相当最重要的,它承担的任务包括:
1、干粉料压实,剪切,定量向前输送2、提前预塑化的一个过程,若一区没有达到预塑化会出现以下情况:
1、主机排气孔冒料,2、电流明显变大3、产品非常脆,一区温度设置一般在135-140℃,具体视实际情况设定。
二区(塑化区):
在这个区当中,把一区传递过来的干粉料通过一区的预塑化已压成块状,随着螺杆的转动,把压实的块状物向前输送到达二区,在这个区螺铃的结构发生变化,螺铃变到4~5mm厚而且产生了9~11圈的螺旋,并且两端是断开,所以第二区就完全达到标准塑化度的90%以上。
因为螺铃里面还有好多小槽,就达到了搅拌的目的,所以整体来说二区达到了塑化的90%以上。
若物料在一区没有达到预塑化,那么将会对二区产生不良影响:
1、干粉料不塑化、2、挤掉螺铃。
二区的温度设置一般在145-150℃,具体要根据挤出机的塑化能力来设置,,若挤出机的塑化能力较好,该区温度可以低些,若挤出机的塑化能力不好,该区温度应和相对高些(可以从真空口观察物料的塑化状况)。
三区(均化区):
该区的作用是把二区没有完全塑化的物料进行完全塑化,三区要保证塑化达到100%。
所以挤出机的三区也比较重要,三区的温度设置在160-165℃,具体视塑化程度等实际情况进行调节。
四区(定量输送挤出区):
该区不承担一点塑化任务,若物料塑化相当好,在该区可以看到,螺杆漂浮于挤出机机筒的中心上旋转。
所以挤出机四区的任务是把塑化好的熔体定量的向前输送,若该区承担塑化能力,对挤出机危害作用是非常大的。
四区的温度应该高于三区,一般设置在165-170℃,根据实际情况进行设置。
从以上分析来看木塑制品挤出机的温度设置由低到高的,一区温度是最低的,不允许由高向低,也不允许是平的。
3、合流芯的作用:
1)两只螺杆挤出的熔体物料达到合流、熔接。
2)塑化度的微调装置。
3)通过合流芯的传感器测出熔体压力、熔体温度可以判断塑化度。
塑化度的微调装置的作用:
当塑化度稍稍有点低或塑化度稍稍有点高时,就可以不用去考虑挤出机的其它问题,可以通过降低或升高合流芯的温度来调整塑化度。
降低合流芯的温度增加塑化度,提高合流芯的温度降低塑化度。
合流芯的温度一般设置成155℃或170℃,根据实际情况进行设置和调整。
4、模头的作用就是产出合格产品。
这里我们在阐述一下降低合流芯的温度增加塑化度,升高合流芯的温度反而降低塑化度,我们PVC高分子材料它有一个特性,温度越高,流动性越快,但是不是无限度的,例如墙板,有四个区加热,若左面流动慢、出料比较少,将这边加加温,流动性立马就增加,所以说越是加温,物体的流动性、挤出量就越快,为什么加温物体的流动性就快,是因为没有阻力了,很顺畅的挤出了,实际上我们可以把合流芯看做一个阀门,当我们的水的阀门完全打开的时候,水很顺畅的往下流,当阀门打开一半或完全关闭时,水就不流或流的很少,我们就把合流芯当做水的一个阀门,温度低的时候就等于把阀门关上一会,就是这种道理。
通过来调整合流芯的温度来提高一定的塑化度,但是它不是完全的,用它来提高塑化度微量很小。
塑化不良不是代表不塑化,是指有一定的缺陷,所以当有塑化不良这种情况时,我们可以把合流芯的温度往下调,下调以后是不是塑化就良了,物料的流动就慢了,产生一个压力,产生压力的结果就是增加了塑化度。
第三部分:
塑化度
1、塑化度对产品性能的影响:
PVC产品的性能与塑化度息息相关,塑化度不良,制品发脆,力学性能不能达到要求;塑化度过高,制品会出现黄线,力学性能也不合格,塑化度在PVC制品的加工过程中是非常重要的。
1)当塑化度60%时,拉伸强度最高;
2)当塑化度65%时,冲击强度最高;
3)当塑化度70%,断裂伸长率最高;
2、温度对塑化度的影响:
高分子材料在低于80℃时不能成熔体,呈玻璃态,处于玻璃态的物料即硬又脆,在玻璃态下材料不能加工;随着温度的升高到160℃时物料处于高弹态,但在该区域物料还是无法流动,只能使物料变软、粘弹性增加;真正能达到PVC熔体加工的、而且有流动性的,温度应在160-200℃之间,但是对于任何稳定剂,在温度高于200℃时,长期受热,物料又分解了,所以在控制塑化度时,温度只能控制在160-200℃之间。
在这40℃的温差范围内,PVC的温度设置在170-180℃之间时,塑化较好。
3、提高塑化度的方法:
1)通过提高机身和螺杆的温度。
2)待螺杆转速正常时,提高喂料机的喂料速度来提高塑化
3)在挤出机额定转速和满足喂料的情况下,提高挤出机的转速。
4)给干粉料一个良好的熟化期(12—48h)熟化期的作用:
1、消除静电、减少污染2、增加表观密度3、提高塑化度4、低分子聚合分散均匀,防止挤出不稳定。
5)通过降低合流芯的温度来提高部分塑化度。
4、如何判断塑化度:
1)通过主机电流判定塑化度以(65/132生产线为例,主机电流以42-45A为宜,具体情况视配方和设备而定。
前提是:
喂料充满并与螺杆转速相匹配,温度设定与螺杆转速及主机电流相匹配);
2)通过主机真空排气孔观察物料的塑化度(即物料在螺杆螺棱螺槽中间充满60%以上,螺棱凹槽中粉料呈豆腐渣状态且凹槽底部物料被压平);
3)通过模具口模的熔体物料的粘弹性来判定塑化度(该方法较为适用于刚开机时);
4)通过合流芯的熔体压力及熔体温度来判定塑化度(其缺点为若仪表失灵或合流芯传感器被焦料糊死等因素会影响检测结果的准确性)
二、模具
300、400、600(mm)宽模具,顶线、腰线等线条系列模具,根据实际开模具,可带有模口共挤(带共挤机),配线条模具,根据实际情况开模具(模具注意保养和维护)。
三、原料选择
(一)主体材料
1、PVC树脂粉:
PVC树脂是一种白色粉末,在火焰上能燃烧,离火自熄,介电绝缘性良好,是一种非结晶极性的高分子聚合物,玻璃化温度依分子量大小为75-105℃,其相对分子量越大,黏数就越高,材料的强度、刚度、韧性、耐热及耐低温性越好,但成型加工难,加工性越差,所以发泡制品一般选用黏度低的PVC树脂粉,型号为SG-7、SG-8,平均聚合度(PVC分子量)SG-7分子量850-750、SG-8分子量750-650,主要生产厂家齐鲁石化、天津大沽化、、陕西北园、河南宇航、新疆中泰、唐山三友、长治霍家等。
2、填充料(碳酸钙):
轻质碳酸钙的沉降体积为2.4-2.8ml/g,颗粒微细,呈针纤状,表面较粗糙,比表面大,吸油值高,在60-90ml/㎎;要选择粒径大小均匀,细度要好,过1250目,白度在93以上,木塑发泡制品一般选择轻质碳酸钙,主要作用如下,
①提高塑料制品的硬度、耐磨性及强度;②提高塑料制品的热变形温度,降低成型收缩率和挤出涨大效应;③提高塑料制品的热稳定性和耐候性;④改变塑料制品的导电及导热性;⑤降低塑料制品成本;⑥赋予塑料本身没有的特殊功能。
主要产地河北、江西、广西等(可选用轻质碳酸钙或选择重钙。
重钙体积小、流动性好,选用1500目的重钙)。
3、木粉:
过100目的杨木粉,杨木粉的特点是含有较长的纤维丝、细度好、无油性、分散性好、成本低,使产品具有木质感。
4、稳定剂:
PVC加工时的核心添加剂,PVC热分解时易放出HCI气体,加入稳定剂解决HCI气体生成,木塑发泡制品一般选择复合铅系列稳定剂,建议使用铅含量在30%以上、内外滑均衡,能够增加制品的稳定性,延长开车周期,防止物料糊料,防止出现废料增加生产成本。
稳定剂具备优点:
①稳定性持久;动态热稳定时间大于30min;②能有效促进PVC凝胶化且内外滑平衡,从而有效降低添加量,长时间加工无析出;③不降低硬质PVC制品的维卡温度;
④用于硬质制品时与其他添加剂有良好的协同;⑤易分散、不飞尘;⑥使用简单,单包化,方便计量;⑦用量少,一般为4-7份。
5、润滑剂:
作用如下,
①降低熔体粘度②减少内生热③脱模作用④延迟塑化作用⑤防止熔体破裂。
选择要求:
①分散性②挥发性③适当的相容性④良好的光、热和化学稳定性和高温润滑性⑤对制品的性能无不良影响⑥多功能性⑦不引起颜色的漂移,甚至改善颜色或填料在PVC树脂中的分散性⑧无毒和卫生性⑨具有较好的质量和性价比。
(1)外润滑剂:
PE蜡(聚乙烯蜡),PE蜡与树脂的相容性有限,能够从熔体内部迁移到表面,与金属表面有一定的亲和力,这样在熔体表面和金属之间形成了一层相对稳定的隔离层,从而抑制熔体与金属表面的粘连。
使用PE蜡能增加物料的金属剥离性和制品的光洁度,防止熔体破裂和延长塑化时间,PE蜡应选择熔点为105±5℃,例如河北毅美的F-95,河北毅美PE蜡与其他厂家PE蜡相比添加份数少,做出的制品表面光洁度好,性价比高。
(2)内润滑剂:
硬脂酸,调节物料的流动性,减少内生热,降低熔体粘度。
硬脂酸是极性基团,与PVC树脂有很好的相容性,可以对熔体起到较好的内润滑作用,硬脂酸选择的型号为1801、1820、1838、1842,常用的为1820、1838和1842,不建议使用1801。
(3)评价内外润滑作用的平衡:
①内外滑均不足,特点是熔体粘度较大,塑化扭矩较大,熔体粘壁现象严重。
表现在螺杆上熔融料不好清理,严重的可能提前热分解,制品表面光滑性较差,制品表面易出现水波纹,水波纹呈白色,制品力学性能较低。
如果内外滑剂平衡,则熔融料一碰就下来,螺杆表面基本不粘熔体料。
②内外滑剂均过量,塑化扭矩较小,虽然制品表面光滑度很好,但力学性能较低,严重时用手擦试试有油样感觉,表面有析出现象,制品表面易出现水波纹,水波纹呈黑色。
③内润滑剂较少,外润滑剂较多,塑化时间明显延长,塑化扭矩有所增大,制品表面有涂油的感觉,制品变脆。
④内润滑剂较多,外润滑剂较少,塑化时间明显缩短,有较严重的黏附现象,螺杆不好清理,热稳定时间缩短,制品有分解黄线。
6、发泡调节剂:
ACR-100系列、ACR-903,具有超高的分子量,大大提高PVC熔体强度,可以保持进入熔体的气泡达到均匀的蜂窝结构,防止泡孔塌陷,从而就可以获得低密度的发泡材料。
同时由于气体不会从熔体中逸出,材料表面就会特别光滑有光泽(调节发泡密度,促进物料塑化、增加制品的均实度,调节泡孔结构均匀)。
7、AC(黄):
复合黄色发泡剂ADC/AC,偶氮二甲酰胺,受热后分解产生气体调节制品的密度。
发泡剂须具有以下特性,
①分解产生气体的温度必须在一定的狭窄范围内;②放出气体的速度必须是可控的,而且分解速度较快;③放出的气体必须是无毒、无色、无臭、无腐蚀性、对原材料无性能影响;④必须容易在聚合物中分散,最好能溶解在其中;⑤价廉;⑥常温储存时稳定;⑦分解残渣必须无色、无污染、无不良气体;⑧发泡剂及分解残渣均无毒;⑨发泡剂分解时放热不大;⑩分解残渣应与聚合物相溶、不影响材料的性能;
注:
不建议使用AC发泡原粉。
(二)回料、废料选择,选择塑钢、小管、发泡制品回料并磨粉,降低成本,增加制品硬度。
四、配方
(一)生产料配方如下(以某木塑墙板客户为例):
配方原料名称
300mm及腰线脚线添加份数
400、600mm添加份数
备注
PVC树脂粉
100
100
天津大沽化
轻质碳酸钙
90-120
90-120
木粉
15
15
稳定剂
5.8
6.8
衡水精信JX-04L-B
PE蜡
0.8
1
衡水毅美F-95
硬脂酸
0.7
1.5-2
康桥1838
ACR-100
7
8
AC(黄)
1.2
1.3
磨粉料(自己生产的废料)
15-20
20
注:
(1)腰线、脚线和300mm墙板为同一配方,400mm和600mm墙板为同一配方。
(2)根据实际生产可以添加部分塑钢回料、小管回料、发泡回料。
(二)压条配方参考型材和扣板配方,根据实际情况生产。
(三)清机料配方(高混75℃,冷混40℃)
配方原料名称
添加份数
PVC树脂粉
100
轻质碳酸钙
75-100
稳定剂
12
PE蜡
2.4
硬脂酸
2
注:
也可选用PE蜡和硬脂酸。
五、车间协作及制品加工过程
1、称量
根据制品的性能、加工技术和配方情况的要求选用合格的原料并进行称量,称量要准确无误,作好记录。
2、混料
(1)混料,高低混料机一般混料温度为高混温度125℃(高混机排气孔打开),冷混温度45℃(冷混锅要通水)
(2)投料顺序,先加入钙粉木粉混到65℃,再加入小料、PVC,最后加回料。
(3)热混与冷混。
所谓热混,是指将混合物加热到软化温度或软化温度以上进行的掺混过程。
热混过程中各组分之间不仅有空间位置的相对变化,还有粒子先被打碎,粒径减小而后又逐渐长大的变化过程,因此这是一种分散混合。
当所有原料按配方比例投入热混锅后,热混锅中的搅拌器首先以低速启动,随后立刻切换为高速搅拌。
物料在高速剪切作用下迅速升温,并达到设定的125℃,在此过程中,PVC颗粒逐渐变软膨胀,并产生一定程度的凝胶化作用(预塑化),许多熔点较低的物质如润滑剂也已经融化渗入或黏附在PVC表面,各种原料在高速剪切作用下粒子被打散逐渐细化,表面能急剧增加,然后重新吸附在PVC表面上,使得PVC颗粒粒径渐渐变大,物料获得较好的初步凝胶化作用和分散效果。
热混使干物料同时取得较大的表观密度,物料流动能力加强,这有利于干混料的输送,并取得较高的挤出效率。
比如,PVC表面密度在0.55ml/g左右,而在经过混料过程后,混合料的表观密度能到达到0.62ml/g。
热混的过程中要注意,由于各种原料中难免含有水分和易挥发组分,在热混过程中这些易挥发组分在高温作用下挥发,因此热混时一定要保证热混锅排气通道的畅通。
如果排气不充分,热混锅顶部冷凝的水分会重新落入原材料,使最终制品中内部形成气孔等缺陷。
热混锅的升温主要是来自搅拌叶片的剪切作用,因此叶片的完好程度将明显影响热混效果。
当叶片端部的磨损超过15mm时,热混效果将大打折扣。
实际经验中,当热混时间达到正常时间的两倍时,必须更换受损叶片。
物料在热混锅达到设定的温度后,将被迅速放入冷混锅,在搅拌器的慢速搅动和冷混锅外冷却系统的作用下充分地分散降温,这个过程就是冷混。
冷混锅的容积至少是热混锅的两倍,非常有利于热混料的降温。
如果冷混温度太高,冷却不充分也不均匀,PVC干混料会较长时间处于较高温度,消耗太多稳定剂,导致PVC的降解,干混料发红并影响到最终产品的热稳定性和耐候性。
(4)混料效果的评价
混料的目的是为了取得PVC适度的初步凝胶化作用,配方各组分之间的均匀分布,以及获得适度的表观密度和干流性。
要量化的评价干混料各组分之间的分布均匀程度是较难的,但干混料的一些表观密度等是很容易加以控制的。
在实际生产中干混料的混料质量往往通过以下几项指标进行评价和控制:
①表观密度②表观白度③热稳定时间④挥发分含量⑤流变性能⑥筛余物⑦干流性
上述干混料指标中,干混料的白度能够反映配料的计量准确与否,更重要的是反映原料的初步凝胶化程度。
当白度低于正常值时,反映原料中凝胶化作用过强,原料受热时间过长,需检查热混温度的控制是否准确,如热电偶是否接触不良导致实际温度过高等;表观密度过大,筛余物过多过大,反映同样的问题,原料的热混由过头的倾向,需要检查设备。
当表观密度过低、干流时间过长时,反映混合效果不好,需注意实际温度控制是否有问题。
热稳定时间异常,要么原料的加入计量不准,导致热稳定剂不足或过多,也可能是混料的温度控制系统有问题。
有时,由于搅拌叶片磨损严重,温度很难达到设定温度,结果物料经受过长时间的热混,也会导致干混料热稳定时间缩短。
挥发分含量超标,反映热混时挥发分排除不良,一方面要控制原材料的挥发分含量,另一方面要检查热混锅的挥发分排空通道是否堵塞。
3、开机
(1)挤出机工艺温度设定及喂料转速、主机转速等设定
主机:
Ⅰ区135-140℃;Ⅱ区145-150℃;Ⅲ区160-165℃;Ⅳ区165-170℃(参考)
合流芯:
155℃
口模:
Ⅰ区170-175℃;Ⅱ区170-175℃;Ⅲ区170-175℃;Ⅳ区170-175℃(参考),根据制品的不同设定相应的温度。
新设备开机前,需要依次加入少量PE蜡和硬脂酸、开机料和正常生产料。
加入PE蜡和硬脂酸能够更好地排掉设备内的杂质并起到维护设备的作用。
(2)模具、定型模,注意真空压力和冷却水的温度,和模时找到制品的发泡点进行合模。
4、牵引
根据实际情况设定合理的牵引速度。
5、切割
6、测米重,检查制品的质量
(1)墙板米重
制品规格
米重g/m
300mm
1500
400mm
2300
600mm
3500
(2)线条米重
线条米重视线条种类和生产要求而定
8、包覆或3D打印,具体视实际生产而定
六、常见问题及注意事项
1、不发泡、发泡不良或出现大气泡,根据现场情况查看设备和调整工艺配方
2、制品筋不粘连,制品脆性大,表面不光滑,调整配方中的滑剂体系及工艺参数
3、制品表面不光滑或有波浪纹、断面出现阴阳脸,根据设备和配方情况而定
七、PVC发泡制品挤出成型的原理
注:
生产发泡制品主要是观察物料的状态和泡孔结构(塑化最好达到95%以上,泡孔越密实越好)
PVC发泡挤出制品是指用PVC树脂、稳定剂、加工助剂、发泡剂等经挤出机塑化、压缩剪切挤出,有特定的发泡工艺而成形的表面坚硬、内心发泡的制品。
称之结皮发泡板。
PVC发泡挤出成型主要采用化学发泡剂。
聚合物熔体挤出口模前,发泡剂分解所得气体溶解于聚合物熔体中;挤出口模后,熔体内压力下降,温度降低,使融入熔体的气体处于过饱和的状态,发生相分离,形成大量泡孔而发泡。
离开口模后即被冷却定型模中的冷却水强制冷却,使其表面形成硬质皮层,而熔体在内部迅速发泡扩张形成发泡层。
所得制品其表皮厚度为0.3-0.5mm,表皮的厚度会随熔体温度、冷却速度、牵引速度等的不同而变化。
由于发泡剂在接近PVC熔融温度(约180度)的条件下发泡,但又要求发泡必须发生在PVC熔融之后,所以必须使发生在相同温度下的发泡和熔融这两个过程相互分开,才不会造成相互干扰,影像制品的质量。
为防止熔体提前发泡,应尽可能使发泡阶段后推,含有发泡剂的熔体必须从机头挤出后才膨胀。
同时机头内的压力要应高于气体气体发泡的压力。
若熔体在机头内发泡气体逸出将破坏已形成的泡孔,导致表面粗糙。
PVC发泡板挤出成型的生产工艺参数应遵循如下原则:
1、在冷却定型时水温在10度以下最好。
水温过高,制品表面硬度,不够冷却不充分易变形。
2、PVC发泡配方中通常用AC发泡剂。
配方中的铅盐稳定剂可使AC发泡剂的热分解温度减低由200度降至170度左右,然而PVC的熔融温度高于170度,这就要求