挤塑工作原理.docx
《挤塑工作原理.docx》由会员分享,可在线阅读,更多相关《挤塑工作原理.docx(22页珍藏版)》请在冰豆网上搜索。
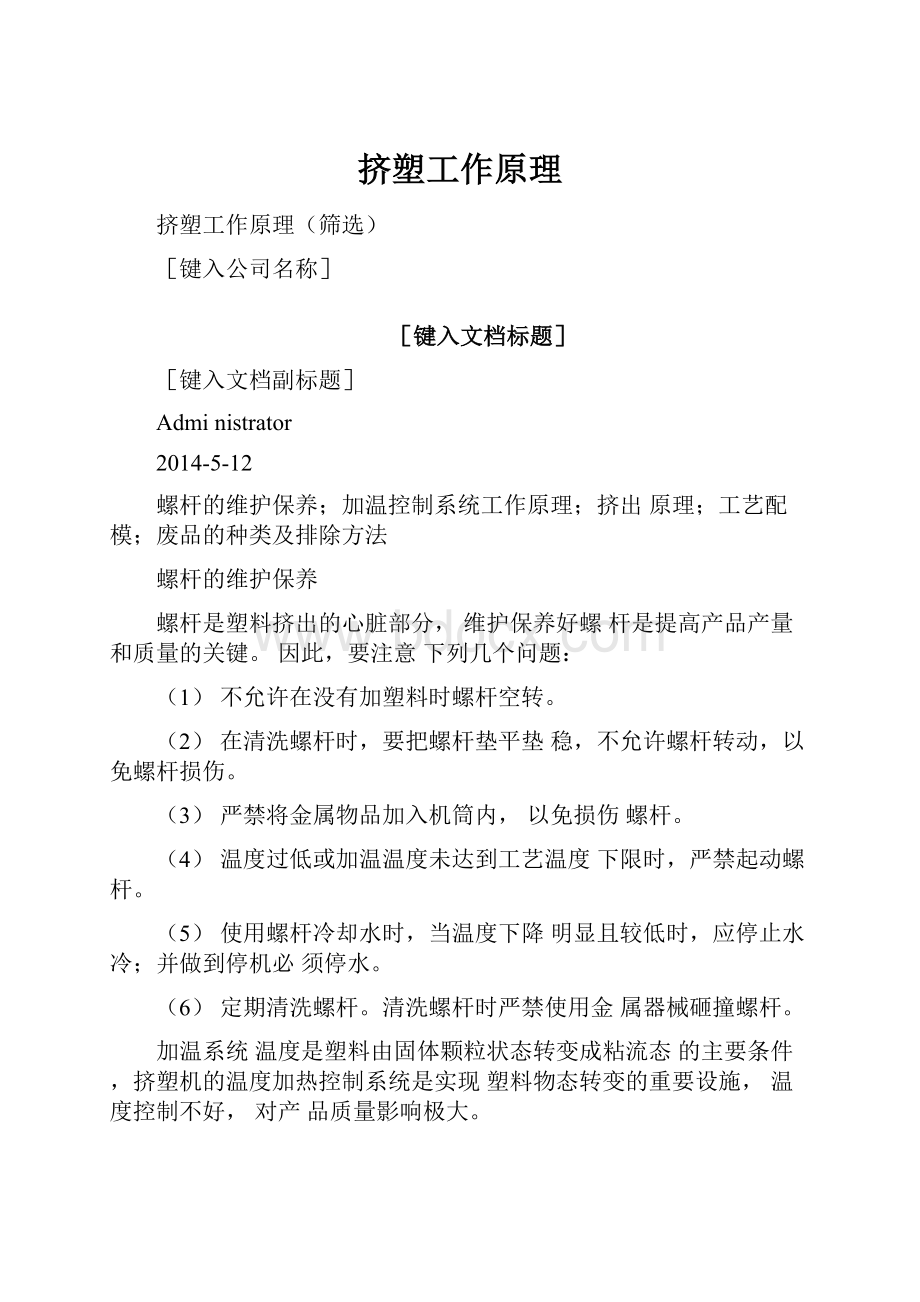
挤塑工作原理
挤塑工作原理(筛选)
[键入公司名称]
[键入文档标题]
[键入文档副标题]
Administrator
2014-5-12
螺杆的维护保养;加温控制系统工作原理;挤出原理;工艺配模;废品的种类及排除方法
螺杆的维护保养
螺杆是塑料挤出的心脏部分,维护保养好螺杆是提高产品产量和质量的关键。
因此,要注意下列几个问题:
(1)不允许在没有加塑料时螺杆空转。
(2)在清洗螺杆时,要把螺杆垫平垫稳,不允许螺杆转动,以免螺杆损伤。
(3)严禁将金属物品加入机筒内,以免损伤螺杆。
(4)温度过低或加温温度未达到工艺温度下限时,严禁起动螺杆。
(5)使用螺杆冷却水时,当温度下降明显且较低时,应停止水冷;并做到停机必须停水。
(6)定期清洗螺杆。
清洗螺杆时严禁使用金属器械砸撞螺杆。
加温系统温度是塑料由固体颗粒状态转变成粘流态的主要条件,挤塑机的温度加热控制系统是实现塑料物态转变的重要设施,温度控制不好,对产品质量影响极大。
一、温度控制系统挤塑机的温度控制系统是由电加热和冷却组成,以实现挤塑机各区域温度的升降和调节,控制适当温度可保证挤出质量。
1.温度控制机理安装在挤塑机上的电加热器和冷却风机是主要的控制机构。
由于电加热具有升温、降温迅速的特点,而温度过高和过低都是挤出中要绝对避免的,所以电加热必须有一套灵敏度相当高的温度调节装置尤溪般包括有自动测量仪器、控制仪表,以及有效的冷却设施。
在挤塑机的适当位置上(越接近塑料层越好)安装有测量元件热电偶,就是极其重要的温度检测元件。
在加温和挤出过程中,测温元件热电偶随时测得的热电势信号被送到控温仪,经放大处理后与温度设定值比较,温度仪表指示不到设定值时,则继续加热,如接近或到达设定值,则按不同的调节规律仪表发出不同的指示信号。
当超过设定值,则开动冷却风机,是机身得到冷却,使温度得以下降,回到预设定值。
如此反复,自动控制或手动调节,使温度稳定在被控制值附近。
2.挤塑机的温控部位
根据挤出原理,挤塑机各部位的温度应有差
别,可以用设置于各部位电加热片的容量差别来实现。
一般的,加料段容量最小,(压缩)塑化段和均化段容量要大些,而机头是保温区,主要以加热克服散热,所以容易不大。
在挤塑机中温控一般是根据加热片的多少分为6〜8段,小型挤塑机一般分为六段,大型挤塑机分成八段,通过控制屏上温度仪表的显示,来对挤塑机的六个加热区进行温控。
以六段加热挤塑机为例,六个温控区域部位如下图所示。
挤塑机的六个温控部位或各加热段的温度,在控制屏上都可以在温度仪表上一一显示,由操作者直接观察而知,便于调
1区(模套出口)
3.温控各部位的作用还是以六段加热挤塑机为例。
六个温控部位在挤塑机的机头处有三个,机身处有三个。
温度可根据需要自动调节,但应满足工艺规定的温度范围。
在使用过程中,加料段加热区温度较低,机脖加热区的温度较高,模具加热区的温度稍低,形成了一般温控部位由低到高到稍低的变化,这是由于各部位的作用而决定的。
(1)机头1、2区的作用:
机头区的温控,对塑料挤出表面质量起着决定作用,如果温度控制得合适,模具选配的恰当,塑料产品的表面就平整光滑。
(2)机头3温区(机脖)的作用:
塑料塑化好以后,在螺杆旋转作用下由机筒进入机脖,由于机脖容积较机筒小,又加上滤板的作用,产生较大的阻力,螺杆旋转产生的推力作用,塑料致密,并塑化压实,保证了塑化效果。
此时需要较高的温度,有利于塑料熔体顺利的进入机头。
(3)机身4、5温区的作用:
此加热区为均化段和塑化段,由于螺杆转动的搅拌压缩作用,经过预热的固体塑料变成可塑的粘滞液体(熔融状态),在温度的作用下,塑料完成塑化均匀。
(4)机身6温区的作用:
颗粒状塑料从加料斗进入机筒内,由于温度的作用,塑料开始被预热,并把多余的气体从加料口排除。
此段的温度控制不宜过高,以免影响颗粒塑料的下料,故为温度控制区域最低的加温区。
二、控制温度的高低对产品质量的影响温度是塑料由固体状态向粘流状态转变的有效手段,同时它也可能造成塑料的烧焦或分解,温度低时,也可能造成严重的设备事故。
由于塑料品种的不同,以及挤出速度、挤出外径、挤出厚度的不同,在实际的挤出过程中,温度控制不尽相同,因此对具体的品种采用相应的挤塑温度。
另外,除塑料和结构尺寸造成的温度控制不同外,环境温度也应予以考虑。
因此,严格按照工艺要求控制温度的高低,保证挤塑过程的顺利进行,保证良好的产品质量,是每一个操作者不可忽视的职责。
(1)温度过高:
指的是温度控制超过某种塑料的最佳塑化温度,容易使塑料焦烧和老化,也容易产生气孔、气泡、气眼、定型不好等质量问题。
温度过高,还会造成挤出过程中挤出压力波动,塑料在机筒内“打滑”,挤出量不稳,使挤包层和产品外径尺寸不均。
(2)温度过低:
指的是温度控制低于塑料的最佳塑化温度,造成塑料塑化不好,挤出表面有树脂疙瘩或未塑化好的小颗粒。
特别是合胶缝合不好,不但影响产品质量,还容易造成塑胶层脱节、裂纹、断胶等现象。
因此,要严格按照工艺规定控制温度,不宜过高或过低。
在实际操作过程中,因设备新旧、外径大小的不同,挤制工艺有所不同,温度控制也不尽相同,挤制绝缘和护套所用塑料一样,但因树脂中的添加剂不同,其温度控制亦有区别。
另外,环境温度的高低也会影响挤塑温度的控制,冬天与夏天就要相差5〜10oC。
塑料挤出的基本原理挤塑机的工作原理是:
利用特定形状的螺杆,在加热的机筒中旋转,将由料斗中送来的塑料向前挤压,使塑料均匀的塑化(即熔融),通过机头和不同形状的模具,使塑料挤压成连续性的所需要的各种形状的塑料层,挤包在线芯和电缆上。
1.塑料挤出过程电线电缆的塑料绝缘和护套使是采用连续挤压方式进行的,挤出设备一般是单螺杆挤塑机。
塑料在挤出前,要事先检查塑料是否潮湿或有无其它杂物,然后把螺杆预热后加入料斗内。
在挤出过程中,装入料斗中的塑料借助重力或加料螺旋进入机筒中,在旋转螺杆的推力作用下,不断向前推进,从预热段开始逐渐的向均化段运动;同时,塑料受到螺杆的搅拌和挤压作用,并且在机筒的外热及塑料与设备之间的剪切摩擦的作用下转变为粘流态,在螺槽中形成连续均匀的料流。
在工艺规定的温度作用下,塑料从固体状态转变为熔融状态的可塑物体,再经由螺杆的推动或搅拌,将完全塑化好的塑料推入机头;到达机头的料流,经模芯和模套间的环形间隙,从模套口挤出,挤包于导体或线芯周围,形成连续密实的绝缘层或护套层,然后经冷却和固化,制成电线电缆产品。
2.挤出过程的三个阶段塑料挤出最主要的依据是塑料所具有的可塑态。
塑料在挤出机中完成可塑过程成型是一个复杂的物理过程,即包括了混合、破碎、熔融、塑化、排气、压实并最后成型定型。
大家值的注意的是这一过程是连续实现的。
然而习惯上,人们往往按塑料的不同反应将挤塑过程这一连续过程,人为的分成不同阶段,即为:
塑化阶段(塑料的混合、熔融和均化);成型阶段(塑料的挤压成型);定型阶段(塑料层的冷却和固化)。
第一阶段是塑化阶段。
也称为压缩阶段。
它是在挤塑机机筒内完成的,经过螺杆的旋转作用,使塑料由颗粒状固体变为可塑性的粘流体。
塑料在塑化阶段取得热量的来源有两个方面:
一是机筒外部的电加热;二是螺杆旋转时产生的摩擦热。
起初的热量是由机筒外部的电加热产生的,当正常开车后,热量的取得则是由螺杆选装物料在压缩、剪切、搅拌过程中与机筒内壁的摩擦和物料分子间的内摩擦而产生的。
第二阶段是成型阶段。
它是在机头内进行的,由于螺杆旋转和压力作用,把粘流体推向机头,经机头内的模具,使粘流体成型为所需要的各种尺寸形状的挤包材料,并包覆在线芯或导体外。
第三阶段是定型阶段。
它是在冷却水槽或冷却管道中进行的,塑料挤包层经过冷却后,由无定型的塑性状态变为定型的固体状态。
3.塑化阶段塑料流动的变化在塑化阶段,塑料沿螺杆轴向被螺杆推向机头的移动过程中,经历着温度、压力、粘度,甚至化学结构的变化,这些变化在螺杆的不同区段情况是不同的。
塑化阶段根据塑料流动时的物态变化过程又人为的分成三个阶段,即加料段、熔融段、均化段,这也是人们习惯上对挤出螺杆的分段方法,各段对塑料挤出产生不同的作用,塑料在各段呈现不同的形态,从而表现出塑料的挤出特性。
在加料段,首先就是为颗粒状的固体塑料提供软化温度,其次是以螺杆的旋转与固定的机筒之间产生的剪切应力作用在塑料颗粒上,实现对软化塑料的破碎。
而最主要的则是以螺杆旋转产生足够大的连续而稳定的推力和反向摩擦力,以形成连续而稳定的挤出压力,进而实现对破碎塑料的搅拌与均匀混合,并初步实行热交换,从而为连续而稳定的挤出提供基础。
在此阶段产生的推力是否连续均匀稳定、剪切应变率的高低,破碎与搅拌是否均匀都直接影响着挤出质量和产量。
在熔融段,经破碎、软化并初步搅拌混合的故态塑料,由于螺杆的推挤作用,沿螺槽向机头移动,自加料段进入熔融段。
在此段塑料遇到了较高温度的热作用,这是的热源,除机筒外部的点加热外,螺杆旋转的摩擦热也在起着作用。
而来自加料段的推力和来自均化段的反作用力,使塑料在前进中形成了回流,这回流产生在螺槽内以及螺杆与机筒的间隙中,回流的产生不但使物料进一步均匀混合,而且使塑料热交换作用加大,达到了表面的热平衡。
由于在此阶段的作用温度已超过了塑料的流变温度,加之作用时间较长,致使塑料发生了物态的转变,与加热机筒接触的物料开始熔化,在机筒内表面形成一层聚合物熔膜,当熔膜的厚度超过螺纹顶与机筒之间的间隙时,就会被旋转的螺纹刮下来,聚集在推进螺纹的前面,形成熔池。
由于机筒和螺纹根部的相对运动,使熔池产生了物料的循环流动。
螺棱后面是固体床(固体塑料),物料沿螺槽向前移动的过程中,由于熔融段的螺槽深度向均化段逐渐变浅,固体床不断被挤向机筒内壁,加速了机筒向固体床的传热过程,同时螺杆的旋转对机筒内壁的熔膜产生剪切作用,从而使熔膜和固体床分界面的物料熔化,固体床的宽度逐渐减小,知道完全消失,即由固态转变为粘流态。
此时塑料分子结构发生了根本的改变,分子间张力极度松弛,若为结晶性高聚物,则其晶区开始减少,无定形增多,除其中的特大分子外,主体完成了塑化,即所谓的“初步塑化”,并且在压力的作用下,排除了固态物料中所含的气体,实现初步压实。
在均化段,具有这样几个突出的工艺特性:
这一段螺杆螺纹深度最浅,即螺槽容积最小,所以这里是螺杆与机筒间产生压力最大的工作段;另外来自螺杆的推力和筛板等处的反作用力,是塑料“短兵相接”的直接地带;这一段又是挤出工艺温度最高的一段,所以塑料在此阶段所受到的径向压力和轴向压力最大,这种高压作用,足以使含于塑料内的全部气体排除,并使熔体压实,致密。
该段所具有的“均压段”之称即由此
而得。
而由于高温的作用,使得经过熔融段未能塑化的高分子在此段完成塑化,从而最后消除
“颗粒”,使塑料塑化充分均匀,然后将完全塑化熔融的塑料定量、定压的由机头均匀的挤出。
塑料挤出温度
塑料品种
加料段
熔融段
均化段
机脖
机头
模口
聚氯
130〜
150〜
175〜
170〜
170〜
170〜
乙稀
140°C
170C
180C
180C
175C
180C
聚氯
150〜
160〜
175〜
175〜
170〜
170〜
乙稀
160C
170C
185C
180C
175C
180C
聚乙
140〜
180〜
210〜
210〜
200〜
200〜
烯
150C
190C
220C
215C
190C
210C
聚乙
130〜
160〜
175〜
170〜
170〜
170〜
烯
140C
170C
185C
180C
175C
180C
氟-46
260C
310〜
380〜
380〜
350C
250C
320C
400C
400C
加料段采用低温,这是由加料段承担的“任务”决定的,加料段要产生足够的推力,机械剪
切并搅拌混合,如温度过度,使塑料早期熔融,不但导致挤出过程中的分解,而且引起“打滑”,造成挤出压力波动,并因过早熔融,而致混合不充分,塑化不均匀,所以这一段温度一般用低温。
熔融段的温度要有幅度较大的提高,这是因为塑料在该段要实现塑化的缘故,只有达到一定的温度才能确保大部分组成得以塑化。
均化段的温度最高,塑料在熔融段已大部分塑化,而其中小部分高分子组成尚未开始塑化,就进入均化段,这部分组成尽管很少,但其塑化是必须实现的,这时其塑化的温度往往需要更高。
因此,均化段的挤出温度有所升高是必要的,有些时候,可以维持不变,而赖以塑化时间的延续,实现充分塑化。
机脖的温度要保持均化段的温度或稍有降低,这是因为塑胶挤出筛板变旋转运动为直线运动,而且由于筛板上的孔将塑胶熔体分散为条状物,在进入机头时必须在其熔融状态下将其彼此压实,显然温度下降太多是不行的。
机头承接已塑化均匀且由机脖压实的熔体塑料,起继续挤压使之密实之作用,塑胶在此有固定的表层与机头内壁长期接触,若温度过高,势必出现分解甚至是焦烧,特别是在机头的死角处,因此机头温度一般要下降。
目前挤出机中模口采用的温度升高、降低都有实例,一般模口温度升高可使表面光亮,但模口温度过高,不但会造成表层分解,更会造成成型冷却的困难,使产品难于定型,易于下垂自行形变或压扁变形。
因此,尽管各种塑料的挤出温度的控制高低不一,但都有一个普遍的规律,即从加料段起到模口止,都有一个温度从低-高-低的变化规律。
如果挤出过程中温度控制的不合适,塑料就会产生很多缺陷,影响挤出制品的质量。
工艺配模
1.模具的选配依据挤压式模具选配主要是依线芯选配模芯,依成品(挤包后)的外径选配模套,并根据塑料工艺特性,决定模芯和模套角度及角度差、定径区(即承线径)长度等模具的结构尺寸,使之配合得当、挤管式模具配模的依据主要是挤出速俩的拉伸比,所谓拉伸比就是塑料在模口处的圆环面积与包覆与电线电缆上的圆环面积之比,即模芯模套所形成的间隙截面积与制品标称厚度截面积之比值,拉伸比:
K=(D2—D2)/(d2—d2)
其中D1为模套孔径(mr);
D
2—为模芯出口处外径(mm;
d
1为挤包后制品外径(
mm;;
d
2为挤包前制品直径(
mm;。
不冋塑料的拉伸比K也不样,如聚氯乙稀
K=1.2〜1.8、聚乙烯K=1.3〜2.0,由此可确定模套孔径。
但此方法计算较为繁琐,一般多用经验公式配模。
2.模具的选配方法
(1)测量半制品直径:
对绝缘线芯,圆形导电线芯要测量直径,扇形或瓦形导电线芯要测量宽度;对护套缆芯,铠装电缆要测量缆芯的最大直径,对非铠装电缆要测量缆芯直径。
(2)检查修正模具:
检查模芯、模套内外表面是否光滑、圆整,尤其是出线处(承线)有无裂纹、缺口、划痕、碰伤、凹凸等现象。
特别是模套的定径区和挤管式模芯的管状长嘴要圆整光滑,发现粗糙时可以用细纱布圆周式摩擦,直到光滑为止。
(3)选配模具时,铠装电缆模具要大些,因为这里有钢带接头存在,模具太小,易造成模芯刮钢带,电缆会挤裂挤坏。
绝缘线芯选配的模具不易过大,要适可而止,即导电线芯穿过时,
不要过松或过紧。
。
(4)选配模具要以工艺规定的标称厚度为准,模芯选配要按线芯或缆芯的最大直径加放大值;模套按模芯直径加塑料层标称厚度加放大值。
3.配模的理论公式
(1)模芯D1=d+e,
(2)模套D2=D+2S+2△+e2
式中:
D——模芯出线口内径(mr);
D2模套出线口内径(mr);
d生产前半制品最大直径(mr)
3模芯嘴壁厚(mr);
△工艺规定的产品塑料层厚度(mr);
e,模芯放大值(mr)
e2模套放大值(mr)
(3)放大值e,或e2的说明。
1)绝缘线芯模芯e,的放大值为0.5〜3mm
2)绝缘线芯模套e2的放大值为1〜3mm
3)生产外护套电缆用模芯e的放大值、铠
装电缆为2〜6mr,i非铠装为2〜4mm
4)生产外护套电缆用模套e2的放大值为
2〜5mm。
4.举例说明模具的选配
1)生产绝缘线芯3X185mm的实心铝导体扇形电缆,其扇形(标称)宽度为21.97mm(其最大宽度允许值22.07mm),绝缘层标称厚度为2.0mm(其最小厚度允许值为2.0X90%^0.1=1.7mm模芯嘴壁厚为1.0mm选用模具。
模芯D=d+e1=21.97+1.5=23.47(mr)i考虑到实体扇形及最大宽度,选取D=24mm
模套孔径D2=D+28+2△+e?
=24+2X1+2X2+3=33
(mm)
2)生产电缆外护套,其型号为VLV,规格为
1X240mm,电压为0.6/1kV,
选用模具。
该电缆成缆后直径为23.6mm,护套
标称厚度为2.0mm取模芯嘴壁厚为1.5mm
模芯孔径D1=d+e1=23.6+3=26.2~27mm模套孔径D2=D+28+2△+e?
=27+2X1.5+2X2+4=38mm
3)在实际生产过程中,模具的选配往往在操作规程或生产工艺卡中给出一定的经验公式,如某厂065挤塑机给出的模具选配公式(△为
塑料挤包层的标称厚度)
挤压式
模芯(mr)i
模套(mm
单线
绞线
导线直径+
(0.05〜0.10)
绞线外径+
(0.10〜0.15)
导线直径+2△+
(0.05〜0.10)绞线外径+2△+
(0.05〜0.10)
挤管式
模芯(mr)
模套(mm
绝缘护套
线芯外径+
(0.1〜1.0)
缆芯最大外径+
(2〜6)
模芯外径+2△+
(0.05〜0.10)模套外径+2△+
(1.0〜4.0)
线芯或缆芯外径不均时,放大值取上限;反之取下限。
在保证质量及工艺要求的前提下,要提高产量,一般模套放大值取上限。
5.选配模具的经验
1)16mm以下的绝缘线芯的配模,要用导线试验模芯,以导线通过模芯为宜。
不要过大,否则将产生倒胶现象。
2)抽真空挤塑时,选配模具要合适,不宜过大,若大,绝缘层或护套层容易产生耳朵、起棱、松套现象。
3)挤塑过程中,实际上塑料均有拉伸现象存在,一般塑料的实际拉伸在2.0mm左右。
根据拉伸考虑模套的放大值,拉伸比大的塑料模套放大值大于拉伸比小的塑料模套放大值,如聚乙烯大于聚氯乙稀。
4)安装模具时要调整好模芯与模套间的距离,防止堵塞,造成设备事故。
废品的种类及排除方法
第一节焦烧
一、焦烧的现象
(1)温度反映超高,或者是控制温度的仪表失灵,造成塑料超高温而焦烧。
(2)机头的出胶口烟雾大,有强烈的刺激气味,另外还有噼啪声。
(3)塑料表面出现颗粒状焦烧物。
(4)合胶缝处有连续气孔。
二、产生焦烧的原因
(1)温度控制超高造成塑料焦烧。
(2)螺杆长期使用而没有清洗,焦烧物积存,随塑料挤出。
(3)加温时间太长,塑料积存物长期加温,
使塑料老化变质而焦烧
(4)停车时间过长,没有清洗机头和螺杆,造成塑料分解焦烧。
(5)多次换模或换色,造成塑料分解焦烧。
(6)机头压盖没有压紧,塑料在里面老化分解。
(7)控制温度的仪表失灵,造成超高温后焦烧。
三、排除焦烧的方法
(1)经常的检查加温系统是否正常。
(2)定期地清洗螺杆或机头,要彻底清洗干净。
(3)按工艺规定要求加温,加温时间不宜过长,如果加温系统有问题要及时找有关人员解决。
(4)换模或换色要及时、干净,防止杂色或存胶焦烧。
(5)调整好模具后要把模套压盖压紧,防止进胶。
(6)发现焦烧应立即清理机头和螺杆。
第二节塑化不良
一、塑化不良地现象
(1)塑料层表面有蛤蟆皮式地现象。
(2)温度控制较低,仪表指针反映温度低,实际测量温度也低。
(3)塑料表面发乌,并有微小裂纹或没有塑化好地小颗粒。
(4)塑料的合胶缝合的不好,有一条明显的痕迹。
二、塑化不良产生的原因
(1)温度控制过低或控制的不合适。
(2)塑料中有难塑化的树脂颗粒。
(3)操作方法不当,螺杆和牵引速度太快,塑料没有完全达到塑化。
(4)造粒时塑料混合不均匀或塑料本身存在质量问题。
三、排除塑化不良的方法
(1)按工艺规定控制好温度,发现温度低要适当的把温度调高。
(2)要适当地降低螺杆和牵引的速度,使塑料加温和塑化的时间增长,以提高塑料塑化的效果。
(3)利用螺杆冷却水,加强塑料的塑化和至密性。
(4)选配模具时,模套适当小些,加强出胶口的压力。
第三节疙瘩
、产生疙瘩的现象
(1)树脂在塑化过程中产生的疙瘩,在塑料层表面有小晶点和小颗粒,分布在塑料层表面四周。
(2)焦烧产生的疙瘩,在塑料层表面有焦烧物,特别反映在合胶缝的表面上。
(3)杂质疙瘩,在塑料表面有杂质,切片的疙瘩里面有杂质。
(4)塑化不良产生的塑料疙瘩,切片后发现疙瘩里面是熟胶。
、产生疙瘩的原因
(1)由于温度控制较低,塑料还没有塑化好就从机头挤出来了。
(2)塑料质量较差,有难塑化的树脂,这些没有完全塑化就被挤出。
(3)加料时一些杂质被加入料斗内,造成杂质疙瘩。
(4)温度控制超高,造成焦烧,从而产生焦烧疙瘩。
(5)对模压盖没有压紧,进胶后老化变质,出现焦烧疙瘩。
三、排除疙瘩的方法
(1)塑料本身造成的疙瘩,应适当地提高温度。
(2)加料时严格检查塑料是否有杂物,加料时不要把其它杂物加入料斗内,发现杂质要立即清理机头,把螺杆内的存胶跑净。
(3)发现温度超高要立即适当降低温度,如果效果不见好,要立即清洗机头和螺杆,排除焦烧物。
(4)出现树脂疙瘩和塑化不良的疙瘩,要适当调高温度或降低螺杆和牵引的速度。
第四节塑料层正负超差
一、产生超差的现象
(1)螺杆和牵引的速度不稳,电流表或电压表左右摆动,因此影响电缆外径,产生塑料层的偏差。
(2)半成品质量有问题,如钢带或塑料带绕包松,产生凸凹不均匀现象或塑料层有包、棱、坑等缺陷。
(3)温度控制超高,造成挤出量减少,使电缆的外径突然变细,塑料层变薄,形成负差。
二、产生超差的原因
(1)线芯或缆心不圆,还有蛇形,而外径变化太大。
(2)半成品有