焊接钢管工艺文件汇总资料.docx
《焊接钢管工艺文件汇总资料.docx》由会员分享,可在线阅读,更多相关《焊接钢管工艺文件汇总资料.docx(18页珍藏版)》请在冰豆网上搜索。
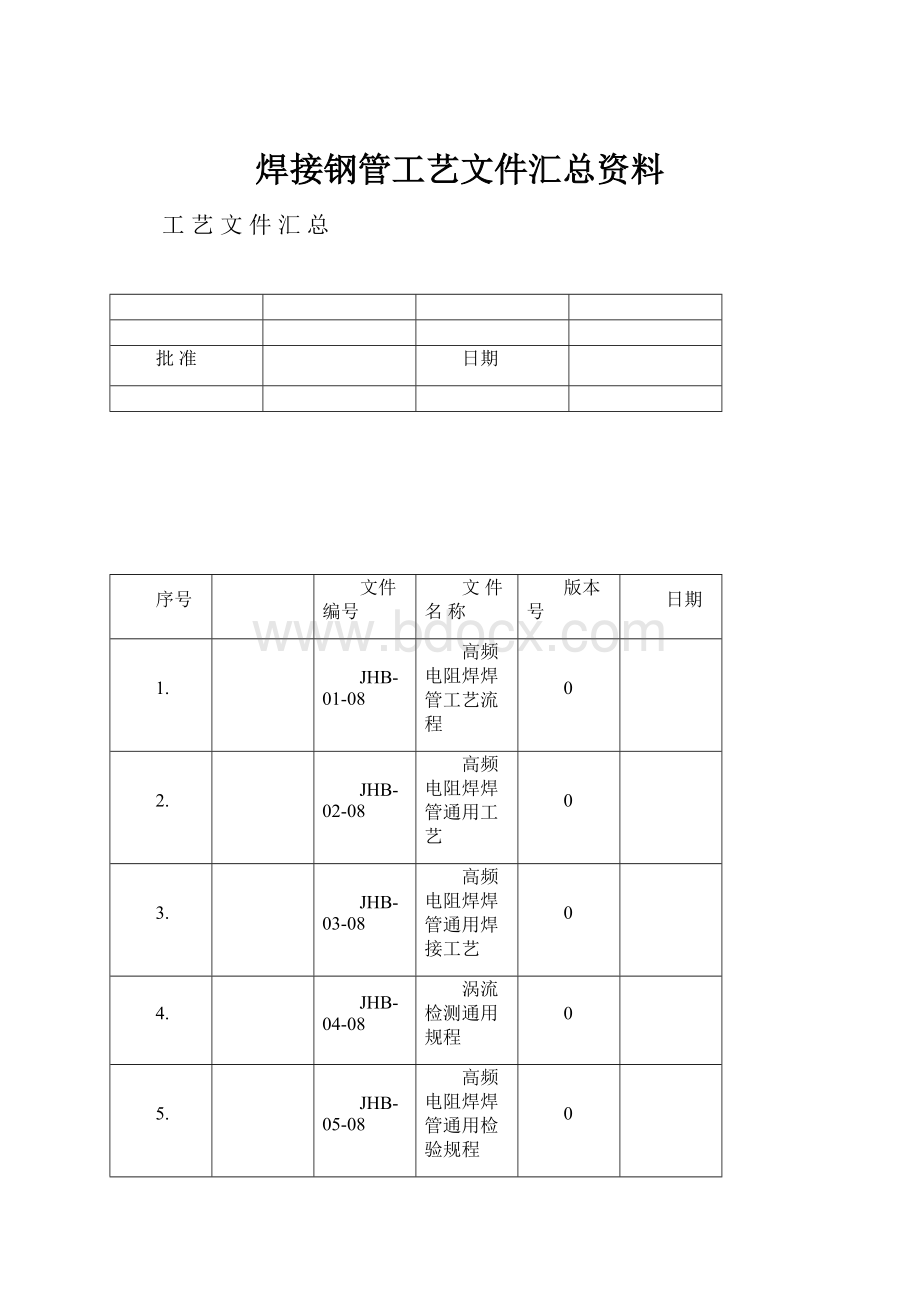
焊接钢管工艺文件汇总资料
工艺文件汇总
批准
日期
序号
文件编号
文件名称
版本号
日期
1.
JHB-01-08
高频电阻焊焊管工艺流程
0
2.
JHB-02-08
高频电阻焊焊管通用工艺
0
3.
JHB-03-08
高频电阻焊焊管通用焊接工艺
0
4.
JHB-04-08
涡流检测通用规程
0
5.
JHB-05-08
高频电阻焊焊管通用检验规程
0
6.
JHB-06-08
高频电阻焊焊管水压试验规程
0
修改记录:
文件编号
标记
修改人
修改单号及修改标记
日期
1.适用范围:
本文件适用于本公司B级高频电阻焊焊管的生产。
2.本公司高频电阻焊焊管由生产线的设备制造,生产线上制造工艺过程有:
上料、纵剪、成型、焊接、刮疤、涡流检测、锯切。
裁头后制成的管子再进行外观检验、弯曲试验、压扁试验、水压试验等检验过程,检验合格后的管子进行热镀锌后再进行包装。
3.
涡流检测
锯切
刮疤
高频电阻焊焊接
成型
纵剪
上料
B级高频电阻焊焊管的整个工艺流程如下图所示:
压扁试验
水压试验
弯曲试验
外观检查
报废
不合格
合格不合格
合格
复验
不合格不合格
包装入库
热镀锌
合格合格
锯切
铣头
其中:
上料----锯切的工序在生产线上完成。
1.适用范围:
本文件适用于本公司B级高频电阻焊焊管的生产。
2.本公司高频电阻焊焊管由生产线的设备制造,生产线上制造工艺过程有:
上料、纵剪、成型、焊接、刮疤、涡流检测、锯切,在外观检查前进行矫直、铣头。
3.上料要求:
3.1.1钢带应堆放整齐,防止滚动,歪倒伤人。
3.1.2挂吊要注意安全,起吊指挥正确。
3.1.3撬开带钢头时必须先用卡具卡紧外圈,防止钢带松开反弹伤。
3.1.4敲打带钢头时要戴护目镜,防止焊渣、毛刺弹伤眼睛。
3.1.5引料时集中精力操作,如有故障及时与上料工和主控台联系,停车检查。
3.1.6当钢带在活套内卡死,翻带时应及时停车,不能在运行中敲击。
3.1.7操作时要准确熟练,发现问题及时处理,防止带钢伤人。
4.纵剪要求:
4.1.1根据生产排产单对刀,检查刀轴、刀具、瓦合、轴承,进行装刀。
4.1.2压下不能太深,两边要平行;动调试,用眼睛观察上下刀间距。
4.1.3卷取和涨力不能分分割,原因是卷取没有涨力带钢容易粘包,带钢卷不紧、检卷,出现塔形等现象;分料盘,必须和刀轴一致。
5.成型要求:
5.1.1轧辊孔型中心与轧制中心线的偏差应小于0.5mm。
5.1.2上下孔型中心偏差应小于0.1mm。
5.1.3配套立辊高低偏差应小于0.1mm。
5.1.4立辊与水平下辊标高应一致。
5.1.5水平上辊两侧压下量应一致。
5.1.6上下轧辊的径向跳动和轴向窜动量应小于0.5mm。
5.1.7按照调整技术要求,找正成型辊、齐压辊、定么辊轧制中心线,调整立辊标高和水平辊压下量。
5.1.8引钢带进入成型机组低速运行,逐架次调整,由未架出来的管筒必须符合焊接要求,出定径机组的管体不得扭转,管径符合标准要求,管体无划伤。
6.焊接要求见JHB-03-08《高频电阻焊焊管通用焊接工艺》。
7.刮疤要求:
7.1.1刮疤工首先磨制好备用的刮疤刀。
7.1.2随时调整刮疤刀角度,保证刮疤光洁、圆滑。
8.涡流检测见JHB-04-08《高频电阻焊焊管涡流检测通用规程》。
9.锯切:
9.1.1根据生产排产单定尺要求,设定微机定尺长度。
9.1.2检察飞锯移动是否匀速,有无异常,定尺是否准确。
9.1.3生产中检查锯切管端口是否合乎标准,不允许有斜口。
9.1.4开锯前应检查导轨,飞锯周围是否有无障碍物,各部位安全防护措施是否齐全,各部位螺栓是否紧固,气压、气路是否正常。
9.1.5飞锯启动前,必须卡紧锯片防护罩,周围不得有人停留,防止火花溅出灼伤或其它意外事故。
9.1.6发生故障或正常停车时,应将锯车退回零位,所有微机按钮要关闭,并关闭整个卸压系统阀门。
9.1.7运转中的飞锯正面不许站人。
10.矫直:
10.1.1矫直机送管前必须和操纵台联系,以防顶管发生事故。
10.1.2矫直钢管时,严禁人员横跨辊道。
10.1.3在矫直弯曲严重的钢管时,必须停车(矫直机)由人将弯曲钢管送人昆道至矫直机第一对辊入口处,等人避开危险区时方可启动矫直机,以防弯管“甩鞭”伤人,或管口毛刺卷住手套等。
10.1.4设备运行中不许触摸传动部位和在矫直中的钢管。
10.1.5严禁开缝管进入矫直机。
11.铣头:
11.1.1查铣头机是否安装防护罩,安装是否牢固。
11.1.2设备运转时,不允许擦试或用手摸转动部位。
11.1.3不允许站在刀盘正侧面看平头情况,以免铁屑飞出伤人。
11.1.4管口毛刺大,或开裂的管不能铣头,以免打伤刀头,飞溅伤人。
11.1.5弯曲度大的钢管不得进平头机。
11.1.6换刀时应保证铣头机完全停止转动后,打开防护罩才能进行。
1.适用范围:
本文件对本公司焊管生产线的高频电阻焊及管子焊缝缺陷返修时的手工氩弧焊的焊接工艺进行规定,各生产线高频电阻焊焊接操作人员和手工氩弧焊焊工应按本文件规定进行操作,并填写工作记录。
2.焊接设备:
Φ32、Φ42、Φ76、Φ89、Φ114、高频电阻焊机组各一条。
3.焊工:
3.1受压元件的焊接必须由有《锅炉压力容器焊工考试规则》考试合格的焊工担任。
3.2焊工必须按设备操作规程或工艺文件要求操作,注意设备及人身安全。
3.3操作工必须做好生产记录。
4.高频电阻焊:
4.1焊接准备:
4.1.1先检验各齿轮箱,稀油润滑站及手动润滑部位的油路是否畅通,油量是否充足。
4.1.2开启冷却系统,检验水路是否畅通。
4.1.3检查联接主电机与减速机的连轴器,看螺丝是否有松动,转动要轻松自如,无卡阻现象。
4.1.4检查各机架螺丝,传动轴螺栓等紧固件,是否拧紧牢固。
4.1.5先点动开车,如无卡阻现象,即可开车,一分钟后停车,检验各润滑部位有无漏油,渗油现象,如一切正常,可先空载运行。
4.1.6在空载运行过程中,检验噪音大小,温度高低及运转是否平衡,如有不正常现象,须排除故障后再开车,如正常可操作高频进行尚生产。
4.2焊接:
规格
焊接速度
用料厚度
(单位mm)
阳压范围
(单位KV)
阳流范围
(单位A)
栅流范围
(单位A)
4分
50-80米/分
0.9-1.5
8.5-11
15-19
2.5-3.7
1.5-2.0
9-12
17-20
3-3.9
2.0-2.5
10-13
18-21
3.5-4.0
80-110米/分
0.9-1.5
9-11.5
17-20
3.0-3.8
1.5-2.0
9.5-12
17-21
3.2-3.9
2.0-2.5
10-13
18-21
3.2-4.0
1.2寸
45-60米/分
0.9—1.5
9—11
17—18.5
2.5—3.0
1.5—2.0
9.5—11.5
17.5—19
3.0—3.5
2.0—2.5
10—12
18—19.5
3.5—3.8
2.5—2.75
10.5—12.5
18—19.5
3.5—3.9
2.75—3.25
11—13
18.5—20
3.6—4.0
1.2寸
60-80米/分
0.9—1.5
9—11.5
17.5—18.5
2.8—3.0
1.5—2.0
9.5—11.5
17.5—19
3.0—3.5
2.0—2.5
10—12
18—19.5
3.5—3.9
2.5—2.75
10.5—12.5
18—20
3.5—4.0
2.75—3.25
11—13
18.5—21
3.6—4.2
2寸
30—50米/分
2.0—2.5
9.5—11.5
18—19
3.2—3.8
2.5—3.5
10—12
18.5—20
3.3—3.9
1.3—2.0
9—11.5
18—19
3.0—3.7
50-70米/分
2.0—2.5
10—12
18.5—20
3.2—3.9
2.5—3.5
11—13
19—21
3.5—4.2
1.3—2.0
9—11
20—24
4.0—5
4寸
20—45米/分
2.0—2.5
10—11
20—25
4.0—4.5
2.5—3.75
11—12
24—28
4.5—6
规格
焊接速度
用料厚度
(单位mm)
直流电压
(单位V)
直流电流
(单位A)
6分
50-80米/分
0.9-1.5
220-260
200-240
1.5-2.0
250-320
230-270
2.0—2.75
300-360
260-330
80-110米/分
0.9—1.5
330-410
300-380
1.5—2.0
360-440
360-420
2.0—2.75
380-460
400-460
1寸
50-80米/分
0.9—1.5
60-80
2800-320
1.5—2.0
70-110
300-430
2.0—2.5
100-130
410-480
2.5—2.75
120-150
470-530
2.75—3.25
140-170
510-550
80-110米/分
0.9—1.5
160-175
540-590
1.5—2.0
170-190
580-650
2.0—2.5
180-200
630-720
2.5—2.75
190-220
700-850
2.75—3.25
190-220
800-920
1.5寸
40-100米/分
1.5—2.0
300-360
300-380
2.0—2.5
330-410
380-460
2.5—2.75
360-440
440-560
2.75—3.25
380-460
550-620
2.5寸
30—60米/分
2.0—2.5
260-350
320-450
2.5—3.5
340-440
440-570
3寸
30—60米/分
2.0—2.5
300-380
380-470
2.5—3.75
380-460
460-630
5.手工氩弧焊:
5.1焊前准备
5.1.1焊工应阅看要施焊部位的焊接工艺要求、焊接工艺参数等。
5.1.2焊接缺陷应彻底清除。
施焊前应施焊表面附近宽度5~10毫米内的氧化皮、铁锈、油污、油漆和其他影响焊接质量的杂物清理干净并露出金属光泽。
5.1.3检查和调试焊接设备,使焊机处于待焊状态,确保电、气、水畅通,仪器仪表工作正常。
5.1.4进行焊接工作时,必须遵守用电安全工作规程及其有关技术安全规程的规定,并作好安全措施。
5.2焊接
5.2.1焊接应在室内进行,在室外进行时应避免风、雨、雷的直接影响。
如果环境温度低于0℃时,焊接应在施焊处50mm范围内预热到手触温度(约15℃)后,方可进行焊接。
5.2.2应尽量采用多层多道焊的工艺,每道焊缝的起弧与收弧处应错开,每道焊缝的宽度不宜大于焊条直径的2~3倍,高度不大于5毫米,焊缝应熔合良好。
5.2.3不允许在焊件非焊表面引弧,如发生引弧,应将弧坑磨平或补焊。
5.2.4中断焊接或收头尾时,焊丝应徐徐提起,不可太快,以使弧坑填满。
重新起弧时,应在断弧处前8~10毫米处进行,以使接头熔化良好。
5.2.5推荐的焊接规范参数:
焊接方法
钨极直径(mm)
焊接电流
焊接电压
备注:
手工氩弧焊
2.0
60~80
11~13
焊接速度由焊工灵活掌握工件越薄,焊接速度越大
2.5
90~110
12~15
6.质量要求:
焊缝高度及外观质量应符合产品标准和检验规程的要求。
1.适用范围
本文件适用于本公司焊管生产线的高频电阻焊的管子的涡流检测,对涡流检测的设备、工艺要求进行了规定,也适用于对返修后的管子的涡流检测。
2.引用标准、法规
2.1JB/T4730-2005《承压设备无损检测》
2.2GB/T3091-2001《低压流体输送用焊接钢管》
2.3GB/T7735《钢管涡流探伤检验方法》
2.4国家质量监督检验检疫总局国质锅检字[2003]248号文《特种设备无损检测人员考核与监督管理规则》
3.检测人员资格
3.1本涡流检测设备的操作人员应按《特种设备无损检测人员考核与监督管理规则》的要求取得II级以上人员资格。
4.检测设备、器材和材料:
4.1检测设备
4.1.1本公司采用EEC-22+智能金属管棒涡流探测仪。
4.1.2本公司焊管的涡流检测采用外穿式方法,对管子对比试样响应的周向灵敏度差小于3DB,缺陷分辨率优于30mm。
4.1.3设备包含1KHZ~500KHZ的工作频率范围。
4.2对比试样
4.2.1对比试样材料为符合GB/T700中Q235B牌号要求的焊管。
4.2.2对比试样表面状态与被检钢管具有相同的表面状态要求。
4.2.3对试样人工缺陷采用通孔形形状。
4.2.4对比试样通孔的尺寸如下:
验收等级A(mm)
验收等级B(mm)
钢管外径D
通孔尺寸
钢管外径D
通孔尺寸
D≤27
1.20
D≤6
0.5
27<D≤48
1.70
6<D≤19
0.65
48<D≤64
2.20
19<D≤25
0.80
64<D≤114
2.70
25<D≤32
0.90
114<D≤140
3.20
32<D≤42
1.10
验收等级A(mm)
验收等级B(mm)
钢管外径D
通孔尺寸
钢管外径D
通孔尺寸
140<D≤180
3.70
42<D≤60
1.40
D>180
双方协议
60<D≤76
1.80
76<D≤114
2.20
114<D≤152
2.70
152<D≤180
3.20
D>180
双方协议
4.2.5对比试样通孔位置:
中部3个孔,其中一个位于焊缝上,3个孔沿圆周方面相隔120°±5°对称分布,轴向间距不小于200mm;两端端部小于或等于200mm处各钻1个相同尺寸的通孔,以检查端部效应。
4.2.6对比试样钻孔时应保持钻头稳定,防止局部过热和产生毛刺。
当钻头直径小于1.10mm时,其钻孔直径不得比规定大0.10mm。
当钻头直径不小于1.10mm时,其钻孔直径不得比规定大0.20mm。
4.2.7对比试样的使用时机:
4.2.7.1每次检测开始前和结束后;
4.2.7.2怀疑检测设备运行不正常时;
4.2.7.3连续检测时,每4小时检查和复验1次;
4.2.7.4各方有争议或认为有必要时。
5.检测表面准备
5.1被检焊管表面应清洁、无毛刺,不应有影响涡流检测实施的粉尘和污物,特别是铁磁性粉屑。
如有,应加以清除,清除时不应损坏被检焊管表面。
5.2被检焊管的表面粗糙度、尺寸公差、弯曲度等参数应满足产品标准的要求。
6.检测环境
6.1检测场地附近不应有影响检测实施的磁场、震动、腐蚀性气体和其他干扰。
7.检测时机
7.1在生产线上的连续检测;
7.2有焊缝缺陷产品在清除缺陷并满足表面要求后。
8.检测工艺和检测技术
8.1本公司采用穿过式线圈检测方法,检测时钢管通过导轨穿过线圈,进行涡流检测。
8.2检测设备通电后,先进行不少于10分钟的系统预运转。
8.3按规定的验收水平调整灵敏度时,信噪比应不小于6DB。
对比试样通孔响应信号的幅度应在仪器荧光屏满刻度的30~50%,对比试样和检测线圈之间的相对移动速度与被检钢管和检测线圈之间的实际相对移动速度相同。
8.4对比试样中间3个对称通孔的显示幅度应基本一致,选取最低幅度作为检测设备的触发报警电平。
9.检测结果的评定和质量等级的分类;
9.1质量验收等级按供需双方合同或按产品标准规定,按GB/T3091-2001标准生产时,为A级。
9.2经检验未发现尺寸(包括深度)超过验收标准缺陷的管材为合格品。
9.3经检验发现有尺寸(包括深度)超过验收标准缺陷的管材在管子公称外径不大于168.3mm时判定为不合格品;如管子公称外径大于168.3mm时,允许补焊后进行复探,若满足9.2条要求为合格品,否则为不合格品。
10.检测记录、报告和资料归档
10.1检测记录、报告和资料按JHA-06-08《无损检测控制程序》要求进行归档。
1.适用范围
本文件适用于本公司高频电阻焊焊管产品的过程检验和成品检验。
2.检验项目:
长度偏差、椭圆度、壁厚偏差、管体外径偏差、管端外径偏差(外径大于168.3mm管子要求)、弯曲度、管端。
3.检查时机
每条生产线按班次和产品批次安排检验。
每班开始和结束、同一批号的产品生产的开始和结束、每隔1~2小时(中间检查)。
4.检查方式
过程抽检,抽查数量:
2~5根;成品:
逐根。
5.长度
5.1通常长度:
电阻焊钢管为4000mm~12000mm。
5.2定尺长度:
钢管的通常长度范围内,允许偏差+20-0。
5.3倍尺长度:
钢管的通常长度范围内,允许偏差+20-0,每个倍尺应留5mm~10mm的切口余量。
6.椭圆度:
7.壁厚允许偏差:
不超过公称壁厚的±12.5%。
8.管体外径和管端外径的允许偏差(见下表)
公称外径D/mm
管体外径允许偏差
管端外径允许偏差/mm
(距管端100mm范围内)
D≤48.3
±0.5mm
--
48.3<D≤168.3
±1.0%
--
168.3<D≤508
±0.75%
+2.4
-0.8
9.弯曲度
9.1公称外径不大于168.3mm的钢管,为使用性平直,或经供需双方协议规定弯曲度指标。
9.2公称外径大于168.3mm的钢管,
10.管端
10.1钢管两端面应与钢管的轴线垂直,且不应有切口毛刺。
10.2外径大于168.3mm的钢管,其切口斜度应不大于5mm。
11.表面质量
11.1焊缝:
钢管焊缝的外毛刺应清除,其剩余高度不大于5mm。
如需方要求并经供需双方协议,焊缝内毛刺可清除或压平,其剩余高度不大于1.5mm,当壁厚不大于4mm时,清除毛刺后刮槽深度应不大于0.2mm;当壁厚大于4mm时,刮槽深度应不大于0.24mm。
11.2表面缺陷:
钢管内、外表面应光滑,不允许有折叠、裂缝、分层、搭焊等缺陷存在;允许有不超过壁厚负偏差的其他缺陷存在。
12.记录
12.1检查数据填写在“产品检查记录”(TJHA-07-1)上,并按产品批号归档。
1.适用范围:
本文件适用于本公司高频电阻焊焊管的水压试验管理。
确保产品质量满足规定要求。
2.职责:
技质部检验员负责水压试验时产品的检验,生产部负责水压试验的实施,检验责任师负责水压试验的控制。
3.水压试验设备及设施
3.1在水压试验场地内要备有一些必要的设备及工具。
水压试验设备要处于良好状态。
3.2应采用标定过且在有效期内的压力表,数量不得少于2只。
试验用压力表应具有约两倍于最大试验压力的量程。
压力表量程不得小于最大试验压力的1.5倍或大于它的4倍。
表盘直径应大于100mm。
精度等级不低于1.5级。
3.3使用时,若发现压力表被损坏或有怀疑时,不能使用。
此时压力表必须更换,重新标定或修理。
3.4水压试验场地应有可靠的安全防护设施,并经安全负责人认可。
3.5水压试验过程中,水压试验人员不得进行与试验无关的工作。
在被检产品有压力的情况下,不得离开工作岗位。
3.6与水压试验无关人员不得在试验现场停留,并应设置明显警示标志。
4.水压试验的条件及要求:
4.1水压试验应在产品涡流检测合格且抽查的弯曲试验、压扁试验合格后进行:
4.2水压试验时用水应是洁净的,水压试验应在周围气温高于5℃时进行,低于5℃时必须有防冻措施,水压试验用水应保持高于周围露点的温度以防产品表面结露,但也不宜过高以防止引起汽化和过大的温差应力,一般为20~70℃。
4.3水压试验压力不得超过规定的压力。
4.4水压试验测温方法:
a.水温采用经过标定的温度计浸没在水中测量。
b.金属壁温以测外壁为准,可采用接触式表面热电偶测温仪测量。
5.水压试验操作程序
5.1水压试验时加压到规定的压力后停留(稳压)规定的时间。
5.2试验压力及停留(稳压)时间如下表所示:
公称外径D/mm
试验压力值/MPa
停留(稳压)时间/s(秒)
D≤168.3
3
不少于5
168.3<D≤323.9
5
5.3水压试验过程中,如发现有异常响声,压力突然下降或加压装置发生故障等不正常现象时,应立即卸压,停止试验,并查明原因。
5.4水压试验在稳压时间后以钢管不渗漏为合格。
5.5“水压试验报告”(T11-1)由检验员填写,检验责任工程师审核,当产品经监检时应有监检单位人员的签名或盖章。
5.6水压试验报告按产品批号归档。